QPQ技术在国内已经普遍大量应用,但由于它的化合物层太浅,在应用方面有相当大的局限性,无法适用于要求耐磨性和耐蚀性更高的零件。深层QPQ技术是在保留原有QPQ技术优点的基础上开发的新技术,其化合物层的深度达到30μm以上,为普通QPQ技术的一倍多,抗盐雾腐蚀能力从140h提高到300h以上,其抗蚀性远高于镀铬、镀镍等表面防腐技术的水平,因此应用范围要比普通QPQ技术广泛得多[1]。目前,深层QPQ技术所具有的高抗蚀性引起了有关行业,尤其是石油、化工、工程机械等腐蚀问题较为严重的行业的极大关注。这对深层QPQ技术的发展和研究以及应用推广注入了新的活力。本文以中低碳钢以为例,从微观角度对深层QPQ技术的高抗蚀机理进行了分析和探讨。
成都工具研究所曾在国内率先开发了QPQ技术,近年来又率先开发了深层QPQ技术,深层QPQ技术主要包含以下几道工序:在深层QPQ氮化盐浴中进行渗氮,在氧化盐浴中进行氧化,然后抛光,再进行二次氧化,在整个处理过程中渗层质量好坏主要取决于深层QPQ盐浴配方优化与否。因此通过对深层QPQ技术的盐浴配方进行了多次的优化试验,提高了盐浴稳定性和渗氮效果,从而大大加深了渗层的深度,改善了渗层质量。并在石油管、工程机械活塞杆以及紧固件等工件上进行了试验,取得了较好的试验结果。
深层QPQ技术提高抗蚀性的机理
本文通过研究深层QPQ处理渗层的微观结构和氮碳氧元素浓度分布以及相组成,来分析深层QPQ技术高抗蚀性的原因。
1.金相分析
图1a、图1b分别为45钢和20钢常规QPQ处理的金相图片,从图中可以看出,渗层由疏松层、化合物层和扩散层组成。 45钢经常规QPQ处理后化合物层厚度为18~20μm,疏松层厚度为5~8μm,20钢经常规QPQ处理后化合物层厚度为18~20μm,疏松层厚度为6~9μm。
(a)45钢
(b)20钢
图1 常规QPQ处理的金相图片
图2a、图2b分别为45钢和20钢深层QPQ处理的金相图片,从图中可以看出,渗层由疏松层、化合物层、中间层和扩散层组成;疏松层是化合物层的一部分,是化合物层外面的不致密的部分。45钢经深层QPQ处理后化合物层厚度为45~47μm,疏松层厚度为7~10μm,中间层厚度为14~16μm,中间层往里为扩散层。20钢经深层QPQ处理后化合物层厚度为50~52μm,疏松层厚度为8~11μm,中间层厚度为15~18μm,中间层往里为扩散层。
(a)45钢
(b)20钢
图2 深层QPQ处理的金相图片
从图1、图2中可以看出,常规QPQ处理45钢、20钢的化合物层的深度偏浅,仅15~20μm,经过深层QPQ处理后,化合物层的深度由15~20μm加深到30μm以上,为普通QPQ技术的一倍多,氮化层具有比基体材料更高的抗蚀性,在各种渗氮技术的应用中已获得公认。因此,经过深层QPQ处理后化合物层厚度增加对提高抗蚀起了关键的作用。
2.渗层的X射线衍射分析
深层QPQ处理20钢渗层的X射线衍射谱线如图3所示。渗层的最表面主要由Fe3O4和Fe3N相组成。这是由于渗层最外层的氧化膜很薄,在对最表层进行X射线衍射时会穿透氧化膜达到化合物层,因此渗层的最表面的相包括氧化膜和疏松层的Fe3O4,还有化合物层中的Fe3N(ε相)。
图3 深层QPQ处理20钢试样渗层的X射线衍射图
3.扫描电镜显微组织和氮碳氧元素浓度分布
