摘要:超高强韧钢同时拥有超高强度和优良韧性,因而在国防和民用工程机械领域中广泛应用。本文首先综述了各类型传统超高强韧合金钢的典型钢种、成分、性能及应用和发展历程,并重点阐述了各典型钢种的组织和强韧化机理;然后介绍了近年所研发的具有代表性的新型超高强韧钢的成分、组织、强韧化机理及力学性能;接着梳理了我国近年来由于快速发展的经济需求和地理、资源等特点,出现了对现役超高强韧钢进行升级换代的迫切需求,包括新型轻质装甲防护钢、大型球磨机用钢、高山隧道挖掘的盾构机刃具用钢以及石油工程机械中的高压压裂泵用钢等;最后介绍了作者团队近期在超高强韧钢的一些最新研究成果,并据此提出超高强韧钢未来发展的思路。
关键词: 超高强钢 ; 韧性 ; 析出强化 ; 马氏体 ; 残余奥氏体
超高强韧钢一般是指屈服强度大于1300 MPa,抗拉强度大于1500 MPa的合金钢[1]。从20世纪40年代初期起,美国海军为了节省造船费用而最先开始研发以能够代替普通钢,满足强度和韧性要求,同时焊接性能良好的超高强度低合金钢[2,3]。多年以来,超高强韧钢已被广泛应用于冶金、矿山、工程机械、电力、造船、国防等各工业领域的关键承力和受压构件中。超高强韧钢除了对高强度的要求外,还要有足够的韧性、疲劳抗力以及根据服役工况条件所要求的抗腐蚀性和抗蠕变等其它要求。但是,超高强韧钢的性能显著受化学成分、加工过程、内在显微结构特征、温度、载荷性质、甚至材料在使用过程中所处的实验环境等因素的影响。在一些代表高新技术和新型材料应用的关键领域,例如飞机起落架用钢、高端轴承钢、高压柱塞泵用钢和火箭发动机用高强度不锈钢等均属于超高强韧钢[4],而这些钢种目前国内生产技术和质量控制不稳定,会出现非金属夹杂、内部裂纹、使用寿命低等问题,严重限制了其使用。从改善环境、节约能源和提高国产超高强韧钢的整体质量方面考虑,降低合金含量,尽可能地降低生产成本,是钢铁材料领域的一个重要研究方向。本文从超高强韧钢的分类及主要工程应用、超高强韧合金钢的最新发展等几方面进行论述,并且对超高强韧钢目前存在的问题进行讨论和展望。
1传统超高强度高韧性合金钢分类及应用
按照化学成分及组织性能的不同,传统超高强度合金钢可以划分为:低合金中低碳马氏体超高强度钢,中、高合金二次硬化超高强度钢,超低碳马氏体时效超高强度钢以及沉淀硬化超高强度不锈钢[5,6,7,8,9,10]。
表1[7,10,11,12,13,14,15,16,17,18,19,20,21,22,23,24,25,26,27,28]为典型的传统超高强度合金钢的化学成分,下面按类别分别讨论。

1.1 低合金超高强韧钢
低合金超高强韧钢是在调质钢的基础上发展起来的合金钢,合金元素含量较低(不超过5%,质量分数,下同),其作用是保证钢拥有高的淬透性,提高马氏体的抗回火稳定性和抑制奥氏体晶粒长大,通常钢中加入的合金元素有Cr、Ni、Mo、Si、Mn和V等。C含量一般在0.25%~0.60%之间,C含量低于0.25%时,钢的塑性较好,但是强度达不到超高强度的要求;C含量高于0.60%后,钢的强度很高,但是韧性很差而不能广泛应用,同时C含量过高也严重恶化了钢的焊接性能。低合金超高强韧钢的热处理制度为淬火加低温回火或等温淬火工艺,热处理后得到如图1[12,29]所示典型的回火马氏体与细小弥散碳化物组织,因而具有超高的强度和适当的韧性。由于低合金超高强韧钢的合金元素含量低、成本低、生产工艺简单,因而广泛应用于制造飞机起落架、发动机轴、高强度螺栓、固体火箭发动机壳体和化工高压容器等领域。
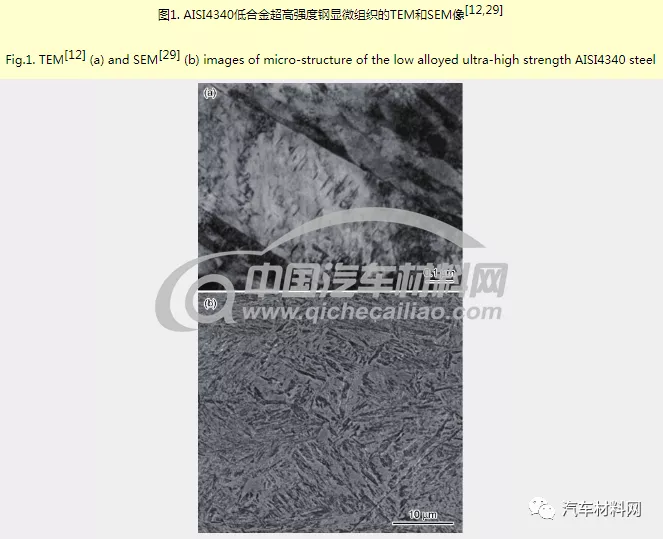
美国的AISI4130、AISI4140和AISI4340系列合金钢是早期低合金超高强韧钢的典型代表[29,30,31,32]。其中AISI4130是最早研发的超高强度合金钢,为了获得最好的强韧匹配,常将该钢进行调质处理,但由于其屈服强度和抗拉强度分别为880和980 MPa,强度不能满足超高强度合金钢的要求,所以在4130钢的基础上继续提高C含量至0.4%,同时加入少量的Ni和Mo元素,形成了4340钢。之后开发的大多数低合金超高强韧钢都是在AISI4130和AISI4340系列合金钢的基础上不断改进的。因为低合金碳钢C含量较高,导致其淬火后强度很高,但是塑韧性很差。因此,Krauss[33]对马氏体碳钢和低合金碳钢进行了低温回火处理(150~200 ℃)。结果表明,由含C量决定的低温回火马氏体的强度与马氏体晶体中位错和过渡碳化物的动态加工硬化有关。在含0.5%C的钢中,当回火马氏体基体中第二相粒子分散时,韧窝在其上形成并导致塑性断裂。含0.5%C以上的低温回火马氏体钢中,容易在原始奥氏体晶界发生脆性沿晶断裂。所以,低合金超高强度钢中的C含量一般不要超过0.5%,并且为了提高其韧性,一般要进行适当的低温回火处理。为了进一步提高低合金超高强度钢的韧性,Chang和Smith[34]研究了Si元素对马氏体回火硬度及显微组织的影响,发现了Si元素对低合金超高强度钢的有利作用,为300M钢的研发奠定了基础。1952年,美国国际镍公司开发设计了300M钢[6],它是在AISI4340钢的基础上添加1.5%~2.0%的Si元素,并略微调整V含量而发展起来的。300M钢可以在较高的温度区间进行回火而不降低强度,扩大了回火温度范围,抑制了马氏体的回火脆性。因为300M钢拥有超高的强度、适当的塑性和一定程度的耐腐蚀等性能而被广泛用作飞机起落架和压力容器用钢,但服役时常面临含Cl-的环境,会导致应力腐蚀开裂。因此腐蚀行为的研究是300M钢今后的研究重点[35]。
