摘要
利用电化学阻抗谱和电化学噪声技术对比研究了国产镀锌钢板在盐水和淡水中的腐蚀行为。结果表明,镀锌钢在两种水溶液中的腐蚀均可分为3个阶段,不同阶段表现出完全不同的电化学特征,镀锌钢在盐水中的腐蚀速率明显高于其在淡水中的腐蚀速率,其在盐水中的腐蚀产物呈棒状或片层状,对基体不具有保护性,而在淡水中的腐蚀产物形态呈规则的球状,对基体具有明显的保护作用。
关键词: 镀锌钢; 水环境; 电化学阻抗谱; 电化学噪声
镀锌因成本低、效率高、耐蚀性能优异,是钢铁腐蚀防护采用的最普遍的技术手段,同时镀锌钢被广泛应用于石油化工、交通运输、输变电力、航空航天、船舶等民用和国防的各个领域。镀锌层主要通过两种方式对钢基体起到保护作用[1],一方面镀锌层与钢基体之间以冶金的方式连接在一起,具有较高的结合强度,可以隔绝钢基体与外部腐蚀介质的接触,起到物理隔绝作用,另一方面,锌的电位较低,镀锌层以牺牲阳极的方式对钢基体起到电化学防护的作用。镀锌钢在不同的环境下服役时,表现出不同的腐蚀特点,研究最多的为大气环境[2-11],王向东等[9]研究了国产镀锌钢在北京、青岛、武汉、江津、广州等我国几个典型大气环境下的腐蚀行为,研究表明镀锌钢在青岛地区的腐蚀最为严重,其次是江津,腐蚀最轻的为武汉,造成该结果的主要原因为大气环境中的SO2等污染物和环境湿度的差异。同时,在湿度较高的环境中,Cl-的存在会加速镀锌钢的腐蚀[10,11]。另一种关注度较高的环境为海水环境或盐水环境[12-14],宁丽君等[12]利用电化学阻抗谱 (EIS) 技术研究了镀锌钝化钢板在不同浓度NaCl溶液中的腐蚀反应过程,结果表明,钝化的镀锌钢板腐蚀过程主要分为3个阶段:第一阶段钝化膜的溶解,主要受Cl-浓度的影响;第二阶段镀锌层的阴极保护阶段,受Cl-浓度和溶解氧含量共同控制;第三阶段腐蚀产物膜的保护阶段。
综上所述,当前对于镀锌钢的腐蚀行为主要集中在大气环境和盐水环境,对于淡水环境中的镀锌钢的腐蚀研究较少,随着海水淡化技术的发展,舰船以及岛礁上管路对海水和淡水的传输,使得镀锌钢面临着不同的水环境。因此,研究镀锌钢在盐水和淡水环境下的腐蚀行为,对于海水淡化设备、水的安全传输具有重要的意义。本文选用了一种国产镀锌钢板,利用电化学阻抗谱和电化学噪声技术对比研究了镀锌钢在盐水和淡水两种水环境下的腐蚀动力学过程,通过电化学信号的解析结合形貌观察,探讨了镀锌钢在两种不同水环境下的腐蚀机理。
1 实验方法
本工作选取的实验对象是国产的热浸镀锌钢板,利用SiC砂纸依次将样品的截面打磨至2000#,抛光后用4%(质量分数) 硝酸酒精擦拭3~5 s,所得截面的显微组织结构如图1所示,镀锌层的厚度约为65 μm,包括η-Zn、ζ-FeZn13、δ-FeZn10和Г-Fe3Zn10等子层[1,15]。实验选取的淡水为沈阳市的自来水,盐水为3.5%的氯化钠溶液,由去离子水和分析纯的NaCl配制得到。
图1 国产热浸镀锌钢板截面显微组织
利用VersaSTAT V3F电化学工作站对浸泡不同时间的镀锌钢板进行了开路电位 (OCP) 和EIS测试,其中待测样品为工作电极,铂片为对电极,饱和甘汞电极为参比电极。电化学阻抗谱测试前先进行10 min的开路电位扫描,待电位稳定后进行测试,频率测试范围105~10-2 Hz,正弦波扰动振幅为10 mV。采用PguTouch电化学工作站对镀锌钢板腐蚀过程中的电化学噪声进行了监测,其中两个相同的镀锌钢板样品为工作电极,饱和甘汞电极为参比电极,数据的采样频率为4 Hz,利用五次多项式拟合的方法对电化学噪声的直流偏差进行了去除,利用Hilbert-Huang分析方法对浸泡不同时间后的电流噪声数据进行了解析。利用MIRA 3型扫描电镜 (SEM) 对在不同水环境中浸泡720 h后镀锌钢板的显微形貌进行了观察。
