引言:材料成型方法是零件设计的重要内容,也是制造者们极度关心的问题,更是材料加工过程中的关键因素。
不同的加工成型方法将会对材料的性能产生不同影响;
成型方法对于材料的适用性也不一;
成型工艺也决定了生产周期,成本,批量等关键性因素。
下面就金属、玻璃、陶瓷的成型工艺做详尽介绍
金属成型工艺
一 铸造
液态金属浇注到与零件形状、尺寸相适应的铸型型腔中,待其冷却凝固,以获得毛坯或零件的生产方法,通常称为金属液态成形或铸造。
工艺流程:液体金属→充型→凝固收缩→铸件
工艺特点:
1、可生产形状任意复杂的制件,特别是内腔形状复杂的制件。
2、适应性强,合金种类不受限制,铸件大小几乎不受限制。
3、材料来源广,废品可重熔,设备投资低。
4、废品率高、表面质量较低、劳动条件差。
铸造分类 :
(1)砂型铸造(sand casting)
砂型铸造:在砂型中生产铸件的铸造方法。钢、铁和大多数有色合金铸件都可用砂型铸造方法获得。
工艺流程:
砂型铸造工艺流程
技术特点:
1、适合于制成形状复杂,特别是具有复杂内腔的毛坯;
2、适应性广,成本低;
3、对于某些塑性很差的材料,如铸铁等,砂型铸造是制造其零件或,毛坯的唯一的成形工艺。
应用:汽车的发动机气缸体、气缸盖、曲轴等铸件
(2)熔模铸造(investmentcasting)
熔模铸造:通常是指在易熔材料制成模样,在模样表面包覆若干层耐火材料制成型壳,再将模样熔化排出型壳,从而获得无分型面的铸型,经高温焙烧后即可填砂浇注的铸造方案。常称为“失蜡铸造”。
工艺流程:
熔模铸造工艺流程
工艺特点
优点:
1、尺寸精度和几何精度高;
2、表面粗糙度高;
3、能够铸造外型复杂的铸件,且铸造的合金不受限制。
缺点:工序繁杂,费用较高
应用:适用于生产形状复杂、精度要求高、或很难进行其它加工的小型零件,如涡轮发动机的叶片等。
(3)压力铸造(die casting)
压铸:是利用高压将金属液高速压入一精密金属模具型腔内,金属液在压力作用下冷却凝固而形成铸件。
工艺流程:
工艺特点
优点:
1、压铸时金属液体承受压力高,流速快
2、产品质量好,尺寸稳定,互换性好;
3、生产效率高,压铸模使用次数多;
4、适合大批大量生产,经济效益好。
缺点:
1、铸件容易产生细小的气孔和缩松。
2、压铸件塑性低,不宜在冲击载荷及有震动的情况下工作;
3、高熔点合金压铸时,铸型寿命低,影响压铸生产的扩大。
应用:压铸件最先应用在汽车工业和仪表工业,后来逐步扩大到各个行业,如农业机械、机床工业、电子工业、国防工业、计算机、医疗器械、钟表、照相机和日用五金等多个行业。
(4)低压铸造(low pressure casting)
低压铸造:是指使液体金属在较低压力(0.02~0.06MPa)作用下充填铸型,并在压力下结晶以形成铸件的方法。。
工艺流程:
技术特点:
1、浇注时的压力和速度可以调节,故可适用于各种不同铸型(如金属型、砂型等),铸造各种合金及各种大小的铸件;
2、采用底注式充型,金属液充型平稳,无飞溅现象,可避免卷入气体及对型壁和型芯的冲刷,提高了铸件的合格率;
3、铸件在压力下结晶,铸件组织致密、轮廓清晰、表面光洁,力学性能较高,对于大薄壁件的铸造尤为有利;
4、省去补缩冒口,金属利用率提高到90~98%;
5、劳动强度低,劳动条件好,设备简易,易实现机械化和自动化。
应用:以传统产品为主(气缸头、轮毂、气缸架等)。
(5)离心铸造(centrifugal casting)
离心铸造:是将金属液浇入旋转的铸型中,在离心力作用下填充铸型而凝固成形的一种铸造方法。
工艺流程:
工艺特点
优点:
1、几乎不存在浇注系统和冒口系统的金属消耗,提高工艺出品率;
2、生产中空铸件时可不用型芯,故在生产长管形铸件时可大幅度地改善金属充型能力;
3、铸件致密度高,气孔、夹渣等缺陷少,力学性能高;
4、便于制造筒、套类复合金属铸件。
缺点:
1、用于生产异形铸件时有一定的局限性;
2、铸件内孔直径不准确,内孔表面比较粗糙,质量较差,加工余量大;
3、铸件易产生比重偏析。
应用:
离心铸造最早用于生产铸管,国内外在冶金、矿山、交通、排灌机械、航空、国防、汽车等行业中均采用离心铸造工艺,来生产钢、铁及非铁碳合金铸件。其中尤以离心铸铁管、内燃机缸套和轴套等铸件的生产最为普遍。
