飞机材料一旦出现腐蚀问题,不仅会对飞机本身性能的发挥造成阻碍,严重时甚至会对人民的生命以及财产安全造成巨大的损失。腐蚀问题是材料与环境发生作用的表面现象,电化学腐蚀发生在固体材料与电解质溶液中的固液界面,化学腐蚀发生在固体材料与周围气体环境的固气界面。因此系统全面地分析一个腐蚀问题,一方面要具体分析材料的本身特性,即内在各个因素;另一方面要全面分析周围的环境,以及环境中的介质及其存在的状态,即腐蚀的外在因素。
铝合金的耐蚀性能
纯铝的化学性质虽然很活泼,但由于它在空气中易与氧结合,在表面形成一层致密、稳定的氧化铝薄膜(钝化膜),可保护内层金属不再继续氧化,因此纯铝在大气中具有很好的耐蚀性能。但退火态纯铝的抗拉强度相当低,只有45 MPa,因此其使用范围仅局限于飞机结构中受力不大的非结构件。飞机结构上使用的铝合金大致可以分为两种,即可热处理强化的铝合金和不可热处理强化的铝合金。
1 不可热处理强化的铝合金
(1)Al-Mn系合金(3000系列)
常用合金为3A21铝合金,合金中锰为主要合金元素,它具有较高的强度、良好的塑性和工艺性能。3A21合金在室温下的组织为a固溶体和在晶界上形成的(α+Al6Mn)共晶体。由于α固溶体与Al, Mn相的电极电位几乎相等,因此合金的耐蚀性较好。该类合金的缺点是在冷变形硬化状态下不能用在温度高于100℃的场合,原因是在该条件下,其对应力腐蚀开裂(SCC)的敏感性较高。
(2)Al-Mg系合金(5000系列)
由于主要合金元素镁的密度比铝还小,加上其良好的焊接性能和抗震性能,所以这类合金在航空工业中得到了广泛的应用,常用的有5A02、5A03、5A06等铝合金。该类合金的强度一般高于3A21铝锰合金的强度。在实际使用中,该材料呈单相固溶体组织,因此具有良好的耐蚀性能。其在大气、海水中的耐蚀性能优于3A21合金,与纯铝相当;在酸性和碱性介质中,其耐蚀性稍逊于3A21合金。
该系合金的含镁量愈高,强度也愈高。但其含镁量不宜过高,应控制在8%(质量分数)以内。原因是当含镁量高于8%以后,如果对其进行退火处理,会在晶界上连续析出Mg5Al8相,导致其耐蚀(晶间腐蚀和应力腐蚀)性能下降。
2 可热处理强化的铝合金
这类铝合金可以通过热处理来产生沉淀强化的效果,其强度较高,又称为硬铝合金,是航空上最为重要的结构件材料之一。
总体上看,铝合金的强度随温度升高而降低,当飞机速度较高时,气动加热会影响铝合金强度。铝合金化后,其耐腐蚀性能减弱,常见的腐蚀形态有点蚀、缝隙腐蚀、晶间腐蚀、剥蚀和应力腐蚀等。
点蚀是铝合金最常见的腐蚀形态之一,硬铝合金等耐点蚀能力较差。铝合金易产生缝隙腐蚀,因为缝隙内易积存水分和污物,使涂层和包铝层发生水化作用,降低其保护作用。
Al-Cu、Al-Cu-Mg、Al-Zn-Mg等合金产生晶间腐蚀的倾向较大。晶间腐蚀与 热 处理工艺有关,采用自然时效腐蚀倾向较低,人工时效腐蚀倾向则较高,而过时效腐蚀倾向又降低。Al-Cu-Mg系硬铝合金中的T6热处理状态比T3热处理状态具有更大的晶间腐蚀敏感性,因此除在高温下工作的构件以外,这类合金一般均采用自然时效处理。
在飞机结构中,Al-Cu-Mg合金产生剥蚀的情况最多,Al-Mg、Al-Mg-Si、Al-Zn-Mg合金也有发生,但在形变Al-Si系中未见发生。
Al-Cu、Al-Cu-Mg硬铝合金,特别是Al-Zn-Mg、Al-Zn-Mg-Cu等超硬铝合金容易产生应力腐蚀。
(1)Al-Cu-Mg和Al-Cu-Mn系合金(2000系列)
