摘要:高强度不锈钢作为强度、韧性及服役安全性俱佳的金属结构材料,广泛应用于航空、航天及海洋工程等领域。本文系统地梳理了高强度不锈钢的研究及发展历程,重点阐述了以析出强化和奥氏体韧化为代表的强韧化机理,及以氢致开裂和H原子扩散富集为主要因素的应力腐蚀及氢脆敏感性问题。认为高强度不锈钢的未来发展将重点关注计算模拟设计,多类型、高共格度析出相复合强化,高机械稳定性的薄膜状奥氏体韧化,综合显微组织和服役环境加深对应力腐蚀及氢脆机理的理解,从而为设计兼备超高强韧性、优良综合服役性能的高强不锈钢提供实际的理论依据。
关键词: 超高强度不锈钢 ; 强韧化机理 ; 氢脆 ; 应力腐蚀 ; 析出相 ; 逆转变奥氏体
高强度不锈钢因其具有优异的强韧性匹配及耐蚀性,在航空航天、海洋工程及能源等关系国计民生的装备制造领域得到广泛的应用,如飞机的主承力构件[1]、紧固件、卫星陀螺仪、飞船外壳、海洋石油平台、汽车工业、核能工业、齿轮和轴承制造等,是未来装备部件轻量化设计和节能减排的首选材料。作为承力、耐蚀结构件的重要候选材料之一,如何兼顾超高强韧性及优良的服役安全性是此类钢种未来的重点发展方向[2,3]。
1.超高强度不锈钢的发展历程
为了满足航空航天、海洋工程对高性能耐蚀结构钢的需求,美国Carnegie Illionois钢铁公司于1946年成功研发了第一代马氏体沉淀硬化不锈钢——Stainless W。在Stainless W钢合金体系的基础上,通过加入Cu、Nb元素并去除Al、Ti元素。美国Armco钢铁公司于1948年开发了17-4PH钢[4],因其良好的强韧性及耐蚀性,除应用于F-15飞机起落架构件外,目前亦广泛应用于制造紧固件及发动机零部件,但其冷变形能力较差。为了减少对横向力学性能不利的高温δ-铁素体,通过降低铁素体形成元素Cr的含量并增加Ni元素含量,研发出了15-5PH钢[5,6,7],该钢克服了17-4PH钢横向塑韧性差的缺点,现已应用于制造舰船及民用飞机等承力部件。20世纪60年代初,国际镍公司发明了马氏体时效钢,为发展高强度不锈钢引入了马氏体时效强化这一概念,从而拉开了马氏体时效不锈钢发展的帷幕。1961年美国Carpenter Technology公司首先研制了含Mo的马氏体时效不锈钢Custom450;此后,在1967和1973年先后研制了Pyromet X-15、Pyromet X-12。在此期间,美国也先后研制了AM363、In736、PH13-8Mo、Unimar CR等;Martin等[8,9]则分别于1997年和2003年获得了Custom465和Custom475钢的发明专利,并应用在民航飞机上。英国研发了FV448、520、520(B)、520(S)等高强度不锈钢牌号。德国于1967、1971年研制了Ultrafort401、402等。前苏联除仿制和改进美国钢号外,还独立研究了一系列新钢种,常见的钢有0Х15Н8Ю、0Х17Н5М3、1Х15Н4АМ3、07Х16Н6等以及Co含量较高的钢号,如00Х12К14Н5М5Т、00Х14К14Н4М3Т等。2002年美国QuesTek公司承担美国国防部战略环境研究与发展计划(SERDP)污染防止项目,通过材料基因组计划设计并开发了新型飞机起落架用超高强度不锈钢Ferrium?S53[10],于2008年底发表公开AMS5922宇航标准,Ferrium?S53强度约1930 MPa,断裂韧度(KIC)达到55 MPa·m1/2以上,在2017年增编入美国的MMPDS主干材料手册中,该材料已经成功应用于美国的A-10战机及T-38飞机,是下一代舰载机起落架的首选材料。
