油田采出液成分复杂,易对金属管道产生腐蚀,导致管道失效等事故发生。因此,油田生产中需要对管道进行保护,添加缓蚀剂是常用防护手段之一。
金属管道腐蚀是由于管道金属(主要成分是铁)在电化学作用下从单质状态转化成金属离子溶解于流动介质中,造成管壁逐渐减薄或发生破损的过程。因此,管道内流动介质中总铁(含量)的变化和管道的腐蚀是存在定量关系的。即介质中总铁增加量可以反映管道腐蚀的严重程度,总铁增加量减少说明腐蚀减缓。据此,可以利用管道中的总铁变化情况来判断缓蚀剂加注等腐蚀防护措施的有效性。
塔河油田原油集输系统目前采用的防腐蚀方法是在各区域加注相同浓度缓蚀剂,但防护效果却大不相同,部分区块存在药剂加注过量或欠量的情况。本工作测量了介质中的总铁变化情况,对不同井次中缓蚀剂的防护效果进行对比,以期为实现缓蚀剂精细加药,精准防护提供理论支撑。
试验原理与方法
塔河油田现用缓蚀剂为咪唑啉类缓蚀剂,检测其含量的方法是利用显色剂与咪唑啉反应形成有色络合物,通过测量有色物质的特定光谱吸收峰值,推算缓蚀剂浓度。本工作主要参考该方法进行缓蚀剂残余浓度测量。
塔河现场使用的咪唑啉缓蚀剂为棕红色液体,pH约为7。使用特定的显色剂显色后,利用紫外分光光度计检测吸光度,在415nm处出现最大紫外吸收峰,且吸光度与缓蚀剂浓度呈线性关系。
油田采出液具有强腐蚀性,与管道内壁接触后在复杂电化学作用下会使金属管道中的铁单质转化为离子状态,发生腐蚀。由于采出液在内密闭条件下运移,与氧隔离,腐蚀产生的金属离子主要是二价亚铁离子。根据氢氧化亚铁的溶度积常数Ksp及介质pH可以估算在特定条件下介质中亚铁离子的最大容许浓度。若现场取样的总铁含量小于该数值,可以认为铁未沉淀凝结而是以离子状态存在的,现场介质中检测出的新增铁可以认为是管道腐蚀产生的铁。
塔河油田采出液pH为6.5~7,本工作取pH为7进行估算。氢氧化亚铁Ksp=8.0×10-16,pH=7则[H+]=[OH-]=10-7mol/L,估算亚铁离子的最大质量浓度为6400mg/L,pH较低时溶液中的亚铁离子容许浓度更高。通常情况下,采出液中的总铁离子含量不会超过该数值。因此,认为某特定管道腐蚀产生的铁全部溶解于流动介质中,即管道进口端、出口端的总铁量发生变化是该管道腐蚀所造成的。本工作主要根据管道进出口两端总铁含量增加值来判管道断腐蚀程度,评估缓蚀剂的缓蚀效果。同时,结合现场挂片所得腐蚀数据,最终确定缓蚀剂的最佳加注浓度。
生产油井产出的采出液经计转站(又称计量站)计量及简单分离,继续输送至联合站进行严格的净化处理,可以得到成品原油。
根据井场大小和位置,加药前后取样点距离一般在200m以内,加药后至进站取样点的距离则可能达到几公里甚至更长。同一时间在同一条管道前后端不同位置取样检测到的总铁会有增加,认为这是管道腐蚀后产生的铁离子进入管道内液体所造成的。
在塔河油田选取高含水的T-101井,含水低的T-202井及对应管道为对象进行取样分析。取样位置分别为单井井口加药装置前端、井口加药后及单井进站汇管部位,单条管道沿线各点流经介质相同,如图1所示,根据不同取样位置的总铁量,分析管道腐蚀情况。
图1 取样分析部位示意图
缓蚀剂加入量为30,60,90,120mg/L,每个加注条件下连续加注30天,每个加注浓度经过7天稳定加注后开始取样,隔天取一次,共取样三次,按照SYT 5329-2012《碎屑岩油藏注水水质推荐指标及分析方法》检测缓蚀剂浓度(也称为缓蚀剂残余浓度)和总铁浓度,取三次测量结果的平均值为最终结果。
试验结果与讨论
1 缓蚀剂残余浓度及总铁含量
(a)T-101井
(b)T-202井
图2 不同缓蚀剂加注条件下单井的缓蚀剂残余浓度
由图2可见:总体看上两口井沿线的缓蚀剂残余浓度变化趋势一致,残余浓度均随加注浓度增加而增加。井口加药前几乎为零(个别不为零,主要原因是不同水样带有不同程度的颜色,使检测结果出现少许的正偏差),加药后浓度增加,沿管道运移至汇管处,浓度略有降低。30,60,90,120 mg/L加注条件下,T-101井加药后残余缓蚀剂浓度的相对误差分别是6.9%、-23.9%、-19.8%、-30.6%,T-202井的分别为40.9%、6.2%、-6.2%、-17.1%。加注量为30mg/L 时,试验周期内测得残余缓蚀剂浓度略高于设计加注浓度,90,120mg/L加注条件下,试验周期内检测到的缓蚀剂残余浓度略低于设计加注浓度。除了现场取样存在一定的偶然差别外(例如液量、放空时间差别等),还有以下两方面原因,一是浓度低时水样本身色度对结果影响较大,产生较大的正误差;二是由于加注装置本身调节流量的开度较难准确控制。实际操作时,为保证最低浓度,低浓度加注量往往存在一定的正偏差,高浓度时则相反。
