为解决粉末高温合金涡轮盘中存在的夹杂物尺寸超标、超声检测不合格等关键问题,我国深入开展了“挤压+等温锻造”工艺的研究,并取得了重要进展。近期,我国在北重集团3.6万吨黑色金属挤压机上成功挤压出用于航空发动机涡轮盘的粉末高温合金棒坯。这一成果标志着我国在粉末高温合金制造技术领域实现了重大突破。研究表明,在挤压过程中,原始颗粒边界(PPB)被有效消除,夹杂物沿挤压方向得到充分破碎和延展。在随后的等温锻造阶段,这些夹杂物在垂直于锻造方向的平面内进一步被细化和弥散分布,从而显著改善了材料的均匀性和综合性能。此外,我国在粉末高温合金挤压变形研究中也取得了积极进展,尤其是在有限元模拟技术方面。通过模拟包覆挤压过程,可以系统分析模具结构参数、工艺条件等对挤压过程的影响,为优化模具设计、实现最佳结构组合提供了科学依据。目前,“挤压开坯+等温锻造”工艺已被确立为我国粉末高温合金涡轮盘制造的核心发展方向之一。这一技术路线的突破为提高涡轮盘的性能和质量奠定了坚实的基础,同时也为我国高端制造业提供了重要支撑。
高温合金是指以第珊主族元素(铁、钴、镍)为基,加入大量强化元素,能在 600℃以上的高温及一定应力作用下长期工作的一类金属材料。高温合金具有较高的高温强度以及良好的抗氧化、抗热腐蚀、抗疲劳性能,在高温下具有良好的组织稳定性和使用可靠性,因此,也被称为热强合金、耐热合金或超合金。此前我们已经对高温合金进行了详细的讲解,有需要了解的小伙伴可以点击链接查看。 粉末高温合金是一种基于粉末冶金技术制造的高性能材料,专为在高温和极端环境下工作而设计。其主要特点是能够在高温条件下保持优异的机械性能、抗腐蚀性和抗氧化性。这类材料广泛应用于航空航天、燃气轮机、核电及化工等领域,是现代高科技产业不可或缺的重要支柱。 粉末高温合金的制备通过将不同成分的金属粉末混合并致密化,形成均匀微观结构,从而克服了传统铸造和锻造工艺的缺陷。这种方法能更精准地调控材料的微观组织与成分分布,使其在高温环境下的表现更加优越。与传统铸造材料相比,粉末高温合金还表现出更高的组织稳定性和抗疲劳性能,这使其在苛刻工况下的寿命大幅延长。 粉末高温合金的发展始于20世纪50年代。随着航空工业的快速发展,传统铸造高温合金逐渐暴露出晶粒粗大、成分偏析、缺陷难以控制等问题,难以满足喷气发动机和燃气涡轮日益苛刻的使用要求。粉末冶金技术的出现,为解决这些问题提供了新的思路。粉末高温合金经历了三代发展,已在先进军、民用航空发动机的涡轮盘等多种关键零件上广泛应用,当前国际粉末高温合金研发已经进入第四代。粉末高温合金铸锭内部无宏观偏析、微观组织均匀、晶粒细小,具有优异的力学性能和热加工性能,可有效地保证发动机的可靠性和耐久性,而且可近净成形,制造周期短,生产成本较低。 1950-1970年代: 粉末高温合金技术初见雏形,研究重点集中于制备技术与性能表征。最早期的应用是航空发动机中的小型零部件。此阶段的粉末高温合金多基于传统铸造高温合金的成分。 1980-1990年代: 随着气雾化技术和热等静压(HIP)技术的发展,粉末高温合金的制备工艺得到了显著改进,合金强度和可靠性显著提升。研究人员逐渐认识到微观结构对高温性能的重要性,推动了合金设计的精细化。 2000年代至今: 粉末高温合金的性能不断优化,微观组织控制技术逐渐成熟。随着增材制造技术(如激光熔化沉积、电子束熔化)的兴起,粉末高温合金的应用范围进一步拓展。不仅在航空航天等传统领域,其在能源、医疗和高端装备制造中的应用也日益广泛。 