电子束表面熔覆技术已经成为当前的研究热点,其能量密度高、加工速度快、功率参数可控性好和绿色环保等优点广泛应用于各个领域。 电子束表面处理是以加速电子为载体的入射能量, 在极短的时间内作用于材料表面薄层内,由此引发快速熔化、凝固、汽化、应力波、冲击波和增强扩散等物理化学现象, 使材料能获得普通热处理方法难以达到的物理、化学及力学性能 ,最终得到基体表面具有特定合金成分及特定性能的改性层。 本文对电子束熔覆技术的原理、研究现状和存在的问题进行了综述。
1 电子束熔覆改性技术的原理
1.1 电子束材料表面加热机理
当高速的电子束流扫射被处理的基体表面时,电子能穿过基体的表面到达距离表面的一定深度,将能量传递给基体的金属原子, 致使金属原子的震动加剧,该过程是把电子的动能转化为热能,从而使被处理基体的表层温度迅速升高。 电子束焊接时热量在被扫射材料表面下的某一薄层下析出, 该薄层被称为电子穿透层,如图 1 所示,电子穿透层的厚度跟电子加速电压的平方成正比,跟基体材料的密度成反比,一般都在 1mm 以内。 当电子撞击到基体表面时首先穿越电子穿透层, 此时电子的动能几乎不变, 仅极少部分能量被弹性散射电子带走或损耗于二次电子发射,因此电子不能对穿透薄层进行加热。当电子进入基体内部后, 穿透至电子行程的那一厚度上,由于在次表层扩散受阻,从而引起能量传输,将动能转化为热能使基体表面发生熔化 。
1.2 电子束熔覆改性原理
电子束熔覆技术作为涂层预置后的改性处理方法,电子束熔覆前,需将涂层预置在基体上,根据要求:厚度一般为几微米到几毫米。然后利用高能量密度电子束热源经聚焦后对预置涂层材料表面进行处理, 瞬间可把涂层由室温加热至奥氏体化温度或熔化温度,使涂层全部熔化,基体表层部分熔化,增加涂层与基体之间的粘结强度,改善涂层性能 。 电子束熔覆时只有严格控制能量密度, 才能精确保证涂层及基体熔化深度。 能量密度过大会导致基体熔化深度加大,涂层成分严重稀释,表面粗糙度增加。 能量密度过小会导致涂层未充分重熔, 进而造成涂层与基体之间的粘结强度降低。 图 2 为电子束熔覆改性原理示意图。
1.3 电子束熔覆改性特点
电子束熔覆技术是近期发展起来的新技术,其在表面熔覆改性方面主要有以下几个特点: 电子束能量密度高,利用率高,仅需毫秒间就可将金属材料表面由室温加热至奥氏体化温度或熔化温度, 且冷却速度可达 10 6 ~10 8 ℃/s ;与激光相比使用成本低。电子束处理设备一次性投资比激光少 ( 约为激光的1/3) ,其运行成本比激光低一半左右 ;电子束能量和能量密度的调节很易通过调节加速电压、 电子束流和电子束的汇聚状态来完成 , 整个过程易于实现自动化;电子束加热深度和尺寸范围比激光大。 电子束加热时熔化层至少几个微米厚, 能量沉积范围较宽,而且约有一半电子作用区几乎同时熔化;电子束加工是在真空条件下进行的,既不产生粉尘,也不排放有害气体和废液,对环境几乎不造成污染,加工表面不产生氧化, 特别适合于加工易氧化的金属及合金材料,以及纯度要求极高的半导体材料。
2 电子束表面熔覆改性技术研究现状
电子束虽然在工业中的应用有几十年的历史,但是在表面熔覆改性方面的应用则始于 20 世纪 70年代初期。 由于该技术在不断的改进和完善, 已经成为材料表面改性方面一个强有力的工具。国内外的相关机构对电子束熔覆进行了广泛而深入的研究。
2.1 国外研究现状
电子束表面熔覆技术在国外研究地区主要集中在北美、欧洲及亚洲。 主要内容包括以下几个方面。
2.1.1 电子束熔覆工艺及强化机理研究
