俄乌战争背后,莫斯科的眼泪
引爆在东欧的一场战争,牵动着数十亿人的心神。
各种媒体充斥着相关新闻,拜登又出台了什么制裁政策,前线战况激烈,俄乌之间的谈判进展如何……
看客们或义愤填膺,或热血沸腾,或冷眼旁观。
更多真实的,如你我这般普通人的故事,却往往看不到。基辅出口,出现长达数公里的堵塞,人们正在逃离首都。有人跪在街头,向上帝乞求和平。边境线上,多达104万乌克兰难民拥挤着,且正以平均每天新增14万人的速度迅速增加。
战火就燃在自己的家园,乌克兰人民当然是最凄惨的。
只是有些媒体,一味宣扬乌克兰方面的伤亡,反过来突出俄罗斯的罪恶。
导致很少有人关注到,在战争中,俄罗斯普通人的日子,同样不好过。没有人比当地的老百姓更清楚自己的处境。也没人是傻子。因为西方的制裁,卢布在国际市场一度暴跌30%,相当于俄罗斯平民手中的现金资产,直接蒸发掉30%。就算加息到20%,也于事无补。把钱放在银行,贬值的速度超过发钱的速度,越来越亏。
别说普京,耶稣来了也罩不住。
无论是哪一国的平民,都是受害者。所以现在,有一个最现实的问题,俄乌之战到底要持续多久?但是这个问题并不是你我小老百姓所能解决和决定的。所以,今天我们不多聊战争啦,随小编来了解一些军工用材吧。
一、常规武器用钢
常规武器用钢 (steels for conventional weapons) 是用于制造枪、炮、坦克和战术导弹等武器主要部件的合金结构钢的总称。现代化的常规武器都具有火力威力大和灵活机动性好的特点,对枪、炮钢的技术要求取决于它们的射击参量(如火炮的瞠压,炮弹的初速度,射击速度,射程等)和炮弹的炸裂参量(如炸片的有效数量,炸片速度等),而坦克和战术导弹用钢则取决于武器的自重以及从一个地方运动到另一个地方所需要的时间。设计制造各类常规武器主要部件所选用的钢材,必须满足这些技术要求。
常规武器用钢主要包括厚壁大口径火炮身管用钢、炮弹弹体用钢、均质装甲钢和导弹发动机壳体用钢。
厚壁大口径火炮身管用钢
在射击时,火炮身管承受着很复杂的应力。由于要经受射击参量(如炮弹初速度可达500~3000m/s),高温、高压、高速火药气体对管壁的作用和冲击,炮弹对管壁的挤压,形成了很高的切向应力;而且身管表面经受着交替地快速加热(以10℃/s的加热速率使温度升高到710℃以上)和快速冷却(10℃/s),使钢的组织产生了奥氏体和马氏体的反复相变,形成了很大的组织应力和热梯度。苛刻的服役条件对火炮身管用钢提出了很高的要求,所以炮钢应具有如下性能:高横向比例极限σp或高屈服强度σ0.1,在射击时不产生永久变形;高横向室温和-40℃的低温韧性,在射击时不发生脆性断裂;低裂纹扩展速率,高的周期疲劳次数,从而具有很长的使用寿命。为使身管用钢在射击条件下不软化胀膛,还应具有高的高温强度。
为保证大口径火炮身管用钢良好的综合性能,在合金设计上,世界各国普遍都采用镍铬钼钒系列(见表1)。为保证钢的淬透性和改善钢的低温韧性,都添加较高的镍,通常为3.O%~3.5%。但从表1可看出,美国的155mm身管用钢与175mm身管用钢相比,在合金设计上是有差异的。155mm身管用钢的碳含量约降低了O.05%,这有利于韧性的提高;铬含量约降低了O.6%,有利于细化晶粒提高韧性;钒含量约增加O.10%,对韧性是不利的。
厚壁大口径火炮身管用钢具有高横向比例极限或高屈服强度和良好的低温韧性(见表2)。为保证这些性能,在热处理工艺中,美国175mm身管用钢和中国相应的身管用钢都采用高温正火加低温淬火加回火的热处理工艺,使钢的成分和组织均匀化,进一步细化晶粒,以获得良好的综合力学性能。表2大口径火炮身管用钢的力学性能。
炮弹弹体用钢
为保证炮弹具有很大的杀伤威力,因此炮弹弹体用钢,通常都采用高强度、低韧性的钢。在合金设计中,通常都采用高碳、高锰、高硅和其他脆性元素,使钢中碳化物数量增加、回火脆性倾向增大、奥氏体晶粒粗大化,以保证弹体钢具有很高的破片率,从而增大杀伤威力。弹体钢的化学成分示于表3,力学性能示于表4。
均质装甲钢
在战争中装甲钢将受到不同距离、口径、速度的各种弹丸的冲击与爆炸物的轰击,瞬间承受巨大的动能、破片、冲击波和聚能效应,使装甲钢在高温、高压和高速作用下发生塑性变形、破裂、甚至部分熔化或气化。因此要求装甲钢具有良好的抗弹性能。装甲钢的抗弹性能主要是指其抗弹丸的侵彻能力、抗冲击能力和抗崩落能力。抗侵彻能力是指在一定装甲厚度和弹丸着角的条件下,装甲钢不被击穿的最大动能弹着速或能抵御某种标准破甲弹的能力。一般认为它随着装甲材料的硬度和弹性模量的提高而提高。抗冲能力是指在弹丸的高速冲击下,装甲不发生开裂和崩落等损伤的能力。它与材料的韧性和强度有关。所以要求装甲钢具有良好的抗侵彻、抗冲击和抗崩落等能力,即要求装甲钢应具有高强度和良好的韧性,以提高钢的抗弹性能。在制造装甲车辆的过程中,还要求装甲钢具有良好的冷热加工性能和焊接性能。典型的均质装甲钢的化学成分和力学性能列于表5和表6。
导弹发动机壳体用钢
为减轻导弹弹体的重量,要求壳体用钢应具有高的比强度,以增大火箭的推力;为防止低应力破坏,要求壳体用钢应具有高的断裂韧性;为降低制造成本,要求壳体用钢应具有良好的加工性能和焊接性能。
导弹发动机壳体用钢的合金设计,通常都采用中碳的镍、铬、钼、钒系列(见表7)。碳可提高钢的强度,但对钢的塑性和韧性有害,在保证强度的前提下,其含量应尽量低,一般为O.3%~O.4%;为保证钢的淬透性,应加入适量的镍、铬和钼;由于铬在钢中能生成Cr7C3碳化物,降低了最大阻力的温度(或二次硬化温度),为防止软化的产生,钢中的铬含量应受到限制。力学性能示于表8。从表8可以看出,在热处理过程中,对硅、钼含量较高的钢种,可采用中温回火,对硅、钼含量较低的钢种,可采用低温回火。
