钢铁和常用有色金属(铝、镁、钛和铜)是传统材料,在经济和社会发展中,具有广泛的用途。随着工程科技的发展,世界钢铁和常用有色金属材料应用领域不断拓展,仍然充满活力,在促进人类文明进程中占有重要地位。
一、国际发展现状
近年来,世界钢铁产量增长缓慢。国际钢铁协会(World Steel Association)统计数据表明,2017年,全球粗钢产量为16.91亿吨,同比增长 5.3%,除独联体地区粗钢产量与 2016年持平外,全球其他地区粗钢产量均同比增长。2017年全球粗钢产量前十的国家如表 12-5所示。
表12-5 2017 年全球粗钢产量前十国家
数据来源:世界钢铁协会
(一)高品质特殊钢材料
国外特殊钢(不含电工钢)材料,年产量约 8800万吨,产量和所占钢产量比例,也相对稳定且呈缓慢增长趋势。工业发达国家特殊钢产量一般占其钢总产量的 15%~20%,其中瑞典的特殊钢占比高达 45%~50%。日本特殊钢的产量和出口量位居发达国家之首。其他发达国家在某些特殊钢品种上也各有特色。例如,瑞典是世界上“特殊钢比重”最高的国家,其 SKF公司的轴承钢、山德维克公司的工模具钢在国际上具有很高的知名度;法国的不锈钢、精密合金,奥地利的工模具钢,美国和英国的高温合金等都为国际一流水平。国外的特殊钢产品具有尺寸精度高、钢中有害物质少、夹杂控制水平高、使用寿命长、耐热耐腐蚀等优异使用性能。
海洋工程装备建造商的第一阵营公司主要在欧美地区。这些公司垄断了海洋工程装备开发、设计、工程总包及关键配套设备供货;而海洋工程装备用钢的国外生产厂家分布在日本和德国,其中的代表厂家为日本JFE公司、日本新日铁公司与德国迪林根公司。国外由于海洋工程装备用钢开发时间较长,产品更加成熟,主要体现为如下特点:
(1)标准专用化。日本JFE公司,对海洋平台钢板形成了自己的企业标准系列,如 JFE-HITEN系列高强钢板、JFE-HITEN系列良好焊接性及大线能量焊接钢板、低温用钢板及耐海水腐蚀钢板等;美国有针对海洋平台用钢的API2W和2Y标准,对有特殊要求的钢板,如低温、应变时效、表面质量等进行了规定。
(2)大规格高强度。目前,JFE公司,海洋平台用钢抗拉强度为360-980MPa,可以生产厚度达 125~150mm 的特厚板。
(3)特殊使用性能。
(二)高温合金材料
高温合金材料的研发和生产,不断受到用户技术发展和经营模式变化的影响,获得了长足的发展。航空发动机提高推重比、增加安全性和经济性,航天器速度超声速倍率的增大,车用发动机降耗减排的高增压技术等,牵引了粉末高温合金、单晶高温合金、金属间化合物等新材料的发展,且使研发与产业部门更加重视材料的工程化技术研究,以加快新材料进入工业化稳定生产的过程;竞争的压力驱使发动机用户提高燃料效率、减少油耗(趋势是年平均减少1%),而这主要需依靠空气动力效率、燃烧室设计的改进和材料使用温度的提高而产生的热力学效率提高。其中,双性能/ 双组织涡轮盘由于更符合涡轮盘的工况特点将成为高推重航空发动机的必然选择,而使用温度可达 1100℃的第三代单晶高温合金高压涡轮叶片和密度只有4.0g/cm3 的钛铝金属间化合物低压涡轮叶片将是提高涡轮机效率的重要材料基础。
(三)有色金属材料
世界各发达国家,都非常重视有色金属材料(特别是先进轻型合金)的研究发展及产业化技术开发工作。随着发展中国家制造业的兴起,低端有色金属材料的生产加工正逐步转向发展中国家,但日本、美国、德国、俄罗斯等发达国家在新型有色金属材料领域仍然保持着技术资本的领先优势,在一些关系到高技术工业的高性能有色金属结构和功能材料上一直占据着垄断地位。奥科宁克、诺贝丽斯、海德鲁等世界先进企业在高强高韧铝合金材料的研制生产领域占据世界主导地位,是全球航空航天、交通运输等领域轻质高强材料的供应主体;全球钛加工企业经过联合和兼并,已向集团化、国际化的方向迈进了一步,形成了美国、日本、独联体三足鼎立的局面。美国的Timet、RMI 和 AllegenTeledyne三大钛生产企业的总产量占美国钛加工总量的 90%,也是世界航空级钛材的主要供应商。日本的三菱化学控股公司、古河及美国的奥林等企业则主导着全球高强高导铜合金市场,凭借技术先导优势赢得了高额利润和竞争优势。
