通讯作者信息
曹学强
曹学强,1964年生。1994年在中国科学院长春应用化学研究所获无机化学专业理学博士学位,2004年在德国鲁尔-波鸿大学(Ruhr Univ.-Bochum)获机械制造专业工学博士学位。2002.01-2015.09在中国科学院长春应用化学研究所工作,二级研究员,2008年获国家杰青,2001年获中科院百人计划。2015.09迄今在武汉理工大学硅酸盐建筑材料国家重点实验室工作,首席教授。
主持科技部863计划、国家自然科学基金等十余项国家级项目。主要研究方向是热障涂层新材料和新结构,出版专著2部,发表论文230余篇,其中3篇论文的SCI被引次数在国际同研究领域的8000余篇论文中排名前1%。主要荣誉:2008年吉林省科学技术进步一等奖,2013吉林省科学技术一等奖,2012国防科技进步二等奖,4项成果已在国家重点装备上应用。
作者说
热障涂层表面腐蚀斑点的形成机理研究
——为热障涂层质量保驾护航
曹学强 武汉理工大学
热障涂层(Thermal Barrier Coatings,TBCs)一直是国防工业的核心技术之一,决定着我国航空发动机、燃气轮机的使用寿命,多年来,难以打破技术封锁的壁垒。进入21世纪后,TBCs技术日臻成熟并广泛应用,偶尔在公开场合也能看到实物,TBCs技术从秘密研究开始走向市场。从2007年第12届北京航展到2010年第8届珠海航展,美国GE公司在中国多次展示了CF34-10航空发动机,可以看到其燃烧室和叶片都制备了TBCs。俄罗斯SU-30和SU-35以及美国F-16、F-22和F-35战斗机的尾喷管都使用了TBCs。高推重比发动机将大量采用以TBCs为代表的先进热防护技术,必须具有非常高的可考性。在航空发动机上使用的TBCs,必须经受飞机数千次起降落过程中的温度急剧变化;在地面燃气轮机上使用的TBCs,尽管工作温度比航空发动机低,但使用时间很长,必须能连续工作3万小时以上。
纳米YSZ涂层(nYSZ)在我国使用很广泛。在实验室的环境中,nYSZ的性能往往很好,但在发动机实际工况条件下,寿命远低于预期值而且难以预测。我们在研究过程中发现,nYSZ可能存在腐蚀风险,即涂层表面出现带颜色的斑点或脱落。航空、航天部门的产品都出现过类似问题,有些产品甚至出现了涂层穿孔的现象。针对此问题,我们研究团队收集了100余个国内外单位制备的TBCs涂层样品,走访了多家单位,采用体式显微镜、扫描电镜(SEM)和激光烧蚀-耦合等离子-质谱(LA-ICP-MS)方法证实涂层表面的斑点来源于金属基体或金属粘结层的腐蚀,YSZ中残余Cl是腐蚀的根源。我国YSZ粉末的行业或国家标准缺乏Cl含量指标,为涂层的质量控制埋下了隐患。
编者说…
《热喷涂技术》期刊上的大论文
《热喷涂技术》编辑部酉琪
第一次见到武汉理工大学的曹学强老师是在洛阳召开的2018年热喷涂技术研讨会上,那高亢有力的声音一直回荡在我的耳边,“只做了十几个点的LA-ICP-MS不能说明腐蚀斑点的形成机理,那我就做3300个点的激光面扫描才具有代表性”。他这种对学术研究一丝不苟的精神深深地感染着我。TBCs腐蚀斑点是一个很常见的现象,但是获得关注很少,却影响着热障涂层的质量,曹老师抓住这一点进行深入的研究,在《热喷涂技术》上发表的论文“热障涂层表面腐蚀斑点的形成机理研究”,详细介绍了斑点的特殊分析方法、产生机理以及控制方法,指出YSZ中残余Cl-是腐蚀的根源,对于提高TBCs产品的质量有重要意义,以期为叶片涂层的实际生产应用提供指导。
《热喷涂技术》2019年第一期,曹老师非常痛快的答应我们的约稿,而且早早的提交了长达18页的全部研究数据。研究数据是科学研究者最宝贝的财富,曹老师选择了我们正是他对我们的信任以及期待更多的同行看到热喷涂行业共同进步。技术的更新换代离不开这些科研工作者的支持,我们强烈期望更多的同行加入到我们《热喷涂技术》期刊来,支持我们国家热喷涂技术的进步,推动我们热喷涂技术的繁荣发展。
正文
