疲劳断裂是金属构件断裂的主要形式之一,在金属构件疲劳断裂失效分析基础上形成和发展了疲劳学科。自从Whler的经典疲劳著作发表以来,人们充分地研究了不同材料在各种不同载荷和环境条件下试验时的疲劳性能。尽管大多数工程技术人员和设计人员已经注意到疲劳问题,而且已积累了大量的实验数据,目前仍然有许多设备和机器发生疲劳断裂。
疲劳设计现在已从无限寿命设计发展到有限寿命设计。零件、构件和设备的寿命估算,已成为疲劳强度的一个重要组成部分。疲劳已从一个古老的概念发展成为材料科学、力学和工程设计相结合的一门新兴学科——疲劳强度。
疲劳断裂的基本形式和特征
1 疲劳断裂失效的基本形式
机械零件疲劳断裂失效形式很多:
按交变载荷的形式不同可分为:拉压疲劳、弯曲疲劳、扭转疲劳、接触疲劳、振动疲劳等;
按疲劳断裂的总周次的大小 (Nf)可分为:高周疲劳 (Nf>10) 和低周疲劳 (Nf<10);
按零件服役的温度及介质条件可分为:机械疲劳(常温、空气中的疲劳)、高温疲劳、低温疲劳、冷热疲劳及腐蚀疲劳等。
但其基本形式只有两种,即由切应力引起的切断疲劳及由正应力引起的正断疲劳。其它形式的疲劳断裂,都是由这两种基本形式在不同条件下的复合。
(1) 切断疲劳失效
切断疲劳初始裂纹是由切应力引起的。切应力引起疲劳初裂纹萌生的力学条件是:切应力/缺口切断强度≥1;正应力/缺口正断强度<1。
切断疲劳的特点:疲劳裂纹起源处的应力应变场为平面应力状态;初裂纹的所在平面与应力轴约成45角,并沿其滑移面扩展。
由于面心立方结构的单相金属材料的切断强度一般略低于正断强度,而在单向压缩、拉伸及扭转条件下,最大切应力和最大正应力的比值(即软性系数)分别为2.0、0.5、0.8,所以对于这类材料,其零件的表层比较容易满足上述力学条件,因而多以切断形式破坏。例如铝、镍、铜及其合金的疲劳初裂纹,绝大多数以这种方式形成和扩展。低强度高塑性材料制作的中小型及薄壁零件、大应力振幅、高的加载频率及较高的温度条件,都将有利于这种破坏形式的产生。
(2) 正断疲劳失效
正断疲劳的初裂纹,是由正应力引起的。初裂纹产生的力学条件是:正应力/缺口正断强度≥1,切应力/缺口切断强度<1。
正断疲劳的特点:疲劳裂纹起源处的应力应变场为平面应变状态;初裂纹所在平面大致上与应力轴相垂直,裂纹沿非结晶学平面或不严格地沿着结晶学平面扩展。
大多数的工程金属构件的疲劳失效都是以此种形式进行的。特别是体心立方金属及其合金以这种形式破坏的所占比例更大;上述力学条件在试件的内部裂纹处容易得到满足,但当表面加工比较粗糙或具有较深的缺口、刀痕、蚀坑、微裂纹等应力集中现象时,正断疲劳裂纹也易在表面产生。高强度、低塑性的材料、大截面零件、小应力振幅、低的加载频率及腐蚀、低温条件均有利于正断疲劳裂纹的萌生与扩展。
2 疲劳断裂失效的一般特征
金属零件在使用中发生的疲劳断裂具有突发性、高度局部性及对各种缺陷的敏感性等特点。引起疲劳断裂的应力一般很低,断口上经常可观察到特殊的、反映断裂各阶段宏观及微观过程的特殊花样。
(1) 疲劳断裂的突发性
疲劳断裂虽然经过疲劳裂纹的萌生、亚临界扩展、失稳扩展三个元过程,但是由于断裂前无明显的塑性变形和其它明显征兆,所以断裂具有很强的突发性。即使在静拉伸条件下具有大量塑性变形的塑性材料,在交变应力作用下也会显示出宏观脆性的断裂特征,因而断裂是突然进行的。
(2) 疲劳断裂应力很低
