去除杂质提高耐蚀性和强化改进
1
提高镁合金的纯度
一般高纯的镁合金比纯度不高的镁合金有较好的耐蚀性,提高镁合金的纯度是一种常用的提高镁合金耐腐蚀能力的手段。当杂质含量不超过它们的允许极限时,镁合金的腐蚀速度会很低,例如,AZ91和AM60在盐雾条件下的耐腐蚀性能比压力铸造的A1380(Al-4.5Cu-2.5Si)和冷滚轧钢还要好。
提高镁合金的纯度主要是通过冶金的方法进行,如对镁合金进行精炼,但一般成本比较高。
2
杂质无害化
将镁合金中的有害元素的含量降到较低的水平在技术上较难实现,成本也较高。实际上,去除杂质的有害性不一定要将杂质从镁合金中去除,如果能将杂质转化成无害的物质,则即使这些杂质还留在合金中,也对腐蚀性无大碍。较为容易和经济地达到这一目的的方法是在镁合金中加入一些易与杂质反应的元素,使杂质与这些元素结合后变成对腐蚀危害不大的物质。目前已知的有这种功能的元素有锰或错。所以,在镁合金中加锰或锆是镁合金杂质无害化的主要手段。一般含铝的镁合金中加入一些锰,或不含铝的镁合金中加入一些锆后,耐蚀性都会有较大的提高。
3
合金化
合金化是改变镁合金化学成分、相组成与微观结构的重要手段,它是提高镁合金耐蚀性的重要途径。
从提高耐蚀性的角度看,合金化的目的是促进基相的耐蚀性和耐蚀阻挡相的生成与合理分布,以提高镁合金的耐蚀性。
从目前常用的合金化元素来看,公认的对镁合金耐蚀性提高有益的元素是铝,只要镁合金中含有适量的铝,它的耐蚀性要比未加铝时的高。铝的加入,一方面促使合金中基相(α相)钝性提高;另一方面,有利于生成更多的更耐蚀的β相,在α相晶粒间形成连续的网络,阻止α相腐蚀的扩展。但铝的量应适中,否则会影响到镁合金的其他性能。另外,β相是否有阻挡腐蚀的作用,关键还是看是否形成了有效的阻隔网。此外,稀土与锆也能提高镁合金的耐蚀性,稀土元素主要是会促进镁合金的钝性,而锆可能会促使α相的化学稳定性。
特种铸造工艺
1
采用压力铸造工艺
压力铸造是最常用的一种镁合金构件生产方式,特别适用于大批量的生产。镁合金在冷腔压铸时,铸件表层的冷却速度较高,可认为是快速凝固过程,而铸件内部的冷却速度较低,与普通铸造较为接近。这样,快速凝固的镁合金的表层就有一定的特殊性,现以AZ91D压铸件为例说明。
由于铸造过程的特殊性,熔融镁合金在被压入模腔前就已凝固出部分含铝极低的α相晶粒。当被挤入金属压力模腔后,由于流体力学的作用,这些固体的低含铝α相晶粒倾向于集中到铸件表层,剩下的液态镁合金含铝较高。进入金属模腔后,在与模腔壁接触时,由于金属模的高热容量,表层受金属模壁的冷却速度较大,快速凝固。所以,镁合金的压力铸造件的表面总是有一层快速凝固而形成的表面层,晶粒很细,相对富铝而β相的量较多,并且分布十分均匀,沿着晶间形成了几乎连续的β相网络。这样的表面层显然有利于该压铸件的抗腐蚀。相反,在压力铸造的镁合金内部,α相晶粒粗大,β相较少且分布不连续,所以不耐蚀。压铸AZ91D合金在pH=11的1mol/L的NaCl溶液中的腐蚀情况见表1。
简言之,由于冷腔压力铸造,试样的表面微观结构一般比普通铸造的要细,β相的分布比较连续,能有效地阻止腐蚀的发展,故其耐蚀性也就相应较高。如果能适当地优化压力铸造的工艺过程,进一步地细化合金试样表面的晶粒度,提高耐蚀的第二相的含量与连续分布,镁合金的耐蚀性完全有可能得到进一步的提高。
2
采用半凝固铸造
