导读:梯度纳米结构最近引入了大多数金属材料通过几何必要位错适应的变形不相容性来提高强度和延展性。然而,很少深入地研究梯度结构对变形孪晶演化的影响以及由此产生的性能改进。在本文中,我们生产了梯度结构的 AZ31 镁合金,具有细晶粒层、平行孪晶层和从两个最上表面到板中心的粗晶粒核。令人惊讶的是,这种结构化的镁合金同时表现出强度和延展性的增强。随后的显微组织观察表明,由于较高的强度和多轴应力状态产生的丰富的孪晶相互作用可以对加工硬化能力的提高做出巨大贡献。通过测量整场演变过程进一步证明了这一点——塑性变形。这种设计策略可以为生产先进结构材料提供一条新途径,其中变形孪生作为主要的塑性机制之一。
镁合金是一种很有前途的结构材料,由于质量密度低,因此比强度高,可广泛应用于现代工业。然而,镁合金(六方密堆积(HCP)晶格结构)相对较低的屈服强度和较差的延展性成为其在实际工程中广泛应用的限制因素。从文献中可以看出,对于多晶材料,经典的Von Mises判据指出,对于均匀塑性变形,至少需要五个独立的滑移系统,而大多数HCP金属材料无法满足此标准。由于各种滑动系统的临界解析剪切应力 (CRSS) 存在巨大差异,因此无法同时操作足够的滑动系统以保持良好的塑性行为。同时,主要滑移系统和孪生系统之间CRSS值的严重区别也可能使此类合金的变形机制复杂化。先前的研究一致表明,对于Mg及其合金,HCP晶格a轴方向的基底滑移最容易被激活,因为它们的CRSS值较低,而当施加应力沿c轴方向时,非基底滑移和金字塔孪晶也发生以适应塑性变形。特别是,虽然这些孪晶有利于延展性,但相对较低的孪晶应力只会导致非常低的屈服强度。为了满足工业对材料性能的要求,进一步拓宽镁合金的工程应用,强度和延展性成为必须妥善解决的两个关键问题。因此,提高镁合金的力学性能一直是一个持续的焦点话题。
近年来,基于对镁合金变形行为和微观机制研究的努力,已经提出了许多强化和增韧策略以追求更好的机械性能。例如,晶粒细化已被认为是提高镁合金机械强度的有效途径,其中最常用的是严重塑性变形(SPD)方法来实现微观结构的细化。然而,如果仅在室温或较低温度下进行SPD,通常会导致显着的延性损失。因此,在SPD过程中,设置适当的环境温度以通过动态再结晶 (DRX) 过程。据报道,通过这种方式,可以通过减小晶粒尺寸尺度以增加晶界分数并同时提高强度和延展性。需要强调的是,特别是对于一些超细晶(UFG)纯镁,主要变形模式向晶界滑动的转变对塑性起到了关键作用。同时,当平均晶粒尺寸下降到亚微米时,强度开始下降。此外,UFG Mg几乎没有表现出加工硬化能力。相反,能够观察到明显的应变软化行为。对于一些具有再结晶超细晶粒(小于1 μm)的镁合金,由于在高流动应力下激活了非基底滑移,它仍然具有优良的加工硬化行为。但当平均晶粒尺寸接近0.1 μm时,UFG Mg合金甚至会出现脆性断裂弹性变形阶段的行为。还应该指出的是,随着晶粒尺寸的减小,形变孪生受到强烈抑制,这可能不利于此类HCP材料机械性能的进一步提高。
除了上述事实之外,由于在高温塑性加工过程中显着的再结晶和晶粒生长,将再结晶晶粒超细化为亚微米级实际上仍然是镁及其合金最具挑战性的任务。 出于这个原因,提出了一些其他策略来制造具有先进性能的块状镁合金。如前所述,对于HCP金属或合金,在某些情况下变形孪晶作为主要的塑性机制,同时在一定温度下通过预变形或热处理引入的预先存在的孪晶也可以产生出色的性能改进,很好地验证了孪晶界不仅可以降低可活化位错的平均自由程以有效提高金属材料的强度,而且还可以阻碍位错运动以提高加工硬化率或为位错运动提供滑移通道。