精密超精密加工技术的发展历史
近年来,美国开始实施了“微米和纳米级技术”国家关键技术计划,国防部成立了特别委员会,统一协调研究工作。美国目前至少有30多家公司研制和生产各类超精密加工机床,如国家劳伦斯利佛摩尔实验室(LLNL)、摩尔(Moore)公司等在国际超精密加工技术领域久负盛名。同时利用这些超精密加工设备进行了陶瓷、硬质合金、玻璃和塑料等材料不同形状和种类零件的超精密加工,应用于航空、航天、半导体、能源、医疗器械等行业。日本现有20多家超精密加工机床研制公司,重点开发民用产品所需的超精密加工设备,并成批生产了多品种商品化的超精密加工机床,日本在相机、电视、复印机、投影仪等民用光学行业的快速发展与超精密加工技术有着直接的关系。英国从60年代起开始研究超精密加工技术,现已成立了国家纳米技术战略委员会,正在执行国家纳米技术研究计划,德国和瑞士也以生产精密加工设备闻名于世。1992年后,欧洲实施了一系列的联合研究与发展计划,加强和推动了精密超精密加工技术的发展。
国内真正系统地提出超精密加工技术的概念是从20世纪80年代~90年代初,由于航空、航天等军工行业的发展对零部件的加工精度和表面质量都提出了更高的要求,这些军工行业投入了资金支持行业内的研究所和高校开始进行超精密加工技术基础研究。由于当时超精密加工技术属于军用技术,无论从设备还是工艺等方面,国外都实施了技术封锁,所以国内超精密加工技术的开展基本都是从超精密加工设备的研究开始。由于组成超精密加工设备的基础是超精密元部件,包括空气静压主轴及导轨、液体静压主轴及导轨等,所以各家单位也正是以超精密基础元部件及超精密切削加工用的天然金刚石刀具等为突破口,并很快就取得了一些进展。哈尔滨工业大学、北京航空精密机械研究所等单位陆续研制了超精密主轴及导轨等元部件,并进行了天然金刚石超精密切削刀具刃磨机理及工艺研究,同时陆续搭建了一些结构功能简单的超精密车床、超精密镗床等超精密加工设备,开始进行超精密切削工艺实验。
非球面曲面超精密加工设备的研制成功是国内超精密加工技术发展的里程碑,非球面光学零件由于具有独特的光学特性在航空、航天、兵器以及民用光学等行业开始得到应用,从而简化了产品结构并提高了产品的性能。当时加工设备只有美国、日本及西欧等少数国家能够生产,国内引进受到严格限制而且价格昂贵,国家从“九五”开始投入了人力物力支持研发超精密加工设备。到“九五”末期,北京航空精密机械研究所、哈尔滨工业大学、北京兴华机械厂、国防科技大学等单位陆续研制成功代表当时超精密加工最高技术水平的非球面超精密切削加工设备,彻底打破了国外的技术封锁。之后其他各类超精密加工设备,如超精密磨削设备、小计算机数控磨头抛光设备、磁流变抛光设备、离子束抛光设备、大口径非球面超精密加工设备(如图1所示)、自由曲面多轴超精密加工设备、压印模辊超精密加工设备等也陆续研制成功,缩小了超精密加工技术国内外的差距。同时由于有了超精密加工设备的支撑,在超精密加工工艺方面也有了很大进展,如ELID超精密镜面磨削工艺、磁流变抛光工艺、大径光学透镜及反射镜超精密研抛及测量工艺、自由曲面的超精密加工及测量工艺、光学薄膜模辊超精密加工工艺,超精密加工技术的应用领域也从军工行业转向了民用行业。
超精密加工技术的发展随着时代的进步其加工精度也不断提高,目前已经进入到纳米制造阶段。纳米级制造技术是目前超精密加工技术的巅峰,其研究需要具有雄厚的技术基础和物质基础条件,美国、日本及欧洲一些国家以及我国都在进行一些研究项目,包括聚焦电子束曝光、原子力显微镜纳米加工技术等,这些加工工艺可以实现分子或原子级的移动,从而可以在硅、砷化镓等电子材料以及石英、陶瓷、金属、非金属材料上加工出纳米级的线条和图形,最终形成所需的纳米级结构,为微电子和微机电系统的发展提供技术支持。
