特种合金钢表面处理类别
特种合金钢表面处理过程中,在外界输入能量、合金元素或材料,与产品表面交互作用,使得产品表层材料的物理化学特性发生剧烈改变。表面处理的微观实质就是材料表层发生可控的物理化学变化,具有不同于基体的优异性能。
不同的能量输入方式,使得材料表面产生物理化学效应,形成不同的表层结构。根据特种合金钢表面处理后产生的效应,可以将表面处理分为以下3类:
① 机械作用:特种合金钢表面受到单纯机械作用而导致表面改性,如喷丸 、辊压、孔挤压等表面形变强化,见图1(a)。处理后表面具有抗疲劳性能。
② 物理作用:特种合金钢表面由于能量作用而导致表面产生物理变化或者形成新的涂层,通过物理作用进行表面处理的工艺较多,如表面相变强化、热喷涂、表面离子注入、化学物理沉积和激光熔覆等表面处理,见图1(b),(c),(e)。提高表面抗疲劳性能、耐磨、耐蚀性能。
③ 物理化学作用:特种合金钢表面在能量 作 用 下 元素渗入扩散、反应而导致表面改性,如渗碳、渗氮、碳氮共渗及其他金属元素渗入等表面处理工艺,如图1(f)。
图1 表面处理技术
表面化学热处理技术
利用某种元素的固态扩散渗入,来改变特种合金表面层的化学成分,以实现表面强化的方法称为表面化学热处理强化,也称为扩散热处理。包括渗碳及碳氮共渗、渗氮及氮碳共渗、渗硫及硫氮碳共渗、渗铬、渗铝及铬铝硅共渗、石墨化渗层渗硼、渗金属等,种类繁多、特点各异。渗入元素或溶入基体金属形成固溶体,或与金属元素结合形成化合物。渗入元素既能改变表面层的化学成分,又可以获得不同的相结构。其中渗碳、渗氮等离子化学热处理方式可以改变了特种合金钢零件或构件表面状态,提高耐磨、耐蚀、耐热性能而应用较为广泛。
一 离子化学热处理
离子处理真空炉体
离子化学热处理设备的真空炉体主要有两大类。一是水冷双层炉壁,可分为钟罩式、立式、井式多种规格,内置1~2层隔热屏(低碳钢、不锈钢或铝合金制造),功率l0~500kW、有效加热区直径300~1700mm、高400~4000mm这种炉型结构简单、造价低、组合方便,但能耗较大、温度均匀性较差、无法控制工件处理后的冷却速度,该炉型主要用于离子渗氮处理;另一类炉型是带油淬装置的双室离子渗碳炉,它的炉温均匀性好、操作方便、工艺调节范围宽,但结构复杂、造价高、装炉量有限(≤300kg),很少用于离子渗氮加工。近年来,随着真空热处理设备制造技术的发展和产品需求的提高,设备制造厂家又相继开发了带对流系统的热壁真空炉体和带高压气淬装置的离子渗碳炉。前者是在冷壁炉的基础上增加炭毡或硅酸铝纤维保温层、热辐射加热装置及循环风扇,提高了加热区的温度均匀性和工件混装能力,降低能耗,工艺调节范围大大提高,工件的升温及冷却速度均能较好控制,特别适于离子氮碳共渗等处理后需快冷的工件;后者多为单室结构,离子渗碳结束后通过高压气体淬火(国内生产的设备最高气冷压强已达6bar, lbar=0.1MPa),消除了油淬对炉膛带来的污染,工件光洁、形变量小,设备结构和操作过程得以简化。
离子化学热处理电源