粉末高温合金材料的性能特征: 粉末高温合金的优异性能主要体现在以下几个方面: 高温强度 在高温下仍能保持较高的抗拉强度和屈服强度,适用于涡轮叶片等高温承载部件。其强度源自精细的晶粒和析出强化机制。 抗蠕变性能 在长期高温工作条件下表现出优异的抗蠕变性能,能够抵抗材料在应力作用下的永久变形。这主要得益于其均匀的晶粒和分布合理的第二相颗粒。 抗氧化性和耐腐蚀性 表面能够形成稳定的保护膜,防止氧化和腐蚀,尤其适用于高温氧化和化学腐蚀环境。特别是在含硫气氛中,粉末高温合金具有独特优势。 微观组织均匀性 粉末冶金技术制备的材料具有均匀的组织结构,减少了传统铸造工艺中的偏析现象,提高了材料的可靠性。 疲劳抗性 粉末高温合金的均匀组织和致密微观结构赋予其极高的抗疲劳性能,尤其在循环载荷和热循环条件下表现卓越。 根据合金的基体元素、性能特点和应用领域的需求,粉末高温合金可以分为以下几类: 镍基粉末高温合金 特点:镍基合金是目前使用最广泛的高温合金,具有卓越的高温强度、抗蠕变性和抗氧化性能。这些性能得益于其主要基体金属镍的高熔点及其对铝和钛等强化元素的优良兼容性。镍基合金中常添加铬以提高抗腐蚀性,同时通过铝和钛的析出强化形成γ′相(Ni3Al)。 应用:镍基合金广泛应用于航空发动机燃烧室、涡轮叶片及导向叶片等高温部件,是燃气涡轮核心部件的首选材料。 钴基粉末高温合金 特点:钴基高温合金以其在高温氧化环境下的优异表现而著称,特别适用于需要长时间承受高温热腐蚀的场合。钴基合金因其良好的延展性和韧性,能够更有效地抵抗热疲劳和热震。其基体结构通常含有碳化物和析出相强化,但与镍基合金相比,其高温强度稍低。 应用:钴基合金主要用于航空航天燃烧室、涡轮壳体以及化工行业中抗腐蚀性要求高的部件。 铁基粉末高温合金 特点:铁基合金是一种成本较低的高温合金,适合在中高温条件下工作。铁基合金中常掺入铬、镍、钼等元素以提高其抗氧化和抗腐蚀性能,但其高温性能较镍基和钴基合金逊色。 应用:铁基高温合金适用于化工设备中的耐热部件、锅炉热端组件及部分中温燃气涡轮组件。 复合型粉末高温合金 特点:复合型合金通过组合多种金属基体元素的优势,实现了性能的协同优化。例如,基于镍-钴复合体系的高温合金既具有镍基合金的高温强度,又兼备了钴基合金的耐腐蚀性。此类合金在一些极端环境下具有不可替代的优势。 应用:复合型粉末高温合金主要用于特殊高温环境中的关键部件,例如需要承受强热流和复杂应力的核反应堆核心部件。 新型超高温粉末合金 特点:新型超高温合金是近年来发展的热点领域,旨在满足极端温度(超过1200°C)的工作需求。通常采用高熔点元素如铼、钽、铼-铱等材料制备,具有极高的热稳定性和抗氧化能力。 应用:主要用于超高温燃气涡轮、尖端航空航天技术以及高温核能装置中的核心部件。 粉末高温合金的生产工艺总体上是通过在惰性气氛保护下制备和处理金属粉末,然后利用热成形技术实现粉末的固结与致密化。经过多年的技术发展,目前主要形成了两种代表性工艺路线:以欧美国家为主的“氩气雾化法 (AA) 制粉 + 热挤压 (HEX) + 等温锻造 (ITF)”工艺,以及以俄罗斯为主的“转电极法 (PREP) 制粉 + 热等静压 (HIP) 直接成形”工艺。 粉末高温合金盘件制造的主要工艺流程 我国在粉末高温合金制造领域取得了显著进展,研发了一条“等离子旋转电极法 (PREP) 制粉 + 热等静压 (HIP) 成形 + 包套锻造/热处理”的工艺路线。