CO2/H2S引起的碳钢腐蚀是油气田行业中常见的腐蚀类型,由其引发的事故屡见不鲜。抑制CO2/H2S腐蚀的方法有很多,其中加注缓蚀剂是一种操作简单、经济有效的腐蚀防护手段,目前已得到广泛应用。单一的缓蚀剂在实际应用中一般无法满足设备设施的防腐需求,此时可利用两种或多种缓蚀剂间的协同效应来制备复合缓蚀剂,在降低成本的同时提高了缓蚀剂的性能[1]。
虽然缓蚀协同效应相关研究已取得长足进展,产生了包括架桥理论[2,3,4,5,6,7]、补强理论[8,9]、协同吸附理论[10,11]等在内的缓蚀协同效应理论,但整体来说,协同效应的研究多数还集中在无机酸性体系 (如HCl,H2SO4,H3PO4)[1,6,7,12,13,14,15]或CO2腐蚀体系[8,11],在CO2/H2S共存的盐水溶液中,相关报道较少。
此外,之前对协同效应的研究往往依赖于大量的实体实验,如失重法、电化学测试、表面分析等,这些方法只能在宏观上研究缓蚀剂间的协同效应,较难从微观上解释协同机理,且实验过程缺乏一定的理论指导。分子模拟技术目前已成为研究微观机理的有效手段,并已被众多学者用来评估缓蚀剂的性能[16,17,18,19,20,21,22,23]。本课题组首次将分子模拟技术应用于缓蚀协同效应的研究,并取得一定进展[24],但这方面的报道依然较少。
本文采用分子模拟技术研究了IAS与3种阳离子表面活性剂间的缓蚀协同效应,发现IAS与DTAB和TTAB间可能存在协同效应;进而通过静态失重、极化曲线、XPS等方法对缓蚀剂间的协同效应进行验证,并探讨了缓蚀协同机理。此外,本文的研究成果证明了课题组在文献[24]中提出的方法在一定程度上可以预测缓蚀剂间协同效应,有继续深入研究的价值。
1 实验方法
1.1 实验材料
实验中所用腐蚀试片为Q235钢,化学成分 (质量分数,%) 为:C 0.12-0.20,Si 0.10-0.25,Mn 0.30~0.70,P<0.045,S<0.045,Cu<0.15,Al<0.020,Fe余量。实验前将钢片切割成50×10×3 mm用于失重实验,10 mm×10 mm×3 mm用于电化学测试,5 mm×5 mm×2 mm用于XPS测试,用砂纸逐级打磨至2000#后,去污粉清洗,丙酮去脂,乙醇脱水,热风吹干后备用。
实验介质为3.5% (质量分数) NaCl溶液,实验前通1 h N2除氧,除氧结束后继续向溶液中通CO2/H2S混合气体 (20:20 mL/min) 1 h,制备腐蚀溶液,60 ℃时腐蚀溶液的pH值约为4.1。咪唑啉季铵盐 (IAS) 由北京龙飞恒信科技有限公司提供,纯度为95%;3种阳离子表面活性剂分别是十二烷基三甲基溴化铵 (DTAB)、十四烷基三甲基溴化铵 (TTAB) 和十六烷基三甲基溴化铵 (CTAB),均为分析纯。IAS与3种阳离子表面活性剂的分子结构如图1。
图1 IAS与3种阳离子表面活性剂的分子结构式
1.2 分子模拟
采用Material Studio中的Discover模块构建用于计算自由体积分数 (FFV) 的缓蚀剂膜模型并进行分子动力学模拟。模型包含一种或两种缓蚀剂分子 (分子总个数为50)。计算过程中先进行500 ps的NPT模拟用以计算缓蚀剂膜层的真实密度;之后用所得密度重新构建模型,并进行1000 ps的NVT模拟,NVT模拟后的终态结构用于计算膜层FFV值。模拟过程采用Compass力场;温度为333 K (采用Andersen恒温器控制);压力为1.01×105 Pa (采用Berendsen恒压器控制);长程Coulomb力及van der Waals作用力分别采用Ewald和Atom Based,截断半径为1.25 nm。详尽的模型构建及模拟过程可参见本课题组前期工作[24]。FFV的计算公式如下:
