0 前言
航空发动机在服役过程中,由于受自然磨损、疲劳、腐蚀和叶片表面积垢等诸多因素的影响,随使用时间的增加发动机性能会衰退,其中压气机叶片表面积垢是引起发动机性能衰退的最重要的因素之一[1]。 MORINI等[2]基于级叠加模型,通过增加叶片的表面粗糙度和厚度,研究了叶片积垢对压气机性能的影响,结果显示,积垢降低了气流流量系数, 同时也会使压力系数降低,积垢严重时,可以使流量系数降低约5%,压力系数降低近9%。 CHEN等[3] 认为叶片前缘和吸力面积垢导致表面粗糙度增加, 对压气机的气动性能产生明显影响,使压气机效率和总压比明显降低。王松等[4] 的研究表明,积垢扩大了叶片气流分离区域,使叶片尾缘低速区增大,导致能量损失区域增大。积垢成分复杂,可能含有盐、酸等物质,积垢堆积必然会伴随腐蚀现象的发生,腐蚀严重时可能导致部件失效[5]。由此可以看出,积垢是造成压气机性能恶化的主要原因之一,积垢主要是增加了叶片表面粗糙度,改变了叶片型面,使得叶片表面气流流动发生变化,同时还会对叶片造成腐蚀破坏。因此,通过清洗消除积垢就显得尤为重要,发动机清洗作为一种经济有效的性能恢复手段, 已在燃气轮机和航空发动机上广泛应用,但是不同的清洗方法和清洗材料清洗效果不同,各有优缺点[6]。为了高效准确去除积垢,有必要对积垢的形成机理和性质进行深入研究,以利于选择合适有效的清洗剂和清洗方法。
压气机叶片表面积垢是发动机吸入气体中含有的颗粒物在油雾水气的黏性作用下,黏附在压气机叶片表面,主要来源是空气中混杂的各种粉尘、盐雾等物质[7]。沉积在压气机叶片表面的颗粒物通常是微米级的,通常在10 μm以下,由于黏性效应的作用,大气中含有的水分和压气机内部存在的油气加速了叶片表面积垢的堆积[8]。以上研究证明了积垢的来源,分析了积垢的影响因素,但是没有对积垢的成分和形成机理进行研究。王立文等[9] 通过收集两台民航发动机清洗废液,对沉积污垢进行分析,得到了主要附着物的成分及粒径范围。这种方式采集的污垢经过水洗沉淀,有些成分可能会溶解于溶剂而导致无法准确反映实际,而且也无法反映不同位置的叶片积垢形貌和成分。刘金豆[10] 对发动机进气部位的油污进行分析,确定了压气机不同部位叶片上油污的元素组成,以及有机相中有机物的大致类型,但没有进一步对叶片积垢的形成机理和性质进行研究。杨化动[11] 对积垢的形成机理进行了研究,主要是针对颗粒物的沉积理论和形成影响因素开展研究,进行了一些有益的数值研究,得出了很多有意义的结论,但都是基于数值计算和理论分析,未参考实际运行的发动机压气机积垢情况开展对比分析研究。
国内外针对压气机叶片上颗粒物的空气动力学因素进行了广泛的研究,但是有关发动机压气机各级叶片积垢成分性质和形成机理的研究很少。通过对返厂大修发动机压气机积垢情况的观察,发现高压压气机最后3级高温合金叶片表面积垢程度呈现逐级增加的趋势,并呈红褐色,与低压压气机和高压前几级钛合金叶片表面积垢呈现不同污染趋势和形貌。为了搞清楚压气机叶片积垢行为,分别从大修发动机低压压气机第2级、高压压气机第1级和最后1级转子叶片上实地采集积垢样品3份,试验分析压气机叶片表面积垢的微观形貌和化学成分,并对积垢形成机理和性质进行分析。
1 试验准备
1.1 样品的采集
从返厂大修的航空发动机压气机低压第2级、高压第1级和最后1级叶片上采用刀片刮取法分别实地取样三份,取样位置如图1中的1、2、3所示。为了后续分析方便,这里将低压第2级取样样品定义为1号样品,高压第1级取样样品定义为2号样品,高压最后1级取样样品定义为3号样品,取样样品实物如图2所示。
图1 混排涡扇发动机内涵气流温度示意图[12]
1.2 样品预处理
将待测的样品置于真空干燥箱内,120℃ 下充分干燥;将干燥后的样品置于玛瑙研钵中研磨成粉末;对于难以干燥的油性样品,干燥后采用液氮脆断的方式处理。
1.3 样品表征分析
航空发动机压气机叶片表面积垢样品表征分析流程如图3所示。
