摘要
采用电化学阳极氧化技术在含NH4F的乙二醇电解液中对Ti48Al5Nb合金进行阳极氧化处理,以获得富铝含氟阳极氧化膜。研究了阳极氧化处理对Ti48Al5Nb合金在1000 ℃空气中的氧化行为及氧化膜组成和结构的影响。结果表明:阳极氧化处理的Ti48Al5Nb合金经高温氧化后表面可形成连续、致密的Al2O3氧化膜,且氧化膜与基体具有良好结合力,有效阻止了氧向内扩散,进而显著提高了合金的抗高温氧化性能。经1000 ℃氧化100 h后,阳极氧化试样增重由未经阳极氧化处理试样的26.73 mg/cm2降至1.18 mg/cm2。同时,阳极氧化处理改变了合金的氧化机制,抑制了氧化膜/基体界面处富Nb层的出现。阳极氧化提高Ti48Al5Nb合金抗高温氧化性能是由于氧化膜中F在高温氧化过程中表现出的“卤素效应”所致。
关键词: 钛铝合金 ; 阳极氧化 ; 卤素效应 ; 抗高温氧化
TiAl基金属间化合物 (简称TiAl合金) 具有密度低、杨氏模量高、耐蚀性能和抗蠕变性能良好等特点,在航空航天和汽车等领域中有广泛的应用前景。然而,高温下TiAl合金表面易形成非保护性的TiO2和Al2O3混合氧化膜,导致其抗氧化性能较差,制约了TiAl合金的实际应用。
为此,国内外学者进行了大量研究,采用合金设计和表面处理来提高TiAl合金的抗高温氧化性能。研究表明,提高合金中Al含量或加入第三种元素,如:Mo,Y,Si和Nb等可不同程度提高TiAl合金抗高温氧化性能;其中,添加Nb的效果最佳。Lin等的研究结果表明,合金中的Nb在高温氧化过程中可掺杂到TiO2晶格中并取代Ti的位置。由于Nb5+比Ti4+化合价更高,因而Nb的掺杂可有效降低TiO2晶格中的氧空位,从而抑制氧的内扩散。此外,有研究者认为Nb可提高Al的活性,促进Al2O3生成[10];也有研究者认为Nb促进了稳定、致密的TiN层在氧化物/基体界面的形成。
尽管合金设计是提高合金抗高温氧化性能的有效措施之一,但合金元素加入量不可过高,如TiAl合金中Nb加入量过高会导致TiNb2O7,AlNbO4及Nb2O5等的形成,致使合金的抗高温氧化性能恶化。此外,添加高含量合金元素必然会对合金的力学性能产生有害影响。对合金进行表面处理可在不改变合金自身力学性能的前提下有效提高其抗高温氧化性能,因而得到广泛应用。
TiAl合金表面处理主要包括制备防护涂层和表面改性,其中,基于“卤素效应”的表面改性由于可显着提高TiAl合金的抗高温氧化性能而受到关注。将卤族元素有效引入TiAl合金表面的技术包括:离子注入、在合金表面喷涂或涂覆含氟聚合物及直接将合金浸置在含F的酸性溶液中等。研究人员系统研究了TiAl合金表面掺杂卤素对合金高温氧化行为的影响。TiAl合金表面引入少量卤素提高合金抗高温氧化性能的主要作用机制如下:(1) 卤素可抑制O2的内扩散,进而降低TiO2的生长速率;(2) 在高温氧化的过程中,卤化钛的挥发促使Al在氧化膜/基体界面富集,从而促进保护性Al2O3的生成;(3) 高温氧化过程中,卤化铝可通过孔洞或者裂纹向外扩散至氧化层/基体界面,促使连续的Al2O3膜在界面处生成。此外,已有报道[18]表明在高温循环氧化测试过程中,与Br、I相比,F提高TiAl合金抗高温氧化性能的效果更明显。近年来,本课题组提出在含氟体系中采用阳极氧化技术在TiAl合金表面原位生长一层含氟氧化膜以提高合金抗高温氧化性能。结果表明,在高温氧化过程中,阳极氧化膜中的氟化物可促进合金表面生成连续致密的Al2O3层,进而提供优异的防护效果。
本文以更具实际应用价值的高铌TiAl合金为基体,采用阳极氧化和卤素效应相结合的方式,选用含少量氟化铵 (NH4F) 的乙二醇有机溶液作为电解液体系,在Ti48Al5Nb合金表面制备一层富氟阳极氧化膜,以提高合金的抗高温氧化性能。同时研究了阳极氧化合金在空气中1000 ℃下的氧化行为。采用场发射扫描电镜 (FE-SEM) /能谱 (EDS)、X射线衍射 (XRD) 及X射线光电子能谱分析 (XPS) 等技术分析了高温氧化前后试样表面形貌以及氧化层的结构与组成,探究阳极氧化预处理对Ti48Al5Nb合金高温氧化过程的影响机制。
1 实验方法
将Ti48Al5Nb合金线切割成尺寸为15 mm×15 mm×1 mm的薄片。在阳极氧化前对试样进行预处理,首先用250 μm砂纸打磨以去除试样表面的氧化层,随后分别在丙酮和无水乙醇中超声清洗5 min,清洗完全后的试样使用暖风吹干,然后放置在干燥器中保存备用。
预处理后的试样在含0.15 mol/L NH4F的乙二醇电解液中进行恒电压阳极氧化。以距离为5 cm的两块石墨片 (面积为100 mm×25 mm) 作为阴极,预处理的Ti48Al5Nb合金悬挂于两块石墨电极中间作为阳极。阳极氧化过程中采用磁子对电解液进行搅拌,电解液温度控制在25 ℃。阳极氧化后的试样分别在去离子水、丙酮以及无水乙醇中超声清洗,最后暖风吹干。
