当反应堆发生失水事故(LOCA)时,冷却剂压力会迅速下降,使高压水瞬间汽化,压力容器水位降至燃料组件活性段以下,此时锆合金包壳表面温度急剧升高,锆合金包壳在高温蒸汽环境中氧化,直至应急堆芯冷却水将包壳管淹没。如果发生小破口失水事故,锆合金包壳裸露时间相对较长,发生高温蒸汽氧化的时间较长,氧化动力学由抛物线规律转变为线性规律,氧化速率大大增加,同时伴随大量吸氢,该现象被称之为失稳氧化。2008年,美国阿贡国家实验室(ANL)发布了《LOCA工况下的包壳脆化行为》研究报告,提出失稳氧化是导致包壳脆化的原因之一。
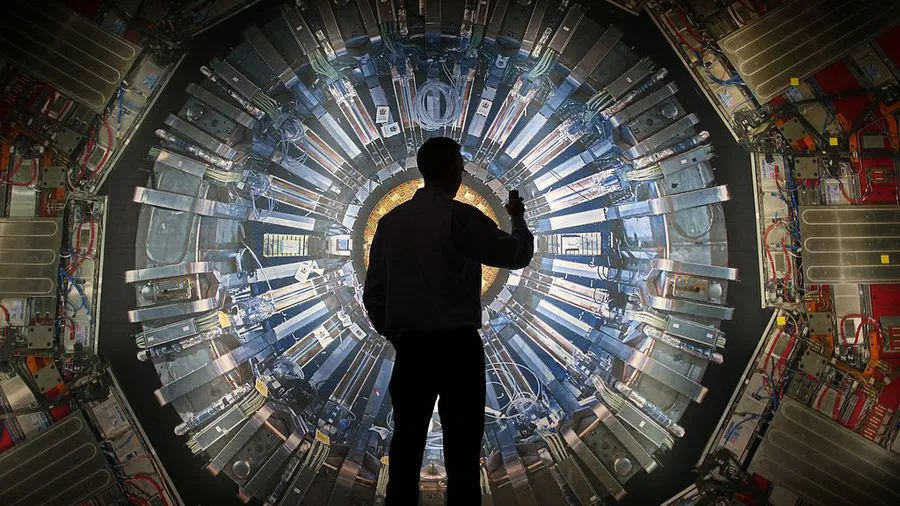
01
失稳氧化的氧化膜特征
目前,在不同系列锆合金中,E110合金的失稳氧化最为明显。发生失稳氧化时,Zr-4合金表面变成灰色,而E110合金最早在黑色基体表面形成白色的疖状腐蚀物,疖状腐蚀扩张使相邻区域也出现白点,最后发生严重的失稳氧化现象,大量吸氢,但是氧化膜/金属(O/M)界面较平坦。总的来说,发生失稳氧化后,肉眼可见氧化膜表面开始出现白点或灰点,后期氧化膜疏松,整体呈白色或灰色。锆合金失稳氧化后氧化膜形貌具有以下特征:氧化膜明显增厚;O/M界面呈波浪状(E110合金除外);靠近O/M界面的氧化膜内有大量横向裂纹和纵向裂纹;靠近O/M界面的金属基体内有大量纵向裂纹。
02
失稳氧化的机理
失稳氧化导致氧化膜出现大量裂纹,氧化膜中的裂纹为氧扩散提供了短路通道,该通道成为主要的氧扩散路径。
关于失稳氧化和裂纹产生的原因,目前业内持不同的观点。其中一种主流观点认为它与氧化膜中t-ZrO2转变成m-ZrO2的相变有关。
锆合金的氧化物ZrO2通常有三种晶体结构:低温稳定的单斜相(monoclinic,m-ZrO2)、1205℃以上稳定的四方相(tetragonal,t-ZrO2)和2377℃以上稳定的立方相(cubic,c-ZrO2)。在无应力状态下,t-ZrO2相转变为m-ZrO2相的温度为1150℃。t-ZrO2相主要分布在O/M界面,这是因为锆氧化生成氧化锆的PB比(ZrO2中Zr离子与金属Zr中Zr原子的体积比)为1.56,在形成的氧化膜中产生很大的压应力,压应力使得t-ZrO2相稳定;m-ZrO2相主要分布在远离O/M界面的位置。
