摘要
研究了等离子喷涂热障涂层 (TBCs) 和激光重熔热障涂层在75%Na2SO4+25%NaCl (质量分数) 熔盐中不同时间下的热腐蚀性能。通过SEM和XRD分析了热腐蚀后两种热障涂层表面和截面的微观形貌和物相组成。结果表明,未经过激光重熔的涂层在前50 h的热腐蚀过程中重量增加;在后续腐蚀过程中重量减小,100 h时腐蚀减重达到了6.8 mg/cm2,同时出现了涂层剥落的现象;表面物相分析检测到ZrO2和Y2(SO4)3相。激光重熔热障涂层在热腐蚀过程中重量一直在增加;后期阶段趋于平缓,100 h时腐蚀增重为3.7 mg/cm2;表面物相分析仅检测到ZrO2相。激光重熔改善了热障涂层的抗热腐蚀性能。
关键词: 热障涂层 ; 等离子喷涂 ; 激光重熔 ; 热腐蚀 ; 镍基高温合金
GH4169合金是一种镍基时效强化高温合金,在高温下具有较好的力学性能、热工艺性能和焊接性能,可在-253~650 ℃范围内使用,也可在约800 ℃短时间使用,目前多应用于航空发动机涡轮盘、叶片等结构件[1,2]。随着航空、航天技术发展,高温合金的使用温度越来越高,热障涂层 (TBCs) 对进一步提高合金材料的使用温度发挥着重要作用,其可以提高使用温度150~200 ℃,在提高航空发动机服役寿命的同时提升工作效率,降低油耗[3,4]。
热障涂层在服役过程中经常受到高温氧化、热腐蚀、冲蚀等侵害,特别是对航空发动机,燃料中的Na和S对涂层产生熔盐热腐蚀,是降低其使用寿命的一个重要因素[5,6,7],因此对热障涂层热腐蚀性能进行研究是非常必要的。由于目前等离子喷涂技术的局限性,制备的热障涂层孔洞、裂纹较多,与基体结合性较差,抗热疲劳与裂纹扩展能力相对较差。激光重熔为进一步改善等离子喷涂TBCs性能提供了新的途径。激光重熔能消除涂层的层状结构、大部分孔隙和氧化物夹杂,形成均匀致密的陶瓷涂层,保证了涂层的性能,从而提高工件的使用寿命[8,9]。
GH4169合金作为航空发动机冷端部件材料在实际服役环境中,会存在短期极限工作温度达到约950 ℃。为了探索热障涂层在合金极限工作温度下对基体的防护性能,故本工作中采用等离子喷涂方法在GH4169合金表面先制备了NiCoCrAlY粘结层,然后制备了ZrO2-7%Y2O3 (质量分数) 陶瓷涂层,并用激光重熔工艺对热障涂层进行处理,最后对比研究了喷涂态和激光重熔热障涂层在950 ℃下75%Na2SO4+25%NaCl (质量分数) 复合熔盐中的热腐蚀行为。
1 实验方法
1.1 实验材料
实验所选用的基体材料GH4169由北京航空材料研究院经锻造加工制成,化学成分为52.4Ni-18.4Cr-5.5Nb-3.2Mo-1.4Co-18.2Fe-0.9Ti (质量分数,%)。使用电火花线切割机,将合金加工成10 mm×10 mm×4 mm的片状试样。实验所选用粘结层材料是由中州合金材料有限公司提供的Ni-25Co-18Cr-10Al-Y合金粉末 (质量分数,%)。实验所采用的陶瓷层材料是由锦州金江材料公司提供的7%Y2O3稳定的ZrO2,原始粉末粒度为纳米级,经喷雾干燥团聚后粒度在25~80 μm。
1.2 涂层制备工艺
实验采用等离子喷涂制备粘结层和陶瓷层。喷涂前试样经打磨、清洗、喷砂等预处理。经过前期的探索和实验,两种涂层的等离子喷涂工艺参数见表1。喷涂时,激光功率550 W,扫描速率350 mm/min,光斑尺寸3 mm×3 mm,搭接量30%。