Weisenburger 采用高速火焰热喷涂方法用镍基合金制备 CoNiCrAlY 涂层,再进行电子束重熔研究。结果表明:距离表层 30~40μm 范围内气孔被彻底消除, HVOF 涂层表面粗糙度由 62μm 下降至 3.7μm ,而 VPS 涂层表面粗糙度也从 47μm 下降至 8μm ,高温氧化试验涂层氧化膜增长尺度减小。 重熔的CoNiCrAlY 涂层作为电子束物相沉积热障涂层与基体间的粘结层,近表层气孔的消除、快速熔凝的表层细小晶粒和表面粗糙度的降低对 EB-PVD 热障涂层的形成十分有利。 粘结层中氧化物 (TGO) 的生长导致热障涂层 (TBC) 中应力的引入,并最终导致TBC 涂层撕裂。 电子束处理有助于 HVOF 涂层中TGO 的生成方式由脱离式转变为连续式。
2.1.2 电子束表面熔覆层相组成控制的研究
Eunsub 采用 Ti-6Al-4V 钛合金作为基体,在其表面电子束熔覆 Ti+B 4 C , 研究改性层硬质相分布。结果表明表面熔覆后的改性层中均匀分布大量的硬质相 TiC 和 TiB ,且改性层耐热性能得到提高。 AGTyurin 等在建筑类钢材 45 钢和 20 钢表面预涂混合粉末涂层 VK6 和 T15K6 ,之后用电子束扫描熔覆处理。 结果显示:在 0.8mm 深的热影响区形成了魏氏组织。 改性 层呈现出树 枝状 结 构 ,硬 度 达 到1700 HV , 在包含一些碳化物粒子的区域硬度达2500~2700HV ,改性层的耐磨性也得到提高。 IgbalM 等将合金粉末碳化硼涂覆在低碳钢 (MS) 基体上,利用电子束对其进行表面熔覆处理。 研究表明:经过 10keV , 50~100mA 的电子束扫描后, 合金粉末熔入基体中;经过 XRD 分析,基体热影响区中含有碳化硼成分; SEM 分析显示基体纤维组织中铁素体转变为枝晶,珠光体重结晶后得到细化,基体的硬度是处理前的 6 倍。
2.1.3 电子束表面熔覆制备合金层耐磨性的研究
乌克兰的 Pogrebnjak 等人主要研究了强流脉冲电子束对材料结构的影响, 提高了表面熔覆层对于各种材料表面的性能。 他们采用电子束蒸镀金属薄膜与 HCPEB 后处理结合的方法, 在纯铁表面实现了钼、钽、铝、铬等元素的合金化,最终提高了纯铁的耐腐蚀性和耐磨性。 Zenker 等研究了在较软基体上,利用电子束熔覆高硬度合金粉末,结果表明,经电子束扫描后,基体与涂层之间熔为一体,其涂层的表面硬度、强度和耐磨性都有所提高。
2.2 国内研究现状
国内电子束表面熔覆技术起步落后于国外工业发达国家,这方面的研究尚处于起步阶段。目前国内研究内容主要涵盖以下几个方面。
2.2.1 电子束表面熔覆对材料表面力学性能提高的研究
叶宏等人在 AZ91D 镁合金基体上采用真空电子束熔覆制备了铝涂层。 AZ91D 镁合金基体的硬度 为 60 ~80 HV0.05 , 喷 铝 层 的 硬 度 为 40 ~45HV0.05 。 经电子束熔覆处理后,涂层与基体结合良好,主要由熔覆区、合金化区和热影响区 3 部分组成。 在涂层表面,由于 Mg 溶入 Al 中产生固溶强化,使铝层的硬度提高到 115HV0.05 左右。 中间 Al-Mg合金化层因存在大量 Mg 17 Al 12 、 Mg 2 Al 3 等金属间化合物 , 硬度最高 , 达到 220HV0.05 。 在热影响区 , 由于基体金属快速熔凝产生晶粒细化, 从而导致硬度增加,约为 130HV0.05 。 镁合金材料表面硬度的显著提高,有利于材料表面耐磨性能的提高。 陆斌锋等用(Cr , Fe)7 C 3 和 52Cr 3 C 2 -48Fe( 质量分数为 52%Cr ,8%C- 和 40%Fe) 混合粉作为原料粉预置于 903 钢表面上,经电子束熔覆后,合金层的显微硬度在 1020~1080HV0.5 ,约为基体显微硬度 (350HV0.5) 的 2.3~3.1 倍。 合金层的相对耐磨性也比基体提高了 10.5倍。 这说明在低合金钢表面电子束熔覆合金层能显著提高基体的耐磨损性。 