(6)金属型铸造(gravity die casting)
金属型铸造:指液态金属在重力作用下充填金属铸型并在型中冷却凝固而获得铸件的一种成型方法。
工艺流程:
工艺特点
优点:
1、金属型的热导率和热容量大,冷却速度快,铸件组织致密,力学性能比砂型铸件高15%左右。
2、能获得较高尺寸精度和较低表面粗糙度值的铸件,并且质量稳定性好。
3、因不用和很少用砂芯,改善环境、减少粉尘和有害气体、降低劳动强度。
缺点:
1、金属型本身无透气性,必须采用一定的措施导出型腔中的空气和砂芯所产生的气体;
2、金属型无退让性,铸件凝固时容易产生裂纹;
3、金属型制造周期较长,成本较高。因此只有在大量成批生产时,才能显示出好的经济效果。
应用:金属型铸造既适用于大批量生产形状复杂的铝合金、镁合金等非铁合金铸件,也适合于生产钢铁金属的铸件、铸锭等。
(7)真空压铸(vacuumdie casting)
真空铸造:通过在压铸过程中抽除压铸模具型腔内的气体而消除或显著减少压铸件内的气孔和溶解气体,从而提高压铸件力学性能和表面质量的先进压铸工艺。
工艺流程:
工艺特点
优点:
1、消除或减少压铸件内部的气孔,提高压铸件的机械性能和表面质量,改善镀覆性能;
2、减少型腔的反压力,可使用较低的比压及铸造性能较差的合金,有可能用小机器压铸较大的铸件;
3、改善了充填条件,可压铸较薄的铸件;
缺点:
1、模具密封结构复杂,制造及安装较困难,因而成本较高;
2、 真空压铸法如控制不当,效果就不是很显著。
(8)挤压铸造(squeezing die casting)
挤压铸造:是使液态或半固态金属在高压下凝固、流动成形,直接获得制件或毛坯的方法。它具有液态金属利用率高、工序简化和质量稳定等优点,是一种节能型的、具有潜在应用前景的金属成形技术。
工艺流程:
直接挤压铸造:喷涂料、浇合金、合模、加压、保压、泄压,分模、毛坯脱模、复位;
间接挤压铸造:喷涂料、合模、给料、充型、加压、保压、泄压,分模、毛坯脱模、复位。
技术特点:
1、可消除内部的气孔、缩孔和缩松等缺陷;
2、表面粗糙度低,尺寸精度高;
3、可防止铸造裂纹的产生;
4、便于实现机械化、自动化。
应用:可用于生产各种类型的合金,如铝合金、锌合金、铜合金、球墨铸铁等
(9)消失模铸造(Lost foam casting )
消失模铸造(又称实型铸造):是将与铸件尺寸形状相似的石蜡或泡沫模型粘结组合成模型簇,刷涂耐火涂料并烘干后,埋在干石英砂中振动造型,在负压下浇注,使模型气化,液体金属占据模型位置,凝固冷却后形成铸件的新型铸造方法。
工艺流程:预发泡→发泡成型→浸涂料→烘干→造型→浇注→落砂→清理
技术特点:
1、铸件精度高,无砂芯,减少了加工时间;
2、无分型面,设计灵活,自由度高;
3、清洁生产,无污染;
4、降低投资和生产成本。
应用:适合成产结构复杂的各种大小较精密铸件,合金种类不限,生产批量不限。如灰铸铁发动机箱体、高锰钢弯管等。
(10)连续铸造(continual casting)
连续铸造:是一种先进的铸造方法,其原理是将熔融的金属,不断浇入一种叫做结晶器的特殊金属型中,凝固(结壳)了的铸件,连续不断地从结晶器的另一端拉出,它可获得任意长或特定的长度的铸件。
工艺流程:
技术特点:
1、由于金属被迅速冷却,结晶致密,组织均匀,机械性能较好;
2、节约金属,提高收得率;
3、简化了工序,免除造型及其它工序,因而减轻了劳动强度;所需生产面积也大为减少;
4、连续铸造生产易于实现机械化和自动化,提高生产效率。
应用:用连续铸造法可以浇注钢、铁、铜合金、铝合金、镁合金等断面形状不变的长铸件,如铸锭、板坯、棒坯、管子等。
铸造相关设备供应商:
免责声明:本网站所转载的文字、图片与视频资料版权归原创作者所有,如果涉及侵权,请第一时间联系本网删除。
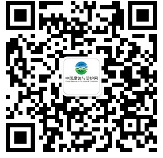
官方微信
《中国腐蚀与防护网电子期刊》征订启事
- 投稿联系:编辑部
- 电话:010-62316606-806
- 邮箱:fsfhzy666@163.com
- 中国腐蚀与防护网官方QQ群:140808414