高温氧化测试在箱式炉 (KSL-1200X,合肥科晶) 中进行。高温氧化测试前先将所有刚玉坩埚置于1200 ℃下烧至恒重。在室温下将待测试样垂直放入坩埚并自然地斜靠在坩埚内壁,待箱式炉稳定在1000 ℃后放入炉中开始高温氧化测试。经过选定的时间间隔后将坩埚从炉中取出,放置在室温空气中冷却30 min后,使用精度为0.1 mg的电子天平 (Satorious) 称量并记录。试样称量完成后,将试样再次放回炉中继续进行高温氧化测试,累计高温下氧化总时间达到100 h后停止实验。计算不同时间下各试样的单位面积增重 (mg/cm2),绘制氧化增重曲线。为减小实验误差,每个条件至少测试3个平行试样,结果取平均值。
高温氧化前后的试样使用XRD (Panalytical X'Pert PRO,Cu Kα (λ=0.154056 nm),40 kV,40 mA) 进行相组成分析。利用带有EDS (Oxford 80X) 的FE-SEM (FEI nano nova 450) 对试样的表面形貌、截面结构和相应的元素组成进行分析。同时使用XPS (Kratos Axis ultra DLD,Al Kα,hυ=1486.6 eV) 对试样表面的元素组成进行分析。
2 结果与讨论
2.1 阳极氧化膜的形貌表征
图1为Ti48Al5Nb合金和不同电压下阳极氧化的Ti48Al5Nb合金表面微观形貌。由图1a和e可知,阳极氧化处理前的Ti48Al5Nb合金表面较平整,可见砂纸打磨痕迹。经10 V电压下阳极氧化1 h的Ti48Al5Nb合金,除打磨形成的划痕外 (图1b),高倍SEM像中可见阳极氧化后试样表面存在形状不规则的纳米孔洞 (图1f),且EDS分析结果显示氧化膜中存在F (图1j)。当阳极氧化电压提高至20 V时,试样表面出现了大量裂纹 (图1c),而未产生裂纹的区域依旧存在不规则的纳米孔洞 (图1g)。进一步将阳极氧化电压提高至30 V时 (图1d和h),整个试样表面布满了纳米孔洞;且相对于其它电压条件而言,此时纳米孔形状更加规则。EDS分析显示,随阳极电压升高,氧化膜中F含量逐渐升高 (图1j~l)。由于阳极氧化之后试样经过了充分清洗,如此高含量的F说明在阳极氧化过程中,溶液中的F-参与了氧化膜成膜反应。
2.2 阳极氧化膜的化学组成
图2为Ti48Al5Nb合金经30 V电压下阳极氧化1 h后的XPS谱。从图2a可知,阳极氧化膜主要由Ti、Al、Nb、O及F组成;且半定量分析结果进一步显示,阳极氧化膜外表面中F含量较高 (图2a中插入的表格)。图2b为Ti 2p的XPS谱,其中结合能为459.1和464.6 eV的峰分别与TiO2的2p 3/2和2p 1/2自旋轨道耦合双峰相对应。此外,从图中可看出,氧化膜中还含有少量的Ti-F化合物 (见图2b中插入的放大图)。图2c为Al 2p的XPS谱,其中结合能为75.8和75.0 eV的峰分别与Al-F化合物和Al2O3相吻合。Nb 3d的XPS谱如图2d所示,3d 5/2和3d 3/2均可用单峰较好地拟合,可归属为Nb2O5。图2e为F的XPS谱,可用两个峰较好的拟合,分别归属于Ti-F化合物和Al-F化合物,且通过对比峰面积可知,外表面中的铝氟化合物含量高于钛氟化合物。O 1s的XPS谱如图2f所示,其中结合能为533.2,532.4,531.4和530.9 eV的峰分别对应于吸附氧、Al2O3、Nb2O5和TiO2。
2.3 氧化动力学
在1000 ℃空气环境下对阳极氧化Ti48Al5Nb合金的抗高温氧化性能进行评估。如图3所示,氧化100 h后,Ti48Al5Nb合金增重达26.73 mg/cm2 (曲线1);而阳极氧化处理的Ti48Al5Nb合金增重明显降低,且增重量随阳极氧化电压增大而减小 (曲线2~4)。经30 V阳极氧化1 h处理后的试样增重仅为1.18 mg/cm2 (曲线4),说明阳极氧化显着降低了合金的高温氧化速度。此外,从图中插入的宏观光学照片也可直观的看出,阳极氧化处理的Ti48Al5Nb合金表面完整、致密,说明试样的抗高温氧化性明显提升。在高温氧化过程中,Ti48Al5Nb合金表面生成一层较厚的氧化层,同时伴随着氧化膜脱落;而阳极氧化Ti48Al5Nb合金表面的氧化层未见任何脱落。说明阳极氧化不仅能显着降低合金的氧化速度,还能明显改善氧化膜的抗剥落性能。
2.4 氧化膜的相组成
