“我们发现粉末合金的性能比铸造性能提高了140兆帕,这意味着如果拿粉末合金来做氢泵叶轮,可以承担更高的转速,而且使用起来更加可靠。”
徐磊
中国科学院金属研究所研究员
我今天给大家分享的主题是“氢泵叶轮攻关记”。
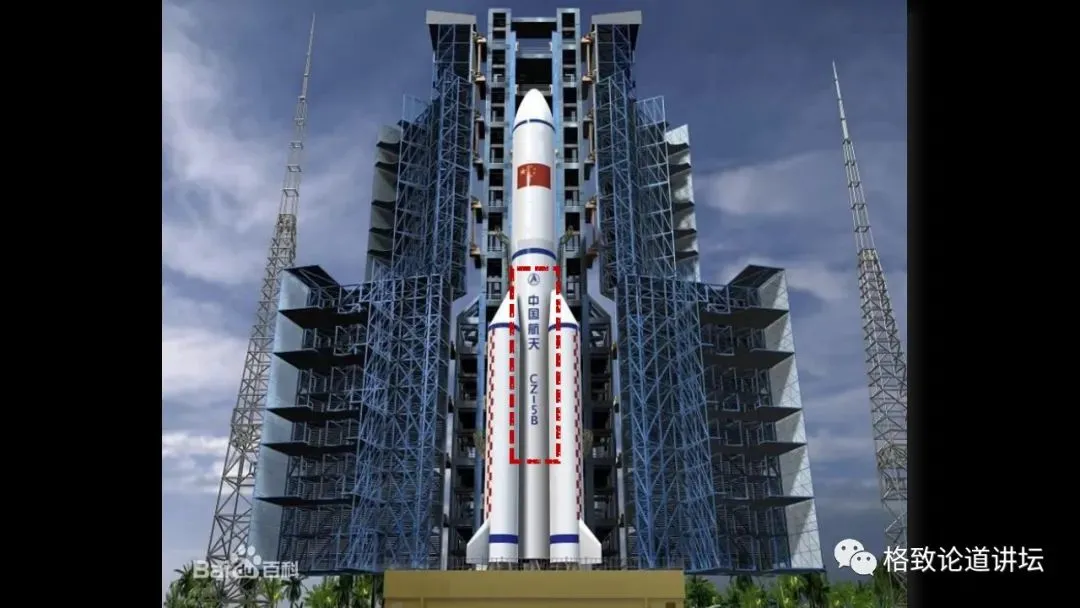
这张照片我们一定不太陌生,这是我国目前近地轨道推力最大的运载火箭:长征五号B型运载火箭。
在火箭液氢液氧发动机的心脏部位,有一个至关重要的核心部件,就是图片中画红框的位置。
为了这个核心关键部件,我和我的团队用了大概12年的时间,才把它研制成功,这个零件就叫“氢泵叶轮”。
我们首先看一下氢泵叶轮的工作环境和工作地点。
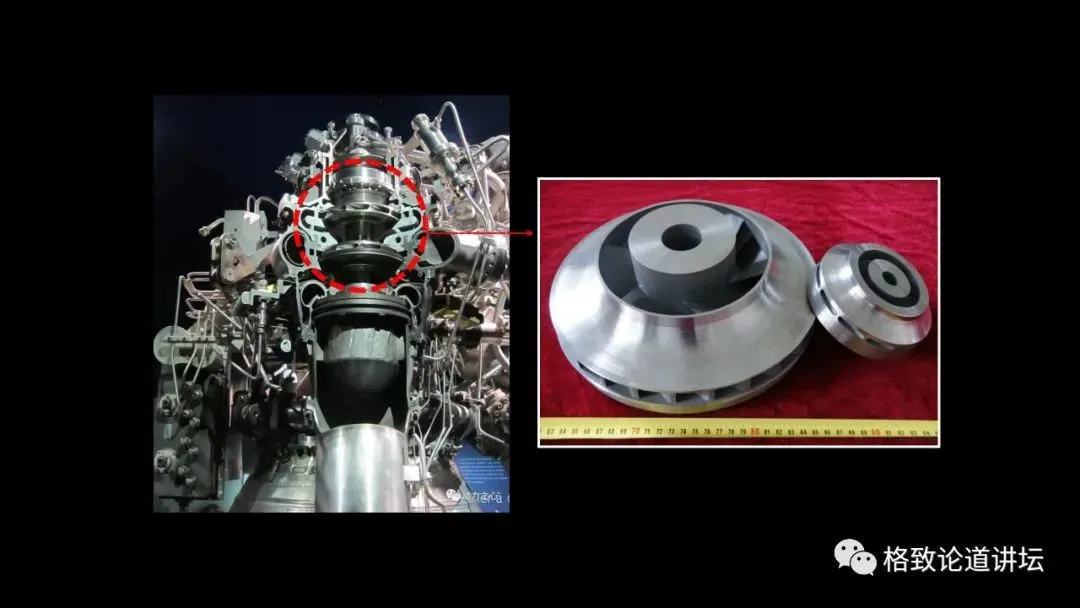
左图是它工作在液氢液氧发动机的氢涡轮泵中,红圈的部位就是氢泵叶轮的工作地点。
右图是我们现在做的给长征五号配套的XX-77和XX-75D的氢泵叶轮。
它看起来不是那么大,怎么研制起来难度这么大,用了十几年的时间?
我们先要看一下它的工作环境。
氢泵叶轮工作在氢涡轮泵中,也就是液氢的环境中,是零下253度。
它的作用是将火箭体内大量低温低压的液态氢气高速输送到燃烧室中,与燃烧室中的液态氧气爆炸混合,对火箭产生推力。
如果想在短时间内将液态氢气输送到燃烧室中,叶轮的转速达到每分钟35000转。
在如此高的转速下,它的轮缘线速度达到每秒430米,这是什么概念呢?
