摘要
采用动电位极化曲线、电化学阻抗谱以及U形弯试样浸泡实验研究了不同组织 (原始组织、固溶组织与敏化组织) 的316L不锈钢在NH4Cl环境下的应力腐蚀开裂 (SCC) 行为与机理,分析了NH4Cl浓度对不同热处理状态的316L不锈钢应力腐蚀行为和机理的影响。结果表明:不同组织的316L不锈钢在NH4Cl环境中均具有明显的SCC敏感性,原始组织、固溶组织、敏化组织的SCC敏感性依次升高;随着NH4Cl溶液浓度升高,316L不锈钢不同组织的钝化膜稳定性降低,原始组织、固溶组织及敏化组织在NH4Cl环境下,破钝电位依次降低,维钝电流密度依次升高,阻抗值依次减小,钝化膜更加活泼易破坏,饱和NH4Cl浓度下极易发生点蚀导致SCC的萌生。316L不锈钢在NH4Cl环境中的SCC裂纹扩展机制主要为穿晶型阳极溶解机制。
关键词: 316L不锈钢 ; NH4Cl环境 ; 热处理 ; 应力腐蚀开裂
随着石油的不断开采,低酸、低盐优质原油越来越少,埋藏较深的高氯、高氮原油的开采量和加工量越来越多,导致许多装置原料中含氯量超过原设计值,从而带来了一系列炼化设备管线的腐蚀问题[1,2]。近年来,为了提高原油采收率和管道运输效率,工业上普遍在原油开采和储运过程中添加含有有机氯的化学助剂,加之天然存在的有机氯,导致原料油中有机氯含量过高[3,4]。油厂通过改用不锈钢设备、采用“一脱三注”等防腐措施[5,6]。很好地控制了均匀腐蚀的发生。但在高有机氯、高氮原油炼制的装置中极易形成高浓度的NH4Cl环境,由于在工艺流程冷却过程中,气相NH3和HCl形成固体NH4Cl盐,当盐沉积在管道或设备的内表面时,极易在表面局部区域形成高浓度的NH4Cl溶液。同时,在某些高温设备表面,如换热器管等,由于水蒸汽的蒸发,NH4Cl结晶沉积情况时有发生,导致装置表面形成高浓度的NH4Cl结盐腐蚀环境[7-9]。同时,铵盐结垢会导致管线装置内部压力升高,停工现象出现剧增,炼化装置及管线的NH4Cl环境下应力腐蚀开裂和泄漏情况严重[10-13]。
国内外对于铵盐在加氢装置内部结晶沉积所引起的应力腐蚀失效的研究表明,这种环境中的应力腐蚀开裂机制主要为阳极溶解[14-17]。Cheng等[11]研究显示,敏化处理降低了304不锈钢的点蚀电位,同时降低了发生点蚀的临界Cl-浓度。马宏驰等[18]研究了不同热处理态的304和321不锈钢在NH4Cl环境中的应力腐蚀行为,两种不锈钢在NH4Cl环境中均具有应力腐蚀敏感性,敏化处理后显著增加了其沿晶应力腐蚀开裂的倾向。由于铵盐结晶沉积受成分含量、设备结构、温度、应力等众多因素影响,腐蚀机理也更为复杂。316L不锈钢因其具有更好的力学性能和耐均匀腐蚀能力,在石油炼化领域中被广泛应用替代传统使用的304不锈钢。然而,目前对于316L不锈钢在NH4Cl环境腐蚀机理尚不明确,不同热处理 (焊接) 状态的316L不锈钢能否适用于NH4Cl环境还有待进一步研究。
本文利用电化学测试技术、U形弯浸泡试验等方法,研究不同组织状态的316L不锈钢在不同浓度的NH4Cl环境下的应力腐蚀开裂行为与机理,从而通过组织、临界浓度角度进一步分析不锈钢在NH4Cl环境中的应力腐蚀机理,以期为炼油厂的现场防腐工作提供数据支撑。
1 实验方法
实验材料为316L不锈钢,主要化学成 (质量分数,%)分为:C 0.021,Si 0.49,Mn 1.14,P 0.036,S 0.002,Cr 16.64,Ni 10.02,Mo 2.03,Fe余量。316L不锈钢的敏化组织和固溶组织通过不同的热处理方法制备,其中,固溶态的热处理工艺是在1050 ℃的热处理炉中保温30 min后,水淬;而敏化态的热处理工艺是在600 ℃的热处理炉中保温2 h,空冷。
将不同组织试样切割成10 mm×10 mm×5 mm,后使用砂纸打磨至3000#,机械抛光至1 μm,然后,根据GB/T 4334-2008,在水浴40 ℃的10% (质量分数) 草酸电解液中,利用1 A/cm2直流电流电解侵蚀40 s,接着分别用去离子水和酒精冲洗吹干后,在VH-Z100R型体式显微镜下观察其组织成分及晶粒大小。切割材料成1 cm2正方形作为电化学试样,焊接导线后用环氧树脂密封,保留1 cm2工作面,将表面用砂纸逐级打磨至2000#,除油,清洗,脱水后备用。应力腐蚀U形弯试样按照GB/T 15970标准制作,其长度方向均平行于材料轧向,并用砂纸顺试样长度方向逐级打磨至1500#,除油,清洗,脱水后备用。