腐蚀的原理
潮湿以及紧固件和连接件之间发生的电化学反应是紧固件腐蚀的主要原因。
潮湿环境的影响:
形成水膜:空气中的水分在无镀层的紧固件表面凝结形成水膜,为腐蚀反应提供必要的电解质溶液。当空气中相对湿度超过60%,金属表面就容易形成一层薄薄的水膜,溶解空气中的二氧化碳、二氧化硫等气体或灰、煤烟等污染物,形成酸性/碱性的电解质溶液从而引发腐蚀。
加速腐蚀进程:水可作为溶剂,使腐蚀介质中的离子更容易移动,促进金属与腐蚀介质间的化学反应。另外水还能参与一些腐蚀反应,如吸氧腐蚀,水与氧气在阴极反应生成氢氧化根离子,例如下图再与铁离子发生反应就会形成氧化铁沉淀物,分解后的氧快速氧化氢氧化铁,形成氧化铁水合物,也就是我们通常成为的锈。
图1:水滴模式-水滴滴在无镀层的铁表面的示意图
7种紧固件腐蚀的种类及预防攻略
均匀腐蚀
在整个金属表面上几乎以相同的速度进行腐蚀,腐蚀分布较为均匀,金属表面均匀减薄,均匀腐蚀是紧固件常见的一种,最终导致紧固件连接失效或无法拆卸甚至会加速紧固件的疲劳断裂,严重危害各类设备的安全。
图2:均匀腐蚀
均匀腐蚀常见的预防措施
零件防潮和通风干燥处理:最好将零件储存于干燥、清洁、保持良好自然通风的室内环境,若条件受限可使用排风扇、通风机等通风设备、干燥剂吸收空气中水分,或将零件放置于塑料薄膜、铝箔复合袋等防潮包装材料进行包装。
防水设计:在设计零件结构时可将零件表面设计成有一定的倾斜角度或增加排水槽、排水孔等结构,从而避免形成积水区或凹槽,使水分能够顺利流走。
表面清洁:定期对零件表面进行清理,一般采用擦拭、冲洗、喷砂等方式去除表面灰尘、油污、杂质等。
防止连续水分冷凝:尽量减小零件与周围环境的温差,避免因温度变化导致水分在零部件表面连续冷凝。在零件表面或附近放置像活性炭、蒙脱石等吸湿材料来吸附空气中的水分。
使用镀层或涂层:采用电镀、化学镀等方法在零件表面镀上一层锌、铬、镍等耐腐蚀的金属,形成一层能阻止水分和腐蚀介质与零件基体接触的保护膜。或采用涂覆-油漆、环氧树脂等的有机涂料能在零件表面形成一层致密的具有良好耐水性和耐腐蚀性的有机保护膜。
缝隙腐蚀
发生在金属表面的缝隙或凹陷面等其他隐蔽区域内的局部腐蚀。由于这些缝隙或凹陷面易聚集潮湿不易干燥,缝隙中的潮湿可迅速形成缺氧状态并引发图1水滴模型中所述的阳极腐蚀,该腐蚀常见于像螺栓连接的金属部件中间、垫片与金属表面之间等缝隙处。缝隙内形成局部的腐蚀环境,腐蚀速度远快于缝隙外,所以常看到缝隙内金属严重受损而缝隙外金属相对完好。
图3:缝隙腐蚀
缝隙腐蚀常见的预防措施
优化设计:设计时应避免形成狭窄的缝隙和间隙。对于连接部位,采用连续焊接代替螺栓或铆接,减少缝隙产生。如必要需使用螺栓连接,应确保螺栓与连接件间的配合紧密。
材料选择:根据具体的使用环境选择像不锈钢、镍基合金、钛合金等具有良好耐缝隙腐蚀性能的高性能材料。或在表面涂覆、镀上一层锌镀层、镍镀层等耐腐蚀的涂层或镀层。
施工质量控制:在焊接或安装、装配过程中,确保严格按照焊接工艺规范操作,避免出现气孔、夹渣、未焊透等焊接缺陷或各部件间安装精度及配合间隙不符合要求而产生缝隙,另外也要对连接部位进行密封处理,防止腐蚀介质进入缝隙。
定期维护和管理:定期对设备或构件进行机械、化学、高压水冲清洗,去除表面的污垢、沉积物或腐蚀产物,减少腐蚀介质在缝隙处的积聚。建立定期腐蚀监测和检测制度,采用像超声波检测、射线检测等技术进行无损检测技,及时发现并处理。
电偶腐蚀
两种不同的金属在电解质溶液中相互接触时产生电势差,腐蚀原电池,在这种电流反应中,较活泼的金属作为阳极发生腐蚀,较不活泼的金属作为阴极得到了保护。腐蚀主要发生在电位负的阳极金属上,且腐蚀速度通常比单一金属在相同环境中的腐蚀速度快得多。
图4:电偶腐蚀
电偶腐蚀常见的预防措施
合理选材和设计:选择电位相近的金属:尽量选择在工作环境下电极电位相近(一般小于50mV)的金属作为相接触的电偶对,对于安全性能要求更高的航空结构等,通常规定接触金属的电位差必须小于25mV。或者可以设计成大阳极和小阴极的电偶组合,这样阳极溶解速度相对减小不至于短期内引起连接结构的破坏。