声音的速度是每秒340米,它比声音的速度还要快。
为了更形象地介绍氢泵叶轮的工作环境到底有多么苛刻,我举一个例子。
2012年,我针对这个问题,向当时长征五号火箭的副总师王维彬请教。王总告诉我,液氢经过氢泵叶轮加压以后,泵后压力达到16.5兆帕。
这就意味着氢泵叶轮要在短时间内将液氢输送到两万多米的高空,也就相当于三个珠穆朗玛峰的高度。
这么严苛的使用环境,除了要求材料在低温下有很好的强度外,还要保证它能够平稳稳定地运转。
这就和汽车动平衡比较类似,如果汽车车轮动平衡不好,会带来几个问题:第一,方向盘抖动;第二,车轮抖动;第三,轮胎异响,可能还会翻车。
因为火箭发动机氢泵叶轮是输送动力的,如果它运转不平稳,火箭会因瞬间丧失动力而坠毁,这个恶果非常可怕。
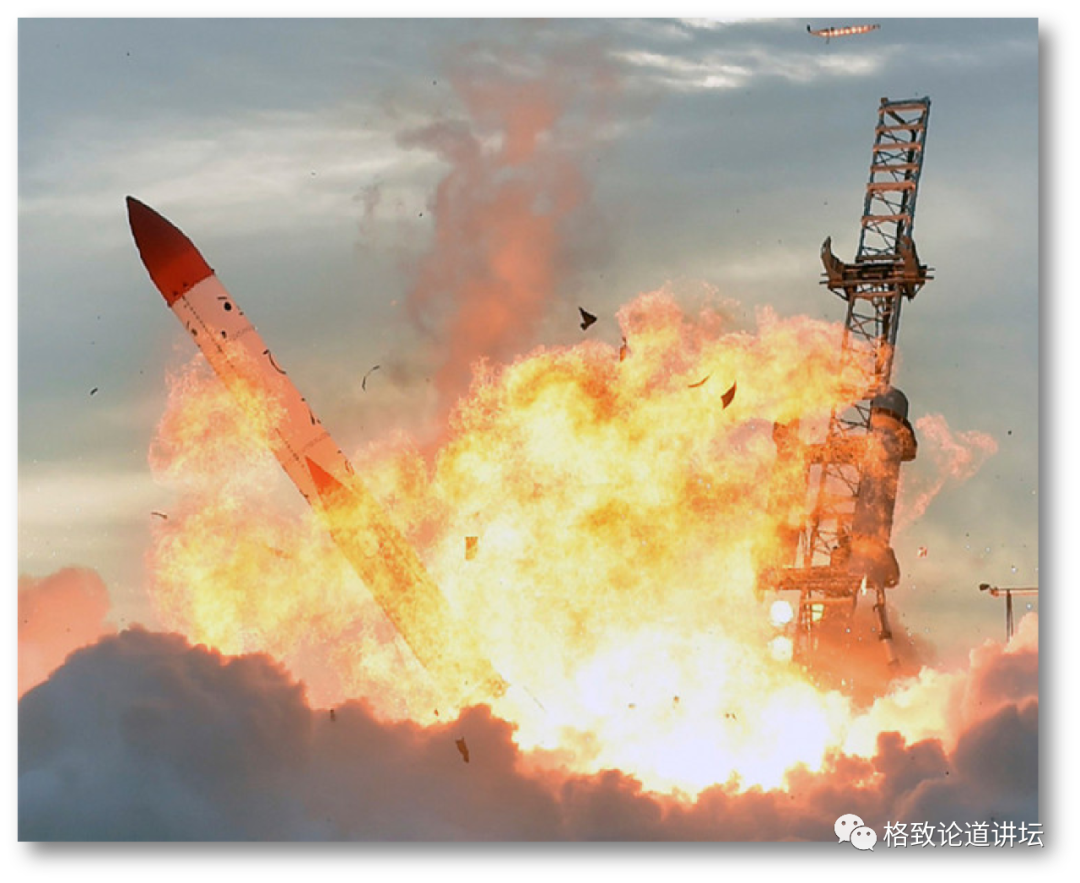
长征五号运载火箭研制初期,氢泵叶轮采取传统的精密铸造的方式来制备,但精密铸造有它本身难以克服的“缩孔、疏松”的铸造缺陷。
另外,它的铸造强度比较低,材料如此高强度地运转,经常会出现掉块的现象。
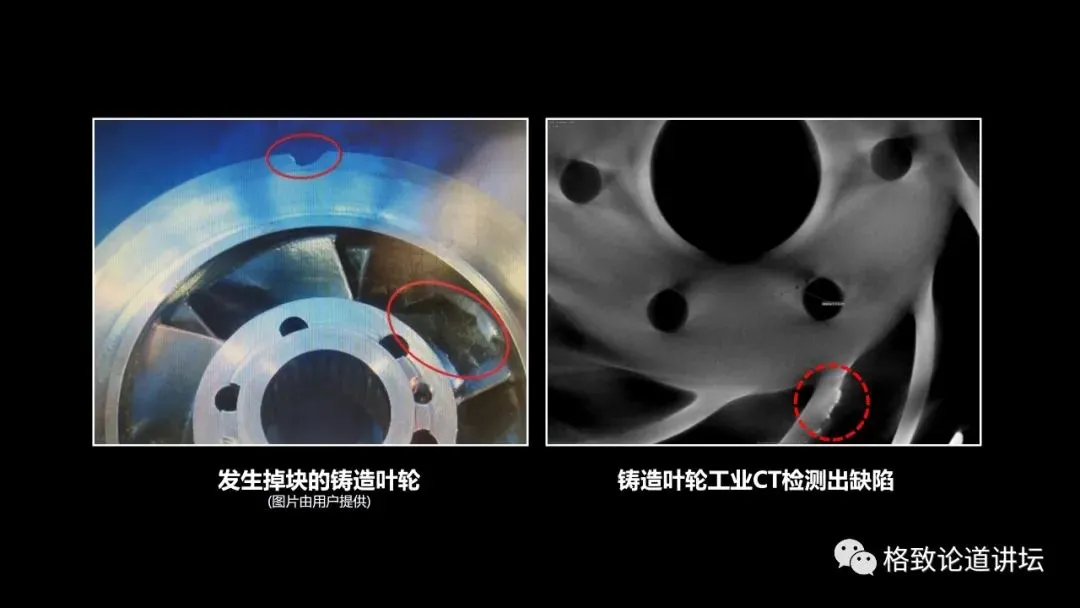
如同照片中的红色部位,叶轮做完实验后,叶片掉一块,边缘也掉一块。
有时掉块恰好会堵住燃料管道,有一次堵住管道后把发动机试车台都烧红了,险些造成爆炸,酿成重大的安全事故。
此外,我们采用工业CT对叶轮的叶片进行了探伤,我们发现,它有一些“缩孔、疏松”的铸造缺陷。
这种缺陷在高速旋转的过程中,会给用户带来很大的安全隐患。
思想晚餐
已完成:20% //////////
粉末冶金成形
用户一直为氢泵叶轮头疼,因为铸造叶轮出现这么多问题,就想着能不能采取一种新的成形工艺方法解决这个问题。
这个答案是肯定的。
因为早在上世纪八九十年代,美国和俄罗斯这种航天强国,他们也发现铸造叶轮存在安全隐患,纷纷采用粉末冶金成形的方式制造了氢泵叶轮,并获得了很好的效果。
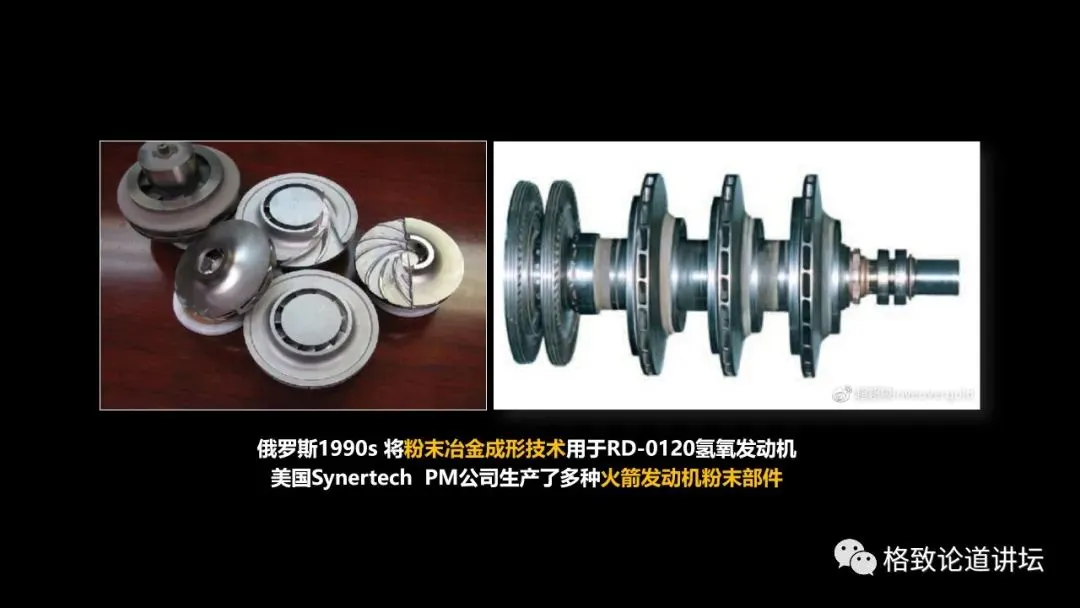
什么是粉末冶金成形?