采用德国蔡司SIGMA500场发射扫描电子显微镜,观察积垢样品表面的微观形貌,电压10kV。采用德国蔡司SIGMA500EDS能谱仪,选择点扫模式, 取四个点进行积垢样品的元素分析(质量/原子相对百分含量)。采用德国AXS D8Advance X射线粉末衍射仪,表征积垢样品X射线衍射图谱,定性和定量地对样品的物相、结构或晶粒度进行分析判断, 对样品晶型结构进行解析,称取0.1g的样品置于消磁样品台中,用称量纸压匀,使用Cu靶,分析程序设置为步进扫描,扫描角度范围为10~80℃。采用德国BrukerVERTEX 70傅里叶变换红外光谱仪, 表征积垢样品红外光谱,定性分析样品表面的基团特征吸收频率,定量分析特征峰的强度,对样品中有机化合物的结构解析提供依据,采用KBr压片法将样品制成透明的薄片,使用的KBr为光谱纯,波数为600~4 000cm-1。采用美国日立Diamond TG/DTA热重分析仪,检测积垢样品热解失重量,称取少量样品置于热重仪的天平中,设置升温速率为5℃/min,试验气氛为空气,温度区间为0~800℃, 采用德国Pfeiffer OmniStar气体质谱分析仪,检测热解气体组份,将样品在TG测试中因为加热而分解的产物进入质谱仪,设置GC-MS程序,扫描范围0~200amu,间隔0.3amu,进样次数为1次/8℃,共计分析100次。
图2 样品实物示意图
图3 样品表征分析流程
2 试验结果与分析
2.1 样品外观分析
对样品实物(见图2a、2b、2c所示) 观察,可以看到,1号样品为黑色粘稠油状物质,2号样品为黑色粉末状物质,3号样品为红褐色粉末状物质,做简单磁性试验,发现3号样品带有一定的磁性。
2.2 SEM分析
使用SEM分别对1、2、3号样品试样表面不同区域进行采样观察,并拍摄记录其不同倍数下的形貌,结果如图4所示。
图4a、4b、4c为1号样品分别在5 000、10 000和50 000倍下的组织形貌图。由图可知,1号样品为团状包覆物,内部可见颗粒团聚且凝结在一起,其团聚粒子直径在1~3 μm,样品的SEM影像清晰度不高,这与样品本身含有大量油性物质有关,样品导电性不好导致积垢污染物成像不够清晰。
图4d、4e、4f为2号样品分别在10 000、50 000和100 000倍下的组织形貌图。由图可知,2号样品表面有大量不规则颗粒物,更多为团絮状,可以明显看到直径大于2 μm的不规则块状颗粒物被亚微米级的颗粒物(100~300nm)黏附现象,而其余大多为板状颗粒物,亚微米级颗粒物大多都团结在其表面, 形成7 μm以下颗粒。
图4g、4h、4i为3号样品分别在10 000、50 000和100 000倍下的组织形貌图。由图可以明显看出3号样品表面有大量不规则絮状颗粒物,由于高压压气机最后一级出口温度接近500℃ (见图1所示),因为热效应,存在颗粒物凝结在一起的现象, 其粒子最大直径可到0.8 μm左右。
图4 样品在3种倍数下的组织形貌图
2.3 EDS分析
以3号样品为例,在4 000倍放大倍数下对试样进行4次选点取样,4次能谱分析,如图5a所示, 从而得出试样各元素质量百分比和原子百分比,以图5a中区域1为例,其EDS元素峰值如图5b所示。 1、2、3号样品的EDS分析结果如表1所示。
图5 3号样品4 000倍取样位置及区域1的能谱分析