其中,Vfree为腐蚀粒子能够进入的所有孔洞的体积;除Vfree外,剩余的体积为Voccupy。
1.3 静态失重法
将称重后3个相同的试片置于700 mL腐蚀溶液中,用704室温固化硅橡胶封闭瓶口,并在60 ℃恒温水浴锅中保温。72 h后,取出的试片先浸泡在酸洗液 (15%盐酸+1%酸洗缓蚀剂) 中5 min,并用去污粉清洗,乙醇脱水,热风吹干后称重。
1.4 动电位极化曲线测试
在Gamry interface 1000电化学工作站上进行电化学测试,采用传统的三电极体系,参比电极和辅助电极分别为饱和甘汞电极 (SCE) 和Pt电极。测试前,需将工作电极浸泡在200 mL腐蚀溶液中1 h,使电极达到稳定状态。测试过程中,电位扫描范围为-200~+200 mV,扫描速率0.167 mV·s-1。采用弱极化区三参数法对极化曲线进行拟合,得到腐蚀电流密度 (Icorr) 等电化学参数进行拟合,缓蚀率 (ηp) 可由下式计算:
其中,Icorr与Icorr (int) 分别为溶液中不含有和含有缓蚀剂时的自腐蚀电流密度值。
1.5 XPS测试
样品制备过程与失重实验相同。试样从腐蚀溶液中取出后,直接热风吹干,置于干燥器中备用。采用PHI-5300 ESCA光电子能谱仪 (XPS) 进行能谱分析,扫描范围为0~1255 eV,步长1 eV,高分辨窄谱的扫描范围与所测元素有关,步长为0.05 eV。XPS数据采用XPSPEAK软件进行拟合分析,分析过程中以C在284.6 eV处的结合能校准其它结合能。
2 实验结果
2.1 分子动力学模拟
有机缓蚀剂通常会自发地吸附在金属表面来达到抑制金属腐蚀的目的。虽然缓蚀剂膜层可以有效防止腐蚀介质向金属基体表面扩散,但腐蚀介质依然可以通过缓蚀剂膜中较大的孔洞[19],且孔洞越大,腐蚀粒子的扩散速度就会越快。因此,缓蚀剂膜中孔洞的尺寸直接影响了缓蚀剂的性能。本课题组在分子动力学模拟研究中发现[24],两种缓蚀剂复配后对FFV值的降低程度与二者间的缓蚀协同效应强度存在相关性。依据这一研究成果,本节以H2O、H3O+、HCO3-、Cl-和HS-为探针,计算了IAS与3种表面活性剂按一定质量浓度比 (1∶0,1∶0.1,1∶0.2,1∶0.3,1∶0.4,1∶0.5,1∶0.7,1∶0.8,1∶1,1∶1.5,1∶2,1∶5,1∶8和0∶1) 复配后的缓蚀剂膜的FFV值,见图2。可以看出,随着探针直径的增大,各缓蚀剂膜的FFV值也相应减小,但无论使用何种探针,曲线的形状均一致。
图2 以H2O、H3O+、Cl-、HCO3-或HS-为探针时不同复合缓蚀剂膜层的FFV值随c%IAS的变化曲线
对图2a中3种复配体系的FFV计算结果进行分析可以看出,与表面活性剂相比,IAS单独成膜时,缓蚀剂膜的FFV值更小,为7.95%;当3种表面活性剂分别以不同比例与IAS混合时,复合缓蚀剂膜层的FFV值出现了不同程度的变化:(1) 对于IAS+DTAB体系来说,当IAS的质量浓度在复合缓蚀剂中的占比 (c%IAS) 在65%附近时,部分曲线在虚线下方,说明膜层的FFV值在这一区域内低于7.95%,也就是说,IAS与DTAB复合使用,可以显著增加膜层致密性,二者间可能存在较好的缓蚀协同效应;(2) 对于IAS+TTAB体系,当c%IAS在60 %附近时,有少部分曲线处于虚线下方,说明IAS与TTAB间也可能存在缓蚀协同效应,但协同强度小于IAS+DTAB体系;(3) 当IAS与CTAB复合使用时,曲线全部处于虚线上方,说明二者间可能存在拮抗效应。
