引言
铜及其合金具有优良的导电、导热和耐腐蚀性能,又具有良好的力学性能和加工成形性,它们还能被循环利用,所以被广泛地应用于人类的生产和生活各个领域。它们是人类最早使用的金属材料之一,距今已有近五千年的历史。随着时代的进步,科学技术的发展,铜及其合金应用更为广泛,涉及电子、电力、汽车、舰船、交通、通信、家电、建筑、冶金、人类生活等。
舰船和海洋工程中的应用
舰船和海洋工程中所用的关键部件,需要具备优良的耐海水腐蚀性能,而铜及铜合金恰恰具有优良的耐海水腐蚀性及防止海生物生长和附着性能,加之铜合金还具有其他优良的综合性能,使它们成为这类工程中不可或缺、甚至不可替代的材料。
舰船和海洋运输船使用铜及铜合金制备的主要部件有各类导线、海水管路和阀门、热交换器、冷凝器、加热器、螺旋桨等,表1列出了其主要用途,铜材用量相当于钢材用量的3%~5%。
表1 舰船重要用铜部位举例
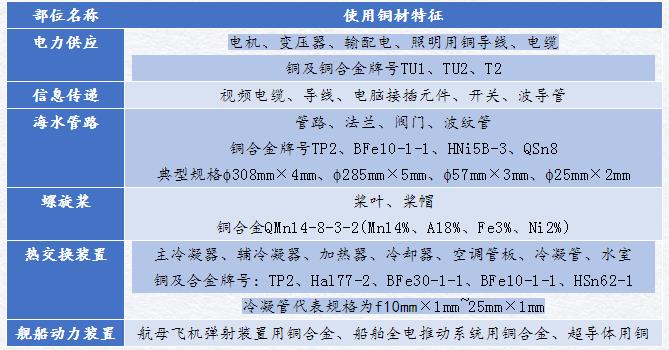
在海洋工程里,铜合金主要用于海水淡化、海盐生产、海上石油开采、滨海电站等。在多级闪蒸海水淡化装置中,铜合金冷凝管是关键材料。近十年随着海水淡化装置增多,铜管需求量大幅增加,据估计2010年至2020年的十年中,需求总量在8万吨左右。但是,目前我国船用换热器、冷凝器、螺旋桨等铜合金部件制造业还有待改进,国产的船用铜合金部件与国外知名厂家的产品相比质量水平偏低,耐蚀性稍差,使用寿命偏短。它们一旦被腐蚀破坏,就会影响设备的正常运行,从而导致船舶在航率降低和运营成本上升,甚至威胁整船的安全。近年来在一些电厂也发生过铜镍合金管的腐蚀泄漏事故,造成重大经济损失。
铜及其合金的分类、牌号和标准化
我国铜及铜合金习惯按色泽分类,一般分为四大类。紫铜,指纯铜,主要品种有无氧铜、普通紫铜、磷脱氧铜、银铜;黄铜,指以铜与锌为基础的合金,又可细分为简单黄铜和复杂黄铜,复杂黄铜中又以第三组元冠名,如镍黄铜、硅黄铜、铅黄铜、铁黄铜;青铜,指除铜-镍、铜-锌合金以外的铜基合金,主要品种有锡青铜、铝青铜、硅青铜、特殊青铜(又称高铜合金);白铜,指铜镍系合金。
