导 语
金属材料的化学成分、加工工艺、热处理工艺对其组织有着重要的影响,且金属材料的组织对其力学性能及物理性能有着重要影响。金相检验是研究金属材料显微组织的一种方法。在使用光学显微镜观察低碳钢时,会发现部分铁素体晶粒表面发灰,根据制样的情况不同,发灰晶粒的数量和颜色也不同。这种情况对金属材料的定量分析造成了一定干扰,也降低了显微组织形貌的质量。因此,分析灰晶粒的形成原因,对提高显微组织形貌质量具有一定的意义。
许多学者对金相试样中的划痕、假象、浮雕、污染等缺陷进行了大量的研究,但对低碳钢铁素体晶粒表面发灰问题的研究较少。研究人员采用一系列理化检验方法分析了铁素体晶粒发灰与其表面形貌的关系,以避免该类问题再次发生。
01 理化检验
1.1 金相检验
采用尺寸为15mm×18mm(直径×长度)的20钢标样。将20钢标样依次用320,600,1000,1500,2000目的碳化硅砂纸进行预磨机磨制,预磨机的转速为700r/min,直到划痕均匀统一;然后依次用粒度为0.5μm和2.5μm的金刚石磨粒抛光膏对试样进行抛光,抛光机的转速为1400r/min,加水间隔时间为20s,抛光时间为6min;用4%(体积分数,下同)硝酸乙醇溶液腐蚀试样7s;最后,将试样置于光学显微镜下观察,结果如图1所示。
由图1可知:试样中珠光体层片状组织明显,但大部分铁素体晶粒发灰,只有小部分晶粒呈亮白色。将光阑孔径调到最小以获得更清晰、景深更大的图像,但亮度降低,图像发暗。
选择图1中的3个晶粒放大观察,其中A晶粒为亮白晶粒,B晶粒为浅灰晶粒,C晶粒为深灰晶粒(见图2~4)。A晶粒表面有微小颗粒感,粗糙度较小,A晶粒左上角晶粒也较为亮白,其表面有均匀、统一的微小划痕,但划痕较细小,漫反射较弱,晶粒并没有明显发暗。B晶粒表面除微小颗粒外,还有明显划痕,划痕相对较粗,且划痕沿统一方向紧密排列。C晶粒表面呈坑点状,且非常粗糙。
图5为20钢的低倍显微组织形貌。由图5可知:以晶界为界,每个晶粒内部的灰色程度和表面形貌几乎是一致的,不存在一半灰一半亮白的晶粒。并且晶粒与晶粒之间的颜色不存在过渡,如暗灰晶粒的右侧就是一个亮白晶粒,没有从暗灰晶粒过渡到浅灰晶粒、再过渡到亮白晶粒这一情况,相邻晶粒之间都存在明显的色差。
1.2 腐蚀试验
1.2.1 腐蚀剂对灰晶粒的影响
在腐蚀剂中掺入水,擦拭试样表面后吹干,将试样置于光学显微镜下观察,结果如图6所示。由图6可知:试样表面产生水迹斑痕,呈片状分布,该部位为水滴吹干最后位置,颜色呈灰色或黄色,边界清晰,但未沿晶界分布,水迹内的晶粒颜色有灰色和白色,并不是均匀、统一的颜色;调小光阑孔径后发现水迹边界处晶粒的表面形貌一致,但水迹内外的颜色不一致。综合上述分析,判断水迹不是灰晶粒的产生原因。
将试样腐蚀后进行冲水,等待1min后再擦拭试样表面并吹干,将试样置于光学显微镜下观察,结果如图7所示。由图7可知:试样表面分布有大面积的锈斑,锈斑呈独立的小区域,边界较为模糊;锈斑呈铁锈色,颜色暗灰,表面布满麻点,锈斑未沿晶界分布,大部分是贯穿晶粒的。说明锈斑不是导致灰晶粒形成的原因。
将1mL4%硝酸乙醇腐蚀溶液与99mL无水乙醇混合,对试样进行腐蚀、冲水、擦拭、吹干处理,模拟乙醇被腐蚀剂污染的情况。将试样置于光学显微镜下观察,结果如图8所示。由图8可知:腐蚀斑痕呈片状随机分布,其尺寸大小不一,颜色偏蓝紫色,局部呈彩色;腐蚀斑痕未沿晶界分布,大部分是穿过晶粒的,被穿过晶粒的表面形貌一致,但斑痕内呈蓝紫色,斑痕外呈灰色或白色。说明腐蚀斑痕不是导致灰晶粒产生的原因。
1.2.2 腐蚀程度对灰晶粒的影响
