0 前言
随着我国经济的快速发展,对石油以及石化产品需求不断增加,对进口原油的依赖越来越强。2011年我国原油消耗量4.9亿吨,其中进口原油占54.8%。我国进口原油的主要产地有中东(沙特、阿曼、苏丹等)、哈萨克斯坦、俄罗斯、南美(委内瑞拉)。不同产地的原油,其物性和腐蚀性不一样,原油的腐蚀性可从五个指标来评价:即原油酸值、硫含量、盐含量、氮含量和水含量。其中,硫含量<0.5%为低硫原油,硫含量0.5%~2.0%为中硫原油,硫含量>2.0%则为高硫原油。中东原油90%以上是含硫油,俄罗斯和哈萨克斯坦含硫原油占一半,委内瑞拉大多属于高含硫原油。而国产原油除胜利原油属于含硫原油外,其它多为腐蚀性较轻的低硫含蜡原油。含硫原油的大量进口和炼制给我国原油输送管道和储罐以及炼化厂的加工与贮运设施均会带来严重的腐蚀问题,给安全运行带来威协。因此,研究含硫油品的腐蚀与防护,选择适用的防腐蚀涂料与涂层体系,就显得尤为重要。
1 硫对钢铁的腐蚀
硫在原油中的存在形态主要有元素硫、硫化氢、硫醇、硫醚、二硫化物、噻吩类化合物以及分子量大、结构复杂的含硫化合物。一般将原油中存在的硫分为活性硫和非活性硫。元素硫、硫化氢和低分子硫醇等能直接与金属作用而引起设备的腐蚀,统称为“活性硫”,其余不能直接与金属作用的硫化物统称为“非活性硫”。但在高温下,“非活性硫”能向“活性硫”转化。不同产地的含硫原油,除了含硫量不同之外,由于所含硫化合物的种类及活性硫的含量也不同,也会影响到其腐蚀性能。含硫原油在炼制过程中,硫会不可避免地进人下游装置的生产过程中并且和部分产品油共存。
而硫对金属的腐蚀性,也与温度及其它腐蚀性成分含量等有极大的关系。通常,在介质温度≤120℃的情况下才会考虑采用涂层防护,因而,该温度区间下的含硫油品的腐蚀与防护才是防腐蚀涂料技术工作者需要关注的重点领域。
相关资料认为,当温度≤120℃,硫对钢材的腐蚀形式主要分为以下几种:
① H2S-H20型腐蚀
H2S气体在没有液态水时(气相状态)对钢材的腐蚀很轻,甚至根本没有腐蚀,但是当遇到水时,极易水解,在水中发生H2S-H20型腐蚀,其反应的电离方程式为:
H2S—H+ + HS-
H2S—H+ + S2-
在H2S-H20体系中的H+、HS-、S2-和H2S分子对金属的腐蚀为去极化作用,其反应方程式为:
阳极反应:
Fe—Fe++ 2e
Fe2++S2- — FeS
或Fe2++ HS-— FeS+ H+ +e
阴极反应:
2H++ 2e — 2H +H2
② .积水中SO2腐蚀
贮运装置积水部位中的SO2对防腐层脱落的钢材发生改性再生循环腐蚀,首先是S02在水中以亚硫酸形式存在,与Fe反应生成硫酸亚铁FeSO3,之后硫酸亚铁水解又形成游离的亚硫酸,而游离的酸又加速了铁的腐蚀,生成新硫酸亚铁,如此反复循环加速了对钢材的酸性腐蚀。
③ 硫酸盐还原菌腐蚀
原油中硫化物含量的增加,加大了硫酸盐还原菌腐蚀的风险。硫酸盐还原菌在缺氧的条件下,可以在金属表面的水膜中,利用溶液中的硫酸盐进行繁殖,硫酸盐在细菌作用下被还原为腐蚀性硫化物和有机酸。在缺氧的条件下,硫酸盐还原菌的代谢引起硫化物在金属表面附近的积累,当金属表面被生物膜覆盖时,硫化物在金属表面附近的浓度最高。如果铁离子和硫化物离子都存在,硫化铁很快在碳钢上形成并覆盖其表面。硫化铁的生成促进了阴极反应,电通道一旦形成,一个以低碳钢表面为阳极的电偶就生成了,电子通过硫化铁来传递。在铁离子浓度低时,暂时附着的保护性硫化铁膜在钢铁表面形成,从而降低了腐蚀速率,因此在完全无氧条件下的硫酸盐还原菌具有较低的腐蚀速率。然而一旦有氧存在时,硫酸盐还原菌代谢过程中产生的硫化亚铁开始氧化,最常见的有两种氧化过程:一种是直接吸收氧,生成硫酸亚铁,硫酸亚铁在水中水解并氧化成铁的氧化物和硫酸,加大了腐蚀速度。另一种是硫化亚铁氧化成铁的氧化物和硫磺,反应生成的硫磺将溶于油品中,在腐蚀钢材的同时造成油品污染。