对这四类铜及铜合金,国家制定了四大类标准。其一为基础标准,其中GB/T 5231-2012规定了加工铜及铜合金的化学成分及产品形状;其二为化学分析方法标准;其三为理化性能试验方法,其中包括了电阻系数、超声波探伤、涡流探伤、残余应力、脱锌腐蚀、无氧铜含氧量、断口、晶粒度等测定方法;其四为产品标准,其中包括阴极铜、电工用铜线锭、铸造黄铜锭、铸造青铜锭、粗铜、铜-铍中间合金、铜精矿以及铜合金加工材标准。
表2 常见海洋工程用紫铜在国内外标准中相近牌号对照表
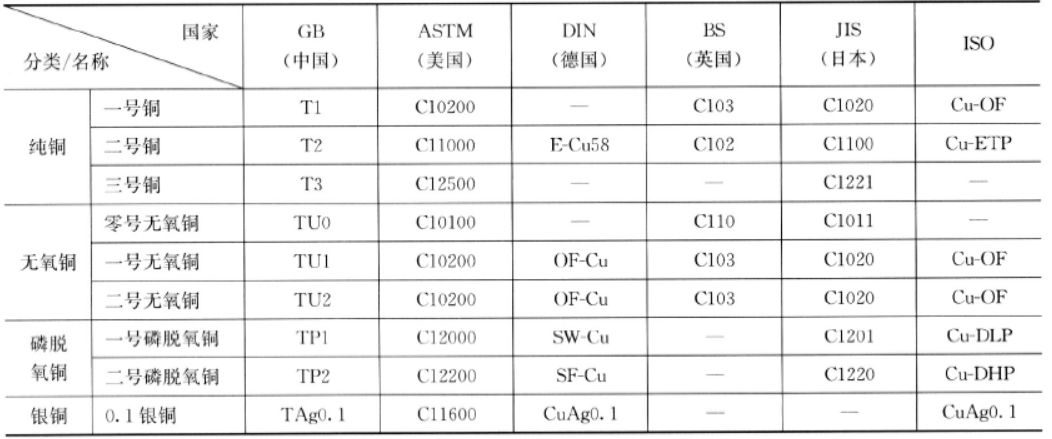
表3 常见海洋工程用黄铜的牌号及成分
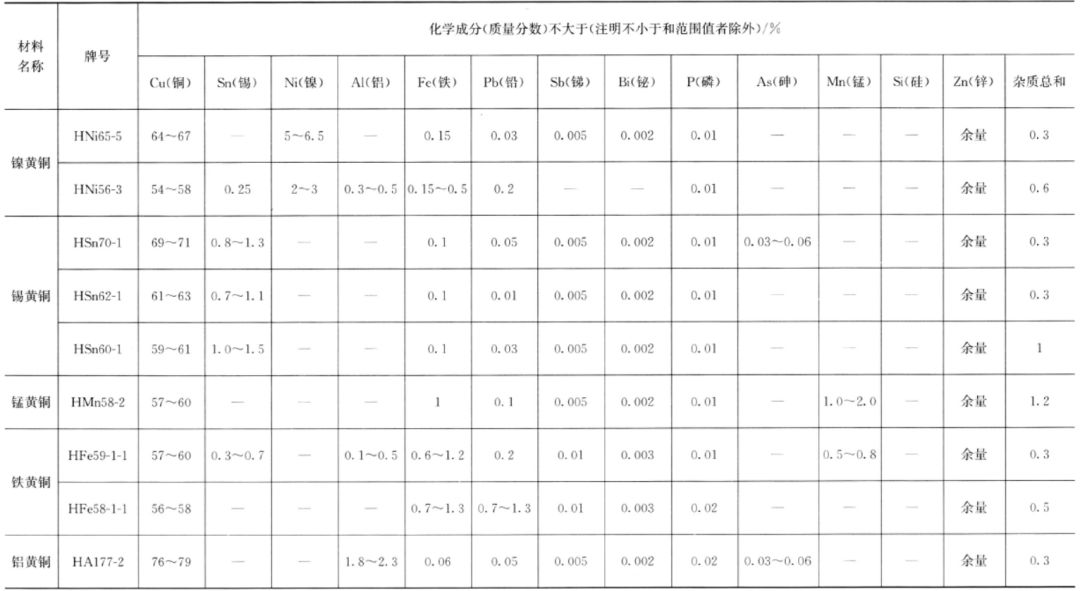
舰船和海洋工程用铜合金的腐蚀
01 海洋环境的腐蚀特性
海水是一种类电解质溶液,溶有一定的氧,含盐量、海水电导率、溶解物质、pH值、温度、海水流速和海生物等都会对腐蚀产生影响,这就决定海水腐蚀的电化学特征:
①海水中的氯离子等卤素离子能阻碍和破坏金属的钝化;
②海水腐蚀的阴极去极化剂是氧,阴极过程是腐蚀反应的控制性环节;
③海水腐蚀的电阻性阻滞较小,异种金属的接触能造成显著的电偶腐蚀;
④在海水中由于钝化的局部破坏,很容易发生点蚀和缝隙腐蚀等局部腐蚀。
海洋环境是指从海洋大气到海底泥浆这一范围内任一种物理状态,包括海 洋大气区、飞溅区、潮汐区、全浸区、海泥区,每个区带都有其特有的腐蚀环境,铜及铜合金在同一海域的不同区域内的腐蚀性是不同的,如图1所示。而全球不同地区的海洋,表现的腐蚀性也有差异,这些差异是由以下的腐蚀因素造成的:温度、风速、流速、日照、盐度、pH值、海生物种类等,可归纳为化学因素、物理因素、生物因素,如表4所示。
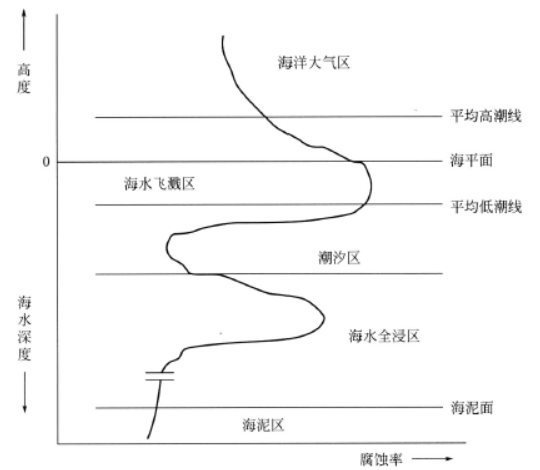
图1 海洋腐蚀环境划分示意图
表4 海水环境划分示意图
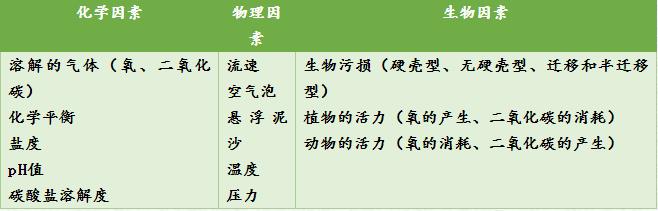
02 铜及铜合金在海洋环境中的耐蚀性
铜及铜合金在海水中耐蚀性优良有多方面的原因。
