导语:北京时间2019年8月22日,《自然·通讯》(Nature Communications)在线刊登了北京航空航天大学管娟副教授课题组的最新研究成果“野生柞蚕丝/碳纤维混杂构建抗冲击复合材料”(Integrating tough Antheraea pernyi silk and strong carbon fibres for impact critical structural composites)[1],首次将野生柞蚕丝和碳纤维混杂作为强韧相,构建了一系列高刚性、高强度的环氧树脂基体复合材料,实现了两种高性能纤维的完美结合,并为天然蚕丝纤维的应用开辟了全新的方向。文章的第一作者为杨康博士,第一通讯作者为材料科学与工程学院、先进结构材料与生物材料研究中心管娟副教授,资深通讯作者为美国加州大学伯克利分校Robert Ritchie院士,复旦大学邵正中教授、日本理化学研究所的Keiji Numata研究员参与合作。这项研究得到北京航空航天大学卓越百人计划和青年拔尖人才计划的支持。
图1 中国出产的桑蚕茧和柞蚕茧、对应两种蚕丝的功能分别为纺织和保护蚕蛹。
大自然赋予中国人的礼物——野生柞蚕丝野生柞蚕丝主要产于中国辽宁和山东等地,经过千万年的自然选择历程,其蛋白质分子序列结构(寡聚丙氨酸片段)、聚集态结构和纳米纤维结构相比桑蚕丝更接近蜘蛛牵引丝,可谓“蚕丝中的蛛丝”。此外,虽然柞蚕丝的拉伸强度只比桑蚕丝略高(均高于普通环氧树脂),但其拉伸断裂能150 MJ m-3远高于桑蚕丝~70 MJ m-3 [2],因此十分强韧。然而,柞蚕丝并未用来强韧化复合材料。本论文聚焦用力学性能优异的柞蚕丝来提升复合材料的韧性和吸能特性,可能为航空和汽车领域中轻质高韧性、抗冲击材料的选择提供新思路。
图2 a.柞蚕丝织物的微观形貌;b.柞蚕丝的2D同步辐射图谱显示beta折叠晶体结构;c.柞蚕丝蛋白分子结构示意图。
植根于北航的天然蚕丝复合材料研究牛津大学动物丝专家FritzVollrath教授预测蚕丝纤维复合材料最可能的应用领域为高缓冲吸能需求的结构材料,如军用头盔和风电叶片等。管娟课题组于2014年对蚕丝纤维复合材料(SFRP)开展系统研究表明[3-5],体积分数高于50%的桑/柞蚕丝纤维复合材料的冲击性能十分优异,并且具有-50℃的低温韧性;亚麻植物纤维能够有效调控蚕丝复合材料的力学性能,提升蚕丝复合材料的刚性和强度。无独有偶,大洋彼岸的休斯顿大学,YoussefK. Hamidi课题组也开展了蚕丝纤维复合材料的研究,为蚕丝增强体研发出更匹配的树脂体系[6]。
构建强度和韧性兼备的混杂纤维复合材料蚕丝纤维复合材料相对于多数的高性能结构材料,其强度和刚度仍有不足。本论文研究人员选用碳纤维和野生柞蚕丝纤维进行混杂,碳纤维增刚、柞蚕丝增韧,成功构建层内/层间混杂复合材料,既保证了蚕丝纤维复合材料在弯曲和冲击模式下的韧性,同时达到了工程结构材料对强度和刚度的要求,研究者还深入研究了经典混杂方式(如层间混杂和层内交织)和混杂比对复合材料力学性能的影响。
图3 高韧性柞蚕丝/高刚强碳纤维混编织物。
面向产业化——全面的性能评估本论文研究人员认为,工程材料的研究最终应指向产业化的应用,因此他们对柞蚕丝/碳纤维混杂复合材料各项性能进行了全面的评估:拉伸、弯曲、层间剪切、冲击、动态力学热分析、吸水老化行为、拉伸蠕变、弯曲蠕变等。丰富的实验数据表明交替铺层的柞蚕丝/碳纤维混杂复合材料在所有混杂材料里具有最好的纤维-基体界面,具有2倍于同体积分数碳纤维复合材料的冲击强度,并表现出优异的综合力学性能,为天然纤维复合材料产业化展示了应用前景。
图4 a.抗冲击性能指标;b.各项力学性能指标雷达图。 CFRP:碳纤维增强复合材料;5C5S-1:层层交替的丝纤维/碳纤维混杂增强复合材料;SFRP:柞蚕丝纤维增强复合材料。
文章官网链接:https://www.nature.com/articles/s41467-019-11520-2
参考文献:
[1]Yang K, et al, Nature Communications, 2019, 10;doi.org/10.1038/s41467-019-11520-2.
[2]Fu C et al. Advanced Functional Materials, 2015, 21(4):729-737.
[3]Yang K et al. Materials & Design, 2016, 108: 470-478.
[4]Yang K et al. Scientific Reports, 2017, 7: 11939-11947.
[5]Wu C et al. Composites Part A-Applied Science and Manufacturing. 2019, 117: 357-368.
[6]Hamidi Y K et al. Materials. 2019, 11,2135.
免责声明:本网站所转载的文字、图片与视频资料版权归原创作者所有,如果涉及侵权,请第一时间联系本网删除。
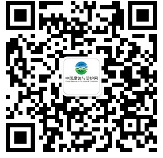
官方微信
《中国腐蚀与防护网电子期刊》征订启事
- 投稿联系:编辑部
- 电话:010-62313558-806
- 邮箱:fsfhzy666@163.com
- 中国腐蚀与防护网官方QQ群:140808414