高强度材料常因缺乏加工硬化而受到损害,使其易出现开裂和灾难性失效。具体来说,通过添加一种或多种元素的合金化方法可以提高纯金属和合金的强度,但往往会不可避免地降低塑性和韧性。由于元素在晶界( GBs )的偏析,合金化有时会面临晶间脆化问题 。例如,锡青铜合金(添加了2~20 wt.%的Sn以及其他元素如Zn、Pb、Ni、Al )已被广泛研究,以获得比纯铜更高的强度。但是由于脆性富锡δ偏析相沿晶界处填充,会诱发灾难性的沿晶断裂,导致锡青铜合金表现出有限的加工硬化稳定性,因此其塑性变形能力较低 。
最近一种具有吸引力的方法是利用纳米析出相来显著强化金属而不损失甚至提高塑性。其优异的强度源于共格或半共格的 纳米析出相,这些析出相呈均匀分布,产生大量的共格应变。同时,具有较小晶格失配的共格或半共格纳米析出相-基体界面有助于减少位错的塞积,从而缓解了加载时界面处的应力集中,降低了界面开裂的倾向,有利于保持良好的塑性。尽管如此,在多元合金(一类具有广阔应用潜力的高强度低塑性材料)中在保持强度提高的前提下实现显著的塑性提升仍然具有挑战性。
在这里,北京科技大学王自东教授、陈凯旋副教授等人报告了一种“晶内超细纳米析出”策略,在塑性差的锡青铜合金(即Cu-12Sn-1.5Ni合金)中实现了一种非常稳定的应变硬化响应,显著提高了塑性,并且伴随着强度的提升。具体来说,原始铸态Cu-12Sn-1.5Ni合金的抗拉强度 σu 为327.36±11.55 MPa,屈服强度σy为182.58±1.39 MPa,大约是粗晶纯铜的3倍(63±3 MPa ), 但伴随着较差的均匀延伸率εu为6.70±1.49%,约为纯铜(32±2% )的1/8。通过添加微量的Fe元素(<0.1 wt.%),我们在Cu-12Sn-1.5 Ni合金晶粒内部实现了高数量密度的超细Fe纳米析出相(ultra-nano Fe precipitation,简写为un-Fe)的均匀弥散分布,并且这些纳米Fe析出相具有极小的晶格错配度。细小弥散分布的晶内纳米Fe相不仅缓解了晶间断裂,还通过纳米Fe相-位错相互作用激活了稳定的应变硬化机制,从而形成超高塑性(εu约为20%)和强度提高(σu约为400 MPa,σy约为200 MPa)的独特组合。晶内超细纳米析出是一种很有前景的方法,未来可以广泛用于制造高塑韧性和高强度的合金。
图1a、b、d、e、g、h的OM显微组织表征表明,Cu-12Sn-1.5Ni-xFe (x=0, 0.08, 0.83 wt. %)铸态合金均具有粗大的树枝状枝晶组织,并且枝晶之间存在δ相。OM表征表明,与Cu-12Sn-1.5Ni合金(dgrain=97.0±16.8 μm,Aδ=11.20±1.26)相比,Cu-12Sn-1.5Ni-0.08Fe合金的晶粒尺寸(dgrain)和δ相的面积分数(Aδ)略有降低(dgrain=95.6±15.5 μm,Aδ=10.12±1.79%)。而在Cu-12Sn-1.5Ni-0.83Fe合金中,可以观察到晶粒尺寸dgrain明显降低至80.7±13.3 μm,同时Aδ为10.25±1.66%,与Cu-12Sn1.5Ni-0.08Fe合金相近。晶粒尺寸的减小与先前报道的Fe掺杂在铜 [24]和铜合金[13,14,,]中诱导晶粒的细化的结果一致,这是由于原位形成的Fe纳米析出相的异质形核作用 [13,14]。
图1f中的TEM图显示,Cu-12Sn-1.5Ni-0.08Fe合金中析出了高数量密度的(1.3×1023 m−3,见表1)超细点状Fe纳米析出相(直径为5.0 ± 2.7 nm,见图1k),且分布高度均匀。相比之下,图1i可以看到,在Cu-12Sn-1.5Ni-0.83Fe合金中,分散良好的点状(直径为5.7 ± 1.7 nm,图1l)和球状(直径为35.4 ± 7.6 nm,图1m)的Fe纳米析出相的数量密度较低(0.1×1023 m−3,表1)。后者合金中的Fe纳米析出相的尺寸分布更宽(图1k-m),且体积分数更高(表1)。通过STEM-EDS对点状和球状Fe纳米析出相的富铁成分进行了验证(图1j)。关于析出相特征的详细评估可参见补充数据的第1节。由于在Cu-12Sn-1.5Ni-(0.08, 0.83)Fe合金中,点状Fe纳米析出相的尺寸极小,因此将点状的Fe超细纳米析出相被称为超细纳米Fe(un-Fe)。而在Cu-12Sn-1.5Ni-0.83Fe合金中尺寸分布更宽的球状Fe纳米析出相(15-55 nm,图1i,l和m)被称为纳米Fe(n-Fe)。纳米颗粒诱导的晶粒细化只有在颗粒具有高效能(良好的晶体学匹配关系且尺寸适当)、足够的数量密度、合适的尺寸和足够宽的尺寸分布时才会发生[32,33]。在这种情况下,不同于Cu-12Sn-1.5Ni-0.83Fe合金中具有良好组合un-Fe和n-Fe的明显晶粒细化效果(图1g),单独具有超细尺寸且尺寸分布范围较窄的un-Fe对铜熔体的异质成核能力和效率较低,因此对铜晶粒细化效果很弱(图1d)