① 铜的热力学稳定性,即铜的离子化困难。形成Cu2+和Cu+的标准电位分别是0.337V(SHE)和0.521V(SHE)。铜在海水中腐蚀时,阴极反应不是析氢的阴极去极化反应,而是发生氧的阴极去极化。铜的腐蚀受氧的离子化过程影响。
② 铜合金在海水中,表面直接形成氧化亚铜保护薄膜,上面还沉积有其他腐蚀产物,如氯化铜、氢氧化铜、碳酸铜或碱式碳酸铜和含钙物质。
③ 铜离子有毒性,能阻止海生动、植物的聚集,阻止海生物腐蚀。铜在海水中的腐蚀大多属于均匀腐蚀。但由于海洋环境的复杂性,加上舰船和海洋工程中使用的部件经受的工况条件变化很大,铜合金有可能发生各种局部腐蚀,它们的危害远远大于均匀腐蚀。
03 铜合金的局部腐蚀类型
(1)电偶腐蚀
当两种电偶序相差较大的金属相连接并暴露于海洋环境时,通常会产生严重的电偶腐蚀,在相连的电偶中,一种金属是阳极,另一种是阴极,阳极将被腐蚀。腐蚀程度取决于两种金属的电位差,电位差越大,则腐蚀越严重,阳极和阴极的面积比也是关键,小阳极、大阴极则腐蚀速度快。典型的电偶腐蚀例子是远洋船的青铜螺旋桨和钢船体的裸露面之间产生的腐蚀,青铜的电位约是-0.31V(SCE),船钢板约为-0.61V,如果船板钢有一块裸露,那么就是阳极,而螺旋桨是阴极。
要控制电偶腐蚀则需恪守几项原则。首先,应考虑在两种金属之间加上绝缘层,如不能,则应在电偶的阴极上覆上不导电的保护层,再者,可减小阴极面积。
(2)缝隙腐蚀
金属部件安装在一起时难免有缝隙,在海水中这种缝隙对于能产生氧化膜的金属而言就有可能产生缝隙腐蚀,在缝隙中,氧不足,钝化膜逐渐退化,缝隙外氧充足,钝化膜完整,于是缝隙外是腐蚀的阴极,缝隙内是腐蚀的阳极。由于设计和安装的特点(如密封垫、垫圈、铆钉等),金属部件的缝隙难免会产生,当海洋生物附着或涂层局部脱落时缝隙也会产生。有些铜合金的缝隙腐蚀则有不一样的特点,即在缝隙外的铜离子被流动海水去除了,而缝隙内的铜离子浓度更高,形成了铜的浓度差电池,缝隙内是阴极,缝隙外是阳极。
控制缝隙腐蚀的措施是,改进设计,尽量减少缝隙,实施阴极保护减轻腐蚀,减小缝隙外部的金属面积,减小阴极面积来控制缝隙内部的腐蚀。
(3)点蚀