二、国内发展现状
“十二五”期间,我国的金属材料产业取得了举世瞩目的成就,钢铁和常用有色金属的产量都接近全球产量的一半。2017年,全国10 种有色金属的产量为 5378万吨,比上年增长 3%,增速比上年提高 0.5个百分点。其中,铜的产量为 889万吨,增长 7.7%,增速比上年提高 1.7个百分点;电解铝的产量为3227万吨,增长 1.6%,增速比上年提高 0.3个百分点;铅的产量为472万吨,增长9.7%,增速比上年提高 4个百分点;锌的产量为 622万吨,下降 0.7%,增速比上年增长 2%;氧化铝的产量为 6902万吨,增长 7.9%,增速比上年提高 4.5个百分点。
我国的金属材料产业,顺应国民经济的高速增长、工业化、城镇化等对钢铁和有色金属材料的旺盛需求,在规模扩张上创造了举世空前的纪录,同时产品质量也有了较大提高。目前钢铁材料除少数大类品种外,其他钢材的自给率都达到 100%,关键钢材产品(如汽车用钢、管线钢、硅钢、船板等)的产量大幅提高,22大类钢材品种中有 18类钢材的国内市场占有率达到95%以上。而且一些钢材(如板材、管材)已经打入美国、日本、西欧和韩国等发达产钢国家和地区的市场。这说明,我国钢铁行业不仅在品种质量上已经基本能满足各用钢部门的需求,而且部分品种达到发达国家用户的要求。我国有色金属品种也基本满足国内经济发展需求,多种新研制的轻合金材料已经实现批量生产和应用,钛合金大规格棒材用于国际航空制造业,铜及铜合金复杂管材、大型铝合金型材进入国际市场并占据主导地位。
(一)高品质特殊钢材料
近年来,我国特殊钢行业与整个钢铁行业一样发展迅速,取得了举世瞩目 的成就。不锈钢、轴承钢、齿轮钢、模具钢、高速钢等的产量均居世界第一,为我国国防工业及国民经济建设提供了重要的原材料保障。但我国特殊钢行业的整体发展水平和产品质量与先进国家仍有很大差距。根据战略性新兴产业的需求,现对能源、交通、海洋及航空航天用先进钢铁材料进行阐述。
1.1. 先进能源用钢
先进能源用钢,主要包括风电、水电、核电装备用钢。我国已经具备了风电用宽厚板、高级别 Φ80mm风电轴承用钢(GCr15SiMn)的批量生产能力,偏航轴承总成和风叶主轴轴承总成还在研制之中。目前国内生产风力发电机用轴承钢的企业有江阴兴澄特种钢铁有限公司、湖北新冶钢有限公司、宝钢特钢有限公司等。我国自主生产的 600MPa级压力钢管能满足使用要求,800MPa级的压力钢管正在开发中,基本掌握了水电、核电装备所用的大型不锈钢铸锻件的生产技术,改变了依赖进口的局面。
1.2. 现代交通用钢
现代交通用钢,包括高速轨道用钢和汽车用钢。高速轨道用钢主要有列车转向架、车轮、掣肘、轴承、弹簧及钢轨用钢。目前我国自主研制的微合金化车轮用钢已经成功用于时速200km的列车,时速高于200km 的车轮用钢正在研发中;对于高端车轴用钢S38C,我国正处于工业试验阶段;车辆轴承用钢的高端产品 GCr18Mo能够立足国内生产;高铁弹簧钢研究已有重大突破,有望实现国产化;我国高铁用钢轨的产能已达世界第一,质量也处于世界先进水平。我国的钢轨生产厂家主要是鞍钢集团有限公司、包头钢铁(集团)有限责任公司和攀钢集团有限公司的国有大型企业。