电化学实验温度为近沸腾 (避免沸腾状态产生信号干扰),U形弯浸泡实验温度为沸腾。实验用NH4Cl溶液浓度分别为0.1%,1%,5%,10%及饱和浓度 (约为43%)(质量分数) 电化学实验在2273电化学工作站上进行,采用三电极体系,对电极为铂片,工作电极为316L不锈钢,其测试表面积为1 cm2,参比电极为饱和甘汞电极 (SCE)。电化学阻抗测试在开路电位下进行,交流扰动电压幅值为10 mV,测量频率范围为105~10-2 Hz。电化学阻抗测试完成后,以0.5 mV/s的扫描速率进行动电位极化曲线测试,扫描电位的范围相对开路电位-0.25~1.6 V。U形弯浸泡周期为30 d,浸泡后均采用去离子水、除锈液 (5 mL HNO3+1 mL HF+44 mL H2O) 超声波清洗、无水乙醇去除腐蚀产物。采用QUANTA250型扫描电子显微镜 (SEM) 及GENESIS能谱仪 (EDS) 对断口形貌和试样表面进行观察。将U形弯裂纹沿厚度方向切取试样、封样,将封装好的试样表面用砂纸逐级打磨到3000#,并抛光,除油、清洗、吹干后,用侵蚀剂 (5 g三氯化铁+50 mL盐酸+100 mL去离子水) 进行侵蚀后,清洗吹干,进行SEM观察。在VH-Z100R体式显微镜下观察不同热处理后的样品的组织形貌。
2 实验结果
2.1 显微组织
由图1可知,经过不同热处理后,3种材料均未发生相变,仍为奥氏体单相,固溶组织相比原始组织的晶粒大小变化不大,而敏化处理后晶粒相比原始组织晶粒尺寸较大,但晶界并没有明显的析出物,这是由于316L本身的含碳量较低,晶间析出物较少,表现出较高的抗敏化晶间析出物的能力。
图1 不同热处理组织316L不锈钢的微观形貌
2.2 不同组织在NH4Cl环境中的电化学行为
316L不锈钢不同组织在NH4Cl环境下的极化曲线结果如图2所示。可见,对于敏化组织、固溶组织与原始组织在不同浓度NH4Cl中的阳极区均表现出一定的钝化能力,阴极区均为活化控制。对316L不锈钢在不同浓度的NH4Cl溶液中点蚀电位和自腐蚀电流密度 (Icorr) 进行拟合,结果如图3所示,可以看出,3种组织的点蚀电位均随着NH4Cl浓度的增加而减小,Icorr随着NH4Cl浓度的增加而增加;当NH4Cl浓度在1%左右时,不锈钢各种组织腐蚀电位在-0.2~-0.3 V之间,且具有较大的钝化区间以及较高的点蚀电位,耐点蚀能力较好,钝化膜稳定;而当NH4Cl溶度达到5%以上时,不锈钢各种组织自腐蚀电位下降到-0.4~-0.5 V之间,且钝化区明显变小,点蚀电位明显降低,自腐蚀电流密度升高,此时的钝化膜保护能力下降。而当NH4Cl浓度达到饱和状态时,对比不同组织在饱和NH4Cl浓度下的破钝电位可以发现,敏化态电位最低,从热力学角度上说明敏化态组织更容易发生点蚀。NH4Cl浓度的增加,导致溶液中Cl-浓度升高,不锈钢表面钝化膜更容易被破坏,316L不锈钢的耐点蚀能力降低,更易发生点蚀,伴随着外加应力的作用下,极易引起应力腐蚀开裂。
图2 不同组织316L不锈钢在不同浓度NH4Cl溶液中的动电位极化曲线
图3 不同组织316L不锈钢在不同浓度NH4Cl溶液中破钝电位Eb和腐蚀电流Icorr拟合结果
图4为3种不同组织在不同浓度NH4Cl溶液中的Nyquist图。可以看出,随着NH4Cl浓度的增加,容抗弧的半径逐渐减小,表明耐蚀性随着浓度增加逐渐降低,这表现出与电化学过程相同的趋势,考虑到316L不锈钢具有一定的钝化特征,采用图5的等效拟合电路 (R(Q(R(QR))) 模拟NH4Cl溶液中316L不锈钢表面产物膜性质和阻抗情况[19-21],其中Rs为溶液电阻,Rf为电极表面腐蚀产物电阻,Rt为电荷转移电阻,Qdl和Qf分别代表双电层电容和非理想电容。用极化电阻Rp(Rp=Rt+Rf) 来表征不锈钢的耐腐蚀性,其值越大,耐腐蚀性越好[23]。将极化电阻Rp值与Cl-浓度进行拟合,其结果如图4d所示,从中可以看出316L不锈钢在NH4Cl溶液中的Rp值随着NH4Cl浓度的增加而减小。这一结果进一步说明,NH4Cl浓度的增大,降低了316L不锈钢的耐蚀性能。
图4 不同组织316L不锈钢在不同浓度NH4Cl溶液中的电化学阻抗谱
图5 电化学阻抗谱等效电路示意图
2.3 不同组织在NH4Cl沸腾溶液中的U形弯浸泡实验