铜合金制品表面往往存在多种缺陷,如化学成分不均匀,金相组织不均匀,夹杂物,表面附着物或沉积物,这些不均匀性会破坏铜合金表面的氧化膜,形成点蚀源,这些点蚀源与表面膜完整的地方形成了电偶腐蚀,点蚀源是阳极,不断被腐蚀,最后可使部件穿孔泄漏。
防止点蚀的方法是减少表面缺陷,经常清洗构件,对一些管件,早期预成膜的办法是十分有效的,根据部件特点还可采用缓蚀剂或电化学保护。
(4)脱成分腐蚀
脱成分腐蚀是某些铜合金的特殊腐蚀形式,如最常见的是锌含量大于15%的黄铜,尤其是α+β双相黄铜,还有含有γ-2相的铝青铜的脱铝腐蚀和铜镍合金的脱镍腐蚀。
黄铜是铜和锌的固溶体,锌是固溶体中的阳极成分,锌被优先地选择性溶解,铜合金变成了脱锌的海绵铜,从而引起材料破坏。铝青铜中含有γ-2相时,当γ-2相沿晶界形成网状时,脱铝腐蚀最严重。
抑制黄铜脱锌腐蚀的方法是选用含Zn量较低的黄铜,也可根据情况加入抑制脱锌的合金元素如砷、硼、锡、磷或锑。抑制铝青铜脱铝的方法是通过热处理消除γ-2相的沿晶界析出,或添加l%~2%的铁或4.5%以上的镍。运用搅拌摩擦处理也可大大改善组织结构,抑制铝青铜的脱铝腐蚀。
(5)应力腐蚀
应力腐蚀断裂(或开裂)(stress corrosion cracking, SCC)是指受拉伸应力作用的金属材料在某些特定的介质中,由于腐蚀介质与应力的协同作用而发生的断裂(或开裂)现象。在这里,开裂和断裂分别对应于cracking和fracture,前者突出开始出现裂纹,而后者包括从裂到断,似可通用,因问题而异,不必强调一致。一般认为发生应力腐蚀断裂需具备三个基本条件,即敏感材料、特定介质和拉伸应力。这说明应力腐蚀是一种较为复杂的现象:当应力不存在时,敏感材料在该特定介质环境中腐蚀甚微;施加应力后,经过一段时间,该敏感材料会在腐蚀并不严重而应力又不够大的情况下发生断裂。一般认为纯金属不会发生应力腐蚀断裂,而每种合金的应力腐蚀断裂只是对某些特定的介质敏感。随着合金使用环境不断拓展,现已发现能引起各种合金发生应力腐蚀的环境非常广泛。