表面处理:在金属表面使用金属镀层或非金属镀层,同时采用金属镀层时应在两种金属表面镀同一种金属,避免形成局部的小阳极-大阴极组合。不同的金属间用绝缘垫圈、填料、密封胶等进行电绝缘处理来阻止金属间的电接触。
电化学保护:可采用外加电源对整个设备进行阴极保护,使设备整体处于阴极极化状态来降低腐蚀速率,另一种方式是安装一块电位比两种金属更负的第三金属作为牺牲阳极,这样使得被保护的两种金属都变为阴极从而减缓电偶腐蚀。
使用缓蚀剂:在条件允许下向介质中加入缓蚀剂,让其吸附在金属表面形成一层保护膜,抑制电偶腐蚀的发生。
点蚀
又称孔蚀,是一种在金属表面上产生点状或小孔状腐蚀坑的局部腐蚀形式,通常是由于金属的局部区域存在缺陷或保护膜破裂等导致的。腐蚀坑通常较小且较深,呈点状或小孔分布在金属表面,具有自催化加速腐蚀的特点,一旦点蚀坑形成,坑内的腐蚀环境会变得更加恶劣,加速腐蚀的进行。
图5:点蚀
点蚀常见的预防措施
材料选择与优化:例如在含氯离子的腐蚀性环境中,可以选择高铬、高钼的不锈钢或镍基合金,这些合金中的铬、钼等元素能够提高材料的钝化膜稳定性,增强抗点蚀能力。或者通过通过合理的热处理、加工工艺等手段,改善材料的微观结构,减少杂质、夹杂物和缺陷的存在,提高材料的均匀性和致密性,从而降低点蚀的敏感性。例如,对金属进行细化晶粒处理,可使材料的耐点蚀性能得到提高。
环境控制:尽量降低像氯离子、溴离子等的腐蚀介质中侵蚀性离子的浓度,对于一些循环水系统可以通过离子交换树脂、反渗透等方法去除水中有害离子,减少点蚀的发生风险。将介质的pH值控制在适当的范围内,一般来说大多数金属在中性或弱碱性环境中的点蚀敏感性相对较低。降低温度和压力也是可以减缓化学反应速率、减少点蚀发生的一种方式。
表面处理:在金属表面涂覆油漆、树脂、陶瓷涂层等的防腐涂层形成物理屏障,有效阻止腐蚀介质与金属表面的直接接触。另外,可通过化学或电化学方式使金属表面形成一等稳定的钝化膜,提高金属的耐腐蚀性。
合理设计流体系统:确保流体在系统中均匀流动,避免出现流速过低或过高的区域,防止因流体停滞或冲刷导致腐蚀介质局部聚集或对钝化膜造成破坏。
定期维护和监测。
间晶腐蚀
沿着金属材料的晶界发生的选择性腐蚀,使晶粒间的结合力减弱,材料的强度和韧性显著下降,而晶粒本身的腐蚀相对较小。这种腐蚀主要集中在晶界区域,宏观上金属表面可能没有明显的腐蚀迹象,但材料的内部结构已遭受到破坏,力学性能严重下降。
图6:不锈钢的间晶腐蚀
晶间腐蚀常见的预防措施
材料选择与加工:在热锻或焊接工艺中,选用的不锈钢含碳量应低于0.03%,可有效降低晶间碳化物的析出,从而提高抗晶间腐蚀能力,还有一些若含碳量高于0.03%,则可通过添加含钛、铌、钽的稳定化元素,经高温处理,优先与碳结合形成碳化物,可保持不锈钢的稳定性。优化热加工工艺,在材料的加工过程中,合理控制加热温度、时间和冷却速度等加工参数,避免在敏化温度区间长时间滞留。
如下图:只要在一定温度下,钢的受热温度和持续时间停留在曲线的左边,就不会发生晶间腐蚀。
图7:在一定温度下,冷却过程所需时间
热处理:将合金加热到高温单相区保温,使过剩相充分溶解到固溶体中后快速冷却,以抑制第二相在晶界析出,从而消除晶间腐蚀倾向。而对于含有钛、铌等稳定化元素的不锈钢,在固溶处理后需要进行稳定化处理,即在 850℃-950℃保温一定时间,使钛、铌等元素与碳充分结合形成稳定的碳化物,固定碳元素,防止在后续使用过程中碳与铬结合形成碳化铬,从而提高抗晶间腐蚀能力。
应力腐蚀开裂
是一种在拉应力和特定的腐蚀介质共同作用下,金属材料发生的脆性开裂现象,裂纹通常起源于金属表面的局部腐蚀坑或缺陷处,在应力作用下裂纹逐渐扩展,最终导致材突然断裂,断裂前几乎没有明显的塑性变形。
图8:应力腐蚀开裂
