摘要:本文介绍了钢铁耐磨材料的发展历史,重点综述了高锰钢、高铬铸铁、高钒高速钢3类典型耐磨材料的成分、显微组织、磨损性能、抗磨机理和改性技术。以高锰钢为代表的耐磨钢依靠高强韧性的基体抵抗磨损,而以高铬铸铁和高钒高速钢为代表的耐磨合金主要依靠高硬度的耐磨相抵抗磨损,高钒高速钢比高铬铸铁具有更优良的耐磨性,与VC硬度高、形态好的特性有关。提出了高性能耐磨材料应具备3个要素:高强韧基体,高硬度多尺度协同作用的优质耐磨相,耐磨相与基体良好结合。
关键词: 钢铁耐磨材料 ; 研究进展 ; 展望
磨损是材料损伤的三大原因之一,是机械装备失效的重要方式。统计资料表明[1]:约有80%的机器零部件是由于磨损而失效的,每年因摩擦、磨损造成的损失约占国内生产总值(GDP)的5%,中国工程院调查结果显示,我国2006年摩擦、磨损造成的损失约9600亿元,随着我国工业的快速发展,摩擦、磨损领域对材料的消耗量也迅速增加,根据我国2018年的GDP推测,由于摩擦、磨损造成的损失超过4万亿元。耐磨材料是制造业重要的消耗材料,广泛应用于机械、冶金、电力、建材、国防、船舶、铁道、煤炭、化工等领域,典型产品如冶金工业的挖掘机、破碎机、球磨机等设备中的斗齿、磨球、衬板,金属轧机中的轧辊,电力工业磨煤机中的磨环、冲击板,渣浆泵过流件等,耐磨产品消耗量巨大[2,3,4]。近年来,随着装备制造业向规模大型化、应用条件苛刻化、运转高效化方向发展,对耐磨材料的性能要求越来越高,开发出高性能的耐磨材料具有巨大的经济效益和社会效益,提高耐磨材料使用寿命已经成为国家制造业整体竞争力提升的重要任务之一。
1 磨损的基本认识
磨损被列为材料三大失效方式(断裂、腐蚀、磨损)之一,它是一种复杂的现象,受机械、物理、化学、材料等诸多因素影响,目前对磨损尚无严格统一的定义。克拉盖尔斯基[5]认为:磨损是由于摩擦结合力反复扰动而造成的材料破坏,邵荷生[6]将磨损定义为:由于机械作用、间或伴有化学或电的作用,物体工作表面材料在相对运动中不断损耗的现象。从广义的角度理解,存在各种介质的开放或封闭体系内,在载荷的相互作用下,由于物体相对运动而引起的表面损耗即为磨损。但是,并非所有磨损现象都具有研究价值,在一定时间内,零部件的几何尺寸(体积)明显变小,导致零部件失去其应有的功能的磨损才具有研究价值。
由磨损的定义可知,磨损是一门系统工程,磨损过程是复杂的动态微观作用过程,并受材料成分、组织结构等内因和温度、环境介质、作用方式等外因影响,因此,对磨损有不同的分类方法,且磨损的类型繁多。按表面接触性质分,磨损可分为:金属-磨料磨损、金属-金属磨损、金属-液体磨损;按环境和介质分,磨损可分为:干磨损、温磨损和液体磨损;按磨损机理分类,磨损可分为:磨料磨损、微动磨损、冲击磨损、黏着磨损、疲劳磨损、冲蚀磨损等[7]。由于零部件实际工况的磨损条件和磨损过程的复杂性,材料的磨损常常是多种磨损机制并存,因而,耐磨材料学术界有一句共识:“没有万能的耐磨材料”,需要根据具体的应用工况匹配适用的耐磨材料。
2 代表性的钢铁耐磨材料
近代钢铁材料是伴随第一次工业革命发展起来的,由于机器设备的发展需要高性能的钢铁材料,出现了针对不同应用领域的多种类型的钢铁材料,钢铁耐磨材料就是其中的一类。耐磨钢作为专用钢始于19世纪后半叶,1882年英国人哈德菲尔德(Robert Abbot Hadfield)发明了高锰钢,此钢种在高应力冲击载荷下表面产生加工硬化,显微硬度由250 HV提高到700 HV左右,有利于提高表面抗磨损性能,而工件内部仍保持优良的韧性,因此,该钢种兼具了耐磨性与使用安全性,广泛用于矿山机械、冶金机械、建筑机械、拖拉机履带板等高载荷冲击工况下的耐磨件。