图6为316L不锈钢在不同浓度沸腾NH4Cl溶液中浸泡30 min后的微观腐蚀形貌。在浓度为1%的沸腾NH4Cl溶液中316L不锈钢腐蚀较轻微,原始组织和固溶组织主要发生均匀腐蚀,而敏化组织发生轻微点蚀;当浓度增大为5%时,原始组织发生轻微点蚀,固溶组织出现微裂纹,敏化组织表面出现较大点蚀,且有连成裂纹的趋势;在浓度为10%的沸腾NH4Cl溶液中,不锈钢各种组织表面均出现大量点蚀及微裂纹。在饱和沸腾NH4Cl溶液中出现明显的宏观裂纹,伴随着较大的点蚀坑。不同组织316L不锈钢在饱和NH4Cl沸腾溶液中浸泡30 d均出现宏观裂纹,证明在加氢装置NH4Cl结垢、潮解等环境中,316L不锈钢有较高的应力腐蚀敏感性。
图6 316L不锈钢U形弯试样在不同浓度沸腾NH4Cl溶液中浸泡30 d微观形貌
图7中对不同组织316L不锈钢裂纹扩展过程进行追踪,不难看出,对于3种组织裂纹多贯穿于点蚀,在U形弯边缘裂纹较粗,可认为是裂纹最先扩展处。清洗、除锈过后,对孔洞的标记位置进行EDS成分分析,可知,以Cr的氧化物为主,也有一些Al、Si的夹杂成分存在,可以认为点蚀和微裂纹的产生与夹杂物的存在具有相关性。NH4Cl浓度自1%增大到饱和的过程中,钝化膜薄弱处优先被破坏,表现为覆盖在钝化膜下面的夹杂物 (Al、Si等) 加速溶解的过程,会优先在不锈钢表面形成点蚀,继而在点蚀边缘扩展出微小裂纹;其中一些微小裂纹在NH4Cl环境中继续发展,会与周围其他点蚀和裂纹合并,扩展中产生许多树枝状的分支裂纹,最终形成宏观裂纹,导致失效。由图7可知,原始态组织与固溶态组织的裂纹长度较短,敏化态组织的裂纹最长。
图7 不同组织316L不锈钢在饱和NH4Cl沸腾溶液中裂纹扩展SEM像
图8为316L不锈钢在饱和NH4Cl沸腾溶液中裂纹沿厚度扩展SEM图像,可见3种状态组织裂纹沿厚度扩展分支很多,呈现典型的应力腐蚀裂纹形态。对比不同组织在饱和NH4Cl沸腾溶液中的裂纹可以看出,3种组织的主要裂纹扩展模式是穿晶断裂。这进一步说明了,对于较低含碳量的316L不锈钢的敏化组织其裂纹扩展模式并未因敏化导致晶界结构变化而改变。但对比不同表面 (图6) 可以看出,敏化组织的应力腐蚀敏感性可能与敏化态组织的电化学特征相关,饱和NH4Cl沸腾溶液中的点蚀情况较为严重 (图7)。
图8 不同组织316L不锈钢在饱和NH4Cl沸腾溶液中裂纹沿厚度扩展SEM像
3 分析讨论
316L不锈钢在加氢装置NH4Cl环境下有较强的应力腐蚀敏感性,应力腐蚀开裂机理主要为阳极溶解机制[22-24]。Cl-会在不锈钢表面发生富集和吸附,破坏不锈钢表面的钝化膜,使其容易发生局部溶解而形成许多蚀坑,在蚀坑附近进一步发生应力集中,从而导致应力腐蚀开裂。主要电化学反应如下:
阳极过程:
阴极过程:
NH4Cl为强酸弱碱盐,溶液呈酸性,NH4Cl浓度越高,酸性越强,腐蚀性越强。因此随NH4Cl溶度增加,溶液pH降低,Cl-溶度升高,导致316L不锈钢腐蚀电流密度升高,破钝电位降低 (如图3所示),同时导致不锈钢表面钝化膜被破坏,钝化膜保护能力减弱,同时伴随着pH的下降,进一步引起局部酸化,从而形成闭塞效应,导致点蚀萌生,引发应力腐蚀开裂。
对于3种不同组织的应力腐蚀U形弯浸泡实验可以看出,3种组织的应力腐蚀裂纹萌生于外表面点蚀处,这主要是由于Cl-的存在破坏不锈钢表面的钝化膜,引起局部在夹杂物 (Al、Si等) 等位置 (如图7所示) 的优先溶解,形成点蚀坑,进而在应力的作用下引发局部点蚀处的应力集中,进而引发微裂纹的生成 (如图6所示),并且这些微裂纹在力学-电化学的协同作用下,进一步与周围的点蚀合并扩展,最终形成了宏观裂纹,导致失效[25-27]。对于本研究中的316L不锈钢由于具有极低的碳含量,因此对于敏化态组织,并未在晶间出现明显的析出物,316L敏化组织的应力腐蚀行为与其他组织的比较接近,没有明显的强弱差别 (图1)。而从图6~8中可以看出,在饱和NH4Cl浓度时,3种组织均具有较高的应力腐蚀敏感性,结合电化学结果 (图2) 亦可以看出,在饱和NH4Cl溶液中,316L不锈钢的破钝电位极低,极易引发点蚀萌生。因此,对于现场实际中,可以考虑通过控制NH4Cl的浓度 (注水洗或蒸汽洗),从而避免相关NH4Cl装置结盐,能有效地降低316L不锈钢发生应力腐蚀开裂的敏感性。从而减小316L不锈钢装置发生应力腐蚀的危险。
4 结论
(1) 316L不锈钢在NH4Cl环境下具有明显的SCC敏感性。其SCC机理主要为阳极溶解,裂纹扩展方式以穿晶扩展为主。SCC敏感性随NH4Cl溶度的升高而增大。原始组织、固溶组织及敏化组织均在饱和NH4Cl溶液中表现出最高的应力腐蚀敏感性。
