0 引言
随着我国经济的高速发展以及城市化脚步的加快,多个城市出现生活垃圾围城现象,农村农作物秸秆生物质垃圾的传统燃烧处理方法也对空气质量造成严重威胁,垃圾处理与民生息息相关。垃圾焚烧发电逐渐成为最主要的固废垃圾处理方式,截止2019 第1 季度,全国在运行的生活垃圾焚烧厂数量已突破400 座,预计2020 年底将共有约600 座处于运行状态[1]。与常规化石燃料相比,农作物秸秆等生物质垃圾成分复杂,其中的Cl、S、碱金属等成分在燃烧过程中以不同形态存在,一部分转化为烟气中的HCl和Cl2,一部分和碱金属元素结合形成腐蚀积灰黏附于过热器外管壁,气态氯腐蚀与烟气中的SO2 形成硫氯协同气体腐蚀,并与低熔点的碱金属积灰耦合腐蚀[2-3],导致垃圾焚烧电站受热平面的耐热钢寿命显著缩短,运行成本显著提高。根据调研,未防护的垃圾焚烧锅炉受热面管道服役不到20 个月就会发生严重腐蚀,甚至不得不换管,导致巨大的经济损失[1-3]。
研究表明[4],通过堆焊或者熔覆技术在锅炉受热面管道表面制备高耐腐蚀性能的镍基合金层可显著降低生物质垃圾焚烧锅炉受热面耐热钢部件的腐蚀速率,降低安全事故发生的概率。腐蚀机理分析结果表明[4-5],对于铁基合金管道, 高温条件下碱金属氯化物与铁反应时会产生低粘度的液态甚至是气态的氯化铁,腐蚀产物会迅速流失,导致新鲜金属表面再次暴露,腐蚀速率极快。而Ni和Cr等元素的氯化物熔点均高于1000℃,在服役条件下为固态,且氯化物进一步与氧气反应生成的Cr2O3 与镍铬尖晶石氧化物结构致密,因此表现出比铁基合金更好的耐高温氯化物腐蚀性能。堆焊与熔覆的镍基合金防腐层具有涂层与基材为冶金结合且耐腐蚀性能优异等优点,然而堆焊与熔覆技术多用于新品,具有不能在电厂进行现场施工、涂层制备效率较低、高的热输入导致耐热钢显微组织退化和管排整体发生变形等诸多问题,不能满足在役垃圾焚烧锅炉受热面耐热钢部件对耐腐蚀涂层的需求。热喷涂技术具有涂层制备效率高、可现场施工等优点,但是电弧喷涂、常规火焰喷涂等广泛用于煤电机组的热喷涂由于存在孔隙率高、内粒子层间结合较差等问题,被证实在生物质燃烧锅炉受热面腐蚀防护方面并不能起到长期有效的防护作用[6-9]。空气超音速火焰喷涂( High velocity air fuel, HVAF) 技术将常规超音速火焰喷涂(High velocity oxyger-fuel, HVOF) 用于助燃的氧气换为空气,进一步降低了火焰温度,并通过提高气体流量使得颗粒速度显著提高,使得HVAF制备的金属涂层比常规HVOF涂层氧化程度更低,涂层制备效率更高[10]。因此文中以在生物质燃烧发电锅炉受热面腐蚀防护得到验证的Inconel625 镍基合金为涂层材料, 采用HVAF在广泛应用于生物质焚烧发电受热面的TP347 耐热钢管材表面制备了Inconel625 合金涂层,重点研究了所制备的涂层在模拟生物质发电锅炉受热面服役环境下TP347H耐热钢的耐腐蚀性能,以期为在役生物质发电锅炉受热面的热腐蚀防护提供策略与方法。
1 试验
1.1 涂层制备
以气雾化球形Inconel粉末为喷涂粉末(AMPERIT380, HC Starck Gmbh, Germany),粒度15~45 mm,化学成分(质量分数)为:63.1%Ni、22.4%Cr、9.1%Mo、 3.8%Nb、 1.5%Fe。以外径为 Φ54 mm, 壁厚为10 mm的TP347H耐热钢(1Cr19Ni11Nb)管材作为基材,喷涂前以1.18 mm(16 目)的白刚玉砂在压缩空气压力为0.8 MPa的条件下进行喷砂表面粗化处理。采用M3 TM 型HVAF喷涂系统(UniqueCoat, Oilville, VA, USA) 在优化的参数下制备涂层,具体工艺参数如表1 所示。为防止基材过热,采用压缩空气对基材进行冷却,最终涂层厚度约为1 mm。