在汽车用钢方面,强塑积 20GPa% 的第一代汽车用钢、强塑积在 60GPa%的第二代汽车用钢均可实现国产化,强塑积在30~40GPa% 的第三代高性能汽车用高强度钢的研发已经接近世界先进水平。我国的高强度汽车用钢生产厂家主要是中国宝武钢铁集团有限公司、鞍钢集团有限公司、武汉钢铁集团公司和首钢集团等企业。
1.3. 海洋用钢
海洋用钢主要包括海洋平台、海底油气管线、特种船舶用钢。目前屈服强度 355MPa以下海洋平台用钢基本实现国产化,占海洋平台用钢量的 90%;海底管线钢 X65、X70、X80及厚壁海洋油气焊管均已实现国产化;化学品船用中厚板已经实现国产化,自主研制的2205型双相不锈钢已被成功地应用在化学品船上;液化天然气船用 9%Ni 钢和液化乙烯储罐用 12Ni19钢已经能够批量生产。我国的海洋工程用钢的主要生产厂家为中国宝武钢铁集团有限公司、鞍钢集团有限公司、首钢集团、新余钢铁股份有限公司、武汉钢铁集团公司、南京钢铁集团有限公司、湘潭钢铁集团有限公司、济钢集团有限公司等,其他大部分钢厂产品并不能达到厚度和强度的要求,目前这几个生产厂已具有年产50万吨以上的生产能力。
1.4. 航空航天用钢
大部分航空航天用钢已经实现国产化,但大型客机的轴承、连接螺栓、着陆齿轮等部件用的结构钢还需要进口。大推比运载火箭系统壳体、动力连接装置、星箭或船箭解锁包带等部件用特殊钢及各类空间环境设施用高品质特殊钢还有待进一步开发。
(二)高温合金材料
经过近 60年的发展,我国的高温合金产业在航空发动机、战略导弹等武器装备方面取得了很大进展。
在变形高温合金方面,仿制 Inconel718合金并结合我国的国情和生产装备状况,形成了国内牌号 GH4169及相应的技术条件和标准,基本满足了我国航空航天领域对 GH4169合金的需求。
在铸造高温合金方面,单晶合金以仿制为主,已经发展了第一代、第二代单晶合金,并逐渐走向工程化应用。第三代、第四代单晶合金尚处于研制阶段,基本满足了我国先进航空发动机研制的迫切需求。
在粉末高温合金方面,目前国内的研究主要集中于前三代粉末高温合金的应用研究,第四代粉末高温合金研制处于起步探索阶段。
国内高温合金行业代表企业有宝钢特钢有限公司、抚顺特殊钢股份有限公司、攀钢集团有限公司江油长城特殊钢有限公司、北京钢研高纳科技股份有限公司、沈阳中科三耐新材料股份有限公司、北京航空材料研究院、沈阳黎明航空发动机有限责任公司、西安航空动力股份有限公司等。
(三)高性能有色金属结构材料
高性能有色金属材料,主要包括高性能铝合金、镁合金、钛合金等轻型合金材料,高强高导铜合金及钨钼等难熔硬质合金,是我国发展大飞机、信息技术、高速铁路、海洋工程等国家重大工程的基础。
目前我国已经成为世界有色金属材料的生产消费大国,已连续 10多年居世界产量首位。通过引进消化与自主制造相结合,我国有色金属行业装备水平已达世界一流水平,其中大型冶炼与电解装备,连轧与连铸连轧装备,挤压、轧制与锻压设备的单机规模和整体数量都处于世界前列。在新材料及其制备加工领域取得了一批具有世界先进水平的自主知识产权,具备了一定的产业和技术优势,取得了一批具有自主知识产权、达到国际先进的成果。例如,我国新一代高强高韧高淬透性航空铝合金研究及其工程化制备技术取得突破性进展,铝合金大型特种型材及其挤压工模具研究开发取得成功;成功开发了具有我国自主知识产权的铜带、管拉铸技术及铜铝复合技术等新材料技术;大型钛合金铸锭和锻件研制生产取得明显进展,产品走向国际市场;新一代高强高导铜合金材料及其电子引线框架铜带产业化关键技术研究取得突破,达到万吨级产业规模。
但是,我国有色金属新材料核心技术和知识产权还比较落后,长期处于
技术跟踪状态,还没有建立有特色的完整合金牌号体系,具有自主知识产权并取得国际注册的新材料和热处理制度也寥寥无几,处于新材料开发和应用中美系、俄系、欧系合金混用的局面,巨大的市场优势和规模优势没有转化为技术优势。