实际应用较多的仍然是直流电源,电压0~1000V连续可调,灭弧系统主要采用限流电阻加上LC振荡灭弧,少数采用电子开关,但由于直流电源的固有特性,明显存在一些不足:灭弧较慢,易烧蚀工件;由于空心阴极效应,引起狭缝和小孔过热;无功损耗较大;工艺参数不易调节;对电网干扰较大。脉冲电源的开发和应用促进离子化学热处理技术发展。目前,脉冲电源的最大峰值电流已达300A,输出电压0~1500V,脉冲频率10~20kHz,导通比0.15~0.8连续可调,灭弧时间<10μs。
离子化学热处理技术今后的发展趋势之一为复合处理的扩大应用。离子化 学热处理渗层质量高、综合力学性能好,但形成表面强化层厚度有限、硬度梯度大、性能单一,不能满足各种零部件的服役条件要求,只有采用复合处理技术才能解决这一矛盾。因此,复合处理技术得到了高度重视,如离子渗氮;气相沉积(PVD, PCVD),离子渗氮;表面淬火(感应淬火、激光表面淬火等),低温镀铁;离子轰击强化以及各种多元共渗和复合渗等。
二 特殊合金钢渗碳工艺
渗碳的作用和过程
特种合金钢渗碳工艺具有非常重要的实用价值。轴承、齿轮、模具、工具等特种合金钢产品表层承受磨损、疲劳、机械负载及化学腐蚀等负荷作用,通过渗入碳等元素达到高的表面硬度、高的耐磨性和疲劳强度及耐蚀性。不必通过合金化或其他复杂工艺手段对特种合金钢进行处理。不仅降低成本,而且能够保持心部淬火后的强韧性,使产品能承受冲击载荷。符合节能、降耗,可持续发展的方向。渗碳一般选择优质低碳或中碳合金钢,它具有冷加工性能、耐冲击、渗碳后耐磨、接触疲劳寿命高等优点。
渗碳处理对特种合金钢选用具有一定要求。适合渗碳钢的适宜含碳量在0.10%~0.25%,可以保证心部在淬火及低温回火后仍具有足够的韧性和塑性。
对于重载荷的渗碳零件,含碳量可达到0.25%~0.3%,进一步提高心部强度。中高碳钢不适宜进行渗碳处理;中高碳合金钢临界温度低于渗碳温度,加热到渗碳温度势必晶粒粗大,强度降低而影响使用寿命,不适合渗碳。渗碳用钢要求较高冶金质量,高纯净度、高均匀性、细晶粒化。保证产品各向同性并防止应力集中而导致裂纹。选用低碳钢进行表面渗碳处理,渗碳浓度及其梯度和渗碳深度可以调节,渗碳时间与渗碳深度关系如图2,一般渗层深度在0.4mm以上。表面渗碳需在900℃以上保持较长时间,钢中均添加铬、镍、钼、锰等元素防止渗碳过程中晶粒长大,渗碳后进行淬火加低温回火处理,获得高硬度、高耐磨的表面及强韧的心部。
图2 渗碳时间和渗碳深度的关系
渗碳工艺主要类型可分为气体渗碳、固体渗碳、液体渗碳、离子渗碳。均包括以下3个过程。
① 分解:渗碳介质的分解产生活性碳原子。
② 吸附:活性碳原子被钢件表面吸收后即溶到表层奥氏体中,使奥氏体中含碳量增加。
③ 扩散:表面含碳量增加便与心部含碳量出现浓度差,表面的碳遂向内部扩散。碳在钢中的扩散速度主要取决于温度,同时与工件中被渗元素内外浓度差和钢中合金元素含量有关
渗碳过程的关键问题
问题 |
预防工艺措施 |
碳浓度梯度问题;渗碳零件要求其碳浓度梯度小,保证渗碳零件沿截面的组织变化平稳。碳浓度梯度在硬度上就为硬度梯度。对重要的钢制零件,除了规定渗碳层的浓度、渗碳层深度外,往往还要规定渗碳工艺。碳浓度梯度与渗碳温度、时间及渗碳介质直接相关。不同的渗碳方法所采用的渗碳介质是不同的。一般采用真空渗碳、离子渗碳时,碳浓度梯度小,气体渗碳则可通过调节甲醇和丙酮(或煤油)的滴量来控制碳浓度梯度;固体渗碳则无法控制。 |