循环应力中最大应为幅值一般远低于材料的强度极限和屈服极限。例如,对于旋转弯曲疲劳来说,经10次应力循环破断的应力仅为静弯曲应为的20~40%;对于对称拉压疲劳来说,疲劳破坏的应力水平还要更低一些。对于钢制构件,在工程设计中采用的近似计算公式为:
(3) 疲劳断裂是一个损伤积累的过程
疲劳断裂不是立即发生的,往往经过很长的时间才完成。疲劳初裂纹的萌生与扩展均是多次应力循环损伤积累的结果。
在工程上,通常把试件上产生一条可见的初裂纹的应力循环周次 (N0)或将N0 与试件的总寿命Nf 的比值 (N0/Nf ) 作为表征材料疲劳裂纹萌生孕育期的参量。疲劳裂纹萌生的孕育期与应力幅的大小、试件的形状及应力集中状况、材料性质、温度与介质等因素有关。
(4) 疲劳断裂对材料缺陷的敏感性
金属的疲劳失较具有对材料的各种缺陷均为敏感的特点。因为疲劳断裂总是起源于微裂纹处。这些微裂纹有的是材料本身的冶金缺陷,有的是加工制造过程中留下的,有的则是使用过程中产生的。
部分材料的N0/Nf值
各因素对N0/Nf值影响的趋势
(5) 疲劳断裂对腐蚀介质的敏感性
金属材料的疲劳断裂除取决于材料本身的性能外,还与零件运行的环境条件有着密切的关系。对材料敏感的环境条件虽然对材料的静强度也有一定的影响,但其影响程度远不如对材料疲劳强度的影响来得显著。大量实验数据表明,在腐蚀环境下材料的疲劳极限较在大气条件下低得多,甚至就没有所说的疲劳极限。
疲劳断口形貌及其特征
1 疲劳断口的宏观形貌及其特征
由于疲劳断裂的过程不同于其他断裂,因而形成了疲劳断裂特有的断口形貌,这是疲劳断裂分析时的根本依据。
典型的疲劳断口的宏观形貌结构可分为疲劳核心、疲劳源区、疲劳裂纹的选择发展区、裂纹的快速扩展区及瞬时断裂区等五个区域。一般疲劳断口在宏观上也可粗略地分为疲劳源区、疲劳裂纹扩展区和瞬时断裂区三个区域,更粗略地可将其分为疲劳区和瞬时断裂区两个部分。大多数工程构件的疲劳断裂断口上一般可观察到三个区域,因此这一划分更有实际意义。
2 疲劳断口的微观形貌特征
(1) 疲劳断裂的微观形貌特征
疲劳断口微观形貌的基本特征是,在电子显微镜下观察到的条状花样,通常称为疲劳条痕、疲劳条带、疲劳辉纹等。疲劳辉纹是具有一定间距的、垂直于裂纹扩展方向、明暗相交且互相平行的条状花样 。
延性疲劳辉纹:是指金属材料疲劳裂纹扩展时,裂纹尖端金属发生较大的塑性变形。疲劳条痕通常是连续的,并向一个方向弯曲成波浪形。通常在疲劳辉纹间存在有滑移带,在电子显微镜下可以观察到微孔花样。高周疲劳断裂时,其疲劳辉纹通常是延性的。
脆性疲劳辉纹:是指疲劳裂纹沿解理平面扩展,尖端没有或很少有塑性变形,故又称解理辉纹。在电子显微镜下既可观察到与裂纹扩展方向垂直的疲劳辉纹,又可观察到与裂纹扩展方向一致的河流花样及解理台阶。脆性金属材料及在腐蚀介质环境下工作的高强度塑性材料发生的疲劳断裂,或缓慢加载的疲劳断裂中,其疲劳辉纹通常是脆性的。
(1) 疲劳断裂性质的判别
为了进一步分析载荷性质及环境条件等因素的影响,有必要利用断口的微观特征对零件疲劳断裂的具体类型作进一步判别。
高周疲劳断裂性质的判别
高周疲劳断口的微观基本特征是细小的疲劳辉纹。此外,有时尚可看到疲劳沟线和轮胎花样。依此即可判断断裂的性质是高周疲劳断裂。但要注意载荷性质、材料结构和环境条件的影响。
低周疲劳断裂性质的判别
低周疲劳断口的微观基本特征是,粗大的疲劳辉纹或粗大的疲劳辉纹与微孔花样。同样,低周疲劳断口的微观特征随材料性质、组织结构及环境条件的不同而有很大差别。