LEISTIKOW等认为发生失稳氧化的标志是平坦的O/M界面变为波浪状表面,波浪状表面导致氧化膜局部出现拉应力和压应力,部分区域的氧化膜在拉应力的作用下从t-ZrO2相转变为m-ZrO2相,m-ZrO2相力学性能差,容易开裂,蒸汽通过裂纹直接与内层金属基体反应,氧化速率增加,吸氢加速。
LEISTIKOW等提出的失稳氧化机理与锆合金在高温高压水中腐蚀发生氧化转折(氧化动力学规律发生变化)的机理基本相似。虽然大量试验发现氧化转折后,t-ZrO2相转变成m-ZrO2相,但是LOCA工况下发生的失稳氧化现象与t-ZrO2→m-ZrO2相变之间的关系至今还没有实验依据。
YAN等认为E110合金之所以具有与其他合金不同的失稳氧化行为,主要与表面粗糙度、杂质等因素有关。E110合金是由精细Zr电解液制得,电解过程去除了杂质,单电解液中加入氟化物,氟化物污染对腐蚀有不利影响。
KIM等选取Alloy-A和Zr-4两种合金材料开展了模拟LOCA工况下的高温蒸汽氧化,结果发现失稳氧化后α-Zr(O)中氢化物与氧化物的分布几乎同步,如图1所示。因此推测失稳氧化与α?β相稳定剂及氢化物分布有关。
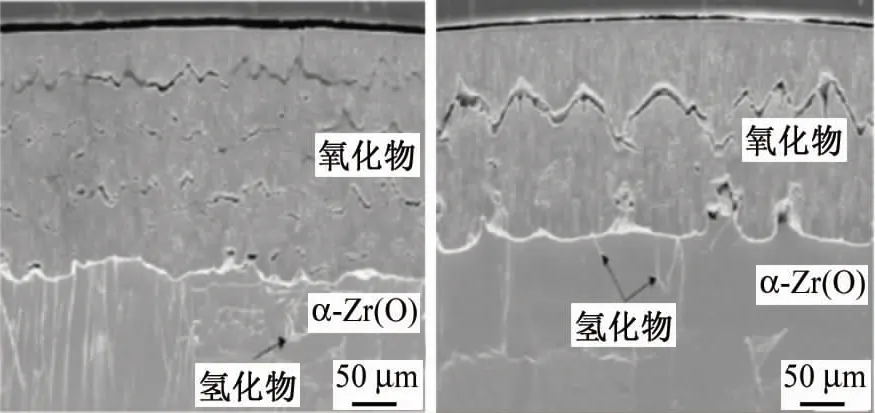
(a) Alloy-A合金 (b) Zr-4合金
图1 氧化5000s后Alloy-A和Zr-4合金表面氧化膜的SEM图
在此基础上,他们提出了另一种失稳氧化机理:当β相稳定剂含量较高时,氧化产生薄片状的α-Zr(O),由于α-Zr(O)晶界多,在氧化物/α-Zr(O)界面处的氢较易进入早期β相,因此冷却至室温后,α-Zr(O)相中几乎没有氢化物;当α相稳定剂含量较高时,形成块状的大晶粒α-Zr(O),聚集在界面处的氢很难进入早期β相,冷却后在α-Zr(O)晶界处有氢化物析出。
图2为氢诱发失稳氧化机理示意。在Alloy-A合金表面,α-Zr(O)的晶粒形貌复杂,既有薄片状,也有块状,也就是说Zr的基体材料中既含α相稳定剂,又含β相稳定剂,在薄片状α-Zr(O)处,氢可扩散进入早期β相,在块状α-Zr(O)处,氢被束缚在氧化物/α-Zr(O)界面和α-Zr(O)晶界处,此处氢气压力随着氧化时间的延长而增大,直至氧化层开裂,表面形成白色的疖状腐蚀物,表现为白点。