批量生产的齿轮应尽量避免采用固体渗碳,采用固体渗碳时应严格执行操作工艺,装炉量适当,催渗剂、木炭要混合均匀。渗碳箱放在炉内温度均匀的中间位置,渗碳过程中间适当调换渗碳箱位置。气体渗碳时,要注意炉内气氛充分循环、炉温要均匀,清除齿面油污,装炉量不宜过多,渗碳炉密封性能要好,漏气的炉膛及时更换,定期检修渗碳炉。淬火后渗碳齿轮表面硬度偏低将会导致齿轮耐磨性和抗疲劳性能降低,对齿面抗摩擦、磨损性能具有不利影响。 |
表面硬度偏低问题;导致硬度偏低主要原因为表面脱碳。通过金相检查发现脱碳层是源于渗碳后正火或淬火过程中缺乏防护措施而产生的表面脱碳现象;冷却速度太低,在显微镜下观察,表层组织不是马氏体组织,而是索氏体组织,金相观察时针状马氏体耐腐蚀明显,而索氏体较暗,易于腐蚀,显微硬度计检测明显硬度差别大;齿轮渗碳温度、淬火温度偏高,造成淬火后表面残余奥氏体量过多;齿轮材料淬透性差及淬火冷却介质冷却能力不足;淬火后回火温度过高,保温时间过长。 |
对已造成齿轮表面含碳量低的齿轮采取适当增碳处理;选择淬透性合适的材料和适当冷却能力的冷却介质,淬火冷却;预先采取措施,减少淬火后的残余奥氏体量,对含有过多残余奥氏体的渗碳齿轮,进行一次650~670℃ , 3h以上的高温回火,析出部分合金碳化物,从而降低重新加热淬火时的奥氏体稳定性,促使奥氏体向马氏体转变;齿轮渗碳冷却或重新加热淬火时应在保护气氛下进行,对已经发生氧化现象的齿轮应去除氧化皮,进行表层渗碳后再进行淬火;齿轮表层硬度偏低应重新淬火,用合适温度进行回火。齿轮心部硬度偏低,齿轮材料的屈服点降低,易产生心部塑性变形,使齿轮表面硬化层抗剥落性能及齿根弯曲疲劳性能降低。 |
钢的心部硬度偏低问题;特种合金钢,诸如心部硬度偏低产生原因:齿轮材料淬透性差,齿轮材质差,钢材内部带状组织严重;齿轮渗碳后,直接淬火前预冷温度过低或渗碳后重新加热淬火时淬火温度偏低;冷却速度不够,金相组织观察,不是低碳马氏体组织,而是索氏体组织;心部有大量未熔铁素体存在,是由于加热温度偏低或加热时间不足造成。 |
选用冷却性能好的冷却介质淬火,保证心部获取低碳马氏体组织;选择适当的淬火温度和加热时间,保证心部获得均匀的奥氏体,从而淬火后获取马氏体组织;选用淬透性好、材质好的特种合金钢作为渗碳齿轮材料。 |
等离子渗碳工艺
等离子渗碳炉在运行期间炉体加热区十分清洁。处理工件后无炭黑产生,其原因有如下两点:①由于渗碳期间强渗周期较短;②因为碳氢化合物分子的激发和离化仅在阴极压降区域发生,即直接在工件附近进行。碳流量仅仅取决于带电的等离子数值时(电流密度),用于气体渗碳对炉体条件的传统要求不能应用于等离子渗碳之中。对于未生产的冷态等离子设备,须待首批工件达到工艺温度后方可进行渗碳处理,这样所得到的结果才会与随后其他所有炉次相同。此外,在等离子渗碳中,用增加渗碳循环次数来逐渐改变渗碳作用,避免在气体渗碳中常发生的炉体烧坏现象。等离子渗碳处理无内氧化,因而在低合金钢表面区域附近避免了低硬度的屈氏体产生。其结果是改善了工件在等离子渗碳后的力学性能,如耐磨性及抗疲劳强度等。
