摘要:
利用样板验证方式探讨了不同除锈方式与磷化底漆的适应情况,以及复合防腐涂层间的配套性,并进行初步现车应用验证磷化底漆的使用效果,为铁路客车车体防腐施工提供了合理化建议。
关键词: 铁路客车; 防腐; 磷化底漆
0 引言
铁路客车车体寿命直接决定客车寿命,车体防腐质量直接影响车体寿命,车体防腐所用防腐底漆质量及其施工工艺与防腐效果有直接关系。为避免车体内部喷丸后发生车体钢结构变形,通常采用以机械或手工打磨为主的除锈方式对车内进行除锈检修,但车体内部除锈又存在难以清除干净的难题,需要采用新的方式来应对车内钢结构及铁质零部件锈蚀,减缓其锈蚀速度,以保证车体运行寿命。
磷化底漆是一种高效金属表面预处理剂,其所形成的10 ~ 15 μm薄膜牢固附着在金属表面,起到磷化和钝化的作用,可增加有机涂层和金属表面的附着力,防止锈蚀,延长有机涂层的使用寿命。它一般不用于代替底漆,而是与其他底漆或防锈漆配合以获得较好的效果,广泛应用于钢板及钢结构增强防锈,尤其适宜湿热环境地区的钢板和钢结构的保护。
1 研究内容
本文主要探讨除锈磷化底漆的选择及应用以及与环氧磷酸锌、环氧重防腐复合涂层间的配套性能,并进行初步现车试用,选择合适的防腐涂装工艺。
1.1 磷化底漆的选用
结合运辆客车函[2015]73号《中国铁路总公司运输局关于印发〈25型客车防腐涂料工艺规范(试行)〉和〈25型客车用涂料技术条件(试行)〉通知》内容要求,选择的磷化底漆既要与金属表面具有良好的化学结合,又要确保与后涂双组分环氧底漆具有良好的配套性,故确定选用双组分环氧磷化底漆(主要基料为环氧树脂)。
磷化底漆又称洗涤底漆,主要作为有色及黑色金属底材的表面处理剂,能起磷化作用,可增加有机涂层和金属表面的附着力。磷化底漆为双组分涂料,由主剂与磷化液组成,使用时按质量比4 ∶ 1配制,其性能应符合HG/T 3347—2013《乙烯磷化底漆(双组分)》的规定,具体技术参数见表1。
1.2 不同除锈程度与磷化底漆的相适应情况
根据样板锈蚀程度,采用手工打磨方式除锈,除锈后表面清洁度不同,然后喷涂磷化底漆,观察不同除锈效果的样板喷涂磷化底漆的情况。
1.3 磷化底漆、环氧磷酸锌底漆、重防腐涂层间的配套性
根据防腐涂层设计结构,观察不同底漆之间的配套性能。
底漆结构一:磷化底漆+环氧底漆;
底漆结构二:磷化底漆+环氧底漆+重防腐。
1.4 磷化底漆的车内现车应用
根据厂修车车体内部锈蚀情况,选择锈蚀严重、阻尼涂料脱落严重的车辆进行磷化底漆应用研究,重点部位为车内侧墙板(含侧墙骨架)、车内顶板(含车顶骨架)等。
2 探讨方法
2.1 试验验证
利用样板验证方式探讨不同除锈程度的表面状态与磷化底漆相适应的情况,以及复合防腐涂层间的配套性,为现车应用做好准备。
2.2 现车应用
现车选用南方路局运行线路环境比较潮湿车辆,初步验证磷化底漆的使用效果。
2.3 处理工艺流程
根据车体防腐的整体要求,制定如下车内防腐工艺路线。
1)含磷化底漆车内防腐工艺流程
防腐结构一:车内手工除锈→磷化底漆→环氧磷酸锌底漆→阻尼涂料;
防腐结构二:车内手工除锈→磷化底漆→环氧磷酸锌底漆→重防腐涂料→阻尼涂料。
2)原车内防腐工艺流程
防腐结构一:车内手工除锈→环氧磷酸锌底漆→阻尼涂料;
防腐结构二:车内手工除锈→环氧磷酸锌底漆→重防腐涂料→阻尼涂料。
3 样板试验
3.1 样板前处理
使用传统手工打磨除锈的方式初步清除碳钢样板表面锈蚀,根据工艺要求,手工除锈表面为St2级,局部不易除锈部位为St3级。
采用样板手工除锈,除锈效果如图1所示(因锈蚀严重,考虑验证的实用性,不以传统除锈等级衡量,仅以实物表面状态为参考)。
3.2 油漆施工及要求
1)表面处理要求:保持表面干燥,无油污、灰尘等异物。
2)配比:m甲 ∶ m乙=4 ∶ 1。
3)将磷化底漆搅拌均匀,如由于颜料沉淀不易搅拌时,可先将上层漆液倒出,把沉淀颜料和剩余漆液搅拌均匀,再逐渐加入漆液搅拌均匀。
