《Life Cycle Costs of Industrial Protective Coatings》
《工业防护涂料的生命周期成本》
本文来源:
澳大利亚一家镀锌厂的技术手册。该公司把这本技术手册做成了公开的网页格式,既可以在线浏览,也可以下载。虽然本文没有明说,但是字里行间都是一句潜台词:镀锌是钢结构最好的防腐方案;
防腐相关文章:
【钢构知识】浅析钢结构的防腐问题
【行业知识】钢桥梁的长效防腐涂装
【钢构知识】钢结构涂料与涂装技术
【钢构知识】钢结构防腐处理
【行业知识】用钢结构做住宅,腐蚀真的是问题吗?
【钢构知识】不锈钢为何也生锈?不锈钢知识详解
【钢构知识】钢桥梁的长效防腐涂装
【行业知识】耐候钢应用是桥梁建设必然趋势(专访中国工程院院士柯伟)
【钢构知识】英国耐候钢钢桥技术之一
【钢构知识】英国耐候钢钢桥技术之二
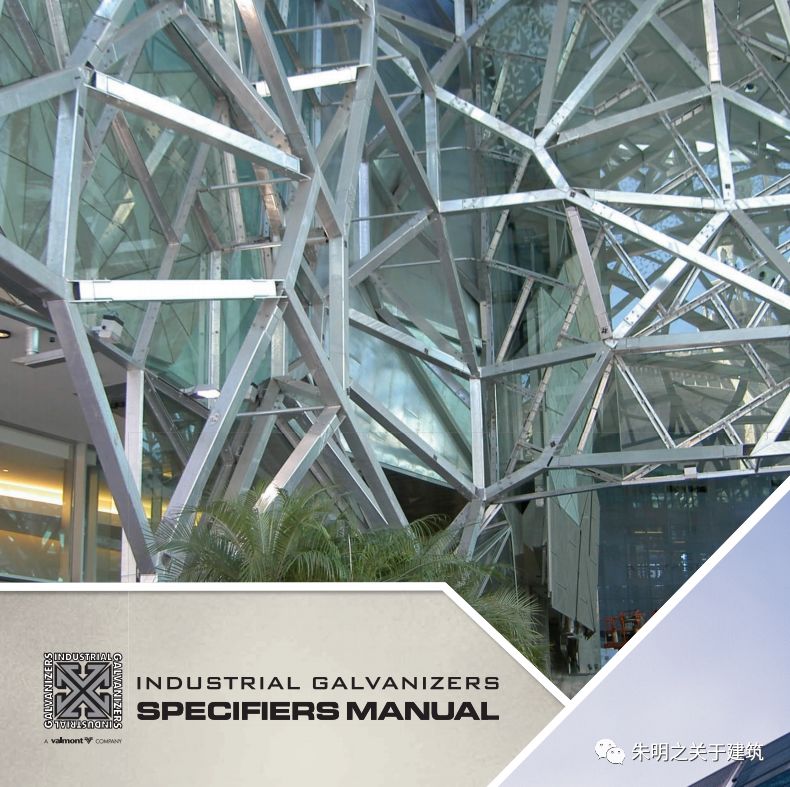
Industrial Galvanizers Corporation (IGC) operates nine galvanizing plants around Australia, ranging in size from large structural galvanizing facilities to specialised small plants designed to process small parts.
工业镀锌公司(IGC)在澳大利亚运营着九个镀锌厂,规模从大型结构镀锌设备到专门加工小零件的小型工厂。
The Australian Galvanizing Division has galvanized in excess of 2.5 million tonnes of steel products in Australia since its first plant was commissioned in 1965 and is recognized for its ability to handle complex and difficult projects, as well as routine contracts.
自1965年第一家工厂投产以来,澳大利亚镀锌部门已经在澳大利亚镀锌了超过250万吨的钢铁产品,并因其处理复杂和困难项目以及日常合同的能力而得到认可。
This experience has been collated in the Specifiers Design Manual, to assist those involved in the design of steel products and projects to better understanding the galvanizing process and allow the most durable and cost-effective solutions to be delivered to these products and projects.