我国从20世纪70年代开始高强度不锈钢的研制工作,典型牌号有00Cr13Ni8Mo2NbTi、00Cr12Ni8Cu2AlNb、00Cr10Ni10Mo2Ti1等10余种[11]。2002年钢铁研究总院设计并研制出一种新型的超高强韧性的不锈钢材料,是我国自主研发并具有自主知识产权的Cr-Ni-Co-Mo合金体系的超高强度不锈钢USS122G,其强度超过1900 MPa,KIC达到90 MPa·m1/2以上[12]。目前该材料已经突破了直径300 mm大规格棒材制备的相关关键技术,在我国航空航天装备制造领域具有广泛的应用前景。
2.超高强度不锈钢的研究现状
超高强度不锈钢良好的综合服役性能主要包括超高强度、优良的塑性及韧性,与传统低合金高强钢及二次硬化型超高强度钢相比,除具备优良的综合力学性能以外,还具有优异的耐腐蚀、抗应力腐蚀及腐蚀疲劳性能。为了提高上述服役性能,揭示其背后的影响因素及机理,国内外学者围绕超高强度不锈钢的强韧化机理、应力腐蚀开裂以及氢脆行为进行了广泛研究。
2.1 高强度不锈钢中的合金设计及强化相
超高强度不锈钢的典型室温组织包括:细小的板条马氏体基体,适量的残余(或逆转变)奥氏体以及弥散分布的沉淀强化相。板条状马氏体由于其自身的高位错密度,具有很高的强度。亚稳残余(逆转变)奥氏体可以缓解裂纹尖端的应力集中从而提高材料韧性。时效处理过程中析出的纳米级强化相可以进一步提高钢的强度,按照析出相的合金组成可将其分为3类,即碳化物(MC、M2C)、金属间化合物(NiAl、Ni3Ti)以及元素富集相(ε相、α‘相)等,在超高强度不锈钢中,沉淀相的强化潜力取决于沉淀相的本质及其尺寸、数密度、体积分数及空间分布情况等。能否获得最优性能主要取决于对沉淀相析出行为的热、动力学特性的掌控,进而指导合金成分的调控以及热处理工艺的制定。典型超高强度不锈钢的化学成分和力学性能见表1[13,14,15,16,17,18,19,20,21]和2[13,14,15,16,17,18,19,20,21]。从表中可以看出,第一代超高强度不锈钢(15-5PH、17-4PH)强度级别较低(1200~1400 MPa),此类钢中的主要强化相为元素富集相,如ε-Cu相;第二代高强度不锈钢(PH13-8Mo、Custom465)中,C含量普遍较低(不大于0.05%,质量分数,下同),主要强化方式为NiAl和Ni3Ti等金属间化合物强化;作为第三代高强度不锈钢的典型代表Ferrium?S53钢的诞生得益于材料基因数据和计算机技术,将C的质量分数增加到0.21%,M2C型碳化物的二次硬化作用使材料性能得到大幅度提升,不同于Ferrium?S53钢的合金设计理念,国产USS122G钢采用了两相复合强化体系,相比于Ferrium?S53钢具有更佳的强韧性匹配。