总之,根据分子动力学模拟计算结果,推测IAS与DTAB、TTAB间存在协同效应,与CTAB间存在拮抗效应;协同效应强度的排序为DTAB+IAS> TTAB+IAS>CTAB+IAS。
2.2 失重实验结果
本节采用失重法对分子动力学模拟的推测结果进行验证。表1为静态失重法实验结果。从表中可以看出,与3种表面活性剂相比,IAS对碳钢的缓蚀效果更好。当3种表面活性剂分别与IAS复配时,复合缓蚀剂的性能排序为IAS+DTAB>IAS+TTAB>IAS+CTAB。此外,5 mg/L IAS+5 mg/L DTAB和5 mg/L IAS+5 mg/L TTAB的复配组合,复合缓蚀剂的缓蚀率明显大于分别使用5 mg/L单一缓蚀剂所得缓蚀率的和,即1+1>2,说明这两种复配体系具有较好的缓蚀协同效应。根据公式 (3) 可计算得到不同复配体系的S值,用以表明缓蚀剂间的协同效应强度。
表1 不同缓蚀剂在含CO2/H2S盐水中对Q235钢的缓蚀效果
其中,ηA和ηB分别表示A与B各自单独使用时测得的缓蚀率;ηAB表示A与B混合使用时测得的缓蚀率。若S值大于1,表明存在协同效应,S值越大,协同效应越明显。S值的计算结果列于表2中,可以看出,IAS与DTAB、TTAB间存在较好的缓蚀协同效应,与CTAB间存在拮抗效应;3种体系缓蚀协同效应强度的排序为IAS+DTAB>IAS+TTAB>IAS+CTAB。失重实验与分子动力学模拟所得结论完全一致,说明考察不同缓蚀剂复合后对缓蚀剂膜FFV值的降低程度,可以在一定程度上预测缓蚀剂间的协同效应。当然,该方法的适用性还需要通过更多的研究进行验证。
2.3 动电位极化曲线测试
极化曲线实验主要是对失重结果的验证。图3为Q235钢在含有不同缓蚀剂的CO2/H2S共存盐水溶液中测得的极化曲线。从图中可以看出,缓蚀剂的加入对碳钢阳极溶解和阴极反应均有一定的影响,曲线均有向左上方移动的趋势。当IAS与DTAB及TTAB复配使用时,腐蚀电位明显向正方向移动,而IAS与CTAB复配时,腐蚀电位略微正移。无论怎样,腐蚀电位的偏移程度均未超过85 mV,说明这些复合缓蚀剂均是以抑制阳极为主的混合型缓蚀剂[25,26]。
图3 Q235钢在含有不同缓蚀剂的CO2/H2S共存盐水溶液中测得的极化曲线
表2为对极化曲线进行拟合后得到的电化学参数,可以看出,IAS与DTAB或TTAB形成的复合缓蚀剂可有效抑制碳钢在CO2/H2S溶液中的腐蚀,而IAS与CTAB复配形成的缓蚀剂缓蚀性能较弱。极化曲线与失重实验所得结论保持一致。
表2 通过拟合Q235钢在含有不同缓蚀剂的CO2/H2S共存盐水溶液中测得的极化曲线得到的电化学参数
2.4 XPS测试结果
为了进一步研究IAS与3种表面活性剂间的缓蚀协同效应,本节采用XPS技术对带有缓蚀剂膜的钢片试样进行检测分析。图4为添加不同缓蚀剂时测得的缓蚀剂膜的XPS全谱。从图中可以明显地观察到F2p、O1s、N1s、C1s、和S2p峰的存在。C1s和N1s主要来源于吸附在碳钢表面的IAS和表面活性剂分子。O1s和S2p来自于铁的氧化物、碳氧化物和硫化物。Fe2p则归因于铁基体和它的腐蚀产物。
图4 Q235钢在含有不同缓蚀剂的CO2/H2S共存盐水溶液中浸泡24 h后测得的XPS全谱
