夹片螺母
夹片螺母又称为簧片螺母或快速螺母(SpeedNut),通常安装在钣金件或塑料件上,与螺栓相配合,来实现两个零件之间的连接。
分类
夹片螺母通常有两种:第一种为一体式,螺纹部分由基材板冲压出来,再通过后续攻丝而成,如图1a)所示;第二种类型是组合式,由夹片(Clip)和独立的螺母(Nut)两部分组成,如图1b)所示。
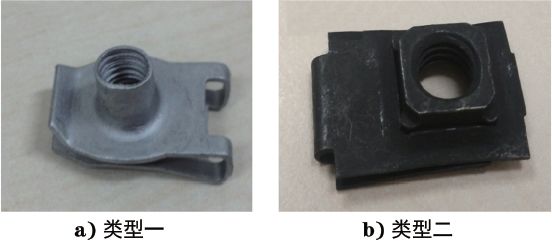
图1 夹片螺母宏观形貌
夹片螺母连接的两个钣金件上均有预留孔。安装时,首先将夹片螺母插入到其中一个钣金件上,然后通过螺栓穿过两个零件的预留孔,拧入到夹片螺母中来实现固定。夹片螺母的锁紧工艺原理如图2所示。
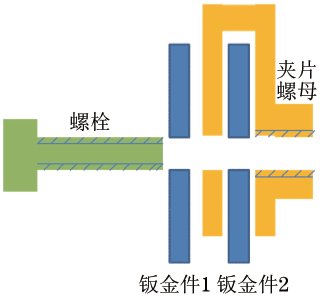
图2 夹片螺母锁紧工艺示意图
基于夹片螺母的这种连接方式,避免了传统的焊接等连接方式,可以节约成本,同时大大地提升了装配效率,在车身上有着广泛的应用。
在此类零件的实际应用中,通常有以下原因可能会导致失效:所用材料强度等级不够;热处理工艺不合格,导致零件表面产生裂纹等系列缺陷;长期载荷导致疲劳断裂;表面处理工艺不当导致氢脆;等等。
某汽车总装线上在装配螺栓的过程中发生了多起失效案例,该装配线上使用的夹片螺母属于第二种类型。安装螺栓时,发现夹片被撕裂的现象,如图3所示。笔者从材料和现场装配两方面分析了夹片螺母失效的原因,同时提出了相应的改进建议并进行验证。
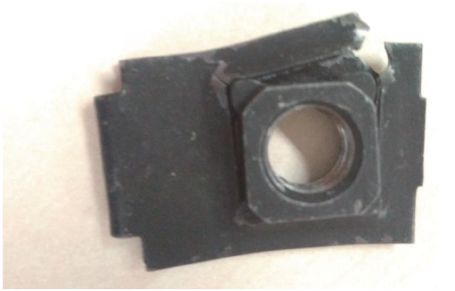
图3 失效夹片螺母宏观形貌
理化检验
1 材料性能分析
采用经标准块校正的Welson万能硬度计测试夹片的硬度。采用Zeiss显微镜进行金相分析。表1和图4分别是夹片的硬度和显微组织分析结果,可见失效夹片的硬度和显微组织均满足相关技术要求,且都与正常零件的接近。因此,可以排除材料和热处理工艺方面的原因。

图4 夹片显微组织形貌
表1 夹片硬度
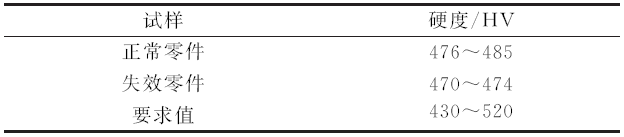
2 断口扫描电镜分析
利用Zeiss扫描电子显微镜(SEM)对失效夹片进行断口分析。
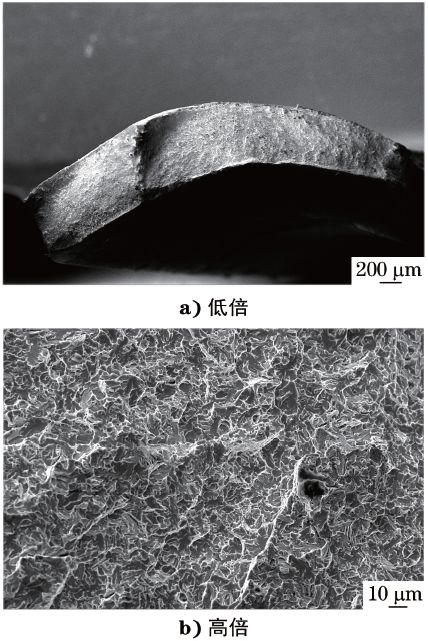
图5 失效夹片断口SEM形貌
图5显示,失效夹片断口处无明显缺陷,断口形貌为韧窝,呈现明显的韧性断裂特征。同时,在裂纹源处未发现杂质等缺陷。此外,该零件为新件,排除后续使用的因素造成断裂的可能性。
综合上述分析,推断夹片是因为受到了过大的外力(即过载,外力超过了零件可承受载荷的极限)而导致的一次性断裂,即一次性过载断裂。
综合分析
1 同批次未安装零件的解剖分析
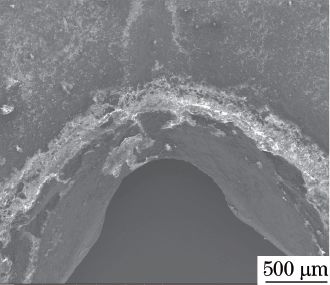