因此,在晶粒内部引入孪晶被认为是另一种有效的强化和韧化机制。通过预冲击工艺,然后在中温下退火,在FG AZ31镁合金中产生了高密度的孪晶。实验结果表明,预孪晶FG AZ31镁合金表现出非凡的强度和延展性组合。在微观尺度上更精细的观察表明,位错和孪晶界之间的相互作用在强度增强和提高应变硬化能力方面起着主导作用。然而,在孪生工程中,加工温度仍然是控制微观结构特性和获得先进的块状结构材料的关键因素。这就提出了一个问题:轻质镁合金能否在常温下仅通过简单的塑性变形就可以具有优异的机械性能,从而避免在生产大块金属材料时考虑镁合金的热稳定性。
如今,受自然界材料的启发,研究人员提出了各种表面机械处理技术,以在室温甚至液氮温度下在金属板或圆柱体表面产生连续的梯度结构。大量研究成果表明,具有晶粒尺寸或孪晶厚度的梯度纳米结构可以诱导强度和延展性的良好结合。在梯度纳米结构材料中,具有增加深度的微结构的连续变化的尺寸可引起强烈的应变梯度,产生了许多相应的几何必要的位错(GND)随后的塑性[期间容纳变形19,20,25 ]。位错密度的增加会导致额外的强化和硬化,这也归因于GND的长程应力或背应力。应该指出的是,延展性的损失通常归因于纳米晶体在最上表面没有位错存储能力。中心区域的粗晶 (CG) 核心可以通过延迟局部塑性来有效推迟梯度纳米结构层的过早失效。但现在大多数梯度结构的(GS)的材料,通过用立方晶体结构,而不是由金属HCP /具有不对称晶格结构[合金的金属材料产生的。Wang等人所做的最新工作揭示了纯镁中的梯度孪晶网格可以在拉伸变形过程中实现两倍的延展性和更高的极限强度。人们认为,由位错-孪晶相互作用、位错壁的发展和多重交叉孪晶引起的微观结构演变是性能提高的主要原因。
最重要的是,可以得出结论:孪晶梯度结构处理是提高镁合金力学性能的合适设计策略,已经系统地研究了梯度结构区域内或界面附近的微观结构演变,以了解强化和硬化机制。然而,以前的研究主要集中在位错的演变及其与双胞胎的相互作用上。对于HCP合金,孪晶也应该是塑性变形过程中的主要机制。还需要考虑结构梯度对孪晶形成和相互作用的影响。在这项工作中,西北工业大学科研人员通过高速喷丸处理制造了GS镁合金板在金属板的两面形成对称几何的板材。下面给出处理和实验细节。在以下部分中,清晰地描绘了GS镁合金板不同深度的变形前和变形后的显微组织特征,以进一步探索该GS AZ31镁合金的强化和硬化机制。
图1a显示了不同深度的GS镁合金样品的SEM图像。整个样本可以分为三个逐渐增加的区域。在深度约50 μm的最外表面,FG区域由亚微米级的动态再结晶晶粒组成。在变形最严重的FG层旁边,孪晶区域包含高密度的变形孪晶,它们是为了适应表面机械处理过程中的塑性而产生的。随着深度的逐渐增加,孪晶率逐渐下降到几乎没有,直到GS镁合金板的中心。这种应变相对较小的中心区域被称为CG核心。实际上,这些相邻区域之间没有尖锐的界面。它是微观结构的不断转变由于变形程度随着深度的增加而变化。以下图1b和c的TEM图像清楚地显示了每个区域内的更多微观结构细节。在FG层中,基于足够数量的晶粒,统计测量的平均晶粒尺寸约为0.5 μm。这里需要指出的是,细化晶粒的大小差异很大。这归因于在30 m/s的高速喷丸处理下由DRX机制引起的晶粒细化。表层发生严重塑性变形并且在 RASP处理过程中显着升温。正如以前的出版物所报道的,对于镁及其合金,DRX晶粒通常经历了晶粒成核和生长的过程。因此,在这个FG区域,可以很好地理解这种具有很大差异的晶粒尺寸分布。然后在孪晶区域捕获的高倍TEM图像清楚地表明具有直线边界线的致密孪晶。在100 μm深度处,孪晶界之间的间距宽度可以达到3 μm。