王德仁,张涛,何业东
(北京科技大学,北京市腐蚀、磨蚀与表面技术重点实验室)
作者简介
王德仁,男,北京科技大学新材料技术研究院副教授,现任北京市腐蚀、磨蚀与表面技术重点实验室秘书。研究方向:为高温腐蚀机理和表面防护技术。在国内外刊物上发表论文60余篇,其中EI检索论文40篇,SCI检索论文35篇,申报中国国家发明专利11项,获得授权专利10项。负责的国家自然科学基金“热障涂层中强附着性TGO的生成机理和抗热冲击特性研究”中,利用高频电脉冲技术制备了多种微晶MCrAlY ODS合金涂层,显著提高了合金的抗高温氧化性能,制备了梯度分布的α-Al2O3弥散强化MCrAlY合金涂层,提出了制备新型热障涂层粘结合金涂层的新思路以及提高热障涂层中TGO性能所涉及的关键科学问题,为解决因TGO失稳导致热障涂层的失效这一热障涂层研究中的关键问题提供了新的途径。在合金涂层和陶瓷涂层制备工艺、抗氧化(含水水蒸汽)、抗硫化性能评估方面承担过多项研究工作,提出了利用微波加热来制备铝化物、硅化物等合金涂层,有效地解决了石化、电力、冶金行业中存在的多个难题;在国家自然科学基金项目“阴极微弧电沉积氧化锆-氧化钇陶瓷涂层的研究”和“水溶液中电极表面气膜微弧放电的机理及其物理化学效应研究”中也获得许多创新的成果。目前在研国家自然科学基金课题“大面积阴极等离子电解沉积金属涂层的机理及其涂层特性研究”中负责大面积阴极等离子电解沉积Ni-P、Ni-Cr、Co-Cr等合金涂层的机理及其特性研究。
王德仁
摘要:为了提高Nb-TiAl在900℃以上的抗高温氧化性能,本文通过微波加热方式,结合粉末包埋渗工艺在高铌钛铝合金基体上成功制备出了均匀致密的硅化物涂层。采用2.6KW微波加热功率渗制2h,快速获得了30μm厚的硅化物涂层。利用扫描电镜、能谱分析和X射线衍射等研究了氧化前后涂层的形貌、元素分布和物相组成。分析结果表明:涂层有15μm厚的外层,物相为TiSi2和NbSi2;内层为15μm富铝层。1000℃下100h的氧化动力学测试结果表明:硅化物涂层大大提高了Nb-TiAl合金的抗高温氧化性能,增重量和剥落量为0.5714mg/cm2和0.7143mg/cm2,仅为空白试样的1/22倍和1/59倍。
关键词:高铌钛铝合金;微波加热包埋渗硅;高温氧化
1 引言
TiAl金属间化合物同时兼有金属的高温韧性及陶瓷的高温性能,以及高比强度,良好的抗氧化性,优良的高温强度、蠕变性能、刚度,低密度等,使之成为一类很有发展前景的高温结构材料[1-4]。同时近些年发展起来的Nb-TiAl金属间化合物体系明显改善了TiAl体系的高温强度和抗高温氧化性能。由于高熔点元素Nb的加入使得该合金体系的使用温度达到了900℃以上,从而显示出替代Ni基合金的巨大潜能[5]。该体系合金与Ni基合金相比,质量减轻了50%左右,这对于航空领域有着重要意义。但是其在900℃以上温度下抗高温氧化性能不足成为制约其在航空领域广泛使用的巨大瓶颈。因此,如何进一步改善高铌钛铝合金的抗高温氧化性能是研究的关键所在。
国内外学者在改善高铌钛铝合金抗高温氧化性能方面做过不少尝试。张宁[6]等采用离子植入法研究了合金元素Y对高铌钛铝合金抗高温氧化性的影响,发现适量的元素Y具有细化晶粒的作用,并且能促使在外表面形成连续、致密的Al2O3层,能有效地阻止基体的氧化。X.J. Zhang[7]等采用溶胶-凝胶法在γ-TiAl基合金上制备了一层薄薄的Al2O3膜,能有效地阻止Ti元素的氧化,在Al2O3膜下生成富Al2O3的氧化层,从而能有效地防止γ-TiAl基体的氧化。M. Goral[8]等采用料浆法在高铌钛铝合金上制备了硅改性的铝化物涂层,能在高铌钛铝合金表面形成富铝层TiAl3,TiAl3氧化生成的Al2O3能有效地阻挡氧向基体内的扩散,阻止基体进一步被氧化;并且由于Si的加入会在表面形成Ti5Si3,也能较好的提高基体的抗高温氧化性能。Si元素能够有效地降低Ti离子的活度、阻碍Ti离子的向外扩撒,适量的Si元素的加入能够使得TiO2生成量减少,而Al2O3生成量却增加,并能形成连续致密的Al2O3保护膜,从而能够有效地阻止基体的氧化[9]。