由表1可知,1号样品的元素成分包括C、O、Si、 Al、Mg、K元素,78.72%(原子分数) 的C说明1号样品中很可能含有大量的有机物质,后面通过FTIR和TG-MS分析可以进一步确认有机物结构和含量, 3.11%的Si说明空气中的灰尘也是1号样品的主要来源。 2号样品的主要元素包括C、O、S、K、Ti、 Mg、Si和少量的Cr、Na、F元素。 C的含量减少,O的含量增加,说明2号样品有机物含量减少,氧化物增多。 2号样品含有4.57%的Ti,这是因为钛合金在空气介质中加热时,会生成一种极薄、致密的氧化膜,氧化膜中的氧化物主要是TiO2 [13]。高压压气机第1级叶片基体材料为钛合金,由此可知,2号样品中的Ti来源于钛合金叶片表面的氧化膜。 3号样品的主要元素成分包括C、O、Fe、Si、Ni、S、K、Cr、Al和少量的Ti、Na、Ca和Mg元素。 3号样品取样叶片基体材料为Fe-Ni-Cr基高温合金,其主要元素包括33%~37%Ni、 14%~16%Cr、 2.8%~3.5%W、 2.6%~3.2%Ti、0.7%~1.4%Al和≤0.6%Si,以及其他微量元素, 其余为Fe。 3号样品中含有11.48%的Fe、5.06%的Ni,而1、2号样品中未检出这些元素,Al、Cr和Si的含量也较1、2号样品高很多,这些元素的原子分数总和达22.8%、质量分数总和达34.89%,这些元素都是叶片基体材料的主要组成元素,说明这些元素来源与大气环境相关性较低,而且,3号样品O的原子分数达40.29%,说明这些元素大多以氧化物的形式存在,这些元素的来源与高温合金叶片基体材料高温氧化行为相关性较高。
表1 积垢样品主要元素原子/质量分数均值测试结果(原子/质量分数)
2.4 FTIR分析
3 个样品的FTIR测试结果如图6 所示。由图6 可知1 号样品中存在饱和碳原子上的C-H振动,特别是-CH2 的对称 ( 2 855 cm-1 附近) 与反对称 (2 924 cm-1 附近)伸缩振动,结合EDS数据,认为1 号样品中还有C-F键(1 459 cm-1 附近) 和分子内氢键-OH基团(3 271 cm-1 附近),进一步证明了1 号样品中存在含C、 H、 O等元上的C-H振动 (615 cm-1 附近)、-CH2 的对称(2 854 cm-1 附近) 与反对称(2 923 cm-1 附近)伸缩振动,还存在C-O的伸缩振动 ( 1 105 cm-1 附近)、 C=C伸缩振动 (1 622 cm-1 附近) 和酰胺的振动 ( 1 702 cm-1 附近)。结合EDS数据,认为2 号样品中还存在Si-O (736 cm-1 附近) 伸缩振动,分子内氢键-OH基团 (3 407 cm-1 附近)。说明2 号样品中存在含C、H、 O等元素的有机物以及硅酸盐。 3 号样品存在C-O的伸缩振动 ( 1 107 cm-1 附近)、 C=C伸缩振动(1 650 cm-1 附近),可能还存在属于乙炔基的伸缩振动(3 310~3 300 cm-1 附近) 与弯曲振动(615~642 cm-1 附近),3 号样品的特征峰明显比1、2 号样品少,说明3 号样品的有机物含量较低,可能存在少量大分子有机物。
图6 1、2、3号样品中有机物红外谱图
2.5 XRD分析
3 个样品的XRD测试结果如图7 所示。由图7 可知,1 号样品XRD图晶峰比较杂乱,无定型结构,未检测到其他金属衍射峰,这主要与样品本身含油性导致导电性不好有关。 2 号样品具有一定的晶型结构, 根据Jade软件分析,存在含水的Na和Mg的硅酸盐晶型结构。 3 号样品具有较好的晶型结构,根据Jade软件分析,存在SiO2、镍钛氧化物(NiTiO3)、硫酸盐 (CaSO4、NaSO4)、Cr2O3、Fe2O3 等晶型结构。
2.6 TG-MS分析
对1号和2号样品进行热重和质谱测试分析,1号和2号样品的失重曲线见图8所示。由图8可知,1、2号样品在150℃ 前有少量失重,1号样品失重为3.51%,2号样品失重为10.37%,这主要是由于样品表面的水分或燃烧后CO2 等物质的挥发脱除,以及低分子量有机物的分解[9]。在150~500℃ 有明显失重,表明在该温度区间有物种进行了分解。 1号样品失重为62.47%,结合EDS和FTIR分析结果,进一步证明了1号样品存在大量含C、H、O等元素的有机物。 2号样品失重为54.98%,结合EDS和FTIR分析结果,说明2号样品主要是有机物进行了分解,可能还存在少量硅酸盐的分解;当大于500℃ 时,TG曲线接近直线,表明所有的有机物分解完成。
