"卡脖子"重灾区,九大关键战略材料介绍
2023-10-30 11:08:32
作者:中国表面工程 来源:中国表面工程
分享至:
导语
材料产业是国民经济的基础,具有举足轻重的地位。随着我国国力和国家地位的提高,南海石油的开采,以及国防、海洋开发、航空航天、先进轨道交通、核电和平利用等大型工程的建设均急需高温合金、高性能碳纤维等核心关键材料。
在国民经济需求的百余种关键材料中,约三分之一国内完全空白,约一半性能稳定性较差,部分产品受到国外严密控制,突破受制于人的关键战略材料,具有十分重要的战略意义。高端新材料是重大工程成功的保障,需要高端新材料核心技术全面突破时代已经到来。我国的关键工程战略材料转移高端、加大国产化比重迫在眉睫。关键战略材料的发展重点主要有高端装备用特种合金、高性能分离膜材料、高性能纤维及复合材料、新型能源材料、新一代生物医用材料、电子陶瓷和人工晶体、稀土功能材料、先进半导体材料、显示材料等。
“卡脖子”重灾区
关键战略材料主要包括高端装备用特种合金、高性能分离膜材料、高性能纤维及其复合材料、新型能源材料、电子陶瓷和人工晶体、生物医用材料、稀土功能材料、先进半导体材料、新型显示材料等高性能新材料,是实现战略新兴产业创新驱动发展战略的重要物质基础,且关键战略材料是支撑和保障海洋工程、轨道交通、舰船车辆、核电、航空发动机、航天装备等领域高端应用的关键核心材料,也是实施智能制造、新能源、电动汽车、智能电网、环境治理、医疗卫生、新一代信息技术和国防尖端技术等重大战略需要的关键保障材。但我国部分核心关键战略材料受制于人,约50%关键战略材料性能稳定性较差,使高端制造面临“无材可用”和“有材不敢用”困境。2019年工业和信息化部的调研显示,130多种关键战略材料中,中国有32%处于空白、52%依赖进口,存在巨大的国产化替代空间。《科技日报》曾从2018年4月起陆续报道的中国当时尚未掌握的35项关键技术中,近50%与关键战略材料相关。关键材料依赖进口导致中国制造企业被锁定在全球制造业产业链与价值链中低端。关键战略材料“卡脖子”,已成为中国制造业转型升级的突出短板。近年来,国际形势变化给中国关键战略材料技术创新乃至智造强国战略实施带来了严峻的挑战。实现关键战略材料的国产化替代,不仅是缓解技术断供风险和保障供应链安全可控的重要手段,更是突破“卡脖子”瓶颈、实现经济高质量发展和塑造国际竞争新优势的必然选择。加速中国关键战略材料的国产化替代进程时不我待。