通过微波加热包埋渗硅的新工艺在高铌钛铝合金基体上开展了制备硅化物涂层的研究,利用微波加热特性(内部快速整体加热),尝试获得快速制备硅化物涂层的新途径,并对获得的硅化物涂层微观组织结构及抗高温静态氧化动力学进行了测试。
2 实验条件
利用SUPRA 55 FE-SEM(NORAN System Six Models 200/300 EDS)对涂层氧化前后进行表面和截面形貌观察;采用Rigaku D/max PB X射线衍射仪对硅化物涂层进行物相分析。
3 实验结果与分析
3.1硅化物涂层的微观组织与形成机制分析
图1 高铌钛铝合金硅化物涂层微观组织:(a)硅化物涂层表面形貌,(b) 硅化物涂层截面形貌
图1为微波加热包埋渗法在2.6KW×2h下得到的硅化物涂层的SEM形貌图。从图1(a)中可以看出涂层表面有一些颗粒状的物质,从能谱图可知这些颗粒状的物质为Si的颗粒。除此之外,涂层表面较为平整,没有明显裂纹的出现;从图1(b)中可以看出通过微波加热包埋渗的方法在高铌钛铝合金表面获得了30μm厚的涂层,明显由两部分组成:外层约15μm,该层致密、连续、完整,颜色为白亮色;内层大约也是15μm厚,由白色岛状物分散在深色基体上所构成。
经涂层元素分布图分析得知:涂层外层主要是NbSi2、TiSi2等;内侧Al元素富集,中间过渡区有Si和少量的Nb和Ti。由于硅化物本身就有较好的抗高温氧化性能,再加上硅化物下面还有一层Al的富集区(在高温下易形成连续的α-Al2O3,从而很好起到阻隔氧扩散),这会大大改善高铌钛铝合金的抗高温氧化性能。
图2 高铌钛铝合金和硅化物涂层XRD衍射结果
高铌钛铝合金渗硅前后的XRD衍射分析图谱如图2所示。可以得出,硅化物涂层主要是TiSi2和NbSi2的衍射峰,同时有少量的Ti5Si3和Nb5Si3的衍射峰,这说明所制备的硅化物涂层主要成分是TiSi2和NbSi2,同时掺杂有少量的Ti5Si3和Nb5Si3。#p#副标题#e#
3.2硅化物涂层抗高温氧化性能
3.2.1 硅化物涂层氧化动力学规律
图3为有无硅化物涂层试样在1000℃下氧化100h的氧化增重曲线和氧化物剥落曲线,可以看出,在静态高温氧化过程中,与无硅化物涂层试样相比,带有涂层的试样无论是在氧化增重量还是剥落量方面都有了非常显著地降低,经过100h小时循环氧化后其氧化增重量和热循环剥落量仅为0.5714mg/cm2和0.7143 mg/cm2,这说明硅化物涂层能极大地改善了高铌钛铝高温合金的抗高温氧化和抗热循环剥落性能。
图3 高铌钛铝合金合金及硅化物涂层在1000℃下氧化100h后的氧化增重曲线(a)和氧化物剥落曲线(b)
3.2.2 硅化物涂层氧化后显微组织形貌
图4 高铌钛铝合金(a, b)及其硅化物涂层 (c, d)在1000℃下氧化100h后的表面和截面(背散射)形貌
图4为高铌钛铝合金和硅化物涂层在1000℃下氧化100h后的表面和截面形貌,对比图4(a)和4(c)可以看出,合金氧化后表面含有大量粗大的柱状晶粒,晶粒间有明显的裂纹出现;而渗硅试样表面主要由一些细小的颗粒组成,表面还有一层玻璃态物质。EDS能谱分析表明,粗大的四方晶粒主要含Ti和O,可以判断为氧化后产生的TiO2,而硅化物涂层表面生成的细小颗粒则主要含有Si、Al、O和极少量的Ti,可知涂层氧化产物主要由SiO2和Al2O3组成。从图4(b)和4(d))可以看出,合金氧化膜由三层组成,其厚度要比渗硅试样氧化膜厚度大得多,并有明显的裂纹和疏松存在,结合EDS可知由TiO2和Al2O3组成,微量Nb2O5;而硅化物涂层试样氧化膜较薄且致密,EDS显示其为Al2O3和SiO2。
3.2.3 硅化物涂层氧化产物物相分析
图5为高铌钛铝合金及其硅化物涂层在1000℃下氧化100h后的XRD衍射图。从图中也可以看出合金氧化后的氧化膜主要物相为TiO2和Al2O3,其中TiO2是最主要的物相。而硅化物涂层氧化膜主要由Al2O3、SiO2、TiO2和Nb2O5组成,其中Al2O3和SiO2是氧化膜的主要物相。SiO2在高温下可以形成玻璃态物质,能密封Al2O3不致密带来的缺陷,具有自愈合功能,有效地阻止氧元素向基体内部的扩散,显著降低合金基体的氧化速度。