如图4a所示,未经阳极氧化处理的Ti48Al5Nb合金氧化后表面可检测到TiO2,Al2O3,Ti3Al及TiAl等。由于Ti48Al5Nb合金在氧化过程中形成的氧化膜与基体结合力较差而不断脱落,导致基体暴露,因此基体TiAl和Ti3Al的衍射峰强度较高,而氧化物TiO2和Al2O3的衍射峰强度较低。由图4b~d可知,经阳极氧化的Ti48Al5Nb合金氧化之后,氧化膜仍然主要由TiO2和Al2O3组成 (Ti3Al和TiAl的衍射峰信号来自基体)。阳极氧化Ti48Al5Nb合金在氧化过程中表面形成的氧化膜较薄,因此,X射线可穿透氧化膜到达基体而检测到明显的基体衍射峰信号。此外,对比不同电压下阳极氧化试样的XRD谱可见,阳极氧化电压越高的试样,经过氧化之后表面TiO2的衍射峰强度约弱,说明Ti48Al5Nb合金的抗高温氧化性能随阳极氧化电压增大而增强,这与高温氧化动力学测试结果一致。
2.5 氧化膜的表面和截面形貌
图5为Ti48Al5Nb合金和不同电压下阳极氧化的Ti48Al5Nb合金经1000 ℃氧化100 h后的表面微观形貌。由图5a可知,未经阳极氧化处理的Ti48Al5Nb合金表面形成的氧化膜发生了严重脱落,导致基体不断暴露并发生氧化,以致形成多层氧化膜结构。图中尚未脱落的氧化膜为最后一次取样时仍未脱落的区域。而阳极氧化处理的Ti48Al5Nb合金氧化后表面形貌发生了显着改变 (图5b~h)。如图5b所示,10 V电压下阳极氧化的Ti48Al5Nb合金经1000 ℃氧化100 h后存在两种明显不同的区域,其高倍率像分别如图5c和d所示。图5c所示区域的氧化膜表面较平整,沟壑形貌的形成可能是砂纸打磨痕迹所致,EDS分析表明该区域Al含量较高,为Al2O3富集区。而图5d所示区域则由大量块状氧化物颗粒组成,根据EDS和XRD的结果分析可知该氧化物主要为金红石TiO2。这说明阳极氧化电压较低时,阳极氧化膜不均匀,高温氧化过程中阳极氧化膜较薄的区域氧化较严重而形成非保护性TiO2;阳极氧化膜较厚的区域高温氧化后则形成保护性的Al2O3。进一步提高阳极氧化电压至20 V (图5e和f) 和30 V (图5g和h) 后,高温氧化形成的氧化膜更为致密且平整,无任何脱落。EDS分析显示此时的氧化膜中Al含量较高,因此可提供良好的抗氧化效果。
值得注意的是,图2h显示30V电压下阳极氧化的Ti48Al5Nb合金表面存在大量孔洞,但该试样经过1000 ℃氧化100 h后表面多孔结构消失,形成了连续、致密的保护性氧化膜 (图5g和h)。这是由于高温氧化过程中,氧化膜中的孔结构被氧化物填充所致。如图6a和b显示,1000 ℃氧化1 h后,纳米孔即被大量颗粒填充,但此时阳极氧化膜中的裂纹仍然存在。当氧化时间延长至3 h以后,阳极氧化膜表面的裂纹和孔洞均被高温氧化形成的氧化物填充,此时氧化膜的表面形貌与氧化100 h后的很类似 (图5h)。该致密氧化膜可有效阻止氧向内扩散和合金中Ti、Al和Nb向外扩散,进而提供优异的高温防护性能。然而多孔阳极氧化膜形成致密的保护性氧化膜的微观过程仍有待深入研究。
图7为未经阳极氧化处理的Ti48Al5Nb合金在1000 ℃氧化100 h后截面微观形貌,以及相应区域的EDS面扫描分析结果。图7a和c给出了试样高温氧化后典型平整区域与凹坑区域的截面微观形貌。结合EDS面扫描结果 (图7b) 和XRD谱 (图4a) 可知,图7a所示区域的氧化膜最外层为Al2O3和TiO2混合层,向内为存在大量条形Al2O3内氧化物的Ti3Al中间层。需要指出的是,未经阳极氧化处理的Ti48Al5Nb合金在截面形貌表征前氧化物已严重脱落,但图7a所示区域的最外层仍然存在厚度约为13 μm的Al2O3和TiO2混合层。图7c所示区域的氧化程度比图7a中的更严重,此区域发生了严重的内氧化。
图8为10 V电压下阳极氧化的Ti48Al5Nb合金经1000 ℃氧化100 h后的截面微观形貌及相应的EDS线扫描和面扫描结果。由图8a可知,此时氧化膜的结构与未经阳极氧化处理合金的图7a所示区域的氧化膜结构十分相似,但外氧化膜厚度更薄。这说明阳极氧化在一定程度上改善了合金的抗高温氧化性能,但氧化100 h后的合金依然发生了较严重的氧化。实际上,从氧化增重曲线 (图3中的曲线2) 上也可见,经10 V阳极氧化后的Ti48Al5Nb合金1000 °C氧化60 h后增重较快,从SEM表面形貌中也观察到部分区域出现TiO2簇 (图5d)。此外,该试样氧化膜外层的Al2O3和TiO2混合层下方存在一层Nb富集层 (表3,图8b和c)。已有报道证实富Nb层可以阻碍Ti的外扩散,从而抑制TiO2的生成。
当阳极氧化电压增加至30 V时,Ti48Al5Nb合金高温氧化后的氧化膜组成和结构发生了明显的改变。如图9a所示,此时合金表面形成了一层致密、连续的氧化膜,并且该氧化层与基体结合十分紧密。根据EDS结果与XRD分析可知,这层连续、致密的氧化层主要由Al2O3和少量TiO2组成。此外,在该连续Al2O3层下方存在约8 μm的贫铝层。Al2O3氧化膜的形成可能包括两种途径:一是基体中外扩散的Al与通过阳极氧化膜内扩散的O2反应形成;二是阳极氧化膜中的Al-F化合物在高温氧化过程中由于“卤素效应”与O2反应形成。在致密的Al2O3层上仍然存在一层较薄的Al2O3和TiO2混合层,可能是高温氧化初期未能形成连续的Al2O3层所致。值得一提的是,阳极氧化电压较低时 (10 V),合金表面氟化物含量较低,卤素效应导致高温氧化过程中铝氟化合物向Al2O3的转变不足以形成连续致密的Al2O3层 (图9c),因此在一段时间后依旧发生了较严重的氧化。