我国有色金属行业已经遍布全国,形成了数千家国有、民营企业和合资企业大小不一、技术水平差别较大的市场化竞争局面。我国重大工程用先进有色金属材料主要由国有大型骨干企业研制生产,其中中国铝业集团有限公司和北京有色金属研究总院联合研制的新一代高强高韧铝合金和镁合金基本满足了我国航空航天重大工程新材料需求,以宝钛集团有限公司为首的钛合金骨干企业为国家重大工程研制并提供了一批重要钛合金材料。我国钨钼业形成了地勘–采选 – 冶炼 – 加工 – 科研开发比较完整的工业体系。硬质合金及钨钼材加工等工艺技术和设备仪器的档次显著提升,部分产品质量达到世界先进水平;钨丝和掺杂钨丝制取和加工方面的主流技术和装备已达世界先进水平;国防和航空用高性能耐震钨丝、汽车和电子行业用抗震耐热钨丝、微波炉和彩电钨热阴极部件已能生产;电子束熔炼加工电子级细晶钼开发成功并得到应用。
三、相关研究前沿
(十四)基于材料基因组的先进钢铁材料设计研发技术
从钢铁材料研发历程和发展趋势来看,高性能先进钢铁材料将向高强度、优异的强韧性匹配、高均匀化、长寿命化等方向发展,以实现材料的绿色化、智能化及定制化生产制备。传统炒菜或试错设计研发模式已难以满足上述需求。例如,航空航天、高技术船舶、轨道交通等高端装备制造用先进钢铁材料的疲劳、持久、蠕变、氢脆、腐蚀等使役性能研究需要大量的数据样本和长期的数据积累;传统超高强度钢研发从原型设计到材料应用至少需要20年。因此,面对先进钢铁材料新的发展需求,基于材料基因组的先进钢铁材料设计研发技术将成为创新和引领材料设计研发的重大基础技术。美国、欧盟、俄罗斯、日本等发达国家和地区均出台了相应的发展规划和计划,以加速高性能钢铁结构材料的研发。
该技术将结合第一性原理、热/动力学、相场、有限元等计算方法与模型进行多因素模块化耦合,研发先进钢铁材料成分 – 工艺 – 组织 – 性能 – 使役行为多尺度集成化计算方法,探索先进钢铁材料电子 – 原子层次每个“基因”片段对钢铁材料各项性能的影响和相关机制(包括合金元素扩散迁移过程、固溶体和析出相驱动力、亚稳相和析出相的材料物理化学性质等),实现合金设计、制备加工及服役行为全流程的高通量计算;发展高通量凝固及锻造基础理论;开发合金成分、微观组织、界面偏聚等多维、多尺度、多参量的高通量表征方法;为构建先进金属材料设计计算方法、高通量实验、高通量计算模拟和智能化数据库管理一体化集成计算创新平台,实现先进金属材料加速研发、综合性能提升及材料构件短流程、低成本和性能可控的高效制备提供理论支撑。
(十五)有色金属材料的绿色冶炼技术
在铝冶炼技术方面,目前全球采用的熔盐电解铝工艺围绕进一步降低电力消耗的目标,以提高电流强度、实现电解槽大型化为主攻方向,仍在继续完善,预计吨铝交流电耗能够降到13000kW·h以下。碳还原等新原理金属铝生产工艺以突破使用材料为重点,继续进行深入研究。一旦取得突破,能够使吨铝电耗降低到 8000kW·h。这将大幅度降低绿的生产成本和能源消耗。
在镁冶炼技术方面,目前普遍采用的硅热法镁冶炼工艺围绕进一步提高能源利用效率的目标,以余热利用为主攻目标,继续完善,预计吨镁标煤消耗能够降低到4t 以下。电解法镁市场工艺以降低生产成本为重点,继续进行深入研究。一旦取得突破,将大幅度减少金属镁生产的二氧化碳排放,降低能源消耗。
在钛冶炼技术方面,目前全球采用的克劳尔法海绵钛生产工艺围绕进一步降低电耗的目标,以镁电解电耗为主攻目标,继续完善,预计吨海绵钛电耗能够降低到18000kW·h以下。电解法金属钛以实际应用为重点,继续进行深入研究,一旦取得突破,将大幅度降低金属钛的生产成本,促进钛的广泛应用。
(十六)高性能轻合金的性能优化