这一经验已被整理在《设计手册》中,以帮助那些参与钢材产品和项目设计的人员更好地理解镀锌过程,并为这些产品和项目提供最持久和最具成本效益的解决方案。
本文是节选的该技术手册第22章。
The concept of life cycle costing is not a new one. Standards Australian produced its first AS/ NZS Standard in 1999 ; AS/NZS 4536 - Life cycle costing – An application guide.
In any life-cycle costing assessment, the initial cost of the coating is an important component in doing any long-term cost analysis, as is the need to determine the likely maintenance free life of the coating and the future costs of maintenance.
生命周期成本计算并不是一个新概念。澳大利亚标准协会于1999年首次制定了AS/ NZS标准;AS/NZS 4536 -生命周期成本计算应用指南。在任何生命周期成本评估中,涂层的初始成本是进行任何长期成本分析的一个重要组成部分,同样需要确定涂层可能的免维护寿命和未来的维护成本。
A bit of History
Protective coating costs on most projects are a relatively small component of the total project cost; typically less than 2%. On a major steel project containing, say, 1000 tonnes of structural steel, the cost of a basic protective coating system may be in the order of $500/tonne, a high performance coating system may be $1000/tonne, and a special super-durable specification may cost $1500/tonne.
在大多数工程项目中,保护层成本占工程总成本的比例相对较小;一般少于2%。对于一个包含1000吨结构钢的大型钢铁项目,一个基本的防护涂层系统的成本可能是500美元/吨,一个高性能的涂层系统可能是1000美元/吨,一个特殊的超级耐用规格可能是1500美元/吨。
This equates to an additional project cost of $500,000 - $1,500,000. If a project accountant applied a net present value analysis to this in the 1980’s, when interest rates exceeded 15% and company taxation was well over 40%, the option of using the cheaper coating and expensing accelerated maintenance costs would seem a sound financial decision.
这等于一个额外项目费用$50万至$ 150万。如果一个项目会计在20世纪80年代将净现值分析应用于此,当时利率超过15%,公司税收远远超过40%,选择使用更便宜的涂层和花费加速维护成本似乎是一个明智的财务决策。
However, in the 21st Century, company tax is only 30% and interest rates are lower, so the Tax Office no longer subsidises maintenance costs to the same degree. In addition, expensed maintenance costs hit the balance sheet at a level that exceeds any interest benefits from the original saving.
然而,在21世纪,公司税只有30%,利率更低,所以税务局不再对维修费用给予同样程度的补贴。此外,支出的维护成本在资产负债表上所占的比例超过了原始储蓄的利息收益。
Also, the labour costs of the 1980’s did not include the on-costs of superannuation, higher workers compensation and other statutory obligations for employers. Nor were the WH&S and environmental obligations anything like they are today.
此外,80年代的劳动力成本不包括退休金、更高的工人补偿和雇主的其他法定义务。WH&S和环境责任也与今天不同。
It is thus very difficult to foretell the distant future for the purposes of life-cycle costing for protective coatings, and conditions in 2035 will have changed as much in that 25-year cycle as they did between 1950, 1975 and 2000.
因此,要预测防护涂层的寿命周期成本,预测遥远的未来是非常困难的。在这25年的周期内,2035年的条件变化将与1950年、1975年和2000年之间的情况一样大。
The other reality faced by asset owners, particularly of infrastructure assets, is that their service life is often far longer that originally anticipated. Many power distribution and transport structures are now well over 50 years old and are subject to numerous maintenance cycles to maintain their functionality.
资产所有者(尤其是基础设施资产)面临的另一个现实是,他们的使用寿命往往比最初预期的长得多。许多电力分配和运输结构现在已经有50多年的历史了,需要进行大量的维护来维护它们的功能。
The other issue with maintenance coatings is that they add very little value to a business. They make no contribution to efficiency or productivity.
维护涂层的另一个问题是,它们对企业的价值贡献很小。他们对效率和生产率没有贡献。
For this reason, the selection of an appropriate protective coating system for steel, be it paint, galvanizing, or a combination of both should be based on the performance of the coating over time rather than its initial cost.
因此,选择合适的钢铁防护涂层系统,无论是油漆、电镀还是两者的结合,都应该基于涂层的长期性能,而不是它的初始成本。
Factors in the Cost of a Coating
涂层的成本因素
Australian Standards such as AS/NZS 2312:2002 – Guide to the protection of iron and steel against atmospheric corrosion contains comprehensive guidelines related to coating selection versus environmental condition to provide an estimated service life for a range of coating systems.
