英国首先在80Ni-20Cr合金中加入少量铝和钛,形成γ'相(gamma prime)以进行强化,研制成第一种具有较高的高温强度的镍基合金。同一时期,美国为了适应活塞式航空发动机用涡轮增压器发展的需要,开始用Vitallium钴基合金制作叶片。
此外,美国还研制出Inconel镍基合金,用以制作喷气发动机的燃烧室。以后,冶金学家为进一步提高合金的高温强度,在镍基合金中加入钨、钼、钴等元素,增加铝、钛含量,研制出一系列牌号的合金,如英国的"Nimonic",美国的"Mar-M"和"IN"等;在钴基合金中,加入镍、钨等元素,发展出多种高温合金,如X-45、HA-188、FSX-414等。由于钴资源缺乏,钴基高温合金发展受到限制。
高温合金材料的性能特征:
Ø优秀的高温强度及塑性
Ø良好的抗氧化性及抗热腐蚀性
Ø优异的抗蠕变性能、抗裂变性能
Ø良好的组织稳定性
Ø变形加工困难
Ø具有较好的性能价格比
在高温合金发展过程中,工艺对合金的发展起着极大的推进作用。
20世纪
40-50
年代初
20世纪
50年代
20世纪
60年代
高温合金生产制备工艺较为复杂,熔炼、铸造、热处理为主要流程工艺。生产流程及工艺的稳定对高温合金材料的力学性能产生直接影响。快速发展的经济和科学技术为各种新型高温合金材料的研发和推广提供了较大的发展空间,在对合金性能要求越来越高的情况下,必须要对各种工艺进行不断的完善和优化,保证各种工艺与高温合金材料的变化相适应。工艺的不断完善引入可实现性能的不断提升,发展新型的高温合金,进而推动相关产品与行业的发展。
高温合金制备工艺
严格控制化学成分是保证高温合金具备优异性能的基础,熔炼工序能有效消除大于临界尺寸的夹杂物,降低氧、氮、及硫的含量,从源头上提高高温合金的纯净度,因此熔炼工序在高温合金的制备工艺中处于首要位置。
目前国际上高温合金的熔炼方法主要有真空感应炉(VIM)、真空自耗炉(VAR)、电渣重熔炉(ESR)。近年以粉末高温合金为代表的新型高温合金应用领域愈加广泛,粉末高温合金的熔炼工艺成为前沿研究的技术,国际上俄罗斯粉末高温合金采用VIM 或VIM+VAR 双联熔炼工艺,美国粉末高温合金采用 VIM+ESR+VAR 三联工艺,而国内粉末高温合金基本采用 VIM 单炼工艺,导致我国粉末高温合金材料纯净度低于国外先进水平。
高温合金精密铸造技术以熔模铸造工艺为主,发展形成了等轴晶类型、定向柱晶与单晶类型的精密铸造形式。目前高温合金铸件已经开始向着复杂化、大型化、高精确度化的方向发展,对铸造工艺、流程形成一定的挑战,也促使熔模精密铸造技术不断进步,从真空冶炼技术发展到无余量铸造技术、定向凝固技术、单晶技术等方面。
定向合金组织
单晶
铸造技术的提升与高温合金原材料生产制造之间也存在直接的联系,需要结合高温合金材料特性、铸件使用情况等,完善相应的工艺技术模式与机制,控制材料的性能,保证生产工艺稳定性。目前在生产的过程中,高温合金的成分参数与凝固参数控制存在难点,很容易在定向凝固生产或是单晶生产期间出现雀斑、热裂和疏松等缺陷,严重影响产品的高温性能。美国在研究的过程中使用高梯度定向凝固技术进行航空发动机叶片的生产,有效降低了雀斑缺陷问题的发生率,严格控制各个零件尺寸条件下的温度梯度参数,形成一定的生产优化、改良的作用。
精密铸造分类:主要有熔模铸造、陶瓷型铸造、金属型铸造、压力铸造、消失模铸造。
常用熔模铸造基本流程:
-
固溶热处理是指在高于高温合金组织内析出相的全溶温度,使合金中各种分布不均匀的析出相充分溶解至基体相中,从而实现强化固溶体并提高韧性及抗蚀性能,消除残余应力的作用,以便继续加工成型,并为后续时效处理析出均匀分布的强化相做准备。
-
时效热处理是指在强化相析出的温度区间内加热并保温一定时间,使高温合金的强化相均匀地沉淀析出,碳化物等均匀分布,从而实现硬化合金和提高其强度的作用。