表1 Inconel625 涂层的喷涂参数
1.2 高温腐蚀及冲蚀试验
采用线切割将HVAF喷涂Inconel625 合金涂层后的TP347H耐热钢管材按照沿径向四等分、轴向长度为20 mm进行切割,切割后单个样品的涂层面积为8.5 cm 2 , 将未制备涂层的TP347H耐热钢管材切割成同样尺寸在相同条件下进行腐蚀试验作为对比。腐蚀试验前,在样品表面的涂层侧涂覆KCl、NaCl及K3Na( SO4)2 摩尔比为3 ∶4:1 的饱和溶液,放入刚玉坩埚中并在200℃ 烘箱内迅速烘干以模拟碱金属盐的腐蚀, 碱金属盐的化学成分根据分析电厂取样获得。在样品从烘箱内取出10 s内采用测量精度为0.1 mg的电子天平对坩埚及样品进行称重,以防止吸附空气中水分。
高温腐蚀装置如图1 所示。由于垃圾焚烧发电锅炉受热面的温度一般介于300~650℃ 之间,以再热管为例,将腐蚀温度定为550℃。将制备好的样品置入温度为550℃ 的管式炉中央, 通过将HCl与H2 SO3 溶液滴入140℃ 的油浴锅加热,蒸馏瓶内蒸发分解形成含HCl气体、SO2 气体与水蒸汽的混合气体,将气瓶中的空气通入蒸馏瓶中,使其携带HCl气体、SO2 气体与水蒸汽混合气体进入管式炉实现气体腐蚀模拟。通过分别调节空气气瓶流量和HCl与H2 SO3 溶液的浓度与流量使混合气体成分满足氧气5%(体积分数)、水蒸汽5%(体积分数)、HCl800 ppm、 SO2 100 ppm、氮气为余量的成分要求[10]。将多个样品分别在不同时间取出(最长为500 h),10 s内完成重量检测,并用于金相观察,每个时间条件下均为3 个相同样品以减小测量误差。对于所有样品,由于碱金属盐仅涂覆在管道外壁单面,其他5 个无涂层面同时受到气体介质的腐蚀,为了避免其造成试验误差,同时放入未涂覆碱金属盐样品,通过称重减去其他5 个面的气体腐蚀增重量。
图1 高温腐蚀性能测试装置及工作原理
采用显微维氏硬度测试对涂层的硬度进行了测试,测试载荷为300 g,保载时间为30 s。每个样品测量5 次,以平均值作为最终硬度评价标准。由于锅炉受热面同时受到灰分颗粒的冲蚀磨损,因此采用粒径为 Φ50~Φ100 mm的氧化硅颗粒在空气压力为0.2 MPa的条件下对带涂层样品和未带涂层样品进行了冲蚀测试。测试区域为样品的弧形表面,冲蚀颗粒束流与弧面中心垂直,测试区域的冲蚀角度介于75°~90°,为高角度冲蚀。每次测试量取重量为20 g的氧化硅颗粒作为磨料,测试前后采用精度0.1 mg的电子天平对样品进行称重。由于真实服役环境下的腐蚀颗粒在单位空间的浓度远远小于测试环境,因此不宜采用不同冲蚀时间后的失重评价耐冲蚀性能。由于涂层密度与基材相当,因此以冲蚀失重与冲蚀测试次数的关系评价耐冲蚀性能。
1.3 涂层组织及腐蚀产物分析
利用扫描电子显微镜( SEM, MIRA 3 LMH, TESCAN, Czech Republic) 对喷涂态和500 h腐蚀测试后的涂层断面组织进行了表征;通过图像法利用5 张500 倍涂层断面背散射电子SEM照片对喷涂态涂层的孔隙率进行了统计;采用能谱分析(EDS)对腐蚀产物的化学成分进行了分析。
2 试验结果与讨论
2.1 HVAF喷涂Inconel625 合金涂层的显微组织
优选参数下喷涂态Inconel625 合金涂层的断面组织如图2 所示。如图2(a)所示,涂层的厚度约为1.1 mm,涂层内部无明显的孔隙和裂纹等缺陷。涂层与基材结合良好,界面处无开裂, 夹砂等缺陷。涂层内无明显的氧化物夹杂形成。图像法孔隙率测试结果显示该涂层的孔隙率仅为0.72%。如图2( b) 中的箭头所示,在高放大倍数下依然可以观察到涂层中的颗粒界面,能谱分析结果表明界面处的深色物质为氧化铬。