王英对 ZL109 铝硅合金采 用 直 径 为 0.8 mm 0Cr25Ni20 和 直 径 为1.0mm 的 1Cr18Ni9Ti 作为涂层, 然后进行表面熔覆处理,发现其表面硬度达 55~60HRB ,是基体硬度的 4~6 倍,与高镍铸铁基本相当,但其耐磨性能高于高镍铸铁。 刘科等人采用 45 钢作为基体,以钴基碳化钨粉末 (WC-12Co) 作为涂层,经过电子束熔覆后,改性层的平均硬度为 1280HV ,最高硬度可达 1450HV ,且改性层的深度更大,其耐磨性也提高了 10~12 倍。 石其年在 45 钢表面用 WC/Co+TiC涂层粉末进行电子束熔覆后, WC/Co 合金化层的耐磨性比常规淬火提高了 52 倍, Ni 、 Cr 粉末合金层的耐磨性约为常规处理的 2~7 倍。
2.2.2 电子束表面熔覆制备合金层耐腐蚀性的研究
张可敏等人将 Ti 粉末预涂在 316L 不锈钢表面后,采用 10 次强流脉冲电子束进行后处理,在电子束对表面涂层快速加热熔化、 混合及增强扩散效应的作用下,部分钛熔入基体表层形成一层富钛层,其在模拟体液中的耐腐蚀性得到了显著提高。 同样马廷涛利用 9310 渗碳轴承钢作为基体, Ti 粉作为涂层,经电子束 10 次强流脉冲熔覆后,耐腐蚀性有了一定的提高。 曹辉在纯镁上利用强流脉冲电子束表面渗透 Al ,发现其耐腐蚀性显著提高,维钝电流降低 2 个数量级以上,并且随着轰击次数的增加,腐蚀性能得到改善。
3 存在的问题和发展前景
通过研究, 电子束熔覆技术可使基体表面局部熔化区以极快的速度冷却, 形成急速凝固的表面微观组织结构,晶粒细化甚至形成微晶、非晶态固体。表面非晶层的形成可使材料表面变得光滑致密,表面力学性能得到很大改善, 同时也可提高表面耐腐蚀性、抗氧化性和隔热性能。但电子束熔覆技术还存在一些欠缺, 今后可从以下几方面进一步开展电子束熔覆技术的研究工作。
(1) 电子束与表层金属热力耦合机理。 与激光熔覆技术的研究相比还有一定差距, 电子束与材料之间的耦合作用机制还需进一步深入研究。 数值模拟技术可以优化电子束熔覆工艺, 将熔覆过程的温度场、残余应力场及流场进行数值模拟,即可把握和控制电子束熔覆工艺的过程。
(2) 电子束熔覆技术的缺陷。 电子束熔覆技术与等离子束喷涂在成本和工艺上有相对的优势,但是该工艺对微小及薄壁零件进行熔覆时, 由于电子束的温度场瞬间温度较高, 易造成薄壁零件的熔化或变形,这也是今后要解决的问题。
(3) 电子束 3D 打印技术。 电子束熔覆技术大部分仅限于二维平面使用,在未来的发展中,电子束熔覆技术可以用于三维产品, 也就是电子束 3D 快速成型技术。 通过计算机程序控制电子束按零件截面轮廓信息有选择性地熔化金属粉末, 一层一层的堆积,直至整个零件全部熔化完成,最后去除多余的粉末,得到所需的三维产品。与激光及等离子束快速成形技术相比, 电子束快速成形技术具有能量利用率高、加工速度快、功率大、运行成本低和高真空保护等优点, 是高性能复杂粉末冶金件的理想快速制造技术,在航空航天、汽车制造及生物医学等领域有着广阔的发展前景。
更多关于材料方面、材料腐蚀控制、材料科普等方面的国内外最新动态,我们网站会不断更新。希望大家一直关注中国腐蚀与防护网http://www.ecorr.org
责任编辑:王元
投稿联系:编辑部
电话:010-62313558-806
中国腐蚀与防护网官方 QQ群:140808414
免责声明:本网站所转载的文字、图片与视频资料版权归原创作者所有,如果涉及侵权,请第一时间联系本网删除。
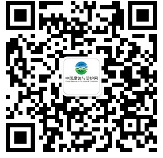
官方微信
《中国腐蚀与防护网电子期刊》征订启事
- 投稿联系:编辑部
- 电话:010-62316606-806
- 邮箱:fsfhzy666@163.com
- 中国腐蚀与防护网官方QQ群:140808414