图7 3种样品的XRD图谱
图8 1号和2号样品的失重曲线
将样品在TG测试中因为加热而分解的产物放入质谱仪,经测试可得到产物的质谱峰,从而得到质谱图,如图9所示。由图9a可知,1号样品在质核比为28、32处能够观察到明显的信号,14、16、18、 29、34、40、44处能够观察到较明显的信号,46处有微弱的信号。由于使用全通道扫描,所进分解气体为混合物,对比EDS可以得到:N(质核比14)、O (质核比16)、H2O(质核比18)、CO(质核比为28)、 CO + (质核比为29)、NO(质核比30)、O2(质核比为32)、H2 S(质核比为34)、CO2 (质核比为44)、NO2 (质核比为46)的碎片或分子离子峰存在,这进一步证明1号样品中有C、H、O、N等元素组成的有机物,样品中的部分硫,主要以含硫有机物形式存在, 其热稳定性差,在低温区出现明显失重。由图9b可知,2号样品在质核比为28、32处能够观察到明显的信号,14、16、18、29、34、40、44处能够观察到较明显的信号,46、64处有微弱的信号,质核比64为SO2 分子离子峰。与1号样品相比,该样品中硫的存在形式相对稳定,在比较高的温度下才开始产生硫的相关离子峰,可以推测其主要形式是硫化物。说明2号样品中有C、H、O、N、S等元素组成的有机物、硫化物,以及少量含硫有机物。 3号样品由于所处的工作环境温度接近500℃ (如图1所示),所含有机物基本已经分解完。
由以上分析可以得知, 1号样品中含有约62.47%的有机物,2号样品中含有约54.98%的有机物,其中还含有硫化物、硅酸盐等物质,3号样品含有少量有机物,样品有机物质量分数如表2所示。
图9 1号和2号样品质谱图
表2 样品中的有机物质含量(质量分数)
3 积垢形成机理和性质
3 个样品分别取自压气机3 级具有代表性的转子叶片。 1 号样品取自低压2 级,低压压气机叶片材质相同,工作环境温度接近,积垢性状相似。 2 号样品取自高压1 级,3 号样品取自高压最后1 级,该型发动机高压压气机最后3 级叶片是Fe-Ni-Cr基高温合金,工作环境温度最高接近500℃,其它级是钛合金,工作环境温度在400~600 K(见图1 所示)。经对高压压气机叶片表面积垢实际污染情况观察,发现钛合金叶片表面积垢性状相似,呈积碳状,逐级递减的趋势;高温合金叶片表面积垢性状相似,呈红棕色,逐级增加的趋势,如图10 所示。
高压压气机最后1级叶片表面积垢宏观形貌和分布情况如图11所示。由图11a可以看出,积垢在叶片上的分布是非均匀性的,吸力面积垢主要分布在30%~40%弦长至尾缘位置,叶片前缘边沿处存在明显积垢,后缘位置积垢程度较重,叶尖处积垢程度低于叶根处,且从图中可以看出,吸力面表面积垢粗糙度较大。从图11b可以看出,压力面积垢程度较轻,分布有少量积垢,积垢程度明显轻于吸力面, 表面粗糙度也明显低于吸力面。
图10 高压压气机高温合金叶片表面积垢污染情况
图11 高压压气机最后一级叶片表面积垢
3.1 压气机叶片表面积垢形成机理
3.1.1 颗粒物沉积理论分析
气流中含有的颗粒物在压气机内运动时,受到了惯性力、重力、扩散力等作用力[14]。当颗粒物的运动速度和方向与气流不一致时,运动轨迹发生偏移,颗粒物越大惯性力越大,偏离气流轨迹的可能性就越大,撞击到叶片的可能性就越大。压气机流道内气流受到动叶施加的圆周速度,使气流方向发生偏转,颗粒物在惯性力的作用下偏离气流流线撞击到叶片表面,颗粒物越大撞击的概率越高。压力面表面积垢主要是较大颗粒物在惯性力作用下输送到叶片表面形成的。
小颗粒物受到的惯性力较小,偏离气流流线的可能性也小,大多数的小颗粒物会沿着气流流线运动,颗粒物越小布朗扩散系数越大[10]。在吸力面由于气流分离的影响,吸力面附近的气流流动为湍流流动,较小的颗粒物在湍流扩散力的作用下,黏附在吸力面后缘位置形成积垢。因此,吸力面积垢主要是较小颗粒物在扩散力作用下黏附形成的。