Al-Cu-Mg系合金是可热处理强化铝合金中最重要的合金系列之一,飞机结构中使用最为广泛的该类合金为2024铝合金,这类合金的主要强化相为S相(CuMgAl2),其次为θ相(CuAl2),通常在T3状态下使用,具有断裂韧性高、抗疲劳裂纹扩展能力强的特点。不过此状态下的抗蚀(晶间腐蚀)性能不够好,薄板一般包铝后使用,也可配合阳极化处理、阿洛丁化学处理进一步提高其耐蚀性能。2000系列中目前最新、性能最好的合金是2524铝合金,其韧性和抗疲劳性能均较2024铝合金有重大改进,已成功应用于B777客机。
(2)Al-Zn-Mg-Cu系合金(7000系列)
Al-Zn-Mg-Cu系合金中最重要的是7075铝合金,在T6状态下其强度最高,但断裂韧性最低,耐蚀性能(尤其是抗晶间腐蚀和应力腐蚀性能)较差。为了增强其耐蚀性能,需对其进行过时效处理,常见的有T73处理,即首先对铝合金进行固溶处理,然后进行双级时效处理(在较低温度下加热保温一段时间后,再在较高温度下加热和保温一段时间)。经此处理以后,虽然材料的抗拉强度下降大约15%,但是材料的耐应力腐蚀性能和晶间腐蚀抗力却大大提高。7055是目前该系合金中合金化程度最高、强度也最高的铝合金,近期研究成功的T77处理工艺,使该合金在高强度下仍能保持较高的断裂韧性和良好的抗应力腐蚀性能,该种合金已成功应用于B777客机的主体结构。需要说明的是,在进行双级时效处理之前,首先应对固溶处理(淬火)的工艺进行严格控制,否则将严重影响材料的抗晶间腐蚀性能。
现代飞机结构极大地依赖于铝合金,它们还用于飞机骨架、蒙皮及受力件。在现代亚声速民用客机上,铝合金材料仍然是飞机构件的支柱材料,并且在不断推出更新的航空铝锂合金等。因此,铝合金在航空领域的重要作用仍会持续很多年。
空客公司在A380客机大部分结构零件采用了新型且先进的金属材料,铝合金占的比例最大(占机体结构质量的61%),尤其是在A380机翼部位(机翼的80%以上是铝合金材料)。为了实现性能改进,以提高强度和损伤容限,增强稳定性并提高抗腐蚀能力,开发出了创新性的铝合金材料和工艺技术。A380-800飞机在铝合金结构上取得的主要成就包括:
①在机身壁板上引用了很宽的钣金材料,减少了连接件,从而减轻了质量;
②在主地板横梁上采用了先进的铝锂合金挤压件,其在这一部位的应用可与碳纤维增强塑料相媲美。
2014年投入使用的A350客机也采用了最新的铝锂合金,不仅由于材料密度降低而减轻了机体质量,同时还可以采用与现有的铝合金零件相同的技术和方法对新材料的零部件进行修理。
钛合金的耐蚀性能
钛不但资源丰富,而且具有密度小、比强度高、耐热性高及优异的耐蚀性,此外,钛还具有很高的塑性和优良的冷热加工性能,从而使其在现代工业中占有极其重要的地位,在航空、化工、导弹、航天及舰船等方面,钛及其合金得到广泛的应用。
钛合金在飞机结构和非结构方面应用广泛(见表1),钛合金在航空领域的广泛应用主要基于以下一个或几个理由:
(1)优秀的抗腐蚀性,在腐蚀过程中不会产生点蚀。
(2)高的比强度。
(3)高的使用温度。
(4)减轻质量,密度大约比钢小40%。
(5)减轻空间约束问题。
(6)和其他材料的兼容性。
表1 各种钛合金在飞机上的应用
1 纯钛
钛有较高的强度(退火后,工业纯钛的抗拉强度σb=550~700MPa),约为铝的6倍,钛同时兼有钢(强度高)和铝(质轻)的优点,因此钛的比强度在结构材料中是很高的。钛的线膨胀系数较小,在高温条件下或热加工过程中产生的热应力小;导热性差,只有铁的1/5;摩擦因数大(μ=0.42),因此切削、磨削加工困难;钛的弹性模量较低,屈服强度高,因此钛及其合金冷变形加工时的回弹性大,不易成形和校直;纯净的钛有良好的可塑性,它的韧性超过纯铁的2倍。