在提高材料高强高韧性能方面,为满足航空等领域不断提高的要求,超高强铝合金研制基本上沿着高强度、低韧性→高强度、高韧性→高强度、高韧性、耐腐蚀方向发展,热处理状态则是沿着T6→ T73→ T76→ T736 (T74) → T77方向发展。
在合金设计方面的发展特点是,合金化程度越来越高,铁、硅等杂质含量越来越低,微量元素添加越来越合理,最终达到大幅度提高合金强度且同时保持合金优良的综合性能的目标。在提高材料耐高温性能方面,钛合金是先进航空发动机的关键支撑材料,高性能航空发动机的发展,对钛合金耐高温性能的要求越来越高。未来发展的主要方向是利用合理的微量元素添加和热处理技术,突破高温强度和热稳定性障碍,不断提升高温钛合金的使用温度,满足高性能航空发动机发展的需要。
在提高材料耐腐蚀性方面,腐蚀问题制约着镁合金的推广应用,提高镁合金的耐腐蚀性能,成为镁材料工程科技的重点。发展方向一是使其相间电位差趋于零,二是把镁合金表面的氧化膜由疏松变为致密,采用不同的元素形成不同的氧化产物,用多元氧化物填补空隙,提高镁合金的耐腐蚀性能。
(十七)金属近净加工技术
粉末冶金技术是一种高效率、低成本的金属近净成型技术。随着现代信息技术的发展,金属材料领域中,基于粉末冶金技术出现的3D打印技术取得重要突破,形成材料领域新的生产方式、产业形态、商业模式。在粉末冶金金属近净加工技术领域,智能制造的技术主要有注射成型(powder injection molding,PIM)、喷射成型、近终形成型(混合元素和预合金)、激光快速成型等。
从技术进展看,在未来 10~20年时间里,粉末冶金金属近净加工技术完全可以在人体器官、机械装备零部件等领域得到广泛应用。在金属近净挤压技术方面,相对于传统的金属铸造、锻造、压延轧制、普通挤压等技术,依托智能制造的金属近净挤压技术可以省略热轧坯锭制造环节,生产流程短、材料消耗少、能源消费低,将大幅度降低金属材料的制造成本。我国对铜及铜合金近净挤压技术开发进行了积极探索,在产业化方面取得了重要进展,居世界领先地位。在此基础上,深入开展多种金属的近净挤压技术开发,用于改造、完善传统金属加工技术,对金属加工技术具有重要意义。金属近净挤压技术主要围绕等静压、凝固成型等方面展开。
四、关键金属材料产业中长期发展战略
(一)发展思路
围绕信息、能源、节能环保、生物、航空航天及产业革新等方面的战略需求,突破海洋工程用钢、交通运输用钢、基础零部件用钢、超超临界电站用合金、铝镁钛等轻合金材料的核心技术,着力提高材料产业的自主创新能力,通过优化组织实施方式,支持量大面广和国家重大工程亟须的结构材料产业化建设,着力促进一批结构材料实现产业化和规模应用。大力发展结构材料新材料产业并建立产业链上下游优势互补、密切合作机制,有效缩短新材料研发、产业化和规模应用的周期,促进新材料企业加强技术创新,形成持续的创新能力,进一步增强我国关键结构材料产业的技术创新能力和产业化技术水平,实现我国从材料大国向材料强国的战略性转变,全面满足我国国民经济、国家重大工程和社会可持续发展对关键结构材料的需求。
(二)战略目标
1. 2025 年目标
钢铁和轻合金材料产业整体达到世界先进水平,钢铁和轻合金材料全面实现绿色、循环制造,基本建成新材料产业创新体系。能源石化用钢,海洋工程用钢,交通运输用钢,基础零部件用钢,超超临界电站用钢,航空用铝合金、钛合金等关键材料,基本能够满足国民经济、国家安全、社会可持续发展的需求,支撑“制造强国”战略,初步完成由材料生产大国向材料制造强国的战略性转变。
2. 2035 年目标
