过/再热器部件是超超临界机组锅炉中负责回收燃煤烟气能量、加热蒸汽、实现能量转化的关键部件,是锅炉中承受压力最大、温度最高、服役环境最苛刻的部分。由于国内外尚无可供600/620/620 ℃二次再热超超临界机组选用的合金,奥氏体钢仍是机组末级过/再热器的首选材料之一,它能满足在650 ℃蒸汽条件下服役的力学性能要求,但过高的蒸汽氧化速率限制了奥氏体钢在更高温度下服役的可能。相比开发更高等级的受热面材料,表面技术可以在不降低合金基体力学性能的基础上显着提高抗氧化性能。
为提高合金的抗蒸汽氧化性能,目前一般采取细化晶粒和内壁喷丸技术。这两项技术通过改变管内壁组织结构,使合金能快速生长出抗氧化所需的Cr2O3膜。但Cr2O3膜在高于600 ℃蒸汽中的稳定性较差,挥发性产物造成的氧化膜疏松问题会引发氧化膜剥落,并进一步导致堵管、爆管事故;另外,合金基体中的Cr 含量比较低,随着服役时间的增加,当生长氧化膜所需的Cr 含量得不到补充时,合金的抗氧化性能也会急剧下降。因此,这两项技术只能在服役初期短时间内提高合金的抗氧化性能,并不能从根本上解决合金的氧化和氧化膜剥落问题。
表面涂层技术因能显着提高合金的抗氧化性能,在航空、航天、石化等领域得到广泛应用,针对超(超) 临界锅炉用奥氏体钢管内表面涂层技术研究相对较少。Agüero 等[14]在P92 基体上制备了Cr 化物涂层,在650 ℃、30 MPa蒸汽下进行氧化1500 h,发现Cr 化物涂层试样虽然氧化膜较薄,在超临界环境下,纯Cr 化物涂层是不稳定的,并不是650 ℃级蒸汽发电站的最佳优化方案。氧化铝在水蒸汽中的稳定性远高于氧化铬,罗新民等将1Cr18Ni9Ti 不锈钢锅炉管试样在730 ℃铝浴中浸镀5 min 先获得良好的热浸镀铝层,然后以NH4Cl 为活化剂,在960 ℃密封扩散6 h,获得了与基体结合良好的扩散渗铝层,发现奥氏体不锈钢经扩散渗铝后的抗高温氧化性能优于未处理态。但是单一铝化物涂层一般脆性较高,Agüero 等制备了铁铝料浆涂层,发现其在600~650 ℃实验室环境下具有优良的抗蒸汽氧化性能,但现场实验中涂层氧化物剥落时间较短,这是因为铁铝涂层氧化物二者的热膨胀系数相差较大,锅炉启停过程会产生较大应力。因此,目前还没有一种合适的表面涂层材料及技术可以完全解决超(超) 临界锅炉用奥氏体合金的氧化问题。
本论文采用料浆法在18-8 系奥氏体钢TP347HFG 合金表面制备硅改性的铝化物涂层,通过对TP347H FG-AlSi 涂层的饱和蒸汽氧化行为的研究,并以更高等级的高铬HR3C合金为参比对象,分析不同耐蚀元素Al、Cr 对降低合金氧化速率的控制措施及机理,为现役18Cr 奥氏体合金管能继续服役于620~650 ℃二次再热机组及下一代锅炉机组提供技术参考。
1 实验方法实
验用TP347H FG、HR3C为供货态锅炉管,合金成分见表1。试样尺寸为10 mm×10 mm×2 mm,线切割加工后经过粗砂纸依次磨光至2000#细砂纸,使得试样表面光滑,没有明显表面缺陷,且具有统一的粗糙度和整洁度。采用料浆法在TP347H FG表面制备铝硅涂层,Al∶Si 配比为5∶1,将喷涂试样置于950 ℃的管式炉中,并在Ar气保护下热处理60 min。图1 为TP347H FG-AlSi 涂层的截面形貌,渗层出现了明显的分层,表现为外层与内层两层,外层为约20 μm 的FeAl 层、内层为Fe-Al 扩散层,深度约为30 μm。内、外层之间为富Al 杂质,外层Al 含量为30%左右,内层Al含量为10%左右。
蒸汽氧化实验在流动的100%水蒸汽环境中进行,动态水蒸气是通过将溶解氧含量为5~7 mg/L 的超纯水(电阻率约为18.25 MΩ·cm) 泵入预热装置(300 ℃) 获得连续的水蒸汽,进而通入反应炉。反应炉体内的蒸汽参数为:温度650 ℃,压力0.1 MPa,蒸汽流速100~120 mL/s,氧化时间为1000 h。采用精度为0.01 mg的电子天平称量样品随氧化时间的质量变化,绘制TP347H FG、TP347H FG-AlSi、HR3C在650 ℃纯水蒸汽环境下氧化1000 h 的氧化动力学曲线。采用ZEISS εigma HD扫描电子显微镜(SEM)观察样品的形貌特征,采用Oxford 能谱仪(EDS)对样品进行成分分析,采用D/MAX-RA 型X 射线(XRD) 对实验特征样品表面进行物相结构分析。