对于超高强度钢,在加载频率较低和振幅较大的条件下,低周疲劳断口上可能不出现疲劳辉纹,而代之以沿晶断裂和微孔花样为特征。
热稳定不锈钢的低周疲劳断口上除具有典型的疲劳辉纹外,常出现大量的粗大滑移带及密布着细小二次裂纹。
高温条件下的低周疲劳断裂,由于塑性变形容易,一般其疲劳辉纹更深、辉纹轮廓更为清晰,并且在辉纹间隔处往往出现二次裂纹。
振动疲劳断裂性质的判别
金属微振疲劳断口的基本特征是细密的疲劳辉纹,金属共振疲劳断口的特征与低周疲劳断口相似。但在疲劳裂纹的起始部位通常可以看到磨损的痕迹、压伤、微裂纹、掉块及带色的粉末(钢铁材料为褐色;铝、镁材料为黑色)。
腐蚀疲劳断裂性质的判别
腐蚀疲劳断口上的疲劳辉纹比较模糊,二次裂纹较多并具泥纹花样。
碳钢、铜合金的腐蚀疲劳断裂多为沿晶分离;奥氏体不锈钢和镁合金等多为穿晶断裂;Ni-Cr-Mo钢在空气中多呈穿晶断裂,而在氢气和H2S气氛中多为沿晶或混晶断裂。加载频率低时,腐蚀疲劳易出现沿晶分离断裂。
金属热疲劳断裂性质的判别
金属热疲劳断裂的微观特征是多为粗大的疲劳辉纹,或粗大的疲劳辉纹加微孔花样,并且其上多有一层氧化物。
接触疲劳断裂性质的判别
接触疲劳断口和磨损疲劳断口特征基本相同,其疲劳辉纹均因摩擦而呈现断续状和不清晰特征。
金属零件的疲劳断裂失效
1 疲劳断裂的形式
(1) 弯曲疲劳断裂
金属零件在交变的弯曲应力作用下发生的疲劳破坏称为弯曲疲劳断裂。弯曲疲劳又可分为单向弯曲疲劳、双向弯曲疲劳及旋转弯曲疲劳三类。其共同点是初裂纹一般源于表面,然后沿着与最大正应力垂直的方向向内扩展,当剩余截面不能承受外加载荷时,构件发生突然断裂。
单向弯曲疲劳断裂
像吊车悬臂之类的零件,在工作时承受单向弯曲负荷。承受脉动的单向弯曲应力的零件,其疲劳核心一般发生在受拉侧的表面上。疲劳核心一般为一个,断口上可以看到呈同心圆状的贝纹花样,且呈凸向。最后断裂区在疲劳源区的对面,外围有剪切唇。
构件的次表面存在较大缺陷时,疲劳核心也可能在次表面产生。在受到较大的应力集中的影响时,疲劳孤线可能出现反向(呈凹状),并可能出现多个疲劳源区。
双向弯曲疲劳断裂
某些齿轮的齿根承受双向弯曲应力的作用。零件在双向弯曲应力作用下产生的疲劳断裂,其疲劳源区可能在零件的两侧表面,最后断裂区在截面的内部。两个疲劳核心并非同时产生,扩展速度也不一样,所以断口上的疲劳断裂区一般不完全对称。材料的性质、负荷的大小、结构特征及环境因素等都对断口的形貌有影响,其趋势与单向弯曲疲劳断裂基本相同。
旋转弯曲疲劳断裂
许多轴类零件的断裂多属于旋转弯曲疲劳断裂。旋转弯曲疲劳断裂时,疲劳源区一般出现在表面,但无固定地点,疲劳源的数量可以是一个也可以是多个。疲劳源区和最后断裂区相对位置一般总是相对于轴的旋转方向而逆转一个角度。由此可以根据疲劳源区与最后断裂区的相对位置推知轴的旋转方向。
当轴的表面存在较大的应力集中时,可以出现多个疲劳源区。此时最后断裂区将移至轴件的内部。
(2) 拉压疲劳断裂
拉压疲劳断裂最典型的例子是各种蒸汽锤的活塞杆在使用中发生的疲劳断裂。在通常情况下,拉压疲劳断裂的疲劳核心多源于表面而不是内部,这一点与静载拉伸断裂时不同。但当构件内部存在有明显的缺陷时,疲劳初裂纹将起源于缺陷处。此时,在断口上将出现两个明显的不同区域,一是光亮的圆形疲劳区(疲劳核心在此中心附近);二是瞬时断裂区。在疲劳区内一般看不到疲劳弧线,而在瞬时断裂区具有明显的放射花样。
应力集中和材料缺陷将影响疲劳核心的数量及其所在位置,瞬时断裂区的相对大小与负荷大小及材料性质有关。
