坦克装甲车辆作为陆军的主要装备,一直是武器装备发展的重点。随着科学技术和武器装备的发展,战争对坦克装甲车辆的机动、防护和火力等性能提出了越来越苛刻的要求,传统金属材料已难以满足其各方面性能的要求。精细陶瓷作为21 世纪的三大工程材料之一,自20 世纪60 年代出现以来就以其优异的性能受到军方的高度关注,并不断应用于坦克装甲车辆等装备,取得了显著的军事和经济效益。
1 精细陶瓷的基本性能
精细陶瓷是利用高纯度的天然无机物及人工合成的无机化合物,采用多种先进制造工艺生产出的一种新型高技术陶瓷,是继钢铁、塑料之后的世界上第3 种工程材料,具有许多金属材料及高分子材料无法比拟的优良特性。
一是高温强度突出。常见的氮化硅陶瓷在1 400 ℃、碳化硅陶瓷在1 700 ℃ 时,强度仍高达700 MPa,而此时大多数金属材料早已软化或熔化成液体。在室温下,氮化硅和碳化硅的抗拉强度仅为钢的1 /3 ~ 1 /2; 但当温度在1 000 ℃以上时,氮化硅和碳化硅便具有比金属材料更高的强度。新研发的氮碳化硅复合陶瓷( 由氮化硅和碳化硅陶瓷复合而成) 在1 600 ℃时,不但可以拉长,还可以挤压,并具有韧性。此外,精细陶瓷还具有导热率低的特点。与钢铁相比,氮化硅是其导热率的1 /4~1 /3,氧化锆是其导热率的1 /15 左右。因此,精细陶瓷的高强度、低导热特点常被用来制造隔热零部件。
二是耐磨性能优越。相关试验表明: 在有润滑条件下,由金属与陶瓷组成的摩擦副不但陶瓷接近零磨损,金属的磨损量也比与金属相互配对时要小得多。特别是氮化硅与钢配对的摩擦副,即使是在恶劣的润滑条件下也具有极大的抗咬合耐磨损能力。
三是密度低、质量小。多数陶瓷的密度是金属密度的50%,如氮化硅和碳化硅的密度比铸铁小55%,与铝相比也仅大10%。因此用陶瓷制成的零部件不但自身质量小,对于一些运动件还可以减少驱动该部件所需的能量,有利于加快响应速度,并减小振动。低密度和高强度的综合特性,使得陶瓷成为制造高速运动零件的最佳材料之一。
四是耐腐蚀性能极佳。陶瓷惰性大,除氢氟酸及高浓度的碱以外,几乎对所有的化学品都具有优异的耐腐蚀性能。既可以用于制作整体零部件,也可以以涂层或衬里的表面处理形式使其他材料免于被侵蚀。
2 精细陶瓷在坦克装甲车辆上的应用
2. 1 在动力装置上的应用
发动机是坦克装甲车辆的心脏和原始动力的源泉,其性能直接决定了坦克装甲车辆的机动性能。在一定储油量条件下,发动机热效率越高,行驶里程越长,坦克装甲车辆的战役机动性就越好。提高坦克装甲车辆的机动性能关键因素之一在于提高发动机性能,并降低全车质量。理论研究表明: 在相同条件下,提高发动机的工作温度,其功率可相应增大,燃烧效率大大提高。而目前世界各国主战坦克的发动机主要以金属材料为主,铝合金的耐温极限为350 ℃,钢和铸铁为450 ℃,最好的超级耐热合金的耐温极限也不能超过1 093 ℃,金属材料的耐温极限极大地限制了发动机工作温度的提升。使用各种冷却装置不但使发动机设计复杂化,还增加质量,耗费大量功率。因此,专家预测,未来发动机推动比的提高,1/3 ~ 1 /2 的可能性取决于发动机材料性能的提高。寻找一种理想的材料来代替现行的金属材料是解决目前发动机结构复杂、热效率低的有效途径。