作为第一代高强度不锈钢的典型代表,15-5PH钢的合金化特点是采用15%左右的Cr来保证钢的耐腐蚀性能;5%左右的Ni含量可以起到平衡实验用钢的Cr-Ni当量,使钢在室温得到马氏体组织,同时降低钢中δ-铁素体;加入4%左右的Cu,起到了强化作用;少量的Nb可以与C形成MC相,起到了钉扎晶界、细化晶粒的作用。经过550 ℃时效处理后,在马氏体基体上析出大量fcc结构的富Cu相,富Cu相与马氏体基体的取向关系满足K-S关系。Habibi-Bajguirani等[22,23]的研究显示,15-5PH钢在时效过程中存在2种不同类型的Cu的析出相,在低于500 ℃时效时,会首先形成bcc结构的簇状颗粒,这种簇状物会随后演变为9R结构,最后转变为fcc的沉淀析出相,对析出相萃取物的X射线微区分析结果显示,这种析出相实际上是富Cu相。在650~700 ℃时效时,fcc的富Cu相一开始与基体保持共格关系,随后转变为半共格的K-S关系。
作为第二代高强度不锈钢的典型代表,PH13-8Mo采用低碳的合金化设计,采用13%左右的Cr来保证钢的耐蚀性,8%左右的Ni可以弥补由于低碳而引起Schaeffler图中Cr-Ni当量不平衡,降低δ-铁素体含量,可使钢得到板条马氏体组织,加入1%Al可在钢中形成强化相,起到强化基体的作用[24,25]。Schober等[26]研究了Ti元素对时效过程中析出相演变规律的影响,结果表明,在未添加Ti元素的PH13-8Mo钢中,析出相仅有NiAl相,添加Ti元素后,钢中的析出相为G相和η相。在时效处理初期未添加Ti元素的PH13-8Mo钢中析出的是有序的金属间化合物NiAl,随着时效时间的延长,NiAl相中的合金元素逐渐趋于化学计量平衡并且硬度达到最大值。在添加Ti元素的钢中,在时效处理初期钢中析出一种富含Ni、Si、Al、Ti的析出相,钢的硬度在此时达到最大值。随着时效时间的延长,钢中会形成椭球状的Ni16Si7Ti6-G相和短杆状的Ni3(Ti, Al)-η相。
在超高强度不锈钢的成分设计时,为保证钢具有良好的耐腐蚀性能,一般钢中Cr的含量应大于10%,Cr也是降低马氏体相变温度的元素。Ni可以提高不锈钢的电位和钝化倾向,增加钢的耐蚀性能,提高钢的塑性和韧性,特别是钢在低温下的韧性,Ni还会形成强化作用的η-Ni3Ti相。加入Mo主要是增加了二次硬化效应,2%左右的Mo可使钢在不同固溶处理条件下均保持较高的硬度,在时效过程中析出的富Mo析出相起到了强化作用,同时能使钢保持良好的韧性,Mo还可以提高不锈钢的耐海水腐蚀性能。Co可以抑制马氏体中位错亚结构的回复,为析出相的形成提供更多的形核位置,降低Mo在α-Fe中的溶解度,促进含Mo的析出相生成,起到了间接强化的作用[25]。另外,在钢中加入少量的Ti会明显提高钢的强度,但过量的加入则会使钢的韧性下降。Li等[27]研究了一种强度高达1900 MPa的Cr-Ni-Co-Mo系的马氏体沉淀硬化不锈钢,认为超高强度的获得是由于多种强化相复合强化的结果。该钢的名义成分为0.004C-13.5Cr-12.7Co-3.3Mo-4.4Ni-0.5Ti-0.2Al (原子分数,%),钢中的析出相主要有3种,η-Ni3(Ti, Al)相、富Mo的R’相和富Cr的α‘相,这些析出相分别是由时效初期富Ni-Ti-Al、富Mo和富Cr的簇状颗粒转变而来,时效过程中由于富Mo R’相和富Cr α‘相的隔离作用使η-Ni3(Ti, Al)相长大缓慢。