发展瓶颈突破困难
相较于其他产业,关键战略材料产业国产化替代具有“长研发周期、高投入”“长验证周期、高难度”“长应用周期、高门槛”的突出特点。关键战略材料产业自身具有5大典型特征,这些特征使得我国现阶段该各行业面临瓶颈问题。第一,原创性基础研究能力是核心壁垒。新材料是科学规律与物质世界之间的桥梁,物理和化学领域的重大发现(很多是诺奖级的发现)直接或间接推动新材料技术发展。因此,美国、日本和西欧等基础科研强国在关键战略材料领域获得了大量原创性突破,并在全球构建专利壁垒,占领产业价值链的顶端。而且我国研发投入分配失调,多用于应用技术的研发,基础研究研发投入占比低,导致关键核心技术攻关后劲不足。另外,基础研究与工业生产结合黏度低,限制了研究成果的转化,导致原始创新能力不足。第二,研发和商业化投入巨大。材料行业属于典型的重资产产业,其研发、生产需大量专用设备投入,设备不断更新产生高折旧率及相应维护费用。更重要的原因是,其研发和商业化应用的不确定性相较于其他新兴产业更高,研发和商业化开销更大。根据Nature Material报道,在研发开销上,新材料企业分别是生物和软件企业的2倍和6倍;在商业化开销上,新材料企业是软件企业的50倍。第三,研发试验过程复杂导致工程化产业化周期漫长。材料最终进入市场投入使用包括理论层面突破及应用层面反复验证,需经历多环节多周期方可正式投入应用;即使通过理论实验或示范生产阶段,仍存在极大可能性因设备、工艺等因素无法进入大规模生产阶段。关键战略材料从研发到应用周期往往长达10-20年,产业的长周期性导致中国关键战略材料的某些技术虽然实现了突破,但在短期内难以转化为进入市场的国产化替代产品。第四,材料创新需要基础设备和技术协同支撑。材料从基础技术变为创新产品,需要包括设备技术、工艺技术、量产技术、应用技术、测量技术及表征技术在内的多种基础技术的高度支撑。比如,我国目前已突破超高纯稀土金属制备技术,但离实现产业化、保障集成电路等电子信息产业发展还有很长距离,很大程度上原因在于共性关键技术研发和中试平台的缺失,限制了已有研发能力向市场产品的应用转化力。第五,材料应用扩散依存于下游场景需求。