利用该工艺成功生产出大尺寸的FGH4095粉末涡轮盘。此外,通过直接HIP成形工艺制备的粉末高温合金涡轮挡板和小尺寸涡轮盘,已完成试车并实现批量生产能力。\n\n在第2代粉末高温合金FGH4096的研发中,双性能涡轮盘的研究工作取得了突破性进展。采用“PREP + 直接HIP + 等温锻造”工艺,攻克了粉末纯净度等关键技术难题,成功研制出用于某高推重比发动机的FGH4096合金涡轮盘。通过细晶锻造与梯度热处理工艺的结合,制备出具有双显微组织特性的盘坯,其轮缘晶粒度达5~6级,轮毂晶粒度达10~11级。这些成果标志着我国在高性能粉末高温合金领域实现了重要技术突破。 粉末高温合金在制备和加工过程中可能产生多种缺陷,这些缺陷直接影响材料的性能和可靠性,尤其是在高温、高应力条件下的应用。夹杂物、PPB和热诱导孔洞(TIP)是粉末高温合金的3大缺陷,严重影响粉末高温合金零件的性能。 缺陷描述:夹杂物是制备过程中外界杂质(如氧化物、硫化物、氮化物)或未充分反应的化合物颗粒,通常来源于制粉、混粉和烧结过程。 影响: 机械性能降低:夹杂物是潜在的裂纹源,导致材料的抗疲劳性能和高温强度下降。 检测不合格:夹杂物容易在超声检测中暴露,影响零部件质量评价。 使用寿命缩短:夹杂物的存在可能导致裂纹在高应力环境下快速扩展,降低构件的可靠性。 缺陷描述:原始颗粒边界是制粉后颗粒间的结合弱区,其主要表现为未完全消除的界面化学杂质和结构缺陷。 影响: 抗蠕变性能减弱:在高温高应力环境下,PPB容易成为蠕变变形的起始点。 延展性降低:PPB导致材料在受力时更易发生断裂,降低了整体塑性。 疲劳寿命减少:PPB的存在容易引发局部应力集中,加速疲劳裂纹的萌生和扩展。 缺陷描述:孔隙和气孔是粉末冶金过程中未完全致密化的结果,可能由气体残留、烧结不足或粉末分布不均引起。 影响: 强度损失:孔隙降低了材料的整体强度和密度。 疲劳裂纹萌生:孔隙是裂纹形成的核心部位,容易在循环载荷下扩展。 韧性降低:气孔的存在削弱了材料的抗冲击能力和延展性。 综上所述,粉末高温合金的缺陷主要集中在夹杂物、孔隙、PPB等方面,这些缺陷对材料的强度、疲劳寿命、高温性能等核心指标有显著负面影响。通过优化制粉工艺(如气雾化或等离子旋转电极法)、提高致密化技术(如热等静压和等温锻造)以及加强质量检测,可以有效减少缺陷,提高粉末高温合金的性能和可靠性。这些改进措施对于满足航空航天、燃气涡轮等领域对高性能材料的严格要求具有重要意义。 金属粉末的生产方法种类繁多,包括固体破碎法、球磨法、雾化法、电解法和化学法等。针对增材制造的需求,由于其对粉末的流动性和填充性要求较高,球形粉末成为首选材料。在众多制备技术中,雾化法被广泛认为是生产增材制造用金属粉末的最理想方法。同时,旋转电极法因其能够制备出高纯度、高球形度的粉末,近年来也逐渐在增材制造粉体材料的制备中得到应用。 这里说明:镍基高温合金球形粉末的制备基本工艺流程包括:母合金的冶炼与加工→制粉→粉末筛分→(电选分离杂质)→粉末性能检测。其中,母合金熔炼、雾化制粉以及电选分离杂质是确保高品质粉末的重要关键环节。 母合金熔炼技术 高温合金母合金的熔炼对高品质球形粉末的制备至关重要,但熔炼过程中可能引入夹杂物、缩孔、疏松等缺陷,影响粉末质量。为解决这些问题,通常采用真空感应熔炼(VIM)+电渣重熔(ESR)/真空电弧重熔(VAR)的多联精炼工艺。