此外,图 1 中的高分辨率TEM图像d说明了由孪晶界位错的发射引起的许多堆垛层错。为了进一步展示不同深度晶粒中孪晶比例的演变,我们进行了大面积的EBSD映射,深度从150μm增加到400μm。如显示在图1个中E,多个沿不同孪晶的取向平行孪晶的表面处理后出现并双胞胎的数目逐渐减少,以在一些晶粒勉强一个或没有。由于每个区域的微观结构特征如此不同,图1f显示随着晶粒尺寸或孪晶间距的增加,硬度值从FG区域的70 HV到CG核心的约50 HV持续下降。这种梯度结构必须在随后的塑性变形过程中产生显着的应变梯度,从而在提高镁合金的机械性能方面发挥关键作用。
图1。通过表面机械处理制造的GS AZ31镁合金的显微结构特征。(a)从最顶层的 FG 到中央核心内部的CG的梯度微结构;(b)距最上表面约10 μm深度处的典型TEM图像,显示平均尺寸约为0.5 μm的超细晶粒;(c) 100 μm深度处的典型TEM图像显示许多孪晶;(d)显示基体和孪晶原子结构的高分辨率TEM图像。在孪晶间距内也发现了一些堆垛层错;(e) EBSDGS Mg合金深度从150μm增加到400 μm的映射图像显示孪晶和更大的晶粒;(f) GS 样品中晶粒尺寸/孪晶间距和维氏硬度随深度变化的统计结果。
图2a展示了GS镁合金在298 K单轴拉伸下的典型真实应力-应变曲线。为了比较,原样的均质CG镁合金和厚度为400 μm的自支撑梯度层从GS 镁合金样品的表面部分也在相同的加载条件下进行了测试。可以看出,均质CG样品显示出低于150 MPa的最低屈服强度和13%的破坏应变。对于RASP后塑性变形最严重的独立梯度层,其屈服强度增加了两倍以上。虽然梯度层样品失去了大部分的塑性能力,但与其他一些均质UFG镁合金相比,它仍然保持更好的延展性,这可能归因于梯度结构和预先存在的双胞胎。更令人惊讶的是,具有对称分布的梯度层的完整GS样品表现出强度和延展性的出色组合。极限强度是均质CG样品的1.7倍,甚至显示出更高的伸长率。晶粒细化和预先存在的孪晶有利于强度的提高。当然,上述应变梯度也有助于额外的强化。根据之前的出版物,这些强化机制很容易被认可。此外,当前工作的另一个关键任务是明确识别导致额外硬化的微观机制。塑性变形过程中硬化速率的演变也显示在图2a的插图中。当然,GS样品的硬化率甚至高于CG样品直至失效。不难理解,对于 GS 镁合金样品,更高的硬化速率可以保持更稳定的塑性,从而延迟拉伸过程中局部变形的发生。这种额外的硬化能力可能归因于晶粒内部GND的产生,类似于之前的研究,但对于HCP合金,收缩/延伸孪晶也是变形过程中的主要塑性机制。因此,需要更多的努力来将宏观力学行为与微观结构演化联系起来。也就是说,除了之前深入研究的位错活动之外,我们还必须解释梯度结构对这种GS Mg合金变形孪晶演化的影响。在本节关于机械性能的最后,为了比较我们工作的GS镁合金与其他具有细晶粒尺寸或梯度结构的AZ31镁合金的性能,我们在图2b中收集了大量数据。很明显,UFG镁合金在接近400 MPa时表现出最高强度,但伸长率非常低,低于5%。大多数不同平均晶粒尺寸的镁合金的强度集中在225-300 MPa的大范围内,而且,这些具有相似晶粒尺寸的合金的伸长率分布分散在5-35%的大范围内。相比较而言,目前的GS镁合金与现有的AZ31镁合金相比具有突出的优势,呈现出更好的强度和延展性平衡。这种高性能轻质合金在先进结构应用方面具有巨大潜力。
图2。GS AZ31镁合金样品在298 K准静态单轴拉伸试验下的机械性能。(a) GS镁合金样品、原样均质CG镁合金样品和独立梯度层以及随着拉应变的增加,应变硬化率的演变;(b)不同平均晶粒尺寸或梯度结构的AZ31镁合金力学性能的统计集合。