精细陶瓷由于其具有耐高温、耐腐蚀、耐磨损、密度小、导热率低等优异性能而受到广大发动机设计、研究人员的青睐。许多专家认为精细陶瓷在发动机上的应用是内燃机发明以来最鼓舞人心的新发展,它将最终解决发动机要在苛刻环境下工作的问题。20 世纪70 年代美国康明斯公司Kamo R 提出了陶瓷隔热涡轮复合发动机( 陶瓷绝热发动机) 的设想,即以精细陶瓷替代现行的金属材料制造发动机,采用减少或取消冷却系统、但保持较高工作温度的设计方案来提高发动机的热效率,并减小发动机质量。该设想得到了美国陆军坦克汽车指挥部和能源部的支持,并于1975 年开始实施一项绝热机的长期研究计划,目标是把绝热机技术应用于军用载重车及坦克装甲车辆,以满足坦克动力装置对单位体积功率大,高可靠性、可使用性、可维护性,以及耗油率低等多方面的要求。在该计划的支持下,美国研制的无冷却式陶瓷发动机坦克,比安装相同功率钢质发动机的坦克速度每千米缩短33 秒,体积和质量减少21%。日本小松制作所在运输省的资助下,于1976 年开展了缸径为125 mm 的全陶瓷喷涂涡轮复合绝热机的研制,并在1984 年完成1 000 h台架耐久试验后转入使用试验。德国联邦科学技术部于1980 - 1983 年开展了一项名为KEBOD的汽油机,柴油机陶瓷零件研究计划。
我国在“七五”、“八五”和“九五”期间也开展了陶瓷柴油发动机的研制工作,先后研制成功6105型无水冷柴油机、6135 型涡轮复合绝热发动机等几种先进陶瓷发动机。研制的6105 型无水冷发动机在进行400 h 台架试验考核后,被装入一辆有45 个座位的大型客车,往返于上海和北京之间完成了4 000 km的装车道路试验,油耗比增压水冷机最大下降5. 5%。此后,该客车作为班车经常使用,至今已累计运行5 万km 以上。“八五”期间,我国自行设计和制造的新型无水冷发动机,在气候情况和地理环境十分恶劣的沙漠中,安全行驶了将近2 000 km。这些先进陶瓷发动机的研制成功,缩短了我国与国际先进水平之间的差距,使我国成为了世界上少数几个能进行陶瓷发动机试验的国家之一。
但是,整体陶瓷发动机开发技术难度非常大,特别是陶瓷材料的高成本和低可靠性这2 大问题仍未圆满解决,在现阶段实现商业化和实用化还很不现实。因此,许多国家采用了先小后大、先近后远、先部件后整机、先常规后先进的方针,研究重点转向陶瓷零部件,并从20 世纪80 年代后期起成为陶瓷材料在发动机上应用的主流方向。到目前为止,这方面的成果已超出了实验室的研究阶段,许多陶瓷零部件已大批生产,并在坦克装甲车辆的发动机上得到广泛应用。如美国M1A1 坦克的AGT-1500燃气轮机采用了陶瓷涡轮叶片,使发动机工作温度提高到1 200 ℃,热效率提高45%,节省燃料30%,并提高了坦克的机动性能。M2 步兵车和M109 自行火炮等使用的AA750 型涡轮复合柴油机采用了整体陶瓷的陶瓷隔热层,汽缸盖底面和活塞顶采用了部分稳定氧气锆隔热,增压器内采用了氮化硅转子和轴承。同水冷柴油机相比,大大减少了零件数量、体积、质量、冷却水,并降低了耗油率。
进入21 世纪以来,美国为研制新型主战坦克,制造了以XAV-28 型低散热柴油机为动力的XAP-1000 整体式推进系统。该机在关键件上用陶瓷替换了传统的金属材料,并且采用陶瓷涂层与空气隙隔热,在高耐热合金活塞顶和合金铸铁缸盖上涂覆陶瓷涂层。新型坦克与传统的M1 主战坦克的燃气轮机相比,它的耗油率、体积和维修费这3 项指标都减少50%,超过了该国先进的整体式推进系统规定的要求。