在气流流动的过程中由于流体的黏性特性,当相邻层流之间速度不一致时就会产生剪切应力,叶片表面与相邻层流之间的速度梯度大,会产生比较大的剪切应力,意味着在高剪切应力的作用下颗粒物存在较大的可能性被吹扫到下游。同时,叶尖位置存在的二次流会在吸力面叶尖部位产生较大的剪切应力。这些都会导致部分积垢被吹扫到下游,湍流流动中的涡流将这些颗粒物带到吸力面,从而在扩散力作用下沉积黏附在吸力面后缘位置,这也就解释了图11a中呈现的积垢分布形貌特征。
颗粒物能否黏附在叶片表面,除了与惯性力和扩散力有关,还取决于颗粒物黏附力的大小,水分和油气会增加颗粒物的黏附力[14]。因此,较高的大气湿度和发动机内部产生的大量油气会加速积垢的沉积,且增大了大颗粒物的黏附可能性。
3.1.2 低压压气机和高压压气机钛合金叶片表面积垢的形成机理
根据试验分析结果,结合以上分析可知,低压压气机和高压钛合金叶片表面积垢主要来源于空气中含有的粉尘、盐雾、SO2 等颗粒物和发动机内部存在的液态物质两个方面,其中有机物含量较高。压力面表面积垢主要是较大颗粒物在惯性力作用下形成的,受气流高剪切应力作用大部分颗粒物被吹扫到下游;吸力面积垢主要是较小颗粒物在扩散力作用下黏附形成的。
空气中的颗粒物随气流运动到压气机后端的量逐渐减少,且尺寸较小。而且,随级数的增加气流温度升高,气流中含有的水分和油气减少,颗粒物的黏附力降低,这也是低压压气机和高压压气机钛合金叶片表面积垢随级数的增加逐级减少的原因。因此,积垢在各级中的分布是非均匀性的,呈现逐级减少的趋势,杨化动[11] 通过相关研究已证明了该结论。郭忠烈等[15] 通过对某型航空润滑油高温氧化产物的研究表明,当温度约为230℃时,航空润滑油开始剧烈氧化,结焦积碳。在长时间较高的温度和压力共同作用下,高压钛合金叶片表面积垢中混杂的部分油类物质结焦形成积碳。
3.1.3 高压压气机高温合金叶片表面积垢的形成机理
高温合金在高温下存在氧化行为,高温合金发生高温氧化行为时,合金中的Cr、Ni、Al、Si四种元素在高温下通过选择性氧化行为,在合金表面形成连续致密的NiO、Al2O3、Cr2O3、SO2 氧化薄膜,隔绝基体材料与氧气的接触,起到抗氧化作用[16-17]。涡轮叶片工作环境恶劣,为了提高材料的抗氧化性能, 涡轮叶片采用的高温合金中添加了多种元素,选择性生成多重氧化物,形成多层抗氧化膜。高温氧化初始阶段,Ti与O的亲和力较强生成TiO2,随着高温氧化的持续进行,合金中的Cr元素首先发生选择性氧化,生成保护性的氧化薄膜Cr2O3,伴随有少量尖晶石NiCr2O4、镍钛氧化物NiTiO3 等生成,同时在内层形成以Al2O3 为主的氧化膜,以抑制合金元素与氧元素之间的相互扩散,抑制氧化膜的生长,延缓退化速度。合金高温氧化产物繁多,往往呈现分层结构, NiO、 CoO、 TiO2 等形成外氧化层, Cr2O3、NiCr2O4 等形成中氧化层,内氧化层主要是Al2O3 和SiO2 [18-19]。
高压压气机最后3级叶片为Fe-Ni-Cr基高温合金,高温氧化时合金中含量最高的Fe离子也会不断扩散析出发生反应,生成Fe2O3 和少量的Fe3O4,当合金的氧化行为发展到一定程度时,Fe2O3 和Cr2O3 形成连续固溶体,从而导致基体中的Fe离子可溶于Cr2O3 中并扩散通过Cr2O3 氧化膜,从而在合金表面抗氧化膜外层形成Fe的氧化层。表1显示3号样品中Fe的原子分数高达11.48%,说明高温合金叶片在长时间的高温使用环境下发生了Fe的离析氧化行为,在合金抗氧化膜外层形成了一层以Fe2O3 为主要成分的锈蚀氧化膜。 Fe2O3 一般形状表现为红棕色粉末,这与3号样品表现的红棕色形貌外观相符。合金中的微量元素Si在高温下易在氧化膜内层形成SiO2,以改善高温合金抵抗循环氧化能力,这也就解释了3号样品中Si的含量高于前两个样品的原因。高温条件下,合金还会发生低温热腐蚀,合金表面会发生硫酸盐的沉积,也会有少量的SO2 生成[20],样品XRD分析结果也证实了硫酸盐的存在。
