在炼油工业加氢装置中,设备腐蚀一直影响着企业的正常生产。2015年4月19日,广西石化柴油加氢精制装置中的原料换热器发生内漏,原因为铵盐结晶导致换热管发生腐蚀减薄甚至穿孔。2016年1月24日,玉门石化柴油加氢改质装置中的分馏塔顶空冷器发生泄漏并着火,原因是空冷器管束外壁发生腐蚀减薄导致管束内物料泄漏,形成静电打火,引发火灾
2018年3月12日凌晨,四川石化重整装置预加氢系统中,反应进出料换热器(E-1004G)管层出口管线发生腐蚀泄漏。如图1所示,物料经过加氢精制反应器、脱氯反应器后,进入反应进出料换热器A~G管层。物料在E-1004G管层出口经过约200m长的管线后,进入反应产物空冷器、水冷器(水冷后温度为40℃、压力为2.6MPa)。
图1 重整装置预加氢系统流程简图
该流程中一共有三处注水点,E-1004A管层前为第一注水点,E-1004G管层出口为第二注水点,泄漏位置位于第二注水点下游5~6m,位于弯头与水平直管段焊缝连接附近的直管段上,距离焊缝20~30mm,如图2所示
图2 泄漏位置
泄漏点处的管线材料为20号碳钢,管内介质包括预加氢精制石脑油、H2、H2S、H2O、NH3。设计温度为116~125℃,实际操作温度为100℃,操作压力为2.82~2.84MPa。
1 失效分析
图3 穿孔附近直管段内壁宏观形貌
如图3所示,穿孔附近直管段内壁表面有腐蚀产物附着,局部有点蚀坑,蚀坑深度最大达0.2mm。腐蚀产物并不致密,表面有龟裂现象。基体腐蚀以均匀腐蚀减薄为主。
对管道材料进行化学分析,各项指标均符合GB/T 699-1999《优质碳素结构钢》中20号钢的要求,可见管道选材符合行业标准
在穿孔部位及远离穿孔部位分别取样,经预磨、抛光、刻蚀后,在显微镜下观察。如图4所示,穿孔部位及远离穿孔部位的组织均为铁素体和珠光体。
穿孔部位 远离穿孔部位
图4 穿孔部位和远离穿孔部位的显微组织
直管、弯头内壁都有腐蚀产物,分别对腐蚀产物的表面和下层进行EDS分析,发现直管和弯头内壁不同部位的腐蚀产物成分有所差异。直管内壁腐蚀产物层由铁、硫、氧组成,硫元素含量较高;弯头内壁腐蚀产物层主要由铁、氧、碳、硫组成。可见不同位置中都有硫元素。在腐蚀产物表层中,硫元素质量分数最高为9.43%。离穿孔位置越近,硫元素含量越低,这可能是由含硫物质被泄漏流体带走造成的。硫含量最高位置为穿孔附近管内壁腐蚀产物的下层,高达31.8%。腐蚀产物下层中有碳存在,是物料中的有机物残留。氧的存在是由于在停工置换、吹扫期间铁被氧化造成。
由以上分析结果可知,失效换热器管的化学成分和显微组织均符合行业标准,可以排除由材料性能下降引起失效的可能。泄漏管的腐蚀以均匀腐蚀和局部点蚀为主,腐蚀产物中都含有硫元素,可以推断腐蚀和硫相关。
四川石化原油来自哈萨克斯坦、俄罗斯、新疆、吐哈和长庆混合原油,含S、N、Cl及金属杂质较高,原油中还按一定比例掺混外购蜡油、外购原油、凝析油及装置回炼的轻、重污油,且混合比例不固定。常减压装置由于原油特性、装置性能及操作条件的限制,产出石脑油的硫含量超标,一般为600~800mg/kg。
石脑油中的有机化合物含有S、O、N、Cl等元素,在预加氢过程中均可与氢气发生反应,生成HCl、H2S、NH3、H2O等腐蚀性介质,其中硫醇、硫醚、环状硫化物、噻吩、苯并噻吩都能发生脱硫反应。H2S溶于水后发生电离,释放出的氢离子作为阴极去极化剂,会引起管道钢的均匀腐蚀。