我国从20世纪50年代起开始了低合金超高强韧钢的研发。目前国内外主要低合金超高强韧钢的力学性能如表2[11,14,30,32,36,37,38,39,40]所示。从最初20世纪70年代仿制美国AISI4340钢、300M钢[36],到根据我国实际的资源情况自主研发的30CrMnSiNi2A钢,之后的45CrNiMo1VA钢[37,38]等,到无Ni、Cr的35Si2Mn2MoVA钢,无Ni的406钢和40CrMnSiMoVA钢[39,40,41]等,我国低合金超高强韧钢的发展经历了从无到有,从仿制到研发,从低端到高端的历程。

1.2 中、高合金二次硬化超高强韧钢
二次硬化钢是指含有Cr、Mo、V、Ti和Nb等碳化物的合金钢,通过淬火后的马氏体在500~600 ℃之间回火时,硬度不仅不降低反而升高的二次硬化机理进行强化。用这一机理研发了多种性能优良的超高强度合金钢,如中温超高强度合金钢38Cr2Mo2VA(GC-19)[42],可用作飞机主承力框架等构件。但是,中合金超高强韧钢与低合金超高强韧钢有类似的缺点,即断裂韧性(KIC)不高和抗应力腐蚀能力差,不能完全满足现代航空航天材料和高压容器的要求。高合金超高强韧钢中含有较多的Ni和Co元素,可以在显著提高硬度的同时提高韧性,如高合金超高强韧钢AF1410和AerMet 100钢通过分别加入10%以上的Ni和Co合金元素[20,43]获得了高强度、优良的疲劳抗力和应力腐蚀开裂抗力,可以替代现有用在制造航空受力件、轮船主轴等大型承力构件上的超高强度合金钢,可减轻质量并延长使用寿命。用AerMet 100钢替代300M钢做飞机起落架,可以克服300M钢的低断裂韧性和对应力腐蚀开裂敏感等缺点。目前常见的二次硬化超高强韧钢的力学性能如表3[20,42,43,44,45,46]所示。
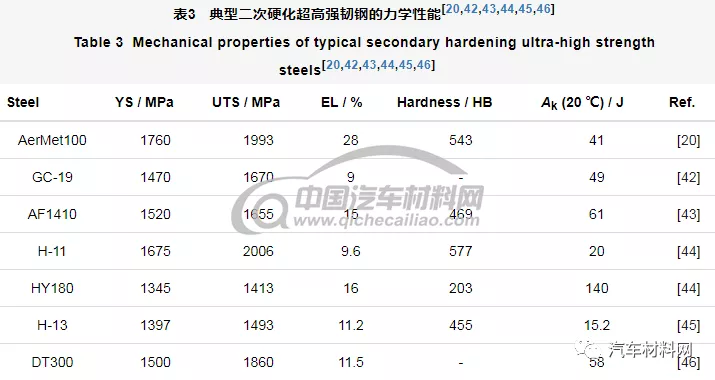
二次硬化超高强度合金钢的高强度是由合金马氏体在高温回火时合金碳化物的脱溶与残留奥氏体的二次淬火共同提供的,钢中典型合金碳化物的显微形貌如图2[47]所示。Morikawa等[48]研究表明,回火时合金碳化物在析出过程中的组成是不确定的,其点阵常数随合金化学成分而改变并影响碳化物与基体的共格关系。当二次硬化达到最大时,钢的韧性最差;而过时效可以显著提高钢的韧性但导致钢的强度明显降低。但通过合理的化学成分配比和仔细调整热处理工艺,可以使二次硬化钢的强度和韧性同步增加,如Speich等[49]发现,往Fe-Ni-Mo-C钢中添加Co可以提高M2C的形核率,细化M2C,同时抑制了回火过程中形成逆转变奥氏体,既增强了固溶强化也提高了韧性。当二次硬化钢10Ni-Cr-Mo-Co中粗大的渗碳体完全被细小的(Mo, Cr)2C取代后,可以获得最高的韧性。对之后开发的AF1410和AerMet 100钢深入研究[8,50]表明,二次硬化反应与析出高共格的细小针状六方结构合金碳化物M2C密切相关,用Cr取代M2C中的Mo使M2C晶格常数变小,并与基体接近,进而获得了更好的共格程度,提高了强韧性。
但AF1410钢中含有大量的Ni和Co元素,合金成本昂贵,且在铸造和锻造时易发生偏析和组织不均匀,造成材料浪费。因此近几年来迅速发展的激光增材制造(LAM)[51]是该类型钢加工技术的未来趋势,能够实现构件的近净成形,节约材料的同时还可以缩短生产周期,从而降低生产成本。目前,LAM技术已经成功用于多种金属材料构件的制备。例如,采用LAM技术成功制备了AF1410钢厚板试样,激光增材制造沉积态组织具有定向凝固组织特征,表现为沉积方向生长的胞状柱晶,且此时硬度相对较低,只有350 HV左右。经过后续热处理后,组织得到细化,获得了细小的回火马氏体组织,强度和塑性与相同热处理条件下的锻件性能相当。
1.3 马氏体时效超高强韧钢
马氏体时效超高强度合金钢是以无碳(或微碳)马氏体作为基体,时效时能产生金属间化合物析出强化的超高强度合金钢。具有工业应用价值的马氏体时效钢,是20世纪60年代初由国际镍公司首次研发的。该公司在Fe-Ni马氏体合金中加入不同含量的Co、Mo和Ti,通过时效硬化得到屈服强度分别达到1400、1700、1900 MPa的18Ni(200)、18Ni(250)和18Ni(300)钢,并首先将18Ni(200)和18Ni(250)应用于火箭发动机壳体[52],典型马氏体时效超高强韧钢的力学性能如表4[18,21,22,23,24,25]所示。在含Co马氏体时效钢中,Co虽然固溶于马氏体基体但并不形成金属间化合物,它主要促进含Mo金属间化合物的析出[53]。通过影响位错亚结构,为析出相提供均匀的形核位置,进而促进析出相粒子细小弥散分布,达到明显的析出强化效果。例如,Duan等[54]研发的CM400马氏体时效钢中含有15%Co,可以获得高达2.4 GPa的抗拉强度,但是只有3%的延伸率,限制了CM400钢的广泛使用。为了改善其塑性,可以对钢板表面进行喷丸处理,使其断裂形核位置由表面集中点向亚表面与试样内部分散转移,喷丸处理之后,钢板的屈服强度略有提高,抗拉强度不变,延伸率提高到4%以上。

马氏体时效超高强度合金钢在相同的强度级别下拥有比低合金超高强韧钢更高的韧性,加工硬化指数低,没有脱碳和焊接困难等难题,热处理工艺简单,冷加工成型性好。但是,常用的18Ni马氏体时效超高强度合金钢中含9%的贵重Co元素,由于全球Co资源严重短缺,导致Co价格急剧飙升,使含Co马氏体时效钢的成本大幅上升,限制其进一步发展和应用。我国Co资源缺乏,因此国内大型固体火箭发动机壳体一般不选用这种材料。20世纪90年代,国内在18Ni马氏体时效钢的基础上,采用取消Co元素,提高Ni和Ti含量的方法,成功仿制出了T250马氏体时效钢[22]。T250抗拉强度为1760 MPa,屈服强度大于1655 MPa,断裂韧性大于80 MPa·m1/2,是制造我国固体发动机壳体的新一代材料。除了已经用于工程材料上的T250钢,我国还在积极研究强韧性更高的无Co马氏体时效钢,何毅等[55]研发的T350无Co马氏体时效钢经过适当的热处理后,其屈服强度达2050 MPa,抗拉强度达2150 MPa,同时拥有近10%延伸率和70 MPa·m1/2的断裂韧性,该性能达到了18Ni(300)型含Co马氏体时效钢的同等水平。