1898年美国机械工程师泰勒和冶金工程师怀特发明了高速钢,该钢种含有大量高硬度的碳化物而具有优良的耐磨性,主要用于制造薄刃和金属切削刀具,经过100多年的不断发展,形成了钨系高速钢、钼系高速钢、钴系高速钢等多个系列,应用工况范围不断扩大。近几十年来,非锰系低、中合金耐磨钢的开发与应用发展很快,20世纪70~80年代在国际上形成了系列并制定了相关的标准,主要包括马氏体、贝氏体和双相耐磨钢系列。铬系白口铸铁起源于20世纪初期,第二次世界大战后开始广泛应用,该材料因含有Cr的碳化物和高强度基体而具有优良的耐磨性,在冶金、矿山、建材、火力发电等领域广泛应用,成为国内外公认的优质耐磨材料。高钒高速钢是伴随轧辊技术发展而发明的一类新钢种,钢中碳化物类型以MC型为主,碳化物硬度高、耐磨性好。20世纪80年代,日本川崎制铁(株)钢铁研究所开发了高钒高速钢耐磨轧辊,1990年前后,日本新日铁公司也成功开发了高钒高速钢轧辊。在国内,20世纪90年代中期,唐山联强冶金轧辊有限公司与钢铁研究总院合作,在我国率先研制成功离心铸造高速钢轧辊,并成功应用于热轧窄带钢轧机、棒材轧机、高速线材轧机等。河南科技大学于2001年成功研制了高钒高速钢,应用于建材行业的锤头、衬板等产品[8]。
经过数十年的发展,现代钢铁耐磨材料种类已非常齐全,针对冲击磨损、磨料磨损、冲蚀磨损等各种磨损形式形成了多类型的耐磨材料系列,许多国家和地区均形成了完善的标准化体系。我国于1982年发布第一个耐磨材料国家标准(中锰抗磨球墨铸铁件GB3180-1982),之后,又陆续发布了高锰钢铸件(GB5680-1985)、抗磨白口铸铁技术条件(GB8263-1987)、铸造高锰钢金相(GB/T13925-1992) 3项耐磨材料国家标准(截止到1992年)。经过几次修订和完善,目前,在铸造钢铁耐磨材料方面,形成了奥氏体锰钢件、耐磨铸钢件、铬锰钨系抗磨铸铁件、抗磨白口铸铁件、耐磨耐蚀钢铸件等10项国家标准,此外,还有机械行业耐磨材料标准4项及中国铸造协会和钢铁耐磨材料产业技术创新战略联盟耐磨材料标准14项。此外,在电力、建材、黑色冶金等行业,也有多项耐磨材料行业标准。耐磨材料种类繁多,本文主要介绍3类具有划时代意义的优质耐磨材料。
2.1 高锰钢
2.1.1 高锰钢国家标准与化学成分
高锰钢自100多年前问世以来,一直是高应力冲击载荷磨损工况下的首选材料,其原因有二:一是高锰钢冲击韧性高,使用安全可靠;二是高锰钢在加载载荷的过程中,会由于孪晶诱导塑性(TWIP)效应产生大的无缩颈均匀延伸变形[9],强度逐渐升高、发生硬化,高锰钢的强加工硬化特性使其在高应力冲击载荷磨损工况下具有优良的耐磨性。近代耐磨材料发展迅速,各种新型耐磨材料层出不穷,但对于高应力冲击载荷磨损工况下的部件,如圆锥破碎机轧臼壁、大型颚式破碎机颚板等,尚无一种材料可以完全替代高锰钢。高锰钢的典型化学成分(质量分数,下同)为:0.9%~1.5%C、10%~15%Mn、0.3%~1.0%Si、S≤0.05%、P≤0.10%[10]。目前,我国国家标准中共有奥氏体锰钢10个牌号,对应国际ISO标准的9个牌号,具体化学成分参见GB/T 5680-2010,各牌号的高锰钢化学成分是在基本高锰钢(Mn13)的基础上,调整Cr、Mo、Ni、W合金元素含量,来改善合金性能,以适应具体的应用工况。
2.1.2 高锰钢组织特征
高锰钢的铸态组织主要由奥氏体、碳化物和珠光体组成,有时含有少量磷共晶,碳化物常常在晶界上呈网状分布,导致铸态高锰钢脆性大而无法使用,为了消除网状碳化物,需对高锰钢进行固溶处理,即将钢加热到1050~1100 ℃,奥氏体化后得到单相奥氏体组织,然后水淬快速冷却,使奥氏体组织保持到常温(图1[11]),固溶处理后高锰钢的强度、塑性和韧性均得到大幅度提高,该热处理技术被称为水韧处理。