图5 高铌钛铝合金及其硅化物涂层在1000℃下氧化100h后的XRD衍射图
3.3 涂层形成机理
包埋渗实际上就是基体被沉积介质包围时发生的一种化学汽相淀积过程。活化剂的加入,实际上是在一定温度下被渗元素与活化剂生成气态的卤化物,气态卤化物扩散至基体表面并发生分解或置换等相界面反应生成待渗元素的活性原子,活性原子首先吸附在金属基体表面自由能高的各点上,然后陆续被金属基体吸收,溶入的金属原子向邻近的点阵空位中迁移,而空位则向相反的方向移动[10]。对于本实验来说,NaF为催化剂,与Si粉在一定温度下反应生成SiFx(x=1~4),SiFx在化学式梯度的驱使下扩散到金属基体表面并发生一系列的反应生成活性Si原子,其发生的反应如下所示[11,12]
Si(s) + xNaF(l) →SiFx(g) + xNa(g) (1)
5SiFx(g) + xNb(s) → xNbF5(g) +5[Si] (2)
2SiFx(g) → 2[Si] +xF2(g) (3)
SiFx(g) + xNa(g) → [Si] +xNaF(l) (4)
(x+1)SiFx(g) → [Si] +xSiFx+1(g) (5)
产生的活性Si原子吸附在基体金属表面上,随后被基体金属吸收并在高温下向基体金属内部扩散而形成相应的硅化物涂层。
微波加热具有体加热、场强高温、高频高温、穿透性强、加热均匀、热惯性小等特点。由于微波具有穿透性,能够穿透到渗剂里面,使渗剂受热更加均匀,而基体本身是块状的,并不吸收微波,所以多余的微波同样会被渗剂和加热介质所吸收,转换成热能,加热效率高。微波加热时产生的高场强,高频率,离子在高场强、高频率的作用下,离子反应速度加快,使Si离子更加快速的沉积到高铌钛铝合金基体表面。同时在电场作用下,离子运动受电场的影响,更容易沉积到高铌钛铝合金基体表面,这样Si离子就更容易被高铌钛铝合金吸收。在Si离子向高铌钛铝合金基体内部扩散的时候,由于高的温度、电场强度,Si离子更容易和金属集体中的元素反应,形成相应的高硅化物(M5Si3,M为Nb、Ti),进而形成MSi2(M为Nb、Ti),大大缩短了形成硅化物涂层的时间,提高工作效率。
3.4 渗硅高铌钛铝合金氧化机理
高铌钛铝合金经过微波加热包埋渗硅后表面均为砖青色,渗硅试样在1000℃下循环氧化100h后表面没有明显的颜色变化,而光样在1000℃下氧化10h后表面为淡黄色,且有明显的增重,20h后就有明显的氧化剥落现象。#p#副标题#e#
图6高铌钛铝硅化物涂层在1000℃下氧化100h后的氧化动力学曲线
图6为高铌钛铝合金硅化物涂层1000℃下氧化100h的氧化增重曲线。由此可知氧化初期涂层氧化较快,氧化膜形成后,氧化趋势明显减缓,是因为氧化膜有很好阻隔氧化气氛的效果,符合特殊金属氧化的对数规律[13,14]。高铌钛铝合金渗硅后在表面获得主要是由NbSi2和TiSi2组成的硅化物涂层,在氧化初期Si和O2反应生成非晶态SiO2,在长时间高温氧化下可以转化成晶态SiO2。TiSi2在900℃便发生分解并氧化生成SiO2和TiO2[4]。由于NbSi2的存在使SiO2优先生成,并且由于涂层内侧富铝层的存在,也能够很好的抑制TiO2的优先生成,使得氧化膜主要成分为SiO2和Al2O3,所以涂层能够很好起到抗高温氧化的作用。
高铌钛铝合金微波渗硅后抗氧化机理如下:
(1) Si和Nb的选择性氧化作用
Si和Ti有着更好的亲和力,能在高铌钛铝合金基体表面形成TiSi2和NbSi2层,TiSi2和NbSi2有着良好的抗高温氧化性能,TiSi2在高于1000℃时主要的氧化产物为TiO2和SiO2[4],由于Si元素的加入降低了Ti离子的活度,并且Nb也抑制Ti向表面的扩散[15],所以Al就会被优先氧化,从而能在表面形成连续的Al2O3层,阻挡氧向基体内的扩散,并且Si氧化生成SiO2,SiO2在高温下为熔融的玻璃态,能够密封由于极少的Ti或Nb向外扩散而使Al2O3层形成的空洞,从而使Nb-TiAl基体在高温下能得到很好的保护。
(2) Al元素富集作用