2 结果与讨论
2.1 镀锌钢在不同水环境中的电化学阻抗谱特征
国产镀锌钢在盐水和淡水中开路电位随浸泡时间的变化如图2所示。可以看出,在720 h的实验周期内,国产镀锌钢在淡水中的开路电位主要分布在-1.02~-0.98 V范围内,在盐水中的开路电位主要分布在-1.06~-1.02 V范围内。无论是处于哪种水环境中,与浸泡前相比,镀锌钢经过720 h的浸泡后,开路电位都有所升高,但整个浸泡过程中,镀锌钢在淡水中的开路电位始终高于其在盐水中的开路电位。
图2 国产镀锌钢在盐水和淡水中开路电位随浸泡时间的变化
国产镀锌钢在盐水中电化学阻抗谱随浸泡时间的变化如图3所示。根据阻抗谱在不同时间阶段所表现出的特征,将镀锌钢在盐水中的腐蚀历程分成3个阶段,在0~144 h阶段,Nyquist图显示 (图3a) 镀锌钢表现出高频容抗和低频容抗两个时间常数的特征,且容抗弧的半径随浸泡时间的增加不断减小,Bode图显示 (图3c) 高频的相位角随着浸泡时间的增加逐渐降低,低频的阻抗模值随着浸泡时间的增加不断降低 (图3b),由4 h的1.3×104 Ω·cm2降低到144 h的1.7×103 Ω·cm2,低频阻抗模值降低了约1个数量级,预示着镀锌钢的耐腐蚀性能不断降低。在144~600 h阶段,Nyquist图 (图3d) 和Bode图 (图3f) 显示镀锌钢在此阶段表现出3个时间常数的特征,高频和中频的容抗以及低频的扩散过程,低频阻抗模值随着浸泡时间的增加表现出先增加后降低的趋势 (图3e)。在600~720 h阶段,镀锌钢的电化学阻抗谱特征与第一阶段相似,再次表现出高频容抗和低频容抗的特征 (图3g),扩散过程消失,同时低频阻抗模值有所增加,由600 h的1.2×103 Ω·cm2增加到720 h的4.4×103 Ω·cm2。
图3 国产镀锌钢在盐水中浸泡不同时间的电化学阻抗谱
国产镀锌钢在淡水中电化学阻抗谱随浸泡时间的变化如图4所示。根据阻抗谱在不同时间阶段所表现出的特征,将其在淡水中的腐蚀历程同样分成3个阶段,在0~144 h阶段,Nyquist图显示 (图4a) 镀锌钢表现出单一容抗弧的特征,且容抗弧的半径随浸泡时间的增加不断增大,Bode图显示 (图4e) 相位角的特征峰随着浸泡时间的增加有向两个特征峰转变的趋势,低频的阻抗模值随着浸泡时间的增加不断增加 (图4b),由0 h的8.8×104 Ω·cm2增加到144 h的6.4×105Ω·cm2,低频阻抗模值增加近1个数量级,预示着镀锌钢的耐腐蚀性能不断增加,这与其在盐水中的变化趋势刚好相反。在144~336 h阶段,Nyquist图 (图4d) 和Bode图 (图4f) 显示镀锌钢由第一阶段的一个时间常数转变为两个时间常数的特征,即高频容抗和低频容抗,容抗弧的半径先增加后降低,低频阻抗模值随着浸泡时间的增加表现出先增加后降低的趋势 (图4e),降低的幅度不是很大。在336~720 h阶段,镀锌钢在此阶段的电化学阻抗谱特征与第二阶段相似,均表现出高频容抗和低频容抗的特征 (图4i),同时容抗弧的半径和低频阻抗模稍有增加 (图4g和h)。
图4 国产镀锌钢在淡水中浸泡不同时间的电化学阻抗谱
根据以上描述可知,国产镀锌钢板在盐水和淡水中的腐蚀过程虽然均可分成3个阶段,但却表现出完全不同的电化学特征,镀锌钢在两种溶液中10-2 Hz低频阻抗模值随浸泡时间的变化如图5所示。从图中可以看出以下几点:第一,从开始的性能表现来看,镀锌钢在淡水中的腐蚀速度明显低于其在盐水中的腐蚀速度,一个明显的特征是浸泡初期镀锌钢在淡水中的阻抗模值比盐水中高出近1个数量级;第二,从变化趋势上来看,镀锌钢在盐水中的阻抗模值在整个浸泡周期内由1.3×104 Ω·cm2降低到4.4×103 Ω·cm2,而淡水中的阻抗模值在整个浸泡周期内由8.2×104 Ω·cm2增加到1.1×106 Ω·cm2,尤其是在0~144 h阶段,镀锌钢在盐水中的防护性能快速恶化,而在淡水的腐蚀速率却越来越低。