工业纯钛按其杂质含量不同,可分为TA1,TA2,TA3三个牌号。牌号顺序数字增大,杂质含量增加,钛的强度增加,塑性下降。
2 钛合金
为了提高强度,可在钛中加入合金元素。合金元素融入α-Ti中形成α固溶体,融入β-Ti中形成β固溶体。铝、碳、氮、氧和硼等元素使α与β同素异晶转变温度升高,称为α稳定化元素;而铁、钼、镁、铬、锰和钒等元素使同素异晶转变温度降低,称为β稳定化元素;锡和锆等元素对转变温度影响不明显,称为中性元素。
根据使用状态的组织,钛合金可分为α钛合金、β钛合金和(α+β)钛合金三类。(α+β)钛合金兼有α和β钛合金两者的优点,耐热性和塑性都较好,并且可进行热处理强化,这类合金的生产工艺也比较简单。因此,(α+β)钛合金的应用比较广泛,其中以TC4(Ti-6Al-4V)应用最为广泛。
钛合金氧化膜的稳定性远高于铝和不锈钢氧化膜的稳定性。保护膜因机械操作遭到破坏时,能很快恢复。所以,钛及钛合金在很多高活性介质中都具有较高的耐腐蚀能力。
合金钢的耐蚀性能分析
一般来说,约有12%~16%的飞机基本结构是用合金钢(包括不锈钢)制作的。其最大的优点是具有高强度(见表2)和高弹性模量,其应用见表3。
表2 飞机常用合金钢的强度范围
强度低于200KSI认为是低强度,强度高于200KSI认为是高强度
表3 飞机常用的合金钢
高强度优质合金结构钢在潮湿工业大气、海洋大气等环境中,抗腐蚀性能比碳钢有所提高。但是,在没有保护措施的情况下,它们仍具有碳钢的各种腐蚀倾向。
一般把在空气和中性介质中能够耐腐蚀的钢称为不锈钢,而把能在各种侵蚀性较强的介质中工作的耐蚀钢称为耐酸钢。通常把不锈钢和耐酸钢统称为不锈耐酸钢,简称为不锈钢。
不锈钢的“不锈”只是相对的,在一定的条件下不锈钢也会腐蚀,因此没有绝对“不锈”的不锈钢。按照内部微观组织结构的不同,可以把不锈钢分为马氏体不锈钢、铁素体不锈钢、奥氏体不锈钢和双相不锈钢四种。
1 马氏体不锈钢
马氏体不锈钢是一类含碳量较高的铬不锈钢,其含碳量在0.1%~0.9%范围,含铬量在12%~18%范围。这类钢的特点是含碳量比其他种类不锈钢要高,除添加合金元素铬外,有时还添加少量的钼或镍,如1Cr17Ni2,9Cr18MoV等。马氏体不锈钢比铁素体不锈钢和奥氏体不锈钢的耐蚀性都差,而且含碳量越高,其耐蚀性越差。
马氏体不锈钢在大气、海水和氧化性介质中耐蚀性较好,但在如硫酸、盐酸等非氧化性酸中不耐蚀。
马氏体不锈钢抗局部腐蚀能力较低,如对点蚀、晶间腐蚀和应力腐蚀较敏感,对氢脆敏感性大,因此在有可能产生局部腐蚀的环境中,应尽量避免使用。
2 铁素体不锈钢
铁素体不锈钢是以铬为主要合金元素(质量分数在12%~18%范围),具有体心立方晶体结构的铁基合金,如Cr13型,Cr17型和Cr25~28型等类型,常加入Ni、Mo、Cu、Ti、Nb等合金元素来提高其耐蚀性。
铁素体不锈钢最突出的特点是在含有Cl-离子的水溶液中具有优异的抗应力腐蚀能力,这比镍铬奥氏体不锈钢要好得多。普通铁素体不锈钢抗点蚀、缝隙腐蚀的能力较差,可通过提高铬含量来改善其性能,比如当Cr含量达25%或以上时,其抗点蚀、缝隙腐蚀的性能会得到改善。另外,也可通过在普通铁素体不锈钢中加入合金元素Mo来提高其抗点蚀、缝隙腐蚀的性能。
3 奥氏体不锈钢