低、中合金超高强韧钢的缺点是KIC不高和抗应力腐蚀能力差,马氏体时效超高强度合金钢则打破了以C作为主要强化元素的传统做法,而以Ni为主要合金元素形成韧性的Fe-Ni基马氏体,通过Co、Mo和Ti等强化合金元素,时效时从过饱和固溶体中析出合金化合物作为第二相质点来实现强韧化。虽然马氏体时效超高强度合金钢有很多的优点,但是也有弹性模量低、刚性不足、抗疲劳性能低于300M钢等缺点。而且,马氏体时效超高强度合金钢化学成分的微小变化都会显著影响析出相的析出行为。例如,当减少马氏体时效钢中Co的使用量时会恶化二次相析出的动力学,进而降低韧性[56],引起力学性能的很大波动,所以限制了它的广泛应用。为了克服这一缺点,可以在铁素体/马氏体钢中析出纳米共格的NiAl析出相,这种具有较小晶格错配度的二次相可以获得优良的机械性能[18]。
1.4 沉淀硬化超高强度不锈钢
为了提高超高强韧钢的耐腐蚀性能,在马氏体时效超高强韧钢的基础上开发出了含Cr大于12%的沉淀硬化(PH)超高强度不锈钢。它们是含有较多的Cr和Ni以及一定量的Mo、Co、Ti、Ni和Al等合金元素的超低碳合金钢,通过马氏体相变和时效强化获得优异的综合性能,典型沉淀硬化超高强度不锈钢的力学性能如表5[27,28,57,58]所示。该系列钢具有强度高、断裂韧性高、焊接性好、易加工、高耐蚀性等优点,在空军、航空航天等许多工程领域得到广泛应用。沉淀硬化超高强度不锈钢的高强度和良好的韧性来自于马氏体基体上均匀、细小分散的金属间化合物(NiAl、Ni3Ti、Laves相)的析出作用。这些细小的析出相在高温淬火之后中温(400~600 ℃)时效时析出。依据合金成分的不同,细小析出相的类型也不同。例如,PH 13-8 Mo沉淀硬化不锈钢[59]在400 ℃以上时效时会析出B2型超点阵结构的β‘-NiAl相,这种析出相的晶格常数是0.2887 nm,与铁素体的晶格常数(0.28664 nm)非常接近,所以NiAl析出相与基体即使在长时间时效后依然保持共格关系。Custom465钢[60]在510 ℃时效后,马氏体基体上弥散析出与基体半共格hcp结构的Ni3Ti相,同时少量逆转变奥氏体起到提高塑韧性的作用,最终获得抗拉强度高于1800 MPa的优良性能。
第一代沉淀硬化不锈钢(PH 17-4、PH 15-5[57,58])的强度一般为1300 MPa左右,并不能很好地满足某些领域对超高强度的要求。所以主要用于制造耐腐蚀的高强度部件,如喷气发动机压气机机匣及大型汽轮机末级叶片。在此基础上,提高Ni和Al含量开发了第二代中高强度沉淀硬化不锈钢(Custom465),尽管第二代沉淀硬化超高强度不锈钢的耐腐蚀性能优于一般的超高强度高韧钢,但是其合金元素Cr、Ni含量较高,导致材料成本较高。为了解决这一矛盾,Kuehmann等[28]通过计算机辅助成分设计研发了新一代的沉淀硬化超高强度不锈钢Ferrium S53,新的超高强度不锈钢中Cr和Ni含量分别下降至10%和5.5%,适当提高了C和Co的加入量。通过析出硬质M2C型纳米共格析出相强化马氏体基体,达到了与300M钢相同的强度级别,同时又具备优于300M钢的耐腐蚀性能。
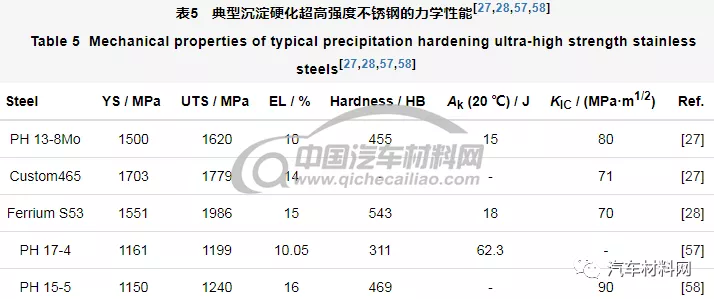
近年来,国内在超高强和高断裂韧性马氏体时效不锈钢方面也进行了大量研究并取得了突出的成果。例如,Li等[61]研发的13Cr-12Co-3.5Mo-4Ni-0.5Ti马氏体时效不锈钢,通过时效过程析出的Ni3(Ti, Al)、富Mo的R’相和富Cr的α‘相,共同起到析出强化的作用,最终获得1649 MPa屈服强度、1928 MPa抗拉强度、10%延伸率和83.6 MPa·m1/2断裂韧性的力学性能。Tian等[62]研发的13Cr-8Ni-7Co-3Mo-2Ti马氏体时效不锈钢,在480 ℃时效不同时间后,析出纳米尺寸的Ni3Ti和富Mo相,其达到了1920 MPa抗拉强度和80 MPa·m1/2的断裂韧性,同时,耐腐蚀性能优于PH 15-5钢。
1.5 传统超高强高韧钢存在的问题
低合金超高强韧钢的优势在于其经济实用、制备工艺简单。但是室温下工作的大受力构件方面的要求逐渐增高,此类钢的一些不足之处就逐渐显露出来,一方面是韧性不足,另一方面是耐蚀性不够。随着强度的升高,塑性、韧性不断下降,应用过程中钢铁材料常发生脆性失效。所以目前传统的低合金超高强度合金钢已经无法满足关键工程领域的高要求。如何在提高强度的同时,改善塑韧性和耐应力腐蚀性,同时还要成本经济性,这是研发新型低合金超高强韧钢的热点和难点。另外,低合金超高强韧钢是中碳钢,热处理过程中存在严重的脱碳倾向,并且C含量过高严重恶化钢板的焊接性能。因此,如何选择合适的热处理工艺尤为重要。
与传统低合金超高强韧钢相比,马氏体时效钢,中、高合金二次硬化钢及沉淀硬化超高强度不锈钢拥有很高的强度、韧塑性、疲劳抗力和良好的耐蚀性。但是,由于钢中添加了大量的Cr、Co、Ni和Mo等贵重合金元素,使钢的生产成本大幅度提高。同时由于钢中加入的大量合金元素降低了钢液的流动性,很容易在浇注过程中发生合金元素的偏析,造成成分不均匀,使钢板在工程应用中发生开裂。为了避免钢中合金元素的大量偏析,通常需要增加钢水冶炼次数或者延长热处理时间使成分均匀,这就显著增加了能耗,降低了生产效率。开发新的冶炼工艺和改进热处理方法是中、高合金超高强韧钢今后的研究热点和难点。
2新型超高强度高韧性合金钢的发展
2.1 新型马氏体时效超高强韧钢