图5 国产镀锌钢在两种水溶液中浸泡720 h电化学阻抗谱低频模值随时间的变化
2.2 镀锌钢在不同水环境中的电化学噪声特征
为了更深入地了解镀锌钢在两种不同水环境中的电化学性质,记录了镀锌钢在不同腐蚀阶段的电化学噪声信号,并对其中的电流信号进行了Hilbert-Huang解析。镀锌钢在盐水中不同时间点的电化学噪声原始信号及其去除直流偏差后的电流噪声信号如图6所示,电流噪声在去除直流偏差后均表现为围绕0上下波动的信号,直接体现了表面镀锌层的溶解状态。可以看出,镀锌钢在腐蚀过程的第一阶段 (4 h,图6a和b),电流噪声暂态峰表现为快速上升和快速下降,波动范围在-1×10-9 A·cm-2至1×10-9 A·cm-2,随着浸泡时间的增加 (48 h,图6c和d),相同时间电流暂态峰的数量减少,预示着电流噪声暂态峰的频率有所降低,但波动幅度明显增加了1倍,增加至-2×10-9~2×10-9 A·cm-2,说明镀锌钢表面局部腐蚀的信号增强。随着腐蚀过程进入到第二阶段 (240 h,图6e和f),电流噪声暂态峰的频率和幅度持续增加,最为明显的是信号波动幅度由第一阶段48 h的-2×10-9~2×10-9 A·cm-2增加至-5×10-9~5×10-9 A·cm-2,预示着镀锌钢表面腐蚀程度的进一步加强。腐蚀过程进入到第三阶段 (600 h,图6g和h),电流暂态峰的幅度稍有降低,但暂态峰的频率依然较高。
图6 国产镀锌钢在盐水中浸泡不同时间的电化学噪声信号
利用Hilbert-Huang变换对镀锌钢不同腐蚀阶段的电流噪声进行了解析,如图7所示,考虑到镀锌层是通过牺牲阳极的方式对基体提供电化学保护,将镀锌钢电流噪声中的高频信号即腐蚀的快过程理解为锌层局部的快速溶解和破坏,低频信号即腐蚀的慢过程定义为由于表面镀锌层的全面溶解所造成的均匀腐蚀。从中可以看出,镀锌钢在腐蚀的第一阶段,低频腐蚀事件即腐蚀的慢过程,全面的均匀腐蚀能量占比相对较高 (图7a),随着时间的增加,低频腐蚀事件在整个时间内占据主导地位 (图7b),全面腐蚀增强;进入到第二阶段,腐蚀较为均匀,低频和高频腐蚀事件所占比例相差不大,腐蚀进入到一个稳定阶段 (图7c);最后的第三阶段,低频腐蚀事件仍然占据主导地位,镀锌钢表面继续维持着全面腐蚀状态 (图7d)。
图7 国产镀锌钢在盐水中浸泡不同时间的电流噪声Hilbert-Huang谱
镀锌钢在淡水中不同腐蚀阶段的电化学噪声原始信号及其去除直流偏差后的电流噪声信号如图8所示。从中可以看出,在淡水环境下,镀锌钢的电位噪声和电流噪声在腐蚀的每个阶段均表现为同步上升的特征 (图8a,c,e和g),且在每个时间节点,电流噪声的暂态峰都表现出了较高的频率 (图8b,d,f和h),随着时间的增加,电流暂态峰的波动幅度不断增大,在腐蚀过程的第一阶段,由4 h的-5×10-11~5×10-11 A·cm-2增加至48 h的-1×10-10~1×10-10 A·cm-2;到了腐蚀过程的第二阶段,电流暂态峰的波动幅度进一步增加至240 h的-1.5×10-10~1.5×10-10 A·cm-2;腐蚀过程的第三阶段,电流暂态峰的波动幅度持续增加至600 h的-2.0×10-10~2.0×10-10 A·cm-2。
图8 国产镀锌钢在淡水中浸泡不同时间的电化学噪声信号