(2) 316L不锈钢原始组织、固溶组织及敏化组织在NH4Cl环境下,破钝电位依次降低,维钝电流密度依次升高,阻抗谱依次减小;不同组织的316L不锈钢在饱和NH4Cl环境中,均具有极低的点蚀电位,更容易发生点蚀。
(3) 316L不锈钢在饱和NH4Cl溶液中的应力腐蚀敏感性最高,现场可通过控制NH4Cl浓度,避免结盐现象,缓解316L在NH4Cl环境中的发生应力腐蚀开裂问题。
参考文献
1 Hou B R, Li X G, Ma X M, et al. The cost of corrosion in China [J]. npj Mater. Degrad., 2017, 1: 4
2 Xing X J, Yang M H, Jiang Y J, et al. Summary of high-chlorine crude oil processing [J]. Pet. Ref. Eng., 2015, 45(1): 7
2 邢献杰, 杨明辉, 江煜杰等. 高氯原油加工情况总结 [J]. 炼油技术与工程, 2015, 45(1): 7
3 Zhou M. Current status of corrosion and control in Chinese petroleum refining and chemical enterprises [J]. Corros. Prot., 2012, 33 (suppl.2): 62
3 周敏. 中国石油炼化企业腐蚀与控制现状 [J]. 腐蚀与防护, 2012, 33(): 62
4 Liu Z Y, Dong C F, Li X G, et al. Stress corrosion cracking behaviour of two stainless steels in hydrogen sulfide environment [J]. J. Univ. Sci. Technol. Beijing, 2009, 31: 318
4 刘智勇, 董超芳, 李晓刚等. 硫化氢环境下两种不锈钢的应力腐蚀开裂行为 [J]. 北京科技大学学报, 2009, 31: 318
5 Sun J L, Zhou D, Jin J, et al. Localized corrosion resistance of three commonly-used stainless steels [J]. Chin. J. Mater. Res., 2017, 31: 665
5 孙京丽, 邹丹, 金晶等. 三种常用不锈钢的耐局部腐蚀性能 [J]. 材料研究学报, 2017, 31: 665
6 Sun L, Hou Y H, Yang X, et al. Effect of chlorine ion and sulfur ion on corrosion of 316L stainless steel and monel alloy in oil refining process [J]. Surf. Technol., 2015, 44(12): 41
6 孙亮, 侯艳宏, 杨席等. 炼油加工过程中氯离子与硫离子对316L不锈钢和Monel合金腐蚀的影响 [J]. 表面技术, 2015, 44(12): 41
7 Toba K, Suzuki T, Kawano K, et al. Effect of relative humidity on ammonium chloride corrosion in refineries [J]. Corrosion, 2011, 67: 055005
8 Toba K, Ueyama M, Kawano K, et al. Corrosion of carbon steel and alloys in concentrated ammonium chloride solutions [J]. Corrosion, 2012, 68: 1049
9 Zheng Z J, Ou G F, Ye H J, et al. Analysis on the under deposit corrosion of air cooler tubes: Thermodynamic, numerical and experimental study [J]. Eng. Failure Anal., 2017, 79: 726