溶解在水中的H2S具有较强的腐蚀性。其在水中发生离解反应释放出的氢离子是强去极化剂,在阴极得到电子。H2S水溶液呈酸性时,材料的腐蚀过程为:
Fe-2e- → Fe2+
2H++ 2e- → H2
Fe2+ + S2- → FeS
腐蚀产物硫化亚铁通常是一种有缺陷的结构,它与钢铁表面的黏结力差,易脱落,易氧化。
泄漏发生在预加氢反应进出料换热器E-1004G管层出口5~6m处,预加氢注水位置在E-1004G管层出口处,注水处与泄漏处距离仅5m左右。注入水温度为30~40℃,没有雾化。E-1004G出口至EA-1002A~D入口管线实际表面温度为95~105℃,是发生腐蚀泄漏的典型温度。这能解释E-1004G管层出口注水点附近直管段无明显减薄,注水点之后弯头附近直管减薄。
另外,由于注水管分布器损坏,除盐水雾化不好,除盐水进入管线后,短时间内全部集中在注入点一侧,不能迅速达到均匀分布的状态,因此在穿孔点附近,可能会存在压力大、流速大或者温差大的区域。在反应进出料换热器E-1004G管层出口处,高速流动的预加氢生成油与酸性水气液混合物在弯头处改变流向,冲击管线弯头及周围区域,导致管线弯头距离焊缝20~30mm处发生腐蚀穿孔泄漏,其他部位腐蚀减薄严重。另外,管线内壁形成的硫化物、氧化物层与管壁的结合较差,当流体强烈冲刷时,这些腐蚀层会被冲刷,腐蚀和冲刷两者不断协同作用下,使得弯头及其附近管壁不断减薄,直至穿孔泄漏。
2 应对措施
(1) 严格控制原料成分。由于公司油源紧张,且原油来源比较复杂,进料配比方式随机变化,根据现有情况增加原料指标分析的过程,合理调配进料。原油储备库各原油罐要脱水干净,增加原油混合时间。
(2) 调整注水方案。保证注水部位总注水量的25%为液态,注水总量应控制在物料总质量的3%~4%。由于重整进料量一般控制在180~230t/h,故注水量设定为6t/h。预加氢连续注水过少,会增加反应产物系统水溶液中的HCl和H2S含量,加重管道腐蚀,注水过多腐蚀层会被冲刷。
(3) 将原注水喷头更换成雾化喷头,确保混合均匀
(4) 增加预加氢系统中原料及反应出料的SClN分析频次。密切监控预加氢反应器预加氢脱氯器的运行情况,如发现异常,及时通知上游常减压装置调整反应器的温度压力流量等相关工艺条件。
(5) 增加循环氢中HClH2S 的分析频次。结合原料及反应出料,判断HClH2S含量升高的原因并采取措施。
(6) E-1004G管层出口管线管径由原设计DN(公称直径)250mm扩至300mm,以降低预加氢生成油物料流速。E-1004G管层出口管线共有7个弯头,将这些直角弯头更换成斜坡式弯头,以减缓腐蚀冲刷。
3 结论
反应进出料换热器E-1004G管层出口管段发生穿孔泄漏的主要原因是硫化氢引起的全面腐蚀和注水方式不合理。通过控制原材料成分、调整注水工艺、改进管道结构等方法,有效降低了设备腐蚀。到目前为止,设备正常运行690天,没有发生腐蚀泄漏。
免责声明:本网站所转载的文字、图片与视频资料版权归原创作者所有,如果涉及侵权,请第一时间联系本网删除。
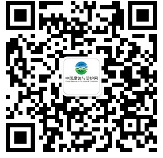
官方微信
《中国腐蚀与防护网电子期刊》征订启事
- 投稿联系:编辑部
- 电话:010-62316606-806
- 邮箱:fsfhzy666@163.com
- 中国腐蚀与防护网官方QQ群:140808414