澳大利亚标准,如/NZS 2312:2002—《钢铁抗大气腐蚀保护指南》,包含了有关涂层选择与环境条件的综合指南,为各种涂层系统提供了估计的使用寿命。
Material Selection
材料选择
The choice between materials of construction will usually be a `steel versus concrete decision’, with a proportion of projects being a composite of both.
建筑材料的选择通常是“钢与混凝土的选择”,有一部分项目是两者的组合。
The decision may be based on familiarity of a designer of working with one material or another, the form of the structure, its location and most importantly, its installed cost.
这个决定可能是基于设计师对一种或另一种材料的熟悉程度,结构的形式,它的位置,最重要的是,它的安装成本。
While the protective coating costs are a relatively small component of the total projects cost, they can be a significant proportion of the structural steel cost. In addition, steel simply cannot be used (with a few exceptions) without protective coatings and these coatings will have a defined life that will determine future maintenance costs.
虽然保护层成本在工程总成本中所占的比例相对较小,但在结构钢成本中所占的比例很大。此外,没有防护涂层,钢就不能使用(少数例外),这些涂层的使用寿命将决定未来的维护成本。
While steel and fabrication costs are volatile, benchmark costs obtained in mid-2012 indicate that the cost components are approximately as follows for standard medium structural steel:
虽然钢材和制造成本波动较大,但2012年年中获得的基准成本表明,标准中结构钢的成本组成大致如下:
Medium structural steel cost: $1200/t
中等结构钢材成本:$1200/t
Fabrication cost: $3000 - $5000/t
制造成本:3000 - 5000美元/吨
Coating Costs for new Steelwork
钢结构的涂料成本
The cost of coating new steelwork is made up of a number of factors. These are:
The type of steel – size, shape, section.钢的型号-尺寸、形状、截面。
The quantity of steel钢材数量
The location of the project with respect to the coating provider, the fabricator and the site.关于涂料供应商、制造商和现场的项目位置。
The regional cost of labour地区劳动力成本
The material cost (paint components/zinc/ chemicals)材料成本(油漆成分/锌/化学品)
The cost of surface preparation (abrasive blasting/chemical/mechanical)表面处理成本(喷砂/化学/机械)
The cost of application – number of coats, plant capability, processing time应用成本-涂层数量,工厂能力,处理时间
Logistic costs – inspection, loading, transport, erection物流成本-检验,装载,运输,安装
Post erection costs – remediation of handling damage, on-site completion安装后费用-处理损坏的补救,现场完成。
For applied coatings (paint, metallising) the surface area of the steelwork and the complexity of the fabrication will be the most significant factors influencing the cost. Logically, thin steel sections with high surface area per tonne will absorb more labour and materials than heavy structural sections.
对于应用涂层(油漆、金属化),钢结构的表面积和制造的复杂性将是影响成本的最重要因素。从逻辑上讲,每吨高表面积的薄型钢将比重型钢吸收更多的劳动力和材料。
For example, a 3 mm thick steel section has a surface area per tonne of over 80 m2, while a 10 mm section has a surface area of 25 m2 per tonne.
例如,3毫米厚的钢截面每吨的表面积超过80平方米,而10毫米厚的钢截面每吨的表面积为25平方米。
For process-applied coatings (hot dip and continuous galvanizing, powder coating), material costs and fixed costs are important, making the profitability of these processes very volume sensitive.