冶炼工艺
制造现代化常规武器主要构件所选用的钢材,基本上都是高强度钢或超高强度钢。这两类钢都易于出现低温(-40℃)脆化和缺口脆化。提高钢的纯净度,即降低钢中的硫、磷含量,减少钢中非金属夹杂物和气体含量,是减轻这两种脆化倾向和提高钢的韧性的有效途径。结构材料冶金工艺的发展,总是在解决“强度高、韧性低”的矛盾中前进的。特种冶金的出现,适应了这种要求。美国175mm加农炮身管用钢,采用真空碳脱氧工艺冶炼。英国挑战者坦克装备的120mm线膛炮采用电渣重熔法冶炼。
20世纪50年代,采用碱性平炉双联法冶炼了加农炮身管;70年代,采用电渣重熔法冶炼了加榴炮身管;80年代中期,采用碱性电炉加喷粉处理加电渣重熔法冶炼了加农炮身管;坦克炮身管是用碱性电炉加喷粉处理加真空脱气工艺冶炼的。超高强度钢,通常采用真空感应炉加真空白耗炉的双真空冶炼法冶炼。均质装甲钢,最近采用电炉加钢包精炼炉冶炼,使钢中的氧含量达到20×10、氢含量1.5×10、氮含量56×10。
发展趋势
随着现代冶金技术的发展,常规武器用钢得到了迅速的发展。
厚壁大口径火炮身管用钢服役条件非常苛刻,要承受高速、高温、高压、急冷急热、反复交变载荷等的作用,因此要求身管用钢必须具有高比例极限郎或高屈服强度和良好的冲击韧性。为达到这个目的,厚壁大口径火炮身管用钢正向追求良好综合性能方向发展,主要发展有两个。一是以美国为代表。开发高强度身管用钢,最高屈服强度σ0.1已达1240~1310MPa,但该钢的冲击韧性比较低,仅为8.3J;二是以中国为代表,重视开发强韧性匹配好的身管用钢,把屈服强度适当降低到980~1120MPa的水平。通过降低钢中碳含量和提高镍含量,提高了身管用钢的韧性,获得了良好的综合性能,延长了身管用钢的使用寿命。
均质装甲钢的最新发展主要表现在以下几个方面。在合金设计思想上,世界各国普遍采用多元少量的合金设计方法,开发中、低碳的低合金装甲钢,不但改善了钢的工艺性能,也降低了钢的生产和加工成本;在钢的冶炼技术上,普遍采用高纯化冶炼技术,大幅度降低钢中的硫和磷,如炉外精炼、喷射冶金和电渣重熔等,其中以电渣重熔法采用的最多。美国和前苏联采用电渣重熔法冶炼的装甲钢,其抗穿甲弹的侵彻能力可提高30%~40%。并已分别列入本国的军标中;在轧制工艺上,普遍采用控制轧制和控制冷却技术生产装甲钢,进一步降低了钢的焊接碳当量,改善了钢的焊接工艺性,降低了生产成本;在装甲类型上,普遍采用复合装甲。作为复合装甲重要组成部分的均质装甲钢,正向中、薄板方向发展,一般使用厚度为35mm以下,最厚不超过50mm。为提高装甲的防护水平,美国研制成功了贫铀复合装甲,已在美国M1A1型主战坦克上应用,具有很高的防护水平,防穿甲大于600mm,防破甲大于130mm,成为世界上最先进的复合装甲之一。因此,积极开展贫铀装甲材料的研究是装甲钢发展的另一个新方向。炮弹弹体用钢,目前正在向高强度(抗拉强度高于1000~1400MPa)、高破片率和低韧性方向发展,以不断提高炮弹的杀伤威力和杀伤面积。弹体钢韧性低、脆性大,可大幅度提高有效破片率,进而提高杀伤威力。但是,弹体钢的低韧性也是有限度的,至少要满足弹体在制造、运输、储存和安全使用等方面的要求。因此,炮弹弹体钢的高强度、高破片率和低韧性的合理匹配,也是重点的研究方向之一。
二、坦克材料系列 —— 工作于最恶劣环境的炮钢
坦克的任务是打击2000米以外的装甲,因为目标一般为移动目标,采用平直低伸的弹道,极高的初速度,眨眼瞬间已经击穿几公里外的目标。想把炮弹在瞬间弹到几公里以外,需要巨大的爆炸能量,而这一巨大能量作用于炮弹的同时也作用于炮筒上,炮筒必须把这一巨大的爆炸所产生的一切压力,热量都要默默承受。
坦克炮管的工作时间只有3秒,是指把所有炮管寿命内所发射的炮弹从引爆到发射出去的时间加到一起大概真的就几秒时间,所以您大概可以从侧面理解为什么说“工作于最恶劣环境的炮钢”,下面就从以下几个方面聊一下,炮管在其短暂的寿命瞬间都经历了些什么?及如何从材料的加工角度让炮管很好的完成其短暂但却重要的一生?
1、膛压有多多大?
2、人多力量大么?—— 身管自紧的作用
01 膛压有多多大?
多大的膛压能把炮弹瞬间弹到几公里之外,在网上很容易找到几知名现代主战坦克的数据:豹2主战坦克安装莱茵金属公司研制的120mm滑膛炮,炮管长5.3m,设计膛压为710MPa,实际使用膛压为500MPa。
500MPa可能您没有直观的认识,先解释一下M Pa 这个单位,M为兆,即一百万,Pa为压强单位,每平米一个牛顿的力,一个牛顿力约为0.1公斤重量产生的力,那个500MPa这个压强就是将5千万公斤重量均布在1平方米上,或5吨重量均布在1平方厘米上,约为一头大象压在1平方厘米上产生的力的效果。
可以再换一个角度解释一下坦克膛压有多大,我们在一般平原地区日常生活承受的大气压,称之为一个标准大气压,约为0.10133MPa。潜水艇每下潜10米,承受的压力增加一个标准大气压,美国洛杉矶潜艇能够下潜的极限深度为530米,也就是53个标准大气压,即不足5.4兆帕。现在对于坦克炮几百兆帕的膛压是不是有了一个大致概念。
下面您可能有进一步疑问,那么这么大的工作压强需要炮钢拥有多大的强度才能消化的了呢?我们常见的钢铁为Q235,Q355,数字代表强度,是否可以作为炮钢呢?