采用4%硝酸乙醇溶液分别腐蚀试样3s和30s,制备出腐蚀程度较轻和较重的金相试样,试样的显微组织形貌如图9所示。由图9可知:当试样腐蚀程度较轻时,晶界不清晰,铁素体晶粒既有白色,也有灰色,且晶粒表面越粗糙,灰色越深;当试样腐蚀程度较重时,晶界较深、较粗,珠光体发黑,铁素体晶粒既有白色,也有灰色,其晶粒的灰度与腐蚀程度较轻的晶粒无明显差别,说明腐蚀程度不是引起晶粒发灰的原因。
1.3 划痕试验
采用粒度为2000目的砂纸将试样沿左右方向进行磨制,沿前后方向进行抛光,因此,水平方向产生的划痕为磨制划痕,竖直方向的划痕为抛光划痕,抛光1min后试样的金相检验结果如图10所示。
由图10可知:砂纸磨制时,许多粗划痕没有被去除,大部分晶粒呈灰色,小部分晶粒呈白色;将光阑孔径调小后发现白色晶粒表面较为平整,划痕较为细小,灰色晶粒表面存在较多的深划痕,方向为垂直方向和竖直方向,分别对应未抛平的磨制划痕和较深的抛光划痕,这些划痕都使得铁素体晶粒表面粗糙,颜色发灰。
抛光3min后试样的金相检验结果如图11所示。由图11可知:试样表面基本没有粗大划痕,残余较多的细长划痕,方向沿竖直方向,该划痕为抛光划痕;将光阑孔径调小后发现已有部分铁素体晶粒呈白色,灰色晶粒也变得较浅,且晶粒表面划痕越深,颜色越灰。
使用粒度为2.5μm的抛光膏对 试样抛光2min,以去除粗大划痕,再使用粒度为0.5μm的抛光膏对试样轻抛8min,抛光10min后试样的金相检验结果如图12所示。由图12可知:大部分铁素体呈亮白色,灰晶粒非常少,放大观察发现试样已没有明显划痕;将光阑孔径调小后发现亮度几乎没有变化,只有极少灰晶粒的表面变暗,说明试样表面已十分平整,光源亮度对其观察结果影响不大;放大观察其中的白色晶粒,发现其表面有沿竖直方向十分细小的划痕,分布较为均匀,判断其是抛光划痕。综合上述分析发现,当抛光划痕足够细小时,铁素体呈亮白色,可以避免晶粒发灰。
02 综合分析
20钢是一种典型的低碳钢,其退火平衡组织为珠光体+铁素体,正常情况下铁素体应该呈亮白色,珠光体应该呈黑白相间的片状。铁素体的亮白程度应与其表面粗糙度成正比,表面越平整,漫反射程度越小,晶粒亮白程度越大;表面越粗糙,漫反射程度越大,晶粒越暗,最终形成灰色晶粒。由上述理化检验结果可知,晶粒位向不同导致抛光内应力及腐蚀速率不同,灰色晶粒的内应力大,腐蚀速率较快,导致试样表面粗糙,造成晶粒发暗。虽然整个抛光面上的抛光状态几乎是一致的,但各晶粒的位向及内应力不同,因此腐蚀后并没有出现大面积灰度一致的晶粒群,甚至相邻的几个晶粒都存在明显的色差。造成晶粒表面凹凸不平、粗糙度大的原因有铁素体表面发生氧化、腐蚀过度、抛光划痕等。划痕引起晶粒表面形貌变化,用显微镜观察时,会发生漫反射现象,最终导致铁素体晶粒表面发灰。虽然微观上的划痕不可能消除,但当抛光划痕足够细小,产生的漫反射作用十分微弱时,晶粒可以达到亮白的效果。
03 结论及建议
金相试样表面抛光划痕残留,引起表面粗糙度较大,造成了漫反射现象,最终导致晶粒发灰。采用延长抛光时间、减小抛光力度、使用更小粒度的抛光膏等措施可以使铁素体晶粒表面划痕变浅,划痕较为细小,从而得到绝大多数呈亮白色的铁素体,提高了金相检验结果的准确性。
免责声明:本网站所转载的文字、图片与视频资料版权归原创作者所有,如果涉及侵权,请第一时间联系本网删除。
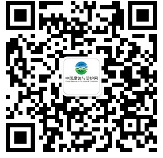
官方微信
《腐蚀与防护网电子期刊》征订启事
- 投稿联系:编辑部
- 电话:010-62316606
- 邮箱:fsfhzy666@163.com
- 腐蚀与防护网官方QQ群:140808414