传统马氏体时效钢中的析出相主要为六方晶系的η-Ni3Ti和正交晶系的δ-Ni3Mo,这2种析出相和周围马氏体基体是半共格或者非共格的,由于在半共格或非共格临界形核形成过程中所需要的界面能较高,所以η-Ni3Ti和δ-Ni3Mo趋向于在显微组织中的特殊位置非均匀形核,例如晶界、位错、层错或其它晶体缺陷处。析出相和基体之间较大的差异虽然能提供较高的强度,但是也促使材料在加载过程中容易过早萌生裂纹或者造成局部应力集中,这将严重恶化材料的整体塑性,而析出相和基体结构上过大的差异必然导致析出过程存在高的形核势垒,最终致使可以起到强化作用析出相的密度降低。因此,传统方法通过添加大量贵重合金元素,在高位错密度的板条马氏体基体内部析出大量纳米半共格析出相的方法已经达到了马氏体时效超高强度合金钢的性能上限,成为马氏体时效超高强韧钢进一步发展的限制。
Jiang等[18]通过创新合金设计理念,实现高密度和最小晶格错配度Ni(Al, Fe)共格纳米粒子的析出强化,使新一代马氏体时效超高强韧钢的研究取得了突破,该钢的抗拉强度达到2.2 GPa,延伸率达到8%。该钢最大限度地减小了析出相与基体的点阵错配度(0.03%±0.04%),并引入“有序效应”作为主要的强化机制,显著降低了析出相的形核势垒,促进高密度和良好热稳定性的析出相均匀弥散分布。同时,这种共格度极高的界面可以有效缓解析出相粒子周围的微观弹性畸变,改善材料宏观均匀塑性变形能力。另一方面,析出相可以有效阻碍位错切过,从而获得综合性能优异的新型马氏体时效超高强韧钢。在该钢中,采用Al元素代替合金元素Co和Ti等,不仅降低了材料成本,而且Ti的去除允许合金中添加一定量的C元素并以碳化物的方式起到协同强化作用,这也将有效简化新型马氏体时效超高强韧钢的制备和精炼过程,扩大马氏体时效钢的工程应用范围[63]。
2.2 超高强高韧纳米贝氏体钢
贝氏体钢是一种具有较高强度和良好韧性的钢种,纳米贝氏体钢的出现吻合了钢铁材料不断提高强度和韧塑性的趋势。英国剑桥大学Bhadeshia和Edmonds[64]利用Si对碳化物析出的抑制作用,发现了超级纳米贝氏体的优异强韧性,这种贝氏体铁素体板条中间不是析出碳化物而是残余奥氏体薄膜,这样的组织结构决定了其具有超高强度和良好的韧性匹配。纳米贝氏体钢的抗拉强度为1.77~2.20 GPa,甚至可高达2.5 GPa,屈服强度高达1.5 GPa,延伸率为5%~30%,断裂韧性可达40 MPa·m1/2 [65]。但是当纳米贝氏体钢的强度在2000 MPa时,塑性超10%,韧性达10 J左右,保持高强度的同时提高其韧性是纳米贝氏体钢需要继续改进的方向。超级贝氏体钢的合金元素设计,首先是显著推迟珠光体和铁素体转变,同时降低贝氏体和马氏体开始转变温度,而且使2个转变温度之间的温度差扩大,保证进行贝氏体转变而不发生珠光体与马氏体转变,得到以贝氏体为主的组织。在超级贝氏体钢的典型合金成分中,C含量较高(0.78%~0.98%),目的是降低贝氏体转变温度,得到纳米级贝氏体铁素体板条组织;含较多的Si (1.5%)以阻碍渗碳体析出;另外添加适量的Mn、Mo、Co或Al元素,起到提高组织淬透性、消除回火脆性、增加奥氏体向贝氏体转变的驱动力和加速贝氏体相变的作用。
如图3[66]典型纳米贝氏体显微结构所示,超级贝氏体钢在125~300 ℃的低温贝氏体区间长时间等温(1~60 d)后,获得20~100 nm的贝氏体铁素体板条和板条间富C的薄膜状残余奥氏体,残余奥氏体分数一般不小于20%。由于超级贝氏体组织中的贝氏体铁素体为纳米级,且处于C过饱和状态,故起着强烈的细晶强化和固溶强化作用;同时,贝氏体铁素体中存在较高的位错密度,故有一定的位错强化作用。超级贝氏体组织具有良好的塑性和韧性,一方面与贝氏体铁素体板条的位错亚结构有关,但最主要的原因是贝氏体铁素体板条间的薄膜状残余奥氏体,在高的应力作用下会发生马氏体转变,可以有效提高材料的塑韧性,其薄膜状的形态分布又增强了对裂纹的吸收效应。

2.3 高位错密度诱导大塑性变形-配分钢
一般而言,钢铁材料随着强度的不断升高塑性逐渐下降,当强度达到2 GPa以上时,延伸率通常不超过10%,这几乎是传统钢铁材料强塑性平衡的极限。以前通过晶界和共格孪晶界的细化解决这一矛盾,但是当晶粒尺寸细化到一定尺度时,不仅仅强度将达到极限同时也由于塑性失稳导致塑性严重恶化。位错可能是解决这一问题的另一个途径,但是根据经典Taylor强化公式[71]可知,金属材料的强度随位错密度单调增加,但是塑性随着位错增加而降低。但是如果存在高密度的可动位错时,情况将有所不同。He等[72]开发了一种廉价的中锰超级钢,钢的化学成分为10Mn-0.47C-2Al-0.7V,不含任何Cr、Ni和Mo等贵重合金元素。将中锰钢经热轧、温轧、两相区退火、冷轧加低温回火的工艺处理后,形成亚稳奥氏体板条嵌在高位错密度马氏体基体中的显微组织,马氏体中的总位错密度高达1.27×1016 m-2,这种独特工艺下获得的马氏体要比传统淬火马氏体中的位错密度高出约2个数量级。因此,在变形时,高密度的位错不仅仅通过位错增殖和交割提供显著的加工硬化从而获得超高强度2.2 GPa;同时由于大量可动位错的滑移并结合残余奥氏体的相变诱导塑性(TRIP)和孪晶诱导塑性(TWIP)效应的共同作用获得了可观的塑性,延伸率达到16%。该钢的工程应力-应变曲线如图4[72]所示,这成功突破了强度和塑性的相互制约关系。这种通过将成分与加工工艺进行创新设计,获得高密度可动位错并结合残余奥氏体的组织,有望用于设计新一代的超高强高韧合金钢。
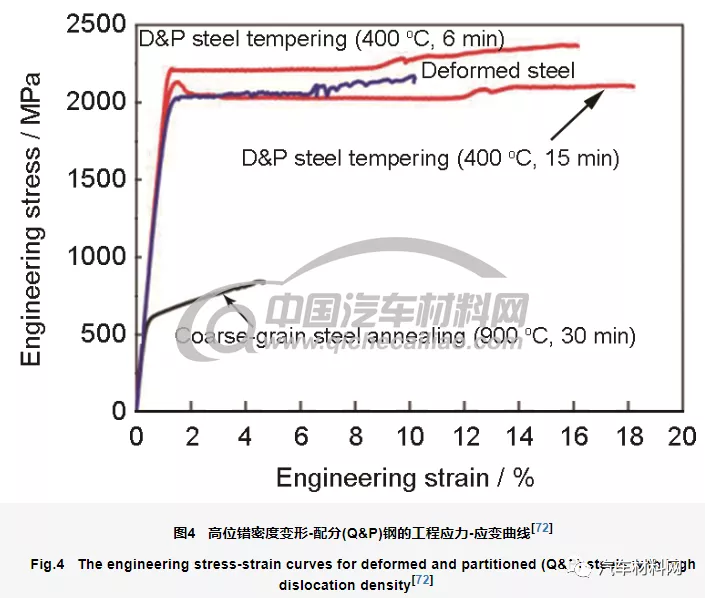
2.4 复合析出纳米相超高强韧钢