对于工艺应用的涂层(热浸镀和连续镀锌、粉末涂料),材料成本和固定成本非常重要,这使得这些工艺的利润对产量非常敏感。
Typical Material Costs
典型的材料成本
Many of the materials incorporated in coatings are traded as commodities with supply and demand affecting prices above and beyond normal inflationary variations. The following indicative prices are for generic materials used in coating in mid-2008, in commercial quantities
涂料中包含的许多材料都是作为商品进行交易的,其供求关系对价格的影响超出了正常的通胀波动范围。以下指示性价格是2008年年中用于涂料的一般材料的商业价格
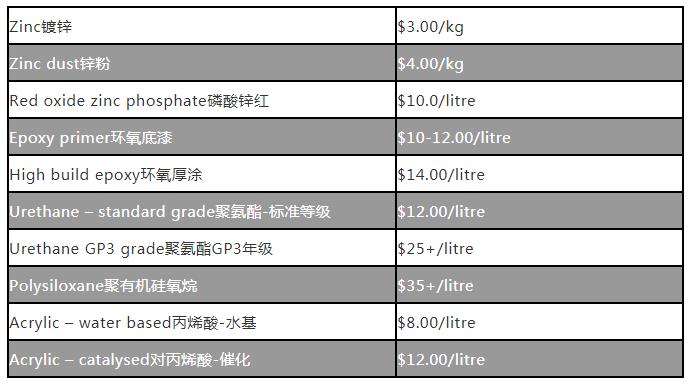
Paint Coatings
The true material cost of paint coatings is determined by how much of what is in the can ends up on the steel surface. This is determined by the volume solids in the paint, the applied thickness of the coating and the coating efficiency (over-spray losses).
油漆涂料的实际材料成本是由罐内的材料在钢表面的含量决定的。这是由涂料中固体颗粒的体积、涂层的厚度和涂层效率(过喷损失)决定的。
Low volume solids will result in higher losses due to solvent evaporation. Simple solid structures (beams, tanks) will experience higher coating efficiencies that open structures (pipe work and trusses)
由于溶剂蒸发,体积小的固体颗粒会造成较大的损失。简单的实体结构(梁、罐)将获得比开口结构(管道和桁架)更高的涂层效率。
One litre of paint, applied to a wet film thickness of 100 microns will theoretically cover 10 m2 of surface. In practice, the same paint applied to a dry film thickness of 100 microns, to medium structural steel by airless spray will cover approximately 5 m2.
一公升的油漆,适用于100微米的湿膜厚度,理论上将覆盖10平方米的表面。在实践中,同样的涂料应用于100微米的干膜厚度,通过无空气喷涂到中等结构钢材上将覆盖约5平方米。
All paint suppliers have product safety data sheets for each of their paints. These documents list technical specifications for the paint, including volume solids, recommendations for wet and dry film thickness requirements and theoretical coverage.
所有油漆供应商都有各自油漆的产品安全数据表。这些文件列出了涂料的技术规格,包括固体体积、干膜和湿膜厚度要求的建议和理论覆盖范围。
In addition to the paint cost, most solvent-based spray applied coatings require the addition of thinners, (typically around 30% by volume) which becomes a component of the paint material cost.
除了涂料成本外,大多数基于溶剂型的喷涂涂料还需要添加稀释剂(通常体积约为30%),这成为涂料材料成本的一个组成部分。
An important point to note is that the paint cost is a relatively small proportion of the applied system cost. Based on a typical practical coverage rate of $5.00/m2, the cost differential between a basic industrial epoxy or urethane and a high performance urethane or polysiloxane is in the order of $3.00-$4.00/m2.
需要注意的重要一点是,涂料成本占应用系统成本的比例相对较小。根据典型的实际覆盖率为$5.00/m2,基本工业环氧树脂或聚氨酯与高性能聚氨酯或聚硅氧烷之间的成本差异约为$3.00-$4.00/m2。
The most significant single cost in paint coatings is surface preparation. Abrasive blasting is almost mandatory to ensure acceptable performance for industrial paint systems.
涂料中最重要的单项成本是表面处理。喷砂几乎是强制性的,以确保工业涂料系统的可接受的性能。
Fabricated steelwork is usually abrasive blasted with chilled iron shot, in a chamber that allows recovery and recycling of the blasting media. Abrasive blasting standards are defined in Australian Standard AS 1627.4. Class 2 ? Blast is most commonly specified for industrial coating, with Class 3 (the highest level) being a requirement for specialised coatings such as zinc metal spray.
预制钢结构通常是在一个允许爆破介质的回收和循环利用的腔体中,用冷硬铁喷丸进行磨料喷砂。喷砂标准在澳大利亚标准中定义为1627.4。指定类2?爆炸是最常见的工业涂料,与3班(最高级别)被要求专业涂料如锌金属喷雾。
Abrasive blasting costs vary regionally, but generally fall in the $15.00 - $20.00/m2 range. Large automated blasting facilities using wheelabrador equipment to process columns, beams and plates can significantly reduce this cost.