从高强度不锈钢的发展来看,随着强度级别的提升,由单一强化相强化逐渐向多相复合强化发展,相较于单一种类析出相的强化,复合强化更有利于钢强度的进一步提升。然而,合金成分和时效制度对于不同种类沉淀相的析出和长大行为的影响差异较大。考虑到不同合金成分和热处理制度在设计新钢种时可以获得不同的多种的沉淀相,采用传统的试错法实验和基于数据积累的人工神经网络模拟在合金设计过程中仍存在不足,因此亟需一种新型的基于物理冶金的模型[28]。Xu等[28,29,30]和Parn等[31]提出了一种基于机器学习的合金成分计算模型,此模型整合了合金成分和相应的热处理参数,实现了所需的性能在遗传框架内演变。此模型应用于设计以MC碳化物为强化相的超高强度钢,亦适用于Cu团簇、Ni3Ti、NiAl沉淀相,也可应用于设计一种由多种类强化相,包括MC碳化物、富Cu相和Ni3Ti金属间化合物共同强化合金。模型包括了对钢力学性能、耐蚀性能以及显微组织等相应参数的模拟,为合金的成分设计提供了更为可靠的路径。
2.2 高强度不锈钢中的韧化相及韧化机理
逆转变奥氏体对高强度不锈钢韧性的影响与其形貌、含量、弥散度和稳定性等有紧密的关系,其特征又受到热处理过程的加热速率、等温温度和时间、奥氏体形成元素的扩散和偏析、奥氏体的形核位置、尺寸以及基体内部位错密度的影响。现有研究表明,逆转变奥氏体的形成机制有如下3种,即无扩散切变逆转变机制[32]、变体限制机制[33]以及残余奥氏体长大机制[34]。切变机制源于奥氏体向马氏体的无扩散切变机制的逆过程,与原奥氏体保持一定晶体学位相关系的马氏体形成的逆转变奥氏体,与原奥氏体保持相同的位相关系。变体限制机制则指出,由扩散控制的逆转变奥氏体形成过程中,其形核位置将与原奥氏体、碳化物及基体严格保持一定的晶体学位相关系,因此限制了逆转变奥氏体的变体种类。而残余奥氏体长大机制则认为,马氏体钢中淬火后残留下的奥氏体会在其后的回火过程中通过奥氏体稳定元素的扩散不断长大,从而进一步“逆转变”为新的奥氏体组织。对0Cr13Ni4Mo马氏体不锈钢的研究[34]显示,在稍高于奥氏体转变开始温度(AS)的两相区回火时,碳化物(Cr23C6)和奥氏体共同析出。进一步分析碳化物和奥氏体及其界面上的Cr、Ni元素分布情况,发现Cr在碳化物中的偏聚促进了Ni元素向逆转变奥氏体中的配分,Ni元素的富集降低了逆转变奥氏体形成的化学驱动力并增加了界面能,因此,富Ni区域可作为逆转变奥氏体在回火过程中的形核点位,即逆转变奥氏体的形成受到Ni元素扩散的控制。进一步提高回火温度,虽然原子的扩散更为显著,但是由于温度的提高,回火马氏体向奥氏体的转变驱动力条件已得到满足,故此时的逆转变奥氏体形成机制为无扩散的切变机制。为了进一步说明变体限制机制,Nakada等[35]研究了逆转变奥氏体同原奥氏体及马氏体基体的晶体学位相关系。13Cr-6Ni钢回火后,一个原奥晶粒内,逆转变奥氏体不仅均匀分布于马氏体板条界,其同位相束(blocks)和板条群(packets)界面处亦存在逆转变奥氏体,并且大部分与原奥保持相同取向,而少部分取向与原奥氏体不同。一个原奥氏体惯习面和一个马氏体板条群中可能存在12种逆转变奥氏体变体的位相关系。可以看到,在遵循K-S关系的前提下,只存在与密排面平行的6种不同方向的马氏体板条束,每一种马氏体板条束内部只存在2种逆转变奥氏体变体。