钛合金的比强度较高、抗腐蚀性优异以及高温性能良好,在航空航天领域得到了广泛的应用。同时,钛合金与碳纤维复合材料具有相近的电极电位,成为复合材料结构连接的首选材料。随着对新型航空航天器结构减重、抗疲劳、耐腐蚀的要求逐渐提高和复合材料用量的大幅度增长,对钛合金紧固件的需求日益增加。对紧固件用材料的静强度和动强度都有严格的要求,这就较大地限制了可选择的钛合金种类。因此,近50多年来航空航天紧固件行业普遍使用的钛合金只有Ti-6Al-4V。
Ti-6Al-4V钛合金紧固件受到强度(1100 MPa级)和淬透性(最大可使用尺寸约19 mm)方面的限制,很难满足新型航空航天器主承力结构减重、可靠性和长寿命的要求。针对更高强度等级(1240 MPa级以上级)钛合金紧固件的需求,近年来开展了大量的探索工作[1,2,3,4]。目前有望成为用以制造1240 MPa级以上紧固件的高强钛合金大多为应力缺口敏感性材料,对表面的完整性要求较高。许多表面因素,如污染、划伤、夹杂、腐蚀等均能诱发疲劳裂纹的萌生和扩展,使紧固件断裂[5,6],这就使许多在研中的高强钛合金紧固件的疲劳性能难以满足要求。因此,系统分析表面缺陷引起的疲劳失效以及增寿机理,对钛合金紧固件的可靠使用有重要的意义。
Ti-3Al-8V-6Cr-4Mo-4Zr(Ti-38644)合金作为一种亚稳型β钛合金,具有比强度高、耐腐蚀性能好和室温成型性能强等优点,是制造高性能航空紧固件的理想材料。经过固溶+时效处理的Ti-38644钛合金其室温抗拉强度可达1380 MPa,通过控制时效温度和时间可在一个较宽的范围内调整其抗拉强度,从而满足不同强度级别紧固件的需要。
本文用Ti-38644材料研制1240 MPa级钛合金高锁螺栓,对断裂螺栓进行观察分析,通过力学性能检测、显微组织检测、断口形貌观察、断口组织和能谱分析等方法确定螺栓断裂的性质和原因,探讨Ti-38644高锁螺栓增寿机理并提出改进措施。
1 实验方法
实验用ϕ6mm的Ti-38644合金丝材的名义成分为Ti-3Al-8V-6Cr-4Mo-4Zr,相变点约730℃。退火态Ti-38644钛合金丝材的微观组织主要由β相基体构成,在晶界处存在少量初生α相,如图1所示。退火态Ti-38644钛合金抗拉强度为1067 MPa,屈服强度约为995 MPa,延伸率为9.4%,断面收缩率为47.3%。
图1 退火态Ti-38644合金的光学照片和扫描电镜照片
经热镦锻—热处理—机加工—磨削---螺纹滚压等工艺制备的轻型钛合金高锁螺栓,其结构如图2所示。在服役承载过程中螺栓头下圆角产生应力集中,在交变载荷作用下疲劳裂纹易在该位置萌生。为了抑制疲劳裂纹的形核提高螺栓疲劳寿命,将钛合金螺栓在滚压强化设备上进行了头下圆角部位挤压强化处理,以提高螺栓头杆结合处的抗疲劳强度。
图2 1240 MPa级轻型钛合金高锁螺栓实物
制备的Ti-38644钛合金高锁螺栓性能达到Q/9S288-2013《1240 MPa级抗拉型平头钛合金高锁螺栓》和Q/9S289-2013《1240 MPa级轻型钛合金高锁螺栓通用规范》的要求。疲劳试验依据GJB 715.30A-2003《紧固件拉伸试验方法疲劳》,利用QBG-100N0.2高频疲劳试验机进行高锁螺栓疲劳试验,疲劳高载=10.89 kN,低载为高载的10%,频率=100 Hz。疲劳断裂试样保留断口原貌,使用SUPRATM55型扫描电镜进行断口分析和显微组织观察。将断口观察后的试样沿对称中径面剖开,高度截取5 mm,制金相样。依次经过180目、500目、800目和1200目的碳化硅砂纸机械研磨,然后使用0.04 μm粒度的二氧化硅胶体溶液多次短时重复进行抛光。将光洁的试样表面浸入Kroll's腐蚀液中进行侵蚀,约5 s后取出,进行显微组织检查和EDS元素组成分析。