铜合金在外界拉应力或自身残余应力作用下,遇到与之匹配的腐蚀介质 (含NH4+的溶液或蒸气、汞盐溶液),就有可能产生应力腐蚀,这是一种能产生贯穿性裂纹的破坏,危害性极大。四大类铜合金中,紫铜和白铜在海洋环境中抗应力腐蚀性能最佳,黄铜对应力腐蚀最敏感,青铜次之。黄铜的“季裂”是典型的应力腐蚀现象,潮湿、含氧的氨气、铵盐、汞盐等都能使黄铜发生应力腐蚀,SO2有加速作用。黄铜发生应力腐蚀的机理是,首先铜的表面产生保护膜,然后保护膜在应力下开裂,促进了沿晶的阳极性溶解,溶解处再形成保护膜,再开裂,再溶解,而沿晶界的阳极性溶解是由于黄铜中的锌被选择性溶解造成的。当黄铜在介质中不生成膜时,有可能产生穿晶应力腐蚀。一般来说α黄铜的SCC是沿晶的,β黄铜是穿晶的,而α+β黄铜可以是穿过β相又沿着。相晶界扩展的。
降低黄铜应力腐蚀敏感性的措施除了降低残余应力、改善环境介质以外,降低锌的含量,或加入适量的抑制应力腐蚀的微量元素Si也是有效的。
部分青铜也有相当的应力腐蚀敏感性,如锰青铜、铝青铜、铍青铜、螺旋桨用复合青铜在污染海水中也有应力腐蚀。但青铜的应力腐蚀抗力高于黄铜。
(6)腐蚀疲劳
腐蚀疲劳是指材料或构件在交变应力与腐蚀环境的共同作用下产生的脆性断裂。交变应力与腐蚀环境共同作用所造成的破坏要比单纯的交变应力造成的破坏(即疲劳)或单纯的腐蚀作用造成的破坏严重得多。船舶推进器、涡轮及涡轮叶片、泵轴和泵杆、海洋平台等常出现这种破坏。腐蚀疲劳与应力腐蚀有共同之处,都涉及应力和腐蚀介质的共同作用,但也有很大区别:腐蚀疲劳是在交变应力作用下发生,而应力腐蚀通常在拉应力作用下发生;纯金属也会发生腐蚀疲劳,且金属构件发生腐蚀疲劳不需要材料一介质环境的特殊组合,只要存在腐蚀介质,在交变应力作用下就会发生。
正常情况下,设计人员总会赋予动态的铜合金关键部件较高的安全系数,发生腐蚀疲劳断裂的可能性小,但一旦发生,后果很严重。为避免腐蚀疲劳应注意如下方面:
① 合理选材,一般来说抗点蚀能力高的材料,抗腐蚀疲劳的性能也较高,应力 腐蚀敏感的材料,腐蚀疲劳的性能也较差。还要注意,材料强度高的,腐蚀疲劳强度未必高。
② 精心设计,尽量降低部件的应力水平,避免部件出现尖锐缺口,减少应力集中 。