摘要 热障涂层(Thermal Barrier Coatings,TBCs)已广泛应用于航空、航天和地面燃机等发动机热端部件和武器装备的防护。TBCs应用的基底材料种类繁多,常见的是镍基高温合金,还有碳钢、铜合金、铝合金、镁合金、复合材料等。氧化钇稳定化的氧化锆(Yttria Stabilized Zirconia,YSZ)涂层的常见颜色是白色和灰色,颜色决定于氧空位含量。TBCs产品的表面可能出现腐蚀斑点现象,特别是在高温潮湿环境下,腐蚀斑点出现机会多、现象更明显。腐蚀斑点的颜色取决于基底或粘结层材料,碳钢和铜合金产生棕色腐蚀斑点,镍基高温合金产生绿色腐蚀斑点,钴基高温合金产生浅红色腐蚀斑点,铝合金、镁合金、树脂则不会出现腐蚀斑点。在镍基高温合金基底表面,依次用大气等离子喷涂(Atmospheric Plasma Spraying,APS)方法制备钴基高温合金粘结层(Bond Coat,BC)和纳米YSZ(n-YSZ)涂层,在自然环境下贮存一段时间后,部分产品的表面出现了大量腐蚀斑点。采用体式显微镜、扫描电镜(Scanning Electron Microscopy,SEM)和激光烧蚀-耦合等离子-质谱(Laser Ablation-Inductively Coupled Plasma-Mass Spectroscopy,LA-ICP-MS)方法证明,腐蚀斑点来源于BC的腐蚀产物。BC的主要成分是Ni、Co和Cr,在涂层制备过程中分别被氧化生成氧化物NiO、CoO和CrO。YSZ粉末中含有大量残余的原料ZrOCl和YCl,在潮湿空气中水解产生HCl,将BC的氧化物溶解,便出现了Ni(翠绿色)、Co(浅红色)和Cr(墨绿色)特有的颜色。
关键词 热障涂层;氧化钇稳定化的氧化锆;腐蚀斑点
0 前言
TBCs是无机涂层中的一个重要分支,起源于20世纪四十年代末五十年代初。为了提高航空发动机的推力和燃料的热效率,必须提高燃料的燃烧温度,发动机热端部件的温度也相应提高。涡轮叶片由镍基高温合金构成,其软化温度提高到了1589 K、已慢慢接近其熔点即1672 K。在过去的四十年里,已经发展了几代高温合金,使得提高燃气轮机涡轮前进气温度成为可能。但是,受高温合金的熔点、表面腐蚀和应力断裂等限制,涡轮前进气温度的提高越来越困难。而且,用于高性能发动机冷却的空气量是有限的。在叶片表面制备陶瓷层即TBCs,可以将叶片高温合金与高温火焰隔离,降低叶片温度,从而保护叶片,提高发动机效率。为了提高陶瓷层与金属基底之间的热膨胀匹配性和结合强度并提高金属基底的抗氧化能力,在制备陶瓷层之前,在金属基底表面制备一金属层即粘结层(BC)。因此,TBCs一般包括粘结层和陶瓷层。
20世纪90年代,国内外广泛开展了纳米YSZ(n-YSZ)热障涂层研究。用低功率APS方法将n-YSZ粉末喷涂成涂层,涂层内部还保留30%左右的半熔化或未熔化的纳米颗粒,因此涂层还保留较多纳米颗粒的特性。很多学者的研究结果表明,n-YSZ粉末制备的涂层,其寿命达到常规微米粉末制备涂层的2~3倍,其它性能也有明显提高。近十年来,我国航空、航天、舰船等领域的发动机已广泛使用n-YSZ涂层。但是,在n-YSZ涂层的应用过程中,出现了未预料到的现象,即涂层表面容易出现腐蚀斑点,高温潮湿天气出现腐蚀斑点的概率远高于其它季节,腐蚀斑点的颜色取决于基底或BC材料的腐蚀产物颜色,常见的有绿色、浅红色、棕色。
2011年至今,本文作者收集了国内外100余个n-YSZ粉末、涂层和块体样品,包括国际知名公司的产品如Inframat、Praxair、Sigma-Aldrich、Wieland Dental、Saint-Gobain、Sulzer-Metco和Tosoh,国内的样品都来源于航空和航天部门。涂层出现腐蚀斑点现象,主要是春、夏高温多雨季节,地点有沈阳、北京、贵阳和西安;有时候涂层外观正常,但经过400℃~600℃煅烧后,便出现密密麻麻的腐蚀斑点;腐蚀斑点严重的涂层样品,出现点状脱落现象即“烂透了”。涂层的腐蚀斑点现象一直困惑着航空和航天发动机部门。经过详细研究,本文作者证实,腐蚀斑点现象是由涂层内部的杂质Cl-引起,高浓度的Cl-导致BC或基底被腐蚀,便出现了BC或基底金属离子的颜色。如果使用有机封孔剂对涂层进行封孔,封孔剂含有残余的催化剂HCl,会加速腐蚀斑点的形成。本文的目的是揭示TBCs的腐蚀斑点形成机理,提出控制方法,对于提高涂层产品的质量有重要意义。