腐蚀过程每个阶段电流噪声的Hilbert-Huang谱图如图9所示。从中可以看出,腐蚀过程的第一个阶段低频腐蚀事件和高频腐蚀事件所占的比例较为平均 (图9a),随着时间的增加,低频腐蚀事件所占的比重逐渐增加 (图9b和c),全面腐蚀增强,最后阶段,低频和高频腐蚀时间依然保持着相对平均的状态 (图9d)。
图9 国产镀锌钢在淡水中浸泡不同时间的电流噪声Hilbert-Huang谱图
2.3 镀锌钢在不同水环境中的显微形貌特征
根据以上对镀锌钢在盐水和淡水中电化学阻抗谱和电化学噪声的分析,可以看到镀锌钢在两种溶液中表现出了完全不同的电化学特征。镀锌钢在以上两种溶液中浸泡720 h后的微观形貌如图10所示。可以看出,镀锌钢在两种溶液中呈现出完全不同的腐蚀形态,在盐水溶液中主要是棒状和片层状腐蚀产物的堆积 (图10a),而在淡水中主要是球状产物规律密集的排布 (图10b)。结合以上电化学数据的分析和微观形貌的观察可以得知,镀锌钢在盐水和淡水中表现出完全不同的腐蚀机理,在盐水中主要是疏松的腐蚀产物不断形成的腐蚀过程,具体表现为,镀锌钢在腐蚀的第一阶段 (0~144 h) 低频阻抗模值不断降低,由最开始的1.3×104 Ω。cm2降低到144 h的4.4×103 Ω·cm2,降低了约1个数量级 (图5a),同时电流噪声信号显示,低频腐蚀事件占据主导,镀锌钢主要发生了全面的均匀腐蚀 (图7a和b);到了腐蚀过程的第二阶段,低频阻抗模值出现了明显的波动,整体趋势上先增加后降低 (图5a),同时低频和高频腐蚀事件所占比例较为平均 (图7c),这可能与表面疏松腐蚀产物的生成和脱落有关;到了第三阶段,由于腐蚀产物膜的保护作用,低频阻抗模值稍有增加 (图5a),达到最初值的三分之一,同时均匀腐蚀的倾向性增加 (图7d),最终表面形成了棒状和片层状腐蚀产物的堆积。
图10 镀锌钢在盐水和淡水中浸泡720 h的微观形貌
与盐水环境完全不同,镀锌钢在淡水中的腐蚀是致密的保护性膜层不断生成的过程,从整个腐蚀过程三个阶段来看,镀锌钢在720 h的浸泡周期内,低频阻抗模值整体呈现波动式上升的趋势,由0 h的8.2×104 Ω·cm2增加到720 h的1.1×106 Ω·cm2 (图5b),低频模值增加了十几倍,同时电流噪声信号的波动频率一直较高 (图8),低频和高频腐蚀事件所占的比例较为平均 (图9),最终形成了致密性保护膜层的覆盖。
3 结论
(1) 镀锌钢在盐水和淡水中的腐蚀均可分为3个阶段,两种水环境中,镀锌钢在不同腐蚀阶段的电化学阻抗谱和电化学噪声表现出完全不同的电化学特征,最大的不同表现为:镀锌钢在腐蚀的第一阶段,其在盐水溶液中表现出双容抗弧的特征,低频阻抗模值迅速下降,低频腐蚀事件占据主导地位,而在淡水溶液中表现出单容抗弧的特征,低频阻抗模值快速上升,低频和高频腐蚀事件所占的比例相当。
(2) 镀锌钢在盐水溶液中的腐蚀速率明显高于其在淡水中的腐蚀速率,镀锌钢在盐水中的腐蚀本质上是疏松的腐蚀产物不断堆积、脱落的形成过程,而在淡水中则是具有明显保护性的致密化腐蚀产物的形成过程。
参考文献
[1]
Wang Y B.
Investigation on interfacial microstructures and properties of hot-dip galvanizing coating
[D]. Xi'an: Northwestern Polytechnical University, 2016
[本文引用: 2]
王友彬.
热浸镀锌镀层界面结构与性能研究
[D]. 西安: 西北工业大学, 2016
[本文引用: 2]
[2]
Cui Z Y, Li X G, Xiao K, et al.
