高温炉管广泛应用于制氢转化炉和乙烯裂解炉,是石化装置的核心构件。高温炉管在其服役过程中的环境极其恶劣,长时间受到高温和应力的作用极易产生损伤,导致高温炉管的强度和稳定性急剧下降。蠕变损伤是高温炉管主要的损伤形式之一,随着服役时间的累积以及因操作不当而引起局部超温或因开停车而受到热应力的作用,容易产生蠕变开裂,当裂纹达到一定尺寸时,炉管随即破裂失效。单个的炉管意外破裂后,其泄漏出来的高温高压气体,往往会影响附近正在服役的其他炉管,造成连锁反应。炉内任何一根炉管的损坏,均将导致整个装置的紧急停车。除造成巨大的经济损失外,还会引发火灾、爆炸和人身伤亡等事故,安全隐患巨大。因此,开展高温炉管开裂的定期检测具有重要的意义。
考虑到高温炉管材质的特殊性以及服役工况的复杂性,高温炉管的在役检测多通过超声检测方法来实现,但常规直接接触式超声检测方法在检测高温炉管时,存在耦合效果较差,回波能量低,信噪比低等问题,不利于判断炉管内裂纹特征。基于此,中国特种设备检测研究院和北方华锦化学工业集团有限公司的检测人员设计开发了一套水耦合超声检测方案,以加工有不同深度人工刻槽的HP40材质转化炉用高温炉管为检测试件进行试验,并结合现场某乙烯裂解炉炉管检测数据,验证水耦合超声检测方案检测高温炉管的可行性。
1 高温炉管损伤机理及其检测方法
01 高温炉管的损伤机理和过程
高温炉管的常用材料是HK和HP系列耐热合金,常应用于制氢转化炉炉管、乙烯裂解炉炉管。高温炉管普遍服役于高温(800~1200℃)和高压(2.5~5MPa)的工况下,在高温时效后耐热合金的组织会发生变化,即使作用于材料的应力小于该温度下的材料的屈服极限,也会产生塑性变形,即产生蠕变,最终引起炉管性能的衰退。蠕变损伤是高温炉管主要的损伤形式之一,炉管蠕变取决于很多因素,主要受温度、时间和应力大小的影响,内部超温过热、内外壁温度梯度引起的热应力及开停炉的内应力是引起蠕变损伤的直接原因。
根据应变率与时间的变化关系,蠕变一般分为蠕变初级阶段、蠕变稳定阶段和蠕变加速阶段,在发展至蠕变稳定阶段时,炉管一般需要停止使用。金属材料在蠕变的过程中可以发生不同的断裂形式,按断裂时塑性变形量的大小,可以分为沿晶蠕变断裂、穿晶蠕变断裂和延缩性断裂,材料抗蠕变的能力通常以蠕变温度和蠕变强度来衡量。研究表明,炉管由于蠕变损伤而断裂的特征表现为在小应力和高温度作用下,在炉管金属材料中晶粒之间的晶界处首先萌生空洞,随着应力作用空洞不断变大、变多,通过聚集和连接在炉管内壁产生大量微小的裂纹,微小裂纹进一步扩展会形成宏观裂纹,并沿着炉管的径向和轴向扩展,最终导致炉管断裂失效。
以某炼油厂制氢转化炉炉管为例, 其外径为140mm,壁厚为13.5mm,工作压力2.05MPa,正常工作温度为800~900℃,超温时可达1100℃,材质为HP型(ZG4Cr25Ni35Nb),工作介质为天然气和水蒸气。该转化炉于2009年12月投用,共有炉管176根,设计寿命为10万小时,累计运行4万小时后,于2016年1月连续发生两次爆管事故,两根炉管开裂的宏观形貌和局部放大如图1所示,可以看到炉管的开裂均为纵向开裂,开裂部位已蠕胀鼓包,纵向主裂纹边缘区及其前端分布有多条粗细、长短不均的小裂纹。
(a) 宏观形貌 (b) 局部放大
图1 辽宁某炼油厂制氢转化炉炉管开裂形貌
对宏观裂纹前端的炉管截面进行解剖分析,发现裂纹主要萌生于炉管内表层并沿壁厚方向向外壁扩展,部分裂纹已贯穿,如图2所示。
图2 辽宁某炼油厂制氢转化炉炉管开裂解剖
02 检测方法
考虑到材质的特殊性以及服役工况的复杂性,高温炉管内壁裂纹的常规检测方法存在以下难点:
1. 考虑到炉管材质为非铁磁性且裂纹由内壁产生,因此不适合采用磁粉、渗透、涡流等表面检测方法;
2. 考虑到炉管内部填充了催化剂,因此不适合采用射线检测方法;
3. 高温炉管的在役检测多通过超声检测方法来实现,但是炉管的外表面多呈杨梅粒子状态,且直径较小曲率较大,耦合效果较差,回波能量低,信噪比低,因此常规直接接触式超声检测方法在检测时不利于判断炉管内裂纹特征。