10 Zhao M, Gong S P, Kang Q L, et al. Detection and control of chlorides in crude oil processing [J]. Corros. Prot. Petrochem. Ind., 2014, 31(3): 16
10 赵敏, 龚树鹏, 康强利等. 原油加工中氯化物的检测及控制 [J]. 石油化工腐蚀与防护, 2014, 31(3): 16
11 Cheng C Q, Klinkenberg L I, Ise Y, et al. Pitting corrosion of sensitised type 304 stainless steel under wet-dry cycling condition [J]. Corros. Sci., 2017, 118: 217
12 Yang X N, Qi H M, Gao J S, et al. Case analysis on corrosion by hydrogenation effluent [J]. Ref. Chem. Ind., 2011, 22(5): 42
12 杨秀娜, 齐慧敏, 高景山等. 加氢反应流出物腐蚀案例分析 [J]. 炼油与化工, 2011, 22(5): 42
13 Qiao G P, Chen W. Ammonium salt corrosion analysis and risk-bask management of hydro-processing reactor effluent system [J]. Corros. Prot., 2012, 33: 618
13 乔光谱, 陈炜. 加氢装置反应系统的氨盐腐蚀分析及风险管理 [J]. 腐蚀与防护, 2012, 33: 618
14 Tsutsumi Y, Nishikata A, Tsuru T. Pitting corrosion mechanism of Type 304 stainless steel under a droplet of chloride solutions [J]. Corros. Sci., 2007, 49: 1394
15 Liu X Y. Ammonium salt corrosion in reactor effluent system of hydrogenation unit and prevention [J]. Corros. Prot. Petrochem. Ind., 2014, 31(2): 17
15 刘新阳. 加氢反应流出物中铵盐腐蚀及预防 [J]. 石油化工腐蚀与防护, 2014, 31(2): 17
16 Shargay C A, Turner J, Messer B, et al. Design considerations to minimize ammonium chloride corrosion in hydrotreater REAC's [A]. Proceedings of the Corrosion 2001 [C]. Houston, Texas, 2001
17 Sun A D, Fan D Y. Prediction, monitoring, and control of ammonium chloride corrosion in refining processes [A]. Proceedings of the Corrosion 2010 [C]. San Antonio, Texas, 2010
18 Ma H C, Wu W, Zhou X C, et al. Comparative study on stress corrosion cracking behaviors of 304 and 321 austenitic stainless steels by different heat treatment in NH4Cl solution [J]. Surf. Technol., 2018, 47(11): 126
18 马宏驰, 吴伟, 周霄骋等. 不同热处理态的304和321奥氏体不锈钢在氯化铵环境中的应力腐蚀行为对比研究 [J]. 表面技术, 2018, 47(11): 126
