锌合金当中各项主要元素及微量元素对铸造性能和铸件性能的影响。
铜(Cu)
在铝合金中固溶进铜(Cu),机械性能可以提高,切削性变好。不过,耐蚀性降低,容易发生热间裂痕。作为杂质的铜(Cu)也是这样。
铜(Cu)含量超过1.25%可以明显增加合金的强度与硬度。但Al-Cu的析出,压铸铸后会收缩,继而转为膨胀,使铸件尺寸不稳定。
镁(Mg)
为抑制晶粒间的腐蚀而加入少量的镁(Mg),镁(Mg)的含量超过了规定值,就会使流动性变差,并且也容易产生热脆性,冲击值也降低。
硅(Si)
是改善流动性能的主要成份。从共晶到过共晶都能得到最好的流动性。但结晶析出的硅(Si)易形成硬点,使切削性变差,所以一般都不让它超过共晶点。另外,硅(Si)可改善抗拉强度、硬度、切削性以及高温时强度,而使延伸率降低。
镁(Mg)
铝镁合金的耐蚀性最好,因此ADC5、ADC6是耐蚀性合金,它的凝固范围很大,所以有热脆性,铸件易产生裂纹,难以铸造。作为杂质的镁(Mg),在AL-Cu-Si这种材料中,Mg2Si会使铸件变脆,所以一般标准在0.3%以内。
铁(Fe)
铁(Fe)虽然能明显提高锌(Zn)的再结晶温度,减缓再结晶的过程,但是在压铸熔炼当中,铁(Fe)来自铁坩埚,鹅颈管和熔化用具,固溶于锌(Zn),铝(Al)所带的铁(Fe)是极微量的,超过了固溶限的铁(Fe) 会以FeAl3 结晶出来。(Fe)所造成的缺陷多生成渣滓以FeAl3的化合物浮起。铸件变脆,机加工性能变差。铁的流动性会影响铸件表面的光滑度。
杂质的铁(Fe)会生成FeAl3的针状结晶,由于压铸是急冷,所以析出的晶体很细,不能说是有害成份。含量低于0.7 %则有不易脱模的现象,所以含铁(Fe)0.8 ~ 1.0 %反而好压铸。含有大量的铁(Fe),会生成金属化合物,形成硬点。并且含铁(Fe)量过1.2 %时,降低合金流动性,损害铸件的品质,缩短压铸设备中金属组件的寿命。
镍(Ni)
和铜(Cu)一样,有增加抗拉强度和硬度的倾向,对耐蚀性影响很大。想要改善高温强度耐热性,有时就加入镍(Ni),但在耐蚀性及热导性方面有降低的影响。
锰(Mn)
能改善含铜(Cu),含硅(Si)合金的高温强度。若超过一定限度,易生成Al-Si-Fe- P+o { T*T f;X
Mn四元化合物,容易形成硬点以及降低导热性。锰(Mn)能阻止铝合金的再结晶过程,提高再结晶温度,并能显着细化再结晶晶粒。再结晶晶粒的细化主要是通过MnAl6化合物弥散质点对再结晶晶粒长大起阻碍作用。MnAl6的另一作用是能溶解杂质铁(Fe),形成(Fe,Mn)Al6减小铁的有害影响。锰(Mn)是铝合金的重要元素,可以单独加入Al-Mn二元合金,更多的是和其他合金元素一同加入,因此大多铝合金中均含有锰(Mn)。
锌(Zn)
若含有杂质锌(Zn),高温脆性大,但与汞(Hg)形成强化HgZn2对合金产生明显强度作用。JIS中规定在1.0%以内,但外国标准有到3%的,这里所讲的当然不是合金成份的锌(Zn),而是以杂质锌(Zn)的角色来说,它有使铸件产生裂纹的倾向。
铬(Cr)
铬(Cr)在铝中形成(CrFe)Al7和(CrMn)Al12等金属间化合物,阻碍再结晶的形核和长大过程,对合金有一定的强化作用,还能改善合金韧性和降低应力腐蚀开裂敏感性。但会增加淬火敏感性。
钛(Ti)
在合金中只需微量可使机械性能提高,但导电率却下降。Al-Ti系合金产生包晶反应时,钛(Ti)的临界含量约为0.15%,如有硼存在可以减少。
铅(Pb) 锡(Sn) 镉(Cd)
在铝合金中有时还存在钙(Ca),铅(Pb),锡(Sn)等杂质元素。这些元素由于熔点高低不一,结构不同,与铝(Al)形成的化合物亦不相同,因而对铝合金性能的影响各不一样。钙(Ca)在铝中固溶度极低,与铝(Al)形成CaAl4化合物, 钙(Ca)能改善铝合金切削性能。铅(Pb),锡(Sn)是低熔点金属,它们在铝(Al)中固溶度不大,降低合金强度,但能改善切削性能。
铅(Pb)含量的增加可以降低锌(Zn)的硬度,增加锌(Zn)的溶解度,但是在含铝(Al):o _;l S%E的锌合金中,铅(Pb),锡(Sn),镉(Cd)任意一种超过规定量,都会产生腐蚀。这种腐蚀是不规则的,经过某段时间以后才产生,而且在高温,高湿气氛下,腐蚀得特。
更多关于材料方面、材料腐蚀控制、材料科普等方面的国内外最新动态,我们网站会不断更新。希望大家一直关注中国腐蚀与防护网http://www.ecorr.org
责任编辑:王元
投稿联系:编辑部
电话:010-62313558-806
中国腐蚀与防护网官方 QQ群:140808414
免责声明:本网站所转载的文字、图片与视频资料版权归原创作者所有,如果涉及侵权,请第一时间联系本网删除。
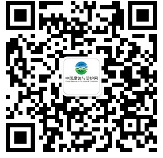
官方微信
《中国腐蚀与防护网电子期刊》征订启事
- 投稿联系:编辑部
- 电话:010-62316606-806
- 邮箱:fsfhzy666@163.com
- 中国腐蚀与防护网官方QQ群:140808414