图4是20钢经深层QPQ处理后在扫描电镜下观察到的渗层显微组织,最外层为氧化膜,向内为疏松层、化合物层、中间层和扩散层。疏松层是化合物层的一部分,是化合物层外面的不致密的部分。从图片可以看出,图4与图2d基本吻合,并最终观测到了最外层的氧化膜,氧化膜厚度为5~10μm。从图中可以清楚的看到,在工件表面疏松氮化层上形成高抗蚀的Fe3O4氧化膜。深层QPQ技术具有高抗蚀的原因就在于这层摩擦系数低、化学稳定性好的Fe3O4氧化膜的存在。氧化膜隔断了腐蚀介质和氮化层之间的通道,保护氮化层不受腐蚀。因此,在基体材料的表面有Fe3O4氧化膜和更深氮化层的双层保护,使工件在QPQ处理后具有高抗蚀能力。
图4 深层QPQ处理20钢渗层的显微组织 700×
为了明确了氧元素进入化合物层内部的详细情况,以及氧元素进入化合物层内部与疏松的关系。作者对经深层QPQ处理的试样的化合物层进行了氮元素和氧元素的扫描,如图5所示。图5左图是对试样由表面向内做氧元素扫描。表面的氧元素含量高,这与表面氧化膜的存在相一致,同时氧元素的含量向化合物层的内部进入很深。图5右图是对化合物层中灰色疏松部分进行的元素扫描,结果表面氮元素的含量大大减少,而氧元素的含量大大增加。这证实了化合物层的疏松层是由于氮原子的分子化,形成气体氮分子,逃离试样的表面,从而形成孔洞,在深层QPQ处理进行氧化时,氧原子沿着孔洞进入化合物层的内部,使化合物层钝化,因此抗蚀性大大升高。显然,致密氮化层的表面积小于多孔疏松氮化层的表面积。如果工件外表面为致密氮化层,氧化时形成的Fe3O4氧化膜面积将小于外表面为疏松氮化层的Fe3O4氧化膜面积。Fe3O4氧化膜具有很高的化学稳定性和抗蚀性,Fe3O4氧化膜面积越大,其抗蚀性就越好。上述试验从理论上证实了深层QPQ处理的抗蚀性比常规QPQ处理抗蚀性高的原因。
图5 化合物层的元素扫描
深层QPQ技术应用研究
1.石油管防腐用深层QPQ技术的研究
成都工具研究所QPQ技术研发中心在2004~2006年接受了国家科技部的研究项目“石油管防腐用深层QPQ技术的研究”。
试验的中心环节是提高石油管的抗蚀性和石油管材料的力学性能达到合格标准。试验中利用了J55、N80、N80Q等多种石油管材料,进行了深层QPQ处理后抗蚀性与原材料和氮化处理的对比。抗蚀性主要盐雾试验方法。同时对常规QPQ处理后和深层QPQ处理后的试样进行了冲击试验和拉伸试验两项力学性能试验。
(1)深层QPQ处理对石油管材料抗盐雾蚀性的影响
J55材料深层QPQ处理后的盐雾试验结果如表1所示,深层QPQ处理试样盐雾试验的生锈时间是未处理的原材料的200多倍,是氮化试样的5倍多,如果深层QPQ处理后再涂密封剂,生锈时间又提高近4倍,达到800倍以上。
表1 J55材料深层QPQ处理后的盐雾试验
试样类型 |
平均生锈 时间/h |
平均抗 蚀性比 |
未处理试样 |
0.5 |
1 |
氮化试样 |
22 |
44 |
深层QPQ处理试样 |
123 |
246 |
深层QPQ+密封剂 |
443 |
886 |
N80材料深层QPQ处理后的盐雾试验的结果如表2所示,深层QPQ处理试样盐雾试验的生锈时间是未处理的原材料的近600倍,是氮化试样的10多倍,如果深层QPQ处理后再涂密封剂,生锈时间又延长1倍多,其中有的试样700多小时尚未生锈。
表2 N80材料深层QPQ处理后的盐雾试验
试样类型 |
平均生锈时间/h |
平均抗蚀性比 |
未处理试样 |
0.5 |
1 |
氮化试样 |
22 |
44 |
深层QPQ处理试样 |
298 |
596 |
深层QPQ+密封剂 |
>443 |
>886 |
N80Q材料深层QPQ处理后的盐雾试验的结果如表3所示,深层QPQ处理试样盐雾试验的生锈时间是未处理的原材料的470多倍,是氮化试样的近78倍,如果深层QPQ处理后再涂密封剂,生锈时间又提高近1倍,其中有的试样700多小时尚未生锈.