铸造高温合金是由合金锭重熔后直接浇注或定向凝固成零件的高温合金 ,其发展始于20世纪40年代 。1943年美国首次在涡轮喷气发动机 J-33上选用了 HS-21制作涡轮工作叶片,替代变形合金 Hastelloy-B的叶片,开创了航空发动机使用铸造高温合金的先例 。随着航空发动机的发展,对高温合金性能提出越来越高的要求 ,为 了提高热强性能,在变形高温合金中相继加入了多种合金元素 ,导致变形加工 困难的问题,于是 ,航空和冶金工作者越来越重视铸造合金的研究 。20世纪50年代 末 ,真空熔炼技术出现,合金中有害杂质和气体去除,合金成分得到精确控制 ,高温性能不断提高,研制出 IN100,B1900,MAR-M200等多种性能优异的合金。20世纪60年代定向凝固技术的发展 ,促进了定向柱状晶和单晶高温合金的蓬勃发展 ,使航空发动机的使用温度达到 1700℃ 以上 。
铸造高温合金不再考虑锻造变形性能 ,可通过精密铸造方法或定向凝固工艺铸造出形状复杂且有通畅内腔的无余量空心薄壁叶片。因此,铸造高温合金元素总量要显著高于变形高温合金 ,其中,固溶强化元素增添了 Re,Ru等元素,难熔金属元素 w 的含量提高(有些 合金超过 10%)沉淀强化合金元素除 Al,Ti之外,还加入 Nb,Ta,Hf,V等元素。研究表明,铸造高温合金元素含量总和可达 50%,沉淀强化相 γ相含量达 60%-70%,此外,铸造高温合金粗大的晶粒和凝固偏析引起的枝晶骨架 以及 晶界和枝晶间形成的一次碳化物骨架,可有效地强化合金,因此,铸造高温合金持久强度、抗拉强度都明显高于变形高温合金。同成分的铸造高温合金要比变形高温合金使用温度提高 10-30℃,同时,加入更多的 合金元素也有利于开发新合金 。
铸造高温合金按凝固方法分类可分为等轴晶铸造高温合金、定向凝固柱晶高温合金和单晶高温合金三类。
1)等轴晶铸造高温合金
2)定向凝固柱状晶高温合金
定向凝固高温合金是通过定向凝固技术制备出晶界平行于主应力轴从而消除有害横向晶界的柱状晶高温合金。20世纪 60年代中期,美国PW公司发明了定向凝固工艺并用于生产镍基合金柱状晶涡轮叶片,可提高叶片工作温度 500C。我国于20世纪 70年代开始定向凝固合金研究工作,到现在已研制出多种定向凝固柱状晶高温合金,并在多种型号的发动机上 使用,某些定向凝固合金叶片已开始批量生产。
定向凝固涡轮盘
3)单晶高温合金
采用定向凝固工艺消除所有晶界的高温合金称为单晶高温合金。20世纪80年代以来。随着合金设计理论水平的提高,成分不断改进,熔炼工艺优化,铸造技术进步,使其力学性能的提高一再获得突破,如今 ,单晶高温合金已经发展到第五代。
典型镍单晶高温合金
单晶高温合金中加入了大量 W,Mo ,Ta,Re,Ru等难熔金属元素 ,其含量比同代次定向凝固柱状晶合金都高。难熔金属产生固溶强化 ,提高固溶温度 ,时效时大量析出沉淀强化相γ相。第一代单晶高温合金不含稀土金属元素 Re,随后 ,发现添加元素 Re后 80%原子能进入γ固溶体,引起较大的晶格畸变,20%的元素 Re直接进入γ相,提 高γ相的溶解度,增加γ相体积分数,从而提高合金承温能力,而且 Re原子的加入有助于减小单晶晶粒缺陷和表面再结晶倾向。从第二代 单晶合金开始添加元素 Re, 3%Re和 6%Re是第二代和第三代单晶高温合金的标志 ,但 Re原子加入会促进有害的 TCP相生成和次生反应区(SRZ)生成 , 降低组织稳定性 。第四代 和第五代单晶合金以分别加入 3%和 6% 的元素 Ru,抑制TCP相析出,增加合金组织稳定性。
第一至第五代单晶高温合金在 137MPa,1000h
条件下的承温能力
等轴晶、定向凝固及单晶 M-M200的蠕变和持久性能