从力学曲线可以看出梯度结构设计对于提高镁合金综合性能的优势。更重要的是,必须深入揭示结构化 GS 镁合金中相应的微观结构特征,以探索设计先进结构材料的新机制。为此,我们表征了单轴准静态拉伸后每层 GS Mg 合金的微观结构演变。在图 3a 中,TEM图像显示了单轴拉伸后FG区域中超细晶粒的显微组织形态。与拉伸前的小尺寸DRX晶粒类似,变形晶粒内部几乎没有微观结构缺陷,但晶界变得相对不清楚。这应该与用于适应UFG Mg或其合金的塑性的晶界滑动。此外,高倍TEM图像插图显示稀疏晶粒内部存在一些平面缺陷。图3b是在孪晶区域内通过FIB技术切割的TEM样品上捕获的。引起的喷丸硬化一些预先存在双胞胎(参见图1 c)中消失,而产生大量的超细晶粒。这些晶粒可能是由孪晶界之间的位错分裂产生的。在图3的TEM图像中可以找到一些条状晶粒(用红色箭头标记)湾,并且在一些较小尺寸的细分晶粒中存在更高密度的缺陷。如图3上方插图所示b、存在许多相交的堆垛层错和位错相互作用。这有助于理解镁合金自支撑梯度层在高应力水平下具有相对较高的硬化能力。即使在通过喷丸硬化产生严重的塑性后,独立的薄梯度层在单轴张力下仍然可以在一定程度上塑性延伸。对于完整的GS Mg合金样品,虽然强度下降到中等水平,但可以获得更好的强度和延展性组合,特别是其延伸率甚至大于均质CG Mg 合金的延伸率。当然,孪晶区这些高密度的孪晶边界也为GS Mg合金试样的强硬化能力做出了重要贡献。在目前的工作中,除了这些一般的塑性和硬化机制外,我们更加关注引入的梯度结构对塑性和硬化行为演变的影响。下面对微观特征的比较分析可以充分证明梯度结构引起的附加硬化效应。
图3。拉伸试验后的显微组织观察显示了GS镁合金每个区域的主要变形和硬化机制。(a) TEM图像显示干净的超细晶粒,几乎没有变形缺陷;(b) TEM图像显示在变形孪晶区形成具有高密度位错的超细晶粒,孪晶界以绿色虚线勾勒;(c)和 (d) EBSDGS和均质CG Mg合金样品在拉伸失效后获得的图像,表明GS样品中具有更高密度的多取向孪晶,但在均质CG样品中,CG内部仅存在平行孪晶;(e)和(f) 为了排除更大的失效应变对交叉双胞胎发生的影响,在10%应变下为GS和CG样品捕获了EBSD图像。GS样本中已经出现了多向双胞胎。在CG样本中,平行双胞胎仍然更薄一些。在这些图像中,各种类型的双胞胎用不同颜色的双胞胎边界表示,包括{101?2}红色的扩展双胞胎,{101?1}黄色收缩孪晶和{101?1}-{101?2}蓝色双胞胎(关于图例中对颜色的解释,读者可以参考本文的网络版)。
在图3c和d中,GS镁合金的CG核和均质CG镁合金在拉伸试验后通过EBSD映射的衍射带对比图适应于区分梯度结构对可塑性过程中孪晶演化的影响。显然,在GS镁合金样品的CG核心区域中,不同取向的相交孪晶密度要高得多。相比之下,在拉伸至破坏后的均质CG Mg合金样品中仅观察到相对较少的平行孪晶。通过孪晶界取向错误分析,我们可以进一步确定GS镁合金和CG镁合金样品的CG核中的孪晶类型。在CHANNEL 5软件中,错误定向角的最大偏差设置为10°。如图中不同颜色所示,在单轴拉伸过程中形成了三种变形孪晶,包括{101?2} 红色的扩展双胞胎,{101?1}黄色的收缩双胞胎和{101?1}-{101?2}蓝色双胞胎。可以肯定的是,更高的孪晶密度和多取向孪晶之间更多的相互作用有利于提高GS镁合金的塑性和硬化能力。然而,应该注意的是,图3c和d都是在破坏后的拉伸样品上获得的,GS Mg合金样品的破坏应变远大于CG Mg合金样品的破坏应变。