俄罗斯的PT-5 等坦克在燃气发动机的转子叶片、透平盘和燃烧室等部件上使用了反应烧结SiC和Si3N4陶瓷,使得最高工作温度达1 400 ℃,功率在880 ~ 1 100 kW 之间,最大时速达85 km。
德国在“豹”Ⅱ等坦克中使用的MT800 系列柴油机在排气口镶嵌了陶瓷构件,燃烧室采用了陶瓷涂层隔热技术,大大提高了燃烧效率、降低了油耗。
日本将非氧化物陶瓷制造的燃气轮机用在坦克上,将坦克发动机的工作温度从900 ℃ 提高到了1 200 ℃,并节省燃料20% ~ 25%,提高功率30%,质量减小30%。这种陶瓷发动机不但可以使用汽油和柴油,而且还可以使用甲醇和煤油。
笔者等一直致力于工程陶瓷在坦克装甲车辆中的推广应用工作,先后研制成功陶瓷柱塞偶件、陶瓷出油阀偶件、陶瓷气门、陶瓷气门座圈等。相关产品和技术的开发丰富了工程陶瓷的应用范围,有力促进了工程陶瓷在坦克装甲车辆等武器装备中的应用。
2. 2 在防护装置上的应用
精细陶瓷的高强度、高硬度、低密度特性使得精细陶瓷成为制造装甲防护系统的理想材料,如陶瓷装甲的维氏硬度值高达1 500 ~ 3 500 HV,常用的碳化硼陶瓷其密度大约是装甲钢的1 /3 左右,同样的防护面积,质量却可大大减小。此外,精细陶瓷还具有比金属材料高得多的动力学弹性极限。利用陶瓷材料的密度效应、吸能效应、磨损效应等特性可显著地提高坦克装甲车辆的防护能力。
根据防护要求的不同,目前应用于装甲防护装置上的陶瓷材料主要有Al2O3、B4C、SiC、TiB2和AlN等5 种,其中应用于坦克装甲防护的主要为氧化铝和硼化物基陶瓷。相对金属材料而言,氧化铝陶瓷硬度是标准均质钢的3 倍以上,而体积质量不到标准均质钢的1 /2,且具有工艺性能稳定、价格相对较低、能够批量生产等优点,因而在坦克装甲车辆得到普遍采用。在上述5 种陶瓷材料中,硼化物基材料的抗弹侵彻性能最好,代表了坦克陶瓷装甲的发展方向,但由于其独特的金属、共价和离子型键相互作用,使得其存在熔点高、烧结困难、制备方法复杂、工艺稳定性难以控制、制造成本高昂等缺点,目前仅在欧美等发达国家得到应用。
陶瓷作为一种脆性材料,其断裂韧度值非常低,不能承受任何疲劳或结构负荷,也不能经受多重打击。因此,要达到满意的防护效果,通常采用与其他装甲材料组合使用的方式。自20 世纪60 年代美国首次在越南战场上使用Al2O3 /Al 陶瓷复合装甲以来,世界各国对陶瓷/金属轻质复合装甲进行了深入研究,陶瓷复合装甲得到快速发展。最初的陶瓷复合装甲主要为双层装甲系统,该系统利用坚硬的陶瓷面板来击碎或钝化弹丸,利用韧性背板发生变形以吸收弹丸和面板碎片的残余动能,从而有效抵抗弹丸侵彻。但是陶瓷与金属之间的弹性模量、硬度、密度等存在阶跃性变化,易于导致层间声阻失配和应力集中,极大限制了复合靶板的抗多次打击能力。
为解决这一难题,陶瓷复合装甲系统由最初的双层装甲系统发展到后来的多层装甲系统。到了20 世纪80 年代,西方国家和前苏联的主战坦克均已广泛采用了多层装甲系统,俄罗斯的新式坦克采用了6 层装甲系统。表1 列出了国外常见主要坦克使用的陶瓷复合装甲基本情况。