变形高温合金是指将铸锭进行冷 、热加工制成各种型材或 零件毛坯 ,最后制成热端零件 的高温合金 ,其关键是合金锭具有成形能力。变形高温合金是最先用于航空发动机的高温合 金 ,1939年英国首先研制成功 Nimonic75,1944年 Nimonic80A 正式使用 ,1956年中国发展了第一种变形高温合金 GH3030,之后又相继研制了GH4033等合金,经过 60多年的发展,全世界目前生产的变形高温合金超过 200种 ,中国生产的变形高温合金超过 70种 。
与铸造高温合金相比,变形高温合金合金化程度低,因此 ,熔点较高,热加工温度上限较高 ,合金再结晶温度较低 ,降低热加工温度下限,因此 ,变形高温合金热加工范围较铸造高温合金宽。此外,变形高温合金偏析较轻,合金组织中的γ析出相数量较少,变形抗力低 ,加工变形性能良好 ,因而可以通过热加工和冷加工工艺制备出不同形状的型材和零件毛坯 。
按基体元素的不同,变形高温合金可分为铁基变形高温合金 、镍基变形高温合金和钴基 变形高温合金。
1)铁基变形高温合金
铁基变形高温合金是从奥氏体不锈钢发展起来的。铁基变形高温合金Fe含量在 18%~45%,为稳定奥氏体,通常要入 25%-45%的元素Ni,也可加入适量的元素 Mn,N,C。代替部分元素 Ni。为保证合金有充分的抗氧化腐 蚀能力,铁基变形合金中还加入 11%~23%的元素 Cr,所以铁基高温合金实际上是以 Fe-Ni-Cr三元系为基,当Ni含量大于40%时一般也称作铁镍基高温合金。铁基高温合金的基体通常有 Fe-15Cr-25Ni型、Fe-15Cr-35Ni型、Fe-15Cr-45Ni型。
常见铁基变形高温合 金的牌号、化学成分及使用温度
铁基变形高温合金按其强化方式可分为三类 :第一类是碳化物 、氮化物或复合碳氮化物强化合金,其使用温度在 550-600℃,现已逐渐被其他合金取代;第二类是固溶强化合金, 在高温下有良好的抗氧化和抗腐蚀能力 ,使用温度在 800~ 950℃,主要用作板材 ,制造承力不大但工作温度较高的零件;第三类是金属间化合物强化合金,使用温度在 600-750℃。
铁基变形高温合金高温力学性能
2)镍基变形高温合金
镍为面心立方结构 ,从室温到高温没有同素异构转变 ,是一种非常良好的基体金属,而且镍化学稳定性良好 ,在 500℃以下几乎不氧化 ,常温下不受湿气 、水及盐类水溶液的作用。镍基变形高温合金通常加入 10%-25%的Cr元素,以保证合金具有良好的抗氧化腐蚀性能,所以镍基合金实际上 以 Ni-Cr为基体。此外 ,有些合金在 Ni-Cr固溶体中加入元素 Co(15Yo-20%),Mo(约 15%)或 w (约 11%),分别构成 以 Ni-Cr-Co,Ni-Cr-Mo,Ni-Cr-W 为基体的三元系变形高温合金。
中国常用镍基变形高温合金的牌号、化学成分及使用温度
镍基变形高温合金高温力学性能
3)钴基变形高温合金
钴在 400℃以下具有密排六方结构 ,在高温时会发生同素异构转变为面心立方结构 ,且这种转变具有非热特性 ,在温度循环过程中具有可逆性 ,为使钴基合金具有稳定面心立方 构的γ奥氏体 ,通常加入 5%-25%的镍或 9%-20%的铁 ,此外 ,还通常加入 20%左右的元素 Cr,以便在合金表面形成防护性能良好的 Cr203氧化膜来提高钴基变形高温合金的抗氧化性能和抗腐蚀性能。所以,钴基变形高温合金实质上是以Co-Ni-Cr三元系为基,另含 W,Mo,Nb,Ta等固溶强化元素和碳化物形成元素。
部分钴基变形高温合金的化学成分 (质量分数)
钴基变形高温合金与镍基变形高温合金相比,其加工硬化速率较大,零件成形后的表面质量较好 ,但在成形过程中,一般需要较多的热加工加热火次或冷变形中间退火次数 ,其加工成形设备的吨位也要求较大。钴基变形高温合金在高于 980℃时 ,其强度很高 ,抗热疲劳、热腐蚀和耐磨腐蚀性优异,但是,钴基变形高温合金以碳化物为主要强化相,缺少共格类的强化相,在较低和中等温度范围内持久强度比镍基变形高温合金低。