半凝固铸造是一种较新的低成本的镁合金铸造技术。在半凝固铸造时,将熔化的镁合金的温度控制在液相线与固相线之间,这样镁合金在凝固时处于半凝固状态,约一半为固相一半为液相。在凝固过程中由于强烈的搅动,凝固中形成的枝晶被打碎。这样得到的固态合金,由于铸造温度较低,收缩率低、黏滞性高、能耗少、产率高、模具寿命长,其微观结构特点是较大的等轴。基相晶粒由较细的共晶a相与其他合金相包围着,β相的含量相对略多些。理论上,由于这些a相粗晶的四周形成了连续的阝相网络,可能会有效地阻止α相腐蚀的发展,同时还有可能使粗晶的a相中的铝含量(摩尔分数为2.7%)较普通铸造的镁合金的α相的(1.6%)高,故半凝固铸件的耐腐蚀性能较高。有时半凝固铸造的镁合金耐蚀性能甚至还会比压力铸造稍高些(见图1)。因此,半凝固铸造有可能成为提高镁合金耐蚀性的手段之一。
但实际上,有些半凝固铸造的AZ91D的腐蚀性能并不总是比普通模铸的好。有人发现,在NaCl溶液中,初期半凝固铸态的腐蚀速度较高,后期其腐蚀速度才降下来。这有可能是半凝固态的AZ91D合金的阴阳极差别较大,故电偶电池的作用较大,于是初期时电偶腐蚀活动较强烈所致。此外,还有报道,半凝固铸造还能提高镁合金在300℃以下的抗氧化能力。
图1 浸泡在5%NaCl溶液中的半凝固铸造与压力铸造AZ91与AM50镁合金腐蚀速度(25℃,72h)
强力塑性成型工艺
轧制、锻造、挤压等也是生产镁合金构件的重要方法。从理论上讲,这些制造过程 会很大程度上改变镁合金的微观组织结构,因此也会导致镁合金耐蚀性能的变化。例如,当变形量较大时,轧制、锻造和挤压成形都会使材料由铸态组织变为加工组织,消除粗大的柱状晶,压合气孔、针孔和疏松,消除枝晶使材料的晶粒细化、致密和均匀,这些显然会提高材料的耐蚀性、力学性能和综合性能。特别是在合金成分、变形温度和变形速度适宜的情况下,得用镁合金的超塑成形或等温度锻造,等温挤压等新工艺可更大程度强化和改性材料的组织与性能,当然其抗蚀性也会提高。
等通道挤压是一种很有效的细化晶粒的方法。四步等通道挤压可使AZ31镁合金获得平均晶粒尺寸为5μm的细晶组织,而对ZK60镁合金进行四步等通道挤压后,平均晶粒尺寸可达1.0~1.4μm。等通道挤压与适当的退火工艺相结合,可以大大提高变形镁合金材料的综合性能。
固溶热处理
热处理是调整合金相、成分分布与晶粒尺寸的有效手段。它对镁合金的腐蚀有很大的影响。热处理对镁合金腐蚀性能的影响,实质上是通过镁合金微观组织的变化而获得的。以AZ91E镁合金为例,T5与T6处理都可大大提高其耐蚀性,而T4处理则使其耐腐蚀性能大大降低。
常用的热处理方法有固溶均匀化热处理(T4)、固溶时效热处理(T6)和时效热处理(T5)。它们也可以用来改变镁合金的耐腐蚀性能。从目前对AZ91镁合金热处理的结果来看,这些热处理对耐蚀性能的改变很大程度上决定于它们对合金中第二相分布的影响。T4热处理减少合金析出的阝相,腐蚀速度因此上升;T5与T6热处理使大量β相析出,形成连续的腐蚀阻挡层,于是腐蚀速度下降。
图2所示为实效热处理对AZ91D压铸件腐蚀性能影响的情况。可以发现,在时效45h左右,AZ91D压铸件的腐蚀速度降到了最低点。这与时效热处理过程中镁合金中铝成分与β相组成和分布的变化有关。如图3和图4所示,AZ91D压铸件中的α相中固溶铝含量随着时效时间的增长而减少,这实际上不利于腐蚀速度的提高。但同时该压铸件中β相的量却是随着时效时间的延长而增大,且新增的β析出相主要分布于晶界上,这就有利于阻挡腐蚀的发展。这两个相反的腐蚀倾向随时效时间的变化,最终导致出现了腐蚀速度的最低值。