奥氏体不锈钢的含铬量一般在18%以上,含镍量一般在8%以上,且室温具有单相奥氏体组织。奥氏体不锈钢不仅具有优良的耐蚀性能,而且也具有良好的综合力学性能、工艺性能和焊接性能,是不锈钢中最重要、用途最广泛的一类不锈钢。18-8类型不锈钢(即含铬17%~19%,含镍7%~9%)为常见的奥氏体不锈钢。
点蚀和缝隙腐蚀是奥氏体不锈钢在氯化物环境中常见的局部腐蚀形态,可通过添加合金元素Cr,Mo来提高其耐蚀性能。随着含Cr量的不断提高,材料表面钝化膜的稳定性也不断增强。Mo的作用有多种解释,通常认为加入Mo后便于形成可溶性钼酸盐,吸附在金属表面的活性位置上,从而抑制了金属的溶解。奥氏体不锈钢对应力腐蚀开裂(SCC)非常敏感,可通过添加合金元素Ni来降低其敏感性。
4 奥氏体-铁素体双相不锈钢
奥氏体-铁素体双相不锈钢的室温组织中同时含有奥氏体相与铁素体相。它既有奥氏体不锈钢所具备的优良的韧性与焊接性能,同时也具有铁素体不锈钢的高强度和耐氯化物应力腐蚀开裂的性能。与纯奥氏体不锈钢相比,奥氏体-铁素体双相不锈钢的晶间腐蚀敏感性也较小,即具有很好的抗晶间腐蚀性能。在较低的应力水平下,奥氏体-铁素体双相不锈钢显示出比奥氏体不锈钢更为优异的耐SCC性能,但是随着应力的不断提高,其耐SCC性能逐渐下降,甚至都不如奥氏体不锈钢。奥氏体-铁素体双相不锈钢具有较高的抗点蚀性能。
总的来说,不锈钢耐蚀性能较高。但是不锈钢在含有氯化物的介质中,由于氯离子的作用,可在不锈钢钝化膜的薄弱区、有缺陷的部位以及有硫化物夹杂或晶界碳化物的地方产生点蚀。在不锈钢构件与其他构件相连的微小缝隙处,易产生缝隙腐蚀。
复合材料的耐蚀性能
复合材料腐蚀主要包括树脂基体腐蚀、增强材料腐蚀、界面腐蚀、应力腐蚀和腐蚀疲劳。非金属材料,如塑料、橡胶等,不能导电,一般来说耐蚀性能都高于金属材料,所以非金属也被广泛地用作保护层,以提高金属材料的耐蚀性。在飞机材料方面,随着民用飞机的安全性、经济性、舒适性和环保性不断提高,复合材料被大量、广泛使用。如波音B737、空客A320等机型已经使用了以环氧树脂为基体,碳纤维、玻璃纤维和芳纶纤维为增强材料的复合材料。
飞机复合材料采用的主要纤维品种有碳纤维、硼纤维等,主要基体材料是环氧树脂。飞机中复合材料结构的形式大致有以下几种:附加于金属结构上的增强铺层,缠绕管件组成的框架,复合材料夹层结构,加强或不加强的蒙皮结构,缠绕旋转壳体或压力容器。复合材料结构须满足飞行温度、湿度、紫外线等介质的大气腐蚀环境的要求。
对于复合材料的构件及机翼前缘、雷达罩等易受雨蚀的部位,飞机在雨中飞行时其迎面受到雨滴的直接撞击,使复合材料构件表面脱黏、破裂且受雨水浸蚀,形成蚀坑甚至使复合材料产生剥离。对于这些部位应采用有效的防雨蚀涂料进行表面防护。
对有导电要求(如防雷击)的复合材料结构应采用搭接线,不可通过复合材料与金属材料(如铝合金)的直接接触或通过紧固件传导电流。
飞机复合材料的防护要求如下:
(1)材料应满足飞机结构温度,湿度,紫外线和大气等腐蚀环境要求;
(2)应优先选与之电位相当的钛合金等;
(3)匹配时,应在结合界面设置不吸湿、不腐蚀和不导电的隔离层;
(4)在易受雨蚀的部位,应采用有效的防雨蚀涂料进行表面防护。
免责声明:本网站所转载的文字、图片与视频资料版权归原创作者所有,如果涉及侵权,请第一时间联系本网删除。
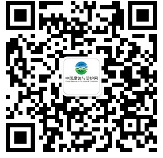
官方微信
《中国腐蚀与防护网电子期刊》征订启事
- 投稿联系:编辑部
- 电话:010-62316606-806
- 邮箱:fsfhzy666@163.com
- 中国腐蚀与防护网官方QQ群:140808414