作为典型产业间共性技术,材料技术开发需满足各种应用需求,需要配合应用场景改进,下游应用中需求的变化影响着材料创新的生死存亡,因此,特别需要材料开发与下游应用企业间的“共生共融、协同发展”。例如,稀土永磁材料生产企业和应用端的电机企业间缺乏有效协作,导致磁性材料性能难以满足电机不同场景的设计需求,阻碍产品的应用和国产化替代进程;新型显示材料缺乏从材料、器件、终端到最终应用的全产业链创新生态体系,产品难以单兵突破。
九大领域破局
2016年7月,国务院印发《“十三五”国家科技创新规划》,面向2030年,再选择一批体现国家战略意图的重大科技项目,其中提到重点新材料研发及应用,重点研制碳纤维及其复合材料、高温合金、先进半导体材料、新型显示及其材料、高端装备用特种合金、稀土新材料、军用新材料等,突破是制备、评价、应用等核心关键技术。2017年2月,《新材料产业发展指南》提出,要紧紧围绕新一代信息技术产业、高端装备制造业等重大需求,以耐高温及耐蚀合金、高强轻型合金等高端装备用特种合金,反渗透膜、全氟离子交换膜等高性能分离膜材料,高性能碳纤维、芳纶纤维等高性能纤维及复合材料,高性能永磁、高效发光、高端催化等稀土功能材料,宽禁带半导体材料和新型显示材料,以及新型能源材料、生物医用材料等为重点,突破材料及器件的技术关和市场关,完善原辅料配套体系,提高材料成品率和性能稳定性,实现产业化和规模应用。《中国制造2025》重点领域技术路线路进一步明确了高端装备用特种合金、高性能分离膜材料、高性能纤维及复合材料、新型能源材料、新一代生物医用材料、电子陶瓷和人工晶体、稀土功能材料、先进半导体材料、显示材料等九大领域的重点发展方向。
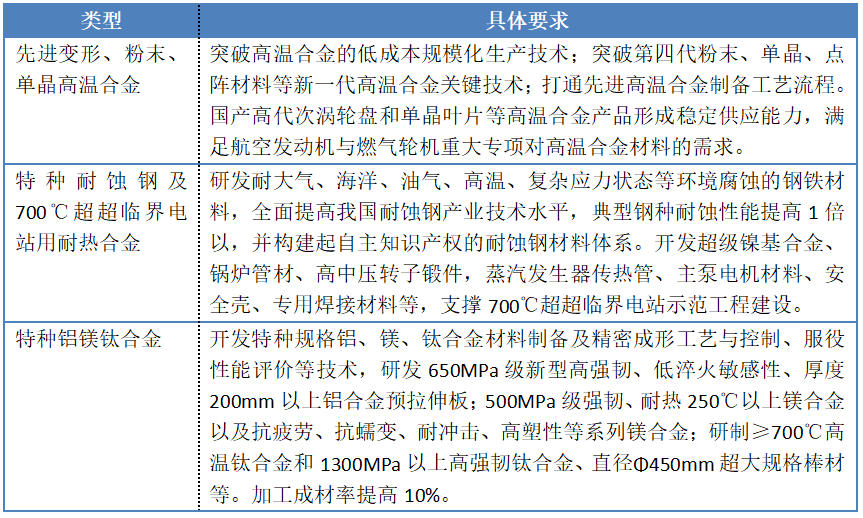


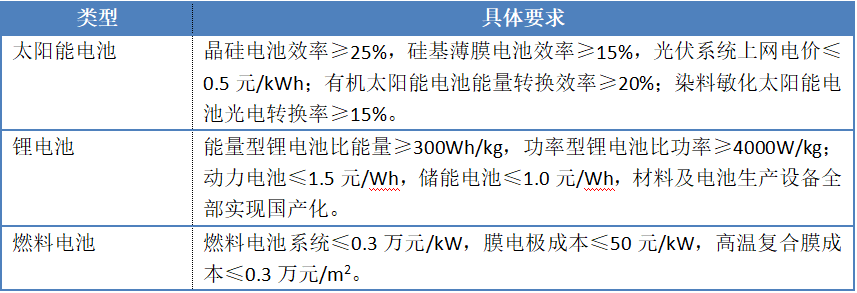
5.新一代生物医用材料
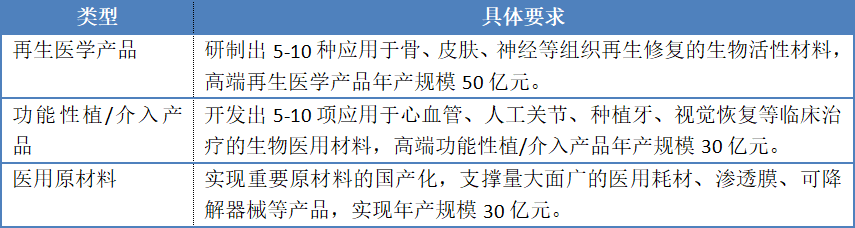
6.电子陶瓷和人工晶体

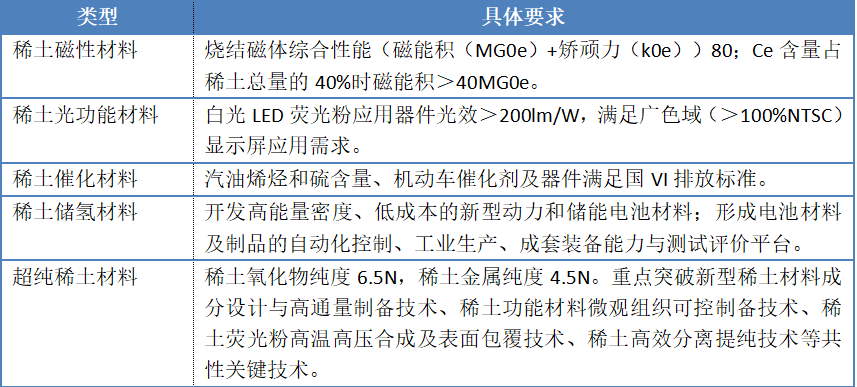
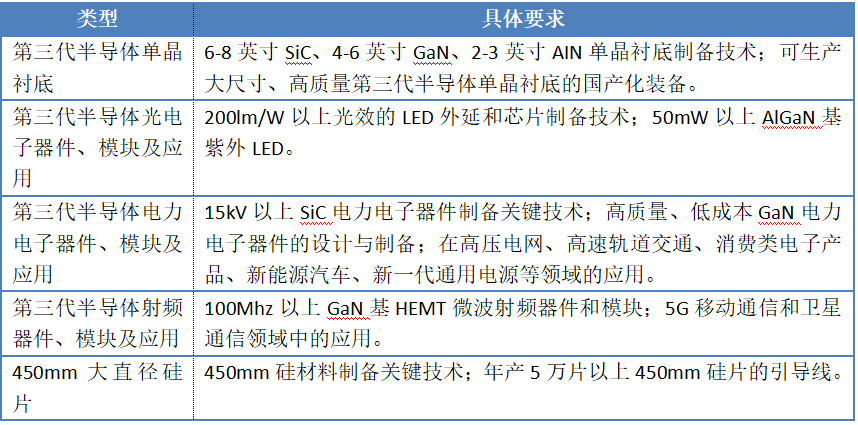
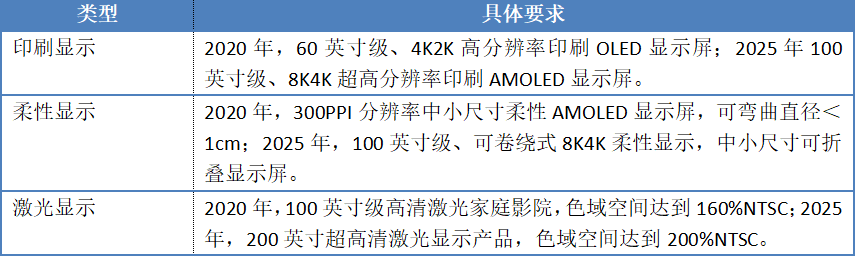