真空感应熔炼可精确控制成分并制备自耗电极,电渣重熔可有效去除非金属夹杂,真空电弧重熔进一步消除宏观偏析,获得组织均匀、纯净度高的母合金。电渣重熔因其卓越的夹杂物去除能力,是高温合金母合金精炼的优选工艺,为高质量粉末的生产提供了保障。 俄罗斯自20世纪90年代起广泛应用真空感应熔炼+电渣重熔工艺生产粉末高温合金母合金锭,显著提升了母合金的纯净度。2002年,钢铁研究总院设计并建造了首台超小断面真空/惰性气体保护快速电渣炉,通过该工艺制备的FGH95母合金显著降低了氧含量,减少了Al和Ti的烧损,同时减少了非金属夹杂物的尺寸和数量。泡沫陶瓷过滤技术利用陶瓷板过滤器对金属熔体进行过滤,同样能够有效去除夹杂物和有害元素,北京科技大学、中科院金属所等单位已通过该技术取得了良好成果。此外,日本的旋转铸锭工艺、北京航材院的优质高温合金锭生产技术,以及西北工业大学的电磁软接触成形净化技术和复合熔盐净化技术等,也在合金净化方面表现出显著优势。近年来,电磁净化技术和超声波处理技术等新型技术成为研究热点,为提升母合金纯净度提供了新的思路。随着航空发动机对粉末高温合金性能和可靠性的要求不断提高,研发高效率、低成本、高纯净的母合金熔炼与净化技术成为未来发展的重要方向。 制粉 粉末制备是粉末高温合金生产中至关重要的环节。通过制备出尺寸细小均匀、球形度高且气体和夹杂物含量低的粉末,可以显著减少甚至消除PPB和夹杂物等冶金缺陷,改善合金盘件的组织和性能,确保其质量。目前,先进的粉末制备技术是生产高品质高温合金粉末的关键,主要工艺包括真空感应熔化气雾化法(VIGA)、等离子旋转电极制粉技术(PREP)、电极感应气体雾化法(EIGA)以及等离子雾化法(PA)。这些技术为高温合金的高性能化提供了重要保障。 1)真空感应熔化气雾化法(VIGA) 真空感应熔化气雾化法(VIGA)是一种在真空环境下制备金属粉末的工艺。其过程包括利用感应加热技术熔化炉料,并在达到一定温度后向熔炼室和雾化室充入惰性雾化气体。熔融金属通过喷嘴流入雾化室后,利用高压惰性气体将金属液流破碎成细小液滴,液滴在高速冷却中凝固形成金属粉末。该方法能够高效制备尺寸细小、球形度高的粉末,适用于高品质金属粉末的生产。 真空感应熔化气雾化法(VIGA)示意图 目前,真空感应熔化气雾化制粉技术不仅广泛应用于镍基高温合金粉末的制备,还可用于多种金属材料的粉末化生产,包括不锈钢(如316L、174PH)、钴基合金(如CoCrMo、CoCrW、CoCrMoW)、钛及钛合金(如TC4、TC11、TA15、TiAl4822、Ti2AlNb)以及其他镍基合金(如FGH95、FGH96、FGH97、GH4169)和稀有金属粉末。这一技术因其高效性和适用性广泛,被广泛应用于高性能金属粉末的生产领域。 2)等离子旋转电极制粉技术(PREP法) 等离子旋转电极制粉技术利用离心雾化原理,在惰性气体环境下,通过等离子电弧快速熔化旋转棒料,熔融金属在离心力作用下形成液滴,并在溅射室内快速凝固成颗粒,最终收集于粉末罐中。该技术适用于制备高反应性金属、耐热镍基和钛合金粉末。据悉,国内制造等离子旋转电极制粉设备的企业包括湖南顶立科技、湖南久泰、西安赛隆等,所生产的设备通过电机驱动棒料旋转,转速可达1000015000 r/min,制得粉末的粒度D50一般大于100 μm。相比之下,俄罗斯在PREP设备领域处于世界领先地位,其Granule 2000型设备设计先进,棒料转速可达2000025000 r/min,制备的粉末粒度更小(D50约为60 μm),球形度高、氧氮含量低、无卫星粉,性能优异。