这说明由于奥氏体在{111}γ晶面族的三重对称性,一个马氏体板条群中的12种逆转变奥氏体变体可被分为2类,即与原奥保持相同取向的V1变体和与V1具有孪生关系的V2变体。根据Lee和Aaronson提出的二维构建模型[35],逆转变奥氏体的临界晶核形状应当满足最小化形核能的要求。在板条界面处形成的逆转变奥氏体通常与原奥氏体晶粒的取向一致,其核心的α'/γ界面与马氏体基体两侧均保持K-S关系,而原奥晶界处的奥氏体核心只与一侧的基体保持了K-S关系。因此,原奥晶界处的逆转变奥氏体由于被共格和非共格界面包裹,及两侧界处表面能和弹性应变能的差异,会形成圆球状的形貌,而位于板条界的逆转变奥氏体则倾向于形成长条针状形貌。
逆转变奥氏体含量的增加可以提高材料的塑性和韧性,而过多的逆转变奥氏体往往会导致钢屈服强度的恶化。Schnitzer等[36]分别计算了PH13-8Mo中强化相NiAl和韧化相逆转变奥氏体对整体屈服强度的影响,时效处理后屈服强度40%的降低量归因于高含量的逆转变奥氏体,其余则归于NiAl相的粗化。因此在要求高韧性的情况,应采用较高的时效温度使逆转变奥氏体含量提高[37],但需以损失材料的强度为代价。另外,一些研究中也发现逆转变奥氏体对塑性的不利作用,如Viswanathan等[38]的结果表明,逆转变奥氏体对塑性的提高仅在时效初期出现,时间延长同样会使材料发生严重的脆性断裂。
2.3 高强度不锈钢的氢脆敏感性和应力腐蚀研究
随着强度级别的升高,高强度钢对应力腐蚀开裂(stress corrosion cracking,SCC)和氢脆(hydrogen embrittlement,HE)亦越发敏感。尤其,当污染性或腐蚀性气体组分及H原子与应力联合作用于高强度钢时,极易导致裂纹萌生并逐渐扩展直至开裂。此种断裂是服役于腐蚀环境中的高强度钢结构件的主要失效形式,造成了巨大的安全隐患和财产损失。
2.3.1 氢脆敏感性
可扩散氢是造成钢塑性损失的主要因素[39],任何降低可扩散氢的移动性的措施均可有效提高材料的氢脆敏感抗力。强氢陷阱可显著增加钢吸收过饱和氢的含量,从而使得进入基体中的氢无害化。上述观点在观察高强钢的氢致延迟断裂的现象中得到了一定程度的证实,即当高强钢在低于其抗拉强度的静态应力作用下,其会在服役一段时间发生瞬时脆断,这种在静载荷下发生的失效是由于侵入基体的H原子造成的[40]。作为钢中最主要的强化相和韧化相,时效过程析出的大量弥散分布的第二相强化粒子和逆转变奥氏体均可视为钢中重要的氢陷阱。大量研究聚焦于通过热处理工艺调控钢中的“良性氢陷阱”(benign hydrogen traps)的数量及密度来阻止H在材料中的扩散,从而提高材料的氢脆敏感抗力。大量研究显示碳化物是钢中典型的“良性氢陷阱”并可以有效提高钢的氢脆敏感性。例如,通过球化渗碳体颗粒或通过在奥氏体单相区内成形冷却后快速加热到回火温度细化渗碳体,可有效提高钢的氢脆敏感抗力[41]。此外,通过添加Ti、V、Nb等微合金化元素,在钢中形成了TiC、VC、NbC等碳化物,均可作为有效的氢陷阱[42,46]。Takahashi等[47,48]利用APT直接观察到了TiC和V4C3陷阱捕获了氘原子。H主要被捕获于TiC和基体的界面上,而V4C3中的陷阱点位主要是半共格界面上错配位错(misfit dislocation)芯部位置。借助第一性原理计算和有限元分析,进一步证实对于TiC析出而言,TiC-基体界面是主要的氢陷阱,而碳空位是V4C3中的主要陷阱位点[49]。