1 试验
1.1 材料和药品
本文中的所有n-YSZ粉末和涂层样品都来源于航天或航空部门,未作任何处理,其中产生严重腐蚀斑点现象的粉末及其对应的涂层,其基本信息是:
(1)n-YSZ粉末:通过ZrOCl + YCl + NH·HO共沉淀法合成、水热处理,最后经过1150℃~1200℃煅烧;晶粒度61 nm,单斜相(M)含量≤1 mol%,残余YO含量0.0034 wt%,Cl含量0.053 wt%;
(2)n-YSZ涂层:APS方法制备,基底为镍基高温合金(火焰筒,尾喷管,火焰稳定器等),BC为钴基高温合金;表面喷涂透明有机封孔剂。
分析纯NiCl6HO、CoCl6HO和CrCl6HO与精密pH试纸由国药集团化学试剂有限公司生产。
1.2 试验过程
(1)APS涂层对沙尘的吸附沙土取自于内蒙古阿拉善左旗051基地,经过洗涤、过筛除去粒度100 m以上的粗砂等杂质,600℃煅烧除去生物质,最后得到干净的沙土。取5 g干净的沙土倒入50 ml去离子水中,超声分散5 min,静置5 min,用滴管取上层清液滴加到涂层样品表面,自然干燥;涂层样品用树脂固定,经过切割、抛光后,用电子扫描显微镜(Scanning Electron Microscopy,SEM,Quanta FEG 450)分析涂层的截面,观察沙尘是否能钻入APS涂层的孔隙中。用激光闪烁法分析表明,沙土清液中的颗粒在30 m以下,与空气中的沙尘粒度范围相近。
(2)Ni、Co和Cr在n-YSZ粉末中的扩散称取适量NiCl6HO、CoCl6HO和CrCl6HO,分别加入适量去离子水中,配制浓度1.0 M的Ni、Co和Cr溶液,以及三种离子的混合溶液。在4支25 ml的酸式滴定管内,分别灌满质量相同的n-YSZ粉末,酸式滴定管直立固定;将1.0 M的Ni、Co和Cr溶液,以及三种离子的混合溶液分别倒入4支酸式滴定管内,每隔60s记录颜色的扩散距离,计算Ni(翠绿色)、Co(浅红色)和Cr(墨绿色)在n-YSZ粉末中的相对扩散速度。相同浓度的Ni和Co溶液混合,颜色是棕红色;相同浓度的Ni、Co和Cr溶液混合,颜色是墨绿色。
(3)LA-ICP-MS分析腐蚀斑点LA-ICP-MS分析在中国地质大学(武汉)生物地质与环境地质国家重点实验室进行,测试仪器为LA(GeoLab 193nm)-ICP-MS(Agilent 7500A),工作参数见表1。在显微镜下找到n-YSZ涂层出现腐蚀斑点的位置,然后用LA-ICP-MS方法分析。
表1 LA-ICP-MS仪器工作参数
(4)n-YSZ粉末中可溶性杂质的提取将200 g的n-YSZ粉末用去离子水浸泡,在90℃保温3 h,滤纸过滤,重复浸泡3次;收集浸泡后的所有水溶液,在90℃蒸发浓缩成50 ml溶液,然后高速离心分离出溶液中的沉淀物,收集离心分离后的溶液,100℃烘干,在烧杯底部可以看到无色透明的结晶状固体粉末,用于其他分析。
n-YSZ粉末中的杂质Cl-含量分析在钢研纳克检测技术有限公司完成。
(5)n-YSZ涂层腐蚀斑点形成过程的模拟通过高温高压加速湿热的方法模拟涂层腐蚀斑点的形成过程。在不锈钢高压容器(聚四氟乙烯PTFE内胆)底部加入容器容积50 vol%的去离子水,容器上面放置一个PTFE筛网,将n-YSZ涂层放置在筛网上;将容器盖拧紧,放置在80℃烘箱里保温10天,容器内部压强约0.5 MPa;容器冷却后,打开容器盖,取出涂层样品吹干,观察涂层的表面变化。
(6)n-YSZ涂层截面腐蚀斑点的观察涂层的腐蚀斑点在成分上与涂层整体相差很小,用SEM无法分辨出腐蚀斑点,用平面光学显微镜也很难观察到涂层截面的腐蚀斑点。为了观察涂层截面腐蚀斑点的起源,将涂层用树脂固定、切割、抛光,用体式显微镜(Olympus SZX-7-2)观察截面形貌和颜色,照明光源从样品的侧面入射到涂层,原理见图1。在观察涂层截面腐蚀斑点时,光源不能垂直照射样品。与照明光源的强度相比,涂层截面腐蚀斑点的颜色很浅,垂直照射将无法分辨出腐蚀斑点的颜色。
图1 涂层截面腐蚀斑点的观察方法
