无损检测技术之前主要应用于金属材料,检测金属表面存在的缺陷通常可以选用液体渗透检测和涡流检测;而金属内部深度区域主要可以通过X射线和超声波来完成检测。
随着科技的发展,新型复合材料的应用日益广泛,而适用于金属的传统无损检测技术在面临复合材料检测时存在着一些不足:
(1)非金属材料对X射线的吸收能力很弱;
(2)超声波会很容易分散和被复合材料吸收;
(3)非金属材料无法通过电磁感应产生涡流来完成检测;
(4)液体渗透技术主要用于检测表面存在的裂纹和一些明显的孔洞缺陷,并不适用于复合材料。
热无损检测(Thermal nondestructive testing,TNDT)技术是通过获取材料的热力学数据和图像来描述材料的内部结构,可用于检测金属以及非金属材料内部存在的缺陷,如裂纹、杂质、分离、结构分层,以及材料本身热力学性能的变化,应用范围非常广泛,尤其适用于复合材料的检测。红外热成像技术就是一种典型的热无损检测技术。
但是每一种无损检测技术都有其优势和不足,对于复合材料产品,红外热成像检测技术是“一枝独秀”呢?还是各种无损检测方法“团结力量大”呢?来自法国的D.Balageas、加拿大的X.Maldgue和美国的D.Burleigh等研究人员就将红外热成像检测技术和其他无损检测技术并用,通过不同的数据处理方法对获取的数据进行综合分析,从而用于复合材料的全面检测。
1.各种无损检测技术比较
表1主要介绍了一些常见无损检测技术的特点,这些检测方法都存在以下共同的特点:
(1)都存在一定的不足,没有单一的方法满足所有领域的检测;
(2)需要一定的理论知识和实验技能,单一的方法需要一定的培训基础(超声除外);
(3)大多数检测手段都可以获取图像数据(超声除外)。
表1.不同种类无损检测技术的特点
根据检测环境和限定条件、需要考虑的缺陷种类、成本、检测速度以及用户需求,再加上不同检测方法存在诸多的限制条件,包括检测条件以及对被测样品的要求,结合检测人员自身丰富的经验,才能最终为样品选出合适的无损检测技术。
2.红外热成像技术的优势
当材料的温度发生变化时存在明显的热传导过程,因此,理论上来说红外热成像技术适用于各种材料。传统的红外热成像图如图1所示。
图1. 太阳能电池的表观图(左)及其红外热成像图(右)
但这里要指出的是,如果材料的热导率很低,热量很难深入到材料的内部,这种情况下就需要限定红外热成像技术的检测深度。
高热导率的金属材料具有很高的热传导速率,因此整个检测过程持续时间非常短,缺陷处产生的温度信号会在很短的时间内消失。具有光泽或者抛光的金属具有较低的热辐射率,因此可以迅速升温,所产生的热辐射能量也就较低。如果想应用红外热成像技术检测这类金属材料时,可以在其表面喷涂一层具有高热辐射率的涂层(如黑色涂层,black painting),然后再进行检测。有了这层黑色涂层以后,检测区域的能量吸收变大,热辐射率增高,就可以产生明显的热差异了。还需说明的是:不论涂层的颜色如何,油性涂料(和大多数其他涂料)的红外谱带热辐射率均约为0.9。
相比金属而言,碳纤维增强复合材料和碳基复合材料也非常适合利用红外热成像技术进行检测。但在检测中也存在一定的限制,如缺陷相比基材往往具有较低的热导率,因此需要产生一个明显的涡流热传递过程。此外,缺陷往往需要达到一定的尺寸且当其垂直于热流方向时更容易被测出。实际上,红外热成像技术最适合检测的样品就是大尺寸的薄样品,即使是脱胶现象也能被有效地检测到。
红外热成像技术的显著特点就是不用接触到样品本身,完全不会破坏样品,测试速度非常快,检测区域往往是平方米级别的,而且是非常安全的,因此它广泛适用于制造工厂、实验室、机场以及大型建筑等各种检测场合。
红外热成像检测和样品表面的光学性能相关,样品表面的光学性能直接影响到材料的能量吸收。这一不足也可以通过引入其他手段,如机械刺激、微波等手段加热样品来解决。
3.多种方法联用
(1)红外热成像+地质雷达
地质雷达(Ground Penetrating Radar,GFR)可以通过发射中心频率为12.5~1200MHz的电磁波信号到检测物上,根据接收到的反射信号的时间间隔来计算出与检测物之间的距离。
Swiderski, W.等利用地质雷达和红外热成像技术模拟杂乱环境中地下地雷的位置,通过两种技术的结合,精准完成了对地雷的检测。
在模拟实验中,研究人员在模拟区域上方放置一个金属罐来模拟杂乱环境下对地质雷达检测的干扰源。图2(a)为普通视图下检测区域的直观呈现。图2(b)为地质雷达的检测结果,可以看出地雷上部存在的杂乱环境显然已经影响到地雷具体方位的检测了。图2(c)为红外热成像结果,可以看出由于金属罐本身对红外辐射的反射作用造成其很难被观测到,而地雷却被精准的检测到了。图2(d)则是将地质雷达图像和热红外图像的数据进行叠加的结果,最终杂乱的环境状况和地雷的位置都被清晰地体现出来了。
图2.地雷位置模拟检测的直观视图(a)、地质雷达检测图(b)、红外热成像检测图(c)和叠加图像(d);
(2)红外热成像+X射线+超声
当玻纤增强复合材料中的缺陷深度不超过几毫米且内部缺陷在微米级别的时候,可以利用红外热成像技术来完成检测。X射线断层扫描技术可以检测截面区域存在的细小缺陷(X射线的能量为120 KeV,最小的检测深度为100微米)。但是该技术检测时间较长,也仅适用于小尺寸样品。而红外热成像技术可以扫描检测的范围达到平方米级别。这两种技术碰撞在一起会产生什么样的火花呢?