19 Freire L, Carmezim M J, Ferreira M G S, et al. The passive behaviour of AISI 316 in alkaline media and the effect of pH: A combined electrochemical and analytical study [J]. Electrochim. Acta, 2010, 55: 6174
20 Andrade C, Keddam M, Nóvoa X R, et al. Electrochemical behaviour of steel rebars in concrete: Influence of environmental factors and cement chemistry [J]. Electrochim. Acta, 2001, 46: 3905
21 Daz B, Joiret S, Keddam M, et al. Passivity of iron in red mud’s water solutions [J]. Electrochim. Acta, 2004, 49: 3039
22 Feng Z C, Cheng X Q, Dong C F, et al. Passivity of 316L stainless steel in borate buffer solution studied by Mott-Schottky analysis, atomic absorption spectrometry and X-ray photoelectron spectroscopy [J]. Corros. Sci., 2010, 52: 3646
23 Luo H, Dong C F, Li X G, et al. The electrochemical behaviour of 2205 duplex stainless steel in alkaline solutions with different pH in the presence of chloride [J]. Electrochim. Acta, 2012, 64: 211
24 Luo H, Dong C F, Xiao K, et al. Characterization of passive film on 2205 duplex stainless steel in sodium thiosulphate solution [J]. Appl. Surf. Sci., 2011, 258: 631
25 Liu Z Y, Wang X Z, Liu R K, et al. Electrochemical and sulfide stress corrosion cracking behaviors of tubing steels in a H2S/CO2 annular environment [J]. J. Mater. Eng. Perform., 2014, 23: 1279
26 Truman J E. The influence of chloride content, pH and temperature of test solution on the occurrence of stress corrosion cracking with austenitic stainless steel [J]. Corros. Sci., 1977, 17: 737
27 Calcagnotto M, Ponge D, Demir E, et al. Orientation gradients and geometrically necessary dislocations in ultrafine grained dual-phase steels studied by 2D and 3D EBSD [J]. Mater. Sci. Eng., 2010, 527A: 2738
免责声明:本网站所转载的文字、图片与视频资料版权归原创作者所有,如果涉及侵权,请第一时间联系本网删除。
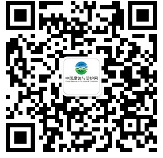
官方微信
《中国腐蚀与防护网电子期刊》征订启事
- 投稿联系:编辑部
- 电话:010-62316606-806
- 邮箱:fsfhzy666@163.com
- 中国腐蚀与防护网官方QQ群:140808414