2 结果和分析
2.1 疲劳寿命
图3a和b给出了失效后的Ti-38644合金高锁螺栓,可见两个螺栓均在头下圆角处断裂,并具有相似的宏观损伤模式。疲劳实验结果表明,未经头下圆角强化后的高锁螺栓承受51700次循环加载后即发生断裂,而经圆角强化后的高锁螺栓疲劳寿命达到2783000次,其疲劳寿命提高幅度超过前者50倍。由此可以推断,圆角挤压强化工艺显著提高了Ti-38644高锁螺栓的疲劳寿命,但是挤压强化工艺对高锁螺栓疲劳失效位置没有影响,高锁螺栓头下仍然是薄弱部位。
图3 强化后的高锁螺栓和未经强化的高锁螺栓的疲劳失效试样
2.2 螺栓的显微组织
图4给出了Ti-38644高锁螺栓的金相显微结构,清晰地反应了经固溶+时效处理后的高锁螺栓微观组织中各物相的形貌及其分布。从图4a可以看出,Ti-38644钛合金高锁螺栓的微观组织由大量次生α相和β转变基体组成,次生α相以两种形态存在,即位于β晶粒的边界处存在的晶界α相,其在晶界连续存在,使β晶界清晰。另一种则是处于晶内纵横交错的短片层状次生α相。晶内析出的次生α相具有较为固定的位相关系,不同取向的片层状α相之间的夹角为60℃,并形成了网状结构,如图4b所示。弥散分布的晶内次生α相和连续的晶界α相阻碍位错在晶内和晶间的运动,对Ti-38644钛合金有强化作用。但是,很多研究显示,相界和晶界作为金属微观组织中的薄弱位置,容易萌生裂纹。对于Ti-38644合金,虽然晶界α相和晶内次生α相能阻碍位错的滑移从而提高钛合金的强度,但是大量的界面也为裂纹的萌生创造了条件。裂纹一旦在界面处形成就沿界面扩展,并彼此桥接形成常裂纹。此外,基体中的α相在循环加载的条件下与基体β相的变形协调性差,易在发生较大塑性变形时出现早期断裂。这表明,Ti-38644合金中起弥散强化的α相虽然可提高材料的整体强度,但是也可能显著影响疲劳裂纹的萌生。
图4 Ti-38644高锁螺栓的微观组织和β转变基体放大
2.3 疲劳断口形貌
图5给出了Ti-38644高强钛合金高锁螺栓拉伸疲劳断口宏观形貌。可见强化前后的高锁螺栓断口具有相似的特征,由于组织细小断口的形貌比较平整。在头下圆角部位分布有多处疲劳裂纹源。主裂纹源的区间范围比较宽,裂纹扩展较快。除主裂纹源外,沿头下圆角周向分布有多处裂纹源,在多裂纹源的共同作用下裂纹迅速扩展,致使头部断裂。对比图5a和b可见,在圆角挤压强化后的高锁螺栓的断口处保留了更多的残余材料。两个试样的断口具有相似的特征,均为线性疲劳源。疲劳断口可分为裂纹萌生区、裂纹扩展区和瞬断区三个部分。断口形貌SEM观察结果表明,高锁螺栓两个试样虽然疲劳寿命有明显的差异,但是疲劳的源位置基本相同,即疲劳裂纹在头下圆角表面发生形核。裂纹源从材料表面及次表面多处薄弱部位起裂,主裂纹源呈放射状并向中央扩展。在疲劳扩展区有细小的放射棱线和清晰的疲劳条带,失效方式以解理断裂为主伴有少量韧窝,如图5c和d所示。这个阶段的裂纹尺寸扩大到晶粒尺寸的数十倍,进入宏观裂纹扩展阶段。扩展区断面光滑、平整,可观察到清晰的疲劳弧线和细密的疲劳条带。扩展区占面积较大,循环加载时位于该区的材料反复变形,裂开的两个面不断张开、闭合并相互摩擦直至进入下一阶段。瞬断区具有明显的韧性断裂特征,是疲劳裂纹扩展到临界尺寸后失稳扩展形成的区域。虽然高锁螺栓头下圆角部位在螺栓的制造加工过程中进行了冷挤压强化[7,8],但是实际的工艺是通过三个滚轮的自转和径向进给实现的。现有的加工设备很难避免挤压不均匀或挤压力不足的情况,致使头下圆角应力集中部位仍存在相对薄弱点,为裂纹的萌生和扩展提供了条件。