对于航天飞机蜂窝结构平板上的水分含量检测,通常会采用标准的X射线扫描成像技术来完成,这是一种非常有效的检测方法,也是目前最为广泛采用的方法之一。然而针对蜂窝结构的平板往往需要对材料的两侧进行检测,而X射线断层扫描技术所需检测时间较长,且往往是对单一面进行检测,无法满足同时对两侧进行检测的要求。另外,X射线检测技术有一个十分明显的不足,就是检测过程需要进行防护,避免对检测人员带来伤害。
然而,红外热成像技术是一种面扫描模式,其形成的图像结果与X射线断层扫描形成的图像相结合,能有效地反映出单一蜂窝结构的水分含量,如图3所示。
图3.利用X射线断层扫描(左)和红外热成像(右)检测蜂窝结构的水分含量;
最后,精准测定水分含量往往要通过超声检测来完成,超声检测技术可以有效地检测水分存在的深度,但检测时间较长,如图4所示。
图4.利用超声检测(左)和红外热成像(右)检测副翼蜂窝结构的水分含量;
(3)红外热成像+声发射
当复合材料承受机械载荷时,如出现细微损伤会产生声信号,声发射检测技术可以有效检测整个工作过程的声信号变化情况。利用检测信号可以计算损伤的深度,并得到机械载荷和工件形变位移之间的关系。这时候如果再加上红外热成像检测,那就更是如虎添翼了!
当红外热成像和声发射结果都能同时检测到损伤,即热信号和声发射信号同时产生,这表明损伤发生在表层的部分;而当只有红外热成像检测到损伤,即热信号落后于声发射信号,这表明损伤发生在材料的内部。如图5、图6所示。
图5.声发射检测技术与红外热成像技术并用检测复合悬架臂承受机械负荷期间发生损伤的检测结果
图6.声发射检测结果与红外热成像数据结合得出的归一化数据分析结果:损伤发生在表层(左)和内部(右)
4.红外热成像vs超声
超声检测技术属于五大常规无损检测技术内的一大类,通常也作为一个测试标准来和其他无损检测技术进行对比。因此这里也将红外热成像技术与超声无损检测技术进行了对比。选用140 Kevlar厚度为5mm的片材,利用压头施加载荷来模拟不同能级的冲击损伤,然后利用这两种检测方式对材料进行检测,如图7所示。
图7.红外热成像(上图右)和超声检测(下图中)的测试结果
(1)测试时间
超声检测需要1个小时才能完成,而红外热成像技术在短短的5秒内就可以完成。
(2)测试结果的检测置信分析
利用HIT-MISS方法对检测结果进行数据分析,得出红外热成像技术的a90为7.81mm,而超声检测技术的a90为12.75mm,a90表示测定损伤的尺寸大小有90%以上的可能性为相应的检测数据。这一置信分析的结果虽然只能对应此次测试条件下获取的数据结果分析,但也确实可以看出红外热成像技术可以实现快速检测,在无损检测技术应用上具有很大的潜力。
更多关于材料方面、材料腐蚀控制、材料科普等等方面的国内外最新动态,我们网站会不断更新。希望大家一直关注中国腐蚀与防护网http://www.ecorr.org
责任编辑:王元
《中国腐蚀与防护网电子期刊》征订启事
投稿联系:编辑部
电话:010-62313558-806
邮箱:ecorr_org@163.com
免责声明:本网站所转载的文字、图片与视频资料版权归原创作者所有,如果涉及侵权,请第一时间联系本网删除。
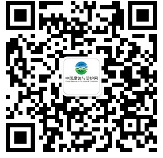
官方微信
《腐蚀与防护网电子期刊》征订启事
- 投稿联系:编辑部
- 电话:010-62316606-806
- 邮箱:fsfhzy666@163.com
- 腐蚀与防护网官方QQ群:140808414