表1 等离子喷涂热障涂层工艺参数
1.3 热腐蚀实验方法
将未处理和激光重熔的两种热障涂层试样用精度为0.1 mg的电子天平称取重量后,在试样表面用毛刷涂抹一层预先配好的饱和盐溶液,用干燥箱干燥后,再次称取重量,控制试样表面的盐膜重量在2~3 mg/cm2。然后将涂有盐膜的试样分别放入陶瓷坩埚中,之后置于Muffle炉中。升温速率设定为15 ℃/min,到达950 ℃开始保温,每10 h取出试样,并将其放入蒸馏水中多次煮沸,以除去试样表面残留的盐膜,然后经过干燥后再次称重并观察涂层表面宏观形貌的变化。继续重复以上实验过程,直至实验时间达到100 h。根据热腐蚀过程中试样重量变化绘制热腐蚀动力学曲线。取热腐蚀10,40和100 h的两种热障涂层试样,一部分用作观察涂层表面宏观形貌;另一部分进行镶嵌、打磨、抛光、腐蚀后,用于扫描电镜 (SEM,HITACHI S-4800型) 和X射线衍射 (XRD,D8ADVANCE) 分析。
2 结果与讨论
2.1 两种热障涂层的表面形貌
图1a是等离子喷涂热障涂层的表面形貌。可以看出,涂层表面凹凸不平,颗粒大小不一,存在一定的孔隙和裂纹。这是由于等离子喷涂过程中,粉末颗粒被加热至完全熔化或半熔化状态后高速冲击基体,部分粉末颗粒在等离子体焰流中停留时间短,未能完全融化,造成颗粒大小不同。由于颗粒快速凝固铺展在基体表面,颗粒相互堆积,造成表面凹凸,且形成孔隙裂纹。图1b是等离子喷涂热障涂层经过激光重熔后的表面微观形貌。可以看出,涂层经过激光重熔之后,表面整体光滑平整,涂层致密度高,没有明显的孔洞和裂纹,仅存在少部分激光重熔时的溅射颗粒。孔隙率的降低将提高涂层对基体的保护作用。
图1 两种热障涂层表面微观形貌
2.2 热腐蚀动力学曲线
图2是两种热障涂层在950 ℃下75%Na2SO4+25%NaCl混合熔盐中热腐蚀100 h的动力学曲线。可以看出,两种热障涂层的腐蚀动力学曲线规律完全不同。等离子喷涂热障涂层在0~50 h腐蚀时间内,试样质量保持稳定上升的趋势,大致呈线性变化,说明在这个时间段内涂层的抗腐蚀性能较好,很好地保护了基体合金。腐蚀达到50 h时,曲线出现极大值,增重为2.7 mg/cm2,说明此时涂层的抗腐蚀性能已经达到极限。在50~100 h时间段内,动力学曲线出现了急剧的下降;当腐蚀100 h后,此时出现了严重的减重现象,除去坩埚重量后的值为-6.8 mg/cm2。通过显微观察和XRD分析可见,部分陶瓷层在陶瓷层层间产生了剥落,而粘结层并未发生剥落。原因主要是陶瓷层的内部缺陷导致的应力集中,高温下陶瓷层的烧结和熔盐的渗入使陶瓷层内裂纹扩展。此时涂层已经发生失效,对基体的保护作用在急剧衰退。热腐蚀后试样的截面照片可以进一步验证这一结论。激光重熔热障涂层在0~50 h腐蚀时间内,保持类似的直线上升的趋势,但在腐蚀增重的数值上明显小于同时间未处理热障涂层的。在50~100 h的腐蚀后期,由于陶瓷层激光重熔后致密的柱状晶结构消除了内部大量的孔隙和裂纹,熔盐仅消耗了表层的少量Y2O3和ZrO2后难以继续渗透进涂层内部,使得腐蚀增重速率放缓,曲线趋于平滑。激光重熔在腐蚀100 h后,腐蚀增重达到3.7 mg/cm2,涂层仍然保持着一定的抗腐蚀性能。
图2 两种热障涂层热腐蚀动力学曲线
2.3 热腐蚀后涂层表面物相分析