图1 高锰钢的典型显微组织[11]
2.1.3 高锰钢的强化机制
在受到大变形时,高锰钢组织易发生相变,形成大范围的堆垛层错、孪晶以及平面位错结构,具有良好的加工硬化能力,这种优良的性能由其变形强化机制所决定。长期以来,对高锰钢的强化机制有大量的研究报道,但目前并没有统一的说法。高锰钢的强化有多种机制,每种强化机制均有一定的证据,高锰钢的强化或许就是多种机制同时起作用。
(1) 形变诱发马氏体相变强化机制。该机制将高锰钢的强化原因归于形变诱发奥氏体向马氏体转变(图2[12])。Krivobok[13]认为变形的奥氏体中交截的切变带提供了新的形变诱发马氏体形核位置,形变时很容易诱发ε相变,ε相成为α‘马氏体相变核胚有诱发马氏体的作用,X线衍射分析证明高锰钢存在马氏体转变[14]。Olson和Cohen[15]提出,应变诱发马氏体转变与层错能有关,奥氏体层错能较低,在形变过程中容易形成层错,在层错处会出现ε-马氏体或形成形变孪晶,但并不容易出现α马氏体;Choi等[16]认为:高锰钢中奥氏体向马氏体转变有不同的方式,奥氏体可直接转变成α-马氏体,也可以形成层错后,先转变成ε马氏体,而后再转变成α马氏体,转变方式取决于层错能。也有一些研究不支持该强化机制,高锰钢的发明人Robert Hadfield也否定了形变诱发马氏体理论[17],后来Raghavan等[18]的研究也未发现高锰钢硬化层中有形变诱发马氏体产生。
图2 18Mn钢900 ℃压缩70%、保温3 min后吹气快速冷却组织取向成像[12]
(2) 孪晶强化机制。高锰钢硬化是由于变形过程中形成孪晶引起的(图3[19])[19,20,21,22],根据孪生机制,高锰钢形变过程中会产生大量孪晶,孪晶将基体切割成很多小块,可以锁住位错,导致位错运动困难,同时孪晶界可以阻碍位错运动,从而提高强度。高锰钢发生变形时,高应变区域先形成孪晶,阻止了高应变区域内位错滑移而得到强化,促使强度较低的低应变区晶面滑移形成孪晶,从而使试样均匀形变,推迟缩颈,提高材料整体强度。
图3 不同压缩变形量下高锰钢显微组织的TEM像及其电子衍射花样[19]
(3) 位错强化机制。高锰钢在形变时产生大量位错,形成高密度位错区,阻碍位错运动而产生强化[23,24,25]。文献[26]认为高锰钢的形变加工硬化行为分阶段进行,通过晶面滑移、位错交割、位错缠结而形成胞状结构或亚晶粒互相锁住,胞壁成为位错运动的障碍,足够高的应力使被阻挡的位错借助于交滑移而运动,同时位错胞数量逐渐增大、尺寸逐渐变小,对基体的割裂作用越强,位错之间的作用也越强。为了使高锰钢发生进一步的塑性变形,必须克服阻碍位错运动的力,需要消耗更高的能量,宏观上表现为加工硬化。
除以上强化机制,高锰钢强化机制还有动态应变时效强化机制[27]、Fe-Mn-C原子团硬化机制[28]、综合硬化机制[29]、纳米晶与非晶相镶嵌硬化机制[30]等。
2.1.4 改性高锰钢发展状况