我们需要计算在炮管承受500MPa压强时,在炮管内部产生的等效应力为多大?在网上找到厚壁圆筒应力分析方法,首先介绍一下为什么用厚壁,材料力学为计算的方便定义外径/内径比值大于1.1~1.2时称为厚壁,而小于1.1称为薄壁,坦克炮管为承受那么大的压强肯定比较厚,适合用厚壁圆筒应力分析方法。
图 2 厚壁圆筒受压示意
厚壁圆筒内压为Pi,外压为Po,分析圆筒壁内任一点处的应力,用相距dr的两个同心圆柱面,互成dθ角的两个相邻纵截面及相距dz的两个水平面截取一个微小扇形六面体所受应力,如图2所示,求出径向应力σr,、周向应力σθ ,和轴向应力σz,结果如图3所示。
图 3 厚壁圆筒管壁内应力趋势示意图
周向应力σθ 及轴向应力σz均为拉应力(正值),径向应力σr为压应力(负值)。周向应力σθ 在内壁处最大,外壁处最小。径向应力内壁处为-Pi,随着r增加,径向应力绝对值逐渐减小,在外壁处σr=0;轴向应力σz为一常量,沿壁厚均匀分布。我们可以看出内壁处的径向应力,及周向应力都是最大的,耐轴向应力为常值,所以可以得出内壁处的等效应力肯定也是最大的,等效应力是材料力学中将三个方向的正应力和切应力折算成一个等效应力,再用这一个等效应力按材料强度选择材料。
那么到底等效应力有多少大呢,如果按内压为300~550MPa,而忽略较小的外压,按壁厚系数k=1.5和2分别计算一下。计算结果如下表1所示。当壁厚系数k为2时,即外径为内径的2倍,当内压为300MPa时,约为二战苏联坦克T-62的内压,此内压所引起的内壁等效应力为693MPa;当内压增至500MPa时,引起的内壁等效应力为1155MPa,我们常见Q355钢的屈服强度为355MPa,而500MPa膛压所产生的应力约为Q355屈服强度的3-4倍。
表 1 不同膛压及壁厚系数时内壁应力值
02 人多力量大么?—— 身管自紧的作用
人多力量大的么?答案大家估计都知道,因为我们自古有“滥竽充数”的典故,这里从另一个角度来聊一下这个问题,答案也可能是人多可能会增加一点力量,但力量的增加与人数的增加并不成正比,因为增加的人不在其位,可能对事情贡献的程度不如在位人那么大。
拿我们本文的主角炮管来说,当内部受装药爆炸压力时,炮管壁上所受的应力并不均匀,我们在上一节的计算结果可以看出,内壁处的压力是最大,而随着位置往外推移,所受的应力是下降的,而到最外壁时应力达到最小。用有限元做个简单的模拟,内部膛压设为500MPa,内径设为120mm,壁厚系数为2时,所得到的等效应力结果为图4所示,红色应力最大,之后到黄绿逐渐减小,再到蓝色应力最小。
图 4 炮管受力云图
这种情况下的结果是,最前沿所受的压力可能已经大到超出其极限而无法承受,但后方的却没有体会到有多大的压力,而产生这样结果的原因就是不在其位,我们的古话“不在其位,不谋其政”,从这一结果也可以得到一种阐释,你不在其位,你受到压力的程度及你所拥有的资源都无法使你很好的解决问题。
那么我们会想到新的问题,人多真的就没用了么?当然不是,对于炮管有一种技术叫身管自紧技术,可以让外壁材料贡献更多的力量。通过机械或液压的方法对其膛内施以高压,那么通过前述介绍我们知道炮管壁内部受力大,而外部受力小,而所加的力掌握在使内壁产生塑性变形(图中Plastic Zone 区域)不开裂,但使外壁保留一部分在弹性变形范围(图中Elastic Return Zone区域)。这里解释一下当材料受力由小到大,先是产生弹性变形,就像橡皮筋一样弹性变形不是永久的变形泄力后会恢复,当力再增加就会产生塑性变形,塑性变形是永久变形,再增加力就会拉断。这样当自紧过程结束后,内壁由于产生的是塑性变形比初始时增大了,而外壁产生的是弹性变形要恢复初始大小但内壁变大了不让外壁恢复,这样炮管内壁产生残余压应力(High compressive hoop stress),外壁产生残余拉应力(Moderate tensile hoop stress)。
图 5 身管自紧过程及之后的应力云图
经过自紧的炮管在承受发射产生的高膛压时,炮管内壁的残留压应力将部分抵消火药爆炸带来的巨大拉应力,从而改善火炮内层金属的受力状况。但对于炮管来说,身管自紧技术所带来的好处却不仅仅是改善受力情况:
提高了炮管的强度,身管自紧技术,相当于使炮管壁受力更加均匀,壁内外一齐抵抗外力,相当于增加了炮管的强度。炮管强度增加,意味着所能承受的压力也会增加。有资料表明,管道最高可达1.8倍原来压力。
提高了炮管的寿命,正常情况下炮管是疲劳损伤,就是刚开始是微小裂纹,之后在外力作用下微裂纹一点一点扩张成宏观裂纹,最后至断裂。产生裂纹相当于裂口要张开,受拉力会使裂纹进一步扩展,而压力使裂纹闭合的趋势。而在受力最恶劣的内壁由于身管自紧残留了压应力,在一定程度上减缓裂纹扩展的速度,提高了炮管的寿命。
可减少炮管壁厚,前文我们重点讲了,坦克不单要求有很强的火力,而且要平衡其机动性能,即在提高炮口能量、射击精度和使用寿命的基础上,要尽可能减轻火炮重量和缩小火炮尺寸。身管自紧技术可提高炮管的强度,为一定程度上减轻炮管重量提供了可能。
身管自紧工艺广泛应用于先进的工业、汽车、航空航天和国防系统,以增加操作压力;应用自增强工艺来提高零件的疲劳寿命是必要的。该技术通常用于制造高压泵缸、柴油发动机燃油喷射系统以及舰船和坦克炮筒。同样,该工艺也用于油气井中管状部件的膨胀。
在现实工程中,还有一些预应力的钢构与身管自紧技术原理相似,预应力钢结构(prestressed steel structure)是指在结构工作以前,对钢结构或构件用特定的方法预加初应力,其应力符号与工作荷载引起的应力符号相反;当工作施加荷载时,预加的初始应力可先抵消一部分工作载荷,这样可使构件承受更大的工作载荷,以保证结构的安全和正常使用。
总结
炮管在炮弹发射时承受巨大的膛压,高达500MPa,在管壁内引起的应力达1000MPa以上,约是普通钢铁强度的3-4倍。
身管自紧工艺是一种预应力技术,可显著提升炮管承压能力,还可以显著提升炮管疲劳寿命。
预应力技术在现实的工程钢构中也有应用,同样可提升钢构的承载能力。
上面介绍了坦克炮发射时的膛压非常大,对炮管壁产生巨大的冲击力,但这只是炮钢恶劣工况之一,本文接着聊火炮身管的另一个严峻挑战,高温烧蚀及磨损,及如何提高炮管耐烧蚀性能。之后总结火炮这种恶劣的工作环境对身管材料的要求及炮钢的发展。最后简要介绍炮管如何在带着裂纹工作时保证可靠性。
1. 炮管的烧蚀
2. 如何提高炮管耐烧蚀性能
3. 炮钢的材料性能要求及发展
4. 轻伤不下火线—— 带着裂纹工作的炮管
01 炮管的烧蚀