围绕经济和社会发展对材料智能化、绿色化、个性化的需求,依靠材料基因组技术,以开发新型合金为重点,构建金属材料的持续创新体系,实现金属材料的智能制造,支撑产业整体达到世界先进水平。着力开发一批适合3D 打印等技术的钢铁、铝、镁、钛等金属材料;突破一批金属近净加工技术;应用一批创新性的金属冶炼制造工艺,完成金属材料产业工程技术由“跟跑”“并行”到“领跑”的跨越,成为引领世界金属材料技术革命的重要力量。
五、高性能轻合金材料重大工程
(一)需求与必要性
轻合金材料包括铝合金、镁合金、钛合金,占全部有色金属使用总量的60%以上,在国民经济中占有重要地位。重点是围绕“陆上三大交通运输工具”——包括轨道交通高速列车和货运与煤运车、公路运输厢式货车和半挂车、公路交通乘用车的轻量化制造,实现降低能耗和减少排放污染的需求,以及以海洋石油钻探、海水淡化和特种船舶为代表的“海洋工程重大装备”制造需求,开展系列新型轻合金材料及其制备加工成套技术、应用技术的创新攻关。支撑我国交通运输业每年减少燃油消耗100万吨及相应的大气污染排放降低,同时带动行业的产品结构向高技术含量、高附加值方向发展,创造显著的经济和社会效益,使我国民用轻合金材料与加工技术全面迈入世界强国之列。
(二)工 程 任 务
形成年产 30万~40万吨高精度快速时效响应型铝合金薄板、1500万~2000万件乘用车覆盖件和框架件的生产制造产业,满足100 万~150 万辆乘用车的轻量化车体制造需求;形成年产 1万~2万吨高耐腐蚀铝合金板材、10万件铝合金精密管材的生产制造产业,满足我国海洋石油钻探装备和特种船舶发展的需求;形成年产 20万~30万吨大断面复杂截面铝合金型材、50万~60万吨铝合金轧制板材和预拉伸厚板及其深加工制品的生产制造产业,满足 10 万~15 万辆厢式货车和半挂车轻量化车体、1万~1.5万辆高速列车和货运车及煤运车轻量化车体的制造需求。创建高性能兼高品质镁合金压铸件、高性能变形镁合金加工材的生产制造产业,满足年产100万~150万辆乘用车的车体零部件制造需求。大卷重、高精度、低残余应力钛带和焊管生产制造产业满足海水淡化装备产业与工程发展的需求;高性能大直径钛合金管材和型材的生产制造产业,满足我国海洋石油钻探装备和特种船舶发展的需求。
(三)工程目标与效果
2025年
汽车覆盖件与框架件制造用高精度快速时效响应型铝合金薄板成套生产工艺技术;汽车动力系统和底盘制造用高性能铝合金精密锻件和高品质压铸件生产工艺技术;汽车零部件用高性能高品质镁合金压铸件和变形加工材生产工艺技术;海洋石油工程和特种船舶用高性能大直径钛合金管材和型材、铝合金精密管材和高耐腐蚀板材的生产工艺技术;水淡化工程用高精度钛焊管及大卷重、高精度、低残余应力钛带的成套生产工艺技术;轨道交通和货运/ 煤运车辆、公路货运和乘用车辆、特种船舶用铝合金 /钛合金 /镁合金的大型、复杂精密结构件成型制造与残余应力消减技术,复杂焊接加工、异质金属间的连接和接头腐蚀控制技术,表面强化及防腐处理技术。
2035年
形成“合金元素原子间的交互作用机制及强化相设计”理论;“多尺度范围的第二相——界面耦合强化”理论;“制备与加工全过程中的微观组织演化规律与控制”理论;基于“高通量计算 – 海量数据库、快速实验检测评价”相结合的材料计算设计与制备加工过程模拟仿真。
免责声明:本网站所转载的文字、图片与视频资料版权归原创作者所有,如果涉及侵权,请第一时间联系本网删除。
相关文章
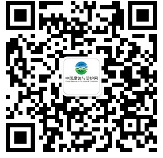
官方微信
《中国腐蚀与防护网电子期刊》征订启事
- 投稿联系:编辑部
- 电话:010-62316606-806
- 邮箱:fsfhzy666@163.com
- 中国腐蚀与防护网官方QQ群:140808414
点击排行
PPT新闻
“海洋金属”——钛合金在舰船的
点击数:7804
腐蚀与“海上丝绸之路”
点击数:6225