图2 160℃时效热处理对AZ91D压铸件腐蚀性能影响的情况
图3 AZ91D压铸件中的β相含量与α相中溶铝含量随160℃时效时间的变化
图4 AZ91D压铸件中的β相含量与分布随160℃时效时间的变化
(a)毛坯铸件;(b)6h;(c)15h;(d)45h;(e)585h
不过,对于杂质含量较高的AZ91C,热处理对腐蚀性能的影响则不明显。短时间的T5时效热处理对AZ91与AM60合金的抗蚀性有不利的影响。但时效时间较长时,合金的耐蚀性能又有所恢复。这种现象已不能简单地用β相变化来解释。
以上结果说明,时效热处理只要控制得好,也可以使镁合金材料的耐蚀性得到提高。
快速凝固
快速凝固一般是将熔融的镁合金,在保护性气氛中,喷送到具有较高热容的低温的金属模上,使熔融的镁合金急剧冷却凝固。当使用的低温金属模为一转轮时,可得到较薄的镁合金带,晶粒十分细小;当镁合金的成分恰当时,甚至还能得到纳米晶或非晶;还可用高压的惰性气体将熔化的镁合金喷到大块低温金属腔内以得到块状的镁合金;此外,也可用溅射、气相沉积、激光处理等手段使熔融的镁合金急剧冷却来获取快速凝固的镁合金。
快速凝固制成的镁合金,不仅可以提高材料的力学性能,而且也能增加其耐蚀性。提高耐蚀性的原因有:
(1)可能生成新相使有害杂质在新相中的电化学活性降低,或提高杂质的允许极限。
(2)使镁合金的晶粒细化甚至非晶化,同时使相与成分分布均匀化而降低微电偶腐蚀的活性。
(3)提高对耐蚀性有益的元素在镁中的固溶度,从而降低镁的电化学活性。例如,镁中如果含有较多的固溶铝,则有可能生成铝含量较高的表面氧化膜。这样镁合金就有较好的自钝性和修复性,这对镁合金的耐蚀性是有益的。
图5所示为快速凝固对镁合金腐蚀速度的降低作用。
图5 3%NaCl溶液中快速凝固镁合金与一些商业镁合金的腐蚀速度比较
镁合金的成分对快速凝固体的微观结构有重要的影响。如Mg-Ni合金的晶态结构会随着Ni含量的升高而变弱,当Ni含量为4.8%(摩尔分数)时,其相结构还主要为α-Mg与Mg2Ni;当Ni含量达到18.3%时,它完全变成了非晶。对应的,该镁合金在0.01mol/L NaCl(pH=12)溶液中的溶解速度也随着Ni含量的增高、非晶程度的变大而降低(见图6)。这种溶解速度的降低与该非晶合金钝性的提高有关。
图6 Mg与Mg-Ni快速凝固薄带在0.01mol/L NaCl(pH=12)溶液中的溶解速度
合金成分对快速凝固的镁合金耐蚀性也有至关重要的影响。图7所示为不同的合金元素对快速凝固二元镁合金腐蚀速度的影响。可以看出,铝是唯一能提高快速凝固二元镁合金耐蚀性的合金元素。
铝在快速凝固的镁合金中的作用就是促进钝化,提高点蚀破裂电位。在腐蚀过程中,由于镁的优先溶解而使铝在镁合金表面富集,表面膜的保护性增强。但锌在快速凝固的Mg-Zn-Y合金中似乎对腐蚀性影响不太确定。此外,固溶于镁中的Y元素能提高镁的耐蚀性。普通镁中Y的溶解度仅为3.75%(摩尔分数)。在快速凝固的镁合金中,Y有可能高于这一含量而不析出,从而对快速凝固的镁合金的耐腐蚀性起有益的作用。如15%~26%(质量分数)的Y能使快速凝固的镁合金出现伪钝化区。Y在快速凝固的镁中不仅提高了镁的钝性,还升高了镁的点蚀破裂电位。将Y加入Mg-Cu合金中不仅提高了该合金的耐蚀性,还增宽了它的钝化区。这与Y2O3进入到表面膜MgO的晶格中有关。