简单地说,粉末冶金是精密铸造的升级版。
精密铸造采用的原材料是熔融的金属液体,它的成形方式是这样的:把金属液体熔化后,浇铸到预先制备的模壳中,模壳一般都是陶瓷材料所做的,金属液体在模壳中逐渐凝固,形成铸造合金,最后把模壳敲掉,得到精密铸件。
而粉末冶金采用的原料是松散的粉末颗粒,是将粉末填充到模具中,模具通常用术语,叫做“包套”。
包套的作用是容纳变形,紧接着松散的粉末颗粒在高温高压下发生烧结,致密化形成一个致密的粉末合金,最后再将包套去除掉,就得到了粉末零件。
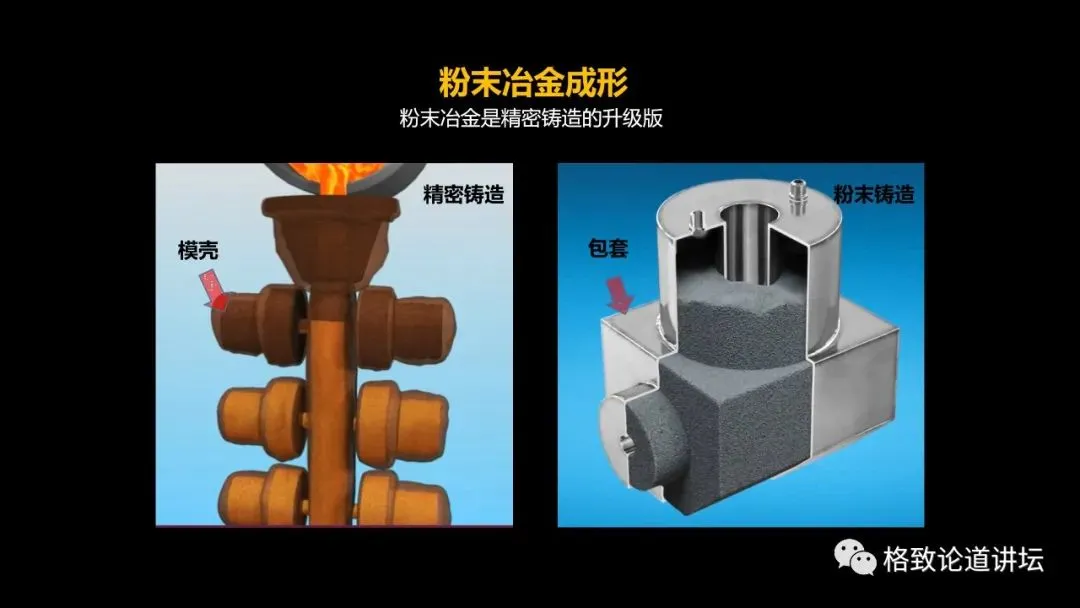
粉末冶金既然在国际上有这么多应用,美国和俄罗斯都纷纷采用这个方式制备氢泵叶轮,那么它有什么好处呢?
第一,省料。
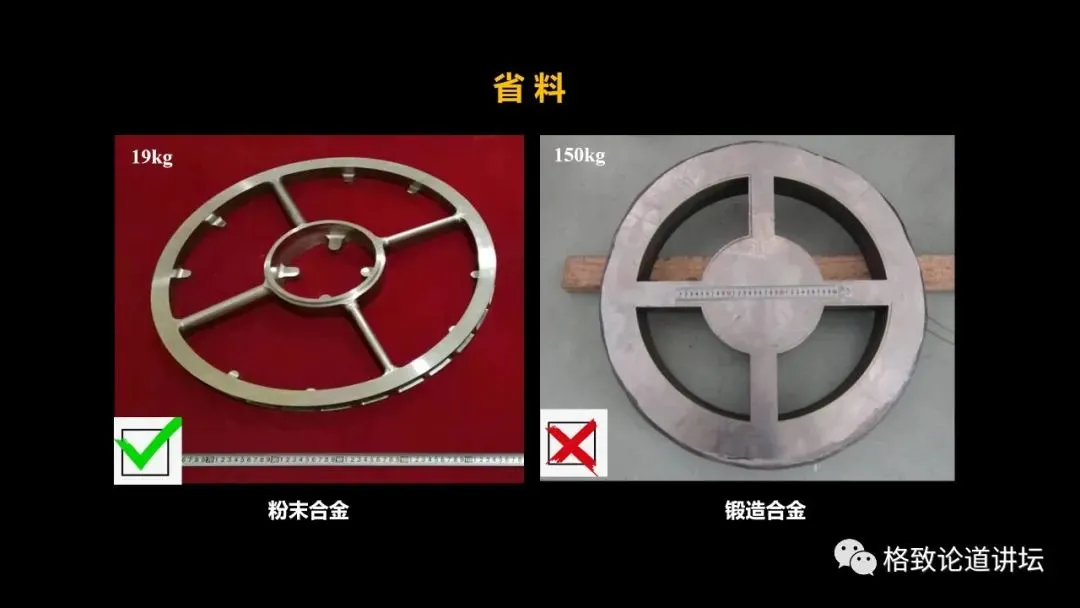
左上角是我们为航天用户做的一个盘件,我们的毛坯重量不到20公斤。
这个盘件交给用户后,用户再简单地加工几个安装边,打几个孔,就可以投入使用了,时间不超过一周。
而采用传统的铸造加锻造方式,第一个问题是费料。
这个毛坯的重量是150公斤,150公斤的毛坯交付给用户后,还要经过将近60天,也就是两个多月的精加工,然后上五轴加工中心铣出零件。
此外,由于这个饼子是锻造出来的,轮盘的边缘和中心还存在一些性能的差异,会在使用中带来安全隐患,用户也是不满意的。
另外,最重要的一点,粉末合金有一个无可比拟的天然优势,就是材质均匀、成分均匀。
下面这两张图是采用X射线三维成像技术得到的,就是对粉末合金的成分和锻造合金的成分进行切片扫描。
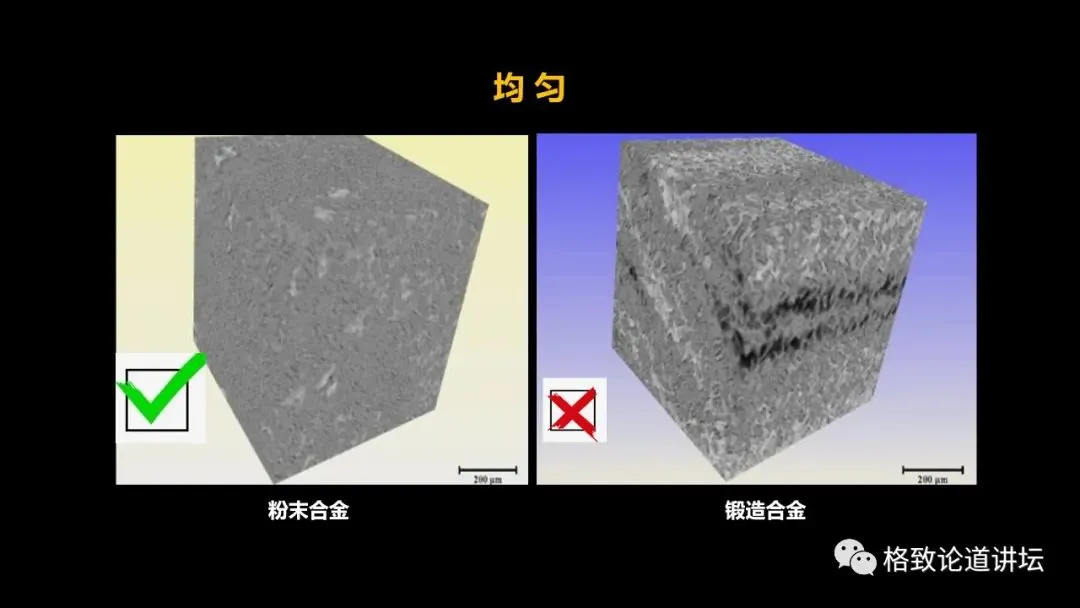
图中色差变化不大的,就说明它的成分均匀、材质均匀性好。
右图是锻造的,可以发现黑色和白色的亮暗不同的条带,说明成分是不均匀的。
这种不均匀的材质如果是一个转动件,在转动过程中有很大的安全隐患,所以这就是粉末合金的另外一个优点。
我国是从什么时候开始研制粉末冶金成形部件,特别是粉末氢泵叶轮这个零件的呢?