图2 HVAF Inconel625 涂层的断面组织
硬度测试结果显示,HVAF喷涂制备的Inconel625 合金涂层的显微硬度为475±37 HV0.3, TP347H耐热钢的显微硬度为184 ± 8 HV0.3,Inconel625 涂层的硬度显著高于TP347 耐热钢基材,约为基材的2.6 倍。研究表明,常规Inconel625 管材的硬度约为210 HV0.3,远低于HVAF喷涂涂层的硬度。 HVAF制备的Inconel625 合金涂层高的硬度主要与热喷涂过程中熔滴高的冷却速度及高的颗粒撞击速度有关。高的冷却速度有利于Inconel625 合金颗粒获得细小的晶粒,强化细晶强化效果 [12-13]。高的颗粒撞击速度可引起已沉积颗粒的剧烈塑性变形,导致已沉积颗粒内部的位错密度显著提高、加工硬化效果显著增强 [12-13]。因此,与常规冶金块材相比,尽管高的冷却速度不利于形成弥散析出物, 但细晶强化和加工硬化的协同强化作用使得HVAF喷涂Inconel625 涂层的硬度显著高于同成分冶金块材。
2.2 HVAF喷涂Inconel625 涂层的高温腐蚀行为
无涂层TP347H耐热钢与HVAF Inconel625 合金涂层涂覆后的TP347H耐热钢在550℃的气体与碱金属盐耦合腐蚀环境下放置169 h后的表面宏观形貌如图3 所示。如图3(a)所示,无涂层TP347H耐热钢样品表面发生了大量的材料剥落,表明其发生了较为严重的腐蚀。如图3( b) 所示,制备HVAF Inconel625 涂层后,样品表面颜色发生了变化,表明其也发生了表面腐蚀,但涂层未出现明显的剥落现象,表明其腐蚀程度低于无涂层的TP347H耐热钢。
图3 169 h高温腐蚀后无涂层TP347H耐热钢与HVAF喷涂Inconel625 涂覆TP347H耐热钢的表面形貌
无涂层TP347H耐热钢与HVAF制备Inconel625 合金涂层后的TP347H耐热钢在550℃气体与碱金属盐耦合腐蚀环境下增重量随腐蚀时间变化关系如图4 所示,图中同时给出了无涂层TP347H耐热钢在单纯腐蚀气氛下的增重曲线。可以发现,所有样品的增重量均与腐蚀时间呈线性关系,且无涂层TP347H耐热钢的腐蚀速率远高于采用HVAF制备Inconel625 合金涂层后的TP347H耐热钢管材,通过HVAF制备Inconel625 涂层可使TP347H耐热钢的腐蚀速率降低7.6 倍,耐腐蚀性能显著提高。另一方面,对比单纯气氛腐蚀和气氛腐蚀与碱金属氯化物耦合腐蚀的TP347H耐热钢增重曲线可以发现,耦合腐蚀条件下TP347H耐热钢的增重约为单纯腐蚀气氛条件下增重的76 倍。这一结果表明,碱金属盐与腐蚀气氛的耦合可使TP347H耐热钢的腐蚀速率提高近两个数量级。通常条件下,以腐蚀介质扩散主导的腐蚀过程,由于扩散距离与扩散时间呈抛物线关系,因此腐蚀速率与时间通常也呈抛物线关系,主要表现为随腐蚀时间的延长腐蚀速率逐渐降低[14-15]。线性关系表明,已产生的腐蚀层不能对腐蚀介质起到良好的物理阻隔效果,导致后面的腐蚀进程不受前期腐蚀产物的影响。