(1) 提高加工硬化能力。为了进一步提高高锰钢的加工硬化能力,研究者在传统高锰钢的基础上进行了改性研究。合金化强化是提高高锰钢加工硬化能力的常用技术,通过调整钢中的Mo、Cr、Ni、V、Cu、Ti、RE、N、Nb等元素含量可以达到强化的目的,获得更好的性能指标[31,32,33]。文献[34,35]利用Cr+N复合合金化的方法,对传统成分的高锰钢进行合金化处理,降低了高锰钢的层错能,使其在塑性变形中更易产生形变孪晶,提高了加工硬化能力,高锰钢的强塑性和抗磨损性能显著提高。在经受循环变形过程中,Cr+N合金化处理还使得高锰钢在低应变幅下产生平面位错结构,而高应变幅下产生形变孪晶,最终提高了其疲劳寿命[36]。C具有固溶强化效果,提高C含量可以提高其加工硬化能力,但C含量高会导致组织中碳化物增多,降低冲击韧性。Mn元素能够降低C原子扩散能力,抑制碳化物形成。基于此,研究者开发了超高锰钢[37,38],超高锰钢在变形的过程中,可以产生大量的Mn-C原子对,造成强烈的不对称畸变,显著提高了加工硬化能力和耐磨性能[39]。
(2) 表面预硬化。高锰钢的缺点是初始硬度低,在低应力磨损或磨损阶段早期时磨损严重,为了提高高锰钢的初始表面硬度,对高锰钢的表面预硬化进行了大量的研究。目前采用的表面预硬化技术主要有:电子束表面强化[40]、机械冲击强化[41,42]和爆炸强化[43]等。最近,科研人员[44,45]利用表面高速重击技术对高锰钢表面进行处理,通过改变冲击载荷和冲击次数,在高锰钢表面获得了毫米级厚度的纳米晶层,提高了表面硬度,并且相比于原始高锰钢界面,纳米晶具有更高的表面活性,使其更易于与空气中的氧反应生成一层保护氧化膜,显著提高钢的高温耐磨性。
(3) 高锰TWIP钢。高锰TWIP钢是伴随汽车工业发展起来的,含有Mn、Al、Si、C、N等多种元素,具有高强、高塑、高应变硬化率和高能量吸收能力,可有效缓解汽车碰撞时的能量冲击,是一种具有很大发展潜力的汽车用钢[46,47,48]。目前,高锰TWIP钢主要有Fe-Mn-Si-Al系和Fe-Mn-C(-Al)系,Fe-Mn-Si-Al钢的强化机制以孪晶形成动态细化晶粒为主,而Fe-Mn-C(-Al)系TWIP钢中动态应变时效可能是主导作用,Al元素合金化后在试样表层下可以形成α-Al2O3,改善了TWIP钢的延迟断裂敏感性[49]。高锰TWIP钢高应变硬化率的特点,使其有潜力应用于冲击磨损工况下。
2.2 高铬铸铁
2.2.1 铬系白口铸铁国家标准与化学成分
铬系白口铸铁在耐磨材料发展史上具有重要的地位,是继高锰钢之后耐磨材料发展史上的另一个里程碑。20世纪50~60年代,我国把高锰钢作为万能的耐磨材料使用,但工程应用实践中发现,高锰钢只有在冲击大、应力高、磨料硬的情况下才能发挥其耐磨性,而铬系白口铸铁具有很高的初始硬度,在低冲击、低应力磨损条件下具有优异的耐磨性。对高铬铸铁的研究从20世纪60年代开始,到80年代中后期达到顶峰,至今仍方兴未艾。目前,我国铬系白口铸铁形成了10个国家标准牌号,具体化学成分参见GB/T 8263-2010。铬系白口铸铁可分为低铬铸铁,中铬铸铁和高铬铸铁,其中高铬铸铁的含Cr量大于11% (质量分数),可参照Fe-C-Cr三元合金的液相投影图分析凝固相[50]。
2.2.2 高铬铸铁组织特点
高铬铸铁是一种综合性能优良的耐磨材料,因为Cr元素形成了高硬度的(Fe, Cr)7C3 (简称M7C3)型碳化物(1300~1800 HV),与普通白口铸铁中网状碳化物Fe3C (800~1200 HV)相比,M7C3型碳化物硬度高,呈杆状独立分布(图4[51])[51,52],基体为连续相,碳化物对基体的破坏作用大大减小,为同时提高冲击韧性和耐磨性提供了基础条件。高铬铸铁的基体组织可以通过热处理调控,以适用不同的磨损工况[52,53],常用高铬铸铁的基体组织为马氏体和奥氏体混合组织,该组织兼具高硬度和较高韧性的特点。此外,高铬铸铁基体含Cr量高,基体电极电位高,在腐蚀和氧化条件下也具有优良的耐磨性[54,55,56]。
图4 高铬铸铁的典型显微组织[51]