2.6 氧化膜的组成
采用XPS研究了阳极氧化Ti48Al5Nb合金表面氧化膜的化学组成 (图10)。如图10a所示,经过100 h氧化后,氧化膜中Al/Ti原子比由阳极氧化膜中的0.5提高至2,说明在高温氧化过程中,外表面逐渐转化成富铝层。这是阳极氧化膜中F的“卤素效应”所致。由于TiF4的沸点仅为284 ℃,因此在高温氧化过程中极易升华;同时AlF3会从氧化膜向外表面扩散进一步促进外表面形成富铝层,结合SEM和XRD结果能够确定外表面的富铝层为Al2O3层。此外,在经过100 h的氧化后,外表面已检测不到F,这是由于含F化合物被消耗所致。图10b~d分别为Ti 2p,Al 2p和Nb 3d的XPS谱。拟合可知,这3个元素的XPS谱均可用单峰完美的拟合,相应的氧化物分别为Al2O3,TiO2和Nb2O5。O 1s的XPS谱仍然可由4个峰拟合,分别对应于吸附氧,Al2O3,Nb2O5和TiO2,且氧化膜中Al2O3的含量高于TiO2的。
3 结论
(1) 在含0.15 mol/L NH4F的乙二醇溶液中对Ti48Al5Nb合金进行阳极氧化,可显着提高合金的抗高温氧化性能。在1000 ℃下氧化100 h后,阳极氧化处理的Ti48Al5Nb合金表面可形成与基体结合良好且致密的氧化膜。30 V电压下氧化1 h的合金,氧化增重由未经过阳极氧化处理Ti48Al5Nb合金的29.73 mg/cm2降至1.18 mg/cm2。
(2) 阳极氧化提高Ti48Al5Nb合金抗氧化性能主要是通过阳极氧化膜中氟化物的“卤素效应”来实现。一方面在高温氧化过程中,阳极氧化膜中的Ti-F化合物易挥发,导致外表面Al含量增加;二是在高温氧化过程中Al-F化合物逐渐向Al2O3转变,促使外表面形成一层连续致密的保护性氧化层。
参考文献
[1] Clemens H, Mayer S. Design,processing, microstructure, properties, and applications of advanced intermetallic TiAl alloys [J]. Adv. Eng. Mater., 2013, 15: 191
[2] Zhang M M, Xin L, Ding X Y, et al. Corrosion resistance of alternately multilayered coating Ti/TiAlN on Ti-alloy Ti-6Al-4V beneath a solid NaCl film in atmosphere of water vapor and oxygen at 600 °C [J]. J. Chin. Soc. Corros. Prot., 2017, 37: 29
[2] 张明明, 辛丽, 丁学勇等. 600 ℃/NaCl-H2O-O2协同环境中Ti/TiAlN多层涂层的耐蚀行为 [J]. 中国腐蚀与防护学报, 2017, 37: 29
[3] Peng X M, Xia C Q, Wang Z H, et al. Development of high temperature oxidation and protection of TiAl-based alloy [J]. Chin. J. Nonferrous Met., 2010, 20: 1116
[3] 彭小敏, 夏长清, 王志辉等. TiAl基合金高温氧化及防护的研究进展 [J]. 中国有色金属学报, 2010, 20: 1116
[4] Pflumm R, Friedle S, Schütze M. Oxidation protection of γ-TiAl-based alloys-A review [J]. Intermetallics, 2015, 56: 1
[5] Dai J J, Zhu J Y, Chen C Z, et al. High temperature oxidation behavior and research status of modifications on improving high temperature oxidation resistance of titanium alloys and titanium aluminides: A review [J]. J. Alloy. Compd., 2016, 685: 784