550℃ 腐蚀500 h所有涂层样品的涂层完整,均未发生涂层的开裂及剥落现象。为了进一步揭示腐蚀过程及腐蚀机理,采用扫描电镜和能谱分析对腐蚀后涂层的表面形貌、断面组织以及腐蚀产物成分进行了系统分析。 500 h热腐蚀后无涂层TP347H耐热钢的断面组织如图5 所示。如图5(a)中的箭头所示,TP347H耐热钢表面产生了大量的材料剥落,这与样品的宏观形貌观察结果一致。由图5( b) 中的高倍组织可以发现, 腐蚀前沿的腐蚀机制主要为沿晶腐蚀,深色的腐蚀产物沿TP347 耐热钢的晶界呈网状分布,整个腐蚀前沿的深度约为150 μm。沿晶腐蚀现象主要与含Cr钢材中晶界的贫Cr有关。由于Cr的氯化物熔点较高,比较稳定,因此Cr含量越高、耐腐蚀性能越好[2,14]。晶界处较低的Cr含量使得碱金属氯化物中的Cl与Fe发生反应,腐蚀沿晶界优先发生,使得发生腐蚀的总界面增大,腐蚀速率加快,管道寿命降低。
图4 TP347H管材HVAF Inconel625 涂层前后腐蚀增重量
500 h腐蚀后,带Inconel625 涂层TP347H耐热管材的断面组织结果如图6 所示。如图6(a)中的箭头所示,腐蚀后的涂层可分为两层,即腐蚀影响区和腐蚀未影响区。腐蚀并不是发生在涂层的最表面, 腐蚀影响区的深度约为100 μm,即腐蚀发生在深度为100 μm的范围内。完整的腐蚀产物厚度仅约20~70 μm,远小于涂层的整体减薄量,说明腐蚀产物在长期腐蚀过程中发生了剥落。
图5 500 h热腐蚀后无涂层TP347H耐热钢管材的断面组织
图6 500 h腐蚀后HVAF Inconel625 涂层的断面组织
为了进一步对腐蚀过程进行深入理解,对腐蚀影响区内布局进行了放大,结果如图6( b) 所示。如黑色箭头所示,深色的腐蚀产物呈连续网状分布在原始Inconel625 合金颗粒的界面,这说明尽管HVAF喷涂制备的金属涂层表现出极低的孔隙率,颗粒界面依然难以达到完全的冶金结合,是腐蚀介质的快速通道,HVAF喷涂Inconel625 合金涂层内部颗粒弱结合界面的存在使腐蚀前沿的面积较冶金块材大幅度增加。
从图6( b) 中还可以发现,对于腐蚀影响区内的每一个颗粒,腐蚀由颗粒界面向颗粒内部逐渐发生。对于同一个颗粒,颗粒上部的腐蚀发生区深度比下部更大,这主要是由于上部距离腐蚀介质更近所致。同时可以发现,在每个颗粒中的暗色腐蚀产物呈连续的点状分布,每个点的尺度介于0.1~10.3 μm,这主要是因为碱金属氯化物和气体耦合腐蚀在Inconel625 合金中的腐蚀机制主要为沿晶腐蚀,即腐蚀优先沿着Inconel625 合金的晶界发生。由于HVAF喷涂Inconel625 合金涂层中的晶粒极小,通常为5 μm以下量级, 因此晶界密度较大,晶界处优先形成的腐蚀产物尺寸较小,且距离较近,因此整体呈现为点状分布。
为了进一步对腐蚀产物的化学成分进行深入理解,采用EDS面扫描方式对样品断面的腐蚀影响区局部进行了表征,S元素用于标定腐蚀介质和可能的腐蚀产物,Ni、Cr元素主要用于标定涂层的主要成分,O元素用于标定腐蚀产物,结果如图7 所示。可以发现,S元素仅在图7(a)中的表层,即腐蚀介质中的浓度相对较高,涂层内的Ni元素仅在如图7(a)箭头所示的涂层内腐蚀产物处少量出现,其他区域分布较为均匀,Cr和O元素的分布高度重合,均在图7(a)中箭头所示的箭头处出现了偏析的现象,进一步分析表明, 腐蚀产物内未出现Cl元素的富集,上述结果表明,腐蚀产物的主要成分为金属元素的氧化物, 这与其他人的研究结果一致[5, 17-18]。除Cr2O3 外,点扫描分析结果显示, 颗粒界面还存在NiCr2O4 尖晶石结构复合氧化物。 Cr2O3 与NiCr2O4 尖晶石均具有致密组织,可在一定程度上防止液态腐蚀介质的浸入,因此Inconel625 合金涂层的耐腐蚀性能较好。同时可以发现尽管腐蚀介质中存在大量Cl、S元素,但最终腐蚀产物中并未检测到这些元素,主要是由于Cl、S与Ni、Cr形成的化合物在腐蚀条件下为亚稳态,在有氧存在的条件下,这些亚稳态的中间产物将会进一步与氧气反应转变成更稳定的氧化物[5, 17-18]。