20 世纪90 年代以来,美国科学家提出了新型梯度装甲的概念,并逐渐成为当前装甲材料发展趋势之一。该梯度装甲材料采用高硬度、高强度的陶瓷材料作面板,采用塑性好、抗拉强度高的金属材料作背板,中间采用陶瓷含量沿厚度连续变化( 或阶梯变化) 的过渡层。该装甲材料既具有陶瓷材料抗侵彻的优越性能,又拥有金属材料的良好韧性,可以显著提高复合靶板的抗多次打击能力,并且可以通过对梯度形式和界面的设计来减小冲击波对复合靶的损伤,有效提高材料的抗弹性能; 同时由于所用组分为低密度陶瓷和轻质合金,因此也为装甲材料轻型化奠定了基础。
透明装甲陶瓷是新兴的一种陶瓷装甲材料,目前主要以铝酸镁尖晶石、硝酸氧化铝尖晶石和蓝宝石等材料为主。该系统由多层组成,第一层通常为硬度较高的陶瓷面板,用于破碎弹头或使其变形; 最后一层为韧性较高的聚合物,用于吸收弹丸和面板碎片的残余动能; 中间夹有柔性隔离层,以逐层添加的方式提供附加的防护能力,缓解由热膨胀错配造成的应力,并防止裂纹扩展。透明装甲陶瓷不但具有明显的防弹能力和较高的透明度,其表面密度还仅为现有玻璃的65% 左右。在美国“未来战斗系统”中,采用S2 玻璃纤维层压材料和陶瓷装甲制造的布雷德利战车车体,质量比原来减轻达35% ~40%,并能降低热信号特征、抑制噪声、节省费用和缩短生产周期。
丁华东等以B4C 基陶瓷为骨架,以Al 合金为金属填充物,提出了3DMC( Tri-dimension MicrostructureComposite,三维微观结构复合) 的新概念,通过粉末冶金的方式将Al 合金熔渗入B4C 基陶瓷骨架,制备了B4C 基3DMC 新型装甲材料,其结构模型如图1 所示。该材料具有硬度高,韧性满足需求的特点,成为集结构与功能于一体具有广阔应用前景的新型陶瓷基装甲材料。
2. 3 在火力装置及其他方面的应用
随着火炮口径的不断增大,炮弹初速越来越快,坦克火炮身管承受的压力和温度也越来越高。在高温高压以及火药气体的综合作用下,特别是连续射击时,炮管的烧蚀极为严重,严重影响了坦克装甲车辆战技性能的发挥。利用陶瓷的抗高压、抗蠕变、高熔点及高温化学稳定性好等特性,可有效抑制炮管的严重烧蚀,延长其使用寿命。美国陆军研究实验室对坦克炮用陶瓷内衬炮管的可行性进行了评估,并采用概率统计方法对120 mm 炮管进行了最佳化设计。研究认为: SiC、Si3N4和SiAlON 等是最适合用作炮管内衬的陶瓷材料,包缠纤维增强复合材料外保护套是解决陶瓷材料拉伸强度低、脆性大等缺点的最佳设计。采用陶瓷内衬复合材料炮管技术可使炮管寿命提高50%,炮管单位长度的质量减小5% ~ 25%,直接火力的炮口动能增加20%。陶瓷材料的高抗压和抗蠕变特性也使其成为口径20 ~ 30mm机枪枪管内衬的理想材料,通过合理设计,使陶瓷材料保持三向压缩状态,不但可克服其脆性,保证陶瓷衬管的安全使用,还可以有效抑制枪管的严重烧蚀。用微球型纳米陶瓷粉末制备的润滑剂,可使普通的滑动摩擦转变成了滚动摩擦,在火炮身管和枪管喷涂这种润滑剂后可提高弹丸初速15%以上,同时可有效减少磨损量,提高武器使用寿命。
利用精细陶瓷的化学稳定性好、耐腐蚀等性能,还能有效地解决两栖装甲装备的腐蚀与防护难题。在高温、高湿、高盐雾和高日照的服役环境条件下,两栖装甲装备腐蚀较为严重。据统计,两栖装甲装备下海训练后,如果不及时清洗, 20 ~ 30 min 后车体就会出现许多红色的浮锈, 12 h 后浮锈部位就会形成直径约1 mm 左右的锈斑。整个车辆会因海水的腐蚀而直接导致装备维修保养工作量增大、保障费用上升、装备故障率增高、战技性能急剧下降。相对金属材料而言,精细陶瓷的化学稳定性极好,在强酸、强碱环境中也能保持较好的物理化学性能。实践表明: 通过在装甲钢上喷涂陶瓷层的方式可有效阻止海水对装甲钢的腐蚀; 采用陶瓷泥技术可有效解决坦克轮毂处螺纹孔与螺栓的锈蚀难题; 氧化铝制的陶瓷炮塔座圈弹子可有效解决坦克炮塔与座圈的咬死与粘连问题。