我所在的金属研究所钛合金研究部,一直在持续追踪国际上先进钛合金的发展方向。
2005年,我们在国家的支持下,建成了国内第一台洁净雾化的钛合金制粉设备。
很有幸,2008年,我们承接了国家长征五号叶轮粉末冶金氢泵叶轮的研制项目,也就是从12年前,我国正式开始粉末冶金氢泵叶轮的研制工作。
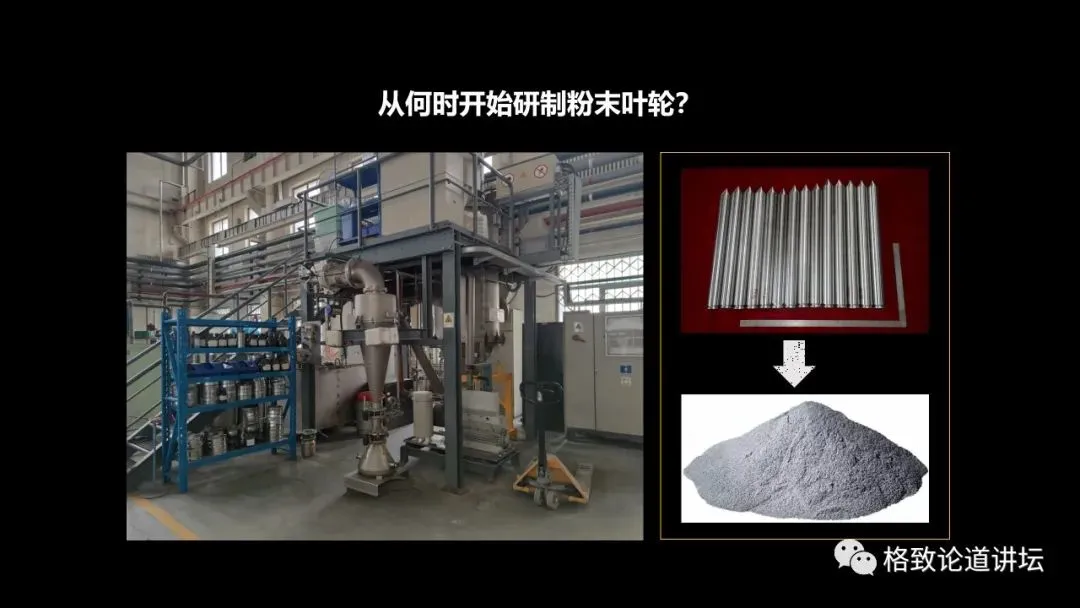
这台设备的作用,就是将右上角那块红布上放的致密的合金锻棒变成松散的合金粉末,就是预合金粉末。
思想晚餐
已完成:40% //////////
粉末合金的制备
有了粉末后,我们就去制备粉末合金。我们要进行性能摸底,我们制备的粉末合金究竟能不能达到用户的使用要求?
粉末合金的制备分为以下几个部分。
第一,要制备包套。包套的英文单词是capsule,就是胶囊的意思。
大家都吃过感冒药,感冒胶囊外面有一层皮,里面是松散的药的粉末,而我们这个就是金属胶囊。
我们要将金属做成一个胶囊的形状,然后把金属颗粒,填充到包套即胶囊中去。
第三步就是对包套进行封装除气,然后进行最重要的一步:热等静压。
热等静压的目的是将松散的粉末变得致密化,最后得到致密的粉末合金。
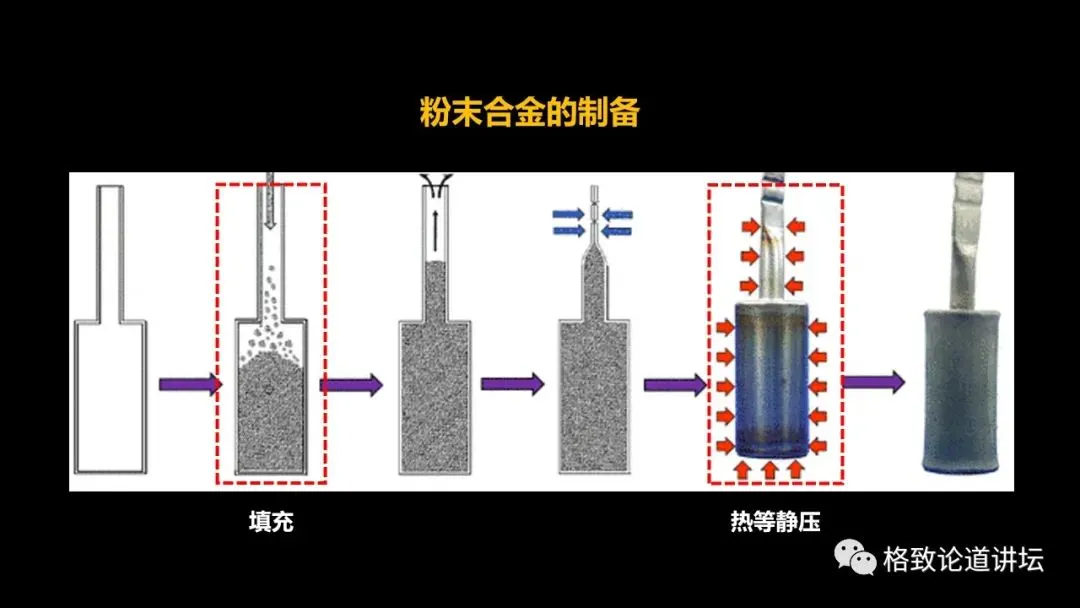
小朋友有可能会想,这个是不是在折腾啊?刚才刚把致密的棒料变成松散的粉末,现在又把松散的粉末压成了致密的棒料,这么折腾到底是为了啥?
第一,可以让它的材质更加均匀。第二,提高性能。
粉末冶金的环节非常多,而且影响因素也非常复杂,举两个影响工艺的最重要的环节。
一个是粉末填充,因为必须填充到一定的致密度,保证其稳定,才能保证后面工序的进行。
影响填充的一个最重要的因素就是粉末粒度,即粉末颗粒的大小对它到底有什么影响。
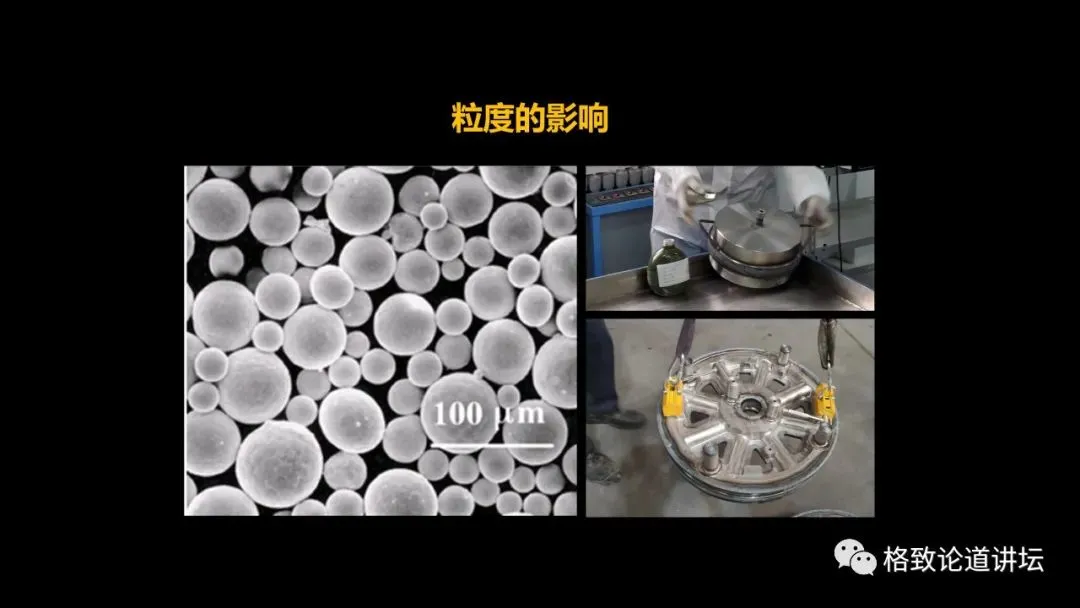
左图就是洁净的雾化制粉机制备的粉末颗粒,它呈现一个完美的球形,但它是大大小小的球。
它的平均粒度大概是100个微米,就是两根或一根头发丝那么粗。如果要把这些松散的粉末填充到包套或模具中不太容易。
右上角的图是一个圆柱形的包套,靠重力加以振荡,基本上是能够进去的。