精密超精密加工技术的作用
20世纪80年代以前,太赫兹(THz)波段(介于微波与红外之间)的研究结果和数据非常少,主要是受到有效太赫兹产生源和灵敏探测器的限制。随着80年代一系列新技术、新材料、新工艺的发展,使得太赫兹技术得以迅速发展。近年来由于太赫兹的独特性能将给宽带通信、雷达、电子对抗、电磁武器、天文学、医学成像、无损检测、安全检查等领域带来了深远的影响,太赫兹基础及应用基础技术已经逐渐成为研究热点。
太赫兹技术在航空领域的重要应用是太赫兹雷达可用于隐身飞行器探测,其中束控元件是太赫兹探测系统的重要功能部件,其透镜主要采用硅基远红外透射材料,反射元件面形有抛物面、椭球面、离轴非球面以及赋形曲面等,采用铝等金属基材料。我国正研的主反射元件尺寸已有φ300mm、φ800mm、φ1000mm等,面形精度要求已要求达微米级,表面质量为镜面,并且要求零件精度质量具有良好的稳定性。我国中期发展的太赫兹系统拟采用φ4~5m的主镜,远期主镜直径将达30m或更大,太赫兹系统束控主反射元件面形也将采用主动控制的拼接式平面、离轴非球面等形状。基于上述要求,需要大型单点金刚石超精密车削设备、复杂曲面超精密加工工艺技术、大型复杂曲面的高精度三坐标测量技术等支撑。
2 精密超精密加工技术是现代高新技术产业发展的基础
国家目前非常重视交通、能源、信息、生物医药等高新技术产业的发展,但是目前这些产业的核心技术国内还没有掌握,关键设备或零部件仍然依赖进口。如高性能轴承是飞机发动机、高铁、风电等产品的关键,但由于目前国内材料、工艺等方面的原因,其使用寿命远远不能满足要求,其他一些承受高频载荷的部件同样面临这些问题。近年国内开始研究的抗疲劳制造技术则是以被加工件的抗疲劳强度及疲劳寿命为判据,其中的核心技术之一是精密超精密加工工艺,可提高表面质量、改善表面应力状态,从而提高零件的疲劳寿命,这不仅要求具有超精密加工设备及工艺,而且还需研制材料及零部件的疲劳寿命精密测试设备(如图2所示)。
新能源产业(如太阳能)国内虽然发展很快,但核心技术还是掌握在国外,如硅片切割、研磨、抛光、刻划设备,高倍聚光菲涅尔透镜模具超精密加工设备等与国外还存在较大差距。信息产业的发展推动了芯片、存储等发展,随着存储密度越来越大,对磁盘的表面粗糙度以及相应的读写设备的悬浮高度及磁头的上下跳动量的要求大大提高,目前国外已经可以把磁头、磁盘的相对间隙最高控制在1nm左右。在医疗器械行业,超精密加工技术也起着很大的作用,人造关节采用钛合金或其他贵金属材料,这些高精度零件的表面处理对清洁度、光整度和表面粗糙度具有极高要求,需要进行超精密研抛,形状要根据个人的身体结构定制,国外价格昂贵,而国内无论从使用寿命和安全性等方面存在较大差距。其他如微型内窥镜中的微小透镜及器件、心脏搭桥及血管扩张器、医用微注射头阵列等国内现在还无法生产。
发动机喷嘴零件(如旋流槽、微小孔等特征)的精密加工与检测技术、发动机叶片型面及进排气边的精密加工与检测技术、整体叶盘的精密加工与检测技术等发展为航空发动机零部件的加工与检测提供了可靠保证,促进了航空发动机性能的提升。图3为发动机零部件专用五轴非接触扫描精密测量机。
超精密加工技术使导弹关键元器件的精度和质量产生了飞跃,进而大大提高了导弹的命中率。例如导弹头罩形状由球形向适应空气动力学的复杂形状发展,材料由红外材料向蓝宝石乃至金刚石发展,这也对超精密加工设备和超精密加工工艺提出了新的要求。
精密超精密加工技术发展趋势
1 超精密加工技术基础理论和实验还需进一步不断发展