(7)抗霉菌性能测试抗霉菌试验在沈阳航电检测技术有限公司完成,试验周期28天,执行标准GJB 150.10-86。
2 结果与分析
2.1 n-YSZ涂层表面的腐蚀斑点现象
在沈阳地区存放66个月的n-YSZ涂层样品全部出现腐蚀斑点现象;在沈阳生产然后在北京保存了6个月以内的涂层产品,有10%以上出现了肉眼明显可见、密密麻麻的腐蚀斑点。图2是n-YSZ涂层的外观,在沈阳地区制备涂层、喷涂封孔剂后在北京地区存放了6个月以内。本文作者收集了一些航天、航空部门的涂层样品,出现腐蚀斑点概率比较大的季节是春季和夏季,高温高湿环境。图2中的腐蚀斑点现象有如下3种情况:
(1)如图2a,原涂层表面为白色,表面没有喷涂封孔剂,外观没有腐蚀斑点。但是,经过400℃保温1 h后,涂层出现了密密麻麻的棕色腐蚀斑点,腐蚀斑点直径在1 mm左右;
(2)如图2b,原涂层表面没有喷涂封孔剂,腐蚀斑点中心的颜色较深、边缘颜色浅,表现出明显的扩散痕迹,腐蚀斑点直径1~2 mm;
(3)如图2c,原涂层表面喷涂了封孔剂,腐蚀斑点呈双圆圈现象,内圆圈颜色深些,为绿色,直径1~2 mm;外圆圈为浅红色,直径3~5 mm。双圆圈的方向很有规律,即基本上沿着火焰筒轴向,从右边向左边呈水滴状分布,有明显的液体喷射状。在喷涂封孔剂时,火焰筒垂直放置,估计右侧端朝上、左侧端朝下,封孔剂液滴从上往下流淌,腐蚀斑点分布表现出明显的液体腐蚀现象。
图2 n-YSZ涂层的腐蚀斑点现象:(a)火焰稳定器,原涂层没有腐蚀斑点现象,经过400℃保温1 h后出现密密麻麻的黑点;(b)火焰筒,涂层表面没有喷涂封孔剂,在沈阳地区制备、北京地区自然环境下短期存放,圆圈内标记的是腐蚀斑点;(c)火焰筒,涂层表面喷涂了封孔剂,在沈阳地区制备、北京地区自然环境下短期存放,双圆圈标记的是同一个腐蚀斑点出现内外两层颜色,箭头标记了腐蚀斑点双圆圈现象的分布规律
另外,3个涂层样品(制备工艺与图2a中的涂层相同,表面没有喷涂封孔剂)经过不同的热处理后,表面出现不同的腐蚀斑点现象,如图3。
由于图3中的第5号样品腐蚀斑点现象最明显,特别是标记A的腐蚀斑点,本文主要以该样品为研究对象,分析腐蚀斑点的形成机理。
图3 热处理产生的腐蚀斑点现象:1号样品经过2次400℃1 h热处理;4号样品没有热处理;5号样品经过1次400℃1 h热处理,其中标记A是5号样品表面最明显的腐蚀斑点之一
2.2 腐蚀斑点分析
2.2.1 定性分析
5号涂层经过切割、树脂固化、金刚石液抛光制备金相试样后,利用体式显微镜观察了涂层的表面(图3)和截面形貌(图4),特别注意腐蚀斑点的观察。
图4 第5号涂层样品截面形貌体式光学照片,箭头指向是腐蚀斑点最明显的地方,其中标记B是5号样品表面最明显的腐蚀斑点之一
从图4可以看到,5号样品的截面有一些陶瓷层污染很明显的斑点,特别是标记B的斑点,可以看到污染物从底部的金属层一直穿透到陶瓷层表面,而且靠近金属层的部位颜色更明显,表明污染物是从金属底层向外扩散造成的。为了判断污染物的成分,对5号样品的截面和表面分别做SEM-EDS。表面分析选取图3中5号样品的腐蚀斑点A,截面分析选取图4中腐蚀斑点B,这两个腐蚀斑点都是最明显的。
将图4中腐蚀斑点B的附近做SEM分析。SEM无法观察到污染腐蚀斑点的存在,腐蚀斑点附近的形貌与其它部位完全相同。腐蚀斑点B对应的金属层,有一颗大而未完全熔化的金属颗粒。用EDS面扫描的方式分析腐蚀斑点B附近的污染物成分,结果见图5。在图5中的金属与陶瓷之间的界面,用虚线区分;Cr、Ni、Co元素含量异常的部位用虚线框1~7标记。由于陶瓷层腐蚀斑点污染物含量低,在EDS面扫描图片中的现象不太明显。但是,经过EDS面扫描图片与电子图像相比较,能够明显观察到腐蚀斑点污染物的存在。如图5中的标记5~7,金属层与陶瓷层的界面靠近陶瓷层的区域,有浓度较高的Cr、Co、Ni存在。非常有意义的是,区域1~4已远离金属层,但仍然能观察到Cr、Co、Ni,而且从金属层向陶瓷层的方向上,污染物浓度逐渐降低。腐蚀斑点污染物聚集在陶瓷层内部的多孔区,证明污染物是通过陶瓷层的孔隙从金属层向陶瓷层方向扩散产生的。