4)将搅拌均匀的底漆放入非金属容器内边搅拌边缓慢加入比例量的磷化液,加毕,加入适量稀释剂调配黏度(涂-4杯)为15 s左右为宜,放置15 ~ 30 min后使用,并在12 h内用完,放置时间过长易于凝胶,不能使用。
5)采用喷涂施工,漆膜厚度以10 ~ 15 μm为宜,施工时要尤其注意磷化膜厚度,不宜过厚。
6)施工环境要比较干燥,如湿度太高,会使漆膜发白,影响漆膜的附着力和使用效果,环境温度应不低于18 ℃。
7)漆膜涂布后2 h即可涂其他防锈漆、底漆和面漆,于不低于18 ℃自干或(60±5) ℃下烘干均可。
3.3 过程记录
3.3.1 磷化底漆样板
磷化底漆在4种不同程度除锈后的样板上结合良好,未出现缩孔、咬底、鼓泡等涂层缺陷等。根据GB/T 9286—1998进行划格试验,4种不同除锈程度的样板表面喷涂磷化底漆后,磷化底漆样板1#、2#、3#、4#的附着力均达到0级的要求,磷化底漆与金属样板间附着力良好。
3.3.2 “磷化底漆+环氧磷酸锌底漆”样板
4种不同除锈程度的样板表面喷涂“磷化底漆+环氧磷酸锌底漆”后,两种底漆层之间均未出现缩孔、咬底、鼓泡等涂层缺陷。根据GB/T 9286—1998划格试验,“磷化底漆+环氧磷酸锌底漆”涂覆后样板1#、2#、3#、4#两涂层层间附着力划格试验均可达到0级的要求,说明两种底漆间配套性良好。
3.3.3 “磷化底漆+环氧磷酸锌底漆+重防腐涂料”样板
4种不同除锈程度的样板表面喷涂“磷化底漆+环氧磷酸锌底漆+重防腐涂料”后,3种底漆层之间均未出现缩孔、咬底、鼓泡等涂层缺陷。根据GB/T 9286—1998进行划格试验,“磷化底漆+环氧磷酸锌底漆+重防腐涂料”涂覆后样板1#、2#、3#、4#的涂层层间附着力均达到0级的要求,说明3种底漆间配套性良好。
4 车辆应用
样板验证结果说明复合防腐涂层性能符合工艺要求。为保证验证的全面性,对现车进行工艺配套性试验,在此仅就复合防腐涂层进行装车应用。根据厂修车车体内部锈蚀情况,选择锈蚀严重、阻尼涂料脱落严重的部分车辆,对磷化底漆进行现车验证。
4.1 施工过程记录
1)除锈
对车体内部锈蚀严重、阻尼涂料脱落严重的部位,采取手工打磨除锈(尽量接近于St2级)。
2)防锈涂层
采用“磷化底漆+环氧磷酸锌底漆+重防腐涂料”的复合体系,分步验证,结果如图2 ~ 6所示。
4.2 试验评定
试验评定结果:磷化底漆现车喷涂施工未出现缩孔、咬底、鼓泡等涂层缺陷,表面覆涂环氧底漆后,两种底漆未出现缩孔、咬底、鼓泡等涂层缺陷,说明复合防腐涂层施工性良好。
对于最终质量效果,应在车辆出厂运用过程中认真进行质量跟踪,并在下次厂修时对其进行质量评价。
5 结语
通过样板和现车试验验证,磷化底漆施工性良好,与不同除锈程度的金属基材基本都能实现良好的配套结合,不同防腐涂层间的配套性能也表现良好。
在实际检修过程中,车辆腐蚀情况各异,对于车辆不同程度腐蚀情况,根据其结构局限性
及表面处理情况采用不同的涂层结构,选用不同的防腐处理工艺。
1)车内腐蚀较轻,除锈效果符合St2级标准,表面处理良好的车辆使用“环氧磷酸锌底漆+其他”的复合涂层,不建议使用磷化底漆。
2)车内腐蚀严重,且除锈后达不到St2级标准,表面存在牢固腐蚀层或浮锈的车辆使用“磷化底漆+环氧磷酸锌底漆+其他”的复合涂层,客车检修时建议磷化底漆配合环氧磷酸锌底漆作为防腐底漆。
免责声明:本网站所转载的文字、图片与视频资料版权归原创作者所有,如果涉及侵权,请第一时间联系本网删除。
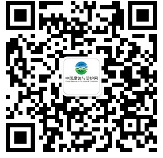
官方微信
《中国腐蚀与防护网电子期刊》征订启事
- 投稿联系:编辑部
- 电话:010-62316606-806
- 邮箱:fsfhzy666@163.com
- 中国腐蚀与防护网官方QQ群:140808414