在Zr-4合金表面,由于氢气产生的压力逐渐增大,导致氧化层性能下降,进而产生了波浪状表面。形成疖状表面还是波浪状表面主要取决于氧化层厚度,若氧化层薄,氧化层性能全面下降,表现为疖状表面,若氧化层厚,氧化层性能部分下降,表现为波浪状表面。由于合金元素会影响α-Zr(O)的晶粒尺寸,从而影响失稳氧化,因此失稳氧化与合金元素也有一定关系。
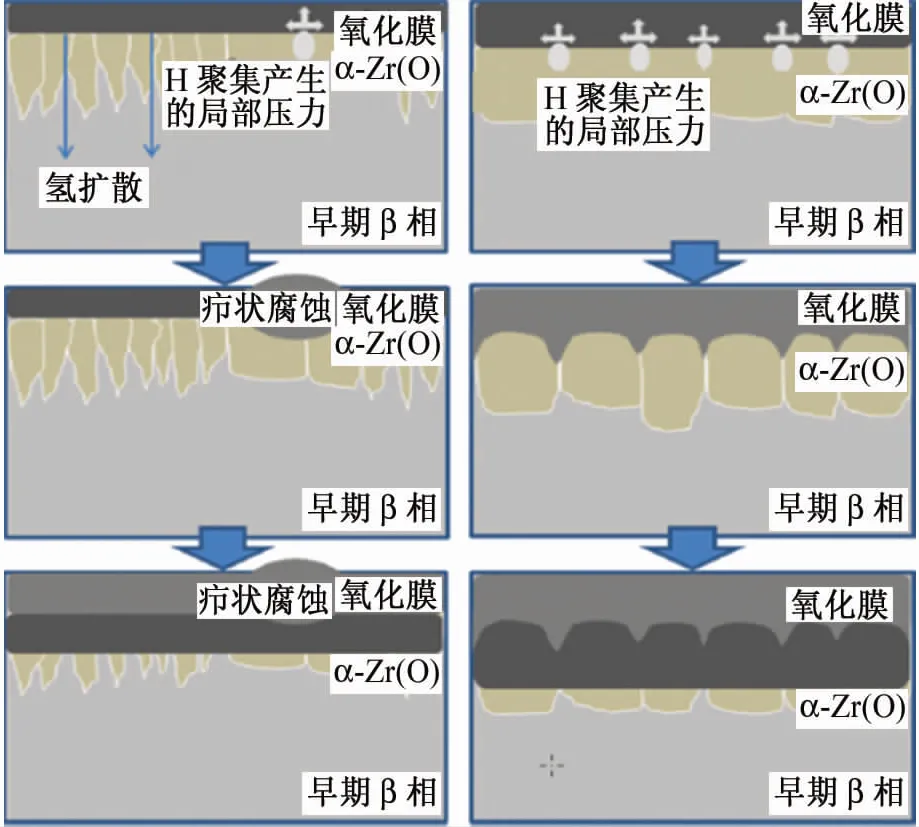
(a) 疖状表面 (b) 波浪状表面
图2 氢诱发失稳氧化机理示意
03
失稳氧化的影响因素
LOCA工况下对于失稳氧化的形成过程目前还缺乏足够的认识,而且失稳氧化的影响因素复杂,既有材料本身性能的影响,也有外部环境的影响,根据目前的研究,锆合金的失稳氧化行为主要与以下因素有关:
(1) 合金成分
按照锆合金的三大体系划分,在合金的添加元素中,影响最大的是Sn和Nb,其中Sn是α相稳定元素,Nb是β相稳定元素。
BARBERIS通过试验发现,在含1.2%(质量分数,下同)Sn的Zr-4合金氧化膜中t-ZrO2相含量较高且晶粒尺寸较小(小于30nm),在含0.8%Sn的Zr-4合金氧化膜中t-ZrO2相含量较低且晶粒尺寸较大(大于30nm)。
BAEK等在1000℃蒸汽环境中对Z4?ZL和H5三种合金进行了高温氧化试验,研究了合金中Sn含量和Nb含量对失稳氧化的影响,结果发现Nb含量对失稳氧化的影响不大,但减少Sn含量可推迟合金发生失稳氧化的时间。
(2) 晶粒形貌
锆合金表面形成的氧化物晶粒尺寸很小,通常为几十纳米。从形貌角度来说,锆氧化形成的氧化膜有柱状晶和等轴晶两种晶粒类型。研究发现,柱状晶沿氧化方向紧密排列,位于氧化膜内侧,对氧的扩散有一定的阻挡作用,等轴晶主要分布在氧化膜外侧,通常疏松多孔,另外等轴晶晶粒尺寸较小,增加了晶界面积,相对于体扩散氧更易沿晶界扩散,因此等轴晶为氧的扩散提供短路通道。所以晶粒形貌对氧化膜的生长有重要影响。除此之外,晶粒形貌与晶体结构也有一定的关系。