自从火炮作为兵器出现以来,人们就不断改进其性能,以期将更重的炮弹更精准地投射到更远的地方,为此,越来越多的发射药被装进炮膛。这就使得射击时火炮身管承受到越来越严重的火药气体热作用和物理化学作用、高速流动火药气体的冲刷以及弹丸对膛壁的磨损作用。大威力火炮身管的烧蚀磨损现象愈来愈严重,已成为降低火炮弹道性能、导致身管报废的重要因素。
火炮身管烧蚀磨损是一种复合的作用机制,由于发射弹丸引起的热、机械、化学等诸多因素同时作用于膛面所产生的一种使膛面损坏的十分复杂的现象。
1.1 火药气体的热烧蚀
在影响火炮身管内膛烧蚀磨损的诸多因素中,热是起主导的、控制作用的因素。身管内壁的机械强度由于受到内膛温升的影响,温度升高,机械强度急剧下降,内膛烧蚀磨损量就越大。在不采用缓蚀添加剂时,内膛表面温度和火焰温度成正比。射击时,发射药燃烧温度高达2500一3700K。烧蚀速度随发射药火焰温度升高而增加。
温度是引起内膛表面开裂的根本原因,火炮射击时,在达到最大膛压的同时,内膛最高温度可达1270K,而表面以下0.5m处,温度只有50K,这种温度的不均匀会造成极大的动态压应力。发射后内膛冷却过程中则产生动态拉应力,这种应力循环,无论是对非镀铬身管还是镀铬身管,均是造成膛面裂纹产生的直接诱因。在后续的发射过程中,裂纹之间会产生贯通,形成烧蚀坑,进而会造成大面积的烧蚀磨损。所以,火药气体的热烧蚀对身管内膛的破坏起着重要的作用。同时,由温度引起的热应力也是导致金属疲劳的内在原因,直接影响身管的疲劳寿命。
图 1 炮管内的热裂纹
1.2 火药气体的化学烧蚀
火炮发射时会产生高温、高压,炮管内膛会产生一系列化学反应,进一步加剧了火炮身管内膛的烧蚀磨损。无论是使用高火焰温度的双基发射药,还是低火焰温度的单基发射药,火炮身管内膛表面都会形成FeO、FeC、FeN等一些铁基化合物以及奥氏体、马氏体等等。这些产物的熔点比钢低250-300K,会在低于钢熔点下熔化,并被火药气体冲刷掉。
此外,火药气体中大量的C元素会增加内膛表面的C浓度,降低了钢的固相线温度和导热性,导致了钢的剪切强度降低以及在较低温度下便会熔化,被火药气体冲刷掉。
1.3 炮管的机械磨损
由于火药气体的冲刷,炮膛直径不断扩大。在阴线部位形成纵向的不断加宽加深的裂纹网,在阳线的顶部和导转侧受到弹带的机械磨损径向尺寸扩大。沿着弹丸前进方向运动的气流夹带着液态和固态生成物,还包括未燃完的发射药粒子,由于它们的速度很高,对膛壁的机械磨损也很大。此外,弹丸在膛内运动时,弹带及弹体都会对炮膛内壁表面产生挤压力和摩擦力,加剧了炮膛的磨损。
02 如何提高炮管耐烧蚀性能
降低炮管烧蚀磨损的技术可从两方面着手,一是从改善发射药的热量散发角度考虑,不是本文观注的重点;我们主要讨论如何从材料角度来提升炮管内膛的耐烧蚀磨损。主要有化学镀铬,激光淬火强化,身管内膛涂层等技术。
2.1 身管镀铬技术
镀铬技术是目前国内外唯一能在生产上大规模用于防止炮管内膛烧蚀磨损的方法。美、英、德、瑞士等国已在多种火炮身管上镀铬。镀铬层虽具有硬度高、耐磨性好、光反射性强的优点,但是脆性大,易脱落,在经受冲击负荷的情况下更为明显,特别是膛口部阴阳线的交界处铬层脱落严重。
2.2 激光淬火强化
随着科技的发展,用激光技术处理镀铬身管成为新一轮研究的热点,激光淬火强化技术从炮膛外激光器发出的高能密度激光束,经置于炮膛内的反射镜转向,快速照射到火炮身管内膛表面(图2),从而使炮膛被照射处瞬间吸收光能并立即转化成热能,温度急剧上升到相变温度以上、熔点温度以下,从而发生加热相变,材料组织变为奥氏体:激光束离开后,该处温度急速下降,发生冷却相变。淬火后材料的组织主要为细化马氏体M,它不仅硬度高,还有利于阻碍裂纹扩展。
对内膛镀铬的身管,内膛铬层经过激光强化后,铬层表面原始裂纹消失、临近铬层的基体金属硬度增加,提高了其抗热冲击性能和基体的防热能力,且由于热处理获得的铁素体再结晶组织而提高了延性,铬层不易脱落。
图 2 激光淬火强化技术
2.3 内膛涂层技术
涂层复合技术是一种能很好的解决炮管整体具有良好综合性,但内表面又具有优异的抗烧蚀磨损能力的技术,现代科技较发达,涂层方法也很多,如化学方法,热方法,爆炸方法,磁控溅射等。
热方法即热熔覆技术,是广泛采用的一种技术,是采用能量非常集中的热源来熔化金属粉末并熔覆到炮管内壁的过程,热源主要有激光,等离子,红外等。而熔覆的材料主要是高温合金,如钼,铌,铼,钽。
美国橡树岭国家实验室的红外加工中心利用当今世界上功率最大的“灯”(300kW、10000℃)产生高强度红外能量,直接照射到难熔金属粉末涂层上,在基体材料上形成冶金结合涂层,身管涂层首选材料是钼铼合金类材料。在美国“十字军”项目的相关预研中,开展的身管涂层热循环试验,证实了这种材料在火炮射击时的耐久性。而现有和预研的铬涂层和激光涂层在强热循环实验后,都显示有严重的开裂,相比之下,铼涂层样品没有任何损坏。
美国贝尼特武器实验室目前正在研究磁控溅射镀膜技术在火炮身管上的应用,以取代传统身管镀铬工艺。它既可以在身管上沉积铬,也可以沉积其它难熔金属或合金。
03 炮钢的材料性能要求及发展
3.1 火炮身管材料的要求
上篇文章有一张图片显示坦克炮发射时的情景,就像是发射一枚小火箭一样,从炮筒里喷出几米的火焰。可以想象出炮筒不但承受着巨大的压力,而且承受较高的烈焰。所以对火炮身管材料的要求也极为苛刻:
材料有足够的室温和中温(500~750℃)强度,以保证在高温高压作用下身管不变形
材料应具备较高的常温和-40℃低温韧性,以保证不发生低应力脆断和疲劳破坏
材料应当有一定的化学稳定性和热稳定性,以抵抗大气或火药气体腐蚀
材料应具有较高的回火温度(>500℃),以充分消除炮身内应力减低延迟破坏的危害
良好的机械加工工艺性能,适应大量生产的要求
所以炮管用钢对强度、韧性、耐高温、耐磨损都有非常高的要求,看有人说用炮管钢打造刀具,看这军工要求可想而之用炮钢打刀具那真是妥妥的。
图 3 炮管件
3.2 火炮身管材料发展
火炮的身管材料对火炮的寿命有重要的影响,身管材料的发展大概经历了以下阶段:早期的身管用材料采用铸铁(钢);自第二次世界大战以后,世界各国火炮身管都采用以4335V钢(相当于中国的35CrNi2MoV钢)为代表的中碳Ni-Cr-Mo-V系调质钢;20世纪70年代以来,由于采用电渣重熔工艺,火炮身管用钢的洁净度和性能大幅提高,在此基础上形成了身管用钢ASTM A723(相当于中国的PCrNi3MoVA),并一直沿用至今,是最主要的身管用钢:近年来,人们研究了各种轻质材料身管和涂层,但并未全面推广应用。国内外常用的枪炮身管用钢为中碳Cr-Ni-Mo-V钢,其高性能化的方向是通过提高冶炼洁净度来保证具有足够的韧性,同时根据强度的要求调整铬、钼、钒等二次硬化元素含量。另一方面,为进一步提高强韧性和耐腐蚀性能,国外也开展了超高强度钢AF1410、沉淀硬化不锈钢PH13-8Mo以及奥氏体不锈钢用作身管用的研究工作(AD-A317919),希望将身管用钢从中低合金钢向高合金钢方向发展,但在保证加工性能上存在一定难度。身管用钢的发展趋势是高性能化,包括强度、韧性、耐烧蚀、耐磨损等性能的提高。与此同时,还要具有良好的加工性能,从而保证加工尺度精度以及服役时射击精度。