2 结果与讨论
2.1 氧化动力学
HR3C合金在650 ℃纯水蒸汽环境下氧化1000 h 的氧化动力学曲线。可以看出,在650 ℃纯水蒸汽环境下氧化时,氧化初期(0~350 h) TP347H FG的氧化增重与氧化时间近似呈抛物线关系,拟合的抛物线速率常数为0.0058 mg2·cm- 4·h- 1;当氧化时间超过350 h 后,高温与水蒸气的共同作用使得氧化膜稳定性变差,此时开始发生剥落,而在600 h 后开始大量剥落,氧化增重曲线明显下降,氧化1000 h 后增重为- 2.91814 mg·cm- 2。TP347H FG- AlSi 涂层在650 ℃纯水蒸汽环境下氧化1000 h 的氧化增重很少,氧化1000 h 后增重为0.06157 mg·cm-2,说明在TP347H FG基体上制备AlSi 涂层,可显着提高基体材料的抗蒸汽氧化性能。相同条件下,TP347H FG合金在650 ℃纯水蒸汽环境下氧化1000 h 后增重为TP347H FG-AlSi 涂层的47 倍。相比之下,HR3C合金在650 ℃纯水蒸汽环境下氧化1000 h 后增重亦很小,氧化1000 h 后增重为:0.08163 mg·cm- 2。说明HR3C合金在650 ℃纯水蒸汽环境下同样具有良好的氧化性能。图2b 为TP347H FG-AlSi、HR3C合金的氧化增重曲线放大图,由图可知,HR3C 合金在200 h 之前的氧化动力学曲线遵从抛物线,拟合的抛物线速率常数为3.464×10-5 mg2·cm-4·h-1,200 h 之后氧化增重基本稳定。TP347H FG-AlSi 涂层的氧化动力学遵从抛物线规律,拟合的抛物线速率常数为3.790×10-6 mg2·cm-4·h-1,且曲线位于HR3C 合金下方,说明在650 ℃饱和水蒸汽中TP347H FG-AlSi 的抗氧化性能优于HR3C合金。
2.2 氧化产物形貌分析
图3 为TP347H FG、TP347H FG-AlSi、HR3C 合金在650 ℃饱和水蒸汽环境下分别氧化50,500 和1000 h 后的表面形貌图。可以看出,在650 ℃纯水蒸汽环境下,TP347H FG基体合金氧化50 h 后表面覆盖致密氧化膜,局部出现了瘤状氧化物,且瘤状氧化物尺寸较小。随着氧化时间延长至500 和1000 h后,TP347H FG 基体表面氧化膜开始发生剥落,1000 h 后出现大面积剥落。在650 ℃纯水蒸汽环境下,TP347H FG-AlSi 涂层表面均形成颗粒状氧化物。而HR3C 合金氧化50,500 和1000 h 后表面均被氧化物所覆盖,氧化膜平整致密,并存在少量瘤状氧化物,且瘤状氧化物尺寸较小。随着氧化时间延长至500 和1000 h 后,合金表面瘤状氧化物的尺寸有所增大,数量有所增加,氧化1000 与500 h 相比,表面瘤状氧化物尺寸、数量变化不大。
图4 为TP347H FG、TP347H FG-AlSi、HR3C 合金在650 ℃纯水蒸汽环境下氧化50,500 和1000 h后的截面形貌图。可以看出,TP347H FG 基体在650 ℃纯水蒸汽环境下氧化50 h 后的氧化膜均匀致密,厚度为1 μm左右。随着氧化时间延长,试样表面氧化膜下方局部出现内氧化,与试样表面瘤状氧化物形成了双层结构氧化膜。氧化500 h 后,外层氧化物较为疏松,出现了裂纹、空洞,局部已出现破碎;氧化1000 h 后,发生严重内氧化,形成一层内氧化物,厚度为50 μm左右,此时外层表面瘤状氧化物发生剥落,与表面形貌结果一致。TP347H FG-AlSi 涂层在650 ℃纯水蒸汽环境下氧化50,500 和1000 h后涂层外层结构完整,并有一层极薄的氧化膜;内层则与合金基体发生互扩散,使得涂层Fe-Al 扩散区变厚,氧化1000 h 后Fe-Al 扩散区约为60 μm。相比之下,HR3C合金在650 ℃纯水蒸汽环境下氧化50,500 和1000 h 的氧化膜整体均匀、完整致密,并随着氧化时间增长,保护性氧化膜厚度增厚,氧化1000 h厚度为1 μm左右。
2.3 氧化产物成分及结构