[6] Pflumm R, Donchev A, Mayer S, et al. High-temperature oxidation behavior of multi-phase Mo-containing γ-TiAl-based alloys [J]. Intermetallics, 2014, 53: 45
[7] Wu Y, Hagihara K, Umakoshi Y. Influence of Y-addition on the oxidation behavior of Al-rich γ-TiAl alloys [J]. Intermetallics, 2004, 12: 519
[8] Taniguchi S, Kuwayama T, Zhu Y C, et al. Influence of silicon ion implantation and post-implantation annealing on the oxidation behaviour of TiAl under thermal cycle conditions [J]. Mater. Sci. Eng., 2000, A277: 229
[9] Li X Y, Taniguchi S, Matsunaga Y, et al. Influence of siliconizing on the oxidation behavior of a γ-TiAl based alloy [J]. Intermetallics, 2003, 11: 143
[10] Shida Y, Anada H. The effect of various ternary additives on the oxidation behavior of TiAl in high-temperature air [J]. Oxid. Met., 1996, 45: 197
[11] Shen Y, Ding X F, Wang F G, et al. High-temperature oxidation resistance of high-Nb TiAl-based alloy [J]. J. Chin. Soc. Corros. Prot., 2004, 24: 203
[11] 沈勇, 丁晓非, 王富岗等. 高铌TiAl基合金高温抗氧化性能研究 [J]. 中国腐蚀与防护学报, 2004, 24: 203
[12] Lin J P, Zhao L L, Li G Y, et al. Effect of Nb on oxidation behavior of high Nb containing TiAl alloys [J]. Intermetallics, 2011, 19: 131
[13] Varma S K, Chan A, Mahapatra B N. Static and cyclic oxidation of Ti-44Al and Ti-44Al-xNb alloys [J]. Oxid. Met., 2001, 55: 423
[14] Jiang H R, Hirohasi M, Lu Y, et al. Effect of Nb on the high temperature oxidation of Ti-(0-50 at.%)Al [J]. Scr. Mater., 2002, 46: 639
[15] Wang D S, Tian Z J, Chen Z Y, et al. High-temperature oxidation resistance coatings on TiAl alloy surface [J]. J. Chin. Soc. Corros. Prot., 2009, 29: 1
[15] 王东生, 田宗军, 陈志勇等. TiAl合金表面抗高温氧化涂层研究 [J]. 中国腐蚀与防护学报, 2009, 29: 1
[16] Shen M L, Zhu S L, Wang F H. Formation kinetics of multi-layered interfacial zone between γ-TiAl and glass-ceramic coatings via interfacial reactions at 1000 °C [J]. Corros. Sci., 2015, 91: 341
[17] Schütze M. The role of surface protection for high-temperature performance of TiAl alloys [J]. JOM, 2017, 69: 2602