稀土元素不仅增加快速凝固合金的热稳定性,还对快速凝固的镁合金的耐蚀性有益。推测可能与如下两个因素有关:
(1)稀土与溶液反应生成保护膜。
(2)使合金中的第二相钝化而降低点蚀倾向。
另外,钙也能提高快速凝固镁合金的耐蚀性与热稳定性。因此,快速凝固的镁合金中加入钙与稀土应是较好的选择。
所以,以上这些对快速凝固镁合金的影响都可被利用来提高镁合金的耐蚀性。
其他方法
1
非晶化
非晶化的镁合金不仅比晶化的镁合金有较高的抗局部腐蚀的能力,而且力学性能 (强度与韧性)也远比多晶镁合金要高。因此,非晶镁合金,尤其是大块的非晶镁合金的研制受到了极大的重视。
目前,有可能形成非晶的镁合金主要限制于以下几个体系:Mg-Zn, Mg-Cu, Mg-Ni, Mg-Ca, Mg-TM-Ln, Mg-Y-Ln, Mg-Ca-Al, Mg-Zn-Al, Mg-Al-Ca等,其中最有前途的非晶镁合金体系当数Mg-TM-Ln。TM是过渡金属,如锌、铜或镍等;Ln是斓系元素,也包括Y。Y是很关键的元素,因为Mg-Y的混合焓具有很高的负值。另外,镧系元素的原子体积比镁大得多,而铜、镍则比镁小。故三者混合有可能会有很高的局部应变能,这样从熔融态固化时,原子的扩散率应较低而难以形核生成晶相。所以,Mg-TM-Ln系有极好的非晶形成能力。此外,该系列合金还有极高的强度。在该系列合金中,Mg65Cu25Y10三元合金具有最好的非晶形成能力,冷却速度只需约50K/s就可使其非晶化。
Mg-TM-Ln(TM=Ni, Cu, Zn),Mg-Ca-Al, Mg-Al-Y与Mg-Y-Ln等非晶合金都有很好的耐腐蚀性,它们的抗腐蚀能力都超过了普通的晶态镁合金。Mg-TM-Ln系中的Ln一般对非晶的耐蚀性是有益的,但TM则对非晶的腐蚀性能不利。此外,其他一些合金元素对非晶镁合金的腐蚀性的影响也不尽一样。Al的加入能使非晶镁的腐蚀速度降低,而添加Si, Ca, Li, Zn等都使非晶镁的腐蚀速度升高。
实验室的研究表明,非晶镁合金Mg65Cu25Y10在0.1mol/L的NaOH(pH=13)溶液中的钝化电流以及用极化曲线方法测出的自腐蚀电流都比纯镁或晶态的Mg65Cu25Y10要低。腐蚀后的非晶表面膜主要是镁的氧化物或氢氧化物。同样,该非晶镁合金在缓冲溶液H3BO3/Na3BO4(pH=5~8.4)与0.lmol/L NaOH溶液中时,也显示出比纯镁或其晶态时更低的钝化电流和自腐蚀电流。若在非晶体系中加入Ag或Mg65Cu25Y10,则腐蚀后的非晶表面膜主要是Mg与Y的氧化物或氢氧化物。Ag的加入并不能提高非晶镁合金的耐蚀性能。
以上这些都说明通过非晶化来提高镁合金的耐腐蚀性有一定的潜力。但是,大部分非晶镁合金耐蚀性的研究都主要集中于钝化区内。应该注意到,非晶化似乎只是加宽了镁合金的钝化区,而对活性区并没有好的影响。若与纯镁相比,即使是非晶的Mg-Ni合金,其活性溶解速度仍较高。与镍相似,铜的加入也不能使非晶Mg-Cu的活性溶解速度低于纯镁。
此外,非晶镁合金的制备受到了目前快速凝固技术的很大限制。并非什么合金体系的镁合金都能通过快速凝固而得到非晶态镁合金。如铬也许对镁合金的耐蚀性有利,但它很难溶在熔融态的镁中,如要得到非晶的Mg-Cr合金就更是困难。