图5为IAS与3种表面活性剂形成的缓蚀剂膜的N1s窄谱。图5中的谱图均可分解为位于402.3和399.8 eV处的两个峰。402.3 eV处的峰源于表面活性剂中的—N+(CH3)3及IAS中季铵化后的N原子[27,28],这些N原子周围均带有一个正电荷,因此下文中将402.3 eV处的峰简称为N+峰;而399.8 eV处的峰则归属于IAS中的C—N=C[29]。
图5 Q235钢在含有不同缓蚀剂的CO2/H2S共存盐水溶液中浸泡24 h后测得的N1s高分辨窄谱
通过对N1s高分辨窄谱的拟合,可以得到N+及C—N=C峰的面积及N+峰面积的占比,见表3。可以看出,IAS与DTAB复配使用时,N+峰面积的占比最大,说明缓蚀剂膜层中含表面活性剂 (DTAB) 的含量最多,证明了IAS与DTAB可以较好的共吸附在碳钢表面。N+峰面积的占比排序为IAS+DTAB>IAS+TTAB>IAS+CTAB,与缓蚀剂间协同效应强度排序一致。
表3 通过分析Q235钢在含有不同缓蚀剂的CO2/H2S共存盐水溶液中浸泡24 h后测得的N1s高分辨窄谱得到的参数
3 缓蚀协同机理分析
从表3可知,IAS与3种表面活性剂复配时,碳钢表面IAS的含量明显多于表面活性剂,而IAS的缓蚀性能却好于表面活性剂,说明复合缓蚀剂中,起主要缓蚀作用的物质可能为IAS,而表面活性剂则起到填补缓蚀剂膜层缺陷的作用。此外,虽然3种表面活性剂缓蚀性能的排序为CTAB>TTAB>DTAB,但与IAS复配后,协同效应强度的排序却为IAS+DTAB>IAS+TTAB>IAS+CTAB,说明协同作用的强度可能与表面活性剂本身的性能差异无关,而与缓蚀剂膜层的致密程度有关。
结合上述分析绘制图6,可以较形象的阐明IAS与3种表面活性剂间的协同作用机理。IAS单独使用时,缓蚀剂膜层存在大量的缺陷 (图6a);当IAS与DTAB复配使用时 (图6b),由于DTAB分子的空间位阻相对较小,其可以较充分的填充IAS膜层的缺陷,使得复合缓蚀剂的膜层更加致密;当IAS与TTAB复配使用时 (图6c),TTAB分子的空间位阻比DTAB大,其填充缺陷的能力有限,使复合缓蚀剂膜层产生较大孔隙,导致TTAB与IAS间的协同作用程度较小;而当IAS与CTAB复配时 (图6d),由于CTAB分子的空间位阻较大,其无法填补IAS膜层的缺陷,因此IAS与CTAB间不存在缓蚀协同效应。此外,CTAB的缓蚀性能相对较好,其与IAS间可能还存在着竞争吸附,这也可能是导致二者间产生拮抗效应的原因。
图6 CO2/H2S共存盐水溶液中IAS与3种表面活性剂在碳钢表面的成膜机理示意图
4 结论
(1) 在3种缓蚀剂复配体系中,复合缓蚀剂膜FFV值的降低程度与缓蚀协同效应强度间具有一定的相关性,所得结论与课题组前期研究成果保持一致。
(2) IAS可有效抑制Q235钢在含CO2/H2S盐水溶液中的腐蚀;IAS与DTAB间存在较好的缓蚀协同效应,与TTAB间的协同作用较弱,而与CTAB间存在明显的拮抗作用。
(3) IAS与3种表面活性剂形成的复合缓蚀剂均属于以抑制阳极为主的混合型缓蚀剂。
(4) IAS与3种表面活性剂复配使用时,起主要缓蚀作用的物质可能为IAS,而表面活性剂则起到填补缓蚀剂膜层缺陷的作用。不同复配体系协同效应的差异,可能与缓蚀剂分子的空间位阻有关。
免责声明:本网站所转载的文字、图片与视频资料版权归原创作者所有,如果涉及侵权,请第一时间联系本网删除。
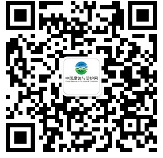
官方微信
《中国腐蚀与防护网电子期刊》征订启事
- 投稿联系:编辑部
- 电话:010-62316606-806
- 邮箱:fsfhzy666@163.com
- 中国腐蚀与防护网官方QQ群:140808414