所谓超精密加工技术基础理论,是指在了解并掌握超精密加工过程的基本规律和现象的描述后才能驾驭这一过程,取得预期结果。例如上世纪90年代初,日本学者用金刚石车刀在LLNL的DTM3上加工出最薄的连续切屑的照片,当时认为达到了1nm的切削厚度,已成为世界最高水平,并至今无人突破(如图4)。那么超精密切削极限尺度是多少、材料此时是如何去除的,此外超精密加工工艺系统在力、热、电、磁、气等多物理量/场复杂耦合下的作用机理是什么、此时系统的动态特性、动态精度及稳定性如何保证等都需要得到新理论的支持。
随着计算机技术的发展,分子动力学仿真技术从20世纪90年代开始在物理、化学、材料学、摩擦学等领域得到了很好的应用,美国、日本等国首先应用该技术研究纳米级机械加工过程,国内从21世纪初在一些高校开始应用分子动力学仿真技术对纳米切削及磨削过程进行研究,可描述原子尺寸、瞬态的切削过程,在一定程度上反映了材料的微观去除机理,但这一切还有待于实验验证。
2 被加工材料和工艺方法也在不断扩展
钛合金是航空最常用的材料之一,氢作为有害杂质元素对钛合金的使用性能有极其不利的影响,如会引起钛合金氢脆、应力腐蚀及延迟断裂等,但是近年来研究表明通过合理有效地控制渗氢、相变及除氢等过程,获得钛合金组织结构的变化,从而可以改善其加工性能,提高加工表面质量和效率。同样通常认为黑色金属是无法利用天然金刚石进行超精密切削加工的,多年来也一直在进行各种工艺研究,如利用低温流体(液氮或二氧化碳)冷却切削区进行低温冷却车削、采用超声振动切削黑色金属、采用金刚石涂层刀具等,采用离子渗氮和气体渗氮工艺对模具钢进行处理,但上述方法到目前为止还无法工程化应用。近年来通过离子注入辅助方式改变被加工材料表层的可加工性能,实现硅等硬脆材料复杂形状的高效超精密切削。
抗疲劳制造技术的发展为超精密加工技术提出了新的发展方向,超硬材料的精密加工工艺要求控制表层及亚表层的损伤及组织结构、应力状态等参数,如航空发动机轴承材料M50NiL表面处理后硬度超过了HRC70。随着单晶涡轮叶盘和单晶涡轮叶片在航空发动机上的应用,要求被加工材料没有重融层和变质层,从而对精密加工工艺提出了新要求。随着导弹马赫数的增加,要求头罩材料的抗耐磨性提高,已从红外材料向蓝宝石材料头罩乃至金刚石材料发展,形状也从球形向非球面乃至自由曲面发展,对超精密加工设备、工艺及检测技术提出了新的要求。
在未来零部件设计与制造将会增加一项功能表面结构的设计与制造,通过在零件表面设计和加工不同形状的微结构,从而提高零部件力学、光学、电磁学、升学等功能,这将是微纳制造的重要应用领域,2006年成立的国际纳米制造学会经专家讨论并认同,纳米制造中的核心技术将从目前以MEMS技术逐步转向超精密加工技术。
4 超精密加工开始追求高效
超精密加工技术从发展之初是为了保证一些关键零部件的最终精度,所以当初并不是以加工效率为目标,更多关注的是精度和表面质量,例如一些光学元件最初的加工周期是以“年”为加工周期。但是随着零件尺寸的进一步加工增大和数量的增多,目前对超精密加工的效率也提出了要求。例如为了不断提高观察天体范围和清晰度,需不断加大天文望远镜的口径,这就同样存在天文版的摩尔定律,即每隔若干年,光学望远镜的口径增大一倍,如建于1917年位于美国威尔逊山天文台的Hooker望远镜的口径为2.5m,是当年全世界最大的天文望远镜;到1948年被Hale望远镜取代,其口径达到了5m;1992年新建成的Keck望远镜的口径达到了10m,目前仍在发挥着巨大的作用。目前正在计划制造的巨大天文望远镜OWL主镜口径达到100m,由3048块六边形球面反射镜组成,次镜由216块六边形平面反射镜组成,总重约1~1.5万t,按照目前现有的加工工艺,可能需要上百年的时间才能完成。此外,激光核聚变点火装置(NIF)需要7000多块400mm见方的KDP晶体,如果没有高效超精密加工工艺,加工时间也无法想象。为此需要不断开发新的超精密加工设备和超精密加工工艺来满足高效超精密加工的需求。