图3是两种热障涂层在950 ℃下75%Na2SO4+25%NaCl混合熔盐中热腐蚀不同时间后表面XRD谱。从图3a中可以看出,喷涂态热障涂层起初以t相、c相为主,经过40 h的热腐蚀之后,m相衍射峰开始变强。随着时间的延长,m相衍射峰进一步增强,t相衍射峰减弱,表明m相体积分数逐渐增多,而t相体积分数在逐渐减小,验证了涂层内部在发生着t→m的转变。同时出现了微弱的Y2(SO4)3相衍射峰,且随腐蚀时间延长逐渐增强,说明不断有新的Y2(SO4)3相生成,反应一直在进行。而从图3b中可以看出,随着热腐蚀的持续进行,涂层内部同样地发生了t→m的相转变,但和图3a相比,m相的峰较弱,说明m相的转变速率更低,体积分数更小。同时,图3b中没有出现Y2(SO4)3,100 h后涂层表面成分主要还是ZrO2相,涂层表现出了良好的耐腐蚀性能[10]。
图3 两种热障涂层热腐蚀不同时间后表面的XRD谱
2.4 热腐蚀后涂层表面微观形貌观察
图4示出了喷涂态热障涂层在950 ℃下75% Na2SO4+25%NaCl混合熔盐中热腐蚀不同时间后的表面微观形貌。从图4a中可以看出,涂层经过热腐蚀10 h后,表面开始变得疏松,出现了一些孔洞和沟壑,局部有剥落的现象,形成了腐蚀坑,且出现了一些细小的ZrO2颗粒,但此时涂层尚处于热腐蚀孕育期,涂层具有较好的抗热腐蚀性能。从图4b中可以看出,经过40 h的热腐蚀,涂层的疏松程度加剧,表面颗粒之间出现了大量的网状连接,颗粒尺寸相比于图4a中的有一定程度的增大,但此时的涂层表面未出现大面积的剥落,说明涂层还保持着一定的抗腐蚀性能。从图4c中可以看出,经过100 h的腐蚀后,涂层表面基本破裂,出现了大面积剥落,颗粒尺寸进一步长大,颗粒数量相比于图4b而言急剧增多。其中还夹杂着小部分的长条状颗粒,是熔盐与涂层表面反应产生的Y2(SO4)3[11]。
图4 喷涂态热障涂层热腐蚀不同时间后的表面微观形貌
图5是激光重熔热障涂层在950 ℃下75% Na2SO4+25%NaCl混合熔盐中热腐蚀不同时间后的表面微观形貌照片。从图5a中可以看到,经过10 h热腐蚀后,涂层表面依然平整光滑,结构致密,晶界清晰,仅能看到细微的裂纹,此时涂层的抗腐蚀性能较好。从图5b中可以得出,经过40 h的热腐蚀后,伴随着体积的膨胀,产生了热应力,涂层表面出现了明显的网状裂纹和孔洞;与10 h腐蚀后的相比,表面依旧比较平滑,没有发生涂层的剥落和破裂,此时涂层还具有抗腐蚀性能。从图5c中可以看到,涂层表面分层较为明显,表面的粗糙度增加,裂纹扩展,导致涂层的表面发生了破裂,但未影响到涂层的核心部分。和喷涂态TBC相比 (图4c),经过100 h热腐蚀后,激光熔覆热障涂层仍然具有一定的抗腐蚀性能。
图5 激光重熔热障涂层热腐蚀不同时间后的表面微观形貌
2.5 热腐蚀后涂层截面微观形貌观察
图6是两种热障涂层在热腐蚀100 h后的截面微观形貌。从图6a中可以看到,未激光重熔的涂层在经过950 ℃/100 h热腐蚀后,涂层内部出现了大量的孔洞以及明显的横向和纵向裂纹。涂层存在大量裂纹,表明涂层此时易于发生剥落。根据XRD分析可知,陶瓷层中大量的Y2O3与熔盐发生如下反应[12]:
图6 两种热障涂层热腐蚀100 h后的截面微观形貌
反应生成Y2(SO4)3,Y含量的减少,导致陶瓷层中的ZrO2发生了t→m的转变,同时伴随着3%~5%陶瓷层体积的膨胀,使涂层中的拉应力转变为压应力,导致热腐蚀后涂层的层状结构出现破裂,部分破裂严重区域已经从表面脱落,出现孔洞,这是裂纹产生的主要原因[13]。