(a)T-101井
(b)T-202井
图3 不同缓蚀剂加注条件下单井的总铁含量
由图3可见:两口井的总铁浓度变化趋势一致,井口到加药后略有升高,沿管道至站内汇管处明显升高。总铁增加值随缓蚀剂加注量升高,略有降低。两口井的总铁增加绝对值差别较大,T-101井的增加值为11~16mg/L,T-202的为2~4 mg/L。
2 缓蚀剂消耗与总铁增加的关系
为更精确定量对比残余浓度与总铁增加值之间的关系,结合缓蚀剂吸附作用原理,分别根据两条管道的长度、管径,求出管道内表面积,根据表面积和该段管道缓蚀剂残余浓度改变量计算出单位面积缓蚀剂的消耗量,再与对应的总铁增加值对比,结果如图4所示。
(a)T-101井
(b)T-202井
图4 单井沿线单位面积缓蚀剂浓度消耗与总铁增加值关系
T-101井的缓蚀剂消耗量为0.0036~0.0106mg/(L·m2),T-202井为0.0043~0.0079mg/(L·m2),缓蚀剂加注量增大消耗量增大。总铁增加值随缓蚀剂消耗量的增加而降低,即缓蚀剂消耗量与总铁增加值呈负相关,但两者并非定量的等比关系。
结果说明,缓蚀剂浓度增加,管道表面吸附量大,对腐蚀的抑制作用也较大。但成倍增长的缓蚀剂浓度并不能等比例减少总铁的量。
3 防护效果及经济性
为比较缓蚀剂残余浓度对总铁的抑制程度,将缓蚀剂加注量为30mg/L条件下的缓蚀剂残余浓度和对应的总铁增加相对值设定为100,比较其他条件下残余浓度相应变化时对应总铁相对变化值,根据两者的变化,对比缓蚀剂浓度对总铁增加的抑制情况。
(a)T-101井
(b)T-202井
图5 不同加注条件下缓蚀剂残余浓度和总铁浓度的相对变化情况
由图5可见:总铁相对值的变化降幅最大的是T-202井在90mg/L缓蚀剂加注条件下的,降幅为33.71%,而此条件下对应的缓蚀剂残余浓度相对值则从100增至200.25,增幅100.25%。
另外还可见:当缓蚀剂加注量为30mg/L时,对总铁的抑制率较高。但在选择缓蚀剂最终加注量时,除了要考虑对总铁抑制率外,还要考虑是否满足腐蚀防护的其他要求。根据西北分公司规定,要求油系统腐蚀速率≤0.025mm/a。
T-101和T-202井的相关腐蚀监测数据如图6所示。根据现场监测点的布置,数据均采自单井进站处。
图6 管线在不同缓蚀剂加注条件下的腐蚀速率监测结果
由图6可见,在T-101井中,当缓蚀剂加注量为30mg/L时,管线的腐蚀速率超过0.025mm/a,其余加注量条件下的腐蚀速率均符合要求。因此,T-101井的缓蚀剂最佳加注量为60mg/L,T-202井的为30mg/L。
缓蚀剂加注优化后经济效益明显。以含水较高的T-101井为例,缓蚀剂加注量从30mg/L调整为60mg/L。以缓蚀剂单价1.1万元/t,液量50m3/d计,每年成本0.602万元,而管道腐蚀速率由0.0301mm/a降至0.0151mm/a,服役期限延长一倍。管道更换成本动辄数十万上百万,以每年几千元的药剂成本减少几十万的管道更换成本,经济效益十分可观;优化缓蚀剂加注还减少了管道刺漏对正常生产的影响,在明显提升经济效益的同时,降低了由于刺漏造成的对环境的影响,社会效益明显。
结 论
1 使用缓蚀剂管道内的总铁增加有一定的抑制作用,缓蚀剂加入量与管道首末端总铁增加值呈负相关。
2 根据原油系统腐蚀速率要求,T-101井缓蚀剂最佳加注量为60mg/L,T-202井的缓蚀剂最佳加注量为30mg/L。缓蚀剂浓度过低无法保证防腐蚀效果,缓蚀剂浓度过高,可进一步减少系统中总铁,但经济性降低。
免责声明:本网站所转载的文字、图片与视频资料版权归原创作者所有,如果涉及侵权,请第一时间联系本网删除。
相关文章
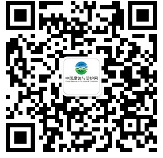
官方微信
《中国腐蚀与防护网电子期刊》征订启事
- 投稿联系:编辑部
- 电话:010-62316606-806
- 邮箱:fsfhzy666@163.com
- 中国腐蚀与防护网官方QQ群:140808414
点击排行
PPT新闻
“海洋金属”——钛合金在舰船的
点击数:7448
腐蚀与“海上丝绸之路”
点击数:5965