根据EDS分析结果,可以定性判断,涂层表面的棕色腐蚀斑点产生的过程是:金属层CoNiCr被腐蚀,腐蚀产物向陶瓷层表面扩散。
图5 5号样品腐蚀斑点B附近的截面SEM-EDS分析,数字1~7分别代表陶瓷层内部的7个区域,这7个区域中的污染物含量不同
2.2.2 定量分析
采用LA-ICP-MS方法对涂层的表面进行定点定量分析。涂层表面腐蚀斑点和空白区域分析见图6,元素含量分析结果见表2,选择一个代表性的腐蚀斑点和空白区域的分析图谱,分别见图7a(腐蚀斑点)和图7b(空白区域)。该仪器采用的标样为NIST 610硅酸盐熔融玻璃,涂层中各种元素的含量是与标样的比值。
图6 第5号样品表面腐蚀斑点的LA-ICP-MS分析:(a)分析过程;(b)腐蚀斑点的激光烧蚀点,标记C;(c)空白区域的激光烧蚀点,标记D
表2 第5号样品表面LA-ICP-MS分析结果
图7 涂层表面腐蚀斑点(a,对应图6中标记C和表2中的序号3)和空白(b,对应图6中标记D和表2中的序号7)剥蚀元素瞬时信号图
分析表2和图7的测试结果,可以判断:(1)空白处的Ni、Co、Cr含量都小于1 ppm,而腐蚀斑点上的Ni、Co、Cr含量比空白处高一个数量级,说明Ni、Co、Cr集中出现在腐蚀斑点上;(2)随着激光脉冲次数的增加(烧蚀深度增加),Ni、Co、Cr含量呈现增大的趋势,说明腐蚀斑点处,越深则三种元素的含量越高,证明这三种元素都是从样品的底部往外渗透出来的;(3)4个腐蚀斑点的元素含量平均值为:Cr=12.64 ppm,Co=210.63 ppm,Ni=224.11 ppm,Co/Ni=0.94,Cr/Ni=0.0564。在CoNiCrAlY金属底层中的元素含量分别是Ni=33 wt%,Co=35 wt%,Cr=25 wt%,Co/Ni=1.06,Cr/Ni=0.76。
在第5号涂层样品表面随意选取一块1.85 mm2.35 mm的面积进行LA-ICP-MS面扫描分析,观察表面是否出现元素集中的现象。激光斑的直径是0.04 mm,1.85 mm2.35 mm的面积包括2720余个激光烧蚀点,分析结果见图8。用红色虚线将肉眼可见、比较明显的腐蚀斑点标记出来,肉眼观察不太明显的区域无法标记。从图8可以看到,在测试区域内,Co、Ni、Cr元素含量集中,元素含量的分布区域形状与肉眼观察的腐蚀斑点形状基本一致;Ca、Mg、Al、Si的分布没有规律,完全是随机分布。
图8 第5号涂层样品表面LA-ICP-MS元素扫描分析
根据LA-ICP-MS元素分析结果,可以得到如下结论:
(1)腐蚀斑点是金属层元素Ni、Co、Cr含量集中的地方,从YSZ陶瓷涂层的表面到金属层都含有大量这3种元素;在截面、表面分析中,并没有观察到任何金属颗粒存在;
(2)Ca、Mg、Si、Al是ZrO原料的主要杂质,来源于原料矿物锆英砂ZrSiO,其分布没有任何规律,没有在斑点集中出现的现象,说明不是从空气中吸附的。
矿物杂质主要是硅铝酸盐即石英砂(SiO,FeO,CaO,MgO,AlO,NaO,KO)。氧化锆ZrO的制备过程是:600~900℃锆英砂ZrSiO4用强碱NaOH+CaO溶解,然后加入强酸HCl将ZrO2浸出:
ZrSiO+NaOH+CaO→NaO-ZrO+CaO-NaO-SiO+ HO (1)
NaO-ZrO+HCl→ZrOCl+HO (2)
因此,氧化锆产品中常见的杂质是SiO、CaO、MgO、AlO和NaO。
2.3 热处理对腐蚀斑点的影响
将涂层样品1、4、5在电炉中、400℃~1000℃分别保温1 h,表面变化见图9。在600℃及以下分别保温1 h后,腐蚀斑点颜色加深;在800℃及以上,颜色逐渐变浅,但不会消失。在600℃以下,金属腐蚀产物被加热、分解成氧化物(CoNiCr的氧化物),所以颜色加深;在更高的温度下,这些腐蚀产物向YSZ的晶格中扩散,所以颜色变浅,而且温度越高则扩散越快、颜色越浅。前期有关n-YSZ涂层的研究表明,YSZ晶格中的离子面扩散(速度很慢)与体扩散(扩散速度快)的转折点(即Taman温度)在850℃~900℃之间。所以,在800℃以上,腐蚀斑点的颜色会变浅,但不会消失。