Corrosion behavior of field-exposed zinc in a tropical marine atmosphere
[J]. Corrosion, 2014, 70: 731
[本文引用: 1]
[3]
De La Fuente D, Castaño J G, Morcillo M.
Long-term atmospheric corrosion of zinc
[J]. Corros. Sci., 2007, 49: 1420
[4]
Meng Y, Liu L J, Zhang D W, et al.
Initial formation of corrosion products on pure zinc in saline solution
[J]. Bioact. Mater., 2019, 4: 87
[5]
Chung S C, Lin A S, Chang J R, et al.
EXAFS study of atmospheric corrosion products on zinc at the initial stage
[J]. Corros. Sci., 2000, 42: 1599
[6]
Yang H Y, Ding G Q, Huang G Q, et al.
Corrosion behavior of galvanized steels in different atmospheric environments
[J]. Corros. Prot., 2017, 38: 369
杨海洋, 丁国清, 黄桂桥等.
镀锌钢在不同大气环境中的腐蚀行为
[J]. 腐蚀与防护, 2017, 38: 369
[7]
Zhong X Z, Wang Z Y, Liu Y J, et al.
Corrosion behavior of galvanized steel in simulated ocean atmosphere
[J]. J. Chin. Soc. Corros. Prot., 2015, 35: 151
钟西舟, 王振尧, 刘艳洁等.
镀锌钢在模拟海洋大气环境下的腐蚀行为
[J]. 中国腐蚀与防护学报, 2015, 35: 151
[8]
Yadav A P, Katayama H, Noda K, et al.
Effect of Fe-Zn alloy layer on the corrosion resistance of galvanized steel in chloride containing environments
[J]. Corros. Sci., 2007, 49: 3716
[9]
Wang X D, Gao L Y, Chen X P, et al.
Corrosion resistance of domestic galvanized steel sheet
[J]. Mater. Prot., 2002, 35(10): 12
[本文引用: 1]
王向东, 高令远, 陈小平等.
国产镀锌钢板的耐蚀性研究
[J]. 材料保护, 2002, 35(10): 12
[本文引用: 1]
[10]
Granese S L, Rosales B M, Fernandez A.
Behavior of Zn in atmospheres containing sulfur dioxide and chloride ions
[A]. 11th International Corroion Congress [C]. Florence: International Corrosion Council, 2009
[本文引用: 1]
[11]
Svensson J E, Johansson L G.
A Laboratory study of the initial stages of the atmospheric corrosion of zinc in the presence of NaCl; influence of SO2 and NO2
[J]. Corros. Sci., 1993, 34: 721
[本文引用: 2]
[12]
Ning L J, Du A L, Xu L K, et al.
Corrosion behavior of galvanized steel in NaCl solution
[J]. Corros. Sci. Prot. Technol., 2012, 24: 291
[本文引用: 2]
宁丽君, 杜爱玲, 许立坤等.
镀锌层在NaCl溶液中的腐蚀行为研究
[J]. 腐蚀科学与防护技术, 2012, 24: 291
[本文引用: 2]
[13]
Liu S, Sun H Y, Fan H J, et al.
Progress of research on corrosion behavior of galvanized steel
[J]. Mater. Prot., 2012, 45(12): 42
刘栓, 孙虎元, 范汇吉等.
镀锌钢腐蚀行为的研究进展
[J]. 材料保护, 2012, 45(12): 42
[14]
Liu S, Sun H Y, Sun L J, et al.
Effects of Zn(OH)2 on corrosion behavior of galvanized steel in seawater
[J]. Mater. Eng., 2013, (8): 60
[本文引用: 1]
刘栓, 孙虎元, 孙立娟等.
海水中Zn(OH)2对镀锌钢腐蚀行为的影响
[J]. 材料工程, 2013, (8): 60
[本文引用: 1]
[15]
Marder A R.
The metallurgy of zinc-coated steel
[J]. Prog. Mater. Sci., 2000, 45: 191
[本文引用: 1]
免责声明:本网站所转载的文字、图片与视频资料版权归原创作者所有,如果涉及侵权,请第一时间联系本网删除。
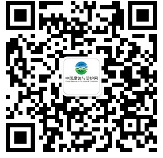
官方微信
《中国腐蚀与防护网电子期刊》征订启事
- 投稿联系:编辑部
- 电话:010-62316606-806
- 邮箱:fsfhzy666@163.com
- 中国腐蚀与防护网官方QQ群:140808414