钢中析出相与位错的相互作用会产生很强的析出强化作用,析出相粒子对位错的钉扎作用如图5所示,主要有2种机制(切过机制和绕过机制)。当析出相尺寸小,与基体保持共格时,位错切过析出相;当析出相不断长大,与基体脱离共格关系时,位错绕过析出相。超高强韧钢经固溶时效后产生的金属间化合物一般与基体保有良好的共格度,属于切过粒子,而钢中的碳化物、氮化物及粗大的析出相一般都是绕过粒子。传统超高强韧钢中的析出相多为合金碳化物、单相半共格或非共格的金属间化合物,这样的析出相虽然能够提供很高的析出强化效果,但是由于弱的共格性一般都会导致钢的韧性较差。所以可以通过析出金属间化合物取代合金碳化物或者改变金属间化合物的种类与配比来减小其与基体的错配度,从而达到提高材料强度的同时增加塑韧性的目的[73]。但是,想要获得共格度非常高的析出相,尤其是当要获得极高的强度和韧性匹配时,往往需要对化学成分和加工工艺提出严苛的要求[18]。此时采用2种及以上析出相的复合强化,就成为一个可行的选择。近年来典型超高强韧钢中复合析出纳米粒子种类如表6[61,74,75,76,77,78,79,80]所示,相对于单一类型纳米析出相,采用复合析出的方法,可以将具有不同成分、晶体结构和微观力学特性的多种析出相协同结合,产生超过纳米析出相单独加入钢中产生的强韧性作用。
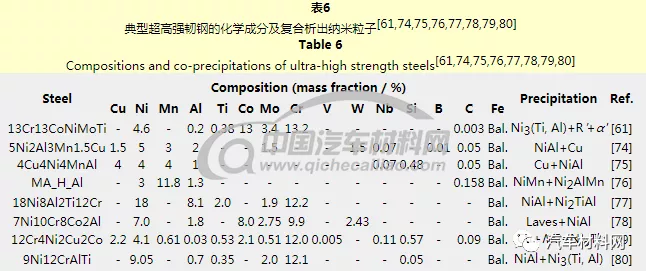
复合析出纳米粒子强韧钢要求精确控制各种纳米析出相的尺寸、数量和空间分布。有2组纳米析出相粒子的晶体结构与bcc-Fe基体有很高的共格性[81]:一组是bcc结构或者bcc结构的派生结构,例如bcc-Cu、B2-NiAl、L21-Ni2AlTi和Ni2AlMn;另一组是hcp结构,例如Ni3Ti和Mo2C。第一组的共格性是通过纳米析出相与bcc-Fe基体在立方体平面上的近似重合实现的,而第二组的共格性是通过纳米析出相的密排方向和bcc-Fe基体的立方体方向近似重合实现的。相反,非共格析出相,例如Fe3C、FeCr、Fe2Mo和Fe7W6通常析出尺寸很大,没有有效的强化效应甚至因为在晶界析出引起材料脆断,所以超高强度高韧合金钢中应该尽可能避免出现此类非共格析出相[28,82]。近年来通过计算机辅助合金设计、纳米结构表征方法的进步,人们研发出多种复合析出纳米共格粒子的超高强度高韧性合金钢。例如,Jiao等[74]研发的Fe-Cu-Ni-Al基超高强度合金钢,通过纳米尺寸的NiAl和Cu粒子的复合析出起到强化作用,展现出了1.9 GPa抗拉强度,10%延伸率的优良力学性能。Kapoor等[75]研发的Cu-Ni-Mn-Al基超高强低碳合金钢中,通过Cu和NiAl的复合析出强化,获得了最高1600 MPa的屈服强度。尽管Cu/NiAl复合析出相在很宽的成分范围内都可以形成,但是依据Cu/Ni和Cu/Al比的不同,复合析出物的析出机制非常不同,有2个主要的析出路径。如图6a所示,当钢中含有较多的Cu和相对较少的Ni和Al时,含少量Ni和Al的富Cu粒子首先在过饱和固溶体内形核,核内主要是Cu,随析出相的不断长大,Ni和Al不断偏聚在Cu和基体之间的界面上,降低Cu析出相的界面能,因此促进NiAl析出相在Cu周围不均匀析出,导致Cu-NiAl型复合析出相[83]形成。在低的Cu/Ni和Cu/Al配比钢中,富含大量Ni、Al和Cu的粒子首先在过饱和固溶体中形核,由于Cu在bcc-Fe中几乎没有固溶度,很容易溶入NiAl的析出过程。随着时效过程的进行,先形成的NiAl粒子开始向表面排出Cu,导致不均匀形核的Cu粒子在NiAl表面产生,因此形成NiAl-Cu型复合析出相。



Millán等[76]研发的Fe-Mn-Ni-Al型超高强度合金钢,通过向钢中加入适量的Mn和Al后可以将钢中的Ni含量降至5%以下,产生新一代的低成本超高强韧钢。加入Al后可以生成B2-NiMn和Ni2MnAl复合纳米析出相,这2种析出相的含Ni量都要低于Ni3Ti,基体中含有较低的Ni即可形成NiMn和Ni2MnAl纳米析出相。同时,2种析出相都是与基体一样bcc结构的有序相,而且Ni2MnAl析出相和基体的错配度更低,所以形核半径更小,导致析出相尺寸更小,数量更多地分散在马氏体基体上,起到很强的析出强化作用。Liebscher等[77]研发的Fe-Al-Cr-Ni-Ti铁素体基合金钢,因为较低的成本、小的热膨胀、良好的抗氧化性和高的热传导性作为高温结构用钢。钢中主要通过析出B2-NiAl和L21-Ni2AlTi复合分层析出相起到强化作用。在时效的早期阶段主要析出B2-NiAl析出相,随着时效时间的增加,在B2-NiAl析出相的内部逐渐形成L21-Ni2AlTi析出相,最终析出分层分布的复合纳米析出相,复合纳米析出相的析出过程如图6b所示。
Sun等[78]最近研发了一种拥有超高强度和耐500 ℃蠕变性能的Al-Co-Cr-Ni-Mo基超高强度马氏体时效钢,作为喷气发动机中的低压涡轮轴的材料。通过复合析出纳米尺寸的金属间化合物Laves相和β-NiAl析出相强化,得到室温屈服强度大于1800 MPa,抗拉强度大于2000 MPa,延伸率达8%和700 MPa下蠕变断裂寿命大于2000 h的优良综合性能。与传统马氏体时效钢利用Ni3Al析出相提高强度不同,新的超高强韧钢含较少的Ni,通过2种纳米尺寸金属间化合物共同起到强化作用,B2型超点阵结构的NiAl和密排拓扑结构的Laves相提供了高强度和良好的抗蠕变特性。在该钢中,奥氏体化温度和时效温度是决定其显微结构演变和力学性能的关键因素,大量初生Laves相在较低的奥氏体化温度下(825 ℃)沿原始奥氏体晶界和奥氏体晶内的孪晶界析出,并在时效过程中始终长大,随着时效时间的增加,二次Laves相的强化增量也在增加[78]。β-NiAl析出相在时效初期开始发生粗化,强化机制逐渐由切过向Orowan绕过转变;时效温度的微小差别(20 ℃)虽然对β-NiAl化学成分的影响很小,但会对其空间分布特点产生显著的影响。所以为了获得良好的综合力学性能,仍然需要对热处理工艺进行仔细设计[78]。