硅化物下面有一层是富Al层,由于Al元素在此区域的相对集中,相对来说更容易形成连续致密的Al2O3层。即使由于在氧化的过程中,由于氧化生成的TiO2造成的涂层氧化膜的脱落,富Al层也能很好的阻挡基体的被进一步氧化。
4 结论
1) 通过在2.6KW微波加热包埋渗硅2h在高铌钛铝合金基体上制备出致密的硅化物涂层,整个涂层厚度约为30μm,涂层外侧大约15μm,主要物相是TiSi2和NbSi2,并有少量的Ti5Si3和Nb5Si3。
2) 硅化物涂层能显著地改善高铌钛铝合金的抗高温氧化和抗热循环剥落性能。这主要是因为硅化物涂层发生Si元素的选择性氧化作用,在高温下能生成熔融的玻璃态,有效阻止氧元素向基体内部扩散,提高Nb-TiAl基体的抗高温氧化性能;并且微波加热渗硅处理在硅化物层下面生成一层Al富集区,少量通过玻璃态二氧化硅层扩散过来的O使得Al能够优先被选择氧化,生成连续致密的Al2O3层,从而阻止高铌钛铝合金被进一步氧化,大大提高了高铌钛铝合金的抗高温氧化性能。
5 参考文献
[1] Y.W. KIM. New material by mechanical alloying. JOM, 1989, 41: 25-27.
[2] M YAMAGUCHI. High temperature intermetallics with particular emphasis on TiAl. Material Science and Technology. 1992, 8: 299-305.
[3]陈国良, 林均品.有序金属间化合物结构材料物理金属学基础. 北京, 冶金工业出版社, 1999.
[4] 张永刚,韩雅芳,陈国良等. 金属间化合物结构材料. 北京,国防工业出版社, 2001.
[5] 闫蕴琪,王文生,张文祺等,Nb-TiAl金属间化合物研究现状. 材料导报, 2000, 14(7): 15-18.
[6] 张宁, 林均品, 王艳丽等. 合金元素Y对高铌TiAl高温合金长期抗氧化性的影响. 航空材料学报, 2006, 26(6): 42-45.
[7] X.J. Zhang, Q. Li, S.Y. Zhao, et al. Improvement in the oxidation resistance of a γ-TiAl-based alloy by sol–gel derived Al2O3 film [J]. Applied Surface Science, 2008, 25(5): 1860-1864.
[8] M. Goral, L. Swadazba, G. Moskal, et al. Si-modified aluminide coatings deposited on Ti46Al7Nb alloy by slurry method. 2009, 17(11): 965-967.
[9] 肖伟豪, 张亮, 姜惠仁. Si对TiAl合金高温抗氧化性能的影响. 北京航空航天大学学报. 2006, 32(3): 365-368.
[10] 任家松. 新型Nb硅化物基超高温合金的氧化行为及其抗氧化涂层技术研究. 西安:西北工业大学, 2006.
[11] 李明, 宋力昕, 乐军等. 铌表面固体粉末包埋渗硅研究.无机材料学报,2005, 20(3): 764- 768.
[12] 乔彦强,郭喜平. Ti-Nb-Si基高温合金表面包埋Si-Cr共渗涂层的组织. 材料热处理学报, 2010, 31(3):125-131.
[13] 朱日彰,何业东,齐慧滨. 高温腐蚀及耐高温腐蚀材料. 上海,上海科学技术出版社, 1995.
[14] 朱日彰. 金属腐蚀学. 北京,冶金工业出版社, 1989.
[15] 王小舟. Ti3A1+11Nb合金的氧化及Nb的作用. 材料工程. 1997, 2: 22-25.
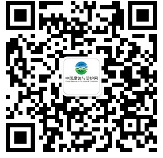
官方微信
《中国腐蚀与防护网电子期刊》征订启事
- 投稿联系:编辑部
- 电话:010-62313558-806
- 邮箱:fsfhzy666@163.com
- 中国腐蚀与防护网官方QQ群:140808414