综上说明,高压压气机最后3级高温合金叶片表面积垢主要来源于高温合金的高温氧化行为,主要是在合金抗氧化薄膜外层形成的以Fe2O3 为主要成分的锈蚀氧化物,其中含有少量Fe3O4。样品中存在的少量K、Na、Mg等金属元素,在2号样品中也有存在,说明还有少部分积垢来源于空气流中细微颗粒物的黏附堆积,其中含有的大部分有机物在高温作用下分解挥发,部分结焦形成积碳。由于高温氧化行为与温度正相关,随着温度的升高,高温合金高温氧化行为加剧,叶片表面积垢沿轴流方向呈现逐级增加的趋势。
3.2 压气机表面积垢的性质
高压钛合金叶片表面积垢,来源与低压压气机相同,但是在较高温度的作用下,部分有机物结焦, 形成积碳,宏观为黑色粉末状物质,微观为不规则颗粒物,直径在2 μm左右,团絮状,被亚微米级的颗粒物(100~300nm)黏附。其中有机物和硫化物、硅酸盐等含量占比最高达54.98%,沿轴流方向随温度的升高逐级减少。
高压最后3级高温合金叶片表面积垢主要来源于高温合金叶片高温氧化行为产生的氧化物,主要是在合金抗氧化薄膜外层形成的以Fe2O3 为主要成分的锈蚀氧化物,少部分来源于空气中的粉尘等细微颗粒物。积垢宏观为红褐色物质,有一定磁性,微观为不规则絮状颗粒物,存在颗粒物凝聚体,直径在0.8 μm左右,只含有少量有机物。
高压最后3级高温合金高温氧化腐蚀还会对叶片基体材料的力学性能产生不利影响。娄学明等[21]研究了IN718高温合金在650℃ 的热腐蚀行为,结果表明,由于合金晶界强度降低,合金持久性能显著降低。 PRADHAN等[22] 研究了IN718高温合金在600℃热腐蚀100h的高周疲劳性能,结果表明,随着热腐蚀的进行,合金表面有Cr、Fe、Ni氧化物生成,腐蚀物质进入合金基体在合金表面形成点蚀坑,使合金疲劳寿命下降。 HOMAEIAN等[23] 研究了617合金热腐蚀后蠕变行为,结果表明热腐蚀降低晶界强度,加速蠕变速率,使合金蠕变性能下降,导致合金持久性能的显著下降。综合以上分析可知,高温氧化腐蚀除了引起高压压气机性能衰退, 还会导致高温合金叶片基体材料的持久性能、疲劳性能和蠕变性能下降。
4 结论
(1) 高压压气机最后3级高温合金叶片表面积垢,主要是合金的高温氧化行为导致在合金抗氧化薄膜外层形成的以Fe2O3 为主要成分的锈蚀氧化物。 高温氧化腐蚀还会导致高温合金叶片基体材料的持久性能、疲劳性能和蠕变性能下降。
(2) 低压压气机和高压压气机钛合金叶片表面积垢主要由来自空气中的外部污染物和来自发动机自身产生的内部污染物共同组成,由于外部污染物与地理位置有直接关系,因此不同的地理位置会造成叶片表面积垢成分和严重程度产生很大的差异, 在清洗时机决策和清洗剂选择时必须考虑地理因素的影响。
(3) 高压压气机高温合金叶片表面积垢受地理位置的影响较小,其主要受合金高温氧化行为影响, 为了更精准地确定清洗时机,需要进一步研究高压高温合金叶片材料在工作环境温度下的高温氧化行为。
参考文献
[1] MOHAMMADI E,MONTAZERI-GH M.Simulation of full and part-load performance deterioration of industrial two-shaft gas turbine[J].Journal of Engineering for Gas Turbines and Power,2014,136(9):092602.
[2] MORINI M,PINELLI M,SPINA P R,et al.Computational fluid dynamics simulation of fouling on axial compressor stages [J].Journal of Engineering for Gas Turbines and Power,2010,132(7):072401.