M7C3型碳化物是高铬铸铁的主要耐磨相,目前对于M7C3的晶体结构还存在争议,晶体结构有正交、六方、三方几种说法。1935年,Westgren[57]首先提出Cr7C3结构是六方对称的菱形晶胞,空间群是P31c,点阵常数为a=1.398 nm,c=0.4523 nm。20世纪70年代Rouault等[58]根据Cr7C3结构和Mn7C3正交结构类似的规律,提出了2种正交结构的Cr7C3晶体,其空间群分别是Pnma和Pmcn,并将其称为高温稳定型结构,他们认为低温下存在的Cr7C3是六方结构。1980年,Dudzinski等[59]研究得到了2种属于三方结构的Cr7C3,空间群均为P31c,但晶胞中原子平移周期选取不同。
2.2.3 高铬铸铁的磨损性能
高铬铸铁的磨损性能受内因(碳化物形态、尺寸、含量、分布和基体组织类型、相对含量等)和外因(磨损形式、受力状况、介质、温度等)诸多因素影响。Larsen-Badse[60]报道:大磨料高应力磨损条件下,碳化硅切削作用会使大尺寸碳化物碎裂、剥落,对耐磨性不利。邢建东等[52]研究了在2种磨料(硬磨料SiC和软磨料石榴石)磨损条件下,不同基体对高铬铸铁两体和三体磨料磨损性能的影响(表1[52]),高铬铸铁的耐磨性表现明显不同,耐磨性受基体、碳化物和磨料硬度影响显著,在硬磨料磨损条件下,磨料的“刻入”会导致粗大碳化物崩落,对磨损性能不利,而在软磨料磨损条件下,初生碳化物不会被破坏,对提高耐磨性更有利。贺林等[61]研究了碳化物尺寸对耐磨性的影响,结果表明,在不同的磨损条件下,碳化物需要适当的尺寸(表2[61])。贾育丁和苏俊义[62]对高铬铸铁在湿砂橡胶轮磨损、三体磨损及冲蚀磨损条件下耐磨性的研究得到了类似的结果。Dogan等[63]研究了不同取向的M7C3对高铬铸铁二体磨料磨损性能的影响,发现M7C3长轴方向与磨损面平行时较垂直时耐磨性好。因此,应根据磨料特性、应力条件等工况来调控高铬铸铁的碳化物位向与尺寸。
表1 不同磨料磨损条件实验结果[52]
表2 碳化物尺寸效应对高铬铸铁耐磨性的影响[61]
高铬铸铁具有优良的冲蚀磨损性能,广泛应用于石油化工、水利发电机等装备耐冲蚀磨损部件[64,65,66]。高铬铸铁冲蚀磨损性能受冲蚀条件影响很大,黎志欣等[67]对高铬铸铁的冲蚀磨损特性进行研究发现:冲击角对高铬铸铁耐磨性有显著影响,冲击能量在磨料和抗磨材料中的分配比例对耐磨性起着关键作用。但是,在含有腐蚀性介质的酸砂浆中,高铬铸铁中的共晶碳化物与其相间形成大量的相界,基体与碳化物之间存在电位差,会造成较为严重的相间腐蚀,因此,普通高铬铸铁不适用于在高浓度酸砂浆中服役[68,69]。路富刚等[70,71]通过在普通高铬铸铁中加入N元素,提了基体的电极电位,显著提高了高铬铸铁的抗冲蚀磨损性能。
2.2.4 超高铬铸铁
为了提高渣浆泵过流件的使用寿命,20世纪90年代,加拿大与澳大利亚的研究人员率先开发出了C含量为4.5%~5.0%、Cr含量为30%~35%的过共晶超高铬铸铁,该铸铁的Cr、C含量高,M7C3型碳化物含量高,体积分数达到38%以上,使用后获得了良好的效果[72]。21世纪初,国内大连耐酸泵厂和石家庄泵业集团先后开发了超高铬铸铁材料,用于耐腐蚀泵上,取得了满意的成效[73,74,75]。郑州机械研究所开发了超高碳高铬堆焊药芯焊丝,获得与摩擦面重直的杆状M7C3型碳化物,解决了腐蚀磨损件的焊补问题[76]。
超高铬铸铁具有显著的组织特点和性能优势。亚共晶超高铬铸铁基体为高铬铁素体,具有Cr的正电极电位,其M23C6型碳化物硬度较高,电极电位与高铬铁素体相近,因此具有优良的耐腐蚀磨损性能。过共晶超高铬铸铁铬碳化物为M7C3型,硬度高、含量高,基体组织为马氏体和残余奥氏体,在严酷的低角度的冲击腐蚀磨损条件下性能优良。但超高铬铸铁也存在明显的问题,如过共晶超高铬铸铁中初生M7C3型碳化物数量多,且形态过于粗大,降低冲击韧性与耐磨性。