2
微晶化和纳米化
快速凝固也能产生纳米结构的镁合金。将熔融的Mg-12%(摩尔分数,下同)Zn-Ce(3%)与Mg-Zn(10%~20%)-La(0~10%)镁合金喷到低温金属轮上,得到20μm厚的金属带,该金属带以非晶为主,其中弥散地分布着3~20nm大小的α-Mg颗粒,颗粒间相距约3~10nm。
通过快速凝固粉末冶金的方法,也能得到高强的纳米结构镁合金。在高压的氩气喷射下将熔融的镁合金雾化快速凝固,形成25μm的微粒粉末。这些粉末先冷压,而后再在高于非晶的晶化温度下进行挤压成形。
具有纳米结构的镁合金的耐腐蚀性较好。如用上述的快速凝固粉末冶金方法制备的具有上述纳米结构的Mg70Ca10Al20,其耐腐蚀性比经T6热处理后的AZ91D还要好(见图7)。
图7 Mg70Ca10Al20与普通AZ91-T6在3% NaCl溶液中300K时的腐蚀速度
因此,微晶化与纳米化也可能成为提高镁合金耐蚀性的方法。
3
气相沉积
用常规的冶金与热处理方法来发展新的耐蚀镁合金,常常受到合金元素在凝固前后溶解度及冷却速度的限制。物理气相沉积的方法可以得到成分范围很广的合金。它可以生成50mm厚的合金,比决速冷却方法适用于更多的镁合金体系。但这样的合金常为多孔的微观结构。
气相沉积制备耐蚀镁合金的原理十分简单。图8所示为该方法的原理图。镁与合金元素经加热蒸发并混合,在低温下被合金收集器凝聚成合金。
用此方法制备的Mg-Mn与Mg-Cr合金,Mn与Cr的含量分别可高达3%与39%。它们的微观结构为柱状结构,并有些孔隙。
用这种气相沉积的方法制备的镁合金的腐蚀性能见表2。气相沉积的纯镁,镁锰与镁铬合金比铸态的纯镁的腐蚀速度要低很多。锰的加入量低于13%时对耐蚀性的影响十分有限;当超过13%后,腐蚀速度比气相沉积的纯镁略大。
图8 气相沉积镁合金的原理
表2 用气相沉积的方法制备的镁合金材料的腐蚀性能
注:MSP为许多小孔;FSP为少许小孔;MLP为许多大孔;FLP为少许大孔;EP为大范围的孔坑;C为开裂;T为失去光泽;BF为黑色表面膜。
利用气相沉积的方法,目前已经成功制得了一些二元镁合金:Mg-Zr、Mg-Ti、Mg-V、Mg-Mn和Mg-Cr。其中Mg-Zr、Mg-Ti、Mg-Mn的耐蚀性能较纯镁好;Mg-V和Mg-Cr则较差。
4
溅射
在真空管中,氩气分子被离子化后在电场的作用下轰击含镁耙材,由耙材轰击出来的原子就在一样品支持面上沉积得到溅射镁合金,用这种方法曾得到了MgAlZnSn,、MgZr、MgTa、MgY等镁合金,其中MgAlZnSn在ASTMD1384腐蚀水中呈现出较宽的钝化区。这说明,可用此法获得耐蚀性较高的镁合金。
免责声明:本网站所转载的文字、图片与视频资料版权归原创作者所有,如果涉及侵权,请第一时间联系本网删除。
相关文章
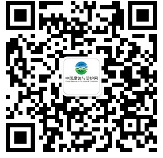
官方微信
《中国腐蚀与防护网电子期刊》征订启事
- 投稿联系:编辑部
- 电话:010-62316606-806
- 邮箱:fsfhzy666@163.com
- 中国腐蚀与防护网官方QQ群:140808414
点击排行
PPT新闻
“海洋金属”——钛合金在舰船的
点击数:7269
腐蚀与“海上丝绸之路”
点击数:5846