采用HRTEM对un-Fe和n-Fe颗粒进行表征(图2)。从<112>Cu带轴拍摄的图像(图2a)的快速傅里叶变换(FFT)图谱显示,un-Fe颗粒和铜基体均为面心立方(FCC)结构,二者呈cube-on-cube的取向关系(OR)。图2a表明,un-Fe/Cu界面清晰且完全共格,理论晶格错配度δ值极低,仅为0.0069,un-Fe颗粒周围没有明显的晶格畸变。需要注意,0.0069的δ值是通过理论计算得出的,计算公式为δ=2(aCu-aFe)/(aCu+aFe) ,其中aCu和aFe分别是纯Cu和γ-Fe的晶格参数 (aCu=0.3615, aFe=0.359 [,])。原则上,un-Fe颗粒和铜基体之间的晶格错配度受到其他合金元素(如Sn和Ni)的影响。颗粒主要由Fe组成,而基体主要由Cu组成,因此此处的晶格失配仅考虑纯Cu和纯Fe。此外,以真实原子尺度分辨率在图2b中15个平面层进行测量计算得到了un-Fe颗粒和Cu基体的(111)面的晶面间距d(111),其平均值分别为0.1976 nm和0.1959 nm。因此实验计算(111)γ-Fe 和(111)Cu 晶面之间的d值错配度为0.008nm。这种低的晶格错配度降低了析出相的形核势垒,从而使具有高数量密度和超细尺寸的un-Fe析出相得以形成和稳定。结合FFT滤波图像(图2b)和晶格条纹的强度变化(图2c),可以在HAADF-STEM下确定单个颗粒的尺寸。HAADF成像的衬度来源于低原子序数,因此,暗柱应该由Fe原子的分区引起。
图3.铸态Cu-12Sn-1.5Ni-(0,0.08,0.83wt.%)Fe合金的力学性能。(a)无Fe、un-Fe增强和un-Fe+n-Fe共增强铜合金(分别为0、0.08、0.83wt.%Fe) 的工程应力-应变曲线;(b) 实验测得的三种Cu合金的应变硬化率Θ=dσ/dε(其中σ和ε分别为真应力和真应变);(c)应变硬化指数(n=d(lnσ)/d(lnɛ))随真应变的变化。(d)拉伸性能和硬度柱状图(HV0.3),其中误差棒代表标准差,表示每种状态下进行的多次测试的离散程度;(e) un-Fe增强铜合金与其他铸造锡青铜合金的抗拉强度与总伸长率(ɛtotal)的比较[14,48-56] ,表明un-Fe增强超出了传统的塑性与强度关系范围;(f) 分别采用分子动力学模拟得到的嵌有球状FCC Fe粒子(直径分别为15.880 nm、12.410 nm、6.896 nm和3.998 nm)的30.3×30.3×30.3 nm³ Cu-Fe体系下沿[001]方向的工程应力-应变曲线(详见附加数据中的图S3,第4节),表明较小的颗粒产生更大的抗拉强度和塑性。
根据Hall-Petch关系[,],在Cu-12Sn-1.5Ni-(0.08, 0.83 wt. %) Fe合金中,晶粒细化有限,平均晶粒尺寸减小了1.4 μm和16.3 μm,对屈服强度σy的贡献很小,分别为0.1 MPa和1.3 MPa,因此Fe增强铜合金屈服强度的提高主要归因于纳米析出强化。在该材料中,un-Fe和n-Fe在Cu基体内提供了更强的相界面,需要更高的应力才能使位错切过或绕过。我们结合位错-颗粒相互作用的TEM表征研究了Fe增强铜合金的强化机制。图4为预先经过0.5%变形处理的Cu-12Sn-1.5Ni-(0.08, 0.83)Fe合金中位错与Fe纳米析出相相互作用的BF-TEM图像。位错在n-Fe/Cu界面上堆积(图4a中的I区域)或者弓出(图4a中的II区域)。显然,n-Fe颗粒没有被滑移位错剪切。相反,位错被un-Fe/Cu界面钉扎,归因于位错与un-Fe颗粒之间的相互作用,un-Fe似乎被位错剪切(图4b中黄色箭头标注)。因此,由un-Fe和n-Fe颗粒引起的位错钉扎促进了位错相互作用而提高强度 []。
研究表明,颗粒剪切和Orowan环机制[26,,]描述了纳米析出强化的屈服强度。因此,我们通过使用模量强化(∆σModulus)和共格强化(∆σCoherency)模型[46],估算了完全共格的un-Fe对Cu-12Sn-1.5Ni-0.08Fe合金的σy贡献分别为约38 MPa和约46 MPa,接近实验结果的25.99 MPa。同样在Cu-12Sn-1.5Ni-0.83Fe合金中,un-Fe (∆σModulus模量强化约13 MPa,∆σCoherency共格强化约16 MPa) 和半共格的n-Fe (~123 MPa,通过Orowan环模型估计) ,二者对σy的总强化贡献约为~136/~139 MPa,基本上与实际σy增量58.60 MPa一致。关于强化响应的估计细节请参阅补充资料的第2部分。需要注意的是,由于强化模型中使用的参数(表S2,补充资料)以及纳米析出相的统计结果(表1)不可避免的存在偏差,因此估算的强化贡献不能与实验值完全一致。
免责声明:本网站所转载的文字、图片与视频资料版权归原创作者所有,如果涉及侵权,请第一时间联系本网删除。
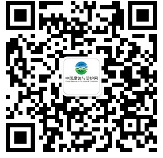
官方微信
《腐蚀与防护网电子期刊》征订启事
- 投稿联系:编辑部
- 电话:010-62316606
- 邮箱:fsfhzy666@163.com
- 腐蚀与防护网官方QQ群:140808414