生物质发电服役环境下热腐蚀产物中不存在Cl元素主要与其热腐蚀机理有关[14-16]。在腐蚀最初阶段、碱金属氯化物沉积物较少,金属表面暴露在富氧腐蚀气氛中,可形成金属氧化物。随着腐蚀产物的增厚,腐蚀产物表面依然处于富氧环境,但腐蚀产物对外界气氛的物理隔离使腐蚀前沿处的金属表面处于贫氧环境。腐蚀前沿处的金属元素主要与碱金属氯化物中的Cl元素反应生成金属氯化物。金属氯化物的熔点和沸点远低于相应的金属氧化物。 Fe、Ni氯化物的沸点分别仅约为315 和987℃,Cr的氯化物熔点约为1150℃。金属氯化物与碱金属盐形成的共晶化合物熔点更低,氯化铁与氯化钠的共晶化合物熔点仅为156℃。
图7 500 h高温腐蚀后HVAF喷涂Inconel625 涂层横截面显微组织和浅表层的EDS面扫描结果
上述结果表明,腐蚀前沿处的金属与碱金属氯化物界面在腐蚀温度下存在液相,液相的存在使腐蚀介质的活性和与金属的接触面积显著增大,腐蚀速率加快。同时氯化物在服役温度下较高的蒸气压会使金属氯化物发生显著的蒸发或升华现象。气相的金属氯化物在到达腐蚀产物表面与富氧环境接触后,会与氧气发生反应形成更加稳定的氧化物,同时生成氯气,进一步参与腐蚀反应,因此最终的腐蚀产物均为金属的氧化物。尽管Cl、S元素不出现在最终产物中,但含Cl、S中间产物(金属氯化物、金属硫酸盐) 的存在会使金属元素的活性显著提高,进而使腐蚀速率大大加快。结合文献[4,17-18] 可以发现,TP347H耐热钢的腐蚀产物主要为Fe的氧化物,或者Fe、 Cr复合氧化物。另一方面,金属氯化物的在服役环境下的稳定性是决定金属耐碱金属氯化物腐蚀性能的关键因素。 Fe、Ni、Cr这3 种金属在550℃条件下形成氯化物的吉布斯自由能分别为-232.1、-274.2 与-286.0 kJ/mol [14],依次提高,同时熔点依次升高,导致其耐碱金属氯化物腐蚀性能依次升高,因此高Cr耐热不锈钢的耐腐蚀性能高于常规结构钢,高Cr镍基高温合金的耐腐蚀性能高于高Cr耐热不锈钢。同时Fe的氧化物具有结构疏松、体积膨胀量大的问题,疏松结构不能有效隔离后续液态的腐蚀介质的浸入, 大的体积膨胀趋向于使已形成的腐蚀产物层剥落和开裂,有利于液态腐蚀介质渗入。因此氧化物的本征属性差异,导致TP347H耐热钢的耐腐蚀性能远低于Inconel625。
2.3 HVAF喷涂Inconel625 涂层的耐冲蚀性能
生物质燃烧发电机组受热面中的再热管以腐蚀失效为主,同时还存在微量灰份的冲蚀磨损,因此在室温条件下对TP347H耐热钢在喷涂HVAF Inconel625 涂层前后的耐冲蚀性能进行了对比评价,结果如图8 所示。
可以发现TP347H的失重曲线与冲蚀颗粒质量呈单一的线性关系,而Inconel625 涂层的失重呈现为冲蚀速率截然不同的两个线性阶段,开始阶段冲蚀速率极高,约为TP347H耐热钢的5.5 倍,后一阶段的冲蚀速率与TP347H耐热钢相当,由于再热管主要以腐蚀失效为主,生物质燃烧后形成的轻质灰份微粒引起的冲蚀磨损较为微弱,与TP347H耐热钢相当的耐冲蚀性能不会导致HVAF Inconel625 涂层由于冲蚀磨损而发生快速减薄。
图8 TP347H耐热钢管材HVAF喷涂Inconel625 合金涂层冲蚀前后失重量对比
尽管HVAF Inconel625 合金涂层的硬度显著高于TP347H耐热钢基材,但涂层耐冲蚀性能较低,这主要与涂层内粒子界面的存在使涂层表现为脆性有关。粒子界面的存在使涂层在受到冲蚀颗粒垂直冲击时容易出现Inconel625 合金粒子的整体剥落,从而导致涂层材料去除较快, 表现为单次数冲蚀试验后涂层失重较多。 HVAF喷涂Inconel625 合金涂层不同冲蚀阶段的典型形貌如图9 所示。