金属间化合物及元素富集相作为氢陷阱的研究则鲜有报道。近期,Li等[50]对比了蒸汽轮机末级叶片用17-4PH钢和PH13-8Mo钢的氢脆行为,其研究结果表明,钢中析出相的类型以及马氏体基体与析出相的晶体学关系,是导致PH13-8Mo钢相较17-4PH钢具有更高的表观氢扩散系数和更低的表观氢溶解度的主要原因。17-4PH钢中存在与基体非共格的富Cu相,相较于PH13-8Mo钢中的共格β-NiAl相,其对H原子具有更强的捕获能力。这是因为富Cu相的八面体间隙的半径为0.0529 nm,约为β-NiAl相八面体间隙的半径(0.0206 nm)的2倍。而且,同β-NiAl相与基体的共格界面相比,富Cu相与基体的非共格界面可捕获更多H原子。此外,共格界面上错配位错的芯部和临近芯部的畸变程度较小的晶格均为弱氢陷阱[51,52],且非共格析出相的氢脱附能(de-trapping energy)高于共格析出相的脱附能[53]。
与马氏体基体相比,H在残余(或逆转变)奥氏体的扩散速率更低(在奥氏体中的扩散速率:10-15~10-16 m2/s,在马氏体中的扩散速率:10-10~10-12 m2/s),且H在奥氏体中的溶解度相较马氏体更高。此外,奥氏体对于H的钉扎能可达55 kJ/mol[54],使其可作为不可逆H陷阱位点。然而,对于不同体系钢中奥氏体相对于材料的氢脆敏感性的影响仍存在广泛的争议。一些结果[55,56]表明,钢中的逆转变奥氏体和细小的残余奥氏体可有效阻止H在基体中的扩散,从而提高了钢的氢脆敏感抗力。与此相反,亦有学者[57,58]指出固溶进入奥氏体中的H原子可降低其层错能,使得TRIP效应更易发生,新生马氏体作为“氢源”会释放出H原子,从而造成材料的脆化[59]。Fan等[60]报道了逆转变奥氏体对于S41500马氏体不锈钢(名义成分为0.04C-13Cr-4.1Ni-0.6Mo-0.7Mn,%)的氢脆断裂行为的影响,H原子主要富集于富Ni的逆转变奥氏体中,而奥氏体/马氏体界面及奥氏体/碳化物界面处无H原子的富集。回火处理后试样准解理断口的TEM观察结果显示,断裂路径是沿着回火马氏体和发生相变诱导塑性(TRIP)效应新生成的马氏体(NFM)的界面,这是因为大部分的H已被逆转变奥氏体捕获,而非偏聚在原奥晶界处,从而降低了逆转变奥氏体的稳定性,促进了马氏体相变。相变发生后,新生马氏体将作为氢源释放大量的H原子,使得其周围界面聚集了大量的H原子,所产生的断口形貌为准解理形貌而非沿晶断裂形貌。
氢致裂纹一般于板条、同位相束、板条群及原奥晶界处形核,而后裂纹在外应力的作用下穿过板条束,沿着板条群和原奥晶界扩展。高强度不锈钢中众多马氏体多级组织界面(原奥氏体晶界、马氏体板条群界、马氏体板条束界及马氏体板条界)以及相界是高强度不锈钢具有较高氢脆敏感性的原因之一。对17-4PH钢中氢的扩散和氢脆行为的研究结果显示,固溶态试样的氢脆敏感抗力高于峰时效态试样,此现象主要是因为在时效态试样中富Cu相和基体的相界面相捕获了较多的H,界面结合力的弱化造成了峰时效态充氢试样的脆断。随着固溶处理温度的升高,17-4PH钢的氢脆敏感性和氢的扩散系数均呈先上升后下降的趋势。这主要归因于固溶温度对于钢中原奥氏体晶界和其后时效处理过程中析出相的数密度的影响,伴随着固溶温度的升高,原奥晶粒变大、晶界面积减小,但基体对于Cu原子的固溶度增加,促进了时效过程中富Cu相的析出,而析出相密度及尺寸的增加提供了更多的相界面,二者共同提供了可捕获H的界面。