在坦克夜视装置中,红外热像仪制冷压缩机中的压缩活塞和汽缸是红外成像系统中的一个关键组件,在实际使用过程常因各种力、力矩的作用使得工作表面形成划痕,磨损极为严重,致使压缩机在运行过程中振动加剧,噪声增大,影响制冷效果。美国Stirling 公司利用精细陶瓷耐摩擦、耐磨损的特点,开发的氮化硅陶瓷压缩活塞和汽缸寿命长达2 000 h,大幅度提高了微型斯特林制冷机的制冷效果。据报道,日本也开展了这方面的研究工作。
3 精细陶瓷材料的应用障碍及发展前景
实践证明: 精细陶瓷的优越性能对武器装备性能的提升具有重要意义,加快精细陶瓷在武器装备中的应用步伐、扩大其使用范围已成武器装备发展必然趋势。但昂贵的加工成本和较低的可靠性成为了束缚精细陶瓷在武器装备中应用的“瓶颈”。因此,要实现陶瓷在武器装备中的实用化和普及化,关键在于提高陶瓷的使用的可靠性,降低其加工成本。
为实现工程陶瓷的实用化和普及化,世界各国纷纷投入大量的人力、物力、财力进行研究,其中最具代表性的为美国。美国自1993 年起实施了一项为期5 年的热机用低成本陶瓷计划,研究开发先进的陶瓷制备工艺和质量控制技术,以期在提高质量和性能的同时,将陶瓷部件的成本降低一个数量级以上。从2000 年开始,美国又实施了一项为期20 年的美国先进陶瓷发展计划,该计划旨在将基础研究、应用开发和产品使用几个环节有机地结合在一起,力争到2020 年时使精细陶瓷能成为一种经济适用、性能可靠的首选材料,并广泛应用于工业制造业、航空、航天、军事以及消费品制造等领域。
经过半个世纪的发展,陶瓷的性能得到显著提升,加工成本明显下降。为解决精细陶瓷的脆性问题,人们相继提出了纤维增韧、晶须增韧、相变增韧、协同增韧及粒子强化等多种增韧强化措施,取得了很多有益的研究成果。特别是纳米技术的广泛应用,使得陶瓷材料的强度、韧性和超塑性大幅度提高,为精细陶瓷的应用开拓了新领域。此外,人们还受贝壳、竹、骨骼等天然生物材料的启发,提出了仿生结构设计概念,为陶瓷材料的强韧化提供了一条崭新的研究和设计思路。
陶瓷作为一种硬脆材料,其加工方式主要以金刚石砂轮磨削为主,加工成本占到陶瓷部件总成本的60% ~ 80%,部分甚至高达90%。因此,要降低陶瓷部件的成本关键在于降低其加工成本。为降低精细陶瓷的加工成本,在发展传统机械加工的基础上,ELID 磨削加工、化学机械加工、电火花加工、超声加工、激光/等离子加工、高压磨料水射流加工以及各种复合加工工艺等先进加工方法和加工工艺如雨后春笋,大大提高了陶瓷的加工效率并降低了加工成本。
可以相信,随着陶瓷性能的不断完善和使用成本的不断降低,精细陶瓷在坦克装甲车辆等武器装备上将发挥越来越大的作用。
免责声明:本网站所转载的文字、图片与视频资料版权归原创作者所有,如果涉及侵权,请第一时间联系本网删除。
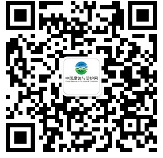
官方微信
《中国腐蚀与防护网电子期刊》征订启事
- 投稿联系:编辑部
- 电话:010-62316606-806
- 邮箱:fsfhzy666@163.com
- 中国腐蚀与防护网官方QQ群:140808414