航空整体叶盘是将叶片和轮毂做成一个整体,具有重量轻、避免榫头气流损失等优点,在先进航空发动机中的应用越来越广泛。整体叶盘结构复杂,叶片型面为复杂自由曲面,扭曲度大,加工精度要求高,相邻叶片之间通道深而窄、开敞性差,使整体叶盘制造困难,加工过程中叶片间加工区域狭窄,刀具可移动范围小,加工区域约束条件苛刻,使得加工过程中刀具矢量方向变化剧烈。
整体叶盘高效加工是在保证零件精度和质量的前提下,通过对加工过程的优化和提高单位时间材料切除量来提高加工效率和设备利用率,降低生产成本的一种高性能加工技术。涵盖了高效加工工艺;高效加工的数控编程技术;高效加工刀具选配及运用技术;加工过程的智能化控制。通过选择小切深、大进给等先进的加工方法,减少工艺性应力集中,降低加工表面非均匀、非稳定残余应力,提高零件的抗疲劳强度。
就国外整体叶盘加工技术来讲,最值得关注的是以下这三家:
1.德国HERMLE整体叶盘精加工流程
2.Mitsui SeikiUSA日本三井精机美国公司整体叶盘加工
3.意大利BRETON龙门5轴高速加工中心XCEEDER1200RT加工整体叶盘
国内外整体叶盘制造采用的主要工艺有:精密铸造、数控铣削、电解加工、电火花加工等。这些工艺各有其优缺点,而数控铣削加工灵活快速、可靠性高,因此发达国家多采用五坐标数控铣削加工整体叶盘。整体叶盘毛坯一般采用高强度难加工材料,不允许有裂纹和缺陷,叶片薄、扭曲度大、叶展长、受力易变形,而且由于叶片间的通道深而窄、开敞性很差,材料切除率很高,严重影响了数控铣削的可加工性。
数控铣削加工技术包括高精度五坐标机床技术、工艺技术、五轴联动编程技术、刀具技术等,它代表了相关技术领域的最新技术和最高水平,是新型高推重比发动机制造的关键技术之一。
钛合金整体叶盘加工工艺分析
钛合金整体叶盘的盘体和叶片材料通常采用(α+β)双相热强钛合金,具有良好的高温强度、耐腐蚀性、断裂韧性、热稳定性和蠕变性能,能够满足损伤容限设计和高结构效益及低制造成本等要求。
某钛合金整体叶盘毛坯采用焊接结构,盘体粗加工和叶片毛坯采用线性摩擦焊方式成为一个整体叶盘毛坯。叶片为变截面扭曲结构,弯扭度大、叶展长、叶片外缘薄、进气边缘和排气边缘厚度更薄(不足0.5mm)。叶盘盘体外型面为圆锥面,叶片外轮廓也是一个倒圆锥面(如图1所示)。
焊接整体叶盘数控加工关键就是叶片的数控铣削,必须突破下面几个重大的技术难题:
(1)叶片之间的通道窄而深,扭曲角度很大,刀具的可达性受到限制,必须采用五坐标方式并严格控制刀具的轴向轨迹;
(2)叶片为变截面扭曲结构,叶展长、叶片薄,造成叶片远端刚性极差,叶片厚度公差不足±0.1mm,较小的刀具切削力就会使叶片外缘产生较大弹性变形,从而使叶片厚度公差难以保证;
(3)钛合金优异的弹性性能使得精加工振颤加剧,必须采取有效的减振措施,避免振动对叶型表面完整性、粗糙度、厚度公差及焊缝造成不利影响;
(4)钛合金属难切削材料,切削加工本身就是个难题,叶片根部与盘体转接半径仅为R3(3mm),只能采用小直径刀具清根,让刀现象严重;
(5)盘体的外形为锥面,叶片外廓也是一个锥面,加工困难;
(6)叶片的型面不但扭曲角度大,进、排气边缘厚度为0.3mm,而且排气边缘有形状要求,刀具端刃切削时易崩刃;
(7)焊接后叶片是一块长方块形毛坯,余量分布极不均匀,此外还有摩擦焊挤出的飞边,又高又细,铣削十分困难。
总之,该整体叶盘五坐标数控铣削加工的关键技术包括叶盘通道与刀轴矢量的控制、刀具轨迹设计及光顺处理、通道的高效粗加工技术、叶片型面的精确加工技术、加工变形控制和叶片与刀具减振技术等。数控加工工艺设计及数控编程必须考虑到以上问题,采取有效的工艺措施才能保证设计要求。
整体叶盘数控加工工艺设计
1选择合适的机床
对整体叶盘进行数控铣削最理想的机床应该是带转台和主轴、能够摆角的五坐标卧式加工中心,并且主轴的摆角范围要足够大,能够实现立卧转换。
由于受设备、任务调度限制,该叶盘的加工采用了双摆头立式五坐标龙门铣,AB摆角范围为A±30°、B±30°。该设备的缺点在于没有转台,不能分度,AB摆角范围有限。因此必须针对每个叶片都有一套数控程序,程序量比带转台的机床多出了30多倍。
