在过去的一百多年以来,金属的疲劳失效问题一直是工业界关注的核心问题之一。统计表明,工业构件的失效中有80-90%属于疲劳失效。发生疲劳失效的构件一般承受动态载荷,如高铁的车轴、发动机叶片等,其工作应力往往显著低于材料的屈服应力,构件失效一般发生在104-107,甚至109周次以上的循环载荷。金属的疲劳过程一般为:构件内部微缺陷或局部应力集中→局部塑性变形→局部微裂纹形成和发展→宏观裂纹出现→构件失效。现有的无损检测方法只能检测到长度2mm以上的宏观裂纹,对于尺寸更小的微裂纹,目前还缺少有效的检测方法。
最近,北京大学工学院李法新课题组在金属疲劳领域取得了突破性进展,他们提出采用测量内耗的方法来监测铝合金的疲劳失效,相关论文“ Detecting fatigue in aluminum alloys based on internal friction measurement using an electromechanical impedance method”作为主编精选(Editor's Pick)发表于Journal of Applied Physics。课题组2019级硕士生唐骥骅和2018级博士生谢明宇为论文的共同第一作者。
李法新课题组前期提出了基于压电机电阻抗、既准又快的模量内耗测量新方法(Rev Sci Instrum 2020, Editor's Pick, https://doi.org/10.1063/1.5135360),该方法测量模量的精度比ASTM标准高一个量级,测量内耗的误差小于2E-5。在此基础上,他们提出采用测量内耗的手段来监测金属的疲劳过程。实验结果表明,铝合金在拉压对称的疲劳加载过程中,内耗随加载的周次单调增加,破坏前的内耗值可以达到初始值的3倍以上(图1b),这表明内耗对于金属的疲劳损伤非常敏感。相比之下,样品的共振频率在失效前仅降低了不到2%(图1c)。不同的样品在疲劳过程中内耗的变化曲线可能相差很大(图2),但有一点是共同的,即在疲劳失效的后段,内耗随疲劳周次增加得很快,这一阶段可认为是微裂纹的形成和发展过程。
图1. 典型铝合金构件在不同疲劳周次加载后的:(a)电纳曲线;(b)内耗;(c)共振频率。
图2. 另外2个铝合金样品在疲劳过程中的内耗和共振频率变化
基于铝合金疲劳监测的实验结果,李法新课题组提出了基于内耗测量的金属疲劳失效预警准则,可在构件50-80%疲劳寿命时给出有效的预警。而且,由于微裂纹导致的疲劳失效是大多数结构材料失效的主要形式,该疲劳失效预警准则同样可适用于复合材料、陶瓷等其它结构材料。进一步,由于大部分机械类损伤失效可以归为材料内部连接的松动(疲劳),或者不同构件之间的连接松动(焊点失效,螺栓松动,胶层劣化等等),而这些内部或外部连接的松动将显著增大材料的内耗(或结构的阻尼)。因此,测量构件的内耗(或阻尼)可有效地判断构件的机械损伤,这比传统的测量频率(或模量)的方法更为敏感和有效。
免责声明:本网站所转载的文字、图片与视频资料版权归原创作者所有,如果涉及侵权,请第一时间联系本网删除。
相关文章
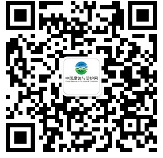
官方微信
《中国腐蚀与防护网电子期刊》征订启事
- 投稿联系:编辑部
- 电话:010-62316606-806
- 邮箱:fsfhzy666@163.com
- 中国腐蚀与防护网官方QQ群:140808414
点击排行
PPT新闻
“海洋金属”——钛合金在舰船的
点击数:7437
腐蚀与“海上丝绸之路”
点击数:5962