图6 同批次未安装夹片直角处形貌
为了对比分析,拆卸了同批次未安装的零件。 观察发现,同批次未发生断裂的夹片直角处没有原始裂纹,见图6。由此可以判定,夹片是在总装线上装配螺栓的过程中发生断裂的。
2 工艺过程检查
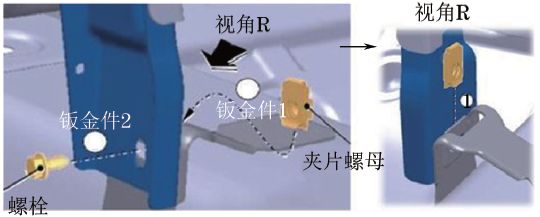
图7 夹片螺母及相关零件装配图
现场装配图如图7所示。首先将夹片插在图7中的钣金件1当中;然后螺栓穿过钣金件2和钣金件1,拧入到夹片螺母中实现连接。
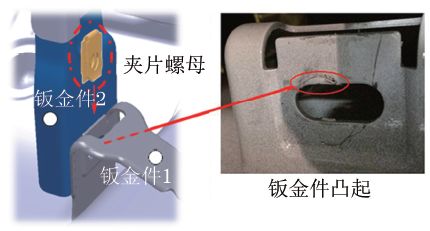
图8 现场装配图
由图8可以看到,钣金件1有明显的拉伤痕迹。说明在装配过程中受到了较大的外力。
综上,对当时的安装情况进行了还原:螺栓与螺母未能对准,工人在安装螺栓的时候也未进行调整,而是继续暴力安装螺栓,使夹片受到了较大的剪切力,直至最终夹片被过载撕裂。
导致这一情况的原因可能有两点:
夹片螺母以及钣金件1和钣金件2尺寸存在问题;夹片螺母与钣金件之间的相对位置出现偏差,从而导致安装螺栓时未对准。
钣金件1和钣金件2以及夹片螺母的尺寸测量结果显示,尺寸均合格,且与正常批次零件的测量结果相近。因此可以推断,夹片螺母与钣金件1的相对位置与正常值之间出现偏差,导致安装螺栓时螺栓未能对准夹片螺母,从而应力过大引起断裂。
结论及建议
夹片螺母是因为受到了较大的外力而发生过载撕裂。夹片螺母被撕裂主要是由于夹片螺母以及另外两个钣金件之间的位置匹配出现了问题,从而导致装配时应力过大引起夹片螺母发生了过载撕裂失效。
作为短期措施,调整了夹片螺母的位置,将其向车头方向移动了一段距离,之后的装配过程未再发生类似失效情况。
更多关于材料方面、材料腐蚀控制、材料科普等方面的国内外最新动态,我们网站会不断更新。希望大家一直关注中国腐蚀与防护网http://www.ecorr.org
责任编辑:韩鑫
《中国腐蚀与防护网电子期刊》征订启事
投稿联系:编辑部
电话:010-62313558-806
邮箱:fsfhzy666@163.com
中国腐蚀与防护网官方 QQ群:140808414
免责声明:本网站所转载的文字、图片与视频资料版权归原创作者所有,如果涉及侵权,请第一时间联系本网删除。
相关文章
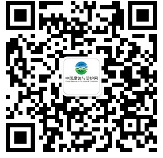
官方微信
《中国腐蚀与防护网电子期刊》征订启事
- 投稿联系:编辑部
- 电话:010-62313558-806
- 邮箱:fsfhzy666@163.com
- 中国腐蚀与防护网官方QQ群:140808414
点击排行
PPT新闻
“海洋金属”——钛合金在舰船的
点击数:5768
腐蚀与“海上丝绸之路”
点击数:4763