喷砂成本因地区而异,但一般在$15.00 - $20.00/m2范围内。大型自动化爆破设施使用轮对爆破设备来处理柱、梁和板可以大大降低成本。
Where galvanized coatings are to be painted, Class 1 or whip blasting is generally specified. This involves using less aggressive media such as garnet or illmentite, at typical cost ranging from $10.00 - $15.00/m2, depending on the complexity of the fabrication.
如果要喷涂镀锌涂层,一般规定为1级或起爆。这包括使用不太激进的媒体,如石榴石或illmentite,典型的成本从$10.00到$15.00/m2不等,这取决于制造的复杂性。
Chemical preparation (pickling, phosphating) is rarely used as a method of preparing fabricated steel for painting, and is confined to process applied coatings such as powder coating and galvanizing.
化学制剂(酸洗、磷化)很少被用作制备涂漆用钢的方法,而且仅限于粉末涂料和镀锌等工艺应用涂料。
Powder coating costs are usually charges on a `window area’ basis rather than surface area, as the area the item takes up on the powder coating line is the main factor in its cost of processing. For standard grades of polyester powder, powder coating costs are typically $15.00 - $20.00/m2, although large quantities of uniform manufactured product that can be loaded to high line efficiencies can be powder coated at lower cost.
粉末涂料的成本通常是按“窗口面积”而不是按表面积计算的,因为产品在粉末涂料生产线上所占的面积是其加工成本的主要因素。对于标准等级的聚酯粉末,粉末涂料的成本通常为$15.00 - $20.00/m2,尽管大量的均匀生产的产品可以装载到高生产线效率,也可以以较低的成本粉末涂料。
With all costs included (labour, overheads, margins) indicative industrial painting costs for commonly specified systems are:
包括所有成本(人工、间接费用、毛利率)后,一般指定系统的指示性工业油漆成本为:
Basic wire brush/Class1 blast and ROZP prime ---> $12.00/m2基本钢丝刷/Class1 blast和ROZP prime -> $12.00/m2
Class 2 ? blast + inorganic zinc primer ---> $25.00/m2类2?爆炸+无机富锌底漆- - - > 25.00美元/平方米
Class 2 ? blast + inorganic zinc primer + epoxy topcoat ---> $35.00/m2类2?爆炸+无机富锌底漆+环氧面漆- - - > 35.00美元/平方米
Class 2 ? blast + inorganic zinc primer + urethane ---> $45.00/m2类2?爆炸+无机富锌底漆+聚氨酯- - - > 45.00美元/平方米
NOTE: These are indicative average prices only and will vary regionally and depending on the design of the items being painted.
注:这些只是指示性平均价格,并将根据地区和项目的设计而有所不同。
Galvanized Coatings
The parameters governing the cost of galvanized coatings are quite different to those determining paint costs.
决定镀锌板成本的参数与决定涂料成本的参数有很大的不同。
Continuously applied galvanized coatings applied to sheet, wire and tube are applied in facilities with high capital and operating cost, with large volumes of steel being able to be processed very efficiently.
镀锌板、线材、管材连续涂敷镀锌板是一种资金和运营成本都很高的设备,大量的钢材可以被高效地加工。
For this reason, the galvanized coating cost component of these products is relatively small and driven by the material (zinc) cost. In addition, these technologies apply relatively thin zinc coatings – usually less than 30 microns per side for a material cost of about $0.75/m2 of surface.
因此,这些产品的镀锌板成本组成相对较小,受材料(锌)成本的驱动。此外,这些技术适用于相对较薄的锌涂层——通常每面不到30微米,材料成本约为0.75美元/平方米。
Hot dip galvanized coatings applied to fabricated steelwork are priced on the basis of the tonnage that can be processed through the galvanizing bath. Surface area is thus not as significant in galvanizing costs. Thin sections that can be loaded into galvanizing jigs at high loading density will attract a relatively low galvanizing cost, while 3-D structural fabrications containing heavy universal sections may be more costly to process.