但是像右下角的图,它有很多流道,还有一些浇口、冒口以及补缩机构,这样填充起来就比较困难。
它不像水,如果水要灌到包套中,就可以流到各个角落,但是粉末就比较难了。
我们的解决方案是采用大颗粒和小颗粒相结合,因为大颗粒的流动性比较好,可以“骨碌”过去。
但是它填充性能比较差,因为它比较大,会堵住一些粉末模具中的间隙。
小颗粒的填充性非常好,因为它比较细小,可以填充到模具的各种角落中,但是由于团聚和静电吸附,它的流动性比较差。
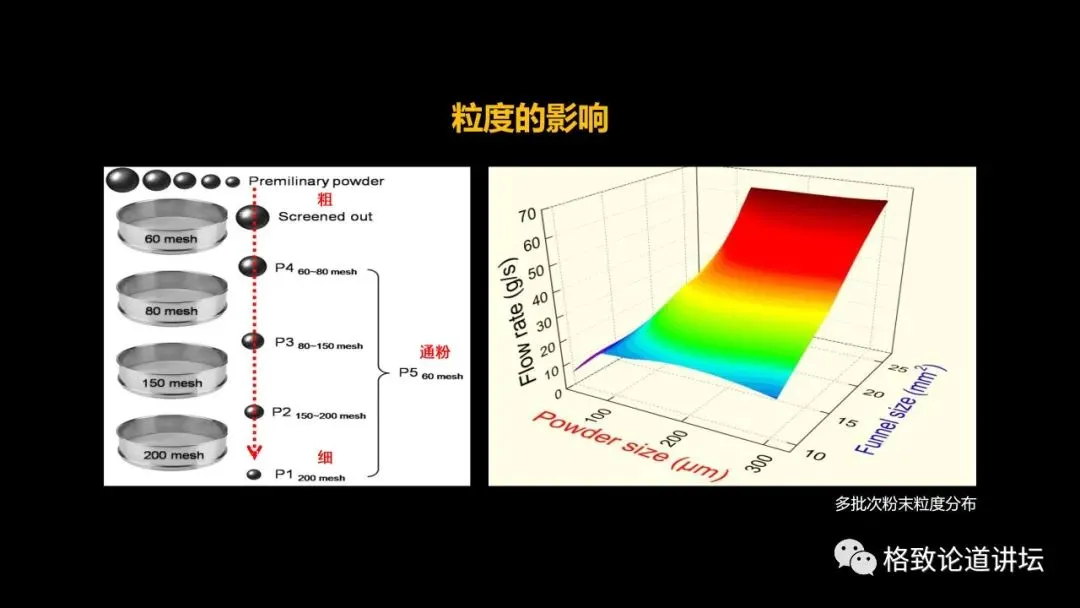
所以我们的解决方法就是大颗粒小颗粒相结合,而且摸索出一套行之有效的、可以达到一个良好致密度的填充方案。
现在我要着重介绍一下热等静压。
热等静压是钛合金粉末成形的一个重要方式,它的目的是使松散的粉末致密化。
“热等静压”这四个字,实际上包含了三个词,第一是“热”,第二是“压”。
热,顾名思义,我们要在热等压炉中给它提高很高的温度。
压,就是要压力给它压扁,压力是靠惰性气体,通常是高纯氩气来实现的。
“等静”是什么意思?
因为它是气体,所以在压制的过程中,各个方向的压力是一样的。
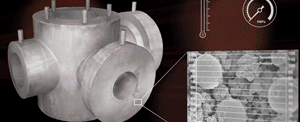
这就是粉末包套放在热等静压炉中,红色的箭头是等静的压力。
这个温度下,钛合金的热压温度大概是900多度,压力是1400个大气压,140兆帕。
所以很容易把它变得柔软,然后致密化成形,得到很好的粉末合金。
热等静压进行完后,我们对粉末合金的性能进行了测试。
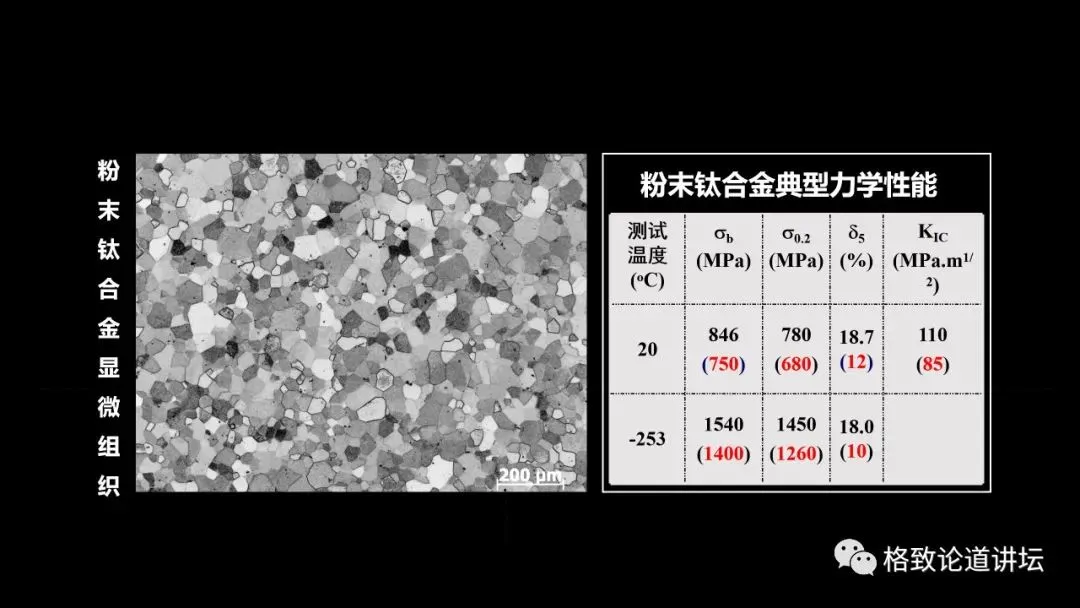
这是我们测的室温和低温的力学性能数据,因为氢泵叶轮是用在低温下的,除了低温强度,我们可以看到红色的字是铸造叶轮的性能。
我们发现低温下粉末合金的性能比铸造性能提高了140兆帕,这意味着什么?
意味着如果拿粉末合金来做氢泵叶轮,可以承担更高的转速,而且使用起来更加可靠。
思想晚餐
已完成:60% //////////
粉末叶轮怎么做?
粉末合金做完后,只是万里长征走完了第一步,我们还要用合格的粉末合金制备复杂的粉末叶轮这个零件。
叶轮到底怎么做?