表3 N80Q材料深层QPQ处理后的盐雾试验
试样类型 |
平均生锈 时间/h |
平均抗 蚀性比 |
未处理试样 |
0.5 |
1 |
氮化试样 |
3 |
6 |
深层QPQ处理试样 |
235 |
470 |
深层QPQ+密封剂 |
>443 |
>886 |
(2)深层QPQ材料对石油管材料力学性能的影响
冲击试验:J55和N80两种材料深层QPQ处理后冲击试验的结果如表4所示。J55材料经深层QPQ处理后,冲击值为35J,远高于QPQ处理的19.5J,远远高于API标准的规定值15J。N80材料经深层QPQ处理后,冲击值为22J,远高于QPQ处理的16.4J,远远高于API标准的规定值15J。J55和N80两种材料经深层QPQ处理后冲击韧性分别比QPQ处理提高80%和30%。
表4 石油管材料的冲击试验
材料 |
深层QPQ 处理平均值/J |
QPQ处理 平均冲击值/J |
API标准 规定/J |
J55 |
35.3 |
19.5 |
≥15 |
N80 |
22 |
16.4 |
≥15 |
拉伸试验:对J55、N80和N80Q三种材料经深层QPQ处理以后,进行了拉伸试验。由于材料的力学性能指标对石油管来说,极其重要;而且QPQ处理的N80材料的延伸率达不到要求的指标,因此为了可靠起见,反复进行了三次拉伸试验,试验的结果如表5所示。所有三种材料经深层QPQ处理以后,材料的屈服强度,抗拉强度和延伸率都达到了API标准的规定值。
上述反复进行的拉伸试验说明,深层QPQ处理以后材料的力学性能可以全面达到API标准规定的指标,尤其是材料的延伸率比QPQ处理有所提高。
表5 深层QPQ处理石油管材料的拉伸试验
材料 |
试验 次数 |
编号 |
屈服强度/MPa |
抗拉强度/MPa |
伸长率(%) |
|||
σ0.2 |
平均值 |
σb |
平均值 |
δ |
平均值 |
|||
J55 |
第一次 |
1 |
436 |
432 |
694 |
690 |
18 |
18 |
2 |
429 |
685 |
18 |
|||||
3 |
431 |
691 |
18 |
|||||
第二次 |
4 |
437 |
437 |
681 |
682 |
22 |
21 |
|
5 |
440 |
689 |
19 |
|||||
6 |
435 |
677 |
21 |
|||||
第三次 |
7 |
420 |
421 |
662 |
665 |
18 |
19 |
|
8 |
421 |
666 |
19 |
|||||
9 |
421 |
666 |
20 |
|||||
API标准规定 |
397≤σ0.2≤552 |
σb≥517 |
e≥18% |
|||||
N80
|
第一次
|
1 |
632 |
635 |
804 |
814 |
15 |
14 |
2 |
628 |
817 |
14 |
|||||
3 |
644 |
821 |
14 |
|||||
第二次
|
4 |
621 |
625 |
793 |
802 |
17 |
17 |
|
5 |
625 |
801 |
17 |
|||||
6 |
630 |
811 |
16 |
|||||
第三次 |
7 |
612 |
618 |
764 |
780 |
16 |
15 |
|
8 |
651 |
813 |
15 |
|||||
9 |
590 |
763 |
14 |
|||||