3.3 火炮身管钢及标准
随着世界材料和工艺技术的不断发展,高强钢以及新型复合材料不断涌现,采用新型材料的火炮身管也在逐渐开发,但炮钢仍然是当今用来制造加农炮、榴弹炮等大口径厚壁火炮身管的主要材料,炮钢的性能水平直接关系到火炮威力及机动性的提高。目前,世界各国的大口径厚壁炮钢基本采用Ni-Cr-Mo-V系中碳低合金钢,这种钢具有较高的淬透性,在淬火和调制处理后获得较好的强度和塑性配合,有较高的抗脆断能力,美国、英国炮钢化学成分见表1。
表 1 美国、英国炮钢化学成分
简单讨论一下炮钢的化学成分:
杂质:P是一种非常影响钢铁韧性的元素,特别是低温韧性。S降低钢铁的塑性。如果你查看一些炮钢的冶炼,经常会看到有提到电渣重熔技术,电渣重熔钢(electroslag remelting)是利用电流通过熔渣时产生的电阻热作为热源进行熔炼的方法。其目的是提高金属纯度,改善铸锭结晶。经电渣重熔的钢,纯度高、含硫低、非金属夹杂物少、钢锭表面光滑、洁净均匀致密、金相组织和化学成分均匀。不是说炮钢非得要用电渣重熔法生产,现代冶炼技术有了十足进步,开发了很多炉外精炼方法生产洁净钢,超净钢。但总之,钢炮对杂质控制是非常严格的,只有这样才能保证炮钢的寿命及可靠性。
Ni: 金属镍是一种非常好用的合金,不但可以提高材料的强度,而且可以改善材料的韧性,所以很多重要、优质的结构用高强度钢材都少不了的元素,如军舰的船板;镍也是不锈钢的重要元素,如304,316奥氏体不锈钢。我国中国镍资源储量少(3.1%)、且镍资源禀赋较差,对外依存度高,所以经常要研制无镍钢。镍资源丰富的,从国家和地区来看,印尼(2100 万吨,占比约 24%)、澳大利亚(2000 万吨,占比约 23%)、巴西(1100 万吨,占比约 12%)等国家镍资源储量居前,资源类型主要为红土镍矿,澳洲兼具红土镍矿和硫化镍矿;但产量方面,2019 年印尼(80 万吨镍金属量)、菲律宾(42 万吨镍金属量)、俄罗斯(27 万吨镍金属量)为前三大镍资源生产国,印尼与菲律宾主产为红土镍矿,俄罗斯则拥有罕见的丰富多金属伴生硫化镍矿,这也是为什么近期俄乌冲击导致镍价大涨的原因。
Mo: 也是一种很好的重要的元素,它一个显著的作用就是保持高温强度的稳定性,所以当高强度材料需要很高的韧性时,一般需要进行高温回火,为在高温回火时保持强度不下降太多,加一些钼,一般0.3%。
火炮身管用钢一般为锻件,主要的标准也一般为军工标准,下面几个代表:
A723/A723M-02 Standard specification for alloy steel forging for high-strengthpressure component application [S]. UnitedStates:ASTM Committee on Standards.2002.
Defence Standard 10-13/Issue 4 Steel Forgings for Guns [S].Britian:Ministryof Defence.8 April 2005.
MIL-S-46119C(MR)Steel Forgings,Tubular Parts for Cannon [S].United States:Military of Refence.26October 1988.
GB1237一91, 炮身管件用钢锻件规范[S]. 国防科学技术工业委员会。1991.
GB5207一2003, 火炮炮身零件用锻件规范[S]. 国防科学技术工业委员会,2003
图 4 炮管锻造
04 轻伤不下火线—— 带着裂纹工作的炮管
看前文介绍可知,炮弹发射产生的高温烧蚀及不均匀温度场造成的拉压应力循环,很快在炮管内表面引起表面裂纹。近代火炮通常在发射100~200发时,即脱离完全弹性变形状态。而在内膛表面不可避免地产生细小裂纹,此后,火炮身管将一直带着裂纹在裂纹扩展过程中进行工作。当裂纹扩展到一定程度后,即迅速进入失稳状态,直至发生断裂。为避免发生严重的炸管事故,需要研制和选用韧性尽可能高的材料制成炮管。
图 5 孔镜下的新旧膛线炮管
对于普通钢构产品的设计,设计人员按照冲击夏比韧性指标来决定材料的韧性是否满足应用,冲击韧性试件是小试件,加工出缺口来引起应力集中,加以高速冲击使裂纹在应力集中处产生并断裂。而对于火炮这一战争中重要的武器,冲击韧性指标的指导就不那么足够及准确了。需要借助断裂力学理论,断裂力学在分析材料力学性能时不但考虑材料内部的应力,而且考虑材料内部的裂纹大小对材料失效的影响,而且断裂力学中的平面应力及平变应变是考虑构件尺寸效应对断裂的影响。今天,低温KIC (断裂韧度值)已列为衡量高强度炮钢低周疲劳性能的重要指标。
断裂力学研究炮钢裂纹的发生、扩展过程,并且重要的是确定裂纹扩展安全门槛值,裂纹超过安全门槛值前是可控,即在每一次炮弹的发射会稍微扩展,但不会自动像玻璃一样一裂到底,而一旦超过门槛值,裂纹就会变为自动扩展直到完全断裂。所以铁匠铺可以打个大门栅栏镰刀斧头之类的冷兵器时代的用品,但对于现代武器必须是建立在高科技积累之上的。图6为裂纹发生、扩展和门槛值的示意图。
图6 随射击发数炮管裂纹发生、扩展和门槛值的示意图
图6中示出初始裂纹出现后,在连续射击过程中裂纹以极低速度扩展。裂纹发展到深度变为4~6mm时,扩展速率急速增加:通常高强度炮钢的裂纹扩展安全门槛值均通过模拟试验及实弹射击确证而定,多分布在4~5m之间。实验过程或服役中的火炮裂纹跟踪和测定问题,已由计算机控制的专用窥膛仪解决。
三、军事工业用新材料大盘点,总结得很全了
一、前言
新材料,又称先进材料(Advanced Materials),是指新近研究成功的和正在研制中的具有优异特性和功能,能满足高技术需求的新型材料。人类历史的发展表明,材料是社会发展的物质基础和先导,而新材料则是社会进步的里程碑。
材料技术一直是世界各国科技发展规划之中的一个十分重要的领域,它与信息技术、生物技术、能源技术一起,被公认为是当今社会及今后相当长时间内总揽人类全局的高技术。材料高技术还是支撑当今人类文明的现代工业关键技术,也是一个国家国防力量最重要的物质基础。国防工业往往是新材料技术成果的优先使用者,新材料技术的研究和开发对国防工业和武器装备的发展起着决定性的作用。