2021年3月发布的“十四五”规划第八章“深入实施制造强国战略”提出,依托行业龙头企业,加大重要产品和关键核心技术攻关力度,加快工程化产业化突破。实施重大技术装备攻关工程,完善激励和风险补偿机制,推动首台(套)装备、首批次材料、首版次软件示范应用。健全产业基础支撑体系,在重点领域布局一批国家制造业创新中心,完善国家质量基础设施,建设生产应用示范平台和标准计量、认证认可、检验检测、试验验证等产业技术基础公共服务平台,完善技术、工艺等工业基础数据库。强化要素保障和高效服务,巩固拓展减税降费成果,降低企业生产经营成本,提升制造业根植性和竞争力。推动工业用地提容增效,推广新型产业用地模式。扩大制造业中长期贷款、信用贷款规模,增加技改贷款,推动股权投资、债券融资等向制造业倾斜。允许制造业企业全部参与电力市场化交易,规范和降低港口航运、公路铁路运输等物流收费,全面清理规范涉企收费。建立制造业重大项目全周期服务机制和企业家参与涉企政策制定制度,支持建设中小企业信息、技术、进出口和数字化转型综合性服务平台。
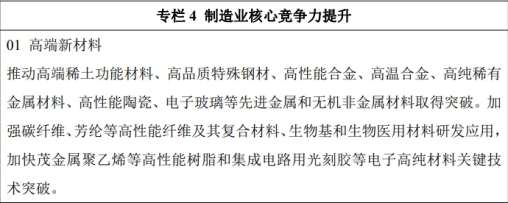
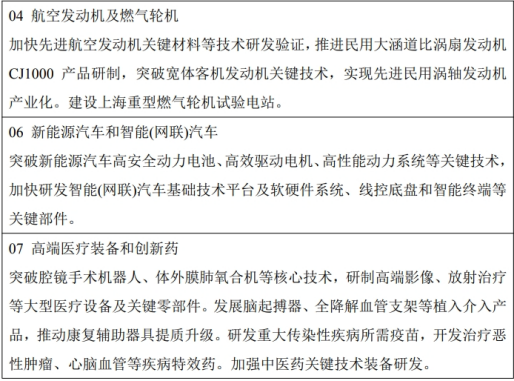
2021年12月,工信部发布《重点新材料首批次应用示范指导目录(2021年版)》,其中共提到高性能纤维及复合材料、稀土功能材料、先进半导体材料和新型显示材料、新型能源材料、生物医用及高性能医疗器械用材料等五大类107种关键战略材料。2021年12月,工信部、科技部、自然资源部发布《“十四五”原材料工业发展规划》。其中提到,坚持材料先行和需求牵引并重,聚焦国防建设、民生短板和制造强国建设重大需求,滚动制定关键材料产品目录,制定发布技术路线图。实施关键短板材料攻关行动,采用“揭榜挂帅”“赛马”等方式,支持材料生产、应用企业联合科研单位,开展宽禁带半导体及显示材料、集成电路关键材料、生物基材料、碳基材料、生物医用材料等协同攻关。实施大宗基础材料巩固提升行动,引导企业在优化生产工艺的基础上,利用工业互联网等新一代信息技术,提升先进制造基础零部件用钢、高强铝合金、稀有稀贵金属材料、特种工程塑料、高性能膜材料、纤维新材料、复合材料等综合竞争力。实施前沿材料前瞻布局行动,支持科研单位联合企业,把握新材料技术与信息技术、纳米技术、智能技术等融合发展趋势,发展超导材料、智能仿生、增材制造材料等,推动新的主干材料体系化发展,强化应用领域的支持和引导。实施材料基因工程计划,探索材料研发新模式的试点应用。