[18] Friedle S, Pflumm R, Seyeux A, et al. ToF-SIMS study on the initial stages of the halogen effect in the oxidation of TiAl alloys [J]. Oxid. Met., 2018, 89: 123
[19] Friedle S, Laska N, Braun R, et al. Oxidation behaviour of a fluorinated beta-stabilized γ-TiAl alloy with thermal barrier coatings in H2O-and SO2-containing atmospheres [J]. Corros. Sci., 2015, 92: 280
[20] Donchev A, Richter E, Schütze M, et al. Improving the oxidation resistance of TiAl-alloys with fluorine [J]. J. Alloy. Compd., 2008, 452: 7
[21] Schütze M, Schumacher G, Dettenwanger F, et al. The halogen effect in the oxidation of intermetallic titanium aluminides [J]. Corros. Sci., 2002, 44: 303
[22] Donchev A, Gleeson B, Schütze M. Thermodynamic considerations of the beneficial effect of halogens on the oxidation resistance of TiAl-based alloys [J]. Intermetallics, 2003, 11: 387
[23] Mo M H, Wu L K, Cao H Z, et al. Improvement of the high temperature oxidation resistance of Ti-50Al at 1000 ℃ by anodizing in ethylene glycol/BmimPF6 solution [J]. Surf. Coat. Technol., 2016, 286: 215
[24] Mo M H, Wu L K, Cao H Z, et al. High temperature oxidation behavior and anti-oxidation mechanism of Ti-50Al anodized in ionic liquid [J]. Surf. Coat. Technol., 2016, 307: 190
[25] Mo M H, Wu L K, Cao H Z, et al. Halogen effect for improving high temperature oxidation resistance of Ti-50Al by anodization [J]. Appl. Surf. Sci., 2017, 407: 246
[26] Wu L K, Xia J J, Cao H Z, et al. Improving the high-temperature oxidation resistance of TiAl alloy by anodizing in Methanol/NaF solution [J]. Oxid. Met., 2018, 90: 617
[27] Norasetthekul S, Park P Y, Baik K H, et al. Dry etch chemistries for TiO2 thin films [J]. Appl. Surf. Sci., 2001, 185: 27[21] SteyerP, PilloudD, PiersonJ F, et al. Oxidation resistance improvement of arc-evaporated TiN hard coatings by silicon addition [J]. Surf. Coat. Technol., 2006, 201: 4158
免责声明:本网站所转载的文字、图片与视频资料版权归原创作者所有,如果涉及侵权,请第一时间联系本网删除。
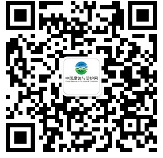
官方微信
《中国腐蚀与防护网电子期刊》征订启事
- 投稿联系:编辑部
- 电话:010-62316606-806
- 邮箱:fsfhzy666@163.com
- 中国腐蚀与防护网官方QQ群:140808414