(3) 扭转疲劳断裂
各类传动轴件的断裂主要是扭转疲劳断裂,扭转疲劳断裂的断口形貌主要有三种类型:
正向断裂
断裂表面与轴向成45°角,即沿最大正应力作用的平面发生的断裂。单向脉动扭转时为螺旋状;双向扭转时,其断裂面呈星状;应力集中较大的呈锯齿状。
切向断裂
断面与轴向垂直,即沿着最大切应力所在平面断裂,横断面齐平。
混合断裂
横断面呈阶梯状,即沿着最大切应力所在平面起裂并在正应力作用下扩展引起的断裂。正向断裂的宏观形貌一般为纤维状,不易出现疲劳弧线;切向断裂较易出现疲劳弧线。
(4) 振动疲劳断裂
许多机械设备及其零部件在工作时往往出现在其平衡位置附近作来回往复的运动现象,即机械振动。机械振动在许多情况下都是有害的,它除了产生噪音和有损于建筑物的动负荷外,还会显著降低设备的性能及工作寿命。由往复的机械运动引起的断裂称为振动疲劳断裂。
当外部的激振力的频率接近系统的固有频率时,系统将出现激烈的共振现象。共振疲劳断裂是机械设备振动疲劳断裂的主要形式,除此之外,尚有颤振疲劳及喘振疲劳。
振动疲劳断裂的断口形貌与高频率低应力疲劳断裂相似,具有高周疲劳断裂的所有基本特征。振动疲劳断裂的疲劳核心一般源于最大应力处,但引起断裂的原因,主要是结构设计不合理。因而应通过改变构件的形状、尺寸等调整设备的自振频率等措施予以避免。
(5) 接触疲劳
2 疲劳断裂原因分析
(1) 零件的结构形状
零件的结构形状不合理,主要表现在该零件中的最薄弱的部位存在转角、孔、槽、螺纹等形状的突变而造成过大的应力集中,疲劳微裂纹最易在此处萌生。
(2) 表面状态
不同的切削加工方式(车、铣、刨、磨、抛光)会形成不同的表面粗糙度,即形成不同大小尺寸和尖锐程度的小缺口。这种小缺口与零件几何形状突变所造成的应力集中效果是相同的。由于表面状态不良导致疲劳裂纹的形成是金属零件发生疲劳断裂的另一重要原因。
(3) 材料及其组织状态
材料选用不当或在生产过程中,由于管理不善而错用材料造成的疲劳断裂也时有发生,金属材料的组织状态不良是造成疲劳断裂的常见原因。一般的说,回火马氏体较其它混合组织,如珠光体加马氏体及贝氏体加马氏体具有更高的疲劳抗力;铁素体加珠光体组织钢材的疲劳抗力随珠光体组织相对含量的增加而增加;任何增加材料抗拉强度的热处理通常均能提高材料的疲劳抗力。组织的不均匀性,如非金属夹杂物、疏松、偏析、混晶等缺陷均使疲劳抗力降低而成为疲劳断裂的重要原因。
(4) 装配与联接效应
装配与联接效应对构件的疲劳寿命有很大的影响。正确的拧紧力矩可使其疲劳寿命提高5倍以上。容易出现的问题是,认为越大的拧紧力对提高联接的可靠性越有利,使用实践和疲劳试验表明,这种看法具有很大的片面性。
(5) 使用环境
环境因素(低温、高温及腐蚀介质等)的变化,使材料的疲劳强度显著降低,往往引起零件过早的发生断裂失效。例如镍铬钢(0.28%C,11.5% Ni,0.73%Cr),淬火并回火状态下在海水中的条件下疲劳强度大约只是在大气中的疲劳极限的20%。
免责声明:本网站所转载的文字、图片与视频资料版权归原创作者所有,如果涉及侵权,请第一时间联系本网删除。
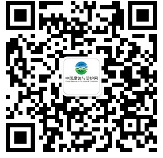
官方微信
《腐蚀与防护网电子期刊》征订启事
- 投稿联系:编辑部
- 电话:010-62316606-806
- 邮箱:fsfhzy666@163.com
- 腐蚀与防护网官方QQ群:140808414