2.2.5 碳化物改善途径
碳化物的特征决定了高铬铸铁的耐磨性,改善碳化物主要有如下几种途径:(1) 控制凝固过程。在凝固过程中控制碳化物的生长,可以有效改善碳化物的形貌;喷射成形技术和半固态成形技术可以显著减小碳化物的尺寸,使碳化物离散均匀分布[77,78];定向凝固技术可以改善碳化物的生长方式,控制碳化物定向生长[79,80]。(2) 变质处理。变质处理可以改变碳化物生长的热力学条件,优化碳化物形貌,细化尺寸,提升高铬铸铁力学性能。张承甫等[81]将变质机理归纳为:界面能理论、界面共格对应理论、偏析系数理论和Tashis参数等。张景辉等[82]根据化学键理论,计算推导出键参数函数图,指出Li、Na、K、Rb、Ba、Cs、Sr、Ca、Ce、La、Y、Sc、Mg等元素对于小平面方式生长的合金均有变质作用,可用于高铬铸铁中改善碳化物形态、分布、细化晶粒。关于稀土、K、Na、Zn、Mg、V、Ti、B、Al等元素变质高铬铸铁有大量的研究,取得了一定的效果[82,83,84,85,86,87,88,89,90,91,92,93,94]。(3) 塑性变形。通过高温塑性变形方法,使高铬铸铁中的碳化物破碎,分布更加均匀,可以提高冲击韧性[95,96]。(4) 热处理。高温热处理可以使高铬铸铁中的碳化物边角处溶解,网状碳化物可变为孤立分布、边缘圆润[97,98]。此外,雾化制粉后烧结成型[99,100]、合金化[101],悬浮铸造[102]等方法均能一定程度上改善碳化物的尺寸与形态。
2.3 高钒高速钢
2.3.1 高钒高速钢的化学成分
高钒高速钢是在传统高速钢的基础上,通过降低W元素含量,提高V元素含量,适量添加Mo、Cr、Nb等元素后形成的新钢种。表3[103,104,105,106,107,108]为几种性能较好的高钒高速钢的化学成分。从化学成分和显微组织上看,高钒高速钢属于白口铸铁范畴。但是由于它是高速钢中在提高V含量,减少W、Mo含量的基础上逐步发展起来的,故国内外学者习惯上称之为“高钒高速钢”。目前,高钒高速钢已在轧钢、水泥、建材等行业成功应用,但尚未形成完善的国家标准。
表3 高钒高速钢化学成分[103,104,105,106,107,108] (mass fraction / %)
2.3.2 高钒高速钢的凝固组织
大城桂作[109]研究了Fe-5Cr-V-C四元系初晶投影图(图5[109]),当V含量超过约5%时,调整C含量即可得到初生VC,但V含量较低时,得到初生VC要求的C含量较高,且VC的量较少,为得到大量初生VC,V含量需大于8%,C含量需大于2.5%[110]。周宏等[111]研究了不同V、C含量高速钢的凝固组织和相组成,建立了(Fe-5Cr-5Mo-5W-2C)-V准二元相图(图6[111])。彭涛等[112]建立了(Fe-5Cr-2Mo-9V)-C的准二元相图(图7[112]),徐流杰[113]分析了不同C含量高钒高速钢(含V约9%)的凝固过程。含C量为1.58%时,凝固过程中先析出铁素体(L→F),随后发生共晶反应析出VC,VC多呈条状沿铁素体晶间分布。含C量达到1.90%时,初生相仍为铁素体,但铁素体中固溶的V含量减少,晶间分布的杆状共晶碳化钒量增加。含C量达到大约2.23%~2.58%后,当合金液冷至液相线温度时,液相中首先析出初生VC (L→VC)。随着温度的降低,VC不断析出,使得液相中V的含量降低,液相成分向γ+MC的共晶线方向变化,当液相中V含量降至共晶成分点时,将以L→γ+MC的共晶反应继续凝固。