③ 如有可能,可以采用消除内应力的热处理,而对工件采用喷丸处理,使工件表层有残余压应力则多半是有益的。
④ 针对性地采用涂层、缓蚀剂或电化学保护也可产生很好的效果。
(7)空泡腐蚀
与流体相对高速运动的铜合金部件其周围的流体压力分布是不均匀的,如舰船推进器,泵阀的进出口或换热器管的进出口,在低压区金属表面局部区域,形成流体的空泡,随后这些空泡在下游溃灭,产生高压的冲击波或微射流,压力可达400atm(latm=101325Pa,下同),甚至更高,损坏金属表面的保护膜,加速了腐蚀的进行,这种空泡形成和溃灭的多次循环所引起的金属的累积损伤叫空泡腐蚀。
空泡腐蚀是冲击波或微射流力学因素和腐蚀介质腐蚀的协同作用造成的。力学作用可破坏铜合金的保护膜,促进腐蚀,而进一步的腐蚀又产生蚀坑或使蚀坑变深、变粗糙,这又反过来促进空泡的形核。表5列举了一些常用铜合金的相对空泡腐蚀速度,表6则列出了一些螺旋桨铜材空泡腐蚀试验结果。
表5 一些常用铜合金的相对空泡腐蚀速度
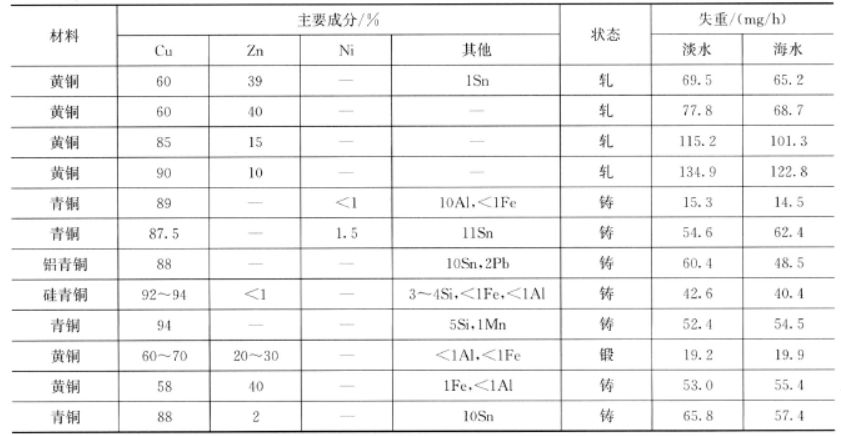
表6 螺旋桨铜材空泡腐蚀试验结果
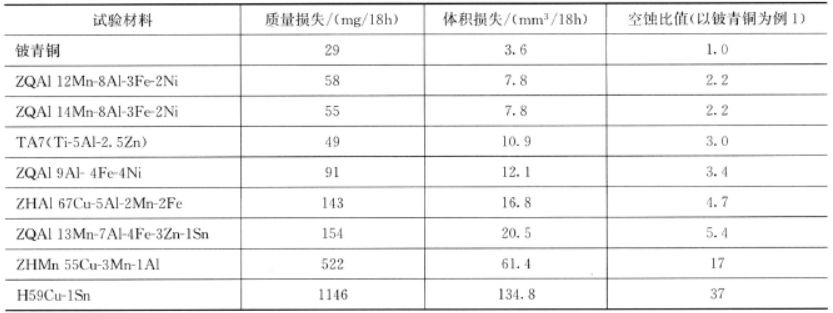
抑制空泡腐蚀的主要措施有:
① 改进设计,从水力学角度降低流体的压力差,减少空泡的形成。
② 提高部件表面光洁度,降低空泡形成概率。
③ 采用弹性高的橡胶或塑料涂层,吸收冲击波。
④ 采用阴极保护,在工件部位产生氢气泡以缓冲空泡的冲击波。
⑤ 合理选用材料。
(8)冲刷腐蚀
金属表面与腐蚀性流体之间由于高速相对运动而引起的金属损坏现象,称冲刷腐蚀。腐蚀性流体可以是单相流,也可能是含有气相和固相的多相流。无论是单相或多相流引起的冲刷腐蚀,一般来说,相对速度越高,流体中悬浮的固体颗粒越多、越硬,质量越大,则冲刷腐蚀越严重。表7给出了几种铜合金在几种流速下的单相海水中的腐蚀速率。
表7 海水流动速度对腐蚀速率的影响
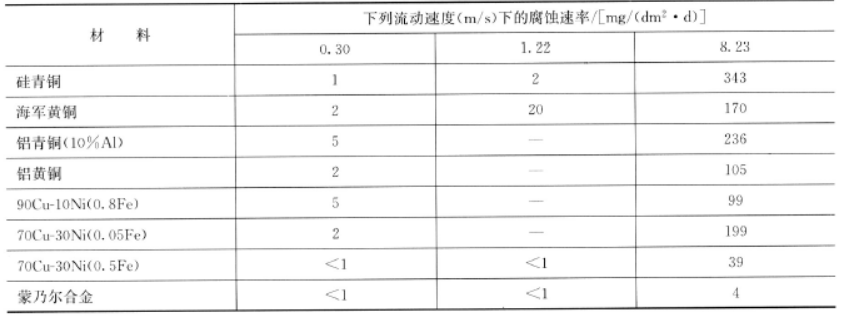