AP标准规定 |
552≤σ0.2≤758 |
σb≥689 |
e≥14% |
深层QPQ处理之所以能够提高处理后材料的韧性,原因在于深层QPQ处理的渗层组织中有一层硬度较低,有一定朔性的中间层组织,这一点可以从图6和图7的比较中明显看出来。图6是QPQ处理的样品拉伸试验以后断裂的情况,其中化合物层产生大量的脆性裂纹以后,裂纹向基体扩展,直接使基体产生断裂。
图6 QPQ处理样品断裂情况
图7是深层QPQ处理的样品拉伸试验以后断裂的情况,从图中可以看到,拉伸使化合物层产生裂纹以后,向内扩展到了有一定朔性的过渡层,应力得到释放,裂纹得以扩展,试样被拉长(图中有较宽的裂纹)以后裂纹才向基体扩展,而此时基体尚未产生裂纹,因此延伸率得到提高。
图7 深层QPQ处理样品断裂情况
综合上述情况,与QPQ处理相比,深层QPQ处理在韧性和延伸率方面大有改善,为解决石油管材料QPQ处理后延伸率不合格和氮化管井下断裂问题提供了一种解决方法。
2.深层QPQ技术在工程机械活塞杆以及紧固件上的应用
深层QPQ技术现在已经在大型挖掘机、装载机等工程机械液压活塞杆以及紧固件方面进行试应用,结果证明采用深层QPQ技术来处理的液压活塞杆以及紧固件,化合物层深度、抗腐蚀性能以及表面硬度都满足技术要求。
45钢活塞杆,经深层QPQ处理后,化合物层深度35~40?m,表面硬度≥600 HV0.1。经深层QPQ处理的45钢活塞杆在中性盐雾试验机中进行盐雾试验,抗蚀性能达到408h还未生锈。
45紧固件,经深层QPQ处理后,化合物层深度30~40?m,表面硬度≥600 HV0.1。经深层QPQ处理的45钢紧固件在中性盐雾试验机中进行盐雾试验,抗蚀性能达到600h还未生锈。
结语
(1)深层QPQ技术的抗蚀性几乎完全依靠它的化合物层,因此化合物层的深度对抗蚀性有决定性作,加深化合物层深度是提高抗蚀性的有效途径。为了得到更满意的抗蚀性,深层QPQ 处理就应该获得面积尽可能大的致密完整的Fe3O4氧化膜。
(2)深层QPQ处理使化合物层的深度由15~20?m增加到到30~40?m,其化合物层深度为普通QPQ技术的2倍,经深层QPQ处理后再涂密封剂,抗盐雾腐蚀能力提高到400h以上。可使石油管材料的抗蚀性达到处理前的800倍以上,为氮化处理的20倍以上。
(3)深层QPQ处理石油管材料的力学性能完全达到美国石油协会API标准标准规定值,为解决石油管防腐难题提供了一种新的解决途径。由于时间和设备条件的限制,本项目尚未进入石油管下井实际应用阶段,目前正在寻求合作单位,准备进入实际生产应用阶段。
(4)深层QPQ技术现在已经在大型挖掘机、装载机等工程机械液压活塞杆以及紧固件方面进行试应用,结果证明采用深层QPQ技术来处理的活塞杆以及紧固件,化合物层深度≥30?m,表面硬度≥600 HV0.1,抗盐雾腐蚀性能达到400h以上还未生锈,完全满足了用户的技术要求。
注:文章、作品、图片版权归作者享有,如有作者来源标记有误或涉及侵权,请原创作者联系小编删除。
免责声明:本网站所转载的文字、图片与视频资料版权归原创作者所有,如果涉及侵权,请第一时间联系本网删除。
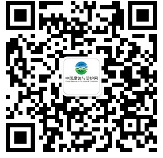
官方微信
《中国腐蚀与防护网电子期刊》征订启事
- 投稿联系:编辑部
- 电话:010-62313558-806
- 邮箱:fsfhzy666@163.com
- 中国腐蚀与防护网官方QQ群:140808414