用于装配式钢结构的热浸镀锌涂层的价格是根据镀锌槽处理的吨位来定的。因此,表面面积是不显着镀锌成本。能够以高负载密度加载到镀锌夹具中的薄片将会吸引相对较低的镀锌成本,而包含重型通用截面的三维结构制造的加工成本可能会更高。
Hot dip galvanized coatings are almost always costed on a $./tonne basis. Typical galvanizing costs per tonne will range from $650/tonne for heavy, simple elements such as columns and beams in large project quantities, to $1500/tonne for light fabrications. Items requiring double-end dipping will usually attract a premium cost and small one-off fabrications (boat trailers, wrought iron, anchors etc) for non-account customers will be charged around $2000-$2500/tonne.
热浸镀锌涂料的价格几乎都是a美元。/吨。典型的镀锌成本从每吨650美元到1500美元不等,如大型工程中使用的柱和梁等重而简单的构件。需要双头浸洗的物品通常会收取额外费用,而非帐户客户的小型一次加工(拖架、熟铁、锚等),每公吨收费约为$2000至$2500。
The cost per square metre for hot dip galvanizing reduces quite significantly as sections become thinner. The following examples illustrate this:
热镀锌的成本每平方米相当显着减少了截面变薄。下面的例子说明了这一点:
Medium structural steel – 10 mm average thickness
中等结构钢- 10毫米平均厚度
Galvanizing cost: $700/tonne
镀锌成本:700美元/吨
Surface area per tonne: 25 m2/tonne
Cost/m2: $28/m2
每吨表面积:25平方米/吨
成本/ m2: 28美元/平方米
Light fabrications - 3 mm average section thickness
轻加工- 3毫米平均截面厚度
Galvanizing cost $1500/tonne
Surface area per tonne: 85 m2/tonne
Cost/m2: $18.00/m2
镀锌成本1500美元/吨
每吨表面积:85平方米/吨
成本/ m2: 18.00美元/平方米
A fringe benefit of hot dip galvanizing, because it is an immersion process, is that all internal surfaces of hollow sections are coated uniformly. This may be an advantage or disadvantage, as the external surface area of a hollow section is only half that of an open section of the same section thickness.
热镀锌的一个附带好处是,由于它是一种浸镀工艺,所有空心型材的内表面都得到了均匀的涂层。这可能是一个优点,也可能是一个缺点,因为空心截面的外表面面积只有相同截面厚度的开口截面的一半。
Another fringe benefit of hot dip galvanizing compared to both paint coatings and continuously galvanized coatings is that the applied coating thickness almost always in excess of Australian Standard requirements.
与油漆涂层和连续镀锌涂层相比,热镀锌的另一个附加好处是涂层厚度几乎总是超过澳大利亚标准要求。
This is a bonus for the customer, as additional zinc pick-up on steelwork cannot be accurately predicted by the galvanizer, as it is influenced by the surface condition, section thickness and chemistry of the steel. It can add $50-$100/tonne to the galvanizer’s material costs, with the added bonus for the customer of the extra zinc adding proportionately to the service life of the coating.
这对客户来说是一个额外的好处,因为镀锌器不能准确地预测钢结构上额外的锌含量,因为它受到钢的表面条件、截面厚度和化学成分的影响。它可以增加50- 100美元/吨的镀锌材料成本,与客户额外的锌按比例添加到涂层的使用寿命额外的奖金。
The Realties of Future Maintenance
未来维护的现实
Where maintenance coating is required on an infrastructure or industrial project, the real cost experienced in 2008 would not have been even considered 25 year ago.
如果一个基础设施或工业项目需要维护涂层,那么在25年前,2008年的实际成本甚至不会被考虑在内。
The major cost factors impacting on maintenance costs include:
影响维修成本的主要成本因素包括:
Access
Containment
OH&S Management
Productivity
It is worth looking at each of these factors in more detail.
值得更详细地研究这些因素。
1. Access
It is now mandatory in most jurisdictions in Australia to use scaffolding systems when working at heights. Ladders and trestles are no longer acceptable for commercial coating contractors.
