高端高强度铝合金熔炼铸造关健制备技术,提升材料综合性的关键
2023-07-26 15:40:44
作者: 材料基 来源: 材料基
分享至:
现代铝合金材料正朝着高综合性能、低密度、大规格、高均匀性和材料/结构一体化方向发展,为航空航天、交通运输和高端装备的高性能制造提供支撑。高综合性能铝合金是高强铝合金材料科学与工程研究的热点。如上所述,新型高强铝合金的研发及现有材料性能的提升都与铝合金成分的创新相关。但是,当成分确定后,实现高综合性能的特征微结构需经过复杂的制备工艺流程才能最终获得,其间冶金遗传效应显著,各个制备环节均会影响微结构的形成和演变,从而最终决定材料的综合性能及其均匀性。如图6所示,高强铝合金材料的重要特征微结构可概括为:在Al基体上弥散分布着凝固形成的微米结晶相,高温沉淀析出的亚微米或纳米弥散相,时效析出的纳米亚稳相。基体组织可概括为:固溶体,晶粒,亚晶粒,晶界/亚晶界,胞状结构,织构,无沉淀析出带,空位与位错等。多尺度的第二相和复杂结构的基体决定了铝合金的性能。值得注意的是,除第二相、晶粒等组织结构外,铝合金材料织构也是研究人员关注的因素。
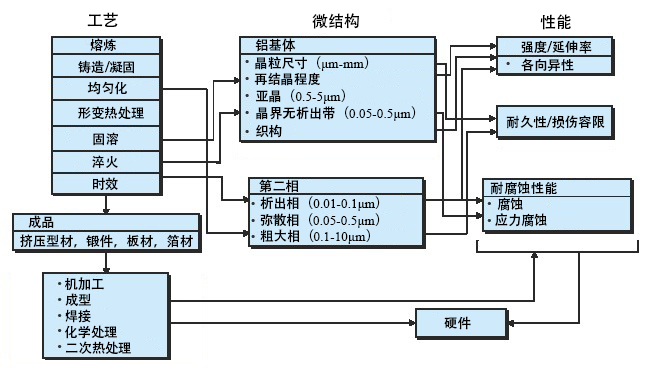
大规格高强铝合金材料制备面临多种挑战,需要发展系列制备技术,以达到组织细化、均匀化、亚稳化以及高综合性能化的目标。近几年,重点发展了大锭坯的高洁净化熔炼与均质铸造、大规格材料的均匀强流变加工和均匀组织的热处理精细调控技术。此外,为了减少或避免在制造过程中产生性能损失,发展材料/构件一体化成形/成性多种制备加工技术,使材料制备与构件制造两者融合,已成为一种发展趋势。合金组织的非均匀性短板效应是大规格/厚截面材料设计与制备的难点和关键。凝固、加工、热处理中流场、温度场、应力场的不均匀作用,往往会造成大规格铸锭成分的宏观不均匀性及非平衡结晶相和杂质相等组织的细观不均匀性、厚截面材料形变与再结晶组织的宏/细观不均匀性,以及热处理组织与残余应力的宏/细观不均匀性。为研究合金成分与组织引发的材料本征特性和制备环境引发的多场分布不均匀两方面作用规律与机理,近些年来,研发了宏/细观组织均匀化的熔铸、塑性加工、热处理等关键制备技术。大规格/厚截面高性能铝合金材料首先需要能稳定地生产出高品质大铸锭。