当然,硫介质只是贮运设施中存在的各种复杂腐蚀性介质中的一种,水的存在是产生硫腐蚀的必要条件,而且在不同的运行环境下,硫对底材的腐蚀形式和程度也不同。但硫在油品中的存在会大大加速腐蚀,从而减短设备使用寿命,甚至导致安全和环境污染事故的发生,这是我们必须引起重视的。
2 含硫原油输送管道内腐蚀与防护
由于国产原油大多为低硫含蜡原油,通常情况下,原油中的蜡会在长输管道内壁沉积,因此早期我国长输管道内腐蚀问题相对较轻,长输管道内腐蚀问题也并没有受到人们的重视,也并没有采取防护措施。但近年来长输管道内腐蚀检测发现,输送进口含硫原油长输管道内腐蚀问题日益突出,如今年针对甬宁线的内腐蚀检测发现,内壁已出现多处腐蚀减薄现象。国外关于管线内腐蚀引起原油泄漏事故的报导也时有发生。
目前,各石油公司多采用原油脱水、除盐、加缓蚀剂和灭菌剂等方式来进行长输管道的内腐蚀防护,尚未采取涂层防护。由于腐蚀过程难于监测,内腐蚀检测费用相当困难和昂贵,现行防护手段是否足够保证管线的设计使用寿命尚未可知。
在含硫原油输送管道内表面采用涂层防护以延长管线使用寿命,技术上完全具有可行性。采用高固体份或无溶剂等液体环氧涂料,通过无空气喷涂或离心喷涂方式在流水线上完成工厂化涂装和现场管道补口,这已经在大量输水、输卤管道等工程上得到了成熟应用。在含硫原油输送管道上推行内涂层防护只是需要进一步的经济性和必要性评估与论证。
3 含硫原油储罐的内腐蚀与防护
国家石油战略储备计划的实施需要建设大量原油储罐,这些储罐多为大型外浮顶罐,大多贮存进口含硫原油。由于油田采油时脱水不完全以及在管输、船运及泵送过程中难已避免地混入水蒸汽及海水,水易在罐底沉积,导致罐底板上表面成为腐蚀最严重的部位。相关资料介绍,罐底板上表面以坑蚀为主,均匀腐蚀减薄也很严重,有些原油罐投用后未到检修年限,底板便腐蚀穿孔。硫在罐底板腐蚀过程中无疑扮演了最为重要的角色。
《GB 50393-2008钢质石油储罐防腐蚀工程技术规范》、中石化《加工高含硫原油储罐防腐蚀技术管理规定》及中国涂料工业协会行业规范CNCIA-HG/T 0001-2006《石油贮罐导静电防腐蚀涂料涂装与验收规范》中均指出:原油储罐底板内表面和油水分界线以下的壁板内表面应采用牺牲阳极和绝缘型防腐蚀涂层保护相结合的保护形式,但在绝缘涂层的表面电阻率和最小干膜厚度要求上存在差异。高固体厚浆型环氧玻璃鳞片涂料、无溶剂环氧防腐涂料等,以其优异的耐油性、耐酸碱性、耐硫化物、绝缘性和易厚涂性,已成为该部位常用的涂料类型。
更多关于材料方面、材料腐蚀控制、材料科普等方面的国内外最新动态,我们网站会不断更新。希望大家一直关注中国腐蚀与防护网http://www.ecorr.org
责任编辑:庞雪洁
投稿联系:编辑部
电话:010-62313558-806
中国腐蚀与防护网官方 QQ群:140808414
免责声明:本网站所转载的文字、图片与视频资料版权归原创作者所有,如果涉及侵权,请第一时间联系本网删除。
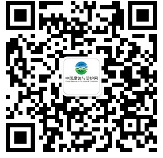
官方微信
《中国腐蚀与防护网电子期刊》征订启事
- 投稿联系:编辑部
- 电话:010-62316606-806
- 邮箱:fsfhzy666@163.com
- 中国腐蚀与防护网官方QQ群:140808414