最新的Granule 2500型设备进一步优化了电极旋转系统,转速达到25000~30000 r/min,显著提高了粉末细度和质量。PREP制粉法中,粉末粒度与棒料转速成反比,转速越高,粉末粒度越小,这使得高转速设备在制备高品质金属粉末方面具有明显优势。 3)等离子雾化法(PA法) 等离子雾化法(PA法)是一种通过等离子枪加热金属丝材,熔化并雾化生成球形粉末的技术。该方法由M.EntezaRian于1998年提出并申请专利,目前加拿大AP&C公司在该领域处于全球领先地位,掌握成套技术专利。PA法的原理是在惰性气体保护下,利用等离子枪将合金丝材熔化成金属蒸汽,通过气淬冷却使其快速团聚并形成超细合金粉末。该工艺制得的粉末粒径分布窄(10~150μm),其中50μm以下粉末占比约40%,球形度高且杂质含量低,细粉收得率极高。然而,PA法的主要限制在于原料需为较细的丝材,制造成本较高且制粉效率较低。\n\n目前,加拿大AP&C公司的等离子雾化设备配备全自动监控系统和气体回收装置,确保粉末质量稳定性并降低生产成本。该技术已广泛应用于大规模生产高品质球形金属粉末,涵盖纯钛及钛合金、镍基合金等材料领域。 4)电极感应气体雾化法(EIGA法) 电极感应熔化气雾化法(EIGA法)是一种不使用陶瓷坩埚的超洁净气体雾化制粉技术,具有生产效率高、产量大、粉末粒径细小的特点。其原理是在惰性气体保护下,将母合金棒料通过送料装置送入锥形超高频感应线圈,尖端逐渐熔化形成连续可控的金属液流,在重力作用下流入雾化室。高压惰性气体将液流破碎成小液滴,小液滴在雾化室内迅速球化并凝固形成金属粉末。EIGA法的关键优势在于整个熔化过程不使用坩埚或导流嘴,显著减少非金属杂质的引入。与VIGA法相比,EIGA法制备的粉末粒度更小,Dv(50)一般控制在50~100 μm之间,粉末球形度高,几乎没有片状物,且生产效率更高。德国ALD公司通过优化该技术,开发了多种型号的制粉设备,广泛应用于钛及钛合金粉末材料的科研与生产。日本OSAKA钛公司使用EIGA法制备的Ti6Al4V粉末粒径Dv(50)约40 μm,球形度高,杂质含量少,并已在增材制造领域实现应用。 电选分离技术 电选分离技术是去除高温合金粉末中非金属夹杂物的关键方法,其利用金属粉末和非金属夹杂物电性能的差异,通过电晕放电使粉末颗粒带电,从而实现分离。在静电分离过程中,金属粉末因电导率高快速释放电荷,在重力和离心力作用下进入成品区,而非金属夹杂物因电导率低被吸附到辊筒上并最终刷除。研究表明,电晕极电压和辊筒转速是影响分离效果的主要因素。以最佳工艺参数(电晕极电压40kV,辊筒转速50r/min)对50~100μm夹杂物处理时,去除率可达76.7%。此外,北京钢铁研究总院和北京航空材料研究院等单位已成功研发摩擦电选分离设备,其分离率超过85%,并可在高纯惰性气体保护下完成,避免粉末氧化。然而,当前电选技术分离范围有限,仅能处理一定粒度范围的夹杂物,分离效率和效果仍需进一步提升。未来的发展方向是扩大分离粒度范围和提高去除效率,以更好满足高温合金粉末生产的需求。 粉末筛分 在金属粉末生产中,雾化后的后处理过程对最终粉末特性至关重要,包括氧化钝化、分级(筛分或空气分级)和混合,以获得均匀的粉末批次。粉末筛分用于去除杂质并获得所需粒度的粉末,为避免筛分过程中粉末氧化,筛分机通常在真空或惰性气体保护下运行。