除了在超高强韧钢中复合析出2种纳米析出相共同强化基体外,Xu等[79]还研究了在Cr-Ni-Cu-Ti-Nb超高强韧钢中通过复合析出MC碳化物、Cu粒子和Ni3Ti 3种纳米析出相共同起到强化作用。超高强韧钢经过奥氏体化和淬火后得到完全马氏体基体,在500 ℃时效24 h后基体内部析出了复杂的析出相:尺寸在100~300 nm之间均匀分布的(Ti, Nb)C碳化物,非常细小分散的10 nm球形Ni3Ti和一些小于10 nm且具有孪晶结构的Cu粒子。正是由于多种析出相的复合强化能力和相对较慢的析出动力学,超高强韧钢在500 ℃时效24 h后才能获得1.6 GPa的抗拉强度和9%延伸率的良好性能组合。
以上这些复合析出共格纳米粒子强化钢明显优于前面提到的典型超高强韧钢,拥有高强度和韧性的良好匹配。但是目前大部分研究中,共格析出的复合纳米粒子多为同一种强化类型(剪切机制),因为可以较容易地在马氏体回火中实现;但是结合了绕过机制粒子(如碳化物)和剪切机制粒子(如bcc-Cu)的共同析出对提高强韧性有更大的潜力,比如Saha等[84]在设计与开发的新型潜艇用钢时,通过多级回火实现Cu与Mo2C共同析出强化,在屈服强度达到1100 MPa的同时常温韧性(Akv)为176 J,这甚至超过了设计目标的韧性值约50%;另外Li等[85]在中锰钢中实现了细小NiAl相(切过机制)和粗大富Cu相(绕过机制)的共同析出,其耦合析出强化贡献高达500 MPa左右,要明显高于单一NiAl相的析出贡献(390 MPa)。所以同时结合切过机制和绕过机制的复合共格纳米粒子强化钢,预期在工程结构上有更大的应用潜能。
2.5 多相复合显微组织超高强韧钢
传统超高强韧钢是通过单相马氏体组织为基体和时效形成纳米析出相获得超高强度,但塑韧性一般都难以继续提高,这意味着通过单相马氏体基体组织获得超高强度和优良韧性的匹配存在瓶颈。当在马氏体基体组织上引入足量的其它辅助相,形成复合组织时,即马氏体基体保证了超高强度,而设计引入的其它辅助相则可抑制裂纹萌生和扩展,提高钢的韧塑性,这是开发超高强韧钢的另一思路。前文提到的超级贝氏体钢就是这一思路的成功案例,而近年来经过持续的研发,已经出现了具有双相甚至三相显微组织的高强合金钢。
Raabe等[86]研发了一种低碳中锰(9%~12%)钢,钢中含有1%~2%的Ni、Ti和Mo合金元素。钢板经淬火加时效处理后的显微组织由马氏体基体和15%的残余奥氏体组成,在马氏体基体上弥散析出大量10 nm大小的Ni3(Ti, Al)析出相。变形后获得1.5 GPa的抗拉强度和12%的良好塑性,强度和塑性的显著增加归因于马氏体中纳米析出相的析出强化和残余奥氏体TRIP效应的协同作用。Li等[87]研发的40SiMnNiCr钢经过适当的一步淬火加配分(Q&P)过程处理后获得2400 MPa的抗拉强度和超过10%的塑性。研究结果表明,经过Q&P处理后合金钢的强度首先增加,之后随配分时间的不断增加开始下降。强度开始下降的原因归因于奥氏体含量的增加,C过饱和马氏体的降低,马氏体中位错密度的减少以及过度碳化物的大量形成。Wang等[88]研发的Fe-0.5C-1.2Mn-1.2Si-1Ni-0.2Nb钢,基于Q&P工艺采用了新的淬火-配分-回火(Q-P-T)工艺,经Q-P-T工艺处理后,钢的拉伸强度超过2000 MPa,延伸率超过10%。Q-P-T钢的超高强度来自于硬相(马氏体)与软相(奥氏体)复合存在的双峰结构,并伴有细小分散的含Nb碳化物。室温下稳定存在的残余奥氏体和马氏体的软化共同提高了Q-P-T钢的延伸率。Qin等[89]基于在Mn钢中加入Si提高残余奥氏体稳定性的想法研发了Fe-0.6C-1.5Mn-1.5Si-0.6Cr-0.04Nb钢。热轧钢板正火后经过Q-P-T过程处理获得抗拉强度达1800 MPa,延伸率超过28%的良好力学性能。
通过调整热处理工艺,不仅可以得到板条马氏体与残余奥氏体组成的双相显微组织,还可以得到贝氏体、马氏体、残余奥氏体组成的三相显微组织。例如,Gao等[90]将Q&P或Q-P-T过程与贝氏体转变相结合,开发出了贝氏体淬火加配分(BQ&P)工艺,并应用于中碳Mn-Si-Cr合金钢中。在Q&P或Q-P-T过程的最初淬火阶段形成无碳化物贝氏体和马氏体,这些无碳化物贝氏体和马氏体分离奥氏体晶粒并减小未转化块状奥氏体的尺寸。随后的配分过程中,马氏体中C向其周围未转化的奥氏体扩散,最终在配分后形成板条贝氏体铁素体、马氏体和薄膜奥氏体组成的三相复合组织。BQ&P处理后合金钢获得抗拉强度1688 MPa,总延伸率25.2%,-40 ℃冲击韧性48 J/cm2的良好力学性能。
2.6 新型超高强韧钢的缺点
与传统超高强韧钢相比,新型超高强韧钢虽然具有前文提到的很多优点,但在制备和研发新型超高强高韧钢时仍然有各种未解决的问题。例如,纳米贝氏体钢的制备需要在低温进行长达数天的贝氏体转变,在实际生产中效率较低。如果想要加快贝氏体转变,就需要在钢中加入Cr、Co、Ni等贵重合金元素,这必然会引起生产成本的增加;另外,贝氏体相变所要求的温度工艺窗口通常较窄,大尺寸工件较难适用。如何在不添加贵重合金元素的前提下通过优化热处理工艺,缩短贝氏体转变需要的时间、增大热处理工艺窗口是今后发展超级贝氏体钢需要解决的难题。高密度可移动位错变形-配分钢中,正确控制每一步变形参数和热处理工艺是得到高密度可移动位错的关键因素,因此需要难度高的大载荷下轧制和对形变过程进行严格设计。对于多相组织钢和复合析出纳米粒子钢,其化学成分的微小变化都会引起合金钢的显微组织构成和复合粒子成分与析出顺序的不同。并且与单相显微组织或析出相相比,多相显微组织与复合纳米析出相之间的相互作用更加复杂,对超高强韧钢的作用机理还不是十分清楚,这些都是发展新型超高强韧钢面临的问题和需要解决的难点。
3中国国民经济发展对新型超高强度高韧钢的需求
我国经济近年来发展非常迅速,尤其是制造业规模已经跻身全球最大,基于中国独有的地理、资源的国情特色,发展了一批独具中国特色的军工和工程机械装备,它们也对超高强度、高韧性的特种钢有迫切需求,举例说明如下。
3.1 轻质超高强装甲钢