表中数据表明,流速高时腐蚀速率高,也表明了不同的铜合金耐冲刷腐蚀的能力差别很大。一般情况下,每一种铜合金都有一个耐冲刷腐蚀的极限流速,被称为临界流速,超过临界流速,材料的破坏速度会突然显著加快。当然这个临界流速的值除与材料相关,还与腐蚀流体的各种参数有关。
文献中显示给出在简单的流体中,即洁净海水中,几种铜合金的临界流速。紫铜的临界流速为0.9m/s,含砷海军黄铜为1.8m/s,含砷铝黄铜为3m/s,90Cu-10Ni(1.5Fe)为3.6m/s,70Cu-30Ni(0.7Fe)为4.5m/s,在冷凝器中典型海水流速为2.4m/s,那么只有后三种铜合金可用于制备海水冷凝器。
如果上述洁净海水流体温度升高,pH变化,海水被污染,含有泥沙等,那么临界流速还会降低。
冲刷腐蚀的机理说到底是金属表面在腐蚀介质中具有一层保护膜,而冲刷作用使这层膜变薄或被破坏,从而使裸露金属进一步腐蚀,如果冲刷的力学作用进一步加大,大大超过临界流速时,那么金属还会被机械性地直接剥离。鉴于这种机理,减小冲刷腐蚀的措施有:
① 选择耐冲刷腐蚀的材料,如表7所示,在铜合金中8m/s高速冲刷时,耐冲刷 腐蚀性能优劣排序为70Cu-30Ni(0.5Fe),90Cu-10Ni(0.8Fe),铝黄铜,海军黄铜,70Cu-30Ni(0.05Fe),铝青铜,硅青铜。
② 改变腐蚀介质,添加缓蚀剂,过滤掉悬浮固体颗粒,降低操作温度,都可降低冲刷腐蚀。
③ 改进设计,降低流速,减小湍流,加厚易损部位或使这些部位易于更换修补。
④ 采用适当的牺牲阳极或电化学阴极保护,也是有效的措施。
免责声明:本网站所转载的文字、图片与视频资料版权归原创作者所有,如果涉及侵权,请第一时间联系本网删除。
相关文章
无相关信息
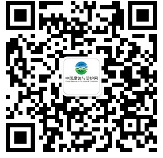
官方微信
《中国腐蚀与防护网电子期刊》征订启事
- 投稿联系:编辑部
- 电话:010-62316606-806
- 邮箱:fsfhzy666@163.com
- 中国腐蚀与防护网官方QQ群:140808414
点击排行
PPT新闻
“海洋金属”——钛合金在舰船的
点击数:7130
腐蚀与“海上丝绸之路”
点击数:5741