筛分工艺的关键参数是振幅和振动频率,VIGA法制备的原粉一般需通过100目预筛,以防较大异形物体损坏筛网。此外,改善钝化后粉末流动性的方法多样,目前已开发多种技术来量化粉末的流变性(流动性和铺展性),但不同方法之间的相关性尚不明确。除了漏斗流速法外(ASTM B213/ISO 4490/ASTM B964),尚未有其他广泛采用的标准方法。同时,增材制造对金属粉末流动性的可接受值仍缺乏明确共识,未来需要进一步研究和量化以提高粉末的性能适配性。 应用背景: 材料与技术: 常用粉末高温合金:FGH95、FGH96、FGH4096等镍基合金。 制备工艺:采用真空感应熔炼气雾化法(VIGA)制粉,结合“挤压开坯+等温锻造”工艺制备高性能涡轮盘。 应用优势: 细晶组织提高了抗蠕变性能和疲劳强度。 减少了冶金缺陷(如夹杂物、PPB),显著提升部件寿命和可靠性。 应用背景: 材料与技术: 常用粉末高温合金:IN738、Rene 95、GH4169等镍基合金。 制备工艺:采用等离子旋转电极制粉技术(PREP)生产高纯度球形粉末,确保叶片性能的一致性。 应用优势: 优异的高温强度和抗氧化性能,延长部件使用寿命。 球形粉末使得增材制造(3D打印)技术可用于复杂结构部件的生产。 应用背景: 材料与技术: 常用粉末高温合金:NiAl基、TiAl基合金(如TiAl4822、Ti2AlNb)。 制备工艺:使用EIGA法制粉,结合增材制造技术,生产轻量化、复杂形状的热屏蔽部件。 应用优势: 提供优异的高温抗氧化和抗腐蚀性能。 显著减轻航天器重量,提高推进效率。 应用背景: 材料与技术: 常用粉末高温合金:钴基合金(CoCrMo)、钛合金(Ti6Al4V)。 制备工艺:等离子雾化法(PA)生产的高球形粉末用于金属增材制造技术。 应用优势: 提供高度定制化的植入物,适配患者的解剖结构。 高纯净度和表面光洁度,减少生物排斥反应。 应用背景: 材料与技术: 常用粉末高温合金:NiCr基和CoCr基合金。 制备工艺:真空熔融气雾化技术(VIGA)生产高纯粉末,结合热等静压(HIP)成形技术。 应用优势: 高温抗氧化性和抗辐射性能,确保组件长期稳定运行。 微观组织均匀,延长使用寿命。 结语
点此处跳转查看:一文了解先进高温合金材料
1. 夹杂物
2. 原始颗粒边界(PPB)
3. 孔隙和气孔
1. 航空发动机涡轮盘
粉末高温合金广泛应用于航空发动机的涡轮盘部件,这是发动机的核心部件之一,需要在高温、高压、高转速下长时间运行。
2. 燃气轮机热端部件
燃气轮机的燃烧室和涡轮叶片需要承受极高温度和氧化环境,是关键的高温部件。
3. 航天器热屏蔽材料
航天器的热屏蔽材料需要在高温和极端辐射环境下保持稳定,粉末高温合金为该领域提供了优质材料选择。
4. 医疗植入物
粉末高温合金也用于医疗植入物,如髋关节和膝关节的人工替代物,必须满足高强度、耐腐蚀及生物相容性要求。
5. 核能反应堆组件
核反应堆中某些部件(如控制棒、燃料包壳)需要在高温、高辐射和腐蚀环境下运行。
免责声明:本网站所转载的文字、图片与视频资料版权归原创作者所有,如果涉及侵权,请第一时间联系本网删除。
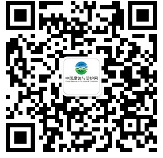
官方微信
《腐蚀与防护网电子期刊》征订启事
- 投稿联系:编辑部
- 电话:010-62316606
- 邮箱:fsfhzy666@163.com
- 腐蚀与防护网官方QQ群:140808414