图5为合金在650 ℃纯水蒸汽环境下氧化1000 h后的元素面分布图,图6 为合金在650 ℃纯水蒸汽环境下氧化1000 h 后的XRD图谱。TP347H FG 合金基体在650 ℃纯水蒸汽环境下氧化后形成的瘤状氧化物富集Fe、O元素,而平整区的氧化物富集Cr、Fe、O元素,以及少量的Mn。结合XRD表征结果,可推知瘤状氧化物由Fe3O4构成,而平整区的氧化物的组成为(Cr,Mn)2O3。TP347H FG 合金氧化后,试样表面氧化膜下方局部发生的内氧化,其氧化物为FeCr2O4,与试样表面瘤状氧化物Fe3O4形成了双层结构氧化膜。TP347H FG-AlSi 涂层表面显示较暗的区域的主要成分是Al,较亮的区域主要是富铝氧化物,说明高温氧化1000 h 后Al 并未被完全氧化成Al2O3 (对应的XRD中显示出比较强的基体峰,同时出现部分Al2O3衍射峰),富铝层还可以为表面生成致密的Al2O3膜提供充足的Al 源,很好地阻挡O对基体的侵蚀。HR3C 合金氧化后,主要形成保护性Cr2O3氧化膜,并含有Mn元素。
氧化初期TP347H FG 合金表面形成一层致密保护性Cr2O3氧化膜,随氧化继续,Fe 通过氧化膜与缺陷向氧化膜/水蒸气界面扩散形成瘤状Fe3O4,与此同时,水蒸汽通过这些缺陷向内扩散氧化基体,发生内氧化,内氧化物与试样表面瘤状氧化物形成双层结构氧化膜。合金外层瘤状氧化物Fe3O4为疏松层,其间有空洞与裂纹,容易开裂脱落,加之氧化过程中内外层界面处会形成孔洞,最终导致外氧化层和内氧化层之间形成剥离空隙,在热应力作用下,发生剥落。对于高Cr 含量的HR3C来说,合金中较高的Cr 含量促使HR3C在较短的热暴露时间内,表面即形成致密连续的Cr2O3膜。氧化膜的生长由Cr3+等阳离子的向外扩散控制,氧化动力学遵循抛物线规律。随氧化时间延长,氧化膜不断增厚。
TP347H FG合金涂覆铝硅涂层后具有良好的抗氧化性能。这主要是因为,氧化初期水蒸气与涂层中Al 元素发生选择性氧化,生成单分子氧化膜,其后是以电化学反应实现膜的生长,且生长速度较慢,Al 并未被完全氧化成Al2O3,富铝层还可以为表面生成致密的Al2O3膜提供充足的Al 源,很好地阻挡O对基体的侵蚀。氧化初期起主导作用的是界面反应。随着氧化膜的形成,反应物质的扩散速度成为氧化速度的控制因素。一方面,形成的Al2O3膜可降低元素扩散系数;另一方面,未被完全氧化成Al2O3的富铝层还可以为合金继续生成Al2O3膜提供充足的Al 源,两方面原因使得TP347H FG-AlSi 涂层具有优良的抗蒸汽氧化性能。
3 结论
(1) 氧化初期(0~350 h) TP347H FG的动力学曲线遵循抛物线关系,抛物线速率常数为0.0058 mg2·cm-4·h-1,氧化600 h 后外层氧化膜发生严重剥落,氧化1000 h 后增重为:-2.91814 mg·cm-2。外层疏松层瘤状氧化物Fe3O4与试样表面氧化膜下方内氧化物FeCr2O4呈双层结构。
(2) Al-Si 涂层试样氧化1000 h 的氧化动力学曲线遵循抛物线规律,氧化增重为:0.06157 mg·cm-2,试样表面形成保护性Al2O3 氧化膜,可显着提升TP347H FG钢抗蒸汽氧化能力,较基体的抗蒸汽氧化性能提高47倍。
(3) HR3C 合金在200 h 之前的氧化动力学曲线遵从抛物线规律,抛物线速率常数为3.464×10- 5 mg2·cm- 4·h- 1,200 h 之后氧化增重基本稳定。HR3C合金中较高的Cr 含量促使HR3C在较短时间内,表面即形成致密连续的Cr2O3膜,在650 ℃纯水蒸汽环境下具有良好的抗氧化性能。
(4) TP347H FG-AlSi 涂层抗蒸汽氧化性能与HR3C 相当,氧化1000 h 内氧化增重略低于HR3C。Cr 元素是提高合金抗氧化性能的关键,表面涂层亦可降低合金氧化速率,两种途径可为现役及下一代锅炉机组提供技术支撑。
免责声明:本网站所转载的文字、图片与视频资料版权归原创作者所有,如果涉及侵权,请第一时间联系本网删除。
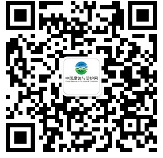
官方微信
《中国腐蚀与防护网电子期刊》征订启事
- 投稿联系:编辑部
- 电话:010-62313558-806
- 邮箱:fsfhzy666@163.com
- 中国腐蚀与防护网官方QQ群:140808414