在澳大利亚的大多数司法管辖区,在高处工作时必须使用脚手架系统。梯子和支架不再被商业涂料承包商所接受。
The cost of erecting, hiring and dismantling scaffolding is a major component of any maintenance coating operation. Since the introduction of more stringent safety requirements on residential building sites, few houses are now built that do not require scaffolding to be erected during their construction. While this is not directly connected to the life-cycle costing of industrial coatings, it is worth noting that the value of the residential scaffolding market in Australia now exceeds $250 million annually.
安装、租用和拆除脚手架的费用是任何维护涂层操作的主要组成部分。由于对住宅建筑工地实施了更严格的安全规定,现在很少有房屋在建造过程中不需要搭建脚手架。虽然这与工业涂料的生命周期成本没有直接联系,但值得注意的是,澳大利亚住宅脚手架市场的价值现在每年超过2.5亿美元。
On industrial projects, much larger scaffolding systems may be required to provide the needed access for maintenance.
在工业项目中,可能需要更大的脚手架系统来提供所需的维护访问。
In assessing the likely maintenance costs, access factors can be applied to life cycle costing models to more accurately estimate costs on a specific structure.
在评估可能的维护成本时,可以将访问因子应用于生命周期成本计算模型,从而更准确地估计特定结构的成本。
It is possible to classify structures for assessing access issues. The following is an example:
可以对评估访问问题的结构进行分类。以下是一个例子:
Level 1 – Simple structure to 15 m. Maintenance able to continue while structure is operational. Easy access for scaffolding or lifts.一级-简单结构,高度15米。结构运行时可以继续进行维护。方便脚手架或升降机。
Level 2 – Simple structure 15-30 m. Greater scaffolding requirements. Maintenance able to be done while structure operational.二级-简单结构,高15-30米。更大的脚手架要求。能够在结构运行时进行维护。
Level 3 – Simple structure over 30 m. Specialised external access required. Operating requirements of other plant and equipment must be considered.三级-简单结构,高度30米以上。需要特殊的外部访问。必须考虑其他工厂和设备的操作要求。
Level 4 – Complex structure to 15 m. Internal and external access required. Operating requirements of other plant and equipment must be considered.四级-复杂结构,高度15米。需要内部和外部访问。必须考虑其他工厂和设备的操作要求。
Level 5 – Complex structure 15 – 30 m. Internal and external access required. Staging at each level may be required. Operating requirements of other plant and equipment must be considered.5级-复杂结构,15 - 30米。需要内部和外部访问。可能需要在每个级别上进行分段。必须考虑其他工厂和设备的操作要求。
Level 6 – Complex structure over 30 m. Staged internal and specialised external access required. Operating requirements of other plant and equipment must be considered.6级- 30米以上的复杂结构。需要阶段性的内部和特殊的外部访问。必须考虑其他工厂和设备的操作要求。
2. Containment
Like access, containment costs will vary with the complexity of the requirements for containment. As with access, models can be developed to classify containment levels and factor in the costs of containment for a specific containment requirement.
与访问一样,控制成本也会随着控制需求的复杂性而变化。与访问一样,可以开发模型来对容器级别进行分类,并考虑特定容器需求的容器成本。
An example of classification of containment factors is as follows:
包容因子分类的一个例子如下:
None – No recovery of residues or paint.没有-没有回收残留物或油漆。
Level 4 (Minimum) – For abrasive blast cleaning only – air penetrable walls, flexible framing, open entryways and natural air flow.4级(最低)-仅用于喷砂清理-可穿透空气的墙壁、柔性框架、敞开的入口和自然气流。
Level 3 (Moderate) – For abrasive blast cleaning – air penetrable walls, rigid or flexible framing, partially sealed entryways and joints, exhaust air filtration.3级(中等)-用于磨料喷砂清理-空气可穿透的墙壁,刚性或柔性框架,部分密封的入口和接头,排气过滤。
Level 2 (High) – For abrasive blast cleaning – air impenetrable walls rigid or flexible framing, fully sealed joints, airlock entryways, negative air flows and exhaust air filtration.2级(高)-用于磨料喷砂清理-空气不透壁,刚性或柔性框架,全密封接头,气闸入口,负气流和排气过滤。
A good example of high-level containment is the maintenance painting program undertaken on under-road steelwork on the Sydney Harbour Bridge, which also incorporates very complex staging and access systems.