若等离子渗碳过程可以被调整或校正的话,可抑制碳化物在平滑表面或 (正常矩形)尖角处的生成。在短的强力循环周期内适当地控制碳流量则是一个决定性的因素。在低压渗碳过程中,尖角处的碳化物形成是一个主要问题。应用等离子渗碳由于采用了诸如低电流密度特殊监测及很短的强循环周期等技术,可以消除上述缺陷。16MnCr钢制构件经930℃等离子渗碳后层深1mm, 870℃加热油中淬火冷却,160℃回火1h,只在最外端的尖角处显现出少量碳化物。表面碳浓度是使用特殊显微探头来测量的,测得结果为靠近边棱尖端的碳浓度为0. 9%C,而平面处为0.75%C。另一个特殊情况是在气体渗碳中氢的活动能力较强,这只能靠用辅助处理的办法予以减少。而应用等离子渗碳,即使是在渗碳后期,氢的含量也十分缺乏,因此也就避免了所处理工件氢脆的产生。这是因为在等离子渗碳处理强循环期间,扩散进入钢中的任何形式的氢,在随后扩散阶段无等离子产生及真空的条件下,均从钢中逸出。氢量至少减到即使有氢化物形成元素存在的情况下,也不会形成氢化物。
等离子渗碳技术优点:不需对炉体进行调节;设备利用率高;生成无内氧化的有利碳层结构;高合金钢渗碳、淬火无软点产生;渗层均匀性好;表面碳势可进行粗略及精确控制;具有极好的再现性;较短的渗碳周期;可用于较高的渗碳温度;用简单的屏蔽方法进行局部渗碳;无环境污染;组成生产线的能力强。
三 特殊合金钢渗氮工艺
渗氮工艺的作用和类别
渗氮是一种以氮原子渗入钢件表面 ,形成一层以氮化物为主的渗层的化学热处理方法。渗氮有三个基本过程:活性氮原子的产生、表面的吸收和氮原子的扩散。渗氮不仅可以提高工件表面的硬度、耐磨性以及耐疲劳性,而且还可以提高工件在腐蚀介质中工作的耐蚀性。
常用的渗氮方法有:固体渗氮 、 液 体 渗氮、气体渗氮、脉冲气体渗氮 (气体周期改变)、直流等离子体渗氮(又称辉光离子氮化)、脉冲等离子体渗氮(电源周期供电)等。从渗入的机理来看,主要有两大类:第一类基于浓度梯度:如液体渗氮、气体渗氮等,这类渗氮通常采用电炉将采用的含氮介质加热,通过含氮介质传递热能,使被处理零件达到处理温度,以浓度梯度作为氮元素渗入的驱动力。第二类基于电场的作用:如直流等离子体渗氮、脉冲等离子体渗氮等。在一定的真空条件下,通过微量的含氮气体,利用辉光放电产生电子和离子,离子直接轰击零件传递热能,使被处理零件达到处理温度,通过离子、活性原子与表面的复杂作用将氮元素渗入金属表面。氮元素与零件的表面相互作用不尽相同,但在渗入金属内部后渗层深度的增长仍然符合扩散定律。
调质处理后零件基体为回火索氏体组织,渗氮层深度可提高20%以上,硬度也有所提高,进而提高基体强度和韧性及疲劳性能。为了减少零件渗氮后变形,在半精加工和精加工中增加一次消除加工应力退火处理。温度一般取550~600℃,保温3~5h,变形量可控制在0.1%以下。
常规渗氮工艺
① 一段渗氮法、二段渗氮法、三段渗氮法