图9 涂层样品1、4、5经过不同温度加热1 h后的表面变化
2.4 n-YSZ粉末中可溶性提取物的分析
200 g的n-YSZ粉末中获得提取物13.2 mg,其水溶液显酸,如图10。提取物主要成分是Cl、Y和Zr,其中Cl含量为0.053 wt%。这些杂质都是原材料ZrOCl2和YCl3的残余物,呈强酸性。ZrOCl2和YCl3溶解在水中会水解产生强酸性,水解过程的离子反应方程式如下:
ZrO + 2HO ZrO(OH) + 2H (3)
Y + 3HO Y(OH) + 3H (4)
2.5 腐蚀斑点的形成机理
2.5.1 BC被腐蚀
图10 n-YSZ粉末的提取物:(a)底部白色粉末;(b)提取物pH值;(c)去离子水pH值
以上分析结果表明,n-YSZ涂层表面的腐蚀斑点是由于BC被涂层里面残余的Cl-腐蚀造成的,其机理如下:
(1)在APS过程中,BC颗粒被氧化,表面生成氧化物CoO、NiO和CrO;
(2)在n-YSZ的合成过程中,残余的原料ZrOCl和YCl没有冲洗干净;在APS过程中被带入了涂层;
(3)在高温潮湿的环境中,残余物ZrOCl和YCl发生水解产生HCl,HCl与BC的氧化物发生反应生成可溶性氯化物:
CoO + 2HCl = CoCl + HO (5)
NiO + 2HCl = NiCl + HO (6)
CrO + 6HCl = 2CrCl + 3HO (7)
(4)BC的可溶性腐蚀产物沿着涂层内部的孔隙向外扩散,在涂层的表面产生腐蚀斑点。由于Co、Ni和Cr在n-YSZ涂层中的扩散速度不同,导致腐蚀产物的颜色发生分离,分离的程度与涂层的表面状态有关。
为了验证涂层腐蚀斑点形成机理,本文进行了如下再现性试验。根据色谱柱中的颜色变化,计算得到Co、Ni和Cr的相对扩散速度如下(L/mm,t/min):
NiCl:L = 238.6 + 3.25t (8)
CoCl:L = 227.8 + 3.06t (9)
CrCl:L = 217.0 + 2.72t (10)
图11 NiCl、CoCl、CrCl以及NiCl+CoCl+CrCl混合液在n-YSZ纳米粉中的相对扩散速度,从左至右的色谱柱分别为NiCl、CoCl、CrCl以及NiCl+CoCl+CrCl混合液
3种离子的扩散速度大小顺序是:Ni≥Co> Cr;如果以Ni的扩散速度为1,则另外两种离子的相对扩散速度分别是:Ni = 1,Co = 0.94,Cr = 0.84。
金属粉末中的元素质量百分含量Co=35 wt%,Ni=33 wt%,Cr=25 wt%,如果不存在选择性腐蚀现象,那么腐蚀产物中的元素含量之比应该为Co/Ni=350.94/331=0.996,Cr/Ni=250.84/331=0.636。在表2中有关腐蚀斑点的LA-ICP-MS分析结果,腐蚀斑点中的Co/Ni含量比为0.94,与理论值0.996很接近,说明BC中Ni和Co的腐蚀速度相似。根据BC中Cr/Ni含量之比,如果Cr与Ni和Co同时被腐蚀,那么腐蚀产物中Cr/Ni含量之比应该为0.636。但是,LA-ICP-MS分析腐蚀斑点中的Cr/Ni含量之比为0.0564,说明BC中Cr的腐蚀程度远低于Co和Ni。在不锈钢和高温合金中,都加入了大量Cr,因为Cr的抗腐蚀能力很强。
n-YSZ粉末对Ni(+2价,离子半径0.072 nm)、Co(+2价,离子半径0.074 nm)和Cr(+3价,离子半径0.064 nm)的吸附能力很强。这3种离子中,Cr的离子半径最小、价态最高,与n-YSZ之间的吸附作用最强;Ni和Co的价态和离子半径都相近,所以与n-YSZ之间的吸附作用相近。将NiCl+CoCl+CrCl混合液(浓度都是1 M)滴入色谱柱,先流出来的是棕红色溶液(NiCl+CoCl),最后才是墨绿色的CrCl溶液。