二、军用新材料的战略意义
军用新材料是新一代武器装备的物质基础,也是当今世界军事领域的关键技术。而军用新材料技术则是用于军事领域的新材料技术,是现代精良武器装备的关键,是军用高技术的重要组成部分。世界各国对军用新材料技术的发展给予了高度重视,加速发展军用新材料技术是保持军事领先的重要前提。
三、军用新材料的现状与发展
军用新材料按其用途可分为结构材料和功能材料两大类,主要应用于航空工业、航天工业、兵器工业和船舰工业中。
1、军用结构材料
1.1 铝合金
铝合金一直是军事工业中应用最广泛的金属结构材料。铝合金具有密度低、强度高、加工性能好等特点,作为结构材料,因其加工性能优良,可制成各种截面的型材、管材、高筋板材等,以充分发挥材料的潜力,提高构件刚、强度。所以,铝合金是武器轻量化首选的轻质结构材料。
铝合金在航空工业中主要用于制造飞机的蒙皮、隔框、长梁和珩条等;在航天工业中,铝合金是运载火箭和宇宙飞行器结构件的重要材料,在兵器领域,铝合金已成功地用于步兵战车和装甲运输车上,最近研制的榴弹炮炮架也大量采用了新型铝合金材料。
近年来,铝合金在航空航天业中的用量有所减少,但它仍是军事工业中主要的结构材料之一。铝合金的发展趋势是追求高纯、高强、高韧和耐高温,在军事工业中应用的铝合金主要有铝锂合金、铝铜合金(2000系列)和铝锌镁合金(7000系列)。
新型铝锂合金应用于航空工业中,预测飞机重量将下降8~15%;铝锂合金同样也将成为航天飞行器和薄壁导弹壳体的候选结构材料。随着航空航天业的迅速发展,铝锂合金的研究重点仍然是解决厚度方向的韧性差和降低成本的问题。
1.2镁合金
镁合金作为最轻的工程金属材料,具有比重轻、比强度及比刚度高、阻尼性及导热性好,电磁屏蔽能力强、以及减振性好等一系列独特的性质,极大的满足了航空航天、现代武器装备等军工领域的需求。
镁合金在军工装备上有诸多应用,如坦克座椅骨架、车长镜、炮长镜、变速箱箱体、发动机机滤座、进出水管、空气分配器座、机油泵壳体、水泵壳体、机油热交换器、机油滤清器壳体、气门室罩、呼吸器等车辆零部件;战术防空导弹的支座舱段与副翼蒙皮、壁板、加强框、舵板、隔框等弹箭零部件;歼击机、轰炸机、直升机、运输机、机载雷达、地空导弹、运载火箭、人造卫星等飞船飞行器构件。镁合金重量轻、比强度和刚度好、减振性能好、电磁干扰、屏蔽能力强等特点能满足军工产品对减重、吸噪、减震、防辐射的要求。在航空航天和国防建设中占有十分重要的地位,是飞行器,卫星,导弹,以及战斗机和战车等武器装备所需的关键结构材料。
1.3钛合金
钛合金具有较高的抗拉强度(441~1470MPa),较低的密度(4.5g/cm3),优良的抗腐蚀性能和在300~550℃温度下有一定的高温持久强度和很好的低温冲击韧性,是一种理想的轻质结构材料。钛合金具有超塑性的功能特点,采用超塑成形-扩散连接技术,可以以很少的能量消耗和材料消耗将合金制成形状复杂和尺寸精密的制品。
钛合金在航空工业中的应用主要是制作飞机的机身结构件、起落架、支撑梁、发动机压气机盘、叶片和接头等;在航天工业中,钛合金主要用来制作承力构件、框架、气瓶、压力容器、涡轮泵壳、固体火箭发动机壳体及喷管等零部件。50年代初,在一些军用飞机上开始使用工业纯钛制造后机身的隔热板、机尾罩、减速板等结构件;60年代,钛合金在飞机结构上的应用扩大到襟翼滑轧、承力隔框、起落架梁等主要受力结构中;70年代以来,钛合金在军用飞机和发动机中的用量迅速增加,从战斗机扩大到军用大型轰炸机和运输机,它在F14和F15飞机上的用量占结构重量的25%,在F100和TF39发动机上的用量分别达到25%和33%;80年代以后,钛合金材料和工艺技术达到了进一步发展,一架B1B飞机需要90402公斤钛材。现有的航空航天用钛合金中,应用最广泛的是多用途的a+b型Ti-6Al-4V合金。近年来,西方和俄罗斯相继研究出两种新型钛合金,它们分别是高强高韧可焊及成形性良好的钛合金和高温高强阻燃钛合金,这两种先进钛合金在未来的航空航天业中具有良好的应用前景。
随着现代战争的发展,陆军部队需求具有威力大、射程远、精度高、有快速反应能力的多功能的先进加榴炮系统。先进加榴炮系统的关键技术之一是新材料技术。自行火炮炮塔、构件、轻金属装甲车用材料的轻量化是武器发展的必然趋势。在保证动态与防护的前提下,钛合金在陆军武器上有着广泛的应用。155火炮制退器采用钛合金后不仅可以减轻重量,还可以减少火炮身管因重力引起的变形,有效地提高了射击精度;在主战坦克及直升机-反坦克多用途导弹上的一些形状复杂的构件可用钛合金制造,这既能满足产品的性能要求又可减少部件的加工费用。
在过去相当长的时间里,钛合金由于制造成本昂贵,应用受到了极大的限制。近年来,世界各国正在积极开发低成本的钛合金,在降低成本的同时,还要提高钛合金的性能。在我国,钛合金的制造成本还比较高,随着钛合金用量的逐渐增大,寻求较低的制造成本是发展钛合金的必然趋势。
1.4 复合材料
先进复合材料是比通用复合材料有更高综合性能的新型材料,它包括树脂基复合材料、金属基复合材料、陶瓷基复合材料和碳基复合材料等,它在军事工业的发展中起着举足轻重的作用。先进复合材料具有高的比强度、高的比模量、耐烧蚀、抗侵蚀、抗核、抗粒子云、透波、吸波、隐身、抗高速撞击等一系列优点,是国防工业发展中最重要的一类工程材料。
1.4.1 树脂基复合材料
树脂基复合材料具有良好的成形工艺性、高的比强度、高的比模量、低的密度、抗疲劳性、减震性、耐化学腐蚀性、良好的介电性能、较低的热导率等特点,广泛应用于军事工业中。树脂基复合材料可分为热固性和热塑性两类。热固性树脂基复合材料是以各种热固性树脂为基体,加入各种增强纤维复合而成的一类复合材料;而热塑性树脂则是一类线性高分子化合物,它可以溶解在溶剂中,也可以在加热时软化和熔融变成粘性液体,冷却后硬化成为固体。树脂基复合材料具有优异的综合性能,制备工艺容易实现,原料丰富。在航空工业中,树脂基复合材料用于制造飞机机翼、机身、鸭翼、平尾和发动机外涵道;在航天领域,树脂基复合材料不仅是方向舵、雷达、进气道的重要材料,而且可以制造固体火箭发动机燃烧室的绝热壳体,也可用作发动机喷管的烧蚀防热材料。近年来研制的新型氰酸树脂复合材料具有耐湿性强,微波介电性能佳,尺寸稳定性好等优点,广泛用于制作宇航结构件、飞机的主次承力结构件和雷达天线罩。
1.4.2金属基复合材料