必须仔细分析较大应变对双胞胎形成的影响,尤其是具有多个取向的双胞胎。因此,我们只是在失效前将GS和CG镁合金样品扩展到指定的10%应变,然后再次进行EBSD映射。在图3e和f类似地,GS样品的CG核心出现了更多具有多个取向的孪晶,但孪晶的宽度稍细一些。这意味着多向双胞胎应该发生在可塑性的早期阶段。这与GS样品的应变硬化率趋势一致,在塑性变形开始时高于均质CG合金。此外,由于GS镁合金样品经历了严重的塑性表面处理,因此该CG核心区域中晶粒的结晶织构也应被视为影响孪晶类型的另一个不可忽略的因素。为此,我们在单轴拉伸试验之前绘制了均质CG镁合金的极图和 GS 镁合金的CG磁芯。1?0}<0001>存在,但在进一步的RASP处理后,由于核心区域的塑性变形非常有限,因此在GS镁合金的 CG核心中没有出现织构成分或强度的差异。因此,它应该有一些其他原因激活更多的双胞胎,特别是引起多方位双胞胎之间的相互作用。综上所述,对于GS镁合金样品的三个区域,我们在本节中系统地分析了各自的机制。最有趣的发现是由于引入了建筑梯度结构而导致的相交变形双胞胎的出现。因此,需要更多的努力来发现多向双胞胎激活和相互作用的驱动力。
在GS镁合金中激活更多具有多个取向的孪晶的第一个原因应该是其增强的强度。较高的外加应力可以促进变形孪晶沿各种孪晶系统的形核。通常在具有各种取向的晶粒中进行施密特因子 (SF) 分析以了解孪晶动力学。例如,变形孪晶更容易在具有特定取向的晶粒中沿具有最高SF值的孪晶系统成核和生长。根据施密德定律,CRSS=SF*σ app,这里对于每个孪生系统,CRSS应该是一个恒定值,只有当达到这个临界值时,对应的孪生系统才能运行。相比之下,外加应力σ应用程序GS镁合金的单轴拉力远高于均质CG镁合金。这意味着当施加的应力足够高时,沿着一些不合适的方向或具有较小SF值的晶粒中的孪生系统也可能被激活。因此,我们在GS 镁合金核心区域的几乎每个粗晶粒中都看到了更高密度的孪晶,甚至在同一晶粒中沿着不同的孪晶系统显示出相互作用的孪晶。显然,GS镁合金强度的提高对在塑性过程中激发更多的变形孪晶起到了至关重要的作用。另一个促进GS镁合金双变体的主要因素可能与单轴拉伸过程中梯度结构的应变不相容性引起的多轴应力状态有关。为了直观地显示应变协调过程并反映GS镁合金样品中每个区域的应力状态,我们通过DIC成像和计算测量了全场应变的演变。在图4f 中,图示图描绘了GS镁合金样品的几何形状、拉伸方向和典型的斑点图案。相机沿X轴布置,以区分拉伸过程中GS样品在横向表面(X 平面)上每个区域的应变变化。图4a和 b显示了典型的ε y沿拉伸方向的应变分布和对应的ε z在不同拉伸应变下的横向应变低于 8%。为了进行定量分析,我们计算了不同深度的ε y和ε z的统计平均值,这意味着沿拉伸方向捕获相同深度的许多数据点以求平均值。图4c和d以曲线的形式清楚地显示了应变变量的平均结果。可以看出,由于拉伸试样两端的边界约束,拉伸方向上的轴向应变ε y在整个试样上几乎保持一致。然而,横向应变 ε z显示梯度层(包括FG和孪晶区域)和CG核心之间的巨大差异。塑性变形首先在CG核心中开始。明显的剪切带似乎适应了可塑性。随着应变的增加,ε z的变化在图4?d中变得更大。根据获得的不同深度的平均应变曲线,我们计算了GS镁合金样品每个区域的塑性泊松比? p。通常,给定材料的弹性泊松比是一个弹性常数。弹塑性变形后材料的总应变包括弹性应变ε e和塑性应变ε p。ε e对应于弹性泊松比 ? e,ε p对应于塑性泊