涂层表面存在的凸起的Inconel625 合金颗粒粗糙结构容易被冲蚀颗粒冲击剥落是导致Inconel625 合金涂层开始阶段冲蚀速率极高的主要原因。随着冲蚀的进行,表面粗糙结构逐渐被去除,如图9(a)箭头所示的整个沉积颗粒被冲击剥离的几率降低,但依然存在,因此冲蚀速率降低,耐冲蚀性能提高,但依然低于同成分的冶金块材。由于表层颗粒仅占整体涂层厚度的5%左右,因此不显著影响涂层的平均耐冲蚀性,HVAF Inconel625 合金涂层的制备不降低TP347H耐热钢管材的耐冲蚀性能。另一方面,测试过程中冲蚀角度在高角度范围(75°~90°),这也会对涂层的耐冲蚀性能测试结果产生影响。对于类似HVAF Inconel625 合金涂层的脆性材料,冲蚀角度越大,越容易出现表面开裂剥落,冲蚀磨损率越高;对于塑性材料,冲蚀角度越小,越容易出现材料表面由于冲蚀颗粒剪切而出现的材料去除,冲蚀速率越高。同时,本文中所采用的SiO2 冲蚀颗粒密度及粒度均大于生物质灰分,更低的密度和粒度可能不会引起Inconel625 合金中整个颗粒的剥离,因此在真实服役条件下,HVAF Inconel625 合金涂层的耐冲蚀性能有望进一步提升,硬度优势有望得以体现。
图9 HVAF喷涂Inconel625 合金涂层冲蚀前期与稳定期表面形貌
3 结论
(1) 在优化的喷涂参数条件下,通过HVAF涂层获得组织致密,孔隙率低于1%的Inconel625 合金涂层,涂层内无明显成分偏析,涂层与基体结合良好。
(2) 在550℃ 的碱金属氯化物、硫酸盐与HCl、SO2、氧气与水蒸汽耦合腐蚀条件下, HVAF喷涂Inconel625 合金涂层的耐腐蚀性能约为TP347H耐热钢的7.6 倍。颗粒间弱结合界面与腐蚀产物层剥落的现象,导致腐蚀增重与腐蚀时间呈线性关系,腐蚀速率恒定。探索可提高颗粒间结合的方法可使HVAF喷涂Inconel625 涂层的腐蚀防护性能进一步提高。
(3) 以粒径为 Φ50~100 μm SiO2 颗粒作为冲蚀介质时,HVAF喷涂Inconel625 合金涂层的耐冲蚀性能表现为冲蚀速率显著不同的两个阶段,最初阶段冲蚀速率极高,稳定阶段的冲蚀速率降低,与TP347H耐热钢相当。
参考文献
[1] 曾升财.城市垃圾焚烧发电发展现状与展望[J].城镇建设,2019,(11):121-122.
ZENG S C.Review and expectation of WTE in China[J].Urban and Rural Studies,2019,(11):121-122(in Chi-nese).
[2] 温利民.垃圾焚烧循环流化床锅炉设备治理与运行优化研究[J].技术与市场,2019,26(12):121-122.
WEN L M.Investigation on optimization of the WTE fluid-bed boiler [J].Technology and Market,2019,26(12):121-122(in Chinese).
[3] 宋景慧,胡平.大型生物质直燃锅炉高温受热面腐蚀问题分析[J].锅炉技术,2013,44(2):56-60.
SONG J H,HU P.Analysis of high-temperature heating sur-face corrosion problems in large-scale biomass-fired boiler[J].Bioler Technology,2013,44(2):56-60(in Chinese).