说实话,我也不知道。
1 但是在12年前,由于这个技术是高度封锁的,我们获得任何技术资料都是比较困难的。
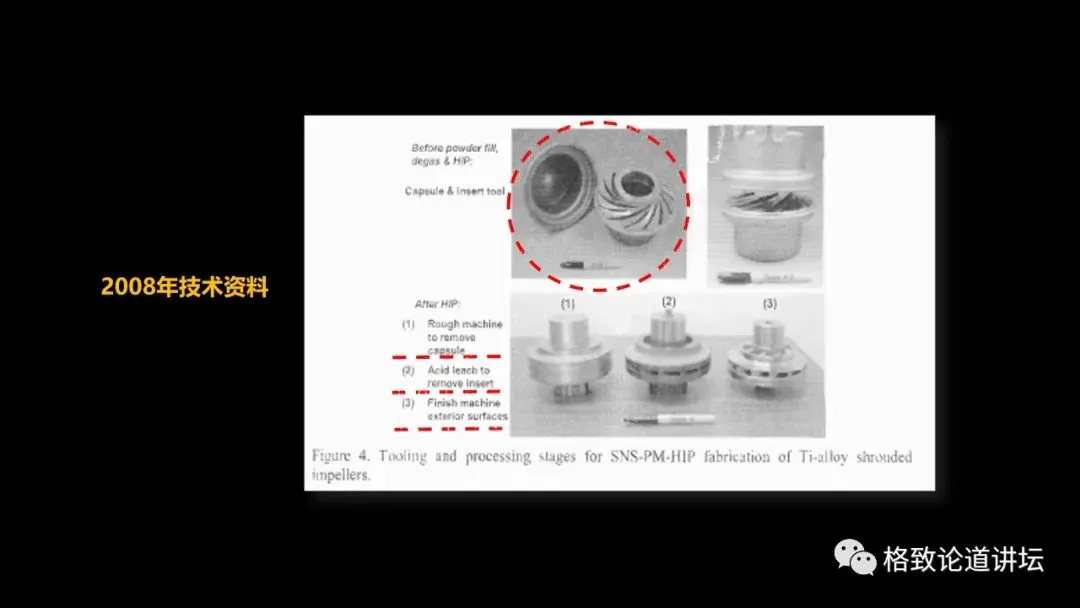
这是2008年,当时的金属所副所长杨锐在国外开会时,正好是一个热等静压会,他拿回来一篇会议文献,当天晚上就给我,说你赶紧看。
我如饥似渴,连夜阅读,发现我想要的东西它都没有。比如包套怎么做、材质是什么、热等静压参数是什么。
最关键的一条,我这个型芯怎么制造,就是图中红圈圈出来的,我只知道包套和型芯模具的长什么样,对于型芯是什么材料做的一无所知。
就是这篇文献,打开了我的叶轮研制之路。
叶轮研制过程中,有一个东西是最需要解决的,就是包套,那个金属胶囊怎么做。
包套绝对是个技术,但是我没想到万事起头难,会难到这个地步。
包套在热等静压过程中是应该收缩的,但是没想到,我这个包套是膨胀的。
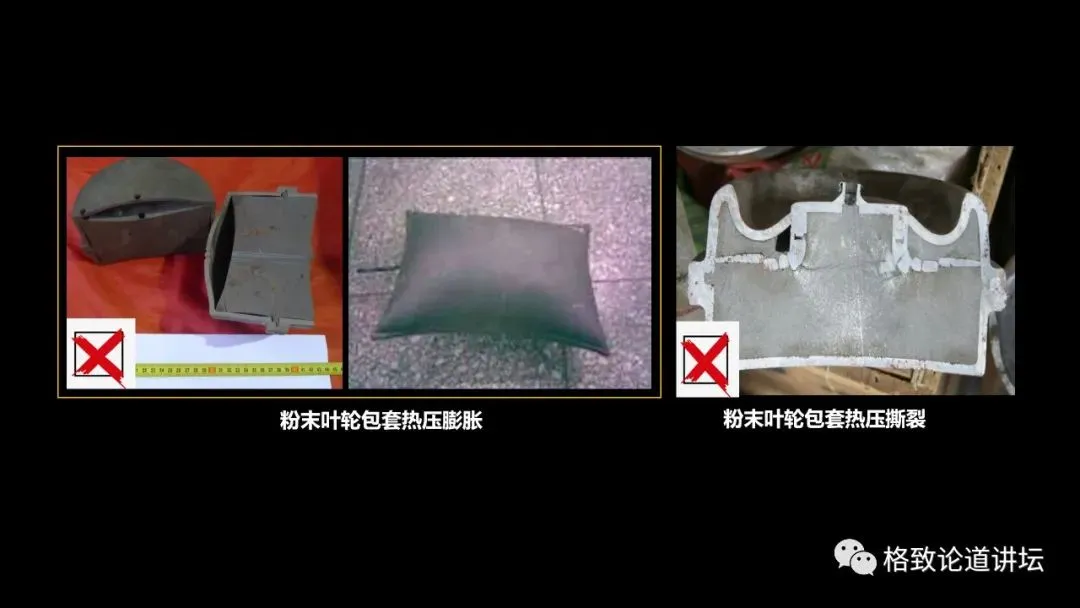
左图红色背底的,这是因为焊缝漏气了,吹泡泡了,这个就废掉了。
最离谱的一次是中间这个,这应该是11年前,在热等静压外协单位,我想做一个试板。
这个试板的体量大概是一张A4纸大小的幅面,厚度是摇控器这么厚。
去热压的话应该被压扁,得到致密的合金,结果不仅没压扁,还吹成了面袋子。
当时在场的一个工程师悄悄把我拉到一边,说小徐啊,你点子挺正啊,再差一点,估计你们单位就得给我们这个发热体掏六七十万的维修费了。
我现在一算,基本上就是,两辆哈弗H9的价钱,还是高配。
这是我们遇到的宏观的问题,比较容易解决,因为爆掉后扔掉就算了,无非增加点成本,费点人力。
但是有时往往进行到最后一步了,相当于我们最后一哆嗦,没哆嗦好。
当我兴冲冲地把我们的叶轮拿去无损探伤、检测荧光时发现,有很多表面气孔、皮下气孔,拿到用户那里,肯定是判废的。
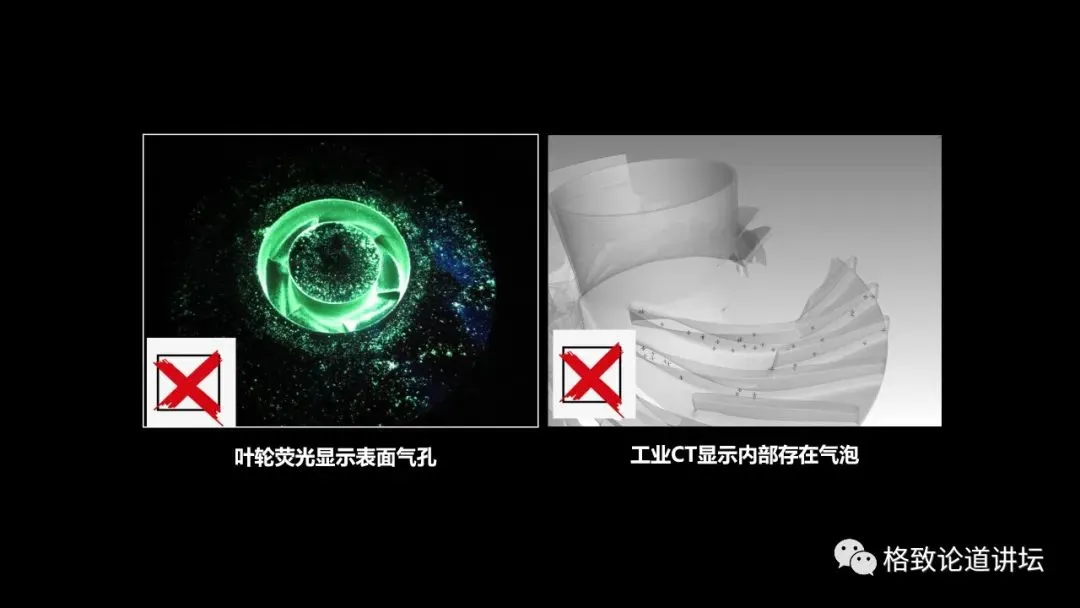
因为荧光显示就是这样,如果这个区域是黑乎乎的,那是很好的,颜色越多是越不好的,我现在最怕看到绿色。
还有的荧光显示过了,X光合格了,外形也是可以的,用户说放到工业CT上看一下,我们发现,工业CT显示里面有很小的气泡,用户说判废。
曾经有一段时间,我做梦都梦见包套因为没压成功而爆掉。
为了解决包套成功率这个问题,解决包套技术,我们和工程师傅在一起设计焊缝,选择焊缝材料,对焊缝进行检漏。
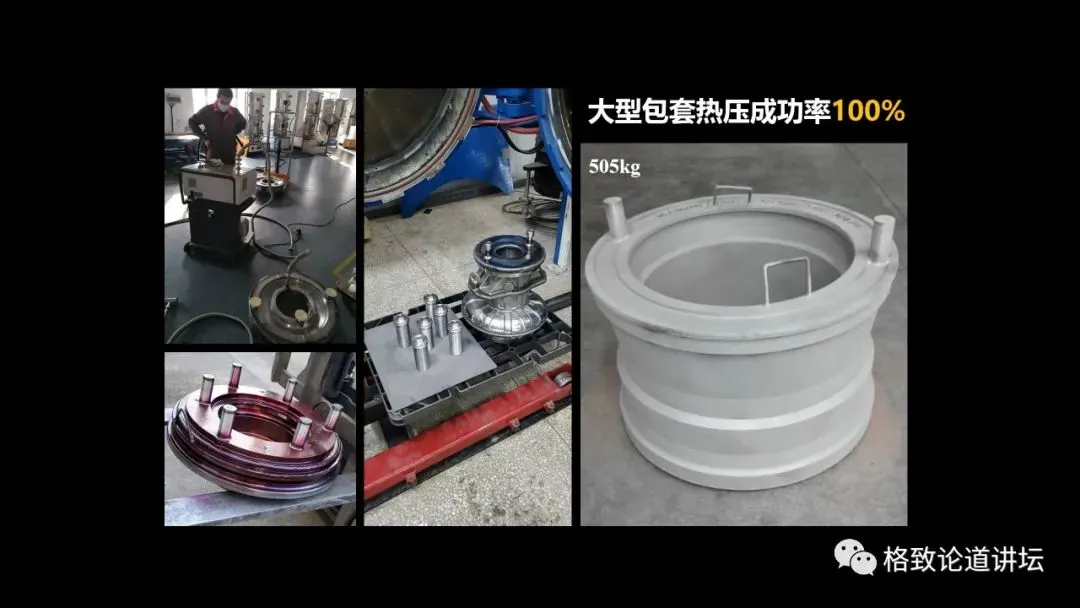
左面上面这张图,就是我们的焊工对焊缝进行氦气检漏。
焊完后,我们用磁粉检测符合核电级材料标准,对焊缝进行检测,如果发现有异常就打磨掉,再去补焊一遍。
另外,由于焊接是一个快速凝固的过程,在焊接的过程中有可能存在残余应力,这个应力往往是拉应力,我们需要变成压应力。
怎么变成压应力呢?
