奥氏体不锈钢以Cr元素和Ni元素为主,其耐腐蚀性高、塑性好、易于加工成型,且具有良好的焊接性能,是目前最重要的耐酸不锈钢。奥氏体不锈钢焊管是将奥氏体不锈钢的钢带卷曲成型后焊接制成的钢管,奥氏体不锈钢焊管的生产工艺相对简单、生产效率高、产品性能优越,且应用十分广泛,如化工设备用管、换热设备用管、装饰管等。不锈钢焊管在使用过程中一旦发生开裂,可能会造成非常严重的后果,所以在焊管加工完成后通常要对其进行密封性测试,如水压测试。研究人员采用宏观观察、化学成分分析、金相检验、扫描电镜(SEM)及能谱分析等方法对裂纹产生原因进行分析,以防止该类问题再次发生。 01 理化检验
1.1 宏观观察 近几年,常有一些焊管客户反馈不锈钢焊管在密封性测试后出现裂纹,与常见的焊管裂纹不同的是,常见焊管裂纹通常发生在焊缝位置,而该类裂纹不是发生在焊缝处,而是发生于焊管的母材位置,且为垂直于焊缝的横向裂纹,裂纹较短,长度通常小于3mm,有时小如针尖状(见图1)。该类裂纹在304、316L、321等奥氏体不锈钢中均被发现过,已发现缺陷的母材试样均为厚度小于1.0mm的薄板。 开裂断口宏观形貌如图2所示,中间为开裂区域,左侧为裂纹两边人为掰断的区域。 1.2 化学成分分析 试样基体为316L不锈钢,母材的化学成分如表1所示。 1.3 金相检验 在母材上截取金相试样,将其置于光学显微镜下观察,结果如图3所示。由图3可知:母材组织为奥氏体,晶粒度为9.0级。焊管规格(外径×壁厚)为25mm×0.5mm,在自动生成线上完成焊接、焊后热处理加工,随后对其进行水压测试。在焊接之后未发现明显裂纹,而在完成水压测试后,发现焊管母材上出现了大量垂直于焊缝的横向短裂纹。 1.4 扫描电镜和能谱分析 将裂纹断口试样进行机械切割、超声清洗、乙醇清洗、烘干,再置于SEM下观察,并对其进行能谱分析,结果如图4及表2所示。 02 综合分析
根据以上分析结果,发现开裂试样具有以下特征:(1)开裂位置在非焊缝区,且没有向焊缝扩展;(2)开裂呈沿晶特征,断口呈冰糖状;(3)开裂处铜元素沿晶界富集。 以上特征符合铜污染裂纹(CCC)的特征,CCC是一种液态金属脆化(LME)现象,即具有较好塑性的固态金属材料在接触到特定的液态金属后,原子间的结合力下降,在受到拉伸力后,金属材料的强度和塑性显著下降,这通常发生在两种熔点相差较大的金属之间。对于奥氏体不锈钢来说,焊接过程中常见的能引起LME现象的低熔点金属为Cu和Zn。裂纹位置富集了大量的Cu元素,纯铜熔点为1083℃,随纯度降低熔化温度降低,比不锈钢的熔点低得多,在焊接过程中,热影响区如果受到铜污染,则可能会发生LME现象,而母材受到铜污染后产生裂纹的原因则为进行了焊后热处理,不锈钢焊后热处理温度通常选择大于1000℃。该温度下热处理时表面沾染的铜变成液态,而奥氏体不锈钢的热膨胀系数较高,在毛细作用下,液态Cu会沿着奥氏体晶界向内渗入,从而形成晶界渗透,破坏了晶界的连续性,导致晶界脆化,结合力下降,在拉应力的作用下产生裂纹。如果材料较薄,则形成穿透性裂纹,因此,将该裂纹确认为CCC。 作为合金添加的铜一般不会引起铜污染裂纹。最有可能引入铜污染的就是焊管自动加工生产线,在焊管生产线上存在较多的铜制工件,如夹具、触头等。防止CCC最有效的办法是避免材料和铜发生刮擦残留,大多数情况下,应注意焊接夹具、导电嘴或其他可能接触材料表面的铜基部件。 对制管生产流程进行调查发现,采用钨极氩弧焊(TIG)焊接方式制管,除了正常的焊枪位置有保护气体外,管内设置内保护气体。用户使用铜管进行内保护气体输送,现场可发现铜管与不锈钢内壁接触,在生产运行时发生刮擦,且铜管已经发生一定程度的磨损,由此确认输送内保护气体的铜管为CCC的来源。用户更换送气管后不再发生开裂问题。 03 结论
(1)316L不锈钢焊管裂纹为铜污染裂纹,为输送焊接内保护气体铜管在焊管内壁刮擦残留导致。 (2)焊管材料在加工及使用过程中要远离铜、锌、铝等低熔点物质,或尽量避免与该类物质的刮碰摩擦,才能从根源上防止该类微裂纹产生。 (3)用户更换不锈钢保护气输送管后,焊管不再发生开裂现象。
免责声明:本网站所转载的文字、图片与视频资料版权归原创作者所有,如果涉及侵权,请第一时间联系本网删除。
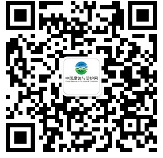
官方微信
《腐蚀与防护网电子期刊》征订启事
- 投稿联系:编辑部
- 电话:010-62316606
- 邮箱:fsfhzy666@163.com
- 腐蚀与防护网官方QQ群:140808414