显然,高强度不锈钢的氢脆敏感性是由钢中复杂多级及多相组织共同决定的,由于分析表征手段的限制,仍很难定量确定各类氢陷阱对于高强度不锈钢的氢脆敏感性的影响。基于不同强度级别、利用不同强化体系强化的高强度不锈钢的氢脆敏感性影响因素仍待系统而深入的研究。具有复杂合金体系、多相耦合强化的超高强度不锈钢的氢脆敏感性更是亟待研究。目前,笔者团队研发了一种由多相复合析出强化的新型2200 MPa级高强度不锈钢,该实验用钢的名义成分为0.2C-9Cr-4.2Ni-3.1Mo-15.2Co-0.3V-0.9W (%),其双时效态试样的APT分析结果如图1所示。由图可见,钢中存在明显的富Mo/Cr/C、Mo/Cr及单纯的富Cr团簇,进一步分析可知钢中的析出相包括金属间化合物、碳化物及富Cr相,其超高强度是由3种析出相耦合强化获得的,亦是目前已报道的强度级别最高的高强度不锈钢。笔者团队亦在进行该钢种的氢脆敏感抗力的相关研究,以期揭示不同种类析出相耦合强化高强度不锈钢中不同种类氢陷阱共同作用对其氢脆敏感抗力的影响,为提高2200 MPa级超高强度不锈钢的综合服役性能提供理论依据。
图1 新型高强度不锈钢时效态试样APT表征结果
2.3.2 应力腐蚀开裂
美国飞机部件破坏调查报告显示,应力腐蚀开裂是飞机关键承力部件在服役过程中发生突发性破坏事故的主要形式之一,起落架多数是由于应力腐蚀或疲劳裂纹扩展而导致最后断裂[61]。目前,不仅是在航空、航天、能源、化工等高新技术和产业,在几乎所有常用的耐腐蚀钢种和合金中都会发生应力腐蚀现象。因此,分析超高强度钢应力腐蚀开裂机理,并对影响超高强度钢的应力腐蚀的因素进行分析,对确定超高强度钢应力腐蚀防护措施具有重大的科学价值和现实意义。
材料的耐蚀性能成为限制高强度钢应力腐蚀开裂的重要因素,而点蚀是最为常见也是危害最大的腐蚀形式。多数应力腐蚀开裂均起源于点蚀坑,超高强度不锈钢由于时效处理过程中,从过饱和马氏体基体中脱溶的析出相造成了显微组织的不均匀性,是超高强度不锈钢发生点蚀的主要根源。析出相附近钝化膜比较薄弱,Cl-的侵入引起钝化膜的破坏,析出相和基体之间形成微电池,从而使基体溶解,析出相剥落,形成点蚀。例如,富Cr型的碳化物M23C6、M6C和金属间化合物Laves相和σ相等周围易形成贫Cr区,造成点蚀现象的发生。Luo等[62]和余强[63]利用三维原子探针层析技术研究了时效时间对15-5PH超高强度不锈钢组织和电化学行为的影响,在时效时间为1~240 min时观察到了富含Cu的团簇和(Cu, Nb)的纳米颗粒,与短期时效处理相比,长期时效处理后的样品表面更容易受到Cl-的侵蚀。在时效240 min后,析出物周围的Cr含量也会下降,这些部位易形成贫Cr区。而钝化膜中Cr/Fe比值的降低是导致钝化膜耐点蚀性能下降的原因。除此之外,富Cr型碳化物在晶界上的连续析出会降低钢的耐晶间腐蚀性能。例如,研究[64]发现,AISI 316Ti不锈钢比AISI 321不锈钢具有更高的抗晶间腐蚀性能,究其原因是由于TiC的析出减少了富Cr型碳化物的形成,而富Cr碳化物是导致晶间腐蚀的析出物之一。
