石化装置生产过程中存在并产生许多腐蚀性的介质,介质的种类、化学成分、浓度、pH 值、杂质、水分和含氧量都是造成腐蚀的外在原因。介质流动速度愈快,愈易腐蚀,因为介质在流动过程中会冲刷保护膜,产生旋涡、湍流、空泡,引起严重的冲击磨损和空泡腐蚀。
另外选材不当,如果设备表面接触腐蚀介质,而设备本身又不耐腐蚀,就会产生表面腐蚀,表面越粗糙,越易腐蚀,其现象是泄漏、早期磨损、破坏、发声等。表面均匀腐蚀有成膜和无膜两种形态,无膜的腐蚀很危险,腐蚀过程以一定的速度进行,这主要是选材错误造成的。
缺乏防腐措施或施工质量低劣等,都为腐蚀破坏提供了环境。环境不同,选材不同。在设备的生产过程中往往不能做到兼顾选材和环境腐蚀的一致性,温度、浓度、压力不同,选材不同、腐蚀情况各异,而且施工过程中把关不严、施工质量低劣,腐蚀问题不可避免。
操作中的超温、超压,设备管理不完善,思想不重视,也是产生腐蚀破坏的原因之一。通常情况下,介质的温度越高,压力越高,腐蚀越快,因为腐蚀是一种化学反应,每升温10℃,腐蚀速度增加1~3 倍。
腐蚀检查方案
所谓腐蚀检查,就是利用各种仪器工具和分析方法,确定材料在工艺介质环境中的腐蚀速度,及时为工程技术人员反馈设备腐蚀信息,从而采取有效措施减缓腐蚀,避免腐蚀事故的发生。装置大修腐蚀检查就是针对装置的具体情况制定腐蚀检查方案,在装置停工大修时,组织专门的队伍,根据腐蚀检查方案,采用宏观检查和其他有效的检查手段,对设备、管道进行腐蚀形貌、腐蚀状态的检查,据此分析其腐蚀机理、计算其腐蚀速率、确定破坏程度。
01 装置大修腐蚀检查的目的
了解该装置在连续运行一个周期后的设备损坏和腐蚀情况。
对本周期来该装置所采取的设备和工艺防腐措施的有效性进行评价。
验证装置RBI风险评价结果的正确性,为RBI评价指导压力容器及压力管道提供可靠验证。
为指导下一周期该装置采取的设备和工艺防腐措施提供依据。
02 装置大修腐蚀检查工作内容
一、腐蚀检查原始资料收集
装置工艺原则流程图、装置操作规程、设备、管道明细表及单体图、装置大修计划、压力容器压力管道检验方案、历史测厚记录、历史检修检验记录、历史化验记录等(包括:原油评价、分析数据,电脱盐分析数据,三顶冷凝水分析数据等)。
大修工程计划(最好有各施工单位负责人电话)
装置操作规程
设备单体图
设备资料台帐
上个生产周期装置原料评价及分析
装置标定报告
历史腐蚀档案
竣工资料(包括安装资料)
历年检修或抢修记录
DCS半年内历史记录及超压、超温报警记录
半年内采样分析数据和最近装置标定报告
定点测厚及在线腐蚀监测数据
二、腐蚀检查方案制定
根据装置实际情况(工艺流程、工艺参数、设备特点),和RBI风险评价结果确定装置不同部位的腐蚀介质;可能的腐蚀机理;可能的腐蚀机理的失效形态和检测方法。从而确定腐蚀调查重点和检验策略。
三、现场腐蚀检查
依照腐蚀调查方案开展现场腐蚀检查;
分析装置设备腐蚀状态;
腐蚀机理初步分析;
装置防腐建议报告;
编写腐蚀检查现场报告。
四、腐蚀检查全面报告
装置简介;
装置历年腐蚀状况分析及上周期装置运行情况及分析;
车间大修设备检查情况;
大修内容(主要是开盖容器、修理、改造的设备管道的完成情况);
压力容器、压力管道检验数据分析;
装置大修测厚数据分析;
装置大修无损检测数据分析;
设备、管道腐蚀检查明细表;
典型腐蚀案例分析及腐蚀机理分析报告;
腐蚀在线监测选点、类型方案;
定点测厚方案分析;
在役检测、检验方案分析;
取样点设置及化验方案分析;
装置总体腐蚀状况分析;
工艺防腐现状分析及优化方案;
设备防腐现状分析及优化方案;
五、装置安全状况评估
就是装置在现有的材质条件和现有的工艺防腐措施之下,腐蚀速率是否在允许的范围之内。若腐蚀速率超过允许范围可以采用哪些措施来降低腐蚀速率。
六、装置薄弱环节评估
根据中国石化股份有限公司的有关规定,实际腐蚀速率大于0.25mm/a就说明此处选材等级偏低,需要进行材质升级。腐蚀速率超标失效可能性偏大的部位就是装置的薄弱环节。一般应该制定下一周期的材质升级方案。
七、工艺适应性评估
在石化厂会经常出现原料性质改变,工艺条件改变,特别是在每一次装置大修都会有一些工艺改造的部分,这些情况到底会对设备、管道造成哪些影响,是否会出现新的问题,需要采取哪些措施来加以预防。
八、其他
包括为完成上述报告,同期各项化验、仿真、试验和活性硫分析等工作。
免责声明:本网站所转载的文字、图片与视频资料版权归原创作者所有,如果涉及侵权,请第一时间联系本网删除。
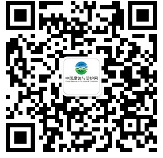
官方微信
《中国腐蚀与防护网电子期刊》征订启事
- 投稿联系:编辑部
- 电话:010-62316606-806
- 邮箱:fsfhzy666@163.com
- 中国腐蚀与防护网官方QQ群:140808414