[3] CHEN S,XU H,SUN S,et al.Influence of additional leading-edge surface roughness on performances in highly loaded compressor cascade [J].International Journal of Turbo & Jet-Engines,2015,32(2):155-163.
[4] 王松,王国辉,韩青,等.叶片积垢对压气机性能衰退的影响[J].哈尔滨工程大学学报,2014,35(12):1524-1528.
WANG Song,WANG Guohui,HAN Qing,et al.Compressor performance deterioration caused by blade fouling[J].Journal of Harbin Engineering University,2014,35(12):1524-1528.(in Chinese)
[5] MISHRA R K.Fouling and corrosion in an aero gas turbine compressor [J].Journal of Failure Analysis and Prevention,2015,15(6):837-845.
[6] MUND F C,PILIDIS P.Gas turbine compressor washing:historical developments,trends and main design parameters for online systems[J].Journal of Engineering for Gas Turbines and Power,2006:128(2):344-353.
[7] IGIE U.Gas turbine compressor fouling and washing in power and aerospace propulsion [J].Journal of Engineering for Gas Turbines and Power,2017,139:122602.
[8] KURZ R,BRUN K.Fouling mechanisms in axial compressors [J].Journal of Engineering for Gas Turbines and Power,2011,134(3):032401.
[9] 王立文,胡建伟,龙飞企,等.航空发动机内涵道污垢组分分析及积垢仿真研究[J].机床与液压,2019,47(15):88-93.
WANG Liwen,HU Jianwei,LONG Feiqi,et al.Analysis of dirt components of aero-engine connotation and research of dirt sedimentary simulation[J].Machine Tool & Hydraulics,2019,47(15):88-93.(in Chinese)
[10] 刘金豆.航空发动机外表面及其发动机表面清洗技术研究 [D].长沙:湖南大学,2018.
LIU Jindou.Study on cleaning technology of external surface and engine surface of aircraft [ D].Changsha:Hunan University,2018.(in Chinese)
[11] 杨化动.积垢的形成机理及其对轴流式压气机性能的影响研究[D].北京:华北电力大学,2014.