作为高强度不锈钢中最主要的韧性相,奥氏体的含量、形貌、尺寸及稳定性同样会影响钢的应力腐蚀敏感性。在尺寸、形貌及稳定性相同的情况下,随着奥氏体含量的增加,应力腐蚀开裂门槛值(KISCC)增大,钢的应力腐蚀开裂敏感性降低。究其原因,是因为马氏体板条界上形成的薄膜状奥氏体组织提高了钢的韧性,降低了氢致裂纹的扩展速率,造成裂纹扩展速率降低的主要原因有2点,其一:裂纹由马氏体基体扩展至薄膜状的奥氏体时,无论是继续扩展进入奥氏体内部或是改变扩展方向绕过奥氏体组织,均会消耗较大的能量,导致裂纹的扩展速率降低,抗应力腐蚀敏感性提高;其二:如前所述,H在奥氏体组织中有较高的固溶度,较低的偏聚倾向,且H在奥氏体中的扩散速率远比在马氏体组织中的小,是高强度不锈钢中有益的氢陷阱,导致裂纹前端的氢脆敏感性降低,进而裂纹的扩展速率降低,应力腐蚀敏感性提高。需要说明的是,奥氏体的稳定性同样是决定钢应力腐蚀敏感性的关键参数,应力或应变诱导发生马氏体相变后,由奥氏体转变的新鲜马氏体非但不能抑制裂纹的扩展,还会作为新的氢扩散源导致钢氢脆敏感提高。
综上所述,钢的强韧性、应力腐蚀及氢脆敏感性均受到复杂多级多相组织的影响,而采用传统试错法设计和制备兼具超高强韧性及优良服役性能的超高强度不锈钢难度大、周期长、成本高。相比于试错法,理性的设计方法,例如通过建立“原子尺寸-纳米尺度-微米尺度”等一系列多尺度的强韧性、应力腐蚀性能及氢脆性能分析模型,将更具有目的性。通过模拟分析结果建立高强度不锈钢的设计标准,优化钢中析出相、马氏体及奥氏体组织的形态、尺寸及含量等,进一步将多尺度模拟和实际材料研发过程相结合,将大大降低材料研发难度,减少成本投入并缩短研发周期。
3 展望
作为兼备优良强韧性及服役安全性的金属结构材料,高强度不锈钢在未来的航空、航天、海洋工程及核工业等领域有着广阔的应用前景。鉴于此类钢种苛刻的应用环境,对新一代高强度不锈钢的探索除了着眼于进一步突破超高强度-优良塑韧性匹配的瓶颈,还应该兼顾优良的服役安全性。在合金设计和热处理工艺制定过程中,由传统的试错法逐渐过渡到热/动力学辅助合金设计、人工智能机械学习等理性设计方法,以极大提高新型高强度耐蚀合金的研发周期、节约研发成本;对于高强度不锈钢中强韧化机理的研究仍待进一步深入,尤其是对多相复合强化第二相粒子的析出行为的理解及强化贡献值的叠加;对于钢中奥氏体含量、尺寸、形貌及稳定性对高强度不锈钢韧性影响的研究较为充分,但仍未建立有效的数学模型定量估算其对于该钢种韧性的贡献量;此外,对于超高强度级别高强度不锈钢复杂强化体系下的应力腐蚀断裂机理和氢脆敏感性的研究亟待解决,从而为超高强度级别高强度不锈钢的耐久性设计提供可以借鉴的理论依据。
免责声明:本网站所转载的文字、图片与视频资料版权归原创作者所有,如果涉及侵权,请第一时间联系本网删除。
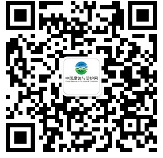
官方微信
《中国腐蚀与防护网电子期刊》征订启事
- 投稿联系:编辑部
- 电话:010-62316606-806
- 邮箱:fsfhzy666@163.com
- 中国腐蚀与防护网官方QQ群:140808414