钴基变形高温合金高温力学性能
随着高温合金工作温度和强度的不断提高以及综合性能的改善,合金中强化元素含量不断增加 ,成分越来越复杂,热加工性能变得很差 ,不少高性能镍基高温合金已不能热加工变形 ,只能以铸态使用 。然而 ,由于铸造组织偏析严重导致了显微组织的不均匀和力学性能的波动,故而开始采用粉末冶金工艺生产高温合金克服上述缺点 ,得到几乎无偏析、组织均匀、热加工性能良好的高温合金材料。粉末高温合金是先进航空发动机关键热端部件的优选材料,主要用于制造涡轮盘、压气机盘、鼓筒轴、涡轮盘、高压挡板等发动机热端高温承力转动部件。目前,用粉末冶金法制得的高温合金可分为普通粉末 (powdermetallurgy, PM)高温合金和氧化物弥散强化 (oxidedispersionstrengthened,ODS)高温合金两类。目前,已经研制了四代粉末高温合金,制备出的涡轮盘等多种粉末高温合金关键零部件已成 功应用于先进航空发动机 。
1)普通粉末高温合金
粉末高温合金的工艺流程大致如下 :制备粉末~ 固实~热加工变形 ~热处理。粉末的质量严重影响着粉末高温合金的性能 ,通常要求粉末的气体含量及夹杂物含量低 ,粒度分布及形状合适。高温合金粉末的制备方法主要有惰性气体雾化法、旋转电机法和真空雾化法三种。惰性气体雾化法应用最广泛 ,在整个真空及密闭的设备中,经真空熔炼的合金熔体经注口流下,在高压高速的气流中雾化成粉末。所用的气体通常是氩气,所得粉末中气体含量约为40-200μg/g,粉末主要呈球状,也有一些空心颗粒、串状颗粒或片状颗粒,粒度分布较宽 ,有粗大的也有特别细小的颗粒 ,需经筛分后再集取 。
粉末高温合金的性能强烈地受制粉、固实化工艺的影响,不 同制粉工艺的粒度分布差异对合金的晶粒和性能有一定的影响 ,在热等静压合金中能表现出来,但在热挤压合金中破碎完全,已显示不出粒度分布的影响。
部分美国、欧洲的粉末冶金高温合金的化学成分与性能
部分俄罗斯研发的粉末高温合金成分及性能
部分中国的粉末冶金高温合金化学成分与性能
中国研制的三种涡轮盘粉末冶金高温合金性能
2)氧化物弥散强化高温合金
氧化物弥散强化高温合金(ODS)是将细小的氧化物颗粒 (一般选用 Y203)均匀地分散于高温合金基体中,通过阻碍位错运动而产生强化效果的一类合金。机械合金化工艺的发明是ODS高温合金发展史上的一个里程碑 ,机械合金化是在高能 球磨机内完成的,常用的高能球磨机有搅拌式、振动式和滚筒式三种。
几种典型的ODS镍基高温合金
ODS高温合金力学性能最大的特点是高温强度 。加入的氧化物颗粒 Y203具有很高的熔点 (2417℃),且不与基体发生反应,所以具有非常好的热稳定性和化学稳定性,其强化作用可以维持到接近合金的熔点温度,因此,ODS高温合金的使用温度可以达到 0.9Tm。
目前国内外已生产和研制的 ODS高温合金主要有三类:
国际上高温合金的研制始于上世纪二三十年代,主要在英美俄等国家展开。目前, 世界范围内仅有不超过 50 家企业具备生产高性能高温合金的能力,主要集中在美英法德等欧美国家,整个行业头部效应明显。
国际知名的高端高温合金生产国家和企业主要有美国的通用电气公司、普拉特-惠特尼公司、佳能-穆斯克贡公司、汉因斯·司泰特公司、国际因科合金公司等,以及英国的国际镍公司、日本的 JFE 钢铁株式会社、新日铁住金株式会社、神户制钢等。这些企业经过多年的技术积累,均已建立了完善的企业级的高温合金工艺、性能体系、过程控制及选材标准,生产的高温合金具有成本低、质量高且稳定性好等优势。