我们可以通过超声加工或热处理的方式解决这个问题。目前,大型包套的热压成功率是百分之百。
右图的零件是我们去年做的10件国内最大的活性金属粉末热等静压坯料,单重505公斤。
解决了包套技术后,我们的研制过程就从此踏上了快车道。
2009年5月,我成功试制了一个粉末叶轮,走通了包套设计、制造、焊接、热等静压、选择性化学铣去除形模。
说到化学铣,还得感谢我们金属所的董俊华老师,他是搞腐蚀的。
中间这个型芯最后热等静压完成要用酸洗掉,但是这个叶轮大家看一看就行了,因为它是一个样子货。
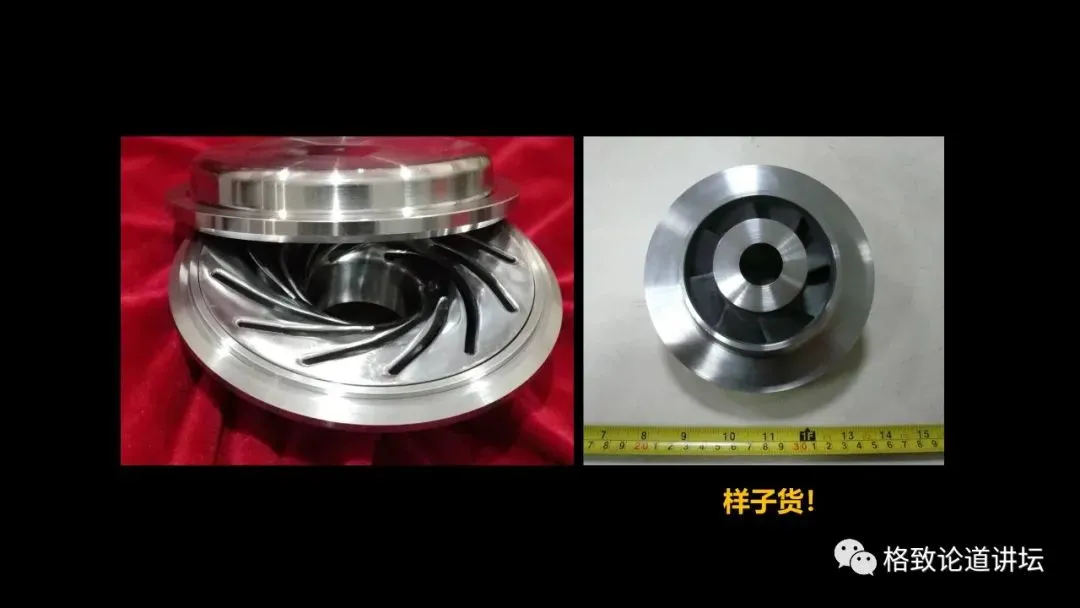
为什么说它是一个样子货呢?
由于我当时不具备这个能力,制备一个1比1的盘件,一个叶轮,我做了一个1比2的。
但是1比2的话,它的叶片少一半,因为在如此局促的空间里,我是放不下24个叶片的。
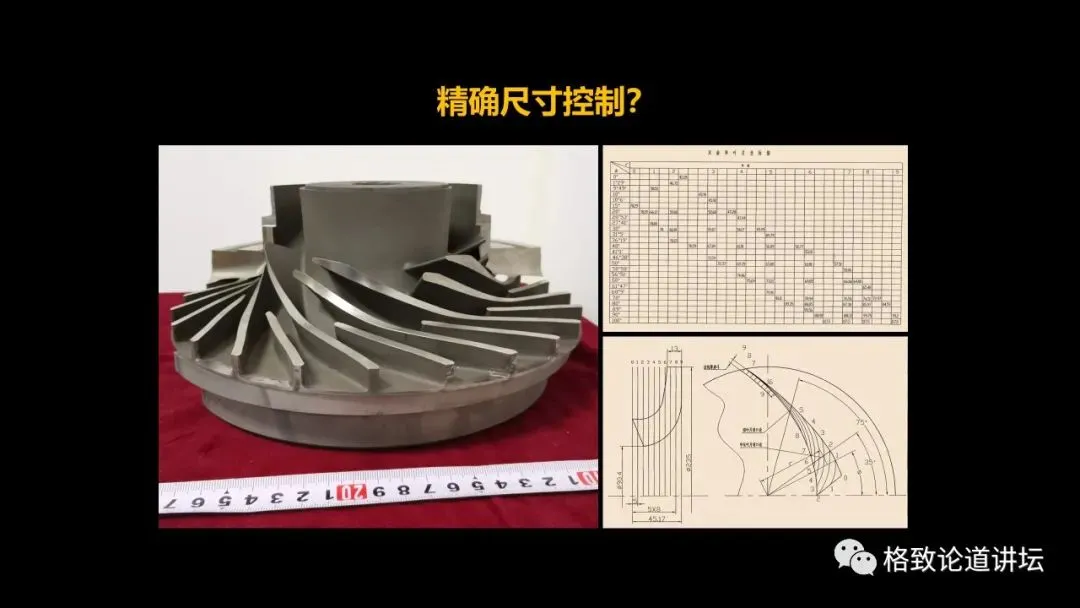
这是真正的1比1的,经过实验考核的,长征五号和长征五号B火箭发动机XX-77发动机上用的氢泵叶轮,它的盘子的直径大概是245毫米。
这是摘掉上盖板后对它进行尺寸测绘的形貌,这个叶轮共有24个叶片,分长中短8组,每组3个。
用户对尺寸的要求到底有多么严苛呢?
第一,他需要测。
从叶片中心到边缘,9个截面、26个角度、70个尺寸,每个尺寸都要和卡板上一模一样,而且它的偏差是正负0.2毫米,这就给我们带来了很大的难度。
叶片中间空的区域就是模具,为什么说它难呢?