YILMAZBAYHAN和KIM等认为,在高温高压水中氧化时等轴晶存在于t-ZrO2含量高的位置,柱状晶主要为m-ZrO2,然而WADMAN等在Zr-4合金氧化膜外侧观察到柱状t-ZrO2。失稳氧化与t-ZrO2向m-ZrO2转变的相变有关,故有必要研究氧化膜的晶粒形貌与晶体结构的关系。
(3) 第二相粒子
第二相粒子对锆合金的氧化行为有重要影响。这主要是因为t-ZrO2相被压应力稳定,而压应力的来源除了锆基体氧化,还有第二相粒子的氧化。第二相粒子与锆基体的氧化行为不同,有些第二相粒子相比于基体延迟氧化,有些则是与基体同时氧化。具有延迟氧化特征的第二相进入氧化膜,当基体与第二相粒子结合不紧密时,如图3(a)所示,金属基体氧化体积膨胀,与第二相之间产生空隙,形成气孔;当基体与第二相粒子结合紧密时,如图3(b)所示,周围金属基体氧化带来的体积膨胀会对第二相粒子与外侧氧化物界面产生拉应力,导致微裂纹的产生。
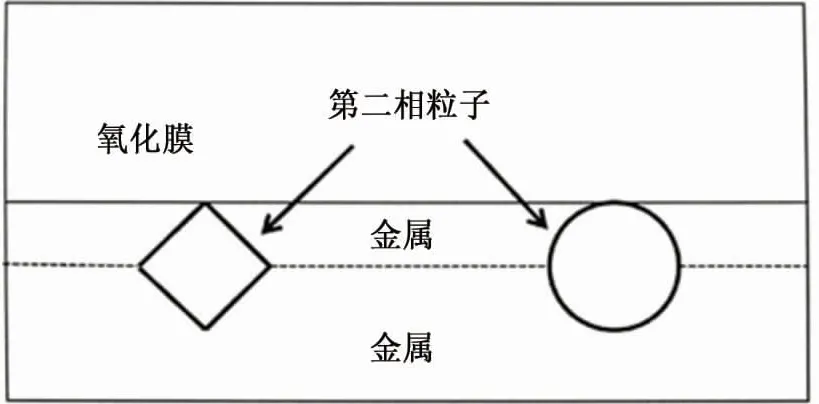
(a) 基体金属与第二相粒子结合不紧密
(b) 基体金属与第二相粒子结合紧密
图3 第二相粒子处孔隙和裂纹形成的示意图
结束语
LOCA工况下,燃料包壳材料的失稳氧化对反应堆的安全运行至关重要,国内外对失稳氧化的研究还不够充分,LEISTIKOW和SCHANZ认为造成失稳氧化与氧化转折的机理相似,都是由于氧化膜的相变,但是目前为止还缺乏确切的依据证实失稳氧化后氧化膜的相变,失稳氧化是否与相变有关,需要试验来验证;关于氢化物致失稳氧化的假说,只是根据Alloy-A 和Zr-4合金表面氢化物的分布与O/M波浪状表面一致这一现象得到的推论,还需利用其他锆合金材料进行验证,因此LOCA工况下失稳氧化的影响因素及机理尚需进一步研究。
免责声明:本网站所转载的文字、图片与视频资料版权归原创作者所有,如果涉及侵权,请第一时间联系本网删除。
相关文章
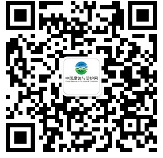
官方微信
《中国腐蚀与防护网电子期刊》征订启事
- 投稿联系:编辑部
- 电话:010-62316606-806
- 邮箱:fsfhzy666@163.com
- 中国腐蚀与防护网官方QQ群:140808414
点击排行
PPT新闻
“海洋金属”——钛合金在舰船的
点击数:7130
腐蚀与“海上丝绸之路”
点击数:5741