金属基复合材料具有高的比强度、高的比模量、良好的高温性能、低的热膨胀系数、良好的尺寸稳定性、优异的导电导热性在军事工业中得到了广泛的应用。铝、镁、钛是金属基复合材料的主要基体,而增强材料一般可分为纤维、颗粒和晶须三类,其中颗粒增强铝基复合材料已进入型号验证,如用于F-16战斗机作为腹鳍代替铝合金,其刚度和寿命大幅度提高。碳纤维增强铝、镁基复合材料在具有高比强度的同时,还有接近于零的热膨胀系数和良好的尺寸稳定性,成功地用于制作人造卫星支架、L频带平面天线、空间望远镜、人造卫星抛物面天线等;碳化硅颗粒增强铝基复合材料具有良好的高温性能和抗磨损的特点,可用于制作火箭、导弹构件,红外及激光制导系统构件,精密航空电子器件等;碳化硅纤维增强钛基复合材料具有良好的耐高温和抗氧化性能,是高推重比发动机的理想结构材料,目前已进入先进发动机的试车阶段。在兵器工业领域,金属基复合材料可用于大口径尾翼稳定脱壳穿甲弹弹托,反直升机 / 反坦克多用途导弹固体发动机壳体等零部件,以此来减轻战斗部重量,提高作战能力。
1.4.3 陶瓷基复合材料
陶瓷基复合材料是以纤维、晶须或颗粒为增强体,与陶瓷基体通过一定的复合工艺结合在一起组成的材料的总称,由此可见,陶瓷基复合材料是在陶瓷基体中引入第二相组元构成的多相材料,它克服了陶瓷材料固有的脆性,已成为当前材料科学研究中最为活跃的一个方面。陶瓷基复合材料具有密度低、比强度高、热机械性能和抗热震冲击性能好的特点,是未来军事工业发展的关键支撑材料之一。陶瓷材料的高温性能虽好,但其脆性大。改善陶瓷材料脆性的方法包括相变增韧、微裂纹增韧、弥散金属增韧和连续纤维增韧等。陶瓷基复合材料主要用于制作飞机燃气涡轮发动机喷嘴阀,它在提高发动机的推重比和降低燃料消耗方面具有重要的作用。
1.4.4 碳-碳复合材料
碳-碳复合材料是由碳纤维增强剂与碳基体组成的复合材料。碳-碳复合材料具有比强度高、抗热震性好、耐烧蚀性强、性能可设计等一系列优点。碳-碳复合材料的发展是和航空航天技术所提出的苛刻要求紧密相关。80年代以来,碳-碳复合材料的研究进入了提高性能和扩大应用的阶段。在军事工业中,碳-碳复合材料最引人注目的应用是航天飞机的抗氧化碳-碳鼻锥帽和机翼前缘,用量最大的碳-碳产品是超音速飞机的刹车片。碳-碳复合材料在宇航方面主要用作烧蚀材料和热结构材料,具体而言,它是用作洲际导弹弹头的鼻锥帽、固体火箭喷管和航天飞机的机翼前缘。目前先进的碳-碳喷管材料密度为1.87~1.97克/厘米3,环向拉伸强度为75~115兆帕。近期研制的远程洲际导弹端头帽几乎都采用了碳-碳复合材料。
随着现代航空技术的发展,飞机装载质量不断增加,飞行着陆速度不断提高,对飞机的紧急制动提出了更高的要求。碳-碳复合材料质量轻、耐高温、吸收能量大、摩擦性能好,用它制作刹车片广泛用于高速军用飞机中。
1.5 超高强度钢
超高强度钢是屈服强度和抗拉强度分别超过1200兆帕和1400兆帕的钢,它是为了满足飞机结构上要求高比强度的材料而研究和开发的。超高强度钢大量用于制造火箭发??压容器和一些常规武器。由于钛合金和复合材料在飞机上应用的扩大,钢在飞机上用量有所减少,但是飞机上的关键承力构件仍采用超高强度钢制造。目前,在国际上有代表性的低合金超高强度钢300M,是典型的飞机起落架用钢。此外,低合金超高强度钢D6AC是典型的固体火箭发动机壳体材料。超高强度钢的发展趋势是在保证超高强度的同时,不断提高韧性和抗应力腐蚀能力。
1.6先进高温合金
高温合金是航空航天动力系统的关键材料。高温合金是在600~1200oC高温下能承受一定应力并具有抗氧化和抗腐蚀能力的合金,它是航空航天发动机涡轮盘的首选材料。按照基体组元的不同,高温合金分为铁基、镍基和钴基三大类。发动机涡轮盘在60 年代前一直是用锻造高温合金制造,典型的牌号有A286和Inconel 718。70年代,美国GE公司采用快速凝固粉末Rene95合金制作了CFM56发动机涡轮盘,大大增加了它的推重比,使用温度显著提高。从此,粉末冶金涡轮盘得以迅速发展。最近美国采用喷射沉积快速凝固工艺制造的高温合金涡轮盘,与粉末高温合金相比,工序简单,成本降低,具有良好的锻造加工性能,是一种有极大发展潜力的制备技术。
1.7 钨合金
钨的熔点在金属中最高,其突出的优点是高熔点带来材料良好的高温强度与耐蚀性,在军事工业特别是武器制造方面表现出了优异的特性。在兵器工业中它主要用于制作各种穿甲弹的战斗部。钨合金通过粉末预处理技术和大变形强化技术,细化了材料的晶粒,拉长了晶粒的取向,以此提高材料的强韧性和侵彻威力。我国研制的主战坦克125Ⅱ型穿甲弹钨芯材料为W-Ni-Fe,采用变密度压坯烧结工艺,平均性能达到抗拉强度1200兆帕,延伸率为15%以上,战技指标为2000米距离击穿600毫米厚均质钢装甲。目前钨合金广泛应用于主战坦克大长径比穿甲弹、中小口径防空穿甲弹和超高速动能穿甲弹用弹芯材料,这使各种穿甲弹具有更为强大的击穿威力。
1.8 金属间化合物
金属间化合物具有长程有序的超点阵结构,保持很强的金属键结合,使它们具有许多特殊的理化性质和力学性能。金属间化合物具有优异的热强性,近年来已成为国内外积极研究的重要的新型高温结构材料。在军事工业中,金属间化合物已被用于制造承受热负荷的零部件上,如美国普奥公司制造了JT90燃气涡轮发动机叶片,美国空军用钛铝制造小型飞机发动机转子叶片等,俄罗斯用钛铝金属间化合物代替耐热合金作活塞顶,大幅度地提高了发动机的性能。在兵器工业领域,坦克发动机增压器涡轮材料为K18镍基高温合金,因其比重大、起动惯量大而影响了坦克的加速性能,应用钛铝金属间化合物及其由氧化铝、碳化硅纤维增强的复合轻质耐热新材料,可以大大改善坦克的起动性能,提高战场上的生存能力。此外,金属间化合物还可用于多种耐热部件,减轻重量,提高可靠性与战技指标。
1.9 结构陶瓷
陶瓷材料是当今世界上发展最快的高技术材料,它已经由单相陶瓷发展到多相复合陶瓷。结构陶瓷材料因其耐高温、低密度、耐磨损及低的热膨胀系数等诸多优异性能,在军事工业中有着良好的应用前景。
近年来,国内外对军用发动机用结构陶瓷进行了内容广泛的研究工作,如发动机增压器小型涡轮已经实用化;美国将陶瓷板镶嵌在活塞顶部,使活塞的使用寿命大幅度提高,同时也提高了发动机的热效率。德国在排气口镶嵌陶瓷构件,提高了排气口的使用效能。国外红外热成像仪上的微型斯特林制冷机活塞套和气缸套用陶瓷材料制造,其寿命长达2000小时;导弹用陀螺仪的动力靠火药燃气供给,但燃气中的火药残渣对陀螺仪有严重损伤,为消除燃气中的残渣并提高导弹的命中精度,需研究适于导弹火药气体在2000oC下工作的陶瓷过滤材料。在兵器工业领域,结构陶瓷广泛应用于主战坦克发动机增压器涡轮、活塞顶、排气口镶嵌块等,是新型武器装备的关键材料。目前,20~30毫米口径机关枪的射频要求达到1200发/分以上,这使炮管的烧蚀极为严重。利用陶瓷的高熔点和高温化学稳定性能有效地抑制了严重的炮管烧蚀,陶瓷材料具有高的抗压和抗蠕变特性,通过合理设计,使陶瓷材料保持三向压缩状态,克服其脆性,保证陶瓷衬管的安全使用。