高强度铝合金由于合金化程度高,结晶范围宽,氧化、吸气严重,易含气夹杂,成分宏/微分布均匀性难以控制,并且铸造时极易开裂,成品率低。宽型厚截面、大扁锭及大直径高合金化均质无裂纹铸锭的熔炼、铸造技术一直是世界铝加工界的热点。铝合金高质量铸锭的杂质与氢含量越少、洁净度越高越好,不同用途的铝合金材料,对铸锭中气体和杂质含量都有相应的标准。在高强铝合金的凝固理论涉及熔体的凝固规律,铸锭的显微组织、表面特性、应力应变分布和变形规律等。在此基础上,发展了多种铝合金熔体高洁净化、晶粒细化、表面亮化的熔铸技术,如气渣杂在线级联去除、电磁和/或超声外场调控铸造、油气润滑铸造、微震铸造、矮结晶器铸造等技术。高强铝合金的冶金缺陷来源于熔体中的气体与非金属夹杂物。由于表层张力、物理和/或化学吸附作用,气体与夹杂物更容易聚积,因此,除气装置往往也具有除夹杂物的功能,当然,去除夹杂物的同时,也有降低气体含量的作用。现代铝熔体净化装置的功能虽然相同,但其原理并不完全相同。因此,工程实际中,可以在生产线上设置相同功能、不同类型的多套装置,视高强铝合金的具体用途,有选择性地启动在线净化装置,从而保证熔体的洁净化程度与质量稳定性。铝合金熔体从熔炼炉(或静置炉)出来后,经过一个容器,该容器中装有一个转子,转子可通入气体,并将气体分成多股甩出进入熔体中,甩入熔体的气体被切割成气泡,气泡溢出的过程中,能将熔体中的气体与夹杂物吸附过来,并带到熔体表面,从而实现除气、除渣。转子材料既要耐铝合金熔体高温冲蚀、又不能与铝合金熔体发生反应。依据上述原理,开发出了多种铝合金气体喷射净化装置,如SNIF、MINT、AlPUR、LARS等等,这些装置大多对其具有创新特点的结构申请了专利进行保护。ALMEX推出的LARS在线净化系统,相对于其它气体喷射原理的装置,集成了多项配套技术,主要体现在气体预加热,熔池为下窄上宽敞开式、多边形、双熔池级联,具有很好的除气、除渣综合效果。采用带孔的泡沫陶瓷板过滤铝合金熔体,去除非金属夹杂物很早就在工程上获得了应用。随着对铝合金中非金属夹杂物含量的限制越来越苛刻,随后又研发出了多种级联的陶瓷过滤装置,已应用于多种高洁度要求的铝合金材料研制与生产。使铝合金熔体流经带孔陶瓷颗粒体,相较于多级泡沫陶瓷板过滤,可以取得更好的过滤效果。