YANG Huadong.Research on the fouling mechanism and the effect of fouling on performance of axial flow compressor [ D].Beijing:North China Electric Power University,2014.(in Chinese)
[12] 何立明.飞机推进系统原理[M].北京:国防工业出版社,2006:10-11.
HE Liming.Principles of aircraft propulsion systems [ M ].Beijing:National Defense Industry Press,2006:10-11.(in Chinese)
[13] 梁锡梅,陈明和,苏楠,等.TA32 钛合金高温连续氧化行为研究[J].钛工业进展,2019,36(2):12-19.
LIANG Ximei,CHEN Minghe,SU Nan,et al.The isothermal oxidation behavior of TA32 titanium alloy at elevated temperature [J].Titanium Industry Progress,2019,36(2):12-19.(in Chinese)
[14] YANG H,XU H.The sensitive parameter study of axial flow compressor fouling [J].Research Journal of Applied Sciences Engineering & Technology,2013,5(10):3057-3062.
[15] 郭忠烈,费逸伟,姜旭峰,等.某型航空润滑油高温氧化产物分析[J].润滑与密封,2018,43(10):81-88.
GUO Zhonglie,FEI Yiwei,JIANG Xufeng,et al.Analysis on high temperature oxidation products of an aviation lubricating oil [J].Lubrication Engineering,2018,43(10):81-88.(in Chinese)
[16] LIU L F,SHU W U,CHEN Y,et al.Oxidation behavior of RE-modified nickel-based superalloy between 950 ℃ and 1 150 ℃ in air[J].Transactions of Nonferrous Metals Society of China,2016,26(4):1163-1169.
[17] 叶董文.GH2135 合金高温抗氧化性能和腐蚀性能研究[D].湘潭:湖南科技大学,2013.
YE Dongwen.Investigation of oxidation and corrosion resistance at high temperature for GH2135 Fe-based superalloy [ D ].Xiangtan:Hunan University of Science and Technology,2013.(in Chinese)
[18] 孙德山,肖旋,王常帅,等.K282 合金的高温氧化行为研究 [J].沈阳理工大学学报,2019,38(2):75-81.
SUN Deshan,XIAO Xuan,WANG Changshuai,et al.Investigation of high temperature oxidation behaviors of K282 alloy[J].Journal of Shenyang Ligong University,2019,38(2):75-81.(in Chinese)
[19] PARK S J,SEO S M,YOO Y S,et al.Effects of Al and Ta on the high temperature oxidation of Ni-based superalloys [J].Corrosion Science,2015,90:305-312.
[20] 曹将栋.提高镍基高温合金抗氧化腐蚀性能的试验及理论研究[D].镇江:江苏大学,2018.
CAO Jiangdong.Experiment and theoretical research on improving the oxidation corrosion resistance of Ni-based superalloy [ D].Zhengjiang:Jiangsu University,2018.(in Chinese)
[21] 娄学明,孙文儒,郭守仁,等.IN718 高温合金热腐蚀行为及其对力学性能的影响[J].稀有金属材料与工程,2008,37(2):259-263.
LOU Xueming,SUN Wenru,GUO Shouren,et al.Hot corrosion behavior of IN718 alloy and its effect on mechanical properties [J].Rare Metal Materials and Engineering,2008,37(2):259-263.(in Chinese)
[22] PRADHAN D,MAHOBIA G S,CHATTOPADHYAY K,et al.Effect of pre hot corrosion on high cycle fatigue behavior of the superalloy IN718 at 600℃ [J].International Journal of Fatigue,2018,114:120-129.
[23] HOMAEIAN A,ALIZADEH M.Interaction of hot corrosion and creep in alloy 617[J].Engineering Failure Analysis,2016,66:373-384.
免责声明:本网站所转载的文字、图片与视频资料版权归原创作者所有,如果涉及侵权,请第一时间联系本网删除。
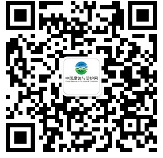
官方微信
《中国腐蚀与防护网电子期刊》征订启事
- 投稿联系:编辑部
- 电话:010-62316606-806
- 邮箱:fsfhzy666@163.com
- 中国腐蚀与防护网官方QQ群:140808414