[4] SCHMID A,MORI G,HONIG S,et al.Comparison of the high-temperature chloride-induced corrosion between duplex steel and Ni based alloy in presence of H2 S[J].Corrosion Science,2018,139:76-82.
[5] CHENG H F,HU Y N.Municipal solid waste(MSW)as a renewable source of energy:Current and future practices in China [J].Bioresource Technology,2010,101(11):3816-3824.
[6] WANG X,HE D Y,GUO X Y,et al.Hot corrosion behav-ior of wire-arc sprayed NiCrB coatings[J].Surface and Coat-ings Technology,2019,367:173-178.
[7] LUO X T,LI C J.Tailoring the composite interface at lower temperature by the nanoscale interfacial active layer formed in cold sprayed cBN/NiCrAl nanocomposite [J].Materials & Design,2018,140:387-399.
[8] FANTOZZI D,MATIKAINEN V,USITALO,et al.Chlorine induced high-temperature corrosion mechanisms in HVOF and HVAF sprayed Cr3C2-based hardmetal coatings [J].Corrosion Science,2019,160:108166.
[9] 雒晓涛,魏瑛康,张越,等.原位微锻造冷喷涂制备高致密铝基涂层及耐腐蚀性能[J].表面技术,2019,48(4):34-39.
LUO X T,WEI Y K,ZHANG Y,et al.Fully dense Al coat-ings sprayed by in-situ micro-forging assisted cold spray and corrosion protection[J].Surface Technology,2019,48(4):34-39(in Chinese).
[10] SILVERRA L L,PUKASIEWICZ A G M,ZARA A J.Study of the corrosion and cavitation resistance of HVOF and HVAF FeCrMnSiNi and FeCrMnSiB coatings[J].Surface and Coat-ings Technology,2019,374:910-922.
[11] 余春江,骆仲泱,张文楠,等.碱金属及相关无机元素在生物质热解中的转化析出[J].燃料化学学报,2000,(5):420-425.
YU C J,LUO Z Y,ZHANG W N,et al.Inorganic material emission during biomass pyrolysis[J].Journal of Fuel Chem-istry and Technology,2000,(5):420-425(in Chinese).
[12] LUO X T,SMITH G M,SAMPATH S.On the interplay be-tween adhesion strength and tensile properties of thermal spray coated laminates—Part I:High velocity thermal spray coatings[J].Journal of Thermal Spray Technology,2018,27:296-307.
[13] LUO X T,SMITH G M,WANG Y,et al.Cracking induced tribological behavior changes for the HVOF WC-12Co cermet coatings[J].Ceramic International,2019,45(4):4718-4728.
[14] SADEGHIMERESHTA E,REDDY L,HUSSAIN T,et al.Chlorine-induced high temperature corrosion of HVAF-sprayed Ni-based alumina and chromia forming coatings[J].Corrosion Science,2018,132:170-184.
[15] LIU S,LIU Z D,WANG Y T,et al.A comparative study on the high temperature corrosion of TP347H stainless steel,C22 alloy and laser-cladding C22 coating in molten chloride salts[J].Corrosion Science,2014,83:396-408.
[16] SADEGHIMERESHT E,MARKOCSAN N,NYLEN P.Mi-crostructural characteristics and corrosion behavior of HVAF-and HVOF-sprayed Fe-based coatings[J].Surface & Coat-ings Technology,2017,318:365-373.
[17] SADEGHIMERESHT E,REDDY L,HUSSAIN T,et al.Chlorine-induced high temperature corrosion of HVAF-sprayed Ni-based alumina and chromia forming coatings[J].Corrosion Science,2018,132:170-184.
[18] SADEGHIMERESHT E,REDDY L,HUSSAIN T,et al.In-fluence of KCl and HCl on high temperature corrosion of HVAF-sprayed NiCrAlY and NiCrMo coatings [J].Materials & Design,2018,148:17-29.
免责声明:本网站所转载的文字、图片与视频资料版权归原创作者所有,如果涉及侵权,请第一时间联系本网删除。
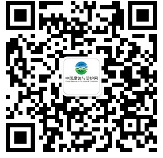
官方微信
《中国腐蚀与防护网电子期刊》征订启事
- 投稿联系:编辑部
- 电话:010-62316606-806
- 邮箱:fsfhzy666@163.com
- 中国腐蚀与防护网官方QQ群:140808414