2 军用功能材料
2.1 光电功能材料
光电功能材料是指在光电子技术中使用的材料,它能将光电结合的信息传输与处理,是现代信息科技的重要组成部分。光电功能材料在军事工业中有着广泛的应用。碲镉汞、锑化铟是红外探测器的重要材料;硫化锌、硒化锌、砷化镓主要用于制作飞行器、导弹以及地面武器装备红外探测系统的窗口、头罩、整流罩等。氟化镁具有较高的透过率、较强的抗雨蚀、抗冲刷能力,它是较好的红外透射材料。激光晶体和激光玻璃是高功率和高能量固体激光器的材料,典型的激光材料有红宝石晶体、掺钕钇铝石榴石、半导体激光材料等。
2.2 贮氢材料
某些过渡簇金属,合金和金属间化合物,由于其特殊的晶格结构的原因,氢原子比较容易透入金属晶格的四面体或八面体间隙位中,形成了金属氢化物,这种材料称为贮氢材料。
在兵器工业中,坦克车辆使用的铅酸蓄电池因容量低、自放电率高而需经常充电,此时维护和搬运十分不便。放电输出功率容易受电池寿命、充电状态和温度的影响,在寒冷的气候条件下,坦克车辆起动速度会显著减慢,甚至不能起动,这样就会影响坦克的作战能力。贮氢合金蓄电池具有能量密度高、耐过充、抗震、低温性能好、寿命长等优点,在未来主战坦克蓄电池发展过程中具有广阔的应用前景。
2.3 阻尼减震材料
阻尼是指一个自由振动的固体即使与外界完全隔离,它的机械性能也会转变为热能的现象。采用高阻尼功能材料的目的是减震降噪。因此阻尼减震材料在军事工业中具有十分重要的意义。
国外金属阻尼材料的应用主要集中在船舶、航空、航天等工业部门。美国海军已采用Mn-Cu高阻尼合金制造潜艇螺旋桨,取得了明显的减震效果。在西方,阻尼材料及技术在武器上的应用研究工作受到了极大的关注,一些发达国家专门成立了阻尼材料在武器装备上应用的研究机构。80年代后,国外阻尼减震降噪技术有了更大的发展,他们借助CAD/CAM在减震降噪技术中的应用,把设计-材料-工艺-试验一体化,进行了整体结构的阻尼减震降噪设计。我国在70年代前后进行了阻尼减震降噪材料的研究工作,并取得了一定的成果,但与发达国家相比,仍有一定的差距。阻尼材料在航空航天领域主要用于制造火箭、导弹、喷气机等控制盘或陀螺仪的外壳;在船舶工业中,阻尼材料用于制造推进器、传动部件和舱室隔板,有效地降低了来自于机械零件啮合过程中表面碰撞产生的振动和噪声。在兵器工业中,坦克传动部分(变速箱,传动箱)的振动是一个复杂振动,频率范围较宽,高性能阻尼锌铝合金和减振耐磨表面熔敷材料技术的应用,大大减轻了主战坦克传动部分产生的振动和噪声。
2.4 隐身材料
现代攻击武器的发展,特别是精确打击武器的出现,使武器装备的生存力受到了极大的威胁,单纯依靠加强武器的防护能力已不实际。采用隐身技术,使敌方的探测、制导、侦察系统失去功效,从而尽可能地隐蔽自己,掌握战场的主动权。抢先发现并消灭敌人,已成为现代武器防护的重要发展方向。隐身技术的最有效手段是采用隐身材料。国外隐身技术与材料的研究始于第二次世界大战期间,起源在德国,发展在美国并扩展到英、法、俄罗斯等先进国家。目前,美国在隐身技术和材料研究方面处于领先水平。在航空领域,许多国家都已成功地将隐身技术应用于飞机的隐身;在常规兵器方面,美国对坦克、导弹的隐身也已开展了不少工作,并陆续用于装备,如美国M1A1坦克上采用了雷达波和红外波隐身材料,前苏联T-80坦克也涂敷了隐身材料。
隐身材料有毫米波结构吸波材料、毫米波橡胶吸波材料和多功能吸波涂料等,它们不仅能够降低毫米波雷达和毫米波制导系统的发现、跟踪和命中的概率,而且能够兼容可见光、近红外伪装和中远红外热迷彩的效果。
近年来,国外在提高与改进传统隐身材料的同时,正致力于多种新材料的探索。晶须材料、纳米材料、陶瓷材料、手性材料、导电高分子材料等逐步应用到雷达波和红外隐身材料,使涂层更加薄型化、轻量化。纳米材料因其具有极好的吸波特性,同时具备了宽频带、兼容性好、厚度薄等特点,发达国家均把纳米材料作为新一代隐身材料加以研究和开发;国内毫米波隐身材料的研究起步于80年代中期,研究单位主要集中在兵器系统。经过多年的努力,预研工作取得了较大进展,该项技术可用于各类地面武器系统的伪装和隐身,如主战坦克、155毫米先进加榴炮系统及水陆两用坦克。
目前,世界上正在研制的第四代超音速歼击机,其机体结构采用复合材料、翼身融合体和吸波涂层,使其真正具有了隐身功能,而电磁波吸收型涂料、电磁屏蔽型涂料已开始在隐身飞机上涂装;美国和俄罗斯的地对空导弹正在使用轻质、宽频带吸收、热稳定性好的隐身材料。可以预见,隐身技术的研究和应用已成为世界各国国防技术中最重要的课题之一。
四、我国军用新材料的产业化趋势
应用于军事工业中的新材料均具有较高的技术含量,因而军用新材料的产业化速度普遍比较缓慢。世界范围内的军用新材料正向功能化、超高能化、复合轻量和智能化的方向发展。由此看来,钛合金、复合材料和纳米材料在军事工业中具有十分良好的产业化前景。
1、钛合金
钛是20世纪五十年代发展起来的一种性能优异、资源丰富的金属。随着军事工业对高强低密度材料需求的日益迫切,钛合金的产业化进程显著加快。在国外,先进飞机上钛材重量已达到飞机结构总重的30~35%。我国在“九五”期间,为满足航空、航天、舰艇等部门需要,国家把钛合金作为新材料的发展重点之一,预计“十五”将成为我国钛合金新材料新工艺的高速发展时期。
2、复合材料
军事高技术的发展要求材料不再是单一的结构材料,在这种条件下??国在先进复合材料的研制和应用方面取得了很大的成绩,它在“十五”期间的发展会更加引人注目。21世纪复合材料的发展方向是低成本、高性能、多功能和智能化。
3、纳米材料
纳米技术是现代科学和技术相结合的产物,它不仅涉及到现有的一切基础性科学技术领域,而且在军事工业中有着广泛的应用前景。随着未来战争突然性的急剧增大,各种探测手段越来越先进。为适应现代化战争的需要,隐身技术在军事领域占有十分重要的地位。纳米材料对雷达波的吸收率较高,从而为兵器隐身技术的发展提供了物质基础。
免责声明:本网站所转载的文字、图片与视频资料版权归原创作者所有,如果涉及侵权,请第一时间联系本网删除。
相关文章
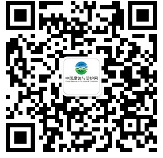
官方微信
《中国腐蚀与防护网电子期刊》征订启事
- 投稿联系:编辑部
- 电话:010-62316606-806
- 邮箱:fsfhzy666@163.com
- 中国腐蚀与防护网官方QQ群:140808414
点击排行
PPT新闻
“海洋金属”——钛合金在舰船的
点击数:7738
腐蚀与“海上丝绸之路”
点击数:6191