传统的超高强装甲钢包括瑞典的Armox系列装甲钢[91]、美国的MIL系列装甲钢[92]及澳大利亚的BISALLOY系列装甲钢[93]等。装甲钢的化学成分及主要性能如表7[91,92,93]所示。其多为Cr-Ni-Mo系低合金中碳钢,通过淬火加低温回火工艺获得超高强度的马氏体组织,起到很好的抵御作用。但是传统装甲钢中含较多Cr、Ni等贵重合金元素,生产成本较高,同时淬火马氏体钢的韧塑性一般较差,很难在获得超高强度的同时拥有高的韧塑性,装甲钢板经高速子弹冲击时会发生冲塞破坏,对装甲和防护人员产生直接的伤害。我国地域辽阔、地形复杂,军事作战需要长途跨区域作战和高的载弹量,都对战车的轻量化和移动性提出迫切需求,这就要求新一代装甲防护材料,在提高强度和韧性的同时还需要降低密度,以实现装甲钢板轻量化、提高车辆机动性和载弹量,因此需要研发密度更低的、新型轻质超高强韧装甲钢。
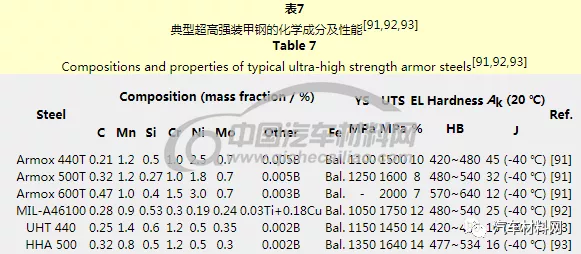
3.2 大型半自磨机用超高强韧耐磨钢
半自磨工艺由于流程简单(省去破碎机及筛分设备)、配置方便、投资小而作为现在主要的磨矿工艺在国内外被越来越多的矿山采用。衬板和提升条钢作为其中主要的受力构件,在半自磨机运作中,提升起的钢球下落时对筒体内部的衬板产生撞击,这就要求自磨机衬板和提升条钢拥有超高的强度、耐磨性和良好的韧性,能够承受钢球尽可能多次撞击不开裂。目前国内外使用的耐磨钢主要有3大类:奥氏体耐磨锰钢、低合金高强度耐磨钢及高铬系耐磨白口铸铁,如表8[94,95,96,97]所示。其中,低合金高强度耐磨钢具有生产工艺简单、硬度高(不低于360 HB)、耐磨性好、焊接性能好和易加工等优点,在半自磨机组上广泛使用。由于常用的半自磨机筒体较小,常在中、低冲击工况下运转,所以中碳Cr-Mo系低合金高强度耐磨钢可以满足普通半自磨机的工况使用。但是,我国富矿储量的枯竭,以及对金属需求的增加,导致需处理的矿石量日益增加,且随着现代矿山规模的发展,磨机及相应配套设备制造水平的提高,为半自磨设备大型化提供了应用基础及制造基础,且为了提高生产效率,自磨机大型化渐成趋势。目前全球最大的自磨机几乎多半是在中国生产,如江西耐普生产并在蒙古额尔登特安装的铜矿半自磨机组,设计规模在1.8×104 t/d。半自磨机直径高达10 m,在这样的高度下,由于钢球的冲击能量显著增加,导致现在使用的珠光体低合金高强耐磨钢服役寿命大幅度降低。曾经尝试将上述的超级纳米贝氏体钢用于此大型半自磨机组上的半自磨机衬板和提升条,经过实际运行一个月后,提升条均出现明显开裂,说明该钢依然不能满足该服役工况要求,需要研发具备更高韧性的新型超高强度钢,才能在如此苛刻的工况条件下长时间服役。
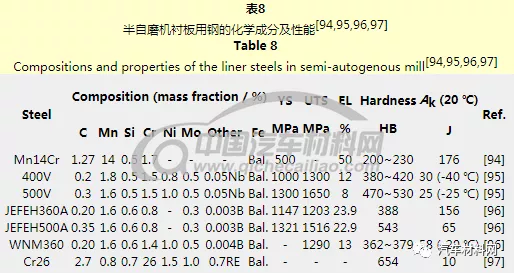
3.3 盾构机刃具用超高强韧钢
盾构机在地铁、能源输送及铁路交通等重大工程建设中应用广泛,具有开挖速度快、施工质量高、经济和环保等优点。作为盾构机关键部件之一的盾构刀具,是实现盾构机高效掘进功能的主要部件。因为盾构刀具在掘进破岩时不仅要承受很大的破岩作用力,同时又受到岩石硬矿物相的剧烈磨损,所以盾构刀具用钢需要具有高硬度、高强度及良好的冲击韧性,这样在掘进时盾构刀具既耐磨,又能在遭受巨大冲击时避免发生崩裂或塑性变形[98]。国内外常见的盾构机刀具用钢如表9[99]所示,此类钢多为中、高碳Cr-Ni-Mo系硬质合金钢,通过二次硬化作用析出大量合金碳化物提高钢的硬度和耐磨性。

我国幅员辽阔,从沿海地区到高山再到沙漠,各个地区的地质状况都不一样,即使同一地区的不同区域,地质状况也会存在较大差异。在盾构施工过程中,常会遇到各种不同地层,从淤泥、黏土、砂砾层到软岩及硬岩等,各种地层岩土的物理力学性能相差较大,对刀具的磨损机理不同,相应刀具的性能要求也不同。比如我国西部多山区,含有花岗石类型极硬岩石,刀盘在挖掘隧道推进过程中,由软地层进入较硬地层的瞬间,会有很高的瞬间载荷,容易使刀具产生崩落、脱落等情况。中铁工程总公司在实际施工和进行理论计算后均发现盾构机掘进不超过2 km,其盾构刀具既会出现严重损坏,须全部更换,即使采用国外进口刃具也于事无补,导致材料费用高昂且工程进度受阻[100]。所以研发超高硬度、耐磨性和优良韧塑性的盾构刀具用钢尤为迫切。
3.4 压裂技术采油工艺中压裂泵液力端用超高强韧钢
在石油开采中,压裂技术是目前充分采掘石油储藏的主要手段。它通过高压流体压裂地下深层的岩石,并产生足够大小的填砂裂缝增加油气的流动性,是提高油气采收利用率的一种有效方法[101]。传统的压裂泵液力端用钢主要有4330V[102,103]、4340钢[13,14]及其衍生钢42CrMo和43CrNi2MoV[104,105]。如表10[102,103,104,105]所示,常用于油气压裂泵液力端钢属于高强度钢,基本满足30 MPa以下工作压力的要求。但是近年来,为了缓解我国油气资源日渐枯竭的现状,国内石油工业随之向西部和沿海地区转移,同时国内汽车使用量逐年增加也加快内陆油气资源的开采,导致现有的油田浅层油藏已经基本开采殆尽,迫使石油开采向地层深处转移,这就要求将采油压裂泵的工作压力由30 MPa提高到100 MPa以上,这时压力泵液力端处于高温高压、沙粒冲刷和盐酸腐蚀的恶劣环境下,在超高强低合金钢表面更易产生裂纹,使得服役寿命从之前低压工况条件下的1000 h大幅度降低,不足300 h液力端就发生开裂和破坏,导致石油生产成本增高、效率下降[101]。因此,我国石油工程机械设备行业对用于高压压裂泵液力端的超高强、高韧和耐腐蚀用钢有迫切需求。
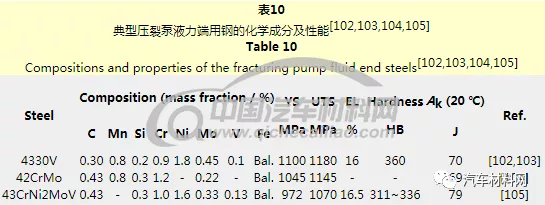
3.5 潜在的解决方案