基于上述情况,为克服常规直接接触式超声检测方法声耦合效果差等问题,检测人员提出了一种水耦合超声检测方案,实现炉管蠕变裂纹的检测。
2 水耦合超声检测方案设计
本方案采用一对“超声波发射/接收探头”对高温炉管进行水耦合穿透法检测,如图3所示。将探头用水径向(相对于炉管轴线)耦合在炉管上,发射探头发出的超声波波束进入水层中并在水/钢界面发生反射和折射,折射的声波以一定的角度在炉管中传播并在钢/水界面再次发生反射和折射,折射的声波再次通过水层最终被接收探头接收。当炉管内无缺陷时,发射探头发出的超声波经炉管内传播后,直接被接收探头接收,接收的能量如图4a所示;当发射探头发出的超声波遇到炉管内裂纹的阻碍时,接收探头接收到的超声波能量会降低甚至完全消失,如图4b所示。因此,通过对比接收探头接收到的能量大小,可以初步判断炉管内是否存在裂纹,以及裂纹在壁厚方向的高度。
图3 水耦合超声检测方案设计
(a) 无缺陷阻碍时的接收能量 (b) 有缺陷阻碍时的接收能量
图4 超声波能量图
本设计方案中,实现炉管的水耦合超声检测需要解决声波入射角度的计算、探头的固定、充水耦合等问题,超声波信号的发射、接收、模数转换、显示、数据分析模块可以利用现有的超声检测仪器实现。下面以管外径R=109mm,管壁厚T=10mm,管内径r=89mm 炉管为例,给出具体实施方案。
探头固定装置(瓦块)的设计
设计的探头固定装置为“瓦块”,用来保证超声波能以一定的角度和路径在炉管中传播。瓦块弧面内径为109mm,与炉管外径一致,瓦块中部钻有两“探头孔”,用以固定超声探头,孔内径略大于探头外径。“探头孔”的加工要求对称性良好,以免造成耦合不佳或入射角偏移。瓦块中水层的深度需要满足探头聚焦的要求。瓦块的结构设计和实物如图5所示。
(a)瓦块结构设计图
(b)瓦块实物图
图5 探头固定装置(瓦块)
进/出水装置的设计
为了将声波能量从超声探头传递至炉管内部,实际检测时需要在探头和炉管之间充水作为耦合剂。由于高温炉管一般为立式安装,水在重力的作用下向下流失,会影响甚至完全阻碍超声能量的传播。
为克服上述困难,将进水口设计在瓦块的底部,出水口设计在瓦块中部“探头孔”的两侧。正常工作时,水在高处重力的作用下,自瓦块底部流入,从瓦块中部“探头孔”流出,并与炉管之间形成耦合水层。当水压较低时,水会在瓦块底部和侧面流出,此时的耦合效果较差;当水压足够时,水会在瓦块的底部、侧面和顶部同时溢出,此时的耦合效果能满足现场检测的要求。
(a)示意图
(b)实物图
图6 进/出水装置
聚焦深度与入射角度的计算
根据声波振动方向与传播方向的关系可以把声波分为纵波和横波。由于横波无法在液体介质(水)中传播,因此入射波选用纵波,传播过程中的纵波,在两种不同介质的界面处会发生一些相关的变化,如反射、折射和透射等,并伴随着声波的波形转换,如图7所示。
图7 声波的入射与折射
根据斯奈尔定律可知,入射纵波与法线的夹角,与折射纵波以及折射横波与法线的夹角满足以下公式:
为避免第二介质(炉管)中纵波与横波的互相干扰,纵波入射角度应选在第一临界角和第二临界角之间,使得炉管中只存在横波传播,不存在纵波传播。
已知炉管外径R=109mm,内径r=89mm,超声波在水中的声速CL1=1480m/s,超声波在炉管中的横波声速CS2=3230m/s,聚焦深度(超声波主声束距离炉管内壁的距离)δ=5mm,则可计算得出纵波入射角度αL为24.59°。
3 试验验证
采用双通道数字超声波检测仪,检测试件采用刻有人工刻槽的HP40材质的转化炉用高温炉管,炉管规格为φ109mm×10mm,炉管内壁刻有5个人工纵向矩形刻槽,刻槽宽度为0.2mm,长度为20mm,深度分别为1.0、2.0、4.0、6.0、8.0mm,聚焦深度设计为5mm,刻槽示意图和刻槽炉管试件水耦合超声检测装置如图8所示。
(a) 炉管刻槽示意图 (b) 炉管试件水耦合超声检测装置
图8 刻槽炉管试件及检测装置
水耦合试验
进水压力的大小会影响超声传感器与炉管之间水耦合的效果,为验证进水压力与耦合效果之间的关系,分两步进行试验:
首先,不使用进/出水装置,将炉管、瓦块和探头完全浸没于水槽中,对炉管无缺陷部位进行检测,如图9a所示,得到的波形信号可以分为四部分,如图9b所示。第一部分为“始波信号”,出现在屏幕左部,其特征是幅值极高,且由于检测增益较大的缘故,其占宽较大。第二部分为“噪声信号”,出现在屏幕中部,其特征是幅值很低且波形杂乱无规律;根据超声波传感器“一发一收”的设计方案,该部位对应声波在炉管中传播的声程,此处尚未接收到超声信号,但容易受到仪器板卡、信号线等外部噪声的干扰。第三部分为管束内横波以最短路径传播至接收探头的“直通波”,是屏幕右部的第一个峰值信号;其特征是速度最快、能量最为集中,且峰值的大小与缺陷的关系最为密切。第四部分为管束内反射波、折射波、变形波等“迟到信号”,出现在屏幕右部;其特征是波形幅值无明显规律,但均滞后于“直通波”。由工程经验可知,此种耦合状态下的“直通波”信号最强,此时将其调整为80%满屏高并保持增益等检测参数不变。
(a)浸没示意图
(b)波形信号
图9 浸没状态下检测试验
然后,使用进/出水装置,将炉管立于地面,瓦块侧贴于炉管表面,同时将水箱置于瓦块上方不同的高度,利用重力供水耦合,如图10a所示。以水位H=6m为例,得到的“直通波”波幅高度只有40%满屏高,如图10b所示。此时,调节水位H并记录“直通波”波幅高度与不同水位之间的关系,结果发现:当水位在0.2~2m之间时,耦合效果与完全浸没时一致,检测效果较好;当水位超出或者低于这个范围时,检测结果均会受到影响。
(a)立式示意图
(b)波形信号(水位6m)
图10 立式水耦合状态下检测试验
人工缺陷检测试验
连接检测系统,将检测水位固定为1m,设置无缺陷部位“直通波”为100%满屏高并对5个人工纵向矩形刻槽进行检测,可以看出“始波信号”和“噪声信号”均无明显变化,“直通波”随着刻槽深度的增加而降低,“迟到信号”无明显规律。
对接收探头“直通波”信号的波幅高度进行均值统计,得到超声波信号穿透不同深度的人工刻槽缺陷后的剩余能量和 “直通波”信号波幅高度衰减曲线,如图11所示,可以看出“直通波”信号的剩余能量随人工缺陷的深度的增加而递减。根据“直通波”信号幅值的高低可推断炉管蠕变裂纹的大致深度。
图11 接收探头超声信号波幅高度衰减曲线
4 现场检测应用
为了进一步验证水耦合超声检测方案的应用性能,对某乙烯裂解炉炉管进行现场检测试验。根据现场炉管规格(φ114mm×14mm)和聚焦深度(7mm)加工探头固定装置(瓦块)并配套电驱动装置后,将“直通波”设置为100%满屏高进行快速扫查,如图12所示。
(a) 瓦块及电驱动装置
(b) 信号采集系统
图12 现场检测试验
现场检测发现,多数炉管的“直通波”在80%满屏高以上波动,但某根炉管的某处“直通波”衰减至40%满屏高,判定为疑似缺陷。对该部位割管后进行PT检测,发现内壁为两条裂纹,长度分别为20mm和7mm,均平行于轴线方向,如图13所示。
图13 疑似缺陷的PT验证结果
从现场试验数据可以看出,利用设计的水耦合超声检测方案能够实现炉管内壁裂纹的检测。
结论
为克服常规直接接触式超声检测方法声耦合效果差等问题,设计开发了一套水耦合超声检测方案,采用一对“穿透法”对高温炉管进行水耦合超声波透射法检测。以加工有不同深度人工刻槽的HP40材质转化炉用高温炉管为检测试件进行试验,试验得到了检测信号随裂纹深度的衰减规律,根据接收探头“直通波”信号幅值的高低可初步推断炉管管壁内蠕变裂纹的大致深度。结合现场某乙烯裂解炉炉管检测数据,进一步验证了水耦合超声检测方案的应用性能。
免责声明:本网站所转载的文字、图片与视频资料版权归原创作者所有,如果涉及侵权,请第一时间联系本网删除。
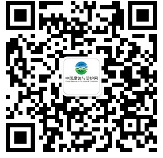
官方微信
《中国腐蚀与防护网电子期刊》征订启事
- 投稿联系:编辑部
- 电话:010-62316606-806
- 邮箱:fsfhzy666@163.com
- 中国腐蚀与防护网官方QQ群:140808414