Ni、Co和Cr在n-YSZ粉末中的吸附能力和速度的不同,可以解释图2c中火焰筒的腐蚀斑点“双圆圈”现象:火焰筒内表面制备涂层,再用封孔剂密封;在潮湿的环境中,涂层吸收空气中的水蒸气,涂层内部的残余原料ZrOCl和YCl发生水解产生HCl,封孔剂也含有大量残余的HCl(合成该种封孔剂时采用HCl作为催化剂,封孔剂经过碱中和与洗涤);HCl将BC中的氧化物腐蚀生成NiCl、CoCl、CrCl并向外扩散,由于受到表面封孔剂的阻挡,腐蚀物到达涂层表面后只能向四周扩散;由于NiCl、CoCl、CrCl在n-YSZ涂层中的扩散速度不同,导致腐蚀斑点出现颜色分布不均匀的现象,即出现水渍状,腐蚀斑点的内圈含CrCl比较多,而腐蚀斑点的外圈含NiCl+CoCl比较多。如果涂层表面没有喷涂封孔剂(图2b),从里向外扩散的腐蚀产物可以畅通地向外扩散,到达表面就被蒸发干燥,不会出现双圆圈现象,腐蚀斑点的中心颜色深、外围颜色浅。如图2a,如果涂层存放时间短,腐蚀产物还没有到达涂层表面,则表面看不到腐蚀斑点,但在高温下煅烧,腐蚀产物NiCl、CoCl、CrCl被分解生成对应的氧化物,腐蚀斑点不会出现明显扩散的迹象,基本都是黑圆点。
2.5.2 其他机理
(1)霉菌生长
霉菌生长需要营养即碳水化合物。n-YSZ涂层没有C、H元素,霉菌没有生长条件。研究结果表明,n-YSZ涂层和封孔剂(添加了杀菌剂)的抗霉菌能力都是1级。另外,从外观上看,霉菌与n-YSZ涂层的腐蚀斑点形貌完全不同。霉菌的种类很多,形貌各异,但共同的特点是“长毛”现象,与n-YSZ涂层的腐蚀斑点形貌、颜色和出现的位置完全不同。喷涂封孔剂后,火焰筒的腐蚀斑点出现在封孔剂的下面而不是表面,腐蚀斑点形状是双圆圈水渍状。
(2)涂层吸附水垢
水垢俗称水锈,一般呈白色或棕色,主要成分有CaCO、MgCO、CaSO、MgSO、CaCl和MgCl等。水垢的棕色来源于Fe离子。有关自来水中的水垢含量,我国现行国家标准为450 mg/L(450 ppm)。将50.0 g自来水蒸干后,得到水垢14.2 mg,即水垢的含量为284 mg/L(284 ppm)。自来水中的水垢,在其熔点(CaCO=825℃,MgCO=990℃,分解)以下,其饱和蒸汽压极低、可以完全忽略不计。因此,在自来水的蒸发过程中,水垢将保留在容器中而不会随水蒸气蒸发,蒸馏水的水垢含量<10 ppm。
水垢中的几种主要成分的折射率是:水=1.33,CaCO=1.658,MgCO=1.534,CaCl=1.52,MgCl=1.559,CaCOMgCO=1.503~1.682,CaSO.2HO=1.521,MgSO.HO =1.52~1.58。从这些折射率数据看,水垢主要成分的折射率相差<10%,不足以使水垢成分产生色差。因此,水垢中的成分,用肉眼是无法分辨的,更不可能由白色转变成棕色。
图13 APS YSZ涂层的显微结构(a)和孔隙率(b)
图13是APS YSZ涂层的显微结构和孔隙率测量结果。涂层的孔隙率一般在10~20 vol%之间,其中大孔(尺寸>0.3 m)的含量占总孔隙率的30%,处于开放或半开放状态,与空气有自由交换;小孔(尺寸<0.3 m)的含量占总孔隙率的70%,处于密闭状态,与空气没有交换。假设陶瓷涂层的厚度为0.3 mm、密度为5 g/cm、涂层中的大孔全部吸满液态水,计算得到涂层的吸水量为涂层质量的6%,涂层所吸收的水垢量极限值为6%10 ppm=0.6 ppm。但是,从图8中分析的Ca、Mg、Si含量来看,这3种元素的含量已超过1000 ppm,远远超过涂层吸收空气中水蒸气所形成的水垢量。而且,在夏天最潮湿的环境中(沈阳和北京地区≤35℃,相对湿度RH≤90%),涂层在空气中吸收的水蒸气也不是液态。因此,涂层从空气中吸收的水垢可以忽略不计。涂层中测试出来的Ca、Mg、Si都来源于ZrO的原材料即锆英砂ZrSiO而不是空气中的水垢。
(3)涂层吸附沙尘
如图13所示,APS制备的YSZ涂层,占总孔隙率70%的是尺寸在0.001~0.3 m之间的微孔,属于密闭状态,与大气没有交换;只有0.3~10 m之间的大孔是开放或半开放,与大气有交换。用压汞法测试涂层的孔隙率时,需要逐步加大压强才能将汞压入微孔中,最大到400 MPa。
图14 沙尘在n-YSZ涂层表面的吸附:(a)涂层表面(带封孔剂)沙尘浆料;(b)涂层表面(无封孔剂)沙尘浆料
图15 沙尘在涂层表面的分布情况:(a,b)涂层带封孔剂;(c,d)涂层无封孔剂