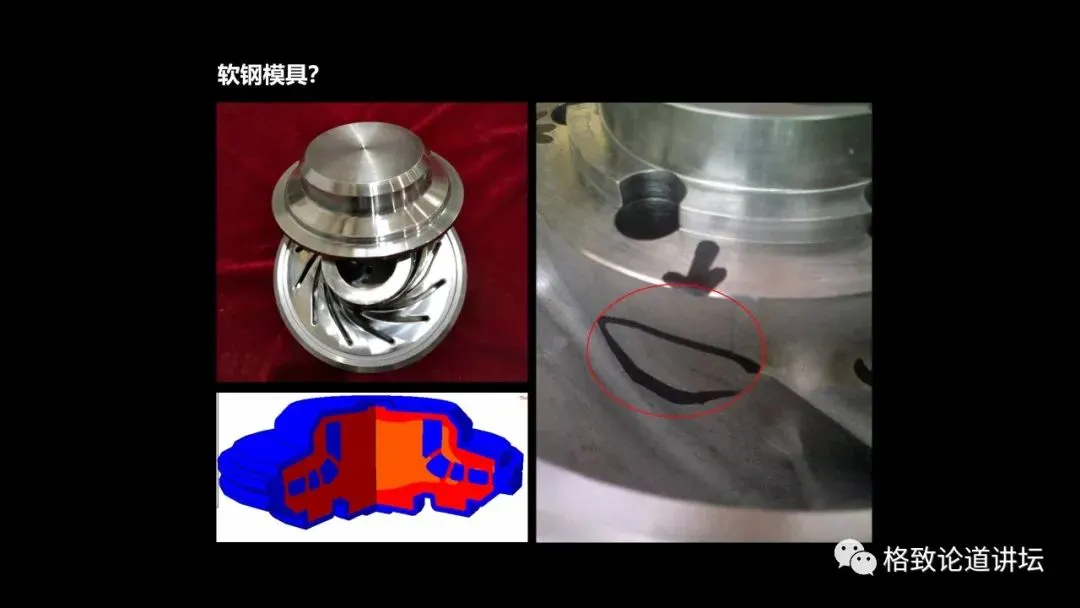
这张图就是叶轮包套和模具,大家肯定想问,要控制尺寸,我把里面那个模具的型芯变成陶瓷的不就行了?
没错,可以变成陶瓷的,但是陶瓷有一个最大的问题,它在加工的过程中会脱落,变成陶瓷颗粒。
陶瓷颗粒对钛合金来说是夹杂,特别是转动件,不能有夹杂,这种方式国外也用过,就摒弃了,我们一开始就没有用。
可能有的人又会说,弄一个硬的型芯不就好了,把中间那个像花瓣一样的东西,高温合金搞得非常硬。
是,高温合金可以,它不动了,叶片的叶形、尺寸都能很好地保证。
但是,我们也做过右图,变成硬质的材料后,最大的问题在降温的阶段。
由于它型芯比较硬,而我们的基体是钛合金的,非常软,它会把叶轮胀破,有裂纹,用户就更不能使用了。
于是我们用了一个最费劲,也是最复杂的方式,即采用软钢包套,里面的内外包套和型芯都是软的材料。
下面这张图可以看到,在热等静压过程中,它是逐渐变小的,不仅粉末在收缩,而且我的型芯也是在收缩的。
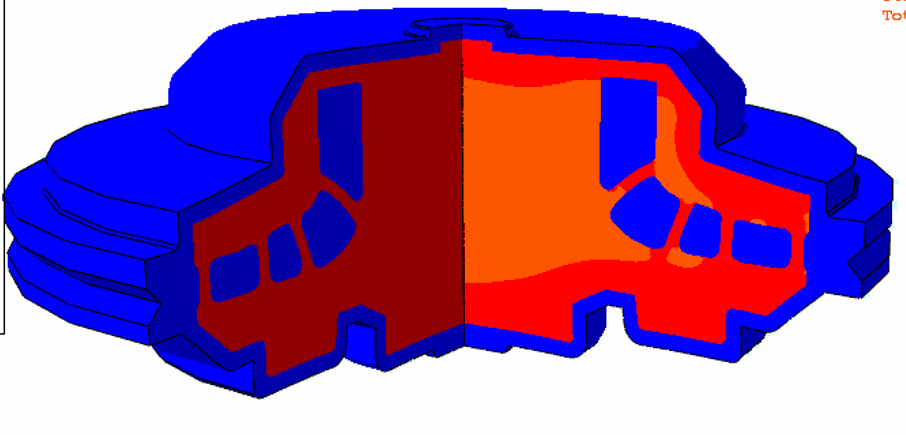
这一下就体现出难度了。
因为钛合金粉末在收缩的过程中,体积收缩达到30%,以直径250mm的盘子来说,高度150mm,直径方向收缩是25%,高度方向是15%,体收缩是30%。
250mm的盘子收缩20%的话,就是50毫米,是很难控制的。
为此,我们采用的解决方案是采用有限元仿真,就是先用实验做出一个数据,教会电脑去算这个事。
然后电脑在我们的不断优化下,不仅能算出它的残余应力,还能算出它的精确尺寸。
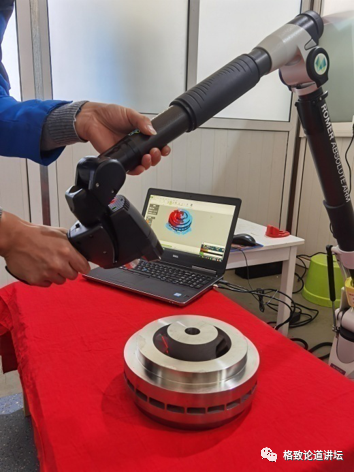
但是里面最重要一条,就是图中,我们要把实际实验的测量结果反馈到电脑和软件中去,让它打得更准。
思想晚餐
已完成:90% //////////
助长征五号首飞
现在经过十多年的探索,我们的软件预测的准确率是99.5%以上,给我一个新型的叶轮,新的型号,它一轮次就能打得很准。
我们用了不到两年的时间,具体来说是14个月的时间就走通了环节。
2010年9月提供的首套叶轮通过了用户的发动机热试考核,用户对我们评价是已满足技术指标要求,具备较高的可靠性。
但是从2010年到2016年,我们又经过了漫长的六年等待,这六年中,我们也不是什么都没做,我们做了三件事。
第一件事,固化优化工艺;第二件事,提高材料的稳定性;第三件事,要建成小批量的生产能力。
2016年11月3日,我们提供的叶轮助力长征五号首飞,当天我们也非常激动。
相当于从2008年12月到2016年,我们用了8年的时间,八年磨一剑,终于成功了。
而且2017年,我们中国科学院金属研究所,这个团队,还被五部联合授予了“长征五号火箭运载火箭首飞任务突出贡献单位”。
而且我们也是科学院唯一获得这个奖项的单位。
这是2019年12月27日,长五遥三火箭在海南文昌复飞的壮观场景,这上面也有我们做的零件。
当时我们非常激动,有多少个大工程、大项目,背后有像我们几十个、上百个这样的团队,有很多普通的工作者、劳动者、科研工作者在一起,才能做成这些事。
我想感谢我们的团队,感谢钛合金研究部的全体职工学生,感谢我们的用户北京航天动力研究所。
特别要感谢我的两位导师杨锐研究员和崔玉友研究员,谢谢大家。
免责声明:本网站所转载的文字、图片与视频资料版权归原创作者所有,如果涉及侵权,请第一时间联系本网删除。
相关文章
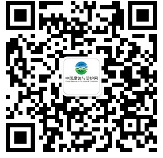
官方微信
《中国腐蚀与防护网电子期刊》征订启事
- 投稿联系:编辑部
- 电话:010-62316606-806
- 邮箱:fsfhzy666@163.com
- 中国腐蚀与防护网官方QQ群:140808414
点击排行
PPT新闻
“海洋金属”——钛合金在舰船的
点击数:7130
腐蚀与“海上丝绸之路”
点击数:5741