随着凝固过程的继续进行,液相不断减少,由于偏析,液相中Mo、Cr等含量升高,当Mo、Cr的含量足够高时,液相将发生三元共晶反应L→γ+VC+M2C。当C含量达到2.82%~2.92%后,其初生相和二元共晶反应与C含量为2.23%~2.58%时类似,继续冷却,最终将会发生多元共晶反应L→γ+VC+M2C+M7C3。因此,高钒高速钢中的V元素可以形成初生碳化钒、二元共晶碳化物和多元共晶碳化钒。根据V、C含量不同,基体组织可为马氏体、奥氏体、铁素体或混合组织。
图5 Fe-5Cr-V-C、Fe-15Cr-V-C及Fe-5Cr-5W-5Mo-V-C 液相面投影图[109]
图6 (Fe-5Cr-5Mo-5W-2C)-V准二元相图[111]
图7 (Fe-5Cr-2Mo-9V)-C 的准二元相图[112]
高钒高速钢中的碳化钒是以VC为主体,微区存在V8C7及V6C5结构的混合体。在VC上分布着大量纳米级的颗粒,可能与C元素缺位形成V8C7及V6C5有关[114]。凝固过程中析出的碳化钒形态多样,主要有:团球状、块状、开花状、条状、短杆状、蠕虫状,分布形式有3种:晶间分布、菊花状分布、均匀分布;合金为亚共晶成分时,碳化钒沿晶间分布;共晶成分时,呈菊花状分布;过共晶成分时,呈均匀分布[110]。
2.3.3 热处理工艺
高钒高速钢的性能与热处理工艺关系密切。由于与传统的高速工具钢在成分、制备工艺等方面存在着较大的差别,新型高钒高速钢不能照搬传统高速工具钢的热处理工艺。周宏等[115]研究了高碳高钒高速钢的淬火、回火热处理及高温硬度,发现峰值硬度温度较常规高速钢低150~250 ℃,随C含量增加,峰值硬度温度降低;相同C含量时,V含量增加,峰值硬度温度升高。随C、V含量的增加,高温硬度增加。回火后的硬度变化和常规高速钢呈相同的趋势,高碳高钒高速钢的淬火温度建议为950~1100 ℃,回火温度530~550 ℃,一次回火即可。Lee等[116]研究了回火温度对高速钢轧辊的耐磨性和抗表面粗糙性的影响,高速钢轧辊在540 ℃回火具有最好的耐磨性,但抗表面粗糙性差,而采用570 ℃回火抗表面粗糙性好,耐磨性也较好。魏世忠等[108]改变高钒高速钢淬火加热温度和回火温度获得不同残余奥氏体量,建立了关于淬火、回火温度的等奥氏体曲线(图8[108])。Xu等[117]建立了残余奥氏体含量、硬度与淬火温度、回火温度之间的关系,获得了最佳的热处理工艺为:1000~1050 ℃空冷淬火,然后530~560 ℃回火(图9[117])。
图8 等奥氏体曲线[108]
图9 残余奥氏体、硬度与淬火温度、回火温度之间的关系模型[117]
2.3.4 高钒高速钢的磨损性能
高钒高速钢因含有大量高硬度的VC而具有优良的耐磨性。目前,已对高钒高速钢的磨粒磨损、冲击磨损、滚动磨损、滑动磨损、滚滑动磨损性能进行了大量研究。新日铁研制出的高钒高速钢轧辊,寿命为高铬铸铁辊的3~7倍[118,119]。随后,欧美各国钢铁企业也纷纷开发使用高速钢轧辊,获得了满意的使用寿命[120,122]。宫开令等[123,124]发明的高速钢轧辊基体上分布着大量的高硬度MC型和M6C型碳化物,耐磨性为高铬铸铁的3倍左右,为高镍铬复合轧辊的5~7倍。文献[125,126,127,128,129]研究了高钒高速钢的磨粒磨损性能,结果表明,C、V含量、热处理工艺和残余奥氏体量均对高钒高速钢的磨粒磨损性能有显著影响,高钒高速钢的相对耐磨性可以达到高铬铸铁的3倍以上、高锰钢的8倍,磨粒磨损失效形式为显微切削,VC失效以剥落为主。