陶瓷颗粒过滤的优点主要体在:在相同的过滤体体积内,熔体与过滤体的接触面积更大;从上到下铺设不同直径的颗粒构成过滤体,过滤体内部可形成变化截面的细长孔道,熔体从一个截面流到另一个截面时,会产生低压涡流,从而提高过滤效益。此外,带孔的陶瓷颗料对夹杂物也具有吸附作用。因此,陶瓷颗粒过滤可以去除的夹杂物尺寸范围要大于陶瓷板过滤。上述过滤方法在原理上都存在一个问题:无法准确地知道陶瓷中吸附的夹杂物何时会达到饱和状态而产生“崩塌”,突然向铝合金熔体中释放出大量夹杂物。为此,又发展出了将带孔陶瓷管过滤方法。熔体首先流进具有过滤功能的陶瓷管内,在重力作用下,洁净的熔体从管内部向管外渗出,从而将夹杂物限制在陶瓷管内,流向结晶器方向的始终是洁净的熔体。陶瓷管因吸附的夹杂物达到饱和状态时,单位时间内流出过滤装置的流量会减少,很容易被仪器监测到。根据航空航天、交通运输领域应用的高强铝合金材料的几何形状与规格尺寸,半连续铸锭(DC)方式是工业生产高强铝合金材料的首选技术方案。为满足高强铝合金大规格材料制备加工的要求,大规格优质铸锭是关键。高强铝合金DC铸锭多采用矮结晶器。从降低结晶器高度这一基本特征出发,已经研发出了多种高强铝合金铸锭技术。下面简要介绍工程上应用较多的热顶铸锭与油气润滑铸锭,以及在较小规格高强铝合金铸锭中获得应用、目前还在进一步完善的大规格铸锭多外场(电磁、超声场等)调控铸锭技术。热顶铸造就是在DC铸锭结构的起冷却作用的结晶器上安装了一个起保温作用的热顶帽,在热顶帽的上部或侧面开一个缺口,使其与分流盘相连接,取消了漏斗,实现横向供流;热顶内的金属液面和流盘内的金属液面保持在同一水平,保持一定的恒定铝液静压力,同时降低熔体在结晶器中的凝固位置,从而实现了稳定的矮结晶器铸造和同水平铸造。如图7所示,热顶铸造结晶器由一个隔热的热顶部分(见图7中的装置2)和一个未隔热的冷却部分(即有效结晶部分)组成。热顶部分的作用是使熔体保温,并使铸锭上部熔体始终保持在同水平。结晶器冷却部分高度小,通常只有20~50 mm,其作用是使铸锭成形。铸锭冷却速度提高,液穴变浅、过渡带变窄,因而铸锭致密性提高,化学成分沿铸锭截面分布更为均匀,具有良好的组织均匀性。
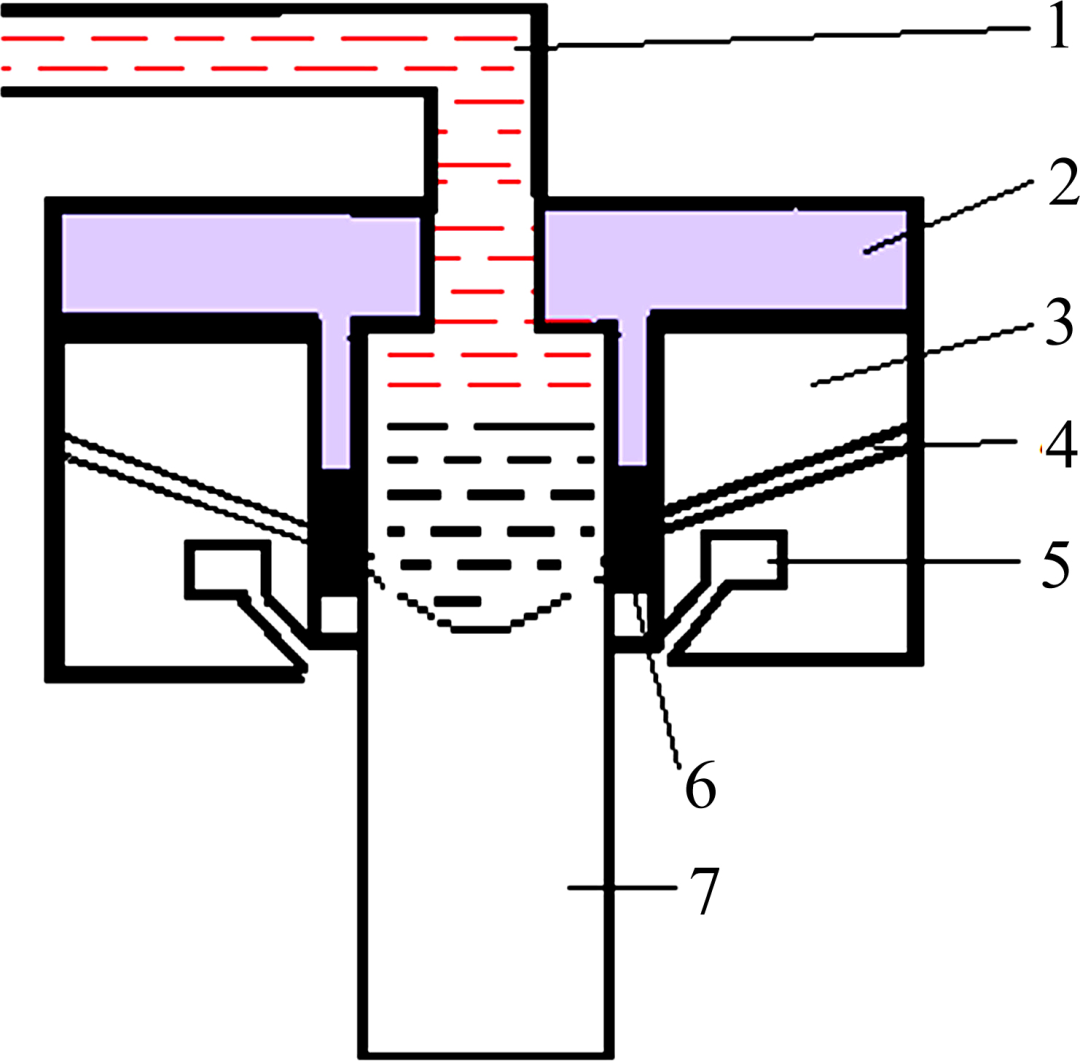