国内高温合金起步较晚,初期以仿制为主,目前已建立较为完备的产品体系。由于高温合金主要运用于航空航天、核电等战略核心领域,因此作为高精尖产品,国外厂商管控严格,很少出口销售。国内高温合金行业从 20 世纪 50 年代末仿制前苏联高温合金体系开始,经过 60 余年的发展,经历了由仿制到仿创结合再到独创的发展历程,形成了我国独特、系统、完整的高温合金体系,是国际上公认的四大较完整的高温合金体系之一。
我们把国内从事高温合金的厂家分为四类:
目前,国内规模较大的高温合金生产企业有抚顺特钢和钢研高纳。此外,宝钢特钢、攀长钢、中科院金属所、北京航材院也具备一定的产能。
目前具备铸造高温合金精铸件的厂家分为两类,一类是钢研高纳、中科院金属所和北京航材院三家公司;另一类是黎明、西航、南方、成发等专业发动机厂自行生产精铸件。三家单位主要承接航天航空发动机厂对外委托的精铸件业务。目前三家单位在铸造高温合金的材料制备、生产技术上均有各自特点,其中钢研高纳产能大于其余两家。
高温合金全球市场持续成长,中国成为主要增量市场。我国高温合金市场中,变形高温合金和镍基高温合金占比最大,根据制造工艺,变形高温合金约占整个高温合金市场 70%左右,其次是铸造高温合金(20%)和粉末高温合金(10%);根据合金基体元素,镍基高温合金占比达 80%左右,镍-铁高温合金和钴基高温合金 占比分别约为 14%和 6%。
高温合金第一大应用场景是航空航天领域,需求份额占比为 55%。高温合金材料是航天航空发动机的重要制造原材料,主要应用于发动机的燃烧室、导向器、涡轮叶片、涡轮盘、尾喷口及机匣等部件。其次,高温合金具备耐高温、耐腐蚀等优良性能,也被广泛应用于燃气轮机、石油化工、工业和汽车领域等场景。
1)航空发动机
高温合金从诞生起就应用于航空发动机,在现代航空发动机中,高温合金材料主要用于四大热端部件:燃烧室、导向室、涡轮叶片和涡轮盘,此外还用于机匣、环件、加力燃烧室和尾喷口等部件。
2)汽车涡轮增压器
汽车废气增压器涡轮也是高温合金材料的重要应用领域。目前,我国涡轮增压器生产厂家所采用的涡轮叶轮多为镍基高温合金涡轮叶轮,它和涡轮轴、压气机叶轮共同组成一个转子。根据每万辆汽车涡轮增压器高温合金用量约为 3.5 吨,2021 年汽车生产行业需要高温合金材料约 9128.7 吨,市场规模约为 18.3 亿元。考虑到未来汽车数量和我国装配率的提高,假设未来年均增长率为 5%,预计到 2030 年我国汽车市场对高温合金材料的需求总计约为 10.6 万吨。
3)核电领域
核电用高温合金包括:燃料元件包壳材料、结构材料和燃料棒定位格架,高温气体炉热交换器等,均是其他材料难以代替的。
世界核能协会发布的核燃料报告预测, 全球核电装机容量预计将以每年 2.6%的速度增长,到 2040 年全球核电装机容量将达到 61500 万千瓦,且装机容量增长将主要来自中国、俄罗斯等国家。2022 年 1 月,随着福清核电站 6 号机组并网发电,我国大陆并网核电机组达到 53 台,总装机容量 5463.695 万千瓦,仅次于美国与法国,位居世界第三位。国家能源局预计,我国核电装机规模将在 2030 年达到 1.2 亿~1.5 亿千瓦,因此估计截至 2030 年 我国还将新建设完成约 8000 万千瓦的核电机组。每座 60 万千瓦核电站约需高温合金材料 600 吨,以此计算,共需高温合金材料约为 80000 吨,考虑到核电站建设国产率约为 80%,预计未来平均每年高温合金国内需求量约 为 7111 吨。
4)其他领域
高温合金材料在玻璃制造、冶金、医疗器械等领域也有着广泛的用途。
免责声明:本网站所转载的文字、图片与视频资料版权归原创作者所有,如果涉及侵权,请第一时间联系本网删除。
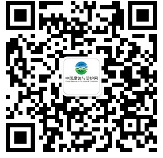
官方微信
《腐蚀与防护网电子期刊》征订启事
- 投稿联系:编辑部
- 电话:010-62316606
- 邮箱:fsfhzy666@163.com
- 腐蚀与防护网官方QQ群:140808414