通过采取上述手段,此类机床能胜任该整体叶盘的数控加工。另外由于该叶盘上叶片的厚度为50mm,叶展为90mm,采取立式加工方式可使用更短的刀具,因此宜采用立式加工。
2 设计专用工装
整体叶盘的工装设计应能够满足角向定位和分度的要求,满足翻面定位夹紧的要求,并能够满足机床摆角后的行程。图2为粗加工时的状态及工装使用的情景。
3 数控铣削加工工艺过程
焊接后的整体叶盘数控加工面临的困难是切除摩擦焊产生的焊接飞边,由于此飞边又细又高又硬,铣削时很容易崩刃,摩擦焊挤出的飞边容易从根部折断而将整体叶盘上的材料带走,铣削效率极低。因此采用线切割或其他方式比铣削方式可能更合适。
整体叶盘外轮廓也是一个倒圆锥面,必须在叶片较厚刚性较好的情况下加工,所以外轮廓必须在粗加工前先加工,采用Z向分层方式加工。
整体叶盘粗加工的目的就是要快速去除大余量。粗加工主轴摆角一方面要能够切到整个叶片表面,另一方面也要考虑盘体的锥度形成。采用直径20~30mm左右的短刀具最为适宜。厚度方向分层切削,粗加工留2mm余量,接着进行半精加工,留0.3mm余量,采用底角带R的刀具,分层也可以再细些。
进、排气边缘厚度仅为0.3mm,必须在叶片有一定刚性但余量又不太大的情况下加工,所以应安排在精加工前进行。采用较小直径刀具,刀具轨迹垂直于叶片边缘进行行切,行距1mm,加工出的边缘曲线效果良好。
由于叶片的扭曲造成叶片两面分为凹面和凸面,考虑到机床的摆角范围,所以要安排双面加工。
4 选择合适的刀具
粗加工刀具首先要控制刀长,采用较短的刀具和直径较大的刀具,采用侧铣方式,切削效率和减振效果会明显提高。精加工叶片型面应选用底角R较大的刀具或球头刀具,配合较小的行距,切出的曲面会很光顺。
由于叶片根部为R3,用φ6的刀具刚性太差,无法加工,所以首先选用φ12R3刀具去除余量,然后用φ16×24°R3的专用锥度刀清根。特制的锥度刀不但保证了刀杆的刚性,而且又能实现R3的清根,刀具单侧12°的锥度,外加盘体17°的锥度,主轴需要摆角29°,刚好在其30°摆角范围之内可以铣到锥形盘体。所以,应适当定做专用刀具,可有效解决加工过程中出现的一些问题。
5 采取有效的减振与变形控制措施
精加工另一面时,叶片的刚性已经较差,切削力作用在叶展的端头,极易产生弹性变形并同时伴随着振颤,所以此面的加工重点是控制变形与振颤。叶片变形可直接导致厚度尺寸超差;而加工振颤可导致叶片表面产生振纹(见图3),并且容易使刀具崩刃,严重影响叶片表面质量。
采取在叶片通道间灌注建筑用胶的方法,改变了零件的阻尼特性,确实有效降低了振颤,并且使刀具转速达到了1000r/min,进给达到100mm/min。在此基础上又改用其他稍硬的物质填充在叶盘通道里(见图4),既能明显减少振颤,又能在叶片背面形成有力的支撑,抵消切削力造成的叶片弹性变形,确保了叶片的厚度。
此外,顺铣方式能明显减少加工振颤。双面加工、减少刀具长度能有效减少刀具振颤。进、排气边缘很薄,安排在叶片有一定刚性的精加工前进行加工,能减少变形与振颤。选择合理的切削参数,调整转速和进给速度,可有效控制振动。
整体叶盘数控加工程序编制时首先要考虑的是控制刀轴方向,因为通道太窄,叶片扭曲,盘体是锥形等因素,导致刀轴控制稍有差错就会出现干涉,此外退刀、空刀快速移动一定要控制幅度。粗加工可以采用定摆角等高线行切,或五坐标侧刃铣削,所有刀具轨迹应实现顺铣。精加工刀位轨迹设计要流畅、光顺,行距要小,才能保证行切出的曲面光顺。清根程序要留少许余量,避免刮伤叶片型面。
责任编辑:李玲珊
《中国腐蚀与防护网电子期刊》征订启事
投稿联系:编辑部
电话:010-62313558-801
邮箱:ecorr_org@163.com
中国腐蚀与防护网官方 QQ群:140808414
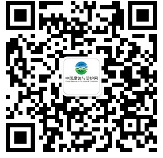
官方微信
《中国腐蚀与防护网电子期刊》征订启事
- 投稿联系:编辑部
- 电话:010-62313558-806
- 邮箱:fsfhzy666@163.com
- 中国腐蚀与防护网官方QQ群:140808414