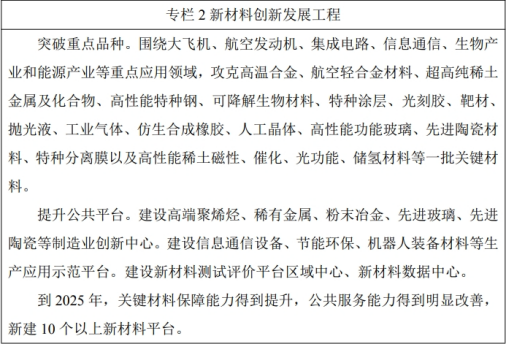
贯彻国家区域重大战略、区域协调发展战略、主体功能区战略,依据国土空间规划,推动原材料工业空间布局调整优化,聚焦产业基础好、比较优势突出、技术领先的行业细分领域或重点产品,发挥产业链龙头企业引领带头作用,推动要素聚集和价值提升,强化专业化协作和配套能力,打造一批石化化工、钢铁、有色金属、稀土、绿色建材、新材料产业集群。做大做强龙头企业,坚持市场主导和政府推动相结合,清除跨地区兼并重组障碍,清理市场分割、地区封锁等限制,协调解决企业跨地区兼并重组重大问题,支持企业加快跨区域、跨所有制兼并重组,提高产业集中度,开展国际化经营。在石化化工、钢铁、有色金属、建材等行业,培育一批具有生态主导力和核心竞争力的产业链领航企业,做强做大稀土企业集团,鼓励稀有金属企业加快整合。完善行业规范管理,促进市场要素向优势企业集中。鼓励金融机构按照风险可控、商业可持续原则,向实施兼并重组、转型升级的原材料企业提供综合性金融服务。培育壮大中小企业,提高原材料行业中小企业创新能力和专业化水平,鼓励龙头企业将配套中小企业纳入共同的产业链管理、质量管理、标准管理、合作研发管理等,建立稳定的供应、生产、销售等协作配套关系,实现大中小企业融通发展。重点围绕原材料产业链先进基础工艺、核心基础零部件等方面,培育一批专精特新“小巨人”企业、制造业单项冠军企业。加强上下游衔接联动。原材料企业加强与上下游企业协同共生、耦合发展,向生产零部件、部品化延伸,向提供一体化的材料系统化解决方案转变。采用研发早期介入、后期持续改进的合作模式,推动商业模式创新和业态创新,促进生产型制造向服务型制造转变。支持行业协会搭建供需衔接平台。建立健全航空材料、重型燃气轮机材料、集成电路材料、新能源汽车驱动电机用稀土永磁材料、生物医用材料、建筑用热轧型钢等上下游合作机制。发挥龙头企业对新材料创新应用带动作用。支持第三方机构组织开展重点材料“一条龙”应用示范推进工作。
免责声明:本网站所转载的文字、图片与视频资料版权归原创作者所有,如果涉及侵权,请第一时间联系本网删除。