在非合金和低合金钢中也可能出现应力腐蚀开裂。其本质属于晶间腐蚀开裂,而奥氏体不锈钢中出现的开裂则属于穿晶腐蚀开裂。
图9:穿晶应力腐蚀 vs. 晶间应力腐蚀
应力腐蚀常见的预防措施
材料选择与设计:选择具有良好耐应力腐蚀性的材料,例如,在含氯离子的环境中,可选用双相不锈钢、镍基合金等;在高温高压的氢环境中,选用抗氢脆性能好的材料,如低合金钢中添加铬、钼、钨等合金元素,提高材料的抗应力腐蚀能力。在优化结构设计上,合理设计结构的形状和尺寸使其受力均匀,减少局部应力过大的情况,而对于要承受较大应力的部件,可增加其厚度或采用加强筋等结构进行加固。
应力控制:通过合适的像对焊接结构进行焊后热处理、机械拉伸、震动时效等方式,降低金属材料中的残余应力。在设备安装和使用过程中也要严格遵守操作规范,避免施加过大的外力或过载运行,防止产生过高的拉应力,而对于长期承受交变应力的部件,要进行疲劳强度设计和评估。
环境控制:需要控制腐蚀介质和调整环境温度和压力。
表面处理和防护:涂覆防腐涂层和采用缓蚀剂进行保护。
定期监测和维护。
氢脆
由于金属材料在冶炼、加工、使用等过程中吸收了氢原子,导致材料的韧性和延展性降低,在一定的应力作用下发生脆性断裂的现象。氢脆断裂通常是突发性的,断裂前是没有明显宏观的塑性变形,断口呈脆性特征,且与氢的来源和存在形式密切相关。
高强度紧固件在酸洗或电镀过程可能导致氢渗入到金属材料中,大部分氢呈气体散出,小部分会以原子的形式扩散进入到金属中,氢原子在金属的晶粒结构中非常活跃,并趋向转移到应力集中区域,而当该高强度紧固件受到应力时,划痕或夹杂物这类微小的表面缺陷就可能导致细纹不断开裂至紧固件失效。
图10:氢脆
氢脆断裂是一种延迟失效的状态,一般发生在数小时或数周后,最容易发生在高性能等级公制10.9及更高或英制8级和更高的螺纹紧固件上,表面硬化的螺纹部件也存在风险。
氢脆常见的预防措施
材料选择与处理:硬度大于320 HV或抗拉强度大于1000N/mm²的高强度紧固件容易发生氢脆,所以需要禁止使用电镀或酸洗,可采用例如喷丸强化、滚压强化等特殊的表面处理工艺,在材料表面引入压应力。此外,通过精炼工艺提高高强度紧固件的纯净度,严格控制材料中特别是硫、磷等有害杂质。
加工与制造过程控制:在金属材料的加工过程中,如锻造、轧制、机械加工等,避免采用可能导致材料产生大量缺陷或残余应力的工艺。另外在加工和制造中应采取措施方式氢的引入,例如在焊接时选用低氢型焊条,严格控制像焊接电流、电压、速度等的焊接工艺参数,避免焊接区域产生过多的氢;在金属表面处理过程中如酸洗、电镀等要严格控制时间和温度,像酸洗后进行烘烤除氢,一般碳钢在200℃左右烘烤2-4小时,合金钢在300℃左右烘烤4-6小时,可有效去除材料中的氢。
环境控制:在设备的使用环境中,尽量减少氢的来源,保持使用环境的干燥和适当的温度。
应力控制:通过合适的热处理工艺,如消除应力退火,将金属材料加热到一定温度并保温一段时间,然后缓慢冷却,可有效降低材料中的残余应力,减少氢脆的发生风险。对于一些大型复杂结构,可采用局部加热、振动时效等方法降低局部残余应力。在设备的安装和使用过程中,要严格按照操作规程进行,避免施加过大的外力或过载运行,防止产生过高的拉应力。对于长期承受交变应力的部件,要进行疲劳强度设计和评估,确保其在使用寿命内不会因应力过大而发生氢脆。
表面防护和监测。
紧固件作为整个装配的一部分,必须保证其品质始终与连接件品质相当甚至高于连接件,只有了解不同类型的防腐和预防措施才能获得有效、持续的连接性能。
免责声明:本网站所转载的文字、图片与视频资料版权归原创作者所有,如果涉及侵权,请第一时间联系本网删除。
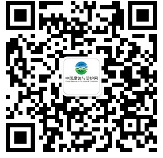
官方微信
《腐蚀与防护网电子期刊》征订启事
- 投稿联系:编辑部
- 电话:010-62316606
- 邮箱:fsfhzy666@163.com
- 腐蚀与防护网官方QQ群:140808414