一段渗氮法又称等温渗氮。作为最初的渗氮工艺是在同一渗氮温度下,长时间保温的一种渗氮方法。渗氮温度一般保持在480~530℃之间。工艺操作简单,工件变形小;缺点是由于较长的工艺时间,渗层浅,易产生脆性层。为了缩短渗氮的时间,且保持较高的硬度,二段渗氮方法得到发展。二段渗氮工艺首先在500℃左右渗氮一段时间,使工件表面形成高度弥散的氮化物颗粒,保证一定的硬度。后升高到550℃左右继续渗氮,加速氮原子扩散,以缩短渗氮时间,变形较一段渗氮大。三段渗氮是在二段氮化的基础上发展起来的,进一步缩短氮化时间。
② 催渗渗氮
为了缩短渗氮的时间,在渗氮介质中添加一种或几种起催渗作用的物质,即催渗渗氮:如加氮渗氮、加钛渗氮等。加氮渗氮是在氨气中加入氮气,氮气占混合气体的30%~90%。不仅可以显着缩短渗氮时间,而且还改善渗层组织,降低脆性。加钛渗氮是在工件上镀一层钛后再渗氮,也可提高渗速。近年来发展起一种新的渗氮方法——电解气相催渗渗氮。即将一定成分的电解气体进入渗氮炉中起到催渗作用,一般工艺时间可以缩短1/2~2/3。
③ 预氧化催渗气体渗氮
气体渗氮在工业上应用较为广泛,但渗氮周期长,成本高。研究表明,工件经短时氧化后,表面会形成氧化薄膜,具有较强的催渗作用,能使N原子的渗入显着加快。如在580℃下经预氧化,渗氮两次循环处理工艺(预氧10min,渗氮3h)可使采用渗氮温度580℃,时间为6h时所形成的0. 29mm渗氮层厚度提高到0. 55mm,使氮化层的硬度梯度分布显着获得改善。
④ 等离子渗氮及复合化
离子渗氮是将工件置于辉光放电装置的真空容器中,以工件为阴极,容器壁或另设金属板作为阳极,充一稀薄的含氮气体,在直流高压的电场的作用下使气体原子电离成离子撞击工件阴极表面上,并向内部扩散形成渗氮层的过程。离子氮化不仅能实现可控氮化、可局部硬化、使用纯氢、氮气为气源无环境污染等优点,且离子渗氮不生成脆性相,渗层致密,与气体渗氮相比具有更高的耐磨性、耐蚀性和抗疲劳性能。离子渗氮要比气体渗氮渗速快、热效率高、设备维修费用低。近年来,离子渗氮技术发展迅速,离子渗氮与其他热处理工艺相结合,进行工件表面改性,提高工件的硬化质量。如离子氮化与PVD离子镀覆TiN工艺复合,可得到结合力良好的复合镀层。处理后工件表面硬度极高,而且硬度梯度平缓,具有一定厚度硬度较高的扩散层支撑,有利抗磨性能提高,复合镀层有良好的回火稳定性,具有一定的耐蚀性。应用于冷作模具和热作模具等。除此之外,还有感应淬火+离子渗氮复合处理;激光+离子氮化复合处理;表层硬化质量的提高同时,其耐磨性、耐蚀性也随之提高。此类复合处理作为新的表面处理技术广泛地应用于工模具中。
注:文章、作品、图片版权归作者享有,如有作者来源标记有误或涉及侵权,请原创作者联系小编删除。
免责声明:本网站所转载的文字、图片与视频资料版权归原创作者所有,如果涉及侵权,请第一时间联系本网删除。
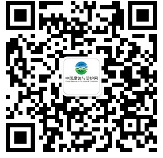
官方微信
《中国腐蚀与防护网电子期刊》征订启事
- 投稿联系:编辑部
- 电话:010-62313558-806
- 邮箱:fsfhzy666@163.com
- 中国腐蚀与防护网官方QQ群:140808414