图4。通过 DIC技术测量的GS镁合金样品侧面全场应变的演变。(a)轴向应变 ε y随外加拉伸应变的分布;(b)随着外加拉伸应变的增加,相应的横向应变 ε z的分布;(c)作为 GS Mg合金样品厚度函数的统计平均轴向应变ε y的演变;(d)作为GS Mg合金样品厚度函数的统计平均横向应变ε z的演变;(e) 塑性泊松比? p计算GS 镁合金样品中每个区域的 (f)说明图显示了GS样品的几何形状、拉伸方向和典型的散斑图案。
图5。单轴拉伸破坏后的变形孪晶比例和单轴拉伸前收缩孪晶对应的Schmid因子。(a) GS镁合金CG核内单轴拉伸破坏后的取向和形貌,根据显微组织观察结果提取的变形孪晶比例;(b)在原样的均质CG样品中,根据单轴拉伸破坏后的取向和形貌,在显微组织观察结果中提取的变形孪晶比例;(c) GS Mg合金CG核心的Schmid因子的等高线图;(d) 均质CG样本的 Schmid因子的等高线图;(e) GS镁合金CG核心的Schmid因子统计数据;(f) 均质CG样本的Schmid因子的统计数据。
最后,通过对GS镁合金试样各区域变形应变分布的分析,还需要强调梯度层可以有效抑制局部剪切带的传播。在图4b中,我们可以看到在CG核心区域形成了许多交叉剪切带以适应可塑性,但很少有它们穿过梯度层到达样品表面。为了比较,我们还记录了均质CG Mg合金的应变演变。在图6中,ε y的应变等值线中存在明显的剪切局部化。对ε z的应变分布进行更仔细的观察。 表明平行剪切局部化已经贯穿整个样品,其中任何一个都可能导致最终的剪切破坏。同时,在图7中,我们还显示了拉伸试验后GS镁合金样品和均质CG镁合金样品的断口形貌。所有均质CG 镁合金均因剪切而失效,但对于GS 镁合金,由于对局部剪切的抵抗力,与表面相邻的梯度层断裂并形成平坦的断裂面。事实上,GS样品CG核内局部剪切带的交叉点也削弱了塑性变形的集中度。总之,梯度结构设计的离域效应也应该是促进延展性增强的重要因素。
图6。通过DIC技术测量的均质CG样品侧面全场应变的演变。(a)轴向应变 ε y随外加拉伸应变的分布;(b)相应的横向应变 ε z的分布随施加的拉伸应变增加。
图7。(a) 和 (b) GS Mg合金样品在拉伸试验后从侧面和正面获得的断口形貌;(c) 和 (d) 均质CG Mg合金样品。
总之,我们通过传统的表面机械处理成功地生产了具有强度和延展性协同作用的GS AZ31镁合金。事实证明,建筑梯度结构有利于额外的强化和硬化,同时提高强度和延展性。显微组织分析充分表明,除了晶界滑动和梯度层中的孪晶相互作用,CG核心区域的高密度多取向孪晶是主要的硬化机制之一,因为孪晶相互作用提供了很强的硬化效果。最后,根据变形过程的探索,我们认为高强度和多轴应力状态是多取向孪晶变体出现并相互作用的主要原因。此外,由于引入梯度结构而产生的离域效应也可以提高延展性。上述讨论的所有优点表明,梯度结构设计应该是创造具有HCP晶体结构的先进轻质结构材料的好策略,特别是考虑到孪晶对机械性能的影响。
免责声明:本网站所转载的文字、图片与视频资料版权归原创作者所有,如果涉及侵权,请第一时间联系本网删除。
相关文章
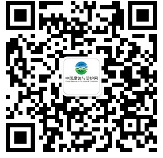
官方微信
《中国腐蚀与防护网电子期刊》征订启事
- 投稿联系:编辑部
- 电话:010-62316606-806
- 邮箱:fsfhzy666@163.com
- 中国腐蚀与防护网官方QQ群:140808414
点击排行
PPT新闻
“海洋金属”——钛合金在舰船的
点击数:7258
腐蚀与“海上丝绸之路”
点击数:5839