高水平遏制的一个很好的例子是对悉尼港大桥上的地下钢结构进行的维护喷漆项目,该项目也包含非常复杂的阶段和入口系统。
Where lead based paints are concerned, additional environmental management systems may be required to monitor local soil and water system during the remediation activities.
在涉及含铅油漆时,可能需要额外的环境管理系统来监测当地土壤和水系统的修复活动。
3. WH&S Management职业健康
Worker safety is now the first priority in any business and where heights are involved, stringent requirements for personal safety equipment are mandatory. Industrial manslaughter laws apply in many Australian States, and while managers should not need the threat of such legislation to care for the welfare of their workers, it is an indication that the most stringent risk assessments must be applied to any hazardous activity.
工人安全现在是任何行业的第一要务,在涉及高度的地方,对个人安全设备的严格要求是强制性的。工业过失杀人法适用于澳大利亚的许多州,虽然经理们不应该需要这种立法的威胁来关心他们的工人的福利,但这表明,最严格的风险评估必须适用于任何危险的活动。
Certified safety equipment is mandatory when working at height, and approved safety harnessing and attachment systems have to be provided by contractors. Other Workcover regulations related to working in enclosed spaces places further onus on employers to ensure that no cost-cutting shortcuts are taken in the provision of maintenance coating services.
在高空作业时,必须配备合格的安全设备,承包商必须提供经批准的安全控制和连接系统。与在封闭空间内工作有关的其他工作覆盖规定进一步规定了雇主的责任,以确保在提供维护涂层服务时不采取任何削减成本的捷径。
4. Productivity生产力
Each of the above factors will have an impact on productivity. With new steelwork, labour costs represent about 75-80% of the coating cost. For on-site maintenance, the labour cost component is far greater and for this reason material costs (paint costs) are less significant and more expensive surface tolerant paints will have little impact on the overall costs of a maintenance project, and represent better value given the expectation of higher levels of performance.
以上每一个因素都会对生产力产生影响。新钢铁厂的劳动力成本约占涂层成本的75-80%。现场维护,劳动力成本组件是更大,为此材料成本(油漆成本)宽容更重要和更昂贵的表面油漆对维修项目的总成本,并代表更好价值的期望更高水平的性能。
Surface preparation is the most labour-intensive part of the process. Surfaces may be contaminated with soluble salts so may require water washing/ blasting prior to mechanical removal of the rusted surface or failed paint coating.
表面处理是整个过程中劳动强度最大的部分。表面可能被可溶性盐污染,因此在机械去除生锈表面或失效的油漆涂层之前,可能需要水洗/爆破。
As a guide, the cost per square metre for maintenance coating a rusted steel structure may be 5-10 times the cost of applying an equivalent coating to new steelwork.
作为指导,每平方米生锈钢结构的维护涂层成本可能是新钢结构的5-10倍。
Summary
总结
Regardless of the protective coating used, there is a strong case, particularly in the present environment of low interest rates and decreasing company taxes, to use the longest life coatings available commensurate with the design life of the asset.
This may mean more stringent inspection with applied coatings, the use of QA certified applicators or the insistence in a coating performance guarantee from the supplier to better manage the risk and avoid the inevitable and more costly than expected future maintenance costs.
无论使用何种防护涂层,都有充分的理由使用与资产的设计寿命相称的最长寿命涂层,尤其是在当前低利率和降低公司税收的环境下。
这可能意味着对应用的涂层进行更严格的检查,使用QA认证的涂敷器,或坚持要求供应商提供涂层性能保证,以更好地管理风险,避免不可避免的、成本高于预期的未来维护成本。
免责声明:本网站所转载的文字、图片与视频资料版权归原创作者所有,如果涉及侵权,请第一时间联系本网删除。
相关文章
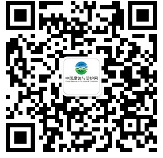
官方微信
《中国腐蚀与防护网电子期刊》征订启事
- 投稿联系:编辑部
- 电话:010-62316606-806
- 邮箱:fsfhzy666@163.com
- 中国腐蚀与防护网官方QQ群:140808414
点击排行
PPT新闻
“海洋金属”——钛合金在舰船的
点击数:7130
腐蚀与“海上丝绸之路”
点击数:5741