文献[130,131]研究了高钒高速钢的冲击磨损性能,高钒高速钢的相对耐磨性为高铬铸铁的2.1倍、高锰钢的2.8倍,冲击磨损机理主要为基体受到的显微切削,导致碳化物脱落,基体受到颗粒的蚕食作用而不断磨损。在滚动磨损条件下,高钒高速钢的相对耐磨性是高铬铸铁的4倍以上[132],其主要失效形式为裂纹萌生后扩展到磨损的表面,造成片状或块状剥落而磨损,当裂纹扩展到VC侧面时,扩展速度减慢或停止[133,134]。文献[135,136]研究了高钒高速钢的干滑动磨损行为,发现高钒高速钢耐磨性好,当压力为500 N时,高钒高速钢的耐磨性是高铬铸铁的3倍以上,失效机理主要为疲劳磨损、显微切削、磨料磨损的复合,并伴有碳化物脆性碎裂及脱落。在滚滑动磨损下,高钒高速钢磨损性能受滑动率影响较大,其相对耐磨性为高铬铸铁的2倍以上,磨损是由滚动和滑动复合作用所致,其失效机理表现为显微切削犁沟和疲劳剥落复合[137,138,139]。
高钒高速钢作为新一代耐磨材料,具有优良耐磨性的原因为:(1) 耐磨相VC硬度高,能有效抵抗磨损过程中硬磨粒划伤,VC形态好,与高铬铸铁中的M7C3相比,在磨损应力的作用下不易弯曲、碎裂,能有效地保护基体(图10[113]);(2) VC与奥氏体基体间存在界面共格关系,界面结合强度高,磨损过程中VC不易脱落(图11[113]);(3) 高钒高速钢经热处理后可以获得兼具高硬度和高韧性的马氏体与奥氏体双相复合组织,能对VC提供良好的支撑,充分发挥VC作为抗磨相的作用。
图10 滚滑动磨损条件下磨损正切面照片[113]
图11 高钒高速钢显微组织[113]
3 钢铁耐磨材料发展展望
钢铁耐磨材料的发展具有阶段性,20世纪是钢铁耐磨材料发展的高峰期,并形成了完善的标准体系,我国耐磨材料已形成了国家标准、行业标准、团体标准三大标准体系。今后,耐磨材料标准应该针对特殊领域出现的新材料、新技术快速更新,并制订先进的耐磨材料系列标准以引领耐磨材料行业的发展。钢铁耐磨材料从抵抗磨损的组相方面可以分为两大类:一类是依靠基体的耐磨材料,另一类是依靠第二相强化的耐磨材料。第一类材料的代表为奥氏体锰钢和马氏体耐磨钢,提高其耐磨性的途径主要为:获得强韧性的基体组织,细化亚结构。近年来发展起来的纳米贝氏体钢具有更高的韧性,在硬度略低于马氏体钢的前提下,表现出更高的耐磨性[140,141,142,143],贝氏体组织中的部分残余奥氏体在磨损过程中会转变为马氏体,也有利于提高贝氏体钢耐磨性[144]。第二类材料的代表为高铬铸铁,近年来发展的高钒高速钢、陶瓷强化钢铁复合材料也是利用更强的耐磨相来提高耐磨性[145,146,147,148]。
未来高性能耐磨材料应具备3个要素:(1) 高强韧基体。高强韧基体不仅自身可以更好地抵抗磨损,也能对高硬度耐磨相提供更有效的支撑作用;(2) 优质的耐磨相。耐磨相要硬度高、形态好,在基体中分布均匀;2种尺度的耐磨相组合强化,微米尺度的耐磨相抵抗磨损,纳米尺度的耐磨相强化基体,可以借助耐磨材料基因组工程高通量计算和高通量实验预测、合成新型的高性能耐磨相;(3) 耐磨相与基体的良好结合。冶金结合的界面,特别是耐磨相与基体存在共格界面时,界面结合强度高,对基体强化效果好,磨损过程中耐磨相不易脱落,可以更好地保护基体。
免责声明:本网站所转载的文字、图片与视频资料版权归原创作者所有,如果涉及侵权,请第一时间联系本网删除。
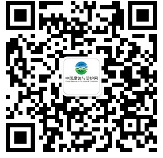
官方微信
《中国腐蚀与防护网电子期刊》征订启事
- 投稿联系:编辑部
- 电话:010-62316606-806
- 邮箱:fsfhzy666@163.com
- 中国腐蚀与防护网官方QQ群:140808414