上述这些钢种,尤其是大型球磨机、山体隧道挖掘盾构机刀具和高压压裂泵液力端所用钢,一方面要求显著提升现有钢铁材料的强度和韧性水平,形成对材料科学的挑战;另一方面,这些需求均与我国地理和资源特色相关,是我国国情特色在超高强高韧钢方面的具体体现,意味着研发这类服务国民经济的新型钢铁材料时,将无国际类似产品甚至类似研究作为参考,必须独立自主地对成分、组织和制备工艺进行创新。
作者在近年来关于中锰钢的研究中,发现该类型钢强度和韧性匹配均很出色,且制备工艺相对简单,成本经济。中锰钢是近年才出现的新钢种,因为其优越的强度和塑性成为国际钢铁材料界的热门研究对象。当钢中加入适量的C和Mn元素后,冷却至室温然后在马氏体形成温度(Ms)点以上温度配分后,可以获得马氏体加适量亚稳奥氏体的双相组织。马氏体基体可以保证材料基本的高强度,在变形过程中,亚稳的残余奥氏体发生TRIP或TWIP作用转变成马氏体,应力不断向未转变的奥氏体转移并生成新的马氏体,所以应力不容易集中,延缓了裂纹的产生和传播,导致抗拉强度升高的同时提高了延伸率、韧性。中锰钢中加入适量的铁素体形成元素Si和Al后,经过化学成分的合理配比,甚至可以在室温得到由马氏体基体、δ-铁素体和残余奥氏体组成的三相复合组织。多相复合组织与单相马氏体组织相比,在保证超高强度的同时可以有效分配应力以提高塑性和韧性。
作者团队基于上述思路,通过对中锰钢化学成分、加工及热处理工艺的合理设计,开发出了适合多种应用领域的高强韧和超高强韧中锰钢。例如,Zhu等[106]发现当在9Mn钢中加入0.3%V后,在奥氏体铁素体两相都析出纳米碳化物,导致300~400 MPa的强化增量(图7a[106])。Hu等[107]利用温轧工艺取代传统的热轧-冷轧工艺,通过部分再结晶获得不同形状和尺寸的残余奥氏体,因此残余奥氏体晶粒有很宽的机械稳定性范围;从而能在变形中逐步转变为马氏体。最终10Mn-V钢获得了超高强度(>1.5 GPa)与足够延伸率(>15%)的结合(图7b[107])。

另外,作者团队近期还研发出新型超高强韧中锰热轧轻质钢板。通过合理的成分设计、热轧和热处理工艺的仔细制定,得到了由高位错密度的板条马氏体、少量高温δ-铁素体和残余奥氏体组成的三相复合层状显微组织。钢中通过复合添加适量的Si和Al元素,成功使热轧板的密度由7.85 g/cm3降低到7.39 g/cm3,实现钢板减重近6%,节省燃料的同时也提高了装甲车辆的机动性。钢板经热轧加低温回火处理后的抗拉强度高达2.1 GPa,延伸率达到13% (图8a),-40 ℃的冲击功达到50 J。对钢板进行冷弯实验,弯曲压头半径取钢板6倍厚度,经90°弯曲后表面完好,没有产生裂纹(图8b),这表明该钢板在常温下冷加工成型性良好。对该钢板进行防弹实验,采用53式普通钢芯弹进行射击,射击距离80 m,测试结果如图8c所示。子弹射击后钢板正面产生凹陷,没有产生可见裂纹。表明新研发的中锰热轧钢板能够有效抵御子弹,用于军用装甲和民用防护的相关领域,对装甲和人员起到很好的防护作用。这一新型超高强韧钢的基本力学性能明显超过了目前现有的超高强韧钢,且具有密度低、成本经济的优点,这也证明了中锰钢作为超高强韧钢未来钢种的巨大潜力。


图9为各类型超高强高韧钢钢种的典型强度与韧性[20,21,22,23,24,27,28,36,37,38,39,40,42,43,44,45,46,89,90,108]。由此可见,二次硬化类型钢通常韧性较好而强度略逊,纳米贝氏体钢则是强度较高而韧性略逊,而低合金钢的强韧性匹配相对更好,作者团队所研发的7Mn中锰钢则将上述强韧性极限又提高到一个新的水平。在设计这一新类型钢时,需要考虑如下因素:(1) 将低合金钢通过单相淬火马氏体强化的思路转变为以马氏体为基体,同时引入次基体相如残余奥氏体、贝氏体铁素体、少量高温δ铁素体等形成多相复合显微组织,在发挥马氏体强化的同时,利用奥氏体的TRIP及TWIP作用和软相铁素体的变形作用提高韧塑性;(2) 高密度纳米共格析出相或复合析出多类型纳米粒子强化的设计,尤其是需要考虑当引入较多残余奥氏体或铁素体时,也必须让这些次基体相发生析出强化,提高屈服门槛;(3) 根据以马氏体为主基体加多种复合基体,并结合多类型析出相实现强韧化的的思路,在前期所积累的实验数据基础上,结合材料热力学和动力学计算设计化学成分和关键工艺,从而最终开发出符合严苛服役工况条件的新型超高强韧钢。综上所述,中锰钢在满足上述我国对超高强高韧钢特有需求方面有很大的潜力。

4总结与展望
经过几十年的发展,超高强韧性钢的研究取得了长足的进步。由最初的传统单相马氏体组织与半共格或非共格碳化物组成的超高强钢正在逐渐向板条马氏体、贝氏体铁素体、残余奥氏体与各种纳米共格析出相强化的、多相复合组织的超高强韧钢转变。近期研究结果表明,多类型析出强化和在马氏体基体上引入塑/韧性相阻碍裂纹扩展这一思路,将有助于进一步提高钢铁材料的强韧性极限,获得超高强度和优良韧塑性的更佳匹配。同时,由于我国国民经济的迅速发展以及国内独特的资源、地理特点,在轻质装甲钢、大型半自磨机、盾构机刀具及油田装备高压压裂泵等装备机械领域,都迫切要求开发出比现有钢材强度和韧性均大幅度提高的新型超高强韧钢,以满足更为苛刻的服役工况要求。因此,对不同类型析出相的耦合强化机制、马氏体基体与塑性相组成的复合组织强韧化机理等科学规律进行研究是必要的,积累相关数据和经验,并通过材料计算和实验研究,最终可望开发出满足我国经济建设所需的超高强韧合金钢。
免责声明:本网站所转载的文字、图片与视频资料版权归原创作者所有,如果涉及侵权,请第一时间联系本网删除。
相关文章
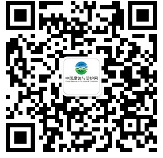
官方微信
《中国腐蚀与防护网电子期刊》征订启事
- 投稿联系:编辑部
- 电话:010-62316606-806
- 邮箱:fsfhzy666@163.com
- 中国腐蚀与防护网官方QQ群:140808414
点击排行
PPT新闻
“海洋金属”——钛合金在舰船的
点击数:7130
腐蚀与“海上丝绸之路”
点击数:5741