热顶铸锭时,由于结晶器冷却部分高度小,二次冷却水的逆流冷却作用较强,有效地防止了凝壳的二次重熔,从而抑制了偏析瘤的生成,同时在铸造过程中,有效地防止了金属液面处的过早冷却,使两相区变得相对稳定,能有效抑制冷隔,使得铸锭周边层逆偏析程度和深度大为降低。但热顶铸锭对结晶器设计和工艺参数控制精度要求更严格。气滑铸锭是一种将连续铸锭过程中凝固层与结晶器界面由滑动接触改为油气混合润滑状态的铸锭方法。如图7所示,高强铝合金的气滑铸锭往往与热顶铸锭技术联合使用。其原理是:在浇注过程中压缩空气和润滑油透过结晶器上的石墨环,在石墨环内壁形成油气膜,金属液在油气膜约束下外部凝固成壳移出结晶器,喷水进行二次冷却形成铸锭。由于在石墨环和金属液之间存在油气膜,可以显著降低一次冷却,减小凝壳厚度和液穴深度,避免低熔点偏析、冷隔,进而获得均匀细小的铸锭组织和良好的表面质量。油气膜可以降低结晶器与铸锭之间的摩擦力,同时由于液穴深度减小,可以减小结晶器的有效结晶高度,因此生产效率高,铸造速度快,比普通热顶铸造速度提高了25%。结晶器的热顶环与石墨环紧密配合,防止粘铝,引起铸铸锭表面出现拉痕。石墨环与结晶器为过盈配合,采用热装工艺装配,石墨环外壁上边沿和下边沿涂抹高温漆,以保证密封,防止空气和润滑油外漏。空气通过相应通道进入空气槽,在一定的压力下透过石墨环,润滑油通过相应通道进入润滑油槽,在大约比空气压力高10倍的压力下透过石墨环。空气和润滑油透过石墨环后,能在石墨环内壁形成油气膜,使铝液和结晶器不直接接触,因此形成均匀的油气膜晶是该项技术的关键环节。在铝液下降过程中,可设计成双排冷却喷水结构,增大冷却水的喷射角和喷射速度,从而消除冷却水喷溅,提高冷却效率,减少冷却水用量。从上述高强铝合金DC铸锭过程中两相区形成的基本规律可以看出,仅仅是通过结晶器的改进、优化,对两相区的影响是有限的。通过在结晶器外圈引入电磁场(见图8)、在结晶前沿和/或熔体中引入超声场,以及同时引入电磁场、超声场等复合外场,对凝固层的质量场、动量场及温度场施加影响,可以进一步增强对两相区尺寸、过渡区、液穴深度、内应力等凝固层特征参数,甚至结晶前沿的晶核特性进行精细调控,有望制备出规格尺寸更大、品质更优的铝合金铸锭。
免责声明:本网站所转载的文字、图片与视频资料版权归原创作者所有,如果涉及侵权,请第一时间联系本网删除。