5 超精密加工技术将向极致方向发展
随着科技的进步,对超精密加工技术已经提出了新的要求,如要求极大零件的极高精度、极小零件及特征的极高精度、极复杂环境下的极高精度、极复杂结构的极高精度等。
欧洲南方天文台正在研制的超大天文望远镜VLT反射镜为一块直径8.2m、厚200mm的零膨胀玻璃,经过减重后重量仍然达到了21t。法国REOSC公司负责加工,采用了铣磨、小磨头抛光等加工工艺,加工周期为8~9个月,最终满足了设计要求,目前许多新的超精密加工工艺如应力盘抛光、磁流变抛光、离子束抛光等出现为大镜加工提供了技术支撑。前面提到的微纳结构功能表面结构尺寸小到几个微米,如微惯性传感器中的敏感元件挠性臂特征尺寸为9μm,而其尺寸精度却要求±1μm。
美国国家标准计量局研制的纳米三坐标测量机(分子测量机)是实现如何在极复杂环境下的极高精度测量的典型例子,该仪器测量范围50mm×50mm×100μm,精度达到了1nm,对环境要求及其严格,最内层壳温度控制17±0.01℃,次层壳采用主动隔振,高真空层工作环境保持1.0×10-5Pa,最外层壳用于噪声隔离,最后将整体结构安装在空气弹簧上进行被动隔振。自由曲面光学曲面精度要求高、形状复杂,有的甚至无法用方程表示(如赋值曲面),但由于其具有卓越的光学性能近年来应用范围不断扩大,但自由曲面光学零件的设计、制造及检测等技术还有待于进一步发展。
6 超精密加工技术将向超精密制造技术发展
超精密加工技术以前往往是用在零件的最终工序或者某几个工序中,但目前一些领域中某些零部件整个制造过程或整个产品的研制过程都要用到超精密技术,包括超精密加工加工、超精密装配调试以及超精密检测等,最典型的例子就是美国的美国国家点火装置(NIF)。
为了解决人类的能源危机,各国都在研究新的能源技术,其中利用氘、氚的聚变反应产生巨大能源可供利用,而且不产生任何放射性污染,这就是美国国家点火工程。我国也开始了这方面的研究,被称为神光工程。NIF整个系统约有2个足球场大小,共有192束强激光进入直径10m的靶室,最终将能量集中在直径为2mm的靶丸上。这就要求激光反射镜的数量极多(7000多片),精度和表面粗糙度极高(否则强激光会烧毁镜片),传输路径调试安装精度要求极高,工作环境控制要求极高。对于直径为2mm的靶丸,壁厚仅为160μm,其中充气小孔的直径为5μm,带有一直径为12μm、深4μm的沉孔。微孔的加工困难在于其深径比大、变截面,可采用放电加工、飞秒激光加工、聚焦离子束等工艺,或采用原子力显微镜进行超精密加工。系统各路激光的空间几何位置对称性误差要求小于1%、激光到达表面时间一致性误差小于30fs、激光能量强度一致性误差小于1%等。如此复杂高精度的系统无论从组成的零部件加工及装配调试过程时刻都体现了超精密制造技术。
更多关于材料、材料腐蚀控制、材料科普等方面的国内外最新动态,我们网站会不断更新。希望大家一直关注中国腐蚀与防护网http://www.ecorr.org
责任编辑:杨扬
投稿联系:编辑部
电话:010-62313558-806
中国腐蚀与防护网官方 QQ群:140808414
免责声明:本网站所转载的文字、图片与视频资料版权归原创作者所有,如果涉及侵权,请第一时间联系本网删除。
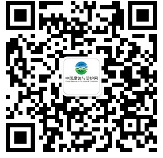
官方微信
《中国腐蚀与防护网电子期刊》征订启事
- 投稿联系:编辑部
- 电话:010-62316606-806
- 邮箱:fsfhzy666@163.com
- 中国腐蚀与防护网官方QQ群:140808414