从图6b中可以看出,激光重熔处理后的涂层经过950 ℃/100 h热腐蚀后,涂层内部也出现了一定数量的孔洞,但孔洞不连续,没有看到裂纹的产生,各层之间依旧结合紧密,较腐蚀之前未发生大的变化。同时从图6a和b都可以看出,经过长时间的高温腐蚀涂层出现了高温氧化现象,在陶瓷层和粘结层中出现了明显连续的热生长氧化物 (TGO),说明O通过熔盐,渗透表面的陶瓷层进入到涂层内部,与粘结层中的元素发生反应,100 h后TGO的主要成分是Al2O3和Cr2O3[14,15,16]。但比较两种热障涂层中的TGO层,激光重熔热障涂层中的TGO层更薄且不连续,说明激光重熔后的陶瓷层一方面有效地阻碍了O的渗入,极大程度上减慢了TGO层的形成;另一方面封堵了熔盐的扩散通道,使熔盐只能与表层的Y2O3和ZrO2反应,大大降低了体积膨胀应力和腐蚀产物的生长应力。相比于传统的等离子喷涂陶瓷层的层片状结构,激光重熔后的陶瓷层消除了层状结构,同时也消除了大量裂纹、孔洞和未融化颗粒,形成柱状晶结构的致密重熔层。在阻碍外部元素渗入的同时,也减缓了在高温下陶瓷层内部裂纹向外扩展的速率,减弱了内应力的生成,对基体形成更有效的保护。
同时从图6中可以看到,在经过100 h的热腐蚀后,两种热障涂层与基体的界面都还保持良好的结合,界面清晰可见,说明涂层和基体的结合并没有受到长时间热腐蚀的影响。
结合热腐蚀动力学曲线,从裂纹扩展角度分析,热障涂层剥落失效主要分为3个阶段[17]:
第一阶段:钠盐随着温度的上升,呈熔融态覆盖在涂层表面形成盐膜,经过由热喷涂形成的孔隙和裂纹进入涂层内部,直接增加了熔盐与涂层的接触面积。
第二阶段:熔融盐与陶瓷层内的Y2O3发生反应,生成腐蚀产物。由于Y2O3不断被消耗,使ZrO2失稳,发生t→m的相转变,相变过程中伴随着体积膨胀,使原有的裂纹发生扩展,促进了热腐蚀进一步深入涂层,腐蚀产物在裂纹处结晶长大,也为裂纹扩展提供了热生长应力。经过长时间热腐蚀后,促进了表面陶瓷层从陶瓷层内的剥落。
第三阶段:在冷却过程中,涂层间热膨胀系数不匹配引起的热应力,综合作用于热障涂层,最终导致涂层的失效剥落。
3 结论
(1) 等离子喷涂热障涂层在950 ℃下75% Na2SO4+25%NaCl混合熔盐中腐蚀50 h后达到性能极限,增重为2.7 mg/cm2;腐蚀100 h后出现了腐蚀减重,达到了-6.8 mg/cm2,涂层发生剥落,涂层失效。激光熔覆热障涂层腐蚀100 h后,氧化增重为3.7 mg/cm2,涂层完好,仍然具有良好的抗热腐蚀性能。
(2) 等离子喷涂热障涂层在热腐蚀过程中,涂层内部出现了明显的裂纹,且生成了一定厚度的连续的TGO;涂层表面Y2O3和熔盐发生化学反应生成Y2(SO4)3,Y2O3的减少使得ZrO2发生了t→m相的转变,带来涂层体积膨胀,加上腐蚀产物所带来的热生长应力,促进了内部裂纹扩展。激光重熔热障涂层腐蚀100 h后,涂层内部依然结合紧密,未产生裂纹;表面未与熔盐发生反应,保持良好的抗热腐蚀性能。
免责声明:本网站所转载的文字、图片与视频资料版权归原创作者所有,如果涉及侵权,请第一时间联系本网删除。
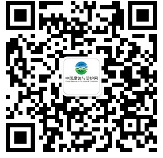
官方微信
《中国腐蚀与防护网电子期刊》征订启事
- 投稿联系:编辑部
- 电话:010-62316606-806
- 邮箱:fsfhzy666@163.com
- 中国腐蚀与防护网官方QQ群:140808414