根据文献报道,在沙尘天气情况下,空气中沙尘粒度的分布是:粒度10~50 μm占49.02%,5~10 μm占21.75%,<5 μm的占27.14%,平均粒径为13.57 μm。因此,空气中的沙尘中,绝大部分的粒度远远大于APS涂层的孔隙,也就是说,绝大部分沙尘无法钻入APS涂层内部。
为了观察沙尘是否能钻入APS涂层内部,我们做了如下试验:将沙土与自来水混合,取上层清液并滴在n-YSZ涂层表面,其中图14a的涂层表面带封孔剂,图14b的涂层表面没有封孔剂;自然干燥后(大概需要12 h),将样品用树脂固定、切割、抛光、做截面分析,观察沙子是否进入涂层内部。沙尘在涂层表面的分布情况见图15,可以看到沙尘的粒度远远大于APS涂层的孔隙,无论涂层是否带封孔剂,所有沙尘都被挡在涂层的外表面。
(4)APS过程中混入金属颗粒
BC使用的钴基高温合金粉的粒度分布是:-30 m(8.5%),+30-74 m(90.7%),+74 m(0.8%)。从粒度分布来看,绝大部分都是粒度30 m以上的颗粒,细小颗粒(-5 m)非常少。因此,如果n-YSZ涂层内有金属颗粒,无论是在涂层表面还是截面,都很容易与n-YSZ涂层分辨出来。在陶瓷粉末中掺入少量钴基高温合金粉然后进行APS喷涂,涂层表面的SEM照片见图16。SEM-EDS元素分析表明,涂层内部的高温合金颗粒非常容易区分
图16 APS涂层表面的背散射SEM,金属颗粒为CoNiCrAlY
2.6 腐蚀斑点现象的再现
从一节火焰筒上切割几个小试片。该火焰筒内表面喷涂了n-YSZ涂层,然后喷涂了封孔剂,表观上看不到腐蚀斑点现象。将这些小试片做不同的模拟实验:
图17 2个涂层试片(取自火焰筒,表面带封孔剂)经过600℃保温1 h后的外观
(1)在600℃保温1 h后表面出现了许多腐蚀斑点,颜色比较浅(见图17)。腐蚀斑点的形状和颜色与火焰稳定器上的腐蚀斑点相似(图2a、图3)。
(2)取3片涂层(表面带封孔剂,侧面用封孔剂密封),做80℃、10天的高温高压加速湿热试验,如图18所示,表面出现了腐蚀斑点,这些腐蚀斑点都呈“双圆圈”现象,与在图2c中火焰筒腐蚀斑点现象相似。模拟试验与自然环境贮存的差别是,高温高压加速湿热后的腐蚀斑点颜色更深、更大,圆圈朝向不明显,其原因是:高温高压湿热时,涂层试片朝上平躺,涂层内部液体的流动在每个方向基本上是均匀的(涂层内部的孔隙分布方向可能不同)。另外,该现象还可以说明,这些带双圆圈的腐蚀斑点是由液体流动产生的。
图18 3个涂层试片(取自火焰筒,表面带封孔剂)经过80℃10天湿热前后的外观:试片1湿热前(a)、后(b),试片2湿热前(c)、后(d),试片3湿热前(e)、后(f);图d中,用箭头标记了2个同心圆圈,这2个同心圆圈的外圈产生了重叠;所有图片的上端即是火焰筒的端面,图片的下端是切割端
3 结论
(1)涂层腐蚀斑点来源于BC腐蚀后的腐蚀产物,LA-ICP-MS是分析涂层腐蚀斑点非常有效的方法。
(2)造成BC腐蚀的因素是Cl-。Cl-的来源有两方面:一是喷涂粉末中残余的原料ZrOCl和YCl,水解产生HCl;二是封孔剂中残余的催化剂HCl。在高温潮湿环境中,BC表面的氧化物与HCl反应,腐蚀产物向外扩散便形成了腐蚀斑点,斑点的颜色决定于腐蚀产物颜色。
(3)防止涂层出现腐蚀斑点最有效的方法,是通过有效的洗涤方法来降低粉末中残余Cl-含量。或者采用电熔YSZ粉末,电熔YSZ经过了3000℃数小时的熔炼,残余Cl-含量很低(≤0.003%)。如果使用封孔剂,封孔剂中不能含有对金属有强烈腐蚀作用的杂质,特别是强酸(HCl,HSO,HAc)。
免责声明:本网站所转载的文字、图片与视频资料版权归原创作者所有,如果涉及侵权,请第一时间联系本网删除。
-
标签: 热障涂层, 氧化钇稳定化的氧化锆, 腐蚀斑点
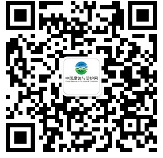
官方微信
《中国腐蚀与防护网电子期刊》征订启事
- 投稿联系:编辑部
- 电话:010-62316606-806
- 邮箱:fsfhzy666@163.com
- 中国腐蚀与防护网官方QQ群:140808414