图5 Ti-38644高锁螺栓的拉伸疲劳断口形貌
2.4 断口表面层的组织和能谱分析
图6给出了高锁螺栓断裂位置微观组织SEM照片。可以看出,未经头下圆角强化的高锁螺栓的微观组织形态与固溶+时效后的Ti-38644钛合金原始材料基本相同,如图6a所示。而经挤压强化处理后的高锁螺栓头下圆角处的Ti-38644合金表层,在剧烈塑性变形作用下次生α相和β转变基体形态呈明显的纤维状,两者在SEM照片下较难分辨。如图6b所示。沿表层向中心处观察,滚压工艺对微观组织的影响逐渐降低,其内部的次生α相与β转变基体恢复至固溶+时效处理后的形态。由此可见,滚压工艺产生的微观组织转变主要集中在表层区域,并形成一个厚度小于2 μm的变形层。其原因是,头下表层材料在滚压工装提供的切应力驱动下发生塑性延伸造成的,且在滚压过程中钛合金与滚压工装接触的部位产生的热量使加工表面处于高温。变形层就是在切应力和高温共同作用下形成的。结合疲劳测试结果可以推断,由滚压引入的表面变形层的厚度虽然较小(<2 μm),但对Ti-38644钛合金高锁螺栓寿命的影响十分显著。
图6 未经挤压强化高锁螺栓和挤压强化后的高锁螺栓断裂位置的微观组织
高锁螺栓强化层和基体能谱线扫描结果,如图7所示。从图7可见,表面变形层主要成份为Ti、Al、V、Mo、Cr、Si等元素,但其含量分布较为稳定,所在位置的影响可以忽略。这表明,虽然表面变形层与合金基体的微观组织形态的差异较大,但是元素组成基本相同。
图7 强化后的高锁螺栓的断口表面层能谱分析
TEM观察结果表明,晶粒内的微观组织有以下几种形态:(1) 在循环加载过程中,α/β晶界处形成的高密度位错缠结(图8a)或“驻留滑移带”。在交变载荷作用下驻留滑移带形成“挤出”和“凹入”,进一步产生应力集中,高密度的位错使裂纹在滑移带处萌生。(2) 较软的次生α相提早发生塑性变形,在变形的累积作用下α相内产生的大量位错塞积和层错(图8b)造成应力集中,最终导致α相破碎而形成微裂纹[9,10]。(3) α相发生孪生变形形成了孪晶(图8c)。这种孪晶是钛合金中α相的典型机械孪晶,孪晶与周围组织变形不协调使孪晶界面开裂,是微裂纹萌生的原因之一[11]。(4) 晶界处是变形最薄弱的环节,最早发生位错开动。在晶界处产生大量平行排列的位错线[12] ,并向次生α相和β相内滑移……两者结构和强度上的较大差异造成位于次生α相内的位错线细小且密集,β相内的位错线相对粗大且稀疏,少量位错线会在前端形成“Y”字形的分叉(图8c和d)。层片状的次生α相、晶界α相与β转变基体的结构和性能差别较大,使Ti-38644钛合金的整体变形协调性差。晶界α相和次生α相是变形薄弱处,在承受交变载荷作用时晶界α相、次生α相和晶界处易堆积位错产生应力集中,导致裂纹萌生。晶内微裂纹沿相界面或较软的α相扩展长大、桥接形成长裂纹[13,14]。若微裂纹萌生于晶界处,则可沿较软的晶界α和原始β晶界扩展形成长裂纹。由此说明,合金的显微组织对高周疲劳裂纹萌生有显著的影响。
图8 疲劳试样的微观组织位错组态
2.5 增寿机理
疲劳断裂实质上是一个累积损伤过程,发生断裂前经历了裂纹形成与扩展两个阶段。构件的疲劳寿命是裂纹形核寿命和扩展寿命之和[15]。裂纹在表面的形核和扩展主要受试样表面形貌、微观组织、材料性能及残余应力状态四个因素的影响,而滚压工艺对Ti-38644钛合金高锁螺栓的四个方面均有显著的影响。
在滚压过程中金属表层金属材料产生塑性流动,将表面不规则的凸出金属填入波谷中,从而降低了表面粗糙度,如图9所示。较为光滑的表面使高锁螺栓在承受交变载荷时不易出现明显的应力集中区域,从而抑制裂纹在表面形核。观察结果显示,在由滚压引入的塑形变形层内晶粒组织严重变形,其内部位错增殖、滑移、交割和缠结,一部分在晶内相互缠结形成位错塞积,另一部分排列成为亚晶界。这些亚结构一方面以加工硬化的形式提高了Ti-38644钛合金高锁螺栓头下区域的硬度,使其在循环加载时能够降低交变载荷对材料的影响[16];另一方面,材料内部的亚结构使晶格发生畸变,并在周围形成较大的应力场。在交变载荷的作用下,滑移依然是金属塑性变形的主要方式。在循环加载过程中,易滑移面上的位错首先开始滑移并随循环次数的逐渐增加,当其滑移至位错塞积和亚晶界附近时周围的应力场阻碍位错的继续滑移或迫使的领先位错沿其它滑移面继续滑移[17],降低了裂纹尖端开裂速度。后者分散了裂纹尖端能量,阻碍了裂纹的扩展。此外,严重变形后的晶粒在径向方向的单位长度内具有更多和更加曲折的晶界,也为裂纹的扩展增加了难度,从而提高了高锁螺栓的寿命。滚压工艺不但使表层材料发生塑性变形而导致表面硬化,同时也在材料内部引入残余压应力,明显改善材料的疲劳寿命。在材料中存在残余压应力场时,外加交变载荷中对裂纹张开起促进作用的正平均应力与残余压应力相互抵消,使裂纹尖端应力强度因子KI(张开型裂纹)下降,从而提高了裂纹扩展门槛值,抑制裂纹源的形成。而已有的裂纹也将在残余应力较高的位置降低或停止扩展,转变成非扩展裂纹,削弱裂纹群体效应对裂纹扩展的促进作用。
图9 Ti-38644钛合金高锁螺栓的疲劳强化机理示意图
3 结论
(1) Ti-38644钛合金高锁螺栓的疲劳性能优异,疲劳寿命达到2738000次,疲劳失效位置在头下圆角处并沿周向分布,失效方式以解理断裂为主伴有少量韧窝。
(2) Ti-38644钛合金高锁螺栓经滚压强化后在头下表面形成强化层,其主要成分为Ti、Al、V、Mo、Cr、Si等,与基体一致。强化层的厚度约为1.5 μm,强化层内的次生α相与β相剧烈变形,呈纤维状排布。
(3) 在交变载荷作用下有强化层的Ti-38644钛合金高锁螺栓的疲劳寿命更高。滚压强化工艺使高锁螺栓表面的粗糙度更低,不利于疲劳裂纹在表面形核。同时,引入的强化层因加工硬化和更加曲折的晶界阻碍了裂纹的扩展。强化层中的残余压应力降低了造成裂纹尖端应力强度因子下降,使裂纹的扩展减速甚至停止。
(4) 滚压强化工艺对提高Ti-38644钛合金高锁螺栓疲劳性能的效果显著。检查强化后的表面强化层,可作为一种检测方法和评价思路预估Ti-38644钛合金紧固件的疲劳性能。
免责声明:本网站所转载的文字、图片与视频资料版权归原创作者所有,如果涉及侵权,请第一时间联系本网删除。
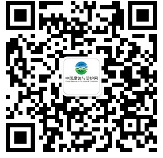
官方微信
《中国腐蚀与防护网电子期刊》征订启事
- 投稿联系:编